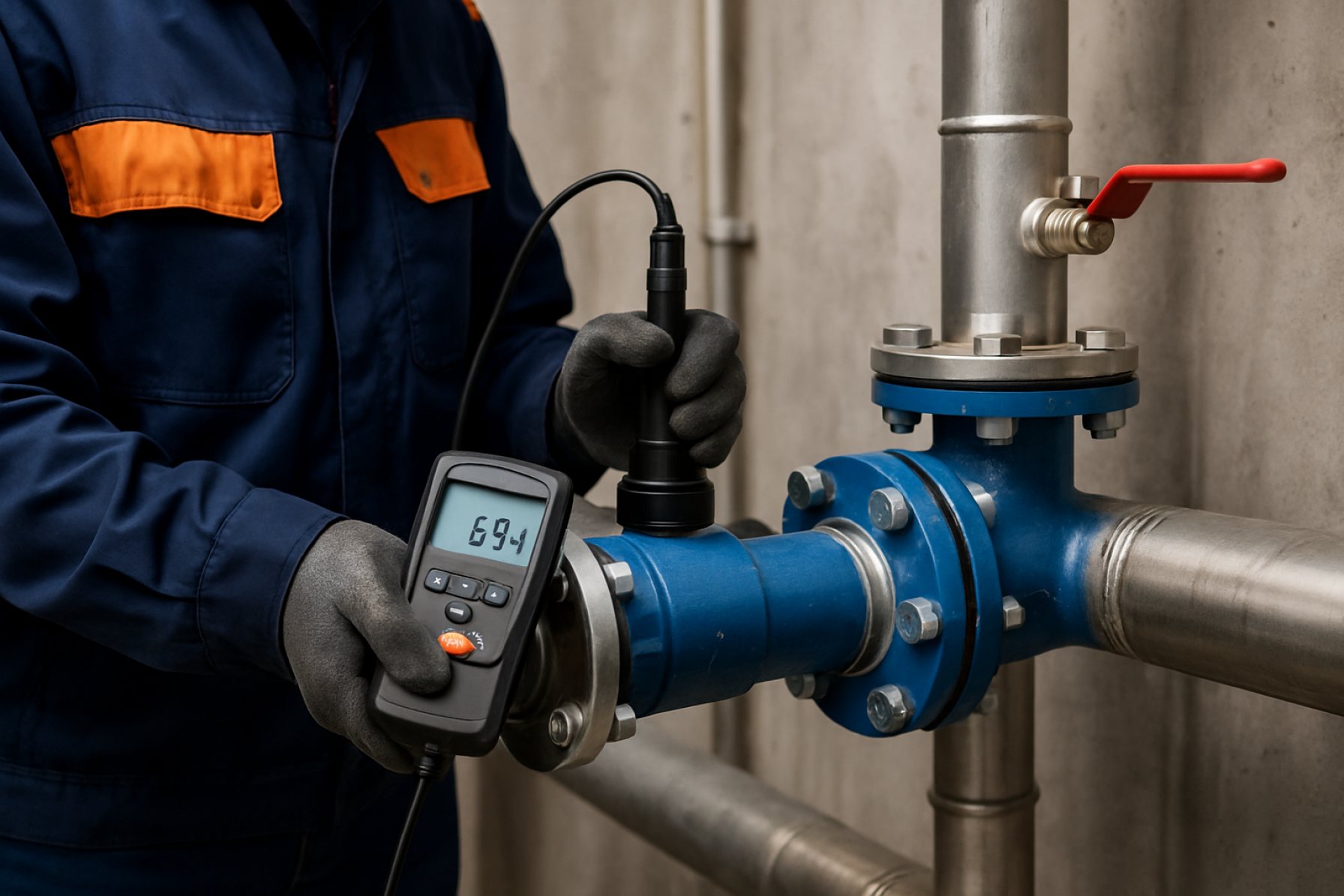
Table of Contents
- Executive Summary: Key Findings and Emerging Trends
- Market Size and 2025–2029 Forecasts: Revenue, Volume, and Regional Breakdowns
- Regulatory Landscape: New Compliance Pressures and Global Standards (e.g., asme.org)
- Latest Testing Technologies: From Ultrasonics to AI-Driven Analytics
- Competitive Analysis: Major Players, Strategic Moves, and Innovations (e.g., flexitallic.com, garlock.com)
- Sector Applications: Oil & Gas, Chemicals, Power Generation, and Beyond
- Risk Mitigation: How Integrity Testing Prevents Costly Failures and Environmental Harm
- Digitalization & IoT: The Next Frontier in Gasket Monitoring (e.g., emerson.com)
- Challenges: Skill Gaps, Supply Chain Constraints, and Evolving Customer Demands
- Future Outlook: What’s Next for Pipework Gasket Integrity Testing Through 2029
- Sources & References
Executive Summary: Key Findings and Emerging Trends
Pipework gasket integrity testing is undergoing significant transformation in 2025, driven by advancements in digital monitoring, heightened regulatory scrutiny, and a growing emphasis on operational safety across sectors such as oil & gas, chemical processing, and power generation. Key findings indicate a widespread shift from traditional manual testing methods toward automated, sensor-based systems capable of providing real-time data on gasket performance and early detection of leaks.
The adoption of digital leak detection and integrity monitoring technologies is accelerating, with leading manufacturers integrating wireless sensors and cloud-based analytics into their offerings. For example, Trelleborg and Garlock have expanded their product lines to include gaskets with embedded monitoring capabilities, enabling predictive maintenance and reducing unplanned downtime.
Regulatory agencies are also tightening standards for gasket integrity, particularly in hazardous environments. Organizations such as the Health and Safety Executive (HSE) in the UK and the Occupational Safety and Health Administration (OSHA) in the United States are emphasizing the criticality of regular gasket integrity assessments to prevent fugitive emissions and catastrophic failures. In response, operators are deploying advanced hydrostatic and pneumatic testing procedures, supported by digital documentation and traceability, to comply with these stricter mandates.
Data from major industry bodies suggest that integrity-related incidents are trending downward in facilities that have adopted real-time monitoring systems. According to BP, the integration of asset integrity programs, including gasket monitoring, has contributed to a measurable reduction in loss-of-containment events over the past two years.
Looking ahead, the market is poised for further innovation as suppliers invest in materials science and smart technologies. The next few years are expected to see broader deployment of AI-driven diagnostics, enabling earlier detection of failure modes and enhanced lifecycle management. Partnerships between gasket manufacturers and digital solution providers are anticipated to accelerate, aligning with the industry’s broader digital transformation and sustainability goals.
In summary, 2025 marks a pivotal year for pipework gasket integrity testing, characterized by increased adoption of digital tools, enhanced safety standards, and a data-driven approach to asset management. These trends are set to redefine best practices and establish higher benchmarks for reliability and environmental stewardship in the years ahead.
Market Size and 2025–2029 Forecasts: Revenue, Volume, and Regional Breakdowns
The global market for pipework gasket integrity testing is poised for notable growth from 2025 to 2029, driven by stringent regulatory standards, increased emphasis on environmental safety, and ongoing investments in industrial infrastructure. In 2025, the market is expected to surpass USD 650 million in revenue, with a projected compound annual growth rate (CAGR) of 6-7% through 2029. This expansion is underpinned by rising demand from oil & gas, chemical processing, power generation, and water treatment sectors, where gasket failure can result in significant safety and environmental incidents.
Regionally, North America and Europe remain leading markets, accounting for over 55% of global revenue, owing to robust regulatory frameworks enforced by bodies such as the American Society of Mechanical Engineers (ASME) and the European Committee for Standardization (CEN). These regions are characterized by aging infrastructure and a high frequency of scheduled maintenance, necessitating advanced testing solutions. The U.S. market, in particular, is propelled by ongoing pipeline modernization programs and the implementation of new emission control protocols by the Environmental Protection Agency (EPA).
Asia-Pacific is forecasted to be the fastest-growing region, with annual revenue growth exceeding 8% through 2029. This surge is attributed to rapid industrialization, especially in China, India, and Southeast Asia, alongside increasing awareness about operational safety and leak prevention. Major industry players such as Fugro and TÜV SÜD are expanding their presence in these markets by offering localized gasket integrity testing services and training programs. Latin America and the Middle East also exhibit strong growth potential, supported by ongoing oil & gas projects and the adoption of international quality standards.
In terms of volume, the number of gasket integrity tests performed worldwide is estimated to reach 2.5 million in 2025, with a steady annual increase projected as infrastructure ages and regulatory scrutiny intensifies. Technological advancements, such as digital leak detection and automated test systems, are expected to further boost market size by enabling more efficient and accurate assessment of pipework gasket integrity (Emerson).
Overall, the outlook for pipework gasket integrity testing from 2025 to 2029 is robust, shaped by regulatory drivers, technological innovation, and expanding industrial activity across both mature and emerging markets.
Regulatory Landscape: New Compliance Pressures and Global Standards (e.g., asme.org)
The regulatory landscape for pipework gasket integrity testing is evolving rapidly in 2025, driven by heightened safety, environmental, and reliability demands across industries such as oil & gas, chemical processing, and power generation. Major global standards bodies are updating their requirements in response to high-profile incidents and new technological capabilities. In the United States, the American Society of Mechanical Engineers (ASME) continues to refine its Boiler and Pressure Vessel Code (BPVC) and the B31 series of pipe codes, placing increased emphasis on validated gasket testing procedures, traceability, and documentation. Recent code updates highlight the necessity of pre-service and in-service testing for gasketed joints, focusing on minimizing fugitive emissions and ensuring long-term joint integrity.
In Europe, the European Committee for Standardization (CEN) and national bodies are aligning EN 1591-1 and EN 13555 standards with new emission reduction targets under the European Green Deal, introducing stricter requirements for type testing and in-situ verification of gasketed connections. The International Organization for Standardization (ISO) is similarly accelerating work on the ISO 15848 series, which governs the testing and classification of valve and flange leakage, with direct implications for gasket performance qualification.
Regulators are also enhancing enforcement and audit mechanisms. For example, the U.S. Environmental Protection Agency (EPA) has expanded Leak Detection and Repair (LDAR) mandates to cover more frequent and rigorous testing of flange connections, including mandatory use of certified testing equipment and digital record-keeping. The United Kingdom’s Health and Safety Executive (Health and Safety Executive) is intensifying oversight of major hazard facilities, requiring detailed demonstration of gasket integrity as part of Safety Case submissions.
Looking ahead, operators face growing compliance pressures as regulators demand not only adherence to evolving standards but also adoption of best-available technologies for in-situ gasket testing and real-time leak detection. The trend toward harmonization of global standards—especially for facilities operating across multiple jurisdictions—means companies must anticipate and adapt to overlapping requirements. Increased digitalization, such as electronic test records and remote audit capabilities, is expected to become integral to future compliance strategies. The regulatory trajectory indicates that by the late 2020s, third-party certification and continuous integrity monitoring may become baseline expectations for critical pipework systems worldwide.
Latest Testing Technologies: From Ultrasonics to AI-Driven Analytics
In 2025, the field of pipework gasket integrity testing is witnessing rapid advancements, driven by operational safety imperatives and the need for minimizing unplanned downtime in energy, chemical, and manufacturing industries. Traditional hydrostatic and pneumatic leak tests have increasingly been supplemented—and in many cases, partially replaced—by advanced non-destructive evaluation (NDE) technologies and digital analytics.
Ultrasonic leak detection has become a frontline method, with leading manufacturers incorporating phased array and time-of-flight diffraction (TOFD) capabilities. These techniques provide high-resolution imaging of gasketed joints, allowing operators to detect micro-leaks and flaws without dismantling equipment. For instance, Olympus has expanded its portfolio of ultrasonic equipment specifically designed for in-situ gasket and flange integrity assessments, offering improved signal processing to better distinguish between actual defects and benign anomalies.
Acoustic emission (AE) monitoring is also gaining greater traction, especially for real-time leak detection during plant operations. AE sensors detect high-frequency stress waves emitted by active leaks or crack propagation in gasketed joints. Companies such as Phoenix Inspection Systems Limited are deploying advanced AE sensor networks that can pinpoint leak locations and quantify leak rates, facilitating predictive maintenance programs.
The most transformative trend in 2025 is the integration of artificial intelligence (AI) and machine learning with sensor data and digital twins. AI-driven analytics platforms now process vast data streams from ultrasonic, acoustic, and thermal sensors to identify subtle patterns that human operators might miss. Emerson offers AI-enabled leak detection and integrity monitoring solutions that deliver real-time risk scoring and automated reporting, dramatically shortening the time between leak initiation and response.
Additionally, the adoption of digital twins—virtual replicas of pipework systems—enables continuous gasket integrity assessment by simulating aging, operational stress, and environmental effects. Companies like Siemens are at the forefront, integrating real-time sensor feedback into digital models for ongoing risk evaluation.
Looking forward, the industry is expected to see broader deployment of these technologies, with regulatory bodies and operators increasingly mandating advanced integrity testing as part of asset management and compliance regimes. The convergence of sensor innovation, AI analytics, and simulation is poised to further enhance safety, reduce fugitive emissions, and optimize maintenance costs across the pipeline and process industries.
Competitive Analysis: Major Players, Strategic Moves, and Innovations (e.g., flexitallic.com, garlock.com)
The pipework gasket integrity testing sector is witnessing increased competition and innovation as industries prioritize safety, emissions reduction, and operational efficiency in 2025. Major players such as Flexitallic Group and Garlock remain at the forefront, leveraging advanced materials and digital tools to improve the reliability and performance of sealing solutions.
- Flexitallic Group continues to expand its global footprint, emphasizing proprietary gasket technologies like Thermiculite® and the use of its Integrity Software suite. This suite, updated for 2024-2025, integrates digital data capture with real-time monitoring, allowing rapid assessment of gasket integrity during plant turnarounds and routine maintenance. Flexitallic’s partnerships with major oil, gas, and chemical companies underscore its commitment to lifecycle asset management and leak prevention.
- Garlock has focused on new product development and testing protocols, particularly in response to tightening fugitive emissions standards. Their graphite-based gaskets and recently enhanced flange leak testing guidance are engineered for high-integrity sealing in challenging environments. Garlock’s investment in training and certification programs for installers and inspectors further differentiates their offering, with a focus on consistent, verifiable installation outcomes.
- Other notable competitors, such as KLINGER and SPETECH, are investing in automated leak detection and remote monitoring. KLINGER has expanded its digital service portfolio, including gasket traceability and condition monitoring, while SPETECH is developing integrated test benches that combine pressure, temperature, and emissions monitoring for comprehensive integrity validation.
Strategically, major players are aligning with global decarbonization efforts and stricter regulatory frameworks (e.g., European Green Deal, US EPA emission standards) by introducing low-emission gasket materials and advanced integrity testing protocols. Collaborations with end-users for field trials and data sharing are expected to accelerate the adoption of predictive maintenance and digital twin technologies in the next few years.
The outlook for 2025 and beyond suggests that digitalization, automation, and sustainability will drive competitive differentiation in pipework gasket integrity testing. Industry leaders are expected to continue investing in R&D and strategic partnerships to meet the evolving needs of process industries, ensuring safer, more reliable, and environmentally compliant operations.
Sector Applications: Oil & Gas, Chemicals, Power Generation, and Beyond
Pipework gasket integrity testing is a cornerstone of operational safety and reliability across sectors such as oil & gas, chemicals, and power generation. In 2025, the adoption of advanced gasket integrity testing methods is accelerating, driven by rising safety regulations and an industry-wide focus on emissions reduction. Operators are prioritizing robust testing regimes to proactively address gasket failures—a leading cause of hydrocarbon releases and fugitive emissions.
- Oil & Gas: With tightening emissions standards, especially for methane, operators are deploying technologies for both pre-installation and in-service gasket integrity validation. Companies like Shell and BP are integrating advanced leak detection and flange management systems to minimize unplanned shutdowns and environmental incidents. Specialized service providers, such as Fugro, offer gasket integrity assessment as part of comprehensive asset integrity management programs.
- Chemicals: The chemicals sector is especially risk-averse due to the hazardous nature of handled substances. Firms like BASF emphasize standardized gasket installation and torque verification processes, complemented by periodic ultrasonic or pressure-based leak testing. This approach ensures compliance with evolving safety standards, such as those outlined by the Institution of Chemical Engineers.
- Power Generation: In nuclear and conventional power plants, gasket failure can have critical safety and operational impacts. Operators such as EDF Energy are investing in predictive maintenance, employing digital monitoring systems to track joint integrity and proactively schedule gasket replacements. This digitalization trend is expected to drive further enhancements in reliability and regulatory compliance.
- Beyond Traditional Sectors: The need for gasket integrity testing is expanding into hydrogen, carbon capture, and battery manufacturing, where high-pressure pipework presents similar risks. Companies like Air Liquide are adapting oil & gas best practices for these emerging sectors, recognizing that robust sealing and testing are vital for safe scale-up.
Looking ahead, adoption of real-time monitoring, smart sensors, and digital record-keeping is set to transform gasket integrity management. Cross-sector collaboration is accelerating the development of harmonized testing standards and data-driven maintenance strategies, with organizations such as the Energy Institute providing industry guidance. These trends underpin a proactive outlook for gasket integrity, supporting safer, more efficient, and environmentally responsible operations through 2025 and beyond.
Risk Mitigation: How Integrity Testing Prevents Costly Failures and Environmental Harm
In 2025, the importance of pipework gasket integrity testing continues to escalate across industries such as oil and gas, chemicals, and power generation, driven by stricter regulatory frameworks and heightened environmental awareness. Gasket failures remain a primary cause of fugitive emissions and unplanned shutdowns, with recent industry data attributing over 30% of flange-related leaks to gasket integrity issues. This risk affects not only operational continuity but also exposes facilities to significant regulatory penalties and reputational harm.
Recent high-profile incidents underscore the need for robust gasket integrity programs. For example, several refineries in North America reported unplanned losses exceeding $10 million each in 2024 due to gasket failures, resulting in both environmental releases and prolonged downtime. These events have prompted a surge in the adoption of advanced integrity testing protocols, including hydrotesting, helium leak detection, and bolt load monitoring, to proactively identify potential failure points before commissioning or restart.
Current best practice emphasizes a combination of non-destructive testing and real-time monitoring. Technologies such as ultrasonic leak detection and smart sensor-enabled gaskets are increasingly deployed to provide early warning of loss of containment. Industry leaders like Flexitallic and Frenzelit are actively developing and delivering integrated gasket testing services that incorporate digital documentation and analytics to ensure traceability and compliance.
Regulatory bodies, including the American Petroleum Institute (API) and ISO, are updating standards to mandate more frequent and rigorous integrity assessments. The recently revised API 570 and ISO 45001 standards emphasize not only initial gasket performance but also ongoing verification throughout the asset lifecycle. This regulatory shift is expected to be further reinforced by upcoming environmental regulations targeting fugitive emissions in both North America and Europe.
Looking forward, industry outlook suggests that digitalization and automation will increasingly shape the landscape of gasket integrity testing. The integration of IoT-based condition monitoring and predictive analytics is anticipated to reduce manual inspection frequency while enhancing detection accuracy. As facilities invest in these technologies, the risk of catastrophic gasket failures—and their associated financial and environmental costs—is expected to decrease, supporting a more sustainable and resilient industrial infrastructure.
Digitalization & IoT: The Next Frontier in Gasket Monitoring (e.g., emerson.com)
Digitalization and the Internet of Things (IoT) are rapidly transforming pipework gasket integrity testing, ushering in a new era of real-time monitoring, predictive maintenance, and enhanced safety. As industrial operators prioritize uptime and environmental compliance, the adoption of digital gasket monitoring solutions is gaining significant momentum in 2025 and is set to accelerate further in the next several years.
One of the most notable trends is the integration of wireless sensors directly at flange connections, enabling continuous tracking of parameters such as temperature, pressure, and even leak detection at the gasket interface. Companies like Emerson Electric Co. have launched digital fugitive emissions monitoring systems that incorporate IoT sensors to detect minute leaks, providing early warnings before they escalate into safety or environmental hazards. This is particularly important as regulatory agencies tighten fugitive emissions standards and require more rigorous documentation and traceability.
Other manufacturers are advancing digital gasket monitoring with smart bolting and load-sensing technology. Hilti Group, for example, has introduced smart tools that record and transmit bolt tightening data, ensuring correct gasket compression. This data can be integrated into asset management systems, supporting both maintenance planning and regulatory compliance.
Data integration and analytics platforms are another key development. Through cloud-based dashboards and mobile apps, maintenance teams can visualize gasket health across entire facilities or remote assets, using predictive analytics to schedule interventions before leaks occur. Honeywell International Inc. has expanded its digital transformation offerings, including connected plant solutions that aggregate sensor data for actionable insights on pipeline and flange integrity.
Looking ahead to the remainder of 2025 and beyond, the outlook for digitalization in gasket integrity testing is robust. The push for zero-leak operations, coupled with workforce shortages and the need for remote monitoring, is expected to further drive adoption. Industry leaders are investing in expanding the interoperability of their IoT solutions, enabling seamless integration with existing plant control and safety systems. As a result, the next few years will likely see more widespread deployment of digital gasket monitoring across sectors such as oil & gas, chemicals, and power generation, with measurable improvements in reliability, compliance, and cost efficiency.
Challenges: Skill Gaps, Supply Chain Constraints, and Evolving Customer Demands
The landscape of pipework gasket integrity testing in 2025 is shaped by several converging challenges, notably skill gaps, persistent supply chain constraints, and evolving customer demands. These factors are prompting both suppliers and end-users to adapt their strategies and invest in new solutions to safeguard reliability and compliance in critical industries such as oil & gas, chemical processing, and power generation.
A pronounced skill gap is emerging as experienced technicians retire and fewer new entrants possess the specialized knowledge required for advanced gasket integrity testing and installation. According to Flexitallic, a global leader in gasket technology, the shortage of trained personnel is a critical concern, leading to increased investment in training programs and digital tools that streamline testing and documentation. Companies are turning to augmented reality and digital twin platforms to accelerate workforce competency and knowledge transfer.
Supply chain constraints, intensified by ongoing geopolitical tensions and the aftershocks of the COVID-19 pandemic, continue to disrupt the availability of high-performance gasket materials and testing equipment. Garlock, a major manufacturer, highlights delays in raw material sourcing and logistics bottlenecks, which can lead to longer lead times for both gaskets and the specialized equipment needed for integrity testing. In 2024 and into 2025, many operators are reassessing their supplier networks and seeking local or regional alternatives to mitigate these risks.
Customer expectations are also evolving, with a growing emphasis on sustainability, regulatory compliance, and predictive maintenance. End-users are demanding not only products that ensure leak-free performance but also integrated testing and monitoring solutions that align with digital transformation initiatives. Freudenberg Sealing Technologies reports a surge in requests for “smart” gaskets and sensors capable of providing real-time data on seal performance and integrity. This shift is pushing suppliers to innovate in both materials science and digital diagnostics, often in collaboration with end-users.
Looking ahead to the next few years, the sector is expected to see continued investment in automation, advanced materials, and workforce development. Collaborative training programs, supply chain diversification, and the integration of digital technologies into gasket integrity testing protocols are likely to be central themes as the industry responds to these challenges and prepares for future regulatory and operational demands.
Future Outlook: What’s Next for Pipework Gasket Integrity Testing Through 2029
The future of pipework gasket integrity testing through 2029 is poised for significant transformation, driven by digitalization, advanced materials, regulatory focus, and the expanding demands of critical industries. As industries such as oil & gas, pharmaceuticals, and chemicals continue to prioritize safety and environmental stewardship, the necessity for reliable gasket testing solutions is only expected to intensify.
One major development is the integration of digital monitoring and data analytics into gasket integrity management. Operators are increasingly adopting smart sensors and digital twins to enable real-time leak detection and predictive maintenance. For example, Emerson and Swagelok have introduced connected solutions that not only monitor gasket performance but also provide actionable diagnostics, helping to minimize downtime and prevent catastrophic failures.
Advancements in non-destructive testing (NDT) techniques are also shaping the landscape. Ultrasonic, thermal imaging, and acoustic emission technologies are being refined for more accurate in-situ assessment of gasket health. EJ and Trelleborg Pipe Seals are among the manufacturers investing in the development and deployment of these techniques, aiming to provide faster, safer, and more reliable test results.
Material innovation is another frontier, with manufacturers developing next-generation gaskets made from advanced elastomers and composites that exhibit greater chemical resistance and longevity. This shift is particularly relevant for hydrogen infrastructure and aggressive chemical processes, where traditional gasket materials may underperform. Companies like Garlock are at the forefront, offering materials tailored for emerging applications and stricter emissions standards.
Regulatory bodies are tightening requirements on fugitive emissions and leak detection, especially in response to global environmental commitments. The American Petroleum Institute (API) and the European Sealing Association have both updated best practices and standards for gasket testing, prompting widespread adoption of more rigorous assessment protocols (API, European Sealing Association).
Looking ahead, automation and remote inspection technologies are expected to further reduce manual intervention and enhance safety. By 2029, it is anticipated that most critical facilities will standardize the use of automated, digital integrity testing platforms, supported by continuous data streams and AI-driven analysis. As the industry adapts to new energy vectors and sustainability imperatives, the evolution of pipework gasket integrity testing will remain central to operational resilience and compliance.
Sources & References
- Trelleborg
- Garlock
- Health and Safety Executive (HSE)
- BP
- ASME
- CEN
- Fugro
- Emerson
- ISO
- Olympus
- Phoenix Inspection Systems Limited
- Siemens
- KLINGER
- Shell
- BASF
- Institution of Chemical Engineers
- Air Liquide
- Energy Institute
- Frenzelit
- American Petroleum Institute (API)
- Hilti Group
- Honeywell International Inc.
- Swagelok
- European Sealing Association