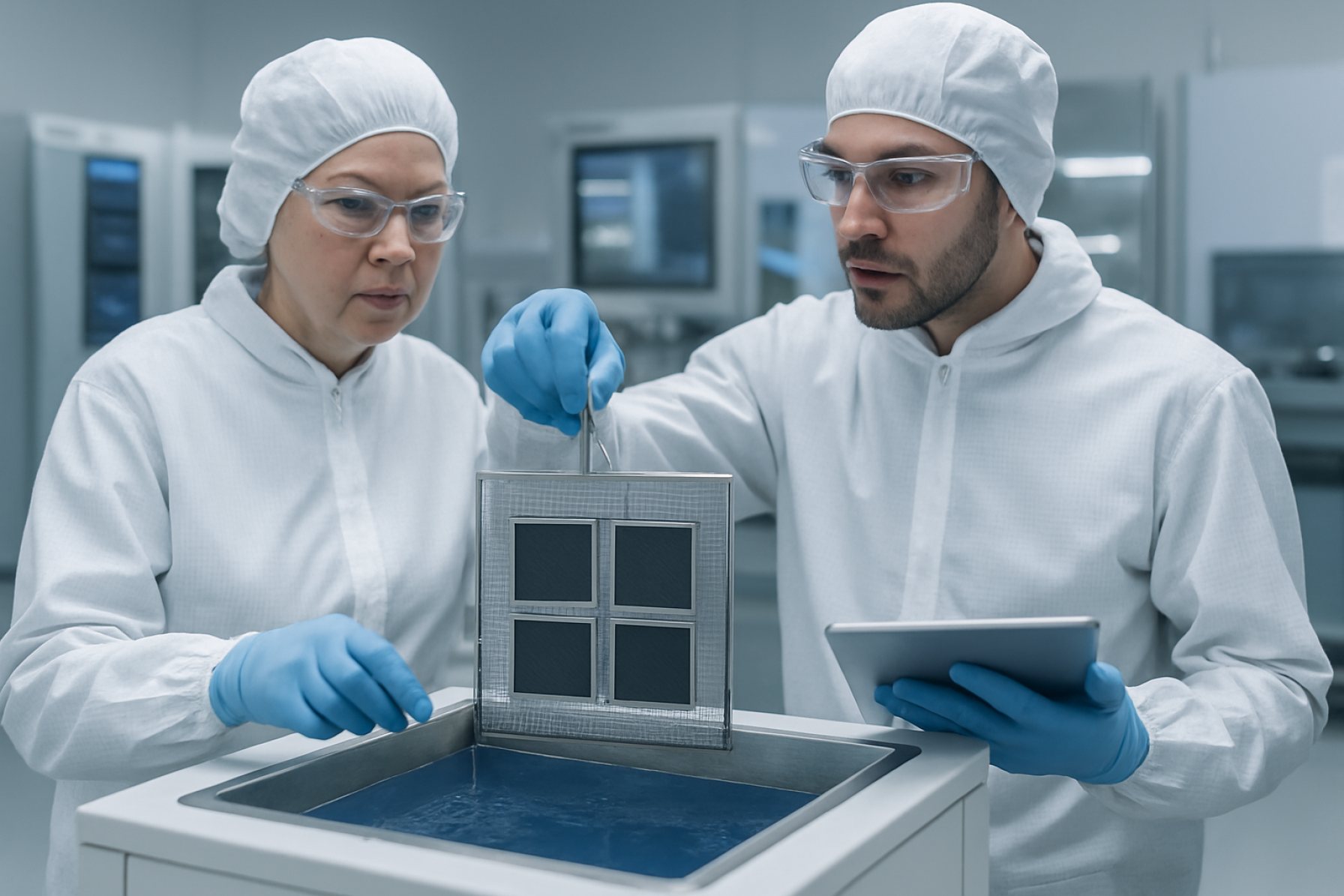
Table of Contents
- Executive Summary: Key Findings and 2025 Outlook
- Market Sizing & Forecasts Through 2030
- Competitive Landscape: Top Wet Chemical Etching Consulting Firms
- Emerging Applications: Semiconductors, MEMS, and Beyond
- Technological Breakthroughs Shaping Wet Chemical Etching
- Sustainability & Environmental Regulations Impact
- Global Demand Drivers and Regional Hotspots
- Key Partnerships: OEMs, Foundries, and Research Institutes
- Strategic Recommendations for Clients and Investors
- Future Trends: Where Are Wet Chemical Etching Consultants Headed by 2030?
- Sources & References
Executive Summary: Key Findings and 2025 Outlook
The wet chemical etching sector is experiencing robust momentum as critical industries—including semiconductors, MEMS, photovoltaics, and advanced packaging—intensify their demand for precision etching solutions. As of 2025, consultants specializing in wet chemical etching are pivotal in guiding manufacturers through process optimization, safety compliance, and the integration of novel chemistries and equipment. This executive summary highlights major trends and forecasts shaping the consulting landscape for the immediate future.
- Surge in Semiconductor and Advanced Packaging Demand: The semiconductor industry’s rapid expansion, driven by AI, automotive electronics, and IoT, is amplifying the need for advanced etching techniques. Wet etching consultants are increasingly engaged to advise on selective etchants, contamination control, and transition to high-volume manufacturing. Applied Materials and Lam Research continue to report strong activity in process development and integration projects.
- Focus on Environmental and Safety Compliance: Stricter global regulations, especially in Europe and East Asia, are prompting fabs to seek expert guidance in waste treatment, chemical recycling, and safe handling protocols. Consultants with experience in compliance with REACH, RoHS, and local water discharge standards are witnessing heightened demand. Equipment suppliers such as Rena Technologies and Entegris are collaborating with consultants to develop eco-friendly wet bench solutions.
- Integration of Digitalization and Automation: The adoption of smart manufacturing and Industry 4.0 technologies is accelerating. Consultants are essential in helping fabs implement automated chemical delivery, real-time monitoring, and process analytics to increase yield and reduce variability. Companies like Siltronic are investing in advanced automation, working closely with external experts.
- Expansion into Emerging Materials: As demand grows for compound semiconductors (SiC, GaN), photonic devices, and flexible electronics, consultants are called upon to develop bespoke etching recipes and assess compatibility with new substrates. This trend is supported by ongoing R&D at firms such as Siltronic and Micron Technology.
Looking ahead to 2025 and beyond, wet chemical etching consultants are expected to play an increasingly strategic role as fabs face mounting technical, regulatory, and economic pressures. Their expertise will be central to enabling innovation, ensuring compliance, and delivering competitive advantage in a fast-evolving global marketplace.
Market Sizing & Forecasts Through 2030
The market for wet chemical etching consultants is closely tied to the overall demand for wet chemical etching services and equipment—essential processes in semiconductor fabrication, MEMS manufacturing, photovoltaics, and advanced packaging. As of 2025, the industry is experiencing robust growth driven by the rapid expansion of the global semiconductor sector, continued innovation in device miniaturization, and the proliferation of advanced materials that require sophisticated etching expertise.
Recent capacity expansions and investments by leading semiconductor manufacturers are fueling demand for specialized consulting services to optimize etching processes, boost yields, and ensure compliance with increasingly stringent environmental and safety regulations. For example, Intel Corporation and Taiwan Semiconductor Manufacturing Company (TSMC) have both announced multi-billion dollar investments in new fabs in the U.S., Europe, and Asia, with commissioning and ramp-up phases extending through 2025 and beyond. These projects invariably require third-party consultants to assist with process selection, chemical management, and equipment integration.
The market size for wet chemical etching consulting, though a specialized subset of the broader process engineering services sector, is projected to grow at a high single-digit CAGR through 2030. This is due to a combination of increasing process complexity (such as the adoption of 3D NAND, FinFET, and heterogeneous integration technologies) and the push toward greener, more sustainable etching chemistries in compliance with evolving global regulations. Major chemical suppliers such as BASF and DuPont are actively working with consultants and end-users to develop and deploy next-generation etchants, further stimulating advisory demand.
- In 2025, the U.S., South Korea, Taiwan, Japan, and China remain the largest markets for wet chemical etching consulting, mirroring the geography of advanced semiconductor manufacturing.
- Consultants with deep expertise in process optimization, chemical lifecycle management, and tool integration are in particularly high demand, especially as fabs transition to smaller nodes and new materials.
- Environmental, health, and safety (EHS) compliance is a growing driver, with new regulations in the European Union and U.S. requiring continuous adaptation of etching chemistries and waste treatment processes (Semiconductor Industry Association).
Looking ahead to 2030, the outlook for wet chemical etching consultants remains positive, with market expansion underpinned by ongoing semiconductor industry growth, rising process complexity, and the necessity for sustainable manufacturing solutions. Consultants who can bridge the gap between chemistry, process engineering, and regulatory compliance will be especially well-positioned for growth.
Competitive Landscape: Top Wet Chemical Etching Consulting Firms
The competitive landscape for wet chemical etching consulting is evolving rapidly in 2025, shaped by increasing demand from the semiconductor, MEMS, photovoltaic, and advanced packaging sectors. A handful of highly specialized consulting firms, along with divisions of major equipment manufacturers, dominate this niche, offering expertise in process optimization, equipment integration, and regulatory compliance.
Among the industry leaders, Lam Research Corporation stands out not only as a supplier of etching equipment but also as a provider of technical consulting and process engineering services. Their experts collaborate with fabs worldwide to optimize wet chemical etching steps, particularly in the context of scaling to sub-5nm nodes and heterogeneous integration. Similarly, Entegris, Inc. leverages its deep material science knowledge to advise clients on wet chemistry selection, impurity control, and yield improvement—critical as device geometries shrink and contamination risks grow.
For photomask and specialty glass etching, Corning Incorporated offers tailored consulting, drawing from its proprietary glass chemistries and decades of process development for display and optical applications. Their consultants work closely with customers to adapt etching chemistries for emerging substrates and application-specific requirements.
The rise of compound semiconductors, such as SiC and GaN, has also brought specialized consultants to the fore. Soitec, known for its engineered substrates, extends consulting services to optimize wet etch steps in the preparation of SOI and Power-SOI wafers, crucial for next-generation power and RF devices.
In the photovoltaic sector, Technolas (a division of the Meyer Burger Group) provides expertise in wet chemical texturing and cleaning, catering to the rapid adoption of high-efficiency cell architectures that demand precise surface engineering.
Additionally, several equipment suppliers, including SUSS MicroTec, have expanded their consulting arms to address customer needs for process transfer, customization, and troubleshooting in both R&D and high-volume manufacturing environments.
Looking ahead, the competitive landscape is expected to intensify as new entrants—often spin-offs from research institutes or former fab process engineers—bring niche expertise in advanced materials and green chemistries. As regulations tighten around chemical usage and environmental impact, the role of wet chemical etching consultants in compliance and sustainability will become even more pronounced, driving further market segmentation and specialization.
Emerging Applications: Semiconductors, MEMS, and Beyond
Wet chemical etching consultants are increasingly pivotal in shaping the trajectory of emerging applications in semiconductors, microelectromechanical systems (MEMS), and adjacent high-tech sectors. As device architectures become more complex and miniaturized, the precision and selectivity offered by wet etching processes have made them integral to advanced fabrication workflows. In 2025 and the near future, several trends and innovations are redefining the role of these consultants.
In the semiconductor industry, the transition to sub-5 nm nodes and the evolution of 3D device structures—such as gate-all-around (GAA) transistors—are amplifying the demand for highly controlled etching processes. Wet chemical etching experts are actively collaborating with leading chip manufacturers to optimize chemistries and process parameters that minimize defects and enhance yields. For example, Intel Corporation has emphasized the critical role of advanced etching techniques in its roadmap for next-generation logic and memory devices, highlighting ongoing partnerships with process specialists to address new challenges in selectivity and uniformity.
In MEMS manufacturing, the rise of sensors for automotive, healthcare, and consumer electronics is driving requirements for etch processes capable of producing intricate microstructures with high aspect ratios. Consultants in this domain are working closely with companies such as STMicroelectronics, a global leader in MEMS production, to develop tailored wet etching solutions that improve feature definition while reducing stiction and contamination risks.
Beyond semiconductors and MEMS, wet chemical etching is seeing new applications in fields such as photonics, flexible electronics, and advanced packaging. For instance, AMD and its packaging partners are leveraging wet etching to create high-density interconnects for chiplets and heterogeneous integration, necessitating consultation on novel chemistries and process flows.
Looking ahead, the outlook for wet chemical etching consultants remains robust. The push for greener manufacturing is driving the adoption of environmentally friendly etchants and waste minimization strategies, with suppliers like BASF investing in sustainable chemical solutions. As materials and device geometries continue to evolve, consultants will play a central role in bridging the gap between novel application requirements and scalable, reliable etching processes, ensuring that manufacturers can meet the technical and regulatory demands of next-generation products.
Technological Breakthroughs Shaping Wet Chemical Etching
Wet chemical etching continues to evolve as a critical process in microfabrication, influencing industries from semiconductors to MEMS and photovoltaics. In 2025 and beyond, the role of specialized consultants is becoming increasingly vital, as new technological breakthroughs reshape process requirements, material compatibility, and environmental standards. Consultants are being sought not only for process optimization but also for navigating the transition to more sustainable chemistries and advanced automation.
A key trend driving consultant demand is the shift toward advanced node semiconductor manufacturing, which requires ultra-precise etching with reduced feature sizes and tighter control over etch profiles. Wet etching specialists are advising fabs on the integration of next-generation chemistries such as dilute HF and alternative acid blends that enable selective removal without damaging adjacent layers. For example, BASF and Solvay have introduced novel wet chemical formulations tailored for advanced semiconductor nodes, and consultants are helping manufacturers qualify and implement these solutions.
Environmental regulations—particularly in Europe and Asia—are pushing the adoption of low-toxicity and recyclable etchants. Consultants are increasingly called upon to guide fabs and solar cell producers through the switch to environmentally compliant chemistries, such as those developed by DuPont for cleaning and etching applications, and to advise on in-line recycling systems that minimize hazardous waste. The expertise of consultants is instrumental in pilot testing and scaling up these greener processes.
Another area of breakthrough is the automation and digitalization of wet etching lines. Consultants with expertise in process control, data analytics, and smart manufacturing are in high demand, as companies look to optimize throughput and yield while maintaining stringent quality standards. Equipment providers like Lam Research and SINGULUS TECHNOLOGIES have introduced wet processing systems with advanced automation, and consultants assist with integration and workforce training.
Looking ahead, the outlook for wet chemical etching consultants is strong. As the industry faces new challenges—shrinking device geometries, sustainability mandates, and the need for rapid technology transfer—their expertise in materials science, process engineering, and regulatory compliance will be increasingly essential for innovation and competitiveness.
Sustainability & Environmental Regulations Impact
The sustainability landscape for wet chemical etching is shifting rapidly as regulatory pressures and environmental considerations intensify worldwide. In 2025, wet chemical etching consultants are increasingly pivotal in helping manufacturers navigate complex compliance requirements, particularly regarding hazardous waste management, reduction of chemical usage, and water treatment. The global move toward greener semiconductor and electronics manufacturing is accelerating, with governments and industry bodies tightening permissible discharge levels for effluents and mandating improved recycling of process chemicals.
For instance, the U.S. Environmental Protection Agency’s recent updates to the National Pollutant Discharge Elimination System (NPDES) have prompted semiconductor fabs and printed circuit board (PCB) manufacturers to reevaluate their etching processes. Consultants are advising on both technological upgrades and process optimizations to comply with these stricter standards, including the adoption of closed-loop systems and advanced filtration technologies (United States Environmental Protection Agency).
Major equipment suppliers such as Lam Research and Entegris are responding by integrating sustainability features—such as reduced acid consumption and wastewater minimization—into their wet processing platforms. Wet chemical etching consultants work closely with these manufacturers to implement best practices and recommend equipment upgrades that align with both regulatory requirements and clients’ corporate sustainability goals.
In Europe, the Registration, Evaluation, Authorisation and Restriction of Chemicals (REACH) regulations, enforced by the European Chemicals Agency, are driving a transition away from certain hazardous etchants. Consultants are facilitating the adoption of alternative chemistries, such as less toxic etchants and recyclable solutions, helping clients maintain production efficiency while reducing environmental risks.
Further, industry initiatives like the SEMI S2 Environmental, Health, and Safety Guideline are being widely adopted, with consultants providing expertise on achieving and documenting compliance. This includes life cycle assessments, emissions tracking, and guidance on environmental reporting.
Looking ahead, the demand for wet chemical etching consultants is expected to increase, with emphasis on digital monitoring, predictive maintenance, and circular economy strategies. As the industry faces mounting pressure to minimize water and chemical footprints, consultants’ roles will expand to include not only regulatory navigation but also innovation scouting and sustainability benchmarking—ensuring clients remain competitive in an increasingly regulated and eco-conscious market.
Global Demand Drivers and Regional Hotspots
The global demand for wet chemical etching consultants in 2025 is closely tied to the growth trajectories of advanced manufacturing sectors, notably semiconductors, photovoltaics, MEMS, and display technologies. As device architectures become increasingly complex and miniaturized, manufacturers are seeking specialized expertise for process optimization, environmental compliance, and yield improvement—key areas addressed by wet chemical etching consultants.
The Asia-Pacific region, led by Taiwan, South Korea, China, and Japan, continues to represent the largest concentration of etching activity and technical consultancy demand. Taiwan’s TSMC and South Korea’s Samsung Electronics are ramping up investment in advanced logic and memory fabs, driving the need for consultants who can implement next-generation etch chemistries and waste management solutions. China’s push for semiconductor self-sufficiency, through companies such as SMIC, has also spurred local demand for process experts who can help close technology gaps in wet etch steps, especially for sub-10nm nodes.
North America, with heavyweights like Intel expanding stateside manufacturing, is seeing a renewed focus on process consulting as part of the CHIPS Act-fueled investment wave. Wet chemical etching consultants are playing a vital role in technology transfer, environmental compliance (particularly with stricter wastewater standards), and integration of sustainable chemistries. Similarly, Europe is experiencing a consultancy uptick, with Infineon Technologies and STMicroelectronics developing new lines for power and automotive semiconductors, which often involve complex etching in silicon carbide and gallium nitride substrates.
Emerging hotspots include Southeast Asia—where countries like Vietnam and Singapore are attracting new fabs—and India, which is making early moves to localize semiconductor manufacturing. Regional governments and industry consortia are seeking consultants to establish best practices in wet chemical handling, safety, and effluent treatment as new facilities break ground.
Looking ahead, the outlook for wet chemical etching consultants remains robust. The drive for greener processes, such as reduced chemical usage and improved recycling, is likely to intensify consultancy requirements, while the global race for advanced node manufacturing ensures sustained technical demand. Regional supply chain realignments and government incentives will continue to shape where and how wet chemical etching expertise is most in demand through the remainder of the decade.
Key Partnerships: OEMs, Foundries, and Research Institutes
In 2025, wet chemical etching consultants are increasingly pivotal in forging key partnerships across the semiconductor landscape, particularly among original equipment manufacturers (OEMs), foundries, and research institutes. The complexity of device architectures—in advanced nodes, MEMS, and compound semiconductors—drives demand for expert guidance on process integration, materials compatibility, and defect control.
A notable trend is the intensified collaboration between consultants and OEMs such as Lam Research and Applied Materials. These companies are innovating wet etch tools for both front-end and back-end processes, and consultants are often brought in to help define requirements for new chemistries, contamination control, and tool customization. For instance, Lam Research has highlighted the importance of process experts in enabling selective wet etch solutions for emerging 3D device structures, where collaboration with external consultants helps accelerate tool qualification and customer adoption.
At the foundry level, leaders like TSMC and GlobalFoundries regularly engage external wet etching consultants to support technology transfer, yield ramp, and defect reduction as they push into sub-5nm process nodes and heterogeneous integration. These partnerships are particularly important in the adoption of advanced wet etch chemistries—such as those required for high aspect ratio features or selective removal in logic and memory devices. Consultants work alongside internal engineering teams to troubleshoot process excursions and validate new cleaning and etching protocols.
Research institutes play a complementary role, with organizations like imec and CSEM collaborating with consultants to bridge fundamental research and industrial implementation. In 2025, joint programs focus on sustainable wet etching—developing low-GWP chemistries and closed-loop systems that meet both performance and environmental goals. Consultants contribute expertise in scaling up lab results to pilot lines and qualifying new processes for industrial partners.
Looking ahead, the outlook for these key partnerships is robust. With the semiconductor industry’s ongoing transition to gate-all-around (GAA) transistors, 2.5D/3D integration, and advanced packaging, the need for cross-disciplinary expertise will only intensify. Wet chemical etching consultants are set to remain crucial partners—enabling knowledge transfer, process optimization, and rapid adoption of next-generation etch solutions across OEMs, foundries, and research institutes.
Strategic Recommendations for Clients and Investors
The wet chemical etching (WCE) sector faces rapidly evolving technological, regulatory, and market dynamics as we move into 2025 and beyond. Clients and investors seeking to leverage the expertise of wet chemical etching consultants should consider several strategic recommendations to optimize outcomes and mitigate risks in this critical semiconductor and microfabrication process area.
- Prioritize Sustainability and Regulatory Compliance: As environmental regulations tighten globally, particularly regarding chemical management and effluent treatment, engaging consultants with deep knowledge of sustainable etching chemistries and up-to-date compliance strategies is crucial. Companies such as BASF and DuPont have highlighted the shift toward environmentally responsible etchants and waste minimization technologies. Consultants should be able to provide actionable roadmaps for transitioning to greener chemistries and implementing closed-loop systems.
- Accelerate Adoption of Advanced Materials: The growing use of compound semiconductors, advanced packaging, and heterogeneous integration demands process expertise beyond traditional silicon etching. Investors and clients should seek consultants with experience in the etching of III-V materials, silicon carbide, and high-k dielectrics. Providers like Entegris have developed specialty chemistries for these materials, and consultants familiar with such advancements can facilitate rapid technology transfer and yield improvements.
- Optimize Yield and Process Control: As device geometries shrink below 5 nm, process uniformity and defect control become mission-critical. Consultants should offer data-driven methodologies for process optimization, leveraging real-time metrology and statistical process control. Collaboration with equipment manufacturers such as Lam Research and ULVAC, who supply advanced wet processing tools, can help identify the best practices for yield maximization and process repeatability.
- Assess Supply Chain Resilience: The volatility of specialty chemicals supply and geopolitical uncertainties can impact production continuity. Consultants with strong industry networks and up-to-date knowledge of suppliers—such as Solvay or AZ Electronic Materials—are valuable for advising on dual sourcing, inventory management, and risk mitigation strategies.
- Invest in Digitalization and Automation: With the increasing complexity of etching processes, digital tools for recipe management, predictive maintenance, and process automation are becoming standard. Consultants versed in the integration of Industry 4.0 technologies and data analytics into wet etching lines can deliver significant productivity and quality gains, as demonstrated by digitalization initiatives from companies like Merck KGaA (operating as EMD Electronics in the U.S.).
In summary, engaging wet chemical etching consultants with cutting-edge technical expertise, regulatory awareness, and a forward-looking approach will be essential for clients and investors aiming to remain competitive and compliant as the industry advances through 2025 and into the future.
Future Trends: Where Are Wet Chemical Etching Consultants Headed by 2030?
As the semiconductor and microfabrication industries continue to evolve, the role of wet chemical etching consultants is undergoing significant transformation. Entering 2025, several trends are shaping the demand, expertise, and service models of these specialized consultants, driven by advances in materials science, sustainability concerns, and the relentless push for device miniaturization.
A major trend is the increasing complexity of materials and device architectures, particularly with the rise of advanced packaging, 3D integration, and compound semiconductors. Wet chemical etching consultants are now required to possess deep knowledge of etching chemistries for a broader array of substrates—such as gallium nitride (GaN) and silicon carbide (SiC)—as these materials become standard in power electronics and RF applications. Companies like Wolfspeed and ams OSRAM are at the forefront of integrating these materials, necessitating new etching strategies and process controls.
Environmental and safety regulations are also intensifying. The European Union and other jurisdictions are tightening restrictions on hazardous chemicals like perfluorinated compounds and acids commonly used in etching processes. Consultants must now guide clients toward greener alternatives and closed-loop systems that minimize waste and exposure. For example, BASF has introduced advanced chemical recycling and recovery solutions tailored for semiconductor manufacturing, a trend likely to accelerate as sustainability becomes a core industry driver.
Digitalization is another disruptive force. Process simulation, real-time data analytics, and AI-driven optimization are becoming standard in etching development and troubleshooting. Consultants are increasingly expected to leverage platforms like Lam Research’s cloud-based process control solutions and to interpret large datasets to enhance yield and process stability.
Global supply chain shifts—exacerbated by geopolitical tensions and the push for regional semiconductor autonomy—are changing the consultant’s role from pure technical advisor to strategic partner. They now assist in qualifying alternate suppliers of chemicals and equipment, as well as advising on localized process adaptation. For example, DuPont has expanded its regional presence in East Asia, emphasizing technology transfer and local support in wet etching materials and processes.
Looking to 2030, wet chemical etching consultants are expected to be more multidisciplinary, blending expertise in chemistry, environmental engineering, data science, and supply chain management. Their role will be increasingly pivotal as manufacturers seek to balance innovation, compliance, and cost in a rapidly changing industry landscape.