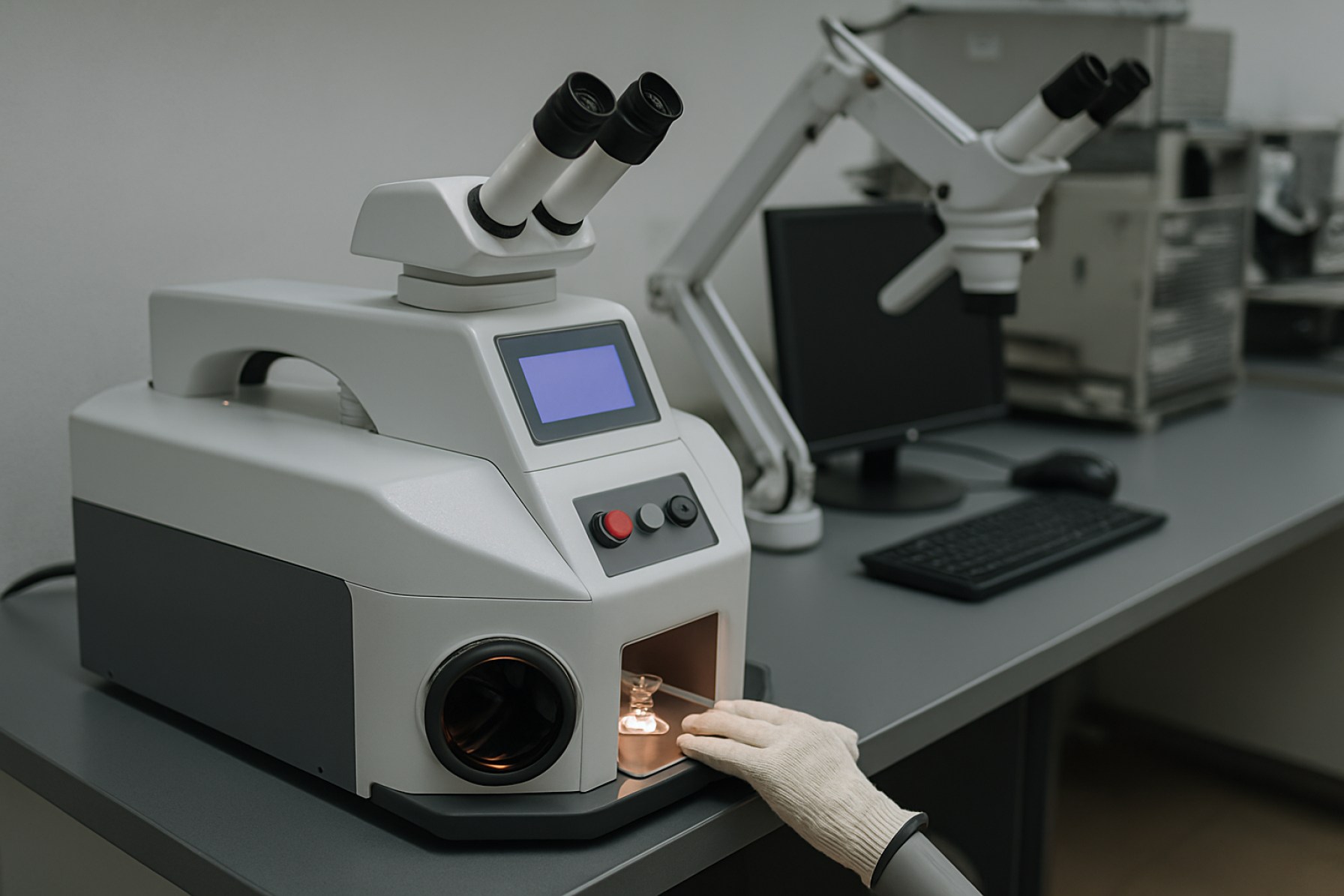
Table of Contents
- Executive Summary: Key 2025 Takeaways & Growth Highlights
- Market Size and Forecast: 2025 & 3-5 Year Projections
- Emerging Technologies in Micro-Welding for Jewelry Manufacturing
- Competitive Landscape: Leading Manufacturers & New Entrants
- Innovation Spotlight: Laser vs. Pulse Arc Welding Advances
- Raw Materials, Supply Chain, and Sourcing Dynamics
- End-User Segmentation: Jewelry Types & Customization Trends
- Regulatory Standards and Industry Compliance (e.g. jewelers.org)
- Regional Analysis: Major Hubs and Growth Hotspots
- Future Outlook: Opportunities, Risks, and Strategic Recommendations
- Sources & References
Executive Summary: Key 2025 Takeaways & Growth Highlights
The jewelry micro-welding equipment manufacturing sector in 2025 is marked by robust innovation, heightened automation, and increasing global demand for precision assembly solutions. As consumer preferences shift towards intricately designed and personalized jewelry, manufacturers are responding by investing in advanced micro-welding technologies—particularly laser and pulse-arc systems—that enable fine, non-invasive joining of precious metals and alloys.
A leading trend in 2025 is the rapid adoption of compact, digitally controlled micro-welding units tailored for jewelry workshops and small-scale manufacturers. Companies such as Rio Grande and Bentley Materials are expanding their portfolios with new-generation laser welders that offer higher energy efficiency, intuitive user interfaces, and network connectivity for process monitoring. The integration of these features aligns with the broader movement towards Industry 4.0 in the jewelry manufacturing ecosystem.
Notably, the push for sustainability and waste minimization is influencing equipment development. Many manufacturers—like Orion Welders—are focusing on micro-welding machines that deliver precision with minimal material loss, supporting eco-friendly jewelry production. This is particularly relevant in the context of rising raw material costs and regulatory pressures regarding metal sourcing and processing.
On the supply side, North America and Europe remain the primary hubs for high-end micro-welding equipment innovation, with a growing number of firms in Asia-Pacific—such as Sisma—entering the premium segment. These manufacturers are emphasizing R&D to support a broader range of metals and alloys, including platinum, titanium, and increasingly popular recycled materials.
Looking ahead to the next few years, the sector is poised for continued growth. The proliferation of digitally enabled, user-friendly micro-welders is lowering barriers for bespoke and small-batch jewelry producers worldwide. At the same time, ongoing collaboration between equipment makers and jewelry designers is expected to yield further advancements—such as integrated vision systems for automated weld inspection and AI-driven parameter optimization.
In summary, 2025 stands as a pivotal year for jewelry micro-welding equipment manufacturing, with innovation, sustainability, and digitalization shaping market expansion and technological breakthroughs. Firms that prioritize R&D, adaptability, and customer-centric design are likely to secure competitive advantages as the industry evolves.
Market Size and Forecast: 2025 & 3-5 Year Projections
The global jewelry micro-welding equipment manufacturing sector is poised for steady growth through 2025 and over the subsequent three to five years. As the jewelry industry increasingly adopts precision welding techniques for delicate assembly, repair, and customization, demand for advanced micro-welding solutions—including laser and pulse-arc welders—remains robust.
Leading equipment manufacturers, such as Sunstone Engineering (under the Orion Welders brand), Sisma S.p.A., and Italtecnica, are reporting sustained order volumes from jewelry workshops and mass production facilities globally. For example, Sisma S.p.A. continues to expand its portfolio of laser welding systems, noting greater adoption among both established luxury brands and independent jewelers seeking to streamline repair and prototyping processes.
Although comprehensive, independently audited market size data specific to jewelry micro-welding equipment is relatively limited, equipment manufacturers have indicated year-on-year growth in sales between 7% and 10% through 2023 and 2024, driven by increased jewelry production in Asia and North America. For 2025, the sector’s value is projected to reach several hundred million USD globally, factoring in both new equipment sales and aftersales services such as maintenance and training, as corroborated by product expansion announcements and annual reports from manufacturers like Sunstone Engineering and Sisma S.p.A..
Looking ahead, technological innovation remains a primary growth driver. Manufacturers are investing in more compact, user-friendly, and digitally integrated micro-welding systems to cater to the needs of small jewelry studios and scalable production lines alike. For instance, Italtecnica has introduced portable micro-welding units aimed at improving flexibility and cost-effectiveness for jewelers. Additionally, the integration of automation, IoT features, and enhanced safety controls is expected to further accelerate market adoption over the next three to five years.
The outlook through 2028 remains positive, underpinned by ongoing global jewelry market expansion, rising consumer demand for custom and repair services, and the industry’s gradual shift toward more sustainable, precision-driven production methods. As a result, key manufacturers anticipate continued annual growth rates in the high single digits, with regional demand particularly strong in Asia, North America, and select European markets, as reflected in product launches and strategic partnerships disclosed by Sisma S.p.A. and Sunstone Engineering in recent years.
Emerging Technologies in Micro-Welding for Jewelry Manufacturing
The jewelry micro-welding equipment manufacturing sector is undergoing rapid evolution in 2025, driven by technological innovation and the growing demand for precision in jewelry design and repair. Recent advances in micro-welding technologies—particularly laser and pulse-arc systems—are reshaping the capabilities of manufacturers and artisans, allowing for intricate assembly and repair processes that preserve the integrity of precious metals and gemstones.
Major equipment manufacturers are investing in R&D to improve adaptability and efficiency. For instance, Sunstone Engineering has released the Orion mPulse 30, a compact pulse-arc welder tailored for jewelry applications, featuring programmable power settings and user-friendly interfaces that cater to both small workshops and large-scale production. Similarly, Sisma S.p.A. continues to refine its laser welding stations, emphasizing enhanced energy efficiency and safety features, such as integrated fume extraction and touch-screen controls.
Automation is a key trend, with several manufacturers integrating smart control systems and IoT connectivity into their latest models. Legor Group has reported successful pilot implementations of AI-assisted micro-welding systems that optimize weld parameters in real time for consistent results and reduced material waste. Such developments are anticipated to become industry standards within the next few years, as jewelry houses look to balance craftsmanship with scalable, repeatable quality.
Sustainability is also influencing equipment design. Companies are developing micro-welding systems that minimize energy consumption and allow for the use of recycled precious metals without compromising weld integrity. Rio Grande, a prominent jewelry supplier, is collaborating with manufacturers to promote equipment that supports closed-loop material workflows, addressing both environmental and economic concerns.
Looking ahead, the outlook for jewelry micro-welding equipment manufacturing is robust. The global market is expected to experience steady growth through 2025 and beyond, fueled by rising demand from emerging markets in Asia and the Middle East. Continued collaboration between equipment manufacturers, jewelry brands, and educational institutions is expected to accelerate the adoption of advanced welding technologies, ensuring that the sector remains agile and responsive to evolving design trends and consumer expectations.
- Enhanced precision and automation are set to define the next generation of micro-welding equipment.
- Integration of digital controls and AI will drive productivity and consistency in jewelry production.
- Sustainable practices, including support for recycled materials, will become increasingly central to equipment design and marketing.
Competitive Landscape: Leading Manufacturers & New Entrants
The competitive landscape of jewelry micro-welding equipment manufacturing in 2025 is defined by a blend of established global leaders and dynamic new entrants. As the jewelry industry continues to prioritize precision, efficiency, and miniaturization, the demand for advanced micro-welding solutions has intensified. Leading manufacturers are responding with innovations in laser and pulse-arc technology, automation, and digital integration.
Among the established players, Sunstone Engineering (Orion Welders) remains at the forefront, offering a comprehensive suite of micro-welding machines tailored for jewelry applications. Its Orion series, well-regarded for reliability and precision, integrates touch-screen controls and advanced weld monitoring features, reflecting ongoing investment in R&D. Similarly, Lampert Werktechnik distinguishes itself with the PUK line, emphasizing compact form factors and intuitive interfaces—key advantages for both small workshops and large-scale manufacturers.
In Europe, Sisma S.p.A. continues to innovate with its LM-D laser welding systems, which have been widely adopted for their efficiency and low-maintenance operation. Sisma’s ongoing expansion of its global sales and support network in 2025 underscores the increasing internationalization of the sector. Meanwhile, Legor Group S.p.A. has diversified its equipment range and leverages synergies with its precious metal alloys business, offering integrated solutions to jewelry manufacturers.
New entrants, especially from Asia, are reshaping the market dynamics. Companies such as Han’s Laser Technology Industry Group Co., Ltd. have started to offer cost-competitive desktop laser welders, targeting price-sensitive markets without compromising on basic precision. These newcomers leverage regional manufacturing efficiencies and are expected to further expand their presence in the coming years, particularly in emerging jewelry hubs across Southeast Asia and India.
Technological collaboration is also evident, with some manufacturers forming partnerships to integrate robotics and IoT capabilities. For instance, select models from Sisma S.p.A. now feature automation-ready interfaces, enabling integration with smart factory systems. This trend is anticipated to accelerate by 2026 as jewelry manufacturers seek to streamline production and enhance traceability.
Looking ahead, the competitive landscape is likely to remain vibrant. Leading Western manufacturers will continue to differentiate through innovation and after-sales support, while Asian entrants drive price competition and broaden access. Strategic alliances, product customization, and digital integration will be key factors shaping the sector’s evolution through the latter half of the 2020s.
Innovation Spotlight: Laser vs. Pulse Arc Welding Advances
Jewelry micro-welding has experienced significant innovation in recent years, with two primary technologies—laser welding and pulse arc welding—driving advancements in equipment manufacturing. In 2025, the sector is characterized by rapid refinement of both methods, as manufacturers cater to the evolving demands of jewelry designers and repair specialists for precision, speed, and versatility.
Laser welding equipment continues to set the benchmark for micro-precision, enabling seamless joins with minimal heat-affected zones. Leading manufacturers such as Legor Group and Rofin-Sinar Technologies have unveiled next-generation benchtop laser welders with enhanced pulse control, touchscreen interfaces, and improved energy efficiency. These systems are increasingly equipped with automated parameter optimization, making them accessible to less experienced users while maintaining the accuracy required for high-value metals and intricate designs.
Pulse arc welding, while generally more cost-effective, has also seen notable improvements. Companies like Sunstone Engineering have introduced compact welders with advanced waveform customization and integrated cooling systems, reducing electrode wear and expanding the range of applicable alloys. Their 2024–2025 product lines emphasize user-friendly operation and modularity, allowing jewelers to switch between welding and engraving functionalities with ease.
A major event shaping the landscape in 2025 is the increased adoption of hybrid systems that blend laser and pulse arc technologies. Sisma S.p.A. has pioneered machines capable of both laser welding and pulse arc processes, offering unparalleled flexibility for small workshops and large manufacturers alike. This versatility addresses the growing trend of mixed-material jewelry, where welders must adapt to diverse metals and complex geometries.
From a data perspective, adoption rates for micro-welding equipment in jewelry manufacturing are rising steadily, driven by demand for custom, small-batch production and efficient repair services. Industry players report that laser welding technology is especially favored in regions with a strong tradition of high-end jewelry craftsmanship, such as Italy and Switzerland, while pulse arc systems are making inroads among emerging markets and independent artisans (Legor Group).
Looking ahead, the outlook for jewelry micro-welding equipment manufacturing remains robust. Continued R&D investment in laser source miniaturization, AI-assisted welding settings, and cross-platform connectivity is expected to further democratize access to advanced welding tools, supporting both the artisanal and industrial segments of the jewelry industry.
Raw Materials, Supply Chain, and Sourcing Dynamics
The manufacturing of jewelry micro-welding equipment in 2025 is deeply intertwined with the broader dynamics of raw material sourcing, supply chain resilience, and technological advancements. Key components of these systems—such as precision lasers, power supplies, optical systems, and control electronics—rely on the steady supply of specialty metals (e.g., tungsten, copper), high-purity optical glass, and advanced electronic components. The ongoing global semiconductor fluctuations and critical material shortages continue to shape sourcing strategies for leading manufacturers.
In response to potential disruptions, major equipment producers like OroAura and Legor Group are diversifying their supply bases and investing in closer supplier relationships, favoring regional sourcing to mitigate logistical risks. For example, Legor Group has emphasized transparent procurement processes for metals and components in its sustainability reports, aiming to ensure both ethical sourcing and production continuity.
The micro-welding equipment segment is also influenced by the rapid evolution of laser sources, particularly the shift toward fiber and diode laser technologies. These advances require access to rare-earth elements and precision optics, which can be subject to geopolitical pressures and export restrictions. Companies like Sisma and Riacetech have invested in in-house R&D and strategic partnerships with European and Asian suppliers to secure these critical inputs.
Sourcing strategies are further shaped by the growing importance of sustainability and traceability in the jewelry sector. Manufacturers are increasingly adopting recycled metals and components when possible, aligning with customer expectations and regulatory requirements. For instance, OroAura highlights the use of responsibly sourced and recycled metals in their system builds, reflecting a broader industry move toward green procurement.
Looking ahead, the outlook for raw materials and supply chains in jewelry micro-welding equipment manufacturing is cautiously optimistic. While ongoing geopolitical uncertainties and potential shortages of high-tech materials remain concerns, companies are responding with digital supply chain management tools, increased inventory buffers, and expanded supplier networks. These efforts are expected to stabilize lead times and ensure the steady availability of advanced micro-welding systems for the jewelry sector through 2025 and into the next several years.
End-User Segmentation: Jewelry Types & Customization Trends
In 2025, the end-user segmentation for jewelry micro-welding equipment manufacturing is increasingly shaped by evolving trends in jewelry types and customization demands. The industry is witnessing a marked shift towards personalized, intricate, and mixed-material jewelry, which directly influences the requirements and preferences of equipment purchasers, including independent artisans, boutique workshops, and large-scale manufacturers.
Fine jewelry—comprising gold, platinum, and gemstone pieces—remains a dominant segment. However, consumer appetite for bespoke and limited-edition designs is fueling demand for micro-welding equipment that can deliver precision and flexibility for small-scale, high-value production runs. For instance, Legor Group highlights the importance of their micro-welding solutions in enabling jewelers to create customized pieces with minimal heat impact, allowing for the safe joining of delicate components and settings. This adaptability is particularly valuable for engagement rings, pendants, and earrings, where intricate repairs and alterations are common.
Fashion and costume jewelry manufacturers are also expanding their micro-welding usage, as the technology enables efficient joining of diverse materials such as stainless steel, titanium, and alloys, alongside traditional precious metals. The ability to weld dissimilar metals and accommodate non-traditional designs directly supports the trend towards mixed-material jewelry, a segment expected to grow in the coming years. Pulsion Laser notes that their equipment is increasingly adopted by brands seeking to innovate in both style and material selection, responding to consumer calls for unique, high-quality fashion jewelry.
Customization remains at the forefront of end-user expectations. Jewelers now routinely offer on-demand personalization—engraving, resizing, and modular assembly—requiring micro-welding tools that are user-friendly and suitable for in-store or on-site applications. Compact, desktop-sized laser welders, such as those offered by Orotig, have become popular among small workshops and retail jewelers, enabling rapid repairs and custom modifications without outsourcing.
Looking ahead, continued growth in the high-end and bespoke jewelry markets is expected to drive further segmentation and specialization in micro-welding equipment. Manufacturers are likely to focus on developing systems with enhanced automation, digital controls, and compatibility with a broader array of materials, catering to the evolving creative and operational needs of jewelry makers worldwide.
Regulatory Standards and Industry Compliance (e.g. jewelers.org)
The jewelry micro-welding equipment manufacturing sector in 2025 faces a dynamic landscape shaped by evolving regulatory standards and increasing demands for industry compliance. As precision welding becomes ever more critical in modern jewelry design—enabling cleaner joins, repairs, and intricate assembly—manufacturers must align with both safety and quality benchmarks established by recognized industry authorities.
Regulatory frameworks governing micro-welding equipment are multifaceted, involving electrical safety, laser emissions, and the use of hazardous materials. In the United States, equipment must comply with standards set by agencies such as the Occupational Safety and Health Administration (OSHA) and the U.S. Food and Drug Administration (FDA), particularly regarding laser device classification and operator safety features. Globally, the International Electrotechnical Commission (IEC) and the European Committee for Electrotechnical Standardization (CENELEC) provide harmonized standards for electrical and photonic equipment used in jewelry manufacturing. Manufacturers like Sunstone Engineering and LaserStar Technologies Corporation publicly emphasize their adherence to these regulatory requirements, ensuring that their micro-welding systems are CE-marked and conform to RoHS and WEEE directives for environmental and consumer safety.
The jewelry industry’s own governing bodies, such as the Jewelers of America and the World Jewellery Confederation (CIBJO), reinforce compliance through best practices and educational outreach. As of 2025, these organizations continue to update their guidelines to include not only traditional metalworking standards, but also best practices for safe operation and maintenance of advanced welding equipment. This involves recommending regular operator training, certification, and audit trails for equipment maintenance, contributing to both product quality and workplace safety.
Looking forward, regulatory trends indicate a tightening of standards related to both environmental impact and user safety. With increasing global scrutiny on the use of hazardous materials and energy consumption, micro-welding equipment manufacturers are expected to innovate further—favoring low-emission lasers and recyclable components. Additionally, digital monitoring features and remote compliance verification are likely to become more prevalent, as regulatory bodies push for traceability and real-time safety assurance.
Overall, the jewelry micro-welding equipment sector in 2025 is marked by an ongoing shift toward greater standardization, transparency, and technological adaptation in response to regulatory and industry pressures. Manufacturers that proactively address these trends—by certifying their equipment, investing in user education, and embracing sustainable practices—are poised to maintain competitiveness and trust within the evolving jewelry market.
Regional Analysis: Major Hubs and Growth Hotspots
Jewelry micro-welding equipment manufacturing is witnessing notable regional dynamics as technological innovation, skilled labor availability, and proximity to jewelry production centers drive growth and investment. In 2025 and the coming years, several geographic hubs are consolidating their positions or emerging as hotspots.
Europe remains a pivotal region, with Italy and Germany at the forefront. Italy, especially the Vicenza and Arezzo districts, continues to host leading micro-welding equipment manufacturers, leveraging the nation’s rich jewelry tradition and advanced engineering capabilities. Companies such as Orotig S.r.l. and SISMA S.p.A. are headquartered here, offering a wide range of laser and micro-welding solutions tailored for high-precision goldsmithing. Germany, similarly, sustains its reputation for industrial precision, with firms like ROFIN (now part of Coherent) providing specialized laser welding systems for jewelry applications.
Asia-Pacific is growing rapidly, driven by expanding jewelry markets and manufacturing bases in China, India, and Thailand. China’s jewelry sector is highly active, with domestic manufacturers such as Han’s Laser Technology Industry Group Co., Ltd. investing in R&D to produce cost-effective yet sophisticated micro-welding equipment for both domestic use and export. India, with its vast jewelry production industry, is increasingly adopting advanced micro-welding technologies, spurring local suppliers and attracting international equipment makers to establish sales and service operations in major jewelry hubs like Mumbai and Surat.
North America continues to show steady demand, particularly in the United States, where established jewelry manufacturing and repair centers in states such as New York and California drive equipment sales. Firms like Romanoff International Supply Corporation distribute and support a range of micro-welding systems for U.S. jewelers, often partnering with European and Japanese manufacturers. The trend toward boutique and custom jewelry production in North America is expected to stimulate further demand for compact, user-friendly micro-welding equipment.
Looking ahead, Southeast Asia—especially Thailand—is set to emerge further as a manufacturing hub, benefiting from government incentives and skilled artisan communities, while Middle Eastern centers such as Dubai leverage their status as global jewelry trade crossroads. Across regions, rising adoption of automation, integration with digital design workflows, and increasing focus on energy efficiency and precision are likely to shape the competitive landscape of jewelry micro-welding equipment manufacturing through the remainder of the decade.
Future Outlook: Opportunities, Risks, and Strategic Recommendations
The jewelry micro-welding equipment manufacturing sector is poised for dynamic changes in 2025 and the years ahead, shaped by advances in technology, evolving consumer preferences, and global manufacturing trends. Several opportunities and risks are anticipated, with strategic recommendations emerging for stakeholders across the value chain.
- Opportunities: The ongoing miniaturization of jewelry designs and the increasing popularity of intricate, customized pieces drive demand for high-precision micro-welding solutions. Laser micro-welding equipment, in particular, continues to gain traction due to its ability to deliver consistent, high-quality welds on precious metals with minimal thermal impact. Major manufacturers such as Ambrell and Orotig have recently unveiled systems with enhanced automation and digital controls, catering to both mass production and artisanal workshops. These innovations open new avenues for manufacturers to offer value-added features, such as remote diagnostics and IoT-enabled maintenance.
- Risks: The sector faces potential headwinds from rising raw material costs, supply chain uncertainties, and the need for ongoing operator training due to equipment sophistication. Additionally, economic volatility in key jewelry markets (such as the US, China, and India) could impact capital investments by small- and medium-sized jewelry manufacturers. Cybersecurity also emerges as a risk, particularly as more equipment integrates with factory networks and cloud-based monitoring systems.
- Strategic Recommendations: To capitalize on growth opportunities, manufacturers should invest in R&D for more versatile and energy-efficient welding systems. Collaborations with end-user jewelers and training organizations can accelerate adoption and ensure workforce readiness. Companies like LaserStar Technologies Corporation emphasize comprehensive customer support, including operator training and after-sales services, which can enhance brand loyalty and reduce equipment downtime. Furthermore, embracing digital platforms for remote equipment monitoring, predictive maintenance, and supply chain transparency will be crucial for long-term competitiveness.
- Outlook: With sustainability gaining prominence, future micro-welding systems may increasingly incorporate energy-saving features and support for recycled materials. As regulatory bodies push for greener manufacturing, equipment makers can differentiate themselves through eco-friendly innovations. Participation in industry forums, such as those organized by the Jewelry Industry Association, will be vital for staying abreast of regulatory changes and technological advancements.
In summary, 2025 and the ensuing years present a landscape of both promise and complexity for jewelry micro-welding equipment manufacturers. Strategic agility, technology adoption, and customer-centric service models will be essential for thriving in this evolving industry.