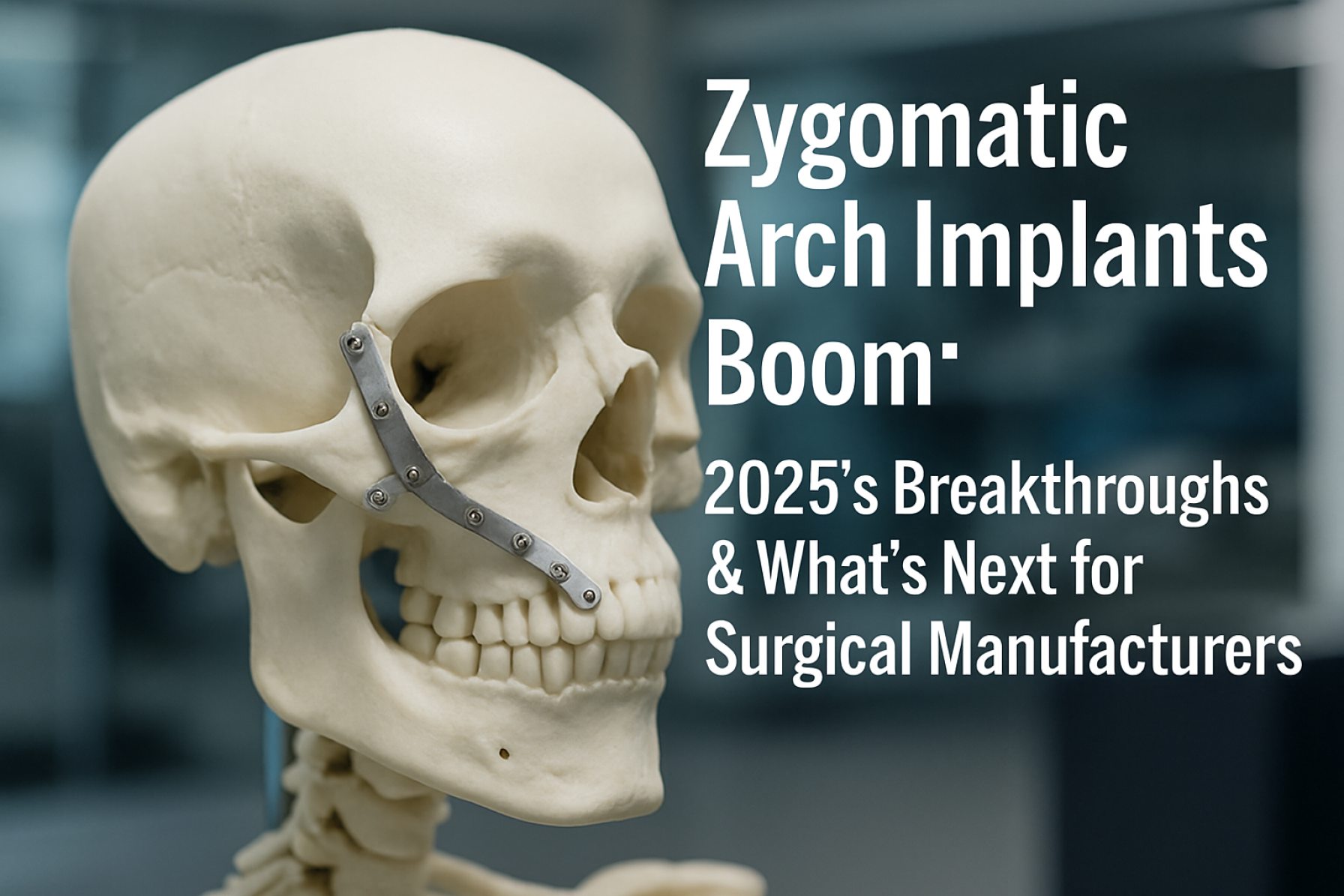
Table of Contents
- Executive Summary: Key Trends and 2025 Outlook
- Market Size, Growth Forecasts, and Global Demand Through 2030
- Regulatory Landscape and International Standards
- Leading Manufacturers and Emerging Industry Players
- Breakthrough Materials Shaping Implant Performance
- 3D Printing, Customization, and Digital Surgical Planning
- Clinical Outcomes and Patient-Centered Advances
- Supply Chain, Manufacturing Technologies, and Scalability
- Competitive Strategies and Strategic Partnerships
- Future Opportunities, Challenges, and Next-Gen Innovations
- Sources & References
Executive Summary: Key Trends and 2025 Outlook
The zygomatic arch surgical implants manufacturing sector is experiencing significant innovation and growth as of 2025, driven by advancements in materials science, digital surgical planning, and increasing demand for reconstructive and trauma-related maxillofacial procedures. Leading manufacturers are integrating new biomaterials and additive manufacturing techniques to produce patient-specific implants with enhanced biocompatibility, mechanical stability, and aesthetic outcomes. The adoption of 3D printing technologies has accelerated, allowing for rapid prototyping and customization of zygomatic arch implants to fit individual anatomical requirements, thereby improving surgical precision and patient recovery times (Stryker; Zimmer Biomet).
A notable trend is the shift towards titanium and PEEK (polyether ether ketone) implants, which offer improved strength-to-weight ratios and osseointegration properties. Companies such as DePuy Synthes and KLS Martin Group are expanding their maxillofacial implant portfolios to include these advanced materials, supporting both trauma and oncological facial reconstructions. Furthermore, the integration of digital workflows—ranging from CT imaging and virtual surgical planning to computer-aided design and manufacturing (CAD/CAM)—is streamlining the pre-operative and intra-operative phases, reducing errors and operative times (Materialise).
- Digital Customization: Manufacturers are increasingly collaborating with surgical teams to provide case-specific, 3D-printed zygomatic arch implants. This approach is being adopted by both established industry leaders and specialized providers such as implantcast and OssDsign.
- Regulatory Advances: The recent harmonization of regulatory frameworks in the US and EU is expected to facilitate faster market entry for innovative products while maintaining safety and efficacy standards (U.S. Food and Drug Administration).
- Market Drivers: Rising incidences of facial trauma and congenital anomalies, an aging global population, and growing acceptance of reconstructive surgery in emerging markets are expanding the addressable patient base (Zimmer Biomet).
Looking ahead to the next few years, the outlook for zygomatic arch surgical implants manufacturing remains robust. Continuous investment in R&D, close partnerships between manufacturers and clinical experts, and further advances in digital manufacturing are set to enhance implant performance and accessibility. Stakeholders anticipate that personalized, minimally invasive solutions will set the pace for innovation and adoption across both developed and emerging healthcare markets.
Market Size, Growth Forecasts, and Global Demand Through 2030
The global market for zygomatic arch surgical implants is anticipated to exhibit steady growth from 2025 through 2030, driven by advancements in maxillofacial reconstructive surgery, increasing incidence of facial trauma, and a growing aging population seeking dental and craniofacial rehabilitation. Notably, demand is rising in both developed and emerging markets as awareness of zygomatic implant solutions expands among clinicians and patients.
Several medical device manufacturers, such as Zimmer Biomet, Stryker, and Nobel Biocare, have reported increased adoption of advanced zygomatic implant systems. These companies are investing in R&D for custom and anatomically contoured implants, often manufactured with titanium alloys using precision CAD/CAM and additive manufacturing technologies. For instance, Nobel Biocare has expanded its zygomatic implant portfolio to address complex anatomical cases, citing robust clinician demand for innovative solutions in atrophic maxilla rehabilitation.
Regional trends indicate that North America and Europe remain the largest markets, supported by favorable reimbursement policies and a high prevalence of reconstructive surgeries. However, growing healthcare infrastructure and increased training in advanced surgical techniques are accelerating adoption rates in Asia-Pacific and Latin America. Zimmer Biomet has highlighted its initiatives to expand access to maxillofacial implants in emerging markets, reflecting an anticipated shift in global demand by 2030.
Industry bodies such as the American Association of Oral and Maxillofacial Surgeons continue to promote education and best practices, which is expected to further stimulate market growth by facilitating adoption of new implant technologies among surgeons.
Looking ahead, the outlook for zygomatic arch surgical implants manufacturing remains positive. The integration of digital planning, patient-specific implants, and minimally invasive surgical approaches are expected to support double-digit annual growth in certain segments. Furthermore, strategic collaborations between manufacturers and academic centers are anticipated to yield new implant designs tailored for personalized patient outcomes. By 2030, industry leaders are preparing for a broader, more technologically advanced global market, with sustained investment in manufacturing capacity and regulatory approvals across diverse geographies.
Regulatory Landscape and International Standards
The regulatory landscape for zygomatic arch surgical implants is evolving rapidly as demand grows for advanced maxillofacial reconstruction solutions. In 2025 and the next several years, manufacturers must navigate increasingly stringent requirements to ensure patient safety, device efficacy, and international market access.
In the United States, the U.S. Food and Drug Administration (FDA) regulates craniofacial implants as Class II medical devices under the 21 CFR 872.4760 code. This requires manufacturers to meet specific premarket notification (510(k)) obligations, demonstrating substantial equivalence to legally marketed predicate devices. The FDA emphasizes biocompatibility testing, mechanical strength validation, and comprehensive labeling. In recent years, the agency has intensified focus on post-market surveillance and unique device identification (UDI) systems, with further digital tracking mandates anticipated through 2025.
In the European Union, the Medical Device Regulation (EU MDR 2017/745), fully enforced since 2021, continues to set a high benchmark for zygomatic arch implant manufacturers. The regulation demands robust clinical evaluation, risk management, and traceability for all implantable devices. By 2025, notified bodies are placing greater scrutiny on technical documentation and post-market clinical follow-up (PMCF) activities. Companies such as Zimmer Biomet and Stryker are adapting their processes to comply with these evolving European requirements, including more rigorous data collection and reporting protocols.
Internationally, the ISO 13485:2016 standard remains the foundation for quality management in medical device manufacturing, including zygomatic arch implants. This standard is often a prerequisite for regulatory submissions in markets such as Canada, Australia, and Japan. The International Organization for Standardization (ISO) is currently reviewing revisions to further harmonize risk-based approaches, with updates expected by 2027. Additionally, ISO 10993 standards, governing biocompatibility, are being updated to address new material technologies and surface modifications commonly employed by leading manufacturers like Nobel Biocare.
Looking forward, there is growing momentum toward global regulatory harmonization. Initiatives such as the International Medical Device Regulators Forum (IMDRF) are promoting common requirements for clinical evidence and post-market oversight, which will impact how companies design, validate, and monitor their zygomatic arch implants. As digital manufacturing and patient-specific implants become more prominent, further regulatory guidance is anticipated to address additive manufacturing processes and personalized device safety.
Overall, the next few years will see zygomatic arch surgical implant manufacturers continually adapting to more comprehensive regulatory and international standard frameworks, fostering innovation while prioritizing patient safety and market access.
Leading Manufacturers and Emerging Industry Players
The landscape of zygomatic arch surgical implants manufacturing in 2025 continues to be shaped by a combination of established global leaders and a dynamic cohort of emerging companies. This sector is driven by advances in craniofacial trauma management, reconstructive surgery, and the increasing adoption of patient-specific solutions.
Among the leading manufacturers, Stryker maintains a significant presence with its comprehensive Maxillofacial product portfolio, including titanium and resorbable implants specifically designed for zygomatic and midface reconstruction. Their ongoing investment in 3D printing and anatomical modeling is enabling more personalized implant solutions, which are expected to see broader adoption through 2025 and beyond.
Zimmer Biomet continues to innovate in the craniomaxillofacial (CMF) sector, offering a range of standard and custom implants for zygomatic arch repair. Their emphasis on digital planning and surgical navigation tools is enhancing precision and outcomes in complex reconstructive procedures. In 2024, Zimmer Biomet expanded its portfolio with new plating systems that further address the intricacies of zygomatic bone fixation.
DePuy Synthes, a Johnson & Johnson company, remains a top player in this market with its MatrixMIDFACE and other modular implant systems, recognized for their adaptability in trauma and reconstructive surgery. DePuy Synthes has also invested in developing biocompatible materials and advanced fixation techniques, aligning with trends toward minimally invasive procedures.
Emerging manufacturers are making notable inroads, particularly those specializing in additive manufacturing and patient-specific implant design. Materialise leverages its expertise in medical 3D printing to collaborate with surgeons on custom zygomatic arch implants, streamlining the transition from digital planning to surgical application. Similarly, KLS Martin Group offers innovative CMF solutions, including the IPS Implants® range, which utilizes advanced imaging and CAD/CAM technology for tailored anatomical fit.
The industry outlook for 2025 and beyond is marked by continued growth in personalized medicine, with major manufacturers expanding digital workflows and rapid prototyping capabilities. Collaboration between device makers, surgical teams, and digital health companies is poised to accelerate the adoption of custom, patient-specific zygomatic arch implants, improving both functional and aesthetic outcomes. As regulatory pathways for novel materials and digital processes become clearer, more startups and regional players are expected to enter the market, further driving innovation and competition in this specialized segment.
Breakthrough Materials Shaping Implant Performance
The field of zygomatic arch surgical implants is witnessing rapid transformation, driven by a new generation of biomaterials that promise to enhance implant performance, compatibility, and patient outcomes. As of 2025, titanium alloys remain the gold standard due to their exceptional biocompatibility, corrosion resistance, and mechanical strength. Leading manufacturers such as Zimmer Biomet and Smith+Nephew continue to refine titanium-based implants, focusing on advanced surface modifications—such as micro-roughening and nano-coating—to promote osseointegration and reduce the risk of infection.
However, breakthroughs in alternative materials are poised to challenge titanium’s dominance. Polyetheretherketone (PEEK), a high-performance polymer, is gaining attention for its radiolucency and elastic modulus close to bone, which may help mitigate stress shielding. Companies like Stryker and DePuy Synthes have expanded their portfolios to include PEEK-based craniofacial implants, leveraging precision additive manufacturing to produce patient-specific geometries. Furthermore, bioactive ceramics, such as hydroxyapatite coatings, are being integrated to enhance bone-implant bonding, with firms like Zimmer Biomet supporting research on ceramic-titanium composites for maxillofacial applications.
The next few years are expected to witness an acceleration in the adoption of hybrid materials—combining metals, polymers, and ceramics—to optimize both mechanical performance and biological response. Customization is also being revolutionized by 3D printing technologies, enabling the fabrication of implants tailored to individual patient anatomy from digital scans. Materialise and Renishaw are collaborating with surgical teams to deliver such bespoke solutions, using both titanium and PEEK, and exploring new biocompatible alloys and composites.
Looking ahead, research into surface functionalization—such as antimicrobial coatings and growth factor delivery systems—hints at implants that not only restore function but actively promote healing and reduce complications. The outlook for 2025 and beyond is one of material convergence and digital innovation, with leading manufacturers and technology partners at the forefront of shaping the future of zygomatic arch surgical implants.
3D Printing, Customization, and Digital Surgical Planning
The integration of 3D printing, customization, and digital surgical planning is rapidly redefining zygomatic arch surgical implant manufacturing as of 2025. Innovations in additive manufacturing have enabled the production of patient-specific implants (PSIs) with unprecedented precision, enhancing both esthetic and functional outcomes in maxillofacial reconstruction. Leading medical device manufacturers are actively investing in advanced digital workflows that begin with high-resolution imaging—typically CT or CBCT scans—which are then converted into 3D models for virtual planning and implant design.
Several industry frontrunners, such as Materialise, are offering comprehensive digital platforms that allow surgeons to collaborate with engineers in real time, ensuring that zygomatic arch implants are tailored to the patient’s unique anatomy. These platforms integrate preoperative planning, surgical simulation, and the generation of 3D-printed guides or implants, streamlining the process from diagnosis to postoperative care. Similarly, DePuy Synthes provides customizable solutions for craniofacial reconstruction, including patient-matched zygomatic implants, manufactured under rigorous quality controls to meet evolving regulatory standards.
- Customization: The trend toward full customization is driven by demand for improved fit, reduced intraoperative time, and faster patient recovery. Companies such as KLS Martin Group and Zimmer Biomet are expanding their portfolios with titanium and PEEK implants, fabricated via selective laser melting (SLM) or electron beam melting (EBM), and designed to match the patient’s bone structure with high precision.
- Digital Surgical Planning: Digital planning tools are now considered standard in complex zygomatic reconstructions. These tools allow surgeons to anticipate anatomical challenges, determine optimal fixation points, and rehearse the procedure virtually. For instance, Materialise’s Mimics Innovation Suite supports the creation of digital surgical plans and 3D-printed anatomical models, which facilitate communication between multidisciplinary teams and improve intraoperative accuracy.
- Quality and Regulatory Momentum: As regulatory bodies refine their requirements for custom medical devices, manufacturers are increasingly emphasizing traceability and process validation. Companies like KLS Martin Group highlight their adherence to ISO 13485 and MDR (EU Medical Device Regulation) standards, ensuring safety and reproducibility of 3D-printed zygomatic arch implants.
Looking ahead, the next few years are expected to bring further automation of digital workflows, improved biomaterials, and expanded AI-driven design applications, ultimately making personalized zygomatic arch implants more accessible and efficient for both surgeons and patients.
Clinical Outcomes and Patient-Centered Advances
Recent advancements in the manufacturing of zygomatic arch surgical implants have significantly influenced clinical outcomes and patient-centered care. The adoption of patient-specific implant (PSI) fabrication using digital workflows and additive manufacturing technologies is notably improving surgical precision and postoperative results. In 2025, manufacturers such as Stryker and DePuy Synthes continue to refine titanium and PEEK-based zygomatic arch implants, emphasizing custom design to accommodate unique anatomical variations and complex trauma cases.
Clinical data from centers utilizing custom-manufactured implants show reductions in operative time, improved fit, and minimized risk of malposition or secondary revision surgeries. For example, Materialise reports that their 3D-printed maxillofacial solutions have contributed to faster patient recovery, more predictable facial symmetry, and increased satisfaction with aesthetic outcomes. In 2024 and 2025, the integration of preoperative virtual surgical planning and intraoperative navigation—supported by manufacturers like Zimmer Biomet—has become more widespread, further enhancing accuracy and patient safety in zygomatic arch reconstruction.
Patient-centered advances also focus on reducing morbidity by enabling minimally invasive approaches. Implant manufacturers are developing lower-profile fixation systems and absorbable materials to minimize palpable hardware and long-term complications. Companies such as KLS Martin Group are actively expanding lines of resorbable plates and screws for midface reconstruction, aiming to address concerns about permanent foreign bodies and improve long-term comfort.
Looking ahead, the outlook for clinical outcomes in zygomatic arch implant surgery remains positive. Industry leaders are investing in real-time feedback mechanisms—including intraoperative 3D imaging and AI-driven outcome prediction—to further personalize patient care and optimize results. The next few years are expected to bring additional regulatory approvals for novel biomaterials and digital design platforms, broadening the range of patient-specific solutions available to surgeons. As manufacturers continue to collaborate with clinical partners, the emphasis on improved functional outcomes, reduced recovery times, and patient satisfaction will likely drive further innovation in zygomatic arch surgical implant manufacturing.
Supply Chain, Manufacturing Technologies, and Scalability
The manufacturing of zygomatic arch surgical implants in 2025 is characterized by an evolving supply chain, rapid technology adoption, and increasing focus on scalability to meet global clinical demands. The sector is dominated by established medical device manufacturers, with significant input from material suppliers and precision engineering firms.
Most zygomatic arch implants are produced using biocompatible materials such as titanium alloys (notably Ti-6Al-4V), which offer strength, corrosion resistance, and osseointegration properties. Leading suppliers like Zimmer Biomet and Smith+Nephew continue to refine their materials sourcing and validation procedures to ensure traceability and regulatory compliance, particularly as global standards tighten post-pandemic.
Additive manufacturing (3D printing) is increasingly supplementing traditional subtractive manufacturing (CNC milling) for custom-fit implants, enabling faster prototyping and production runs. Companies such as Stryker have expanded their additive manufacturing capabilities for patient-specific maxillofacial implants, reporting reductions in lead times and greater geometric complexity in product design. This shift is supported by advances in digital imaging and CAD/CAM workflows, which streamline customization and reduce dependency on manual labor.
The supply chain for these implants is global. While raw titanium is sourced from a few key suppliers, finishing, sterilization, and packaging are often distributed across multiple geographies to meet local regulatory requirements. DePuy Synthes (Johnson & Johnson MedTech) has reported ongoing investments in regional manufacturing hubs and logistics optimization, citing the need for resilience in the face of supply disruptions and fluctuating demand.
Scalability remains a focal point as elective surgeries rebound and markets expand in Asia-Pacific and Latin America. Manufacturers are leveraging automation and predictive analytics to forecast demand and adjust production accordingly. Partnerships with contract manufacturing organizations (CMOs) are also increasing, as exemplified by alliances between OEMs and specialist implant producers to balance in-house innovation with external manufacturing scale.
- Zimmer Biomet and Stryker are investing in next-generation robotics and AI-powered quality control, aiming to further automate inspection and reduce defect rates.
- Regulatory harmonization efforts, led by industry bodies and multinational firms, are expected to ease cross-border distribution and accelerate time-to-market for new implant designs.
- Environmental sustainability—especially recycling of titanium scrap and reduction of packaging waste—is an emerging focus among manufacturers, with companies announcing new green initiatives in 2025.
Collectively, these trends signal a robust, technology-driven supply chain for zygomatic arch surgical implants, with scalability and innovation poised to meet rising clinical needs in the coming years.
Competitive Strategies and Strategic Partnerships
In 2025, manufacturers of zygomatic arch surgical implants are intensifying their competitive strategies and forming targeted partnerships to strengthen their market positions. One of the most notable trends is the integration of digital technologies and additive manufacturing to offer bespoke implants that address complex maxillofacial anatomy. Companies such as Zimmer Biomet and Smith+Nephew have continued to invest in advanced CAD/CAM platforms and 3D printing facilities, aiming to reduce lead times and improve surgical outcomes by providing patient-specific solutions.
Strategic partnerships between implant manufacturers and specialized software providers are also on the rise. For example, DePuy Synthes has established collaborations with digital planning companies to streamline the workflow from virtual surgical planning to implant production. This approach not only enhances precision but also fosters loyalty among maxillofacial surgeons who value integrated, end-to-end services.
Another area of competitive focus is biocompatibility and advanced materials. Stryker has expanded R&D partnerships with universities and biomedical research institutions to develop titanium alloys and surface treatments that promote osseointegration and reduce infection rates. Such collaborations accelerate the introduction of next-generation products and differentiate offerings in a crowded marketplace.
- Geographic Expansion: Leading manufacturers are entering emerging markets through joint ventures with local distributors and healthcare providers. This not only enhances distribution networks but also addresses regulatory requirements unique to each region. KLS Martin Group is a prominent example, extending its footprint in Asia-Pacific and Latin America through regional partnerships.
- Acquisitions and Licensing: Acquisitions remain a key strategy, as larger firms seek to absorb niche innovators with proprietary implant designs or manufacturing technologies. Licensing deals for novel biomaterials and surface coatings are also gaining traction as firms aim to diversify their portfolios rapidly.
- Surgeon Education and Training: Manufacturers are investing in collaborative training programs with hospital networks and surgical societies, such as those supported by Medartis. These initiatives not only promote new product adoption but also build long-term relationships with key opinion leaders.
Looking ahead, the focus on strategic alliances, digital workflows, and region-specific partnerships is expected to intensify, especially as demand for personalized zygomatic arch implants grows. Ongoing innovation, combined with robust collaboration across the supply chain, will likely define competitive success in the sector through the remainder of the decade.
Future Opportunities, Challenges, and Next-Gen Innovations
The field of zygomatic arch surgical implants manufacturing is poised for significant transformation in 2025 and the coming years, driven by technological advancements, evolving clinical needs, and an expanding global patient base. Several opportunities and challenges are shaping the outlook for manufacturers, while next-generation innovations are setting new standards in craniofacial reconstruction.
Future opportunities are closely tied to the increasing prevalence of maxillofacial trauma, oncological resections, and congenital anomalies requiring zygomatic arch reconstruction. Rising awareness about facial reconstructive surgery and expanding access in emerging markets are expected to drive demand for precision-manufactured implants. Leading companies such as Stryker and Zimmer Biomet are expanding their craniofacial portfolios with more customizable and patient-specific solutions to address these needs.
One of the most promising next-gen innovations is the integration of digital planning and additive manufacturing (3D printing) into implant production. Companies like DePuy Synthes are developing patient-specific implants using advanced imaging and computer-aided design, enabling precise anatomical fit and reducing intraoperative adjustment. The adoption of biocompatible materials, such as titanium alloys and high-performance polymers, is further enhancing implant longevity and biocompatibility.
Despite these advances, manufacturers face challenges, including stringent regulatory requirements for custom implants and the need for robust clinical validation. The complexity of zygomatic anatomy demands high precision in manufacturing, which can increase production costs and turnaround times. Furthermore, ensuring global supply chain resilience for critical materials remains a key concern, as highlighted by recent disruptions in medical device logistics (Medtronic).
Looking forward, the convergence of artificial intelligence with surgical planning platforms is expected to streamline preoperative workflows and further personalize implant design. Companies are also exploring bioactive coatings and surface modifications to promote osseointegration and reduce infection risk. Collaborations between manufacturers and clinical centers are likely to accelerate the validation and adoption of these next-generation solutions, ultimately improving patient outcomes and expanding the possibilities for zygomatic arch reconstruction worldwide.