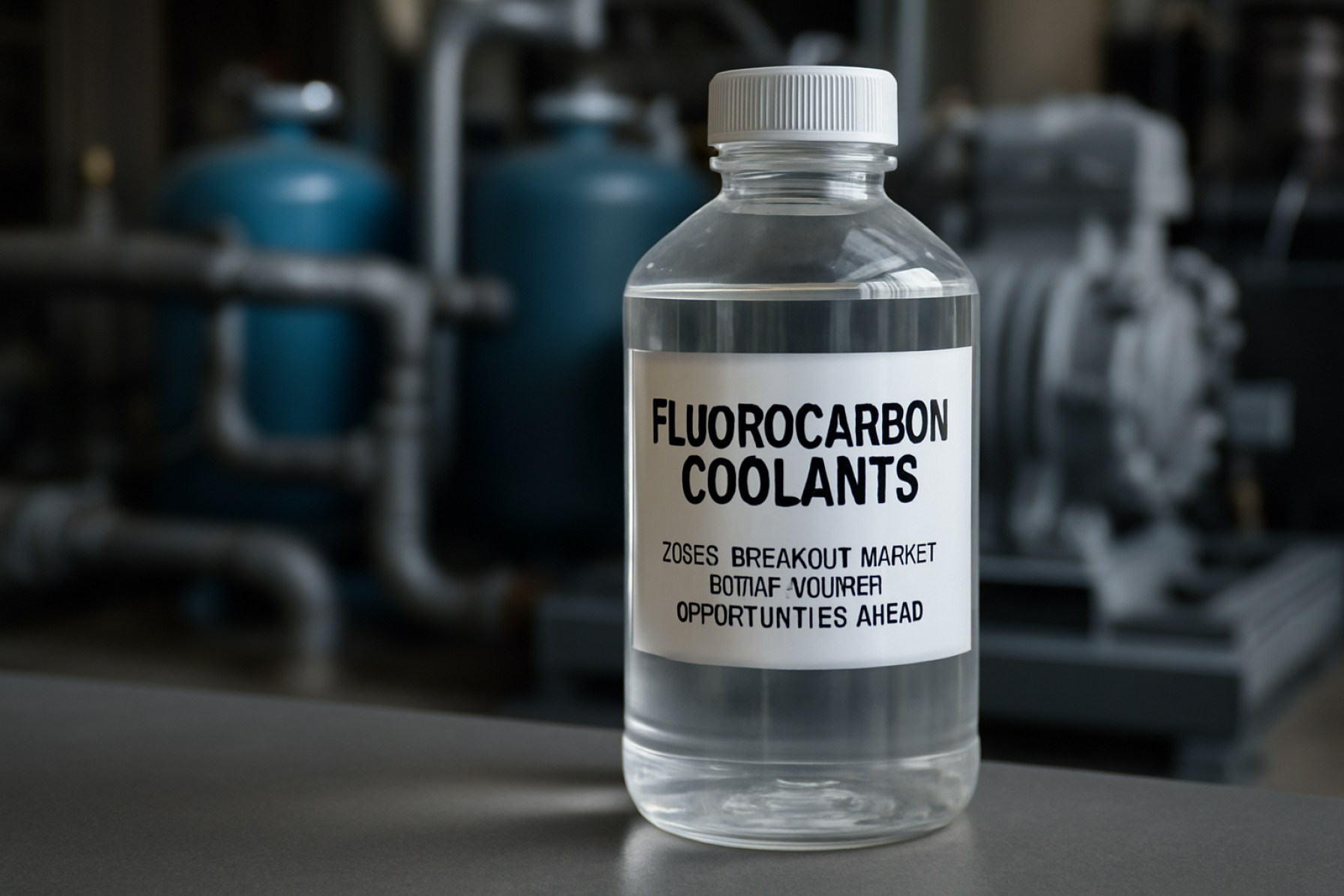
Table of Contents
- Executive Summary: Market Pulse and Key Insights
- 2025 Global Market Forecast and Growth Drivers
- Major Manufacturers and Industry Players (Official Sources)
- Emerging Applications: Data Centers, Electronics, and Beyond
- Technological Innovations in Fluorocarbon Coolant Formulation
- Environmental, Regulatory, and Sustainability Considerations
- Supply Chain, Pricing, and Raw Material Trends
- Competitive Landscape: Mergers, Partnerships, and Strategies
- Regional Analysis: North America, Europe, Asia-Pacific, and Key Markets
- Future Outlook: Opportunities and Challenges Through 2030
- Sources & References
Executive Summary: Market Pulse and Key Insights
The fluorocarbon liquid coolants manufacturing sector is undergoing significant transformation in 2025, driven by advances in high-performance electronics, data center cooling, electric vehicle (EV) thermal management, and evolving global regulations. The demand for efficient, non-flammable, and thermally stable cooling solutions is expanding rapidly, with manufacturers responding through innovation and capacity expansion.
Key market participants, including 3M, Chemours, and Solvay, are at the forefront of developing next-generation fluorocarbon coolants. These companies are leveraging proprietary chemistries to deliver products with low global warming potential (GWP) and enhanced dielectric properties, which are increasingly demanded by the electronics and automotive industries. In 2025, 3M continues to supply its Fluorinert™ and Novec™ brands, although its announced exit from PFAS manufacturing by 2025 is prompting shifts in the supply landscape and new product development cycles.
As regulatory pressure mounts worldwide—particularly in the European Union and North America—to limit or phase down high-GWP and PFAS-based fluids, manufacturers are accelerating the transition to novel chemistries. For example, Chemours is scaling up production of Opteon™ branded hydrofluoroolefins (HFOs), which offer lower environmental impact while maintaining thermal performance and electrical insulation required in critical applications.
- Data center cooling: The hyperscale data center industry’s move toward direct-to-chip and immersion cooling is fueling robust demand for fluorocarbon liquid coolants. Companies such as Solvay are scaling up their Galden® PFPE product lines to meet this need, emphasizing reliability and environmental compliance.
- Automotive and EVs: As EV adoption accelerates, so does the requirement for safe and effective battery and power electronics cooling. Fluorocarbon coolants’ dielectric properties make them ideal for these applications, with manufacturers tailoring products for OEM specifications.
- Supply chain and production: The sector is witnessing investments in new manufacturing capacity and strategic partnerships to secure raw material access and ensure compliance with tightening sustainability standards.
Looking ahead, the market outlook for fluorocarbon liquid coolants manufacturing in 2025 and beyond is shaped by ongoing regulatory change, customer demand for higher performance and lower environmental impact, and the industry’s ability to innovate. The competitive landscape will continue to evolve as established players and new entrants respond to both opportunity and constraint, with a strong focus on sustainable chemistry and global supply assurance.
2025 Global Market Forecast and Growth Drivers
The global market for fluorocarbon liquid coolants is poised for continued expansion through 2025, driven by growing demand in data center cooling, power electronics, and advanced manufacturing sectors. Fluorocarbon coolants, such as perfluorinated and polyfluorinated compounds, are prized for their exceptional thermal stability, dielectric properties, and chemical inertness—making them crucial for next-generation thermal management solutions.
Leading manufacturers including 3M, Chemours, and Solvay continue to invest in scaling production capacity and developing new formulations to meet evolving customer requirements. For example, 3M’s Fluorinert™ and Novec™ engineered fluids are widely used in immersion cooling for high-performance computing and hyperscale data centers, a segment projected to see double-digit growth as demand for AI and cloud computing infrastructure accelerates. Chemours’ Opteon™ fluids and Solvay’s Galden® products also serve critical roles in electronics, semiconductor manufacturing, and medical device cooling, markets expected to expand as electrification and miniaturization trends continue.
A key growth driver in 2025 is the rapid proliferation of data centers and the industry’s shift toward liquid immersion and direct-to-chip cooling to achieve higher energy efficiency and reduce operating costs. According to industry data from 3M, liquid cooling can deliver up to 97% thermal efficiency compared to traditional air cooling, directly supporting sustainability goals and regulatory requirements for lower carbon footprints. In addition, the automotive sector’s transition to electric vehicles (EVs) is propelling demand for fluorocarbon coolants in battery thermal management systems, with manufacturers like Chemours supporting this shift by expanding their production facilities and product portfolios.
- Regulatory Environment: Environmental regulations remain a significant factor shaping the market. Manufacturers are focusing on low global warming potential (GWP) and non-flammable formulations to meet evolving standards, particularly in Europe and North America. Companies like Solvay highlight their ongoing R&D in sustainable fluorochemicals to address these challenges.
- Supply Chain and Investment: In response to supply chain disruptions and increased demand, major players are announcing investments in new plants and expanded production lines. For instance, Chemours has outlined plans to enhance capacity for specialty fluids across its global sites.
Looking ahead, the outlook for fluorocarbon liquid coolants manufacturing remains robust through 2025 and beyond, with innovation in product chemistry and a focus on sustainability expected to drive new applications and market penetration.
Major Manufacturers and Industry Players (Official Sources)
The global fluorocarbon liquid coolants market in 2025 is characterized by a concentrated group of major manufacturers, most of which are established chemical corporations with significant R&D capabilities and global supply chains. These specialty coolants, predominantly perfluorinated or polyfluorinated compounds, are used in demanding electronics, data centers, automotive, and aerospace thermal management applications due to their high dielectric strength and chemical stability.
Among the leading industry players, 3M continues to be a dominant force, notably through its Novec engineered fluids line. Despite announcing a phase-out of PFAS manufacturing by 2025, 3M maintains a strong position in the market, and its production transition is being closely watched for supply impacts and new chemistry alternatives. Solvay remains another significant manufacturer, offering its Galden perfluoropolyether (PFPE) coolants, which are widely adopted in semiconductor and critical electronics cooling. Solvay’s investments in low-global-warming-potential (GWP) formulations and expanded production facilities in Europe underscore its commitment to supporting growth in sustainable cooling fluids.
The Chemours Company is another major player, building on its legacy in fluorochemicals with products such as Vertrel and Krytox fluids, which are tailored for electronics, defense, and industrial cooling sectors. Chemours is actively investing in new production technologies to meet increasing demand for high-performance, low-emission coolants. Daikin Industries, a prominent Japanese manufacturer, produces a range of fluorinated fluids for electronics and high-performance computing, and has announced plans to expand capacity and invest in new product development to address environmental and regulatory trends.
Other notable contributors include Arkema (with its Forane and other specialty fluids portfolios) and AGC Inc. (formerly Asahi Glass), which supplies fluorinated liquids for niche cooling applications, particularly in Asia. These companies are ramping up R&D in response to increasing scrutiny of PFAS compounds and regulatory pressures, especially in the US and EU, prompting a shift toward next-generation, environmentally benign chemistries.
Industry outlook for 2025 and the near future suggests continued consolidation among major global players and a strong focus on sustainable product innovation. Demand for fluorocarbon liquid coolants is expected to grow, particularly in advanced cooling systems for data centers, electric vehicles, and semiconductor manufacturing. The industry’s trajectory will be strongly influenced by regulatory developments and the ability of manufacturers to commercialize new, less persistent fluorinated alternatives without sacrificing performance.
Emerging Applications: Data Centers, Electronics, and Beyond
The manufacturing landscape for fluorocarbon liquid coolants is experiencing significant transformation in 2025, fueled by surging demand from data centers, advanced electronics, and emerging technology sectors. Fluorocarbon coolants, prized for their chemical inertness, dielectric properties, and thermal stability, are increasingly integral to next-generation liquid immersion cooling systems in hyperscale data centers and high-performance computing environments.
Leading manufacturers such as 3M and The Chemours Company are expanding production capabilities to meet this demand. For instance, 3M’s Fluorinert™ and Novec™ engineered fluids remain central to immersion cooling solutions, with the company announcing ongoing investments in global capacity and R&D for next-generation thermal management products. Chemours, with its Opteon™ portfolio, is similarly investing in scalable manufacturing to support growth in immersion cooling for cloud infrastructure and AI/ML workloads.
Several factors are shaping manufacturing strategies in 2025 and the near future:
- Data Center Expansion: According to Eaton, the global explosion of data and the proliferation of AI-driven workloads are accelerating the adoption of immersion cooling, driving up demand for high-purity, reliable fluorocarbon coolants. Manufacturers are responding by refining purification processes and scaling up facilities to ensure consistent supply and quality.
- Electronics Miniaturization: The trend toward denser, more powerful electronics—especially in sectors like automotive ADAS, 5G infrastructure, and advanced manufacturing—necessitates efficient, non-conductive cooling solutions. Fluorocarbon coolants are being tailored for these applications, with major producers developing specialty grades for use in sensitive semiconductor and power electronics cooling (3M).
- Environmental and Regulatory Pressures: With tightening PFAS regulations in North America and Europe, manufacturers are accelerating R&D on lower-global-warming-potential (GWP) and short-chain fluorinated compounds. The Chemours Company is actively investing in sustainable fluorochemical manufacturing, aiming to develop high-performance coolants with improved environmental profiles.
Looking forward, the industry outlook remains robust as digital infrastructure continues to expand globally. Manufacturers are expected to focus on process optimization, vertical integration, and strategic partnerships with data center operators and electronics OEMs. Innovations in fluorocarbon chemistry, combined with responsible stewardship and compliance, will shape the competitive landscape and enable new applications in quantum computing, electric vehicles, and renewable energy systems over the next several years.
Technological Innovations in Fluorocarbon Coolant Formulation
The manufacturing of fluorocarbon liquid coolants is undergoing substantial transformation in 2025, driven by a combination of environmental imperatives, regulatory changes, and the evolving demands of high-performance applications such as data centers, power electronics, and electric vehicles. Central to these innovations are the formulation techniques and chemistry adaptations that enable the production of next-generation coolants with lower global warming potentials (GWPs), improved thermal properties, and enhanced material compatibility.
One significant area of focus in 2025 is the development and commercialization of hydrofluoroolefin (HFO)-based coolants and advanced hydrofluorocarbon (HFC) blends. Manufacturers such as The Chemours Company and 3M are actively expanding their portfolios of engineered fluids, including new HFO chemistries designed to meet increasingly strict environmental standards. For example, Chemours’ Opteon™ line features HFO coolants that offer ultra-low GWPs and are engineered to minimize atmospheric persistence while maintaining high dielectric strength and chemical stability.
In parallel, process innovations are enabling more efficient and scalable production. Companies have invested in proprietary synthesis routes and purification techniques to reduce by-products and energy consumption, directly supporting sustainability goals. Daikin Industries, Ltd. has announced improvements in the catalytic processes for fluorination and olefin conversion, resulting in higher yields of target coolant molecules and lower environmental impact from manufacturing operations.
Material science advances are also playing a role, with manufacturers tailoring molecular structures to enhance thermal conductivity, reduce viscosity, and boost compatibility with a wider range of plastics and elastomers. This is particularly relevant for immersion cooling applications in electronics, where the interaction between coolants and sensitive components must be finely balanced. Solvay is pioneering the integration of performance additives and co-solvents to further optimize the functional properties of their fluorinated heat transfer fluids.
Looking ahead, the outlook for fluorocarbon liquid coolant manufacturing is marked by ongoing R&D investments and collaborative efforts between manufacturers, end-users, and regulatory bodies. The next few years are expected to bring further breakthroughs in molecular design, lifecycle management, and closed-loop manufacturing processes, all aimed at aligning the sector with global decarbonization and circularity objectives. These technological innovations are setting new benchmarks for coolant performance, environmental safety, and operational reliability across diverse industrial domains.
Environmental, Regulatory, and Sustainability Considerations
The manufacturing of fluorocarbon liquid coolants in 2025 is increasingly shaped by a dynamic interplay of environmental, regulatory, and sustainability considerations. Historically valued for their thermal stability and dielectric properties, fluorocarbon-based coolants—such as perfluorocarbons (PFCs) and hydrofluoroethers (HFEs)—are now under heightened scrutiny due to their environmental persistence and high global warming potential (GWP).
Regulatory frameworks are tightening across key markets. In the European Union, the phasedown of high-GWP fluorinated gases under the F-Gas Regulation continues to impact both production and import of certain fluorocarbons. The most recent amendments, set to apply through 2025 and beyond, impose stricter quotas and reporting requirements, compelling manufacturers to reformulate or substitute legacy products 3M. Similarly, the United States Environmental Protection Agency (EPA) is advancing the American Innovation and Manufacturing (AIM) Act, targeting a substantial reduction in the use and production of HFCs and related materials Chemours.
Manufacturers are responding with both process innovation and product reformulation. Leading producers such as 3M and Chemours have introduced new generations of low-GWP fluorinated fluids, including HFEs and hydrofluoropolyethers (HFPEs), which are designed to deliver required performance while minimizing environmental impact. For example, 3M’s Novec fluids, while facing market withdrawal in some regions due to broader company policy changes, have prompted other manufacturers to accelerate the development of alternative sustainable coolant chemistries.
Sustainability initiatives are also focused on minimizing lifecycle emissions. Companies are investing in closed-loop manufacturing systems to reduce process losses, and implementing advanced waste treatment technologies to capture and destroy fluorinated emissions before release. Additionally, producers such as Solvay are expanding research into non-fluorinated and partially fluorinated alternatives, and engaging in life cycle assessments to quantify and mitigate environmental impacts.
Looking ahead, the outlook for 2025 and the following years suggests continued regulatory tightening and increased market demand for sustainable coolants. As end-users in data centers, electronics, and electric vehicle sectors intensify their sustainability criteria, manufacturers will likely accelerate the transition to low-impact chemistries, optimize production efficiency, and increase transparency through environmental reporting and certifications.
Supply Chain, Pricing, and Raw Material Trends
The supply chain for fluorocarbon liquid coolants is characterized by a complex global network of raw material procurement, chemical processing, and distribution logistics. In 2025, the sector continues to be shaped by several key trends, including tightening environmental regulations, fluctuating raw material costs, and increasing demand from advanced electronics and data center cooling applications.
A critical raw material for fluorocarbon coolants is fluorspar (calcium fluoride), which is processed to produce hydrofluoric acid (HF)—the precursor for many fluorinated compounds. China remains the world’s largest supplier of fluorspar, accounting for over 60% of global production. In recent years, Chinese export policies and domestic consumption priorities have introduced volatility to international supply, impacting downstream manufacturers in Europe, Japan, and North America. Companies such as Chemours and 3M—major producers of fluorinated specialty fluids—have reported ongoing efforts to diversify sourcing and invest in recycling initiatives to mitigate these risks.
Pricing trends for fluorocarbon coolants in 2025 are being influenced by both raw material costs and regulatory pressure. The price of fluorspar and HF has shown moderate increases due to supply constraints and stricter mining regulations in China. Additionally, the European Union’s evolving REACH regulation and the U.S. Environmental Protection Agency’s tightening oversight of per- and polyfluoroalkyl substances (PFAS) have led to increased compliance costs for manufacturers. In response, producers like Solvay are investing in new manufacturing technologies that reduce emissions and enable the production of next-generation, lower-global-warming-potential (GWP) fluorinated fluids.
Disruptions in global logistics, including shipping delays and increased transportation costs, have also affected the supply chain for fluorocarbon coolants. In 2025, manufacturers are reporting extended lead times and are adjusting inventory and contracting strategies accordingly. Some, such as Daikin Industries, are re-evaluating their supply chain footprints and pursuing more regionalized production to secure supply and control costs.
Looking forward, the outlook for fluorocarbon coolant manufacturing is marked by cautious optimism. While raw material and regulatory challenges persist, ongoing investments in sustainable production, recycling, and alternative chemistries are expected to gradually alleviate supply pressures. Companies are also exploring partnerships with electronics and automotive OEMs to secure demand visibility and develop tailored formulations, ensuring a more resilient and adaptive supply chain in the coming years.
Competitive Landscape: Mergers, Partnerships, and Strategies
The competitive landscape of fluorocarbon liquid coolants manufacturing in 2025 is characterized by an intensified focus on strategic partnerships, mergers, and technological collaborations. Leading manufacturers are actively consolidating their positions and expanding their portfolios to address evolving demands across electronics cooling, data centers, and advanced industrial applications.
A prominent example is 3M, historically a dominant player in fluorinated liquids with its Novec™ engineered fluids. In recent years, 3M announced its exit from the production of PFAS-containing products by the end of 2025, redirecting focus towards sustainable alternatives and collaborating with customers to transition to next-generation coolants. This strategic pivot has influenced the competitive dynamics, prompting suppliers and end-users to seek new partnerships and alternative sources.
Meanwhile, The Chemours Company, a key global fluorochemicals producer, continues to invest in high-value fluorinated liquids, including its Opteon™ specialty fluids for immersion cooling. Chemours has emphasized supply reliability and innovation, seeking collaboration with technology firms and OEMs to support the rapid growth of cloud computing and hyperscale data centers. Their strategic initiatives include expanding manufacturing capacity and entering long-term supply agreements with major electronics and cooling infrastructure companies.
Japanese firms, such as Daikin Industries, Ltd., are also stepping up their efforts. Daikin has announced investments in R&D and production expansion for low-GWP (global warming potential) fluorinated coolants, positioning itself as a sustainable partner for customers transitioning away from legacy PFAS chemicals. Daikin’s international collaborations with electronics manufacturers and thermal management companies have broadened its footprint in Asia, North America, and Europe.
Additionally, Solvay has sought alliances to bolster its specialty fluids portfolio, focusing on high-purity fluorochemicals for electronic and semiconductor manufacturing. Their recent partnerships with advanced cooling solutions integrators reflect a targeted strategy toward growth segments such as 5G infrastructure and electric vehicle battery cooling.
Overall, the competitive outlook for 2025 and beyond is defined by a shift toward sustainable chemistries, supply chain resilience, and closer collaboration between manufacturers and end-users. As regulatory pressures mount and demand for efficient thermal management escalates, the industry is likely to see further strategic alliances and technology-driven mergers, particularly among players able to offer low-emission, high-performance solutions.
Regional Analysis: North America, Europe, Asia-Pacific, and Key Markets
In 2025, the manufacturing of fluorocarbon liquid coolants continues to be shaped by regional dynamics, with North America, Europe, and Asia-Pacific each exhibiting unique trends and growth drivers. These coolants, prized for their chemical inertness, dielectric properties, and thermal stability, are increasingly critical for sectors such as data centers, power electronics, medical imaging, and advanced manufacturing.
North America remains a leading hub, benefiting from established manufacturers and a robust technological base. Companies such as 3M Company and Chemours are at the forefront, with deep portfolios of engineered fluorinated fluids. The region’s emphasis on high-performance computing and the expansion of hyperscale data centers are fueling demand for two-phase immersion cooling and direct liquid cooling solutions. The regulatory environment is increasingly influential, with U.S. policies targeting the reduction of hydrofluorocarbon (HFC) emissions and encouraging the adoption of lower global warming potential (GWP) alternatives.
Europe is characterized by stringent environmental legislation, particularly under the F-Gas Regulation, which is accelerating the phase-down of high-GWP fluorocarbons. Manufacturers such as Solvay and Arkema are responding by investing in next-generation fluorinated fluids with improved environmental profiles. The European market is also seeing increased demand from the electric vehicles (EV) and renewable energy sectors, both of which require efficient, non-flammable, and thermally stable cooling agents for batteries and power electronics. Ongoing investment in R&D and local production facilities is expected to strengthen Europe’s position in the global market.
Asia-Pacific is the fastest-growing region, led primarily by China, Japan, and South Korea. Local giants like Daikin Industries and Asahi Kasei Corporation are expanding production capacity to meet surging demand from the electronics, semiconductor, and automotive industries. The proliferation of 5G infrastructure and the rapid expansion of cloud computing services are major drivers, as they require advanced thermal management solutions. Additionally, government incentives and the shift of global electronics manufacturing to Asia-Pacific are prompting further investment in both production technology and supply chain integration.
Going forward, all key regions are expected to prioritize sustainability, regulatory compliance, and technological innovation. The competitive landscape will be increasingly defined by the ability to deliver high-performance, environmentally responsible coolant solutions tailored to emerging industrial needs.
Future Outlook: Opportunities and Challenges Through 2030
The manufacturing landscape for fluorocarbon liquid coolants is expected to undergo significant transformation through 2030, driven by technological innovation, regulatory pressure, and evolving end-user demand. As of 2025, the sector is at a crossroads, balancing the robust demand from electronics, data centers, electric vehicles, and industrial cooling with increasing scrutiny over environmental impact and supply chain resilience.
One of the most notable opportunities lies in the expanding adoption of immersive cooling technologies, particularly for high-performance computing and data centers. Companies such as 3M and Chemours continue to develop next-generation fluorocarbon-based coolants with improved thermal properties, lower toxicity, and reduced environmental footprint. These coolants enable efficient heat dissipation in dense server racks and power electronics, supporting the ongoing expansion of cloud computing and artificial intelligence workloads.
However, the industry faces mounting challenges due to tightening global regulations on per- and polyfluoroalkyl substances (PFAS), many of which are used as feedstocks or intermediates in fluorocarbon coolant production. The European Union and the United States are introducing or considering restrictions on certain PFAS compounds, prompting manufacturers to accelerate research into alternative chemistries and reformulated products. Companies such as Solvay are investing in sustainable fluorochemistry, aiming to deliver coolants that meet new regulatory standards while maintaining performance.
Supply chain resilience is also top of mind following recent disruptions in raw material availability and logistics. Key producers are strengthening relationships with upstream suppliers and diversifying sourcing strategies to ensure consistent production. Daikin Industries and Arkema are actively expanding their global production footprints and investing in more localized manufacturing capabilities, particularly in Asia and North America.
Looking toward 2030, the fluorocarbon liquid coolants sector is poised for continued growth—especially in sectors requiring advanced thermal management—provided it can address regulatory compliance and environmental stewardship. Emerging opportunities include the development of ultra-low global warming potential (GWP) formulations, recycling and recovery technologies, and partnerships with industries at the forefront of electrification and digitalization. Industry leaders are expected to further collaborate with stakeholders to shape standards and practices, ensuring the long-term viability and sustainability of fluorocarbon coolants manufacturing.