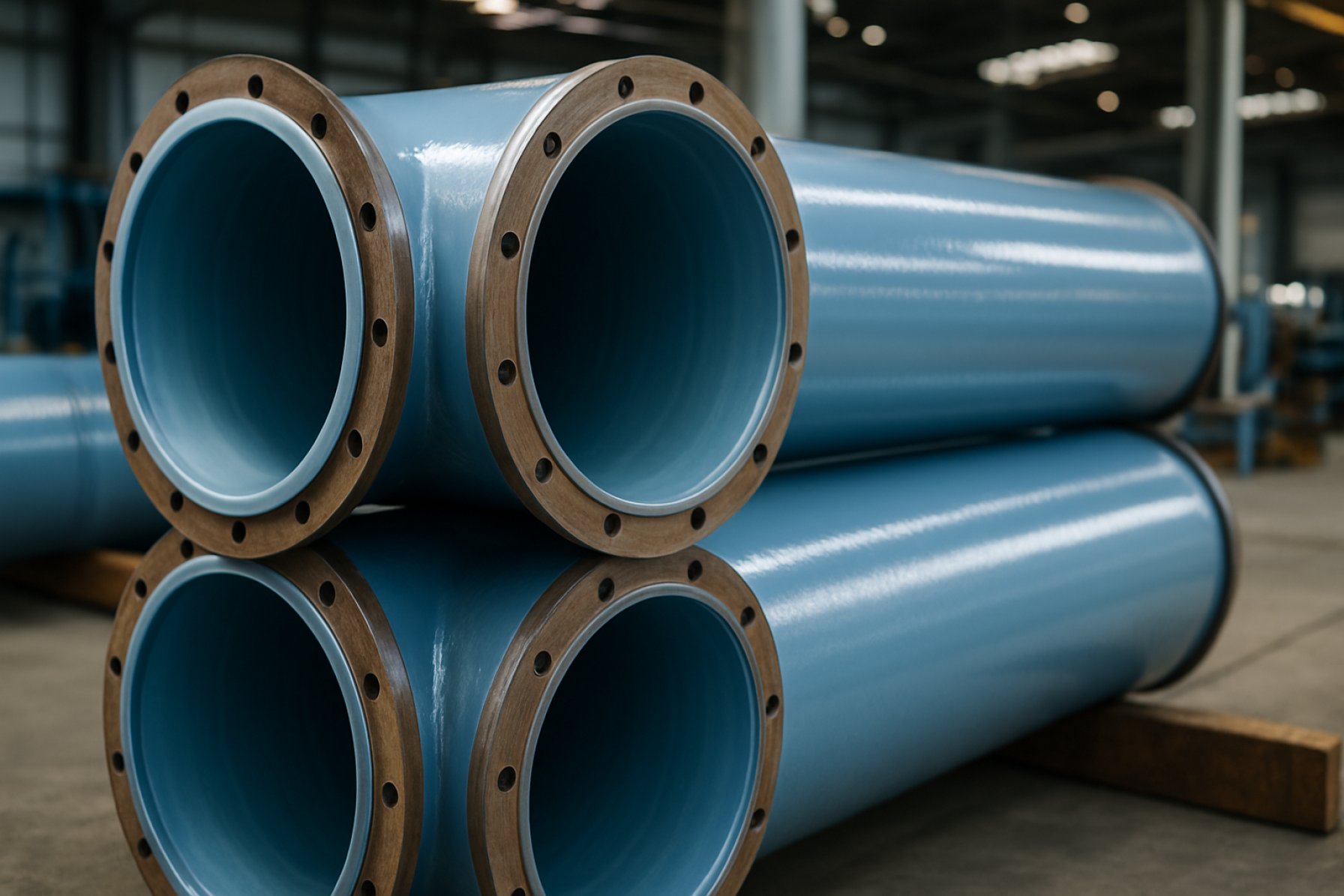
Table of Contents
- Executive Summary: Key Findings for 2025-2029
- Global Market Forecast: Growth Projections & Regional Hotspots
- Competitive Landscape: Leading Players and New Entrants
- Cutting-Edge Fluoropolymer Technologies: PTFE, FEP, PFA, and Beyond
- Application Trends: Oil & Gas, Water, Chemicals, and Energy Infrastructure
- Regulatory Environment: Standards, Compliance, and Sustainability Initiatives
- Innovation Drivers: R&D, Smart Coatings, and Digital Monitoring
- Supply Chain Dynamics: Raw Materials, Pricing, and Geopolitical Impacts
- Customer Perspectives: Adoption Barriers and Buying Criteria
- Future Outlook: Disruptive Trends and Strategic Opportunities Through 2029
- Sources & References
Executive Summary: Key Findings for 2025-2029
The period from 2025 through 2029 is poised to see robust developments and growth in the use of fluoropolymer-based pipeline coatings, driven by increasing demand for long-term corrosion protection, operational efficiency, and environmental compliance in the oil & gas, chemical processing, and water industries. Key findings for this period are outlined below.
- Rising Adoption in Oil & Gas Transmission: As global energy infrastructure faces aging assets and more aggressive transported media, operators are intensifying investments in advanced pipeline coatings. Fluoropolymers such as PTFE and PFA are increasingly specified for their superior chemical resistance and anti-fouling properties. Major industry players like AkzoNobel and 3M continue to expand their fluoropolymer-based portfolio, responding to both onshore and offshore pipeline projects.
- Environmental and Regulatory Drivers: Stricter environmental regulations regarding methane leakage, pipeline integrity, and hazardous chemical transportation are accelerating the shift toward high-performance coatings. Fluoropolymer coatings, due to their low permeability and inertness, are favored for compliance with evolving standards set by authorities such as the U.S. Environmental Protection Agency and European regulatory bodies.
- Enhanced Service Life and Maintenance Reduction: Field data from coating manufacturers suggest that pipelines protected with fluoropolymer-based coatings demonstrate significantly extended service lifespans—often exceeding 30 years in aggressive environments—while reducing the frequency and cost of maintenance interventions. Companies like DuPont and Jotun have reported increasing client adoption, particularly for subsea and sour service applications.
- Technological Advances and Market Expansion: The next several years will see continued R&D into hybrid fluoropolymer formulations and application methods, aiming to improve flexibility, reduce cure times, and lower application costs. Sherwin-Williams and Henkel are among those investing in next-generation solutions for harsh operational environments.
- Outlook: From 2025 to 2029, the market for fluoropolymer-based pipeline coatings is forecast to grow steadily, with double-digit adoption rates in high-value sectors and regions investing in new and replacement pipelines. The evolution of eco-friendly fluoropolymer chemistries is expected to further broaden application scope and regulatory acceptance, reinforcing these coatings as a critical enabler of reliable, low-impact pipeline infrastructure.
Global Market Forecast: Growth Projections & Regional Hotspots
The global market for fluoropolymer-based pipeline coatings is poised for robust growth in 2025 and the subsequent years, driven by the increasing demand for high-performance, corrosion-resistant solutions in oil, gas, chemical, and water transport sectors. Fluoropolymers, notably PTFE (polytetrafluoroethylene), FEP (fluorinated ethylene propylene), and PFA (perfluoroalkoxy alkane), are recognized for their exceptional chemical resistance, low friction properties, and durability in aggressive environments.
In 2025, the North American and Middle Eastern regions are projected to remain dominant hotspots, underpinned by ongoing investments in pipeline infrastructure and maintenance. In the United States, major players such as 3M and Chemours are expanding their fluoropolymer coating technologies to cater to both new pipeline projects and refurbishment of aging assets. The Middle East, led by countries like Saudi Arabia and the UAE, is also witnessing increased adoption of advanced coatings to support large-scale oil and gas projects amid aggressive capacity expansions by national oil companies such as Saudi Aramco.
Asia-Pacific continues to emerge as a rapidly growing region, fueled by urbanization, industrial growth, and a surge in chemical processing and water distribution networks. Regional manufacturers—including Daikin Industries and Asahi Kasei—are investing in capacity expansions and partnerships to address the growing demand for pipeline coatings, particularly in China, India, and Southeast Asia.
In terms of pipeline segments, the oil and gas industry remains the largest consumer of fluoropolymer coatings due to the need for long-term protection against corrosion, abrasion, and chemical attack. Data from Shell highlights that pipeline integrity and maintenance costs can be significantly reduced by deploying advanced fluoropolymer-based coatings, which extend operational lifespans and reduce the frequency of repairs.
Looking ahead, regulatory drivers—especially stricter environmental and safety standards—are expected to accelerate adoption. For example, the European Union’s updated directives on pipeline integrity and emission reduction are prompting operators to adopt more robust, low-emission coatings. Furthermore, innovations such as powder-based and solvent-free fluoropolymer coatings, as developed by DuPont, are gaining traction for their sustainability and application efficiency.
With ongoing R&D investments, strategic collaborations, and increasing awareness of lifecycle cost benefits, the outlook for fluoropolymer-based pipeline coatings remains highly positive. Market participants are expected to focus on scaling production, optimizing application technologies, and addressing regional nuances to capture emerging opportunities through 2025 and beyond.
Competitive Landscape: Leading Players and New Entrants
The competitive landscape for fluoropolymer-based pipeline coatings in 2025 is shaped by established global manufacturers, specialized coating suppliers, and a wave of innovation from new entrants targeting energy transition and infrastructure modernization. Fluoropolymers—primarily PTFE, FEP, and PFA—are prized for their outstanding chemical resistance, low surface energy, and durability, making them critical for pipelines in aggressive environments such as oil & gas, chemicals, and hydrogen transport.
Key industry leaders continue to assert dominance through technological advancements, expansive product portfolios, and global distribution networks. The Chemours Company remains a front-runner, leveraging its Teflon™ coatings for large-scale pipeline projects that demand extended service life and corrosion protection. 3M maintains a strong market presence with its Dyneon™ fluoropolymers, focusing on specialized coatings that withstand extreme chemical and temperature exposure.
In Europe, Arkema is a prominent supplier, with its Kynar® PVDF-based coatings increasingly specified for both new pipeline installations and rehabilitation, particularly in hydrogen and biofuel applications. Similarly, Daikin Industries, Ltd. holds significant share in the Asia-Pacific region, providing high-performance fluoropolymer coatings for both industrial and energy sector pipelines.
New entrants and niche players are actively carving out space by focusing on emerging trends. The push toward hydrogen-ready infrastructure and carbon capture systems has opened avenues for startups and specialist companies developing tailored fluoropolymer formulations with enhanced permeability resistance and sustainability profiles. For example, Solvay has expanded its Solef® PVDF line to cater to the evolving needs of the energy sector, including coatings that meet the exacting standards for hydrogen transport pipelines.
Recent years have also seen increased partnerships between coating manufacturers and pipeline operators to accelerate testing and qualification of next-generation fluoropolymer materials. This collaborative approach aims to address industry demand for coatings that offer not only superior corrosion resistance but also compliance with stricter environmental regulations and reduced lifecycle costs.
Looking ahead, the competitive landscape is expected to intensify as both legacy firms and newcomers invest in R&D to capture opportunities arising from the global shift to cleaner fuels and the rehabilitation of aging pipeline infrastructure. Supply chain resilience and the ability to meet regional regulatory requirements will likely distinguish market leaders through 2025 and beyond.
Cutting-Edge Fluoropolymer Technologies: PTFE, FEP, PFA, and Beyond
Fluoropolymer-based pipeline coatings remain at the forefront of corrosion resistance and chemical protection technologies in 2025, with leading innovations in polytetrafluoroethylene (PTFE), fluorinated ethylene propylene (FEP), perfluoroalkoxy alkane (PFA), and other advanced fluoropolymers. These materials are increasingly favored for their exceptional non-stick properties, low surface energy, and outstanding performance in harsh environments, making them essential for oil & gas, chemical processing, and emerging hydrogen pipeline applications.
Several major manufacturers have advanced their fluoropolymer coating technologies to meet the evolving demands of energy infrastructure. For example, Chemours continues to supply Teflon™ industrial coatings, including PTFE, FEP, and PFA, which are engineered to withstand aggressive chemicals, high temperatures, and mechanical wear. Their latest formulations are designed to provide reliable service in sour gas and high-pressure conditions, addressing the needs of operators pushing further into challenging environments.
Similarly, 3M offers Dyneon™ fluoropolymers, including PTFE and PFA, that are used in pipeline lining and external coatings to extend service life and reduce maintenance. Recent developments focus on improved processability and enhanced resistance to permeation by aggressive fluids, which is particularly relevant for hydrogen pipelines—an area of rapid growth as decarbonization accelerates. In 2024 and into 2025, 3M has expanded its PFA offerings to target hydrogen transport infrastructure, capitalizing on the material’s ultra-low permeability and chemical inertness.
Europe-based Solvay has also reported advances in its Solef® PVDF and Hyflon® PFA fluoropolymers for industrial coatings. Their recent efforts include fine-tuning polymer architectures to improve adhesion to steel substrates and developing coatings capable of withstanding elevated temperatures and cycling pressures seen in modern gas and multiphase pipelines.
The outlook for 2025 and beyond points to increasing adoption of fluoropolymer pipeline coatings, especially as pipeline operators seek longer lifespans, reduced environmental risk, and compatibility with hydrogen and CO2 transport. Ongoing R&D efforts are targeting novel copolymers, blends, and surface treatments to further enhance durability and lower the total cost of ownership. Manufacturers are also responding to regulatory and sustainability pressures by developing fluoropolymers with reduced environmental impact, such as lower residual fluorinated compound levels and recyclable formulations.
As global energy systems evolve, the strategic significance of cutting-edge fluoropolymer coatings will continue to grow, with industry leaders investing in production capacity and innovation to meet the rising demand for high-performance, future-proof pipeline solutions.
Application Trends: Oil & Gas, Water, Chemicals, and Energy Infrastructure
Fluoropolymer-based pipeline coatings are witnessing robust adoption across oil & gas, water, chemical, and energy infrastructure sectors, driven by their superior corrosion resistance, chemical inertness, and low surface energy. In 2025, these coatings continue to play a critical role in extending pipeline lifespans and minimizing maintenance costs, particularly in challenging environments where traditional coatings fall short.
In the oil and gas sector, major operators are prioritizing asset integrity amid increasingly aggressive extraction environments and regulatory scrutiny. Fluoropolymer linings, especially those based on PTFE and PFA, are favored for their ability to withstand sour gas, saltwater, and high-temperature hydrocarbons. Chemours, a global supplier, highlights that fluoropolymer coatings like Teflon™ have become standard for offshore and onshore pipelines exposed to corrosive substances and elevated temperatures.
Water infrastructure is another growth area, particularly as utilities upgrade aging distribution systems to address leakage and contamination. Fluoropolymer coatings offer excellent barrier properties against chemicals and biofouling, making them suitable for both potable water and wastewater applications. AGC Chemicals reports increased demand for ETFE and ECTFE-based solutions in water pipelines due to their compliance with international potable water standards and their proven performance in aggressive cleaning cycles.
In the chemicals sector, the growing diversity and aggressiveness of transported chemicals necessitate durable and inert internal coatings. Fluoropolymers prevent permeation and degradation even under extreme pH or oxidative conditions. Saint-Gobain emphasizes the deployment of PTFE-lined piping systems in chemical plants to mitigate corrosion and ensure product purity, trends expected to accelerate as chemical manufacturing globalizes and intensifies.
The energy infrastructure domain, including hydrogen and renewables, is emerging as a key arena for fluoropolymer coatings. Pipelines transporting hydrogen, ammonia, or CO2 for carbon capture benefit from the impermeability and chemical resistance of fluoropolymers, reducing risk of leaks and embrittlement. INEOS is actively developing fluoropolymer lining solutions tailored for next-generation energy carriers, anticipating rapid market expansion as decarbonization initiatives progress.
Looking ahead, continued investments in large-scale pipeline projects, sustainability-driven retrofits, and the diversification of transported fluids are poised to reinforce the relevance of fluoropolymer-based coatings. Material innovations, such as higher temperature grades and enhanced processability, are expected to further broaden application possibilities and cement their status as a preferred choice across critical infrastructure segments.
Regulatory Environment: Standards, Compliance, and Sustainability Initiatives
The regulatory environment for fluoropolymer-based pipeline coatings in 2025 is characterized by increasing stringency around safety, environmental compliance, and sustainability. As the global pipeline infrastructure modernizes and expands, regulatory agencies and industry groups are placing heightened emphasis on the use of advanced coatings that meet rigorous performance, health, and environmental standards.
A primary focus remains the compliance of coatings with international standards such as ISO 21809, which details requirements for the qualification and application of external coatings for buried or submerged pipelines. Fluoropolymer-based coatings—such as those utilizing PTFE (polytetrafluoroethylene) and PFA (perfluoroalkoxy alkane)—are recognized for their superior chemical resistance, low friction, and durability, helping pipeline operators meet or exceed such standards. Manufacturers like Chemours and AGC Chemicals continue to develop fluoropolymer systems aligned with these global benchmarks.
In 2025, compliance is also driven by stricter environmental regulations, particularly concerning the lifecycle impacts and emissions associated with fluoropolymer production and use. Regulatory authorities in North America and the European Union have introduced tighter controls on per- and polyfluoroalkyl substances (PFAS), influencing the formulation, application, and disposal of fluoropolymer coatings. For instance, the European Chemicals Agency (ECHA) has proposed further restrictions on PFAS, impacting the types of fluoropolymers that can be used and necessitating robust compliance documentation from suppliers (European Chemicals Agency).
Sustainability initiatives are increasingly shaping the regulatory landscape. Pipeline operators and coating suppliers are responding with innovations aimed at reducing environmental footprints and enhancing product recyclability. 3M, for example, has announced a commitment to exit PFAS manufacturing by the end of 2025, signaling a shift toward alternative, more sustainable chemistries for pipeline coatings. Meanwhile, companies like Sherwin-Williams are investing in the development of eco-friendlier fluoropolymer coatings with lower volatile organic compound (VOC) emissions.
Looking ahead, regulators and industry bodies are expected to continue tightening standards for pipeline coatings, emphasizing transparency, product stewardship, and end-of-life considerations. The next few years will likely see increased collaboration between manufacturers, pipeline operators, and regulators to ensure that fluoropolymer-based coatings not only deliver technical performance but also align with evolving environmental and health criteria.
Innovation Drivers: R&D, Smart Coatings, and Digital Monitoring
Innovation in fluoropolymer-based pipeline coatings continues to accelerate in 2025, driven by the pursuit of enhanced durability, environmental compliance, and operational efficiency. Research and development efforts are concentrated on next-generation fluoropolymer chemistries, the integration of smart sensing technologies, and scalable digital monitoring solutions.
A primary driver is the demand for coatings with superior resistance to corrosion, chemical attack, and extreme temperatures—operational realities in the oil, gas, and chemical sectors. Leading manufacturers such as The Chemours Company and Arkema are advancing research into modified polytetrafluoroethylene (PTFE), polyvinylidene fluoride (PVDF), and fluorinated ethylene propylene (FEP) systems. These materials offer heightened barrier properties, reduced maintenance cycles, and compatibility with aggressive transported fluids.
In parallel, the industry is witnessing the emergence of “smart coatings” that incorporate functional additives or embedded sensors. For instance, Dow is developing fluoropolymer coatings with enhanced self-healing capabilities and real-time detection of coating integrity. Such innovations support predictive maintenance by enabling operators to identify and address potential coating failures before they escalate into leaks or environmental incidents.
Digital transformation is also reshaping pipeline integrity management. The deployment of Internet of Things (IoT) devices, in conjunction with advanced fluoropolymer coatings, enables continuous remote monitoring of coating performance, temperature, and local corrosion rates. Companies like Henkel are integrating digital platforms with their coatings, offering cloud-based dashboards for real-time status reporting and historical data analysis. This approach not only improves safety and compliance but also optimizes maintenance schedules, reducing unplanned downtime and life-cycle costs.
Looking ahead to the next few years, regulatory momentum around sustainability and stricter limits on volatile organic compound (VOC) emissions are expected to push further innovation in waterborne and powder-based fluoropolymer coatings. Enhanced recyclability and reduced environmental impact will be essential features. Additionally, as pipeline infrastructure ages and expands into harsher environments (such as offshore or Arctic regions), the need for advanced coatings will only intensify. Direct collaborations between coating manufacturers, pipeline operators, and sensor technology providers will likely become more pronounced, accelerating the commercialization of integrated smart coating solutions.
Supply Chain Dynamics: Raw Materials, Pricing, and Geopolitical Impacts
The supply chain for fluoropolymer-based pipeline coatings in 2025 is characterized by heightened complexity, largely driven by raw material availability, fluctuating pricing, and ongoing geopolitical developments. The core ingredients—fluoropolymers such as polytetrafluoroethylene (PTFE), fluorinated ethylene propylene (FEP), and perfluoroalkoxy alkane (PFA)—are derived from fluorspar and other specialty chemicals. The extraction and processing of fluorspar, predominantly concentrated in China, Mongolia, and South Africa, have faced disruptions due to export controls and regulatory changes. In early 2025, China’s continued focus on environmental compliance and export quotas has contributed to sporadic shortages and price volatility for fluorochemical precursors, directly impacting manufacturers of pipeline coatings such as Chemours and Daikin Industries.
Pricing trends for fluoropolymer-based coatings mirror these supply chain bottlenecks. Since late 2023, average contract prices for PTFE and related polymers have remained elevated, with marginal surges recorded in Q1 2025 due to logistical constraints at Asian ports and sustained energy costs. Major producers, including 3M, have publicly noted increased operational expenditures tied to raw material acquisition and regulatory compliance, which are reflected in their pricing to downstream pipeline coating formulators.
Geopolitical impacts continue to play a crucial role. The ongoing realignment of global supply chains—prompted by trade tensions between major economic blocs—has encouraged North American and European coating manufacturers to seek alternative suppliers and invest in local production capacity. For example, Solvay has expanded its fluoropolymer production footprint in Europe to mitigate import risks. Simultaneously, multinational pipeline operators are increasingly requiring full traceability of coating materials, in response to both regulatory mandates (e.g., PFAS restrictions in the EU) and sustainability goals.
Looking ahead to the next few years, industry outlooks suggest persistent tightness in fluorspar and fluoropolymer markets, with pricing expected to remain above pre-pandemic averages. Efforts are underway to diversify sourcing, recycle fluoropolymer scrap, and develop next-generation sustainable alternatives, but significant shifts in supply chain resilience are projected only after 2026. Stakeholders across the pipeline sector—from raw material miners to coating applicators—are expected to closely monitor geopolitical developments, environmental regulations, and technological innovations that could reshape supply chain dynamics for fluoropolymer-based pipeline coatings.
Customer Perspectives: Adoption Barriers and Buying Criteria
In 2025, the adoption of fluoropolymer-based pipeline coatings continues to be shaped by a combination of technical, economic, and regulatory factors from the customer’s perspective. End-users—primarily in the oil & gas, chemical processing, and water industries—evaluate these coatings based on distinct performance requirements and operational priorities. While the advanced properties of fluoropolymers, such as their exceptional corrosion resistance, low surface energy, and thermal stability, make them attractive for pipeline applications, several barriers and buying criteria influence market uptake.
Adoption Barriers
- Cost Sensitivity: Fluoropolymer coatings, including PTFE, FEP, and PFA, are significantly more expensive than traditional epoxy or polyurethane coatings. This cost differential is a primary barrier, especially for projects with tight capital expenditure constraints. The return on investment is often assessed over decades of service life, making it difficult for customers to justify the upfront cost unless severe corrosion or fouling is anticipated (Chemours).
- Technical Complexity: Application of fluoropolymer coatings can require specialized surface preparation, controlled environments, and highly skilled applicators. This complexity can deter customers who lack access to qualified contractors or who seek rapid project turnaround (AGC Chemicals).
- Supply Chain Limitations: In 2025, some fluoropolymer raw materials, especially those based on specific perfluorinated compounds, face supply constraints due to ongoing regulatory scrutiny and tightening environmental standards around PFAS chemicals. This has led to sporadic availability and uncertainty in project timelines (Dow).
Buying Criteria
- Performance in Aggressive Environments: Customers prioritize coatings that can withstand highly corrosive fluids, high temperatures, or abrasive slurries. Fluoropolymer coatings are often selected for pipelines carrying sour gas, aggressive chemicals, or hot water, where traditional coatings would rapidly degrade (3M).
- Lifecycle Cost: Decision-makers increasingly assess the full lifecycle costs, including reduced maintenance, longer intervals between recoating, and minimized downtime. The prospect of extending pipeline service life by decades is a compelling argument for premium coatings, especially in remote or hard-to-access installations (Chemours).
- Compliance and Environmental Impact: In response to evolving global regulations on PFAS and other persistent chemicals, customers now demand greater transparency on the environmental profile of coatings. Suppliers offering alternatives with reduced environmental footprint or clear documentation of regulatory compliance are favored (AGC Chemicals).
Looking ahead, as regulatory pressures on PFAS chemistry intensify and raw material costs remain volatile, customer adoption decisions in the next few years are expected to hinge on demonstrable lifecycle value, supplier transparency, and supply chain resilience. Coating manufacturers investing in next-generation, compliant fluoropolymer chemistries and robust technical support will be better positioned to address customer concerns and drive wider adoption.
Future Outlook: Disruptive Trends and Strategic Opportunities Through 2029
Fluoropolymer-based pipeline coatings are poised for significant evolution through 2029, driven by increasing demand for corrosion resistance, regulatory pressures, and advancements in material science. As of 2025, several disruptive trends are shaping the market outlook, with major industry players investing in research and strategic capacity expansions.
Environmental regulations and the growing imperative to reduce pipeline maintenance costs are accelerating the adoption of high-performance coatings. Fluoropolymer coatings, such as those utilizing polytetrafluoroethylene (PTFE), ethylene tetrafluoroethylene (ETFE), and fluorinated ethylene propylene (FEP), offer superior chemical and thermal resistance. Their low surface energy properties are particularly valued for mitigating fouling and extending asset life in aggressive environments—critical for sectors like oil & gas, chemicals, and water transmission.
Key manufacturers are expanding their portfolios to address these evolving needs. For example, The Chemours Company continues to innovate with its Teflon™ industrial coatings, focusing on formulations that improve application efficiency and environmental safety. Similarly, 3M has developed next-generation fluoropolymer coatings that integrate advanced dispersion technologies, enabling thinner, more consistent layers with enhanced performance.
New application technologies are also gaining traction. Powder coating processes, which reduce volatile organic compound (VOC) emissions, are being adopted by suppliers aiming to comply with stricter environmental regulations in North America, Europe, and parts of Asia. AkzoNobel and PPG Industries have both introduced powder-based fluoropolymer solutions designed for pipeline protection, with a focus on improved environmental profiles and operational efficiency.
From a strategic perspective, partnerships between coating manufacturers and pipeline operators are intensifying. These collaborations facilitate the customization of coating systems to specific operational conditions, such as high-pressure or sour gas exposure, while supporting predictive maintenance strategies via digital monitoring and data integration. Companies like Sherwin-Williams are investing in digital platforms that allow real-time tracking of coating integrity, helping pipeline operators optimize maintenance intervals and reduce total lifecycle costs.
Looking ahead to 2029, the sector is expected to see further innovation in fluoropolymer chemistries, with ongoing research into perfluoropolyether (PFPE) and hybrid fluoropolymer systems for enhanced durability and safety. Sustainability will remain a central theme, with manufacturers exploring bio-based feedstocks and recycling initiatives to address increasing scrutiny of fluoropolymer production impacts. Overall, the strategic adoption of advanced fluoropolymer coatings is set to play a pivotal role in extending pipeline asset life, minimizing environmental risk, and supporting the industry’s transition toward smarter, more sustainable infrastructure.