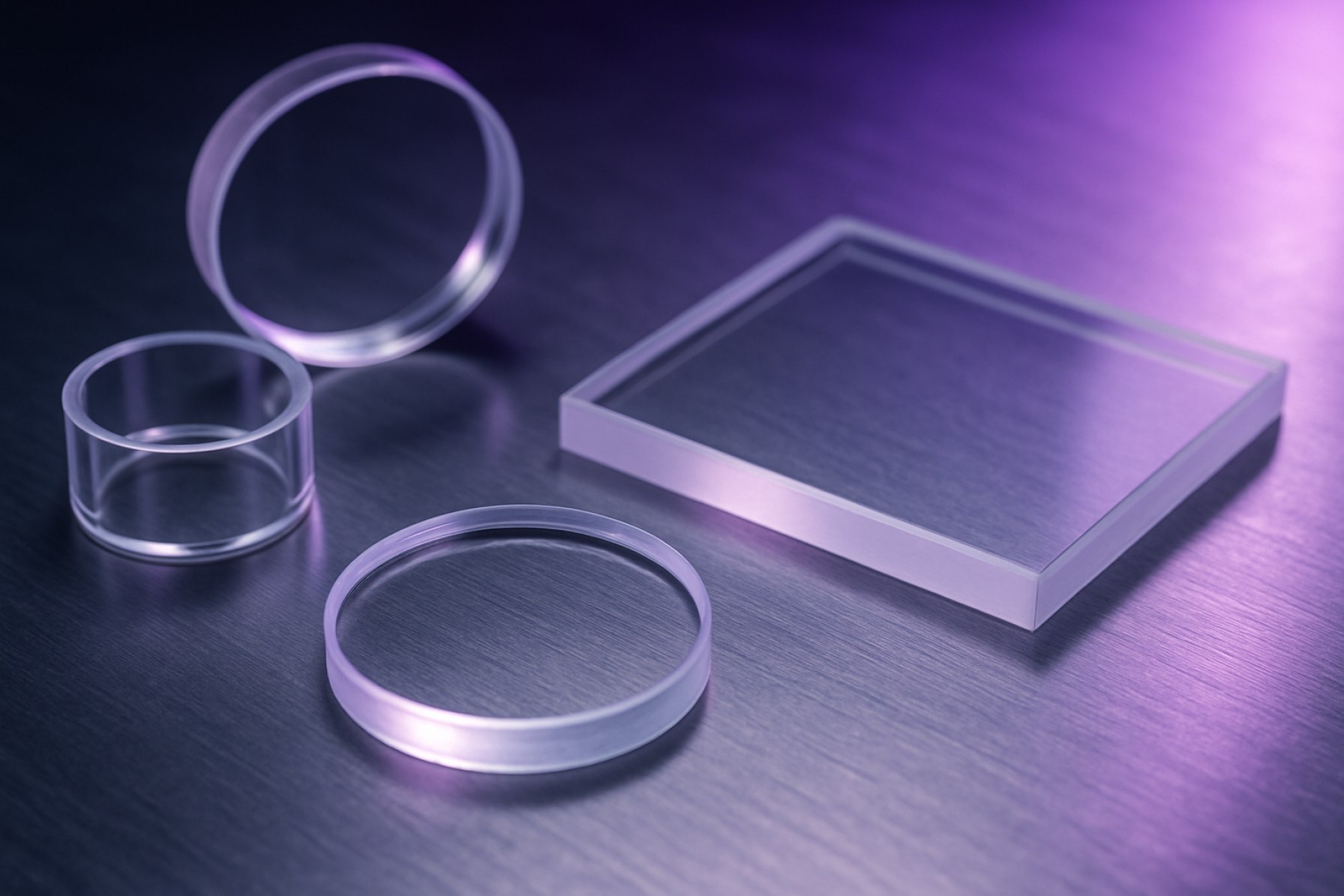
Table of Contents
- Executive Summary: Key Findings & 2025 Outlook
- Market Drivers: UV Laser Applications Fueling Quartz Window Demand
- Competitive Landscape: Leading Manufacturers & Technology Innovators
- Manufacturing Techniques: Precision Advances in Quartz Window Production
- Materials Innovation: Next-Gen Quartz for Enhanced UV Transmission
- Quality Standards & Certification: Meeting Rigorous UV Laser Specs
- Regional Analysis: Growth Hotspots & Global Supply Chains
- Market Forecasts: Revenue, Volume, and Growth Projections to 2030
- Emerging Applications: UV Lasers in Semiconductors, Healthcare, and More
- Future Outlook: Disruptive Tech, Sustainability, and Long-Term Trends
- Sources & References
Executive Summary: Key Findings & 2025 Outlook
The quartz window manufacturing sector for ultraviolet (UV) laser applications is poised for steady growth in 2025, driven by surging demand from semiconductor lithography, medical devices, and advanced scientific instrumentation. As UV laser systems, particularly excimer and solid-state lasers, become increasingly integral to next-generation manufacturing and research, the need for high-purity, defect-free synthetic quartz windows has intensified. Leading suppliers are expanding capacity and refining production methods to address both technical and volume requirements.
Key findings indicate that synthetic fused silica remains the dominant material for UV laser windows, owing to its exceptional transmission in the deep UV spectrum and outstanding resistance to laser-induced damage. Major manufacturers such as Heraeus and Corning are investing in improved melting and refining processes to minimize inclusions and hydroxyl (OH) content, which are critical for long-term window durability under high-power UV exposure. Heraeus reports ongoing development of UV-grade fused silica with even lower absorption and higher homogeneity, tailored for DUV (deep ultraviolet) and EUV (extreme ultraviolet) laser systems.
On the supply side, the industry is witnessing increased automation and adoption of precision metrology for thickness, surface flatness, and parallelism. Gooch & Housego and AGC have both emphasized the integration of advanced quality control systems to ensure each window meets stringent requirements for laser optics. These advancements have become especially relevant as customers in semiconductor and medical sectors demand tighter tolerances and higher consistency for scaled manufacturing.
Looking ahead, the outlook for 2025 and the subsequent few years remains robust. The global expansion of chip fabrication plants and the proliferation of UV-based sterilization technologies are expected to drive further demand for precision quartz windows. Market participants are responding by scaling capacity and introducing new product lines targeting higher laser powers and shorter UV wavelengths. For example, Corning has announced plans to enhance its quartz processing capabilities to support anticipated growth in EUV lithography.
In summary, the quartz window manufacturing sector for UV lasers is set for continued innovation and expansion, underpinned by advancements in material purity, manufacturing automation, and alignment with evolving laser technology requirements.
Market Drivers: UV Laser Applications Fueling Quartz Window Demand
The demand for high-quality quartz windows is experiencing significant growth, primarily driven by the expanding use of ultraviolet (UV) lasers across diverse industries. In 2025 and the immediate years ahead, several market forces are shaping this trend, with quartz window manufacturers ramping up production capabilities and advancing fabrication techniques to meet increasingly stringent specifications.
Key drivers include the proliferation of UV laser applications in semiconductor manufacturing, medical diagnostics, materials processing, and advanced research. The semiconductor sector, in particular, relies heavily on deep ultraviolet (DUV) and extreme ultraviolet (EUV) lithography, processes that require defect-free, high-transmittance quartz windows for critical optical components. Leading equipment manufacturers such as ASML continue to expand their EUV lithography system deployments, fueling demand for precision quartz optics.
In the medical field, UV lasers are increasingly utilized for DNA sequencing, cell sorting, and sterilization applications. Devices such as flow cytometers and UV disinfection systems depend on optical windows with exceptional UV transmission and resistance to photodegradation. Specialty glass producers like Heraeus and Corning Incorporated are addressing this demand by developing synthetic fused silica windows tailored for high-power UV environments.
Manufacturers are also responding to the needs of scientific research, including synchrotron and laser spectroscopy facilities, where the integrity of quartz windows is vital for accurate measurements in the VUV and EUV ranges. Recent advancements in material purity, surface polishing, and coating technologies—adopted by suppliers such as Hellma GmbH & Co. KG and Thorlabs—enable the production of windows with minimal absorption and scattering losses.
Looking ahead, the outlook for quartz window manufacturing remains robust. Growth is anticipated as next-generation UV laser tools require even higher performance standards, pushing manufacturers to invest in automation, metrology, and process control. Strategic collaborations between quartz fabricators and laser system OEMs are expected to accelerate innovation in window design, coating, and lifetime optimization. As the UV laser market evolves, the role of precision quartz windows will become increasingly central, underpinning advances in both industrial and scientific applications.
Competitive Landscape: Leading Manufacturers & Technology Innovators
The competitive landscape for quartz window manufacturing in the ultraviolet (UV) laser sector is evolving rapidly, driven by escalating demand for precision optics in semiconductor lithography, medical diagnostics, and industrial laser systems. In 2025, leading manufacturers are emphasizing both technological innovation and capacity expansion, as the industry responds to stricter UV transmission, durability, and contamination control requirements.
Key global players such as Heraeus and Corning Incorporated continue to dominate the high-purity fused silica segment, leveraging proprietary melting and refining processes to achieve exceptional UV transparency and minimal absorption losses at deep-UV wavelengths. Both companies have announced recent investments in ultra-clean manufacturing environments and automated quality control to meet the stringent demands of UV laser applications, particularly for excimer and solid-state lasers operating below 300 nm.
Japanese manufacturers, notably Shin-Etsu Chemical Co., Ltd. and Tosoh Corporation, are expanding their global footprint by ramping up output of synthetic fused silica, renowned for its low hydroxyl (OH) content and high resistance to UV-induced solarization. These characteristics are critical for the longevity and optical clarity of windows used in high-peak-power laser systems and advanced photolithography tools.
Specialty optics firms such as Hellma GmbH & Co. KG and UQG Optics are strengthening their positions by providing custom-shaped and coated quartz windows tailored for niche UV laser applications, including laser-induced fluorescence and life sciences instrumentation. These suppliers are investing in advanced polishing, anti-reflective coating, and contamination control technologies to deliver optics with high damage thresholds and extended operational lifespans.
Looking ahead to the next few years, strategic alliances and supply chain localization are expected to intensify, as regional governments incentivize domestic production of critical optical components. For example, several manufacturers are establishing or expanding facilities in North America and Europe to reduce reliance on Asian supply chains for semiconductor and defense-related UV laser optics. Additionally, the integration of Industry 4.0 practices—such as in-line metrology and AI-driven defect detection—will be a key competitive differentiator, enabling real-time assurance of quality and faster response to evolving customer specifications.
Overall, the quartz window manufacturing sector for UV lasers in 2025 is marked by vigorous investment in material purity, precision processing, and supply chain resilience, setting the stage for continued innovation and heightened global competition in the years ahead.
Manufacturing Techniques: Precision Advances in Quartz Window Production
The manufacturing of quartz windows for ultraviolet (UV) lasers has undergone significant advancements entering 2025, with a focus on precision, purity, and scalability. The demand for UV laser applications in semiconductor lithography, scientific instrumentation, and medical devices continues to drive innovation in quartz window fabrication. Leading manufacturers are prioritizing improvements in material quality, surface finishing, and contamination control to meet the stringent requirements of high-power, short-wavelength laser systems.
One of the central trends is the adoption of advanced synthetic fused silica production methods, such as flame hydrolysis and chemical vapor deposition (CVD), which yield extremely low hydroxyl (OH) content and superior optical homogeneity. Companies like Heraeus and Corning offer high-purity fused silica specifically engineered for UV transmission, minimizing absorption losses below 200 nm. This is critical for excimer and deep-UV laser applications, where material impurities directly impact window lifetime and system performance.
Precision surface finishing has also seen notable progress. Current industry standards now routinely achieve surface flatness better than λ/10 at 633 nm and surface roughness below 1 nm RMS, as demonstrated by manufacturers such as Hellma and Meller Optics. These tolerances reduce scattering and laser-induced damage, two major concerns in high-power UV laser environments. Computer-controlled polishing, sub-aperture finishing, and advanced metrology tools are increasingly integrated into production lines to deliver consistent, high-precision optics.
Another area of focus is contamination control during manufacturing and packaging. Particle and organic contamination can degrade UV window performance, especially under high fluence. To combat this, manufacturers like Ohara Corporation are investing in cleanroom facilities and automated handling systems, alongside rigorous inspection protocols to ensure defect-free surfaces.
- Material innovations: Enhanced synthetic fused silica and improved CVD methods target lower impurity levels for longer window lifetimes.
- Surface finishing: Advances in polishing and metrology enable sub-nanometer surface roughness and high flatness, reducing scatter and absorption.
- Contamination control: Cleanroom processing and automated inspection mitigate risks of surface contamination and defects.
Looking forward into the next few years, the sector anticipates further integration of AI-driven process optimization, improved real-time metrology, and new coating technologies to extend UV window durability—particularly for wavelengths below 200 nm. As UV laser applications proliferate in emerging fields such as quantum computing and advanced photolithography, the precision and reliability of quartz window manufacturing are expected to remain a critical focus for industry leaders.
Materials Innovation: Next-Gen Quartz for Enhanced UV Transmission
In 2025, the quartz window manufacturing sector for ultraviolet (UV) lasers is witnessing a surge in materials innovation aimed at maximizing UV transmission, durability, and resistance to laser-induced damage. Synthetic fused silica, prized for its extremely low metal impurity content and superior homogeneity, remains the gold standard for high-performance UV laser optics. Leading manufacturers are now pushing the boundaries of material purity and process control, recognizing that even trace contaminants can lead to optical absorption, fluorescence, or premature window failure under high-energy UV exposure.
Recent advances by major suppliers such as Heraeus and Corning Incorporated have focused on refining synthetic quartz production, employing advanced chemical vapor deposition (CVD) and flame hydrolysis methods. These approaches enable the manufacture of ultra-high purity windows tailored for excimer lasers (e.g., KrF at 248 nm, ArF at 193 nm) and deep UV (DUV) applications. For instance, Heraeus has introduced grades like Suprasil 3001 and 312, which offer exceptionally low hydroxyl (OH) content and minimal UV absorption—a crucial attribute for high-repetition-rate laser systems in semiconductor lithography and microfabrication.
Another focal point is the mitigation of laser-induced damage threshold (LIDT) issues. Manufacturers are leveraging tighter control over bubble, inclusion, and striae content during the melt process, alongside advanced annealing cycles to reduce internal stresses. Hellma, for example, is optimizing surface finishing and polishing techniques to minimize surface roughness and subsurface damage, both of which can trigger premature failure under UV irradiation.
Looking ahead, the next few years are poised to see broader adoption of novel synthetic routes and doping strategies to further suppress color center formation and enhance photostability. Some manufacturers are exploring the integration of UV-grade quartz with anti-reflective and damage-resistant coatings tailored specifically for UV wavelengths, as seen in the offerings from USHIO INC.. These multilayer coatings not only improve transmission but also prolong operational lifetimes in harsh laser environments.
With the proliferation of UV laser technologies in precision manufacturing, medical instrumentation, and analytical devices, the demand for next-generation quartz windows is set to intensify. Industry leaders are responding with vertically integrated supply chains and expanded production capabilities, anticipating tighter specifications for UV transparency, robustness, and cost-efficiency as performance requirements escalate through the remainder of the decade.
Quality Standards & Certification: Meeting Rigorous UV Laser Specs
The manufacturing of quartz windows for ultraviolet (UV) lasers in 2025 is characterized by increasingly stringent quality standards and certification requirements, driven by the growing complexity and performance demands of advanced photonics, semiconductor, and medical applications. As UV laser systems push toward shorter wavelengths and higher powers, quartz window manufacturers are compelled to adopt rigorous protocols to ensure optical clarity, durability, and minimal contamination.
Leading manufacturers, such as Heraeus, outline strict criteria for material purity, surface flatness, parallelism, and homogeneity. Fused silica and high-purity synthetic quartz remain the preferred materials due to their exceptional UV transmittance and low absorption, particularly in the deep-UV region (below 200 nm). Heraeus specifies that their quartz windows must meet surface quality standards such as 10-5 scratch-dig (per MIL-PRF-13830B), and flatness tolerances as tight as λ/10 at 633 nm, ensuring minimal wavefront distortion for high-precision laser applications.
Certification protocols increasingly include ISO 9001:2015 for quality management systems and ISO 10110 for optical component specifications. Global suppliers like Hellma and Corning emphasize compliance with these international standards to assure customers of repeatable, traceable manufacturing processes and verified optical properties. Lot-specific material traceability, along with advanced metrology (e.g., interferometric surface mapping, laser-induced fluorescence screening), are now standard practices in top-tier facilities.
There is a notable trend toward collaborative qualification programs with UV laser OEMs, wherein quartz window suppliers undergo joint testing programs to validate window performance under real-world operational conditions. For example, USHIO Inc. details their close partnerships with laser system integrators to ensure component lifetimes, UV transmission stability, and laser-induced damage thresholds (LIDT) meet or exceed industry benchmarks.
Looking ahead to the next several years, the outlook for quartz window manufacturing in the UV laser sector points to even tighter quality control, particularly as applications in semiconductor lithography and advanced medical diagnostics push for higher cleanliness levels and resistance to photochemical degradation. Expect an uptick in automated inspection, expanded certification (including environmental and sustainability standards), and the introduction of advanced coatings to further enhance UV durability and minimize surface contamination. These developments will be critical for maintaining competitiveness and meeting the rigorous demands of next-generation UV laser systems.
Regional Analysis: Growth Hotspots & Global Supply Chains
The global supply chain for quartz window manufacturing, specifically for ultraviolet (UV) laser applications, is experiencing notable regional shifts and growth patterns as of 2025. The demand for high-purity, UV-grade fused silica windows has increased, driven by the proliferation of photonics, semiconductor lithography, and advanced medical and scientific instrumentation. The industry remains highly concentrated, with key manufacturing clusters in the United States, Europe, and East Asia, particularly Japan and China.
The United States continues to be a significant hotspot, leveraging its longstanding expertise in specialty glass and advanced materials. Major players such as Heraeus and Corning Incorporated maintain robust production capabilities for high-purity fused silica, essential for UV laser windows. These companies benefit from proximity to technology customers in photolithography, defense, and medical device manufacturing, as well as established supply chains for raw materials and precision fabrication.
In Europe, Germany remains a focal point with companies like Heraeus investing in R&D and production of laser optics, including UV windows. Their vertically integrated operations ensure quality control from raw silica to finished window, supporting Europe’s growing photonics and semiconductor sectors.
East Asia, and particularly Japan, has consolidated its position as a leader in specialty quartz manufacturing. Firms such as HOYA Corporation and Tosoh Corporation supply both domestic and international demand for UV laser-grade quartz components. Japan’s dominance is underpinned by strong ties to the global semiconductor industry as well as advances in metrology and analytical equipment. China, meanwhile, has rapidly expanded its capacity, with companies like China Quartz Glass Co., Ltd. increasing both quality and output. This expansion is supported by government initiatives to localize semiconductor supply chains and reduce dependence on imports.
Looking ahead, supply chains are expected to become more resilient and regionally diversified. Recent geopolitical and logistical challenges have encouraged manufacturers to develop dual-sourcing strategies and invest in localized production, particularly in North America and Southeast Asia. Automation and precision manufacturing technologies are being adopted to meet the stringent optical and purity requirements of UV laser applications. The outlook for the next few years suggests continued growth in Asia, with incremental capacity additions in the U.S. and Europe to support critical industries and innovation hubs. Collaboration between material suppliers and end-users is anticipated to intensify, fostering advancements in UV window performance and reliability.
Market Forecasts: Revenue, Volume, and Growth Projections to 2030
The market for quartz window manufacturing specifically tailored for ultraviolet (UV) lasers is positioned for significant growth through 2030, driven by expanding applications in semiconductor lithography, advanced medical devices, and industrial laser systems. As of 2025, leading manufacturers report robust demand, particularly for high-purity fused silica windows capable of withstanding the high photon energies and strict transmission requirements of UV laser systems.
Industry data from Heraeus, a major supplier of synthetic quartz, indicates a steady increase in production volumes of UV-grade quartz windows, with a focus on components for excimer lasers in the 193 nm and 248 nm wavelength ranges. This trend is echoed by Corning Incorporated, which notes rising orders from semiconductor equipment manufacturers investing in extreme ultraviolet (EUV) and deep ultraviolet (DUV) lithography platforms.
In terms of revenue, the industry is witnessing mid- to high-single-digit compound annual growth rates (CAGR) through the current decade. Hellma highlights growing adoption of precision quartz optics in life sciences and laser-based analytical instrumentation, sectors expected to drive incremental growth through 2030. The expansion of high-volume manufacturing lines and the trend toward miniaturized, high-power UV laser sources are pushing quartz window suppliers to invest in advanced fabrication technologies, including tighter surface quality tolerances and enhanced anti-reflective coatings.
Volume projections suggest that unit shipments of UV-grade quartz windows will increase in line with the global rollout of new photonics manufacturing hubs, especially in Asia-Pacific and North America. Shin-Etsu Quartz and Momentive Performance Materials report expanding production capacities in response to multi-year supply agreements with laser system integrators.
Looking ahead, the outlook for the quartz window market in UV laser applications remains positive, with innovation in material purity and window geometry expected to unlock further growth opportunities. Collaborative initiatives between quartz suppliers and laser equipment OEMs are likely to accelerate the introduction of next-generation materials, ensuring that the sector sustains its upward trajectory toward 2030.
Emerging Applications: UV Lasers in Semiconductors, Healthcare, and More
The demand for high-purity quartz windows tailored for ultraviolet (UV) laser applications is intensifying as industries such as semiconductors, healthcare, and advanced manufacturing increasingly deploy UV lasers. Quartz windows play a vital role as optical interfaces, enabling precise energy delivery while protecting sensitive internal laser components from contamination and damage. In 2025 and the immediate future, manufacturers are focusing on innovations in material purity, surface finishing, and dimensional tolerances to meet the stringent requirements of next-generation UV laser systems.
In the semiconductor sector, the transition to extreme ultraviolet (EUV) lithography for sub-7nm node fabrication has elevated the demand for ultrapure quartz windows capable of transmitting wavelengths below 200 nm with minimal absorption and defects. Companies such as Heraeus and Corning Incorporated are leveraging advanced fused silica and synthetic quartz manufacturing technologies, including high-temperature fusion and precision polishing, to achieve optical homogeneity and surface roughness at the sub-nanometer level. These advancements directly respond to the semiconductor industry’s call for durable, contamination-free optical components that can withstand intense UV radiation and repeated cleaning cycles.
In healthcare, the adoption of UV-C lasers for disinfection, phototherapy, and diagnostic imaging has prompted manufacturers to develop quartz windows with enhanced resistance to solarization and photochemical degradation. Hamamatsu Photonics continues to improve the transmission stability of its synthetic quartz windows for deep UV exposure, addressing the reliability needs of medical and laboratory equipment. Manufacturers are also introducing anti-reflective coatings and custom geometries to optimize light throughput and minimize stray reflections in sensitive biological environments.
The outlook for 2025 and beyond indicates accelerated collaboration between quartz manufacturers and UV laser system integrators. Companies such as MILTON ROY and Hellma are expanding their portfolios of custom-shaped and application-specific quartz windows, supporting the proliferation of UV lasers in areas like microelectronics, materials processing, and biotechnology. With the anticipated growth in quantum computing and advanced photonics, the industry is expected to invest further in process automation, quality control, and novel material formulations to keep pace with evolving laser specifications and operational environments.
- Semiconductor lithography: Demand for sub-200 nm transmission, extreme surface quality.
- Healthcare devices: Focus on durability, anti-solarization, and biocompatibility.
- Materials processing and research: Custom shapes, coatings, and rapid prototyping.
Overall, the quartz window manufacturing sector is poised for robust growth and technical advancement, driven by the relentless evolution of UV laser applications across high-impact industries.
Future Outlook: Disruptive Tech, Sustainability, and Long-Term Trends
The future of quartz window manufacturing for ultraviolet (UV) lasers is being shaped by advanced material processing technologies, a growing focus on sustainability, and the increasing demands from sectors such as semiconductor fabrication, medical instrumentation, and advanced scientific research. As of 2025, manufacturers are responding to the need for higher purity, greater transmission efficiency, and improved durability of quartz windows that operate in the deep UV (DUV) and vacuum UV (VUV) ranges.
One disruptive technology influencing this sector is the adoption of advanced synthetic quartz production methods, such as flame hydrolysis and vapor-phase axial deposition. These approaches enable the creation of ultra-pure fused silica substrates with minimal hydroxyl (OH-) content, which is key for minimizing absorption and extending window lifespan under high-intensity UV exposure. Leading manufacturers, such as Heraeus and Corning Incorporated, are investing in scaling up these technologies for tighter dimensional tolerances and improved surface qualities, which in turn reduce scattering and losses in high-precision UV laser applications.
Sustainability is becoming an explicit priority. The energy-intensive processes traditionally used in quartz glass production are under scrutiny for their carbon footprint. Efforts to reduce energy consumption and implement closed-loop recycling of quartz scrap are underway at facilities operated by companies like Momentive, which highlights its initiatives towards more sustainable fused quartz manufacturing. Additionally, there is growing interest in extending the service life of quartz windows, both through improved material properties and advanced anti-reflective and protective coatings, decreasing the frequency of replacement and waste.
Looking ahead, the demand for defect-free, large-diameter quartz windows is expected to rise, particularly driven by the next generation of extreme UV (EUV) and DUV lithography systems for semiconductor fabrication. This puts pressure on suppliers to continuously innovate in contamination control and process automation. Industry collaborations, such as those fostered by SEMI, are likely to accelerate knowledge sharing and standard setting for quality and sustainability benchmarks.
From 2025 onward, the quartz window manufacturing industry is poised for steady growth, underpinned by disruptive advances in synthetic quartz production, a commitment to greener practices, and the unrelenting progress of UV laser technology. Companies at the forefront are those integrating automation, data-driven process control, and sustainability into their quartz window fabrication pipelines, ensuring they meet the optical and environmental requirements of tomorrow’s UV laser applications.