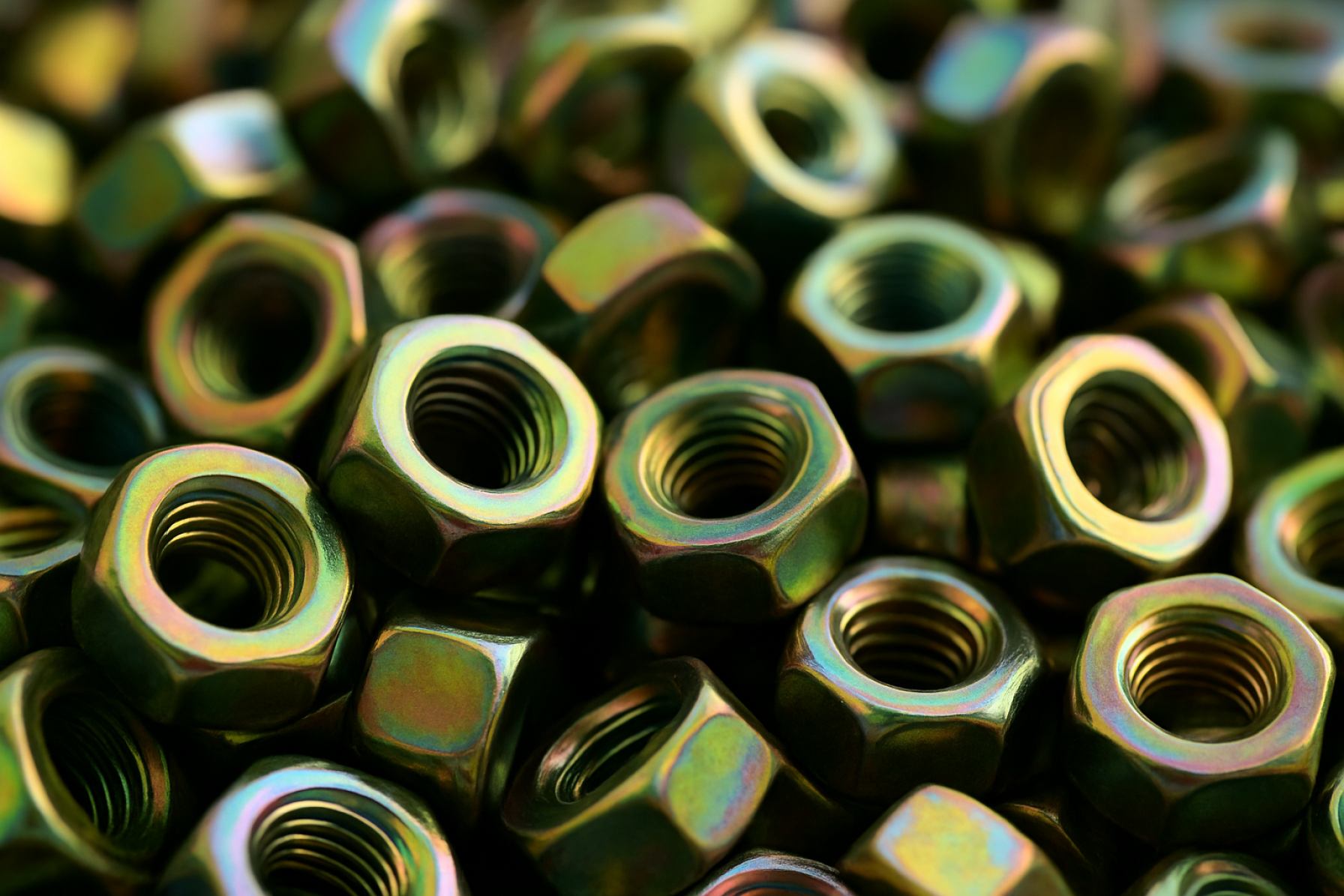
Table of Contents
- Executive Summary: Key 2025-2029 Trends in Zinc-Nickel Layered Coatings
- Technology Overview: Current State and Next-Gen Engineering Advances
- Market Size & Forecast: Global and Regional Demand Through 2029
- Competitive Landscape: Leading Companies & Strategic Partnerships
- Automotive & Aerospace Demand: Sector-Specific Growth Drivers
- Innovation Pipeline: Patents, R&D, and Emerging Processes
- Sustainability & Regulatory Shifts: Environmental and Compliance Factors
- Supply Chain & Raw Material Challenges
- Customer Adoption: OEM, Tier 1, and Aftermarket Perspectives
- Future Outlook: Disruptive Technologies and Strategic Recommendations
- Sources & References
Executive Summary: Key 2025-2029 Trends in Zinc-Nickel Layered Coatings
The engineering of zinc-nickel layered coatings is poised for significant evolution between 2025 and 2029, as industrial sectors intensify their focus on enhanced corrosion resistance, environmental compliance, and cost efficiency. Zinc-nickel coatings, recognized for their superior corrosion protection—particularly in automotive, aerospace, and heavy machinery applications—are expected to experience robust demand as industries transition from traditional pure zinc or cadmium-based alternatives.
Recent years have seen leading manufacturers, such as MacDermid Alpha and Atotech, driving innovations in alloy composition and deposition techniques. These firms are advancing alkaline and acidic zinc-nickel electroplating technologies to improve uniformity, reduce hydrogen embrittlement, and meet tighter global regulatory standards. Notably, the push towards hexavalent chromium-free passivations, in alignment with REACH and RoHS directives, is reshaping coating formulations and post-treatment processes.
Data from the sector indicates a clear shift to high-nickel content coatings (12–15% Ni), which deliver up to 10 times the corrosion resistance of standard zinc coatings in salt spray testing. This is especially critical for automotive fasteners, chassis components, and electrical connectors, where manufacturers such as Automotive Racing Products and Norm Fasteners are increasingly specifying zinc-nickel for both OEM and aftermarket parts.
Automation and digitalization are also set to transform the zinc-nickel coatings landscape. Major plating line providers like AWA are incorporating advanced process controls, real-time quality monitoring, and integrated data analytics. These technological enhancements are expected to yield higher throughput, reduced waste, and greater traceability—key demands from automotive and electronics OEMs seeking to optimize lifecycle costs and quality assurance.
Looking ahead to 2025-2029, market outlook remains robust. The transition to electric vehicles and renewable energy systems will further drive requirements for reliable corrosion protection in harsh environments. Simultaneously, global supply chain pressures are incentivizing localized, flexible coating operations, with companies in Europe, North America, and Asia-Pacific expanding capacity and regional partnerships.
In summary, the next few years will see zinc-nickel layered coatings engineering characterized by regulatory-driven innovation, increased adoption of high-performance alloys, and the integration of smart manufacturing technologies. Stakeholders across the value chain—from chemical suppliers and coating service providers to end-users in automotive and industrial sectors—are poised to benefit from these advancements as the industry pivots toward sustainability and operational excellence.
Technology Overview: Current State and Next-Gen Engineering Advances
Zinc-nickel layered coatings have emerged as a critical technology in advanced corrosion protection, particularly for automotive, aerospace, and industrial applications. As of 2025, this sector is experiencing notable engineering advances driven by increasingly stringent environmental regulations and the demand for higher-performance surface treatments. The core benefit of zinc-nickel coatings—typically containing 12-16% nickel—lies in their enhanced corrosion resistance, which can outperform conventional zinc coatings by up to fivefold in neutral salt spray tests. This performance has spurred widespread adoption amongst OEMs and tier suppliers.
Leading manufacturers such as Atotech and DuPont have invested in refining bath chemistries and process controls, enabling more precise layer thicknesses and uniform alloy composition across complex geometries. Recent process automation, including real-time monitoring of electrolyte composition and advanced current modulation, allows for tighter quality tolerances and improved energy efficiency in electroplating lines. Furthermore, the introduction of trivalent chromium passivation systems—championed by companies like MacDermid Alpha—responds to global moves away from hexavalent chromium for post-treatment, further aligning with regulatory trends.
From a materials engineering perspective, the layering and multi-step deposition techniques are evolving. Next-gen approaches involve not only zinc-nickel alloy layers but also duplex and even triplex systems, where an additional organic or ceramic topcoat is applied to extend service life and add functional properties, such as self-healing or hydrophobic effects. Atotech and peers are developing modular coating systems compatible with both rack and barrel plating, allowing for flexible manufacturing and reduced lead times.
In the near future, digitalization and data-driven process optimization are expected to play a greater role. The integration of AI-guided process feedback, as trialed in pilot plants by several global suppliers, is anticipated to further enhance consistency and throughput. The next few years are also likely to see broader adoption of coatings engineered for compatibility with lightweight alloys and high-strength steels, in line with the automotive industry’s shift towards electrification and sustainability.
Overall, zinc-nickel layered coatings are positioned to remain at the forefront of anti-corrosion solutions in 2025 and beyond, underpinned by both environmental imperatives and ongoing technological innovation from sector leaders such as Atotech, MacDermid Alpha, and DuPont.
Market Size & Forecast: Global and Regional Demand Through 2029
The market for zinc-nickel layered coatings engineering is witnessing robust growth, driven by increasing demand in automotive, electronics, energy, and heavy machinery sectors seeking superior corrosion resistance and environmental compliance. As of 2025, production capacities and adoption rates are expanding across North America, Europe, and Asia-Pacific, with key industry players investing in advanced manufacturing and finishing technologies to meet evolving regulatory requirements and performance standards.
In Europe, the shift away from traditional cadmium and hexavalent chromium finishes, due to REACH regulations, continues to accelerate the adoption of zinc-nickel coatings. Leading suppliers such as Atotech and MacDermid Alpha are investing in new facility upgrades and process innovations aimed at higher throughput and reduced environmental impact. The European market is forecasted to experience a compound annual growth rate (CAGR) in the mid-single digits through 2029, reflecting steady demand from automotive OEMs and component suppliers focused on lightweighting and extended service intervals.
North America remains a significant market, with the United States and Mexico driving adoption in automotive, agricultural equipment, and industrial fastener sectors. Major manufacturers such as A+ Industrial Coatings and Prestige Coating are expanding their zinc-nickel coating lines, responding to OEM mandates for improved corrosion protection in electric vehicle (EV) components and infrastructure. The region is projected to maintain a stable but moderate growth trajectory, supported by infrastructure investments and strict environmental policies.
Asia-Pacific, led by China, Japan, and South Korea, is expected to post the highest growth rates through 2029. The region benefits from booming automotive production, rapidly modernizing manufacturing bases, and expanded electronics output. Companies like Nippon Paint Holdings and Tokyo Kinzoku Industry are scaling up zinc-nickel coating capabilities, with a focus on automated and high-volume plating lines to serve both domestic and export markets.
Globally, the zinc-nickel layered coatings engineering market is anticipated to surpass significant volume benchmarks by 2029, fueled by increasing regulatory stringency on hazardous substances, rising awareness of lifecycle costs, and ongoing technical advances in deposition techniques. Looking ahead, the next few years will likely see continued capacity expansions, more widespread integration of digital process controls, and new alloy formulations that offer tailored performance for specific industry needs.
Competitive Landscape: Leading Companies & Strategic Partnerships
The competitive landscape of zinc-nickel layered coatings engineering in 2025 is characterized by the presence of established surface treatment specialists, global chemical manufacturers, and automotive supply chain leaders. These companies drive innovation through advanced alloy formulations, automated plating processes, and partnerships targeting sustainability and corrosion resistance improvements. As environmental regulations tighten and the automotive and heavy industrial sectors demand longer-lasting, high-performance coatings, industry players are increasingly investing in R&D and strategic collaborations to consolidate their positions.
Key industry leaders such as Atotech, MacDermid Alpha, and otech remain at the forefront, supplying proprietary zinc-nickel chemistries and turnkey plating solutions to OEMs and tier suppliers globally. Atotech, for example, continues to expand its Tricotect and Zintek product lines, emphasizing high deposit efficiency and compliance with automotive OEM standards for corrosion performance. Meanwhile, MacDermid Alpha leverages its global footprint to provide integrated zinc-nickel coating systems tailored for automotive fasteners and chassis components.
Strategic partnerships and technical alliances are integral to this competitive environment. Notably, collaborations between chemical solution providers and automation equipment manufacturers are streamlining the deployment of high-throughput, environmentally friendly zinc-nickel lines. For instance, Galvatek, a specialist in automated surface treatment plants, frequently partners with chemical suppliers to deliver turnkey zinc-nickel plating systems for aerospace and defense clients.
The growing demand for sustainable solutions has also prompted alliances aimed at meeting chromium-free, REACH-compliant, and low-waste process criteria. Leading global automotive manufacturers, such as Volkswagen AG, are actively engaging with coating technology providers to co-develop next-generation zinc-nickel solutions that extend component lifespans while reducing environmental impact.
Looking ahead, the market is poised for further consolidation as companies seek to secure intellectual property, access new regional markets, and diversify their application fields. The entrance of Asian suppliers and the expansion of European and North American players into electric vehicle and renewable energy supply chains will likely intensify competition in the next few years. Continued investment in automation, digital quality monitoring, and greener process chemistries is anticipated, with industry leaders forming new partnerships to address the evolving technical and regulatory requirements of end users.
Automotive & Aerospace Demand: Sector-Specific Growth Drivers
The automotive and aerospace industries are set to remain pivotal drivers for zinc-nickel layered coatings engineering through 2025 and into the coming years. The push for lightweight construction, electrification, and enhanced corrosion resistance continues to raise the bar for surface treatment technologies. Zinc-nickel coatings, particularly those with layered or duplex architectures, are increasingly favored due to their superior corrosion protection—up to eight times greater than traditional zinc plating—while also addressing requirements for high temperature and chemical resistance.
Within the automotive sector, original equipment manufacturers (OEMs) and suppliers are intensifying their adoption of zinc-nickel coatings for critical fasteners, brake components, fuel system parts, and electric vehicle (EV) battery housings. Regulatory pressures, such as the European Union’s End-of-Life Vehicles Directive and the growing restrictions on hexavalent chromium, are propelling the shift toward more environmentally friendly and durable electroplated coatings. Major automotive suppliers—including ZF Friedrichshafen AG and Robert Bosch GmbH—have publicly committed to substituting traditional coatings with advanced zinc-nickel solutions to meet lifetime corrosion warranties and sustainability benchmarks.
Aerospace applications, where weight savings, galvanic compatibility, and reliability under extreme conditions are paramount, also illustrate rising demand for engineered zinc-nickel layers. Aircraft manufacturers and their tiered suppliers are specifying zinc-nickel for fasteners, landing gear components, and hydraulic fittings, often as part of multi-layered systems combining passivation and topcoats for enhanced performance. Companies such as Galvatek and Socomore are further developing process automation and quality control systems tailored to the tight tolerances and traceability demanded by aerospace clients.
From a technology perspective, advancements in bath chemistry, pulse plating, and micro-layering are enabling more uniform deposits and tailored alloy compositions. Ongoing investments by equipment providers like Atotech support scalable, high-throughput installations for both automotive and aerospace production lines. Notably, collaborative R&D efforts between coating suppliers and OEMs are accelerating the transition to trivalent passivations and lead-free chemistries, reflecting both regulatory and corporate sustainability targets.
Looking ahead, the outlook for zinc-nickel layered coatings engineering is robust. Continued electrification in mobility, the need for longer component lifespans, and tighter regulatory frameworks are expected to fuel new process developments and capacity expansions. Industry leaders anticipate that zinc-nickel’s share of anti-corrosion coatings will grow steadily, with adoption extending into adjacent mobility segments such as commercial vehicles and e-mobility platforms.
Innovation Pipeline: Patents, R&D, and Emerging Processes
The innovation pipeline for zinc-nickel layered coatings engineering in 2025 is characterized by robust research and development activities, a dynamic patent landscape, and the emergence of advanced processes optimized for both performance and regulatory compliance. The automotive, construction, and electronics sectors continue to drive demand for high-performance corrosion-resistant coatings, prompting material scientists and coating manufacturers to intensify efforts in alloy formulation, process automation, and environmental stewardship.
One of the most prominent trends is the push toward trivalent passivation systems and cyanide-free plating baths. In response to stricter environmental regulations—particularly in Europe and North America—manufacturers such as Atotech and MacDermid Alpha are developing proprietary zinc-nickel processes that combine high corrosion resistance with reduced hazardous waste generation. For example, Atotech’s innovations focus on high-nickel (12–16%) alloys for automotive fasteners, with reported salt spray resistance exceeding 1,000 hours to red rust, while remaining compliant with REACH and RoHS directives.
The patent landscape is witnessing a steady influx of filings related to layered and composite zinc-nickel coatings. Recent disclosures emphasize multilayer approaches—such as functionally graded coatings or duplex structures—that sequentially combine ductile, sacrificial zinc-rich layers with harder, nickel-rich diffusion barriers. This engineering enables tailored performance for specific application stresses, from marine environments to underhood automotive assemblies. Companies like OC Oerlikon and Nippon Paint Holdings are actively pursuing intellectual property in this arena, underscoring the sector’s competitive intensity.
R&D efforts also extend to process automation and digitalization. Inline quality monitoring, real-time bath composition analytics, and AI-driven process control are becoming standard in state-of-the-art plating lines, as seen in technological offerings from Elaqua and Atotech. These technologies are expected to accelerate commercial adoption of complex layered coatings by ensuring reproducibility and cost-efficiency.
Looking ahead to the next few years, industry outlook is shaped by the need for even higher performance standards—such as extended corrosion protection for electric vehicle components and lightweight alloys. Ongoing collaborations between OEMs, chemical suppliers, and university labs are likely to yield new patent filings and commercial launches in nanostructured zinc-nickel coatings, smart self-healing layers, and coatings compatible with additive manufacturing substrates. With sustainability and digital manufacturing as central drivers, zinc-nickel layered coatings engineering is poised for rapid evolution through 2025 and beyond.
Sustainability & Regulatory Shifts: Environmental and Compliance Factors
Zinc-nickel layered coatings have become a focal point in surface engineering due to their superior corrosion resistance and environmentally favorable profile compared to traditional cadmium or high-zinc alternatives. As of 2025, sustainability and regulatory compliance are defining drivers in this sector, influenced by tightening global standards on hazardous substances and lifecycle emissions.
The European Union’s ongoing enforcement of the REACH regulation and the End-of-Life Vehicle (ELV) Directive continues to restrict the use of hexavalent chromium and other hazardous substances in automotive and electronics manufacturing. As a result, OEMs and tier suppliers are accelerating the adoption of zinc-nickel coatings, which offer high performance without the compliance risks associated with older chemistries. Major coating providers, such as Atotech and MacDermid Alpha, report expanded portfolios of trivalent passivation and RoHS-compliant zinc-nickel processes, aiming to serve both automotive and industrial fastener markets.
In North America, the shift is paralleled by updated ASTM standards and increasing customer requirements for extended salt spray life and reduced environmental impact. DuPont and Aker BP have highlighted the critical role of sustainable coatings for offshore and energy applications, where lifecycle assessments and carbon footprints are now routinely factored into procurement decisions.
Data from recent years show a market-wide increase in the use of zinc-nickel coatings with trivalent chromate or chrome-free passivation systems, reducing the reliance on heavy metals and improving worker safety during application. For instance, Atotech’s latest product lines emphasize energy efficiency, lower waste generation, and closed-loop water recycling, aligning with both EU and US environmental directives.
Looking ahead to the next few years, regulatory momentum is expected to intensify, with the United Nations’ Minamata Convention on Mercury and probable further restrictions on PFAS and other persistent chemicals pushing the industry toward even greener formulations. The rise of the circular economy and digital product passports in the EU will also require transparent tracking of coating chemistries throughout the value chain, further incentivizing the switch to sustainable zinc-nickel systems.
Overall, zinc-nickel layered coatings engineering is positioned for robust growth, driven by regulatory harmonization, customer sustainability mandates, and ongoing innovation from leading suppliers. Companies investing in eco-friendly, compliant technologies are likely to maintain a competitive edge as global environmental expectations continue to rise.
Supply Chain & Raw Material Challenges
The supply chain and raw material landscape for zinc-nickel layered coatings is undergoing significant shifts as the industry enters 2025. The primary inputs—high-purity zinc and nickel—have experienced fluctuating availability and pricing due to geopolitical factors, energy costs, and evolving environmental regulations. In recent years, nickel markets have been especially volatile, influenced by increased demand from the battery sector and supply constraints from major producers. This volatility directly impacts the cost structure for zinc-nickel coatings, where nickel typically constitutes 10–15% of the alloy, but up to 60% of the material cost.
Several leading suppliers, including Umicore and BASF, have publicly noted challenges in securing consistent nickel supply for surface technologies, with ongoing investments to improve recycling and circularity in their value chains. These efforts are expected to partially mitigate raw material pressures, but full decoupling from primary nickel sources remains elusive as of 2025.
Environmental regulations are exerting additional pressure on traditional mining and refining operations. The European Union’s Green Deal and the United States’ Inflation Reduction Act are accelerating shifts toward responsible sourcing and increased scrutiny of supply chain transparency. As a result, OEMs and coating applicators are increasingly seeking certifications and documentation of supply chain compliance from their raw material suppliers, as highlighted by policy updates from Aker Solutions and Technip Energies in their recent sustainability reports.
Another emerging challenge is the competition for nickel between coating applications and the rapidly expanding electric vehicle battery sector. This competition has led to periodic supply shortages and prompted some surface engineering companies to explore alternative alloy compositions or multi-layer coating systems that reduce overall nickel dependence. For example, Atotech has indicated active R&D in lower-nickel and hybrid coatings to respond to anticipated raw material constraints through 2026 and beyond.
Outlook for the near term suggests continued tightness in nickel supply, with zinc remaining relatively more stable due to broader producer base and less intense competition from other industrial sectors. However, supply chain resilience strategies—such as dual sourcing, increased recycling, and closer supplier partnerships—are being prioritized across the zinc-nickel coatings industry. Companies that invest in digital traceability and circular economy initiatives are likely to be better positioned to navigate the evolving raw material landscape in the next several years.
Customer Adoption: OEM, Tier 1, and Aftermarket Perspectives
The adoption of zinc-nickel layered coatings is experiencing a marked uptick across automotive, heavy machinery, and industrial sectors, driven by increasingly stringent corrosion resistance standards and evolving sustainability mandates. Original Equipment Manufacturers (OEMs), Tier 1 suppliers, and the aftermarket are each approaching zinc-nickel coatings with unique priorities, but all are converging on the technology due to its demonstrated performance and regulatory alignment.
OEMs are leading the push for zinc-nickel coatings, especially in regions facing tightening environmental and performance regulations. European OEMs are notably proactive, as evidenced by widespread adoption among major automotive brands and component producers. This is largely due to the superior corrosion protection—often exceeding 720 hours in salt spray tests—and the move away from hexavalent chromium processes. Companies such as DuPont and ZEISS (for quality inspection and process control) are supporting OEMs with advanced process integration capabilities. As vehicle lightweighting and electrification continue into 2025, zinc-nickel coatings’ compatibility with mixed metals and sensitivity to hydrogen embrittlement are major advantages.
Tier 1 suppliers, responsible for complex assemblies and subcomponents, are closely aligning with OEM demands by integrating automated zinc-nickel plating lines and investing in process traceability. Companies such as Atotech are providing turnkey plating systems and chemistry solutions to help Tier 1s meet OEM specifications and sustainability requirements. Tier 1s are also leveraging the increased process consistency of modern zinc-nickel baths, enabling them to deliver highly uniform coatings even on intricate geometries—an essential consideration for electrified drivetrain and chassis components.
In the aftermarket, adoption is more varied but is expected to grow steadily through 2025 and beyond, particularly in regions where extended product lifecycles and corrosion-related warranty claims are primary concerns. Aftermarket players are increasingly specifying zinc-nickel finishes for critical fasteners, brake components, and suspension elements, mirroring OEM practices. Supplier networks such as Wynn's and Bosch are expanding their coated product lines in response to end-user and fleet operator demand for longer maintenance intervals.
Looking forward, the outlook for zinc-nickel layered coatings engineering remains robust. As regulatory pressures intensify and circular economy principles gain traction, the adoption curve is projected to steepen across all customer segments. Key industry bodies, such as the Automotive Industry Action Group (AIAG), are updating recommended practices and supply chain standards to further facilitate the implementation of high-performance, environmentally sound surface coatings.
Future Outlook: Disruptive Technologies and Strategic Recommendations
Zinc-nickel layered coatings are poised for significant evolution in 2025 and the subsequent years, driven by regulatory pressures, the automotive industry’s shift to electrification, and a growing emphasis on sustainability. These coatings—already established for their superior corrosion resistance compared to traditional zinc plating—are increasingly integral in automotive, aerospace, and heavy machinery sectors due to their ability to meet stringent performance requirements under harsh environmental conditions.
A key disruptive trend is the adoption of trivalent passivation and chromium-free sealing systems, which address environmental and health concerns associated with hexavalent chromium. Leading surface treatment providers such as Atotech and DuPont have been investing in next-generation zinc-nickel bath chemistries that not only eliminate hazardous substances but also improve plating efficiency and layer uniformity. These advances are expected to become mainstream as automakers and OEMs demand compliance with REACH and ELV directives.
Another area of innovation is the integration of smart manufacturing and digital process control. Companies like AZ Electronic Materials and ZEISS are developing precision monitoring tools and automated quality assurance systems, which enable real-time adjustments to deposition processes. This shift not only enhances coating consistency but also minimizes waste and energy consumption, aligning with global sustainability targets.
Electrification trends, particularly in the automotive sector, are anticipated to shape the specifications for zinc-nickel coatings through 2025 and beyond. The growing use of mixed-material assemblies and lightweight alloys requires coatings that offer robust adhesion, low contact resistance, and high compatibility with aluminum. This is reflected in ongoing collaborations between OEMs and suppliers such as Bosch and Schaeffler, who are actively specifying advanced zinc-nickel solutions for e-mobility powertrain and chassis applications.
Looking ahead, strategic recommendations for industry stakeholders include: investing in R&D for multifunctional coating systems (e.g., combining corrosion protection with self-lubricating or anti-microbial layers); expanding pilot programs for closed-loop chemical management to reduce environmental impact; and fostering cross-industry partnerships to accelerate the adoption of digitalized plating lines. As the regulatory landscape continues to tighten and end-user demands evolve, those who proactively integrate advanced zinc-nickel engineering will secure a competitive edge in the coatings market throughout the latter half of this decade.