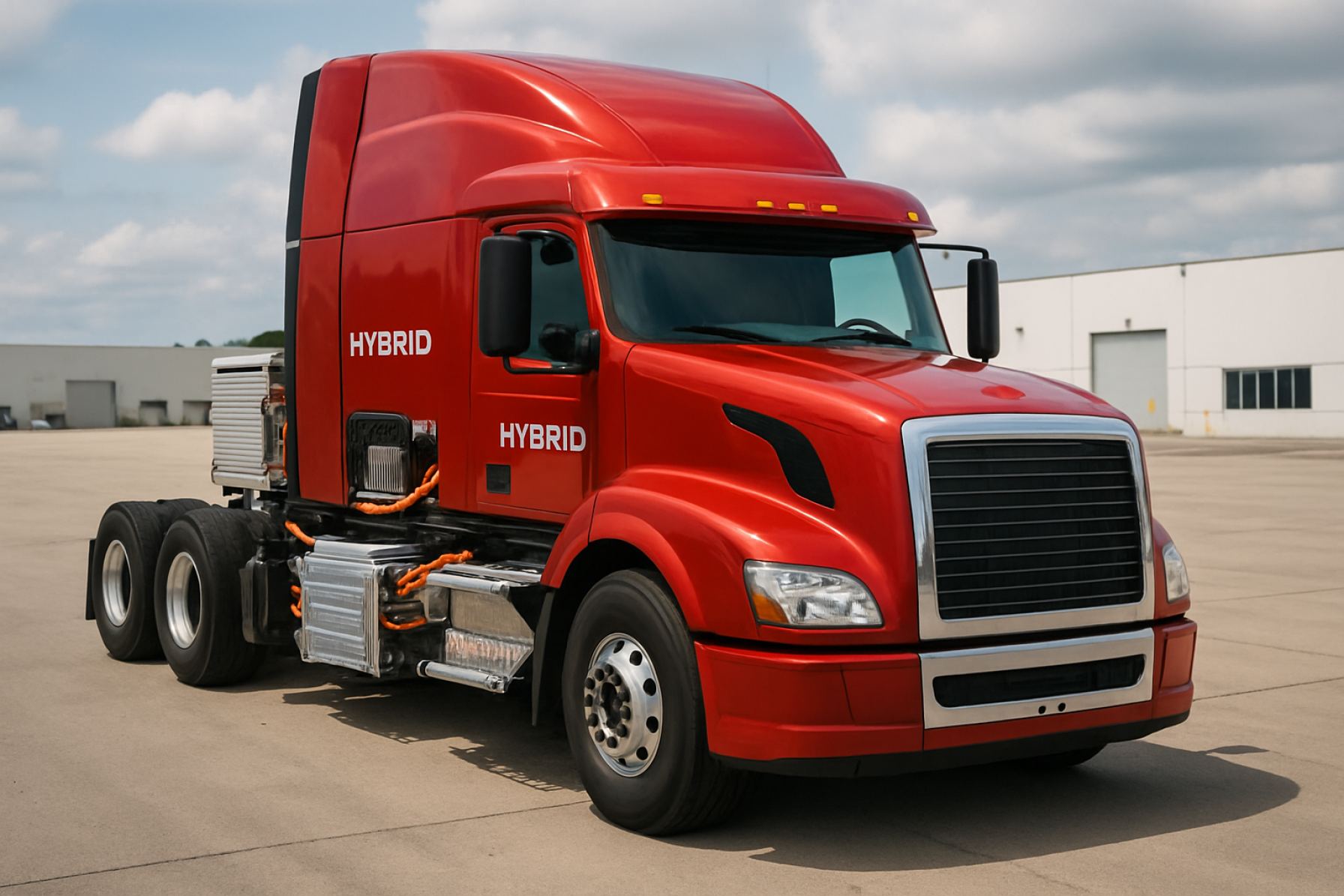
Table of Contents
- Executive Summary: 2025 Market Snapshot & Key Insights
- Technology Overview: Core Components of Heavy Vehicle Hybridization
- Market Size & Forecast: 2025-2030 Growth Projections
- Regulatory Drivers: Global Emissions Mandates and Incentives
- Competitive Landscape: Leading Manufacturers and Innovators
- Supply Chain and Materials: Sourcing, Costs, and Constraints
- Fleet Operator Adoption: Barriers, Incentives, and Case Studies
- Integration Challenges: Retrofitting and New Build Strategies
- Emerging Technologies: Battery, Supercapacitor, and Powertrain Advances
- Future Outlook: Long-Term Trends, Opportunities, and Risks
- Sources & References
Executive Summary: 2025 Market Snapshot & Key Insights
The global market for heavy vehicle hybridization hardware in 2025 is characterized by accelerating adoption, spurred by regulatory pressures, fleet emissions targets, and maturing component technologies. Key hardware systems include high-voltage battery packs, electric drive motors, power electronics (inverters, DC/DC converters), and advanced control units, all integrated into hybrid powertrains for trucks, buses, and vocational vehicles. As of 2025, original equipment manufacturers (OEMs) and major tier-1 suppliers are ramping up production and integration of such systems, targeting both new hybrid models and retrofit solutions for existing fleets.
Industry leaders such as Daimler Truck, Volvo Trucks, and PACCAR have announced expanded hybrid offerings, leveraging scalable architectures that blend internal combustion engines with electric propulsion. Battery system advancements — particularly in lithium-ion chemistry, packaging, and thermal management — are resulting in improved energy density and reduced weight, directly enhancing payload and efficiency. Notably, Cummins and Allison Transmission are supplying integrated hybrid drive systems and modular components compatible with a variety of heavy-duty chassis.
Demand is especially robust in urban delivery, municipal, and transit bus applications, where hybridization hardware delivers measurable fuel savings and enables low- or zero-emission operation in restricted zones. For example, BYD Company and Yutong are deploying hybrid and plug-in hybrid buses in European and Asian cities, utilizing proprietary battery and motor technologies. Simultaneously, suppliers such as BorgWarner and Dana Incorporated are expanding their offerings of e-axles, electric drive modules, and hybrid transmission systems tailored for heavy commercial vehicle platforms.
The 2025 outlook anticipates ongoing declines in battery cost per kWh and increased availability of modular hybrid kits, lowering upfront investment barriers for fleet operators. Hybrid hardware is seen as a transitional but critical technology bridge toward full electrification, especially in segments where infrastructure or payload constraints preclude all-electric solutions. Regulatory initiatives in North America, Europe, and China continue to drive investment and innovation, with hardware manufacturers scaling up to meet anticipated demand for both OEM and retrofit hybrid solutions in the next several years.
Technology Overview: Core Components of Heavy Vehicle Hybridization
Heavy vehicle hybridization hardware encompasses a suite of critical components that enable medium- and heavy-duty vehicles—such as trucks, buses, and vocational vehicles—to operate with a combination of internal combustion engines (ICEs) and electric propulsion. As of 2025, rapid advancements in hybrid technology are being driven by tightening emissions regulations, operational cost reduction targets, and the evolving demands of fleet operators. The central hardware elements in heavy vehicle hybridization include electric drive motors, high-voltage battery packs, power electronics (inverters, converters), hybrid transmission systems, and advanced thermal management systems.
- Electric Motors and Generators: Modern hybrid systems for heavy vehicles feature robust electric motors and generators capable of high torque and power density. These are typically integrated into the drivetrain, enabling regenerative braking and electric-only propulsion under certain conditions. Companies such as Robert Bosch GmbH and Danfoss are leading suppliers of electric drive solutions for commercial vehicles, offering scalable motor and generator systems that can be tailored to various vehicle sizes and duty cycles.
- High-Voltage Battery Packs: Lithium-ion battery technology remains dominant, with ongoing improvements in energy density, cycle life, and thermal stability specifically for heavy-duty applications. Modular battery packs are designed for high charge/discharge rates and rugged operating environments. Contemporary Amperex Technology Co., Limited (CATL) and Samsung SDI are among the battery manufacturers producing high-capacity packs for commercial hybrid vehicles.
- Power Electronics: Efficient inverters and DC/DC converters are essential for managing the bidirectional flow of electricity between batteries, electric motors, and auxiliary systems. Advanced silicon carbide (SiC) technology is increasingly used for its superior efficiency and thermal performance. Schneider Electric and Infineon Technologies provide power electronic modules specifically designed for heavy-duty hybrid platforms.
- Hybrid Transmissions: Dedicated hybrid transmissions, including parallel, series, and power-split architectures, are engineered to seamlessly blend power from ICE and electric sources. Suppliers such as Allison Transmission and ZF Friedrichshafen AG manufacture hybrid transmission systems optimized for heavy commercial vehicles, highlighting modularity and robustness.
- Thermal Management: Maintaining optimal temperatures for batteries, motors, and electronics is critical for safety and efficiency. Integrated liquid cooling and advanced heat exchanger systems are standard in new hybrid architectures, with providers like DENSO delivering solutions tailored for high-power commercial vehicle hybrids.
Looking ahead, the next few years will see further integration of hardware components, advances in digital control, and the adoption of next-generation battery chemistries, all aimed at reducing system weight, enhancing durability, and improving overall vehicle efficiency. As OEMs and suppliers continue to refine hybridization hardware, the commercial vehicle sector is expected to accelerate its transition toward lower-emission, higher-efficiency models.
Market Size & Forecast: 2025-2030 Growth Projections
The heavy vehicle hybridization hardware market is set for substantial growth in the period from 2025 to 2030, as the commercial transportation sector accelerates its transition toward cleaner and more efficient propulsion technologies. This market includes core components such as electric motors, power electronics, high-voltage batteries, onboard chargers, and hybrid control units specifically engineered for trucks, buses, and off-highway vehicles.
Continued regulatory pressure in North America, Europe, and parts of Asia—such as tightened emissions standards and urban low-emission zones—remains a key catalyst. For example, the European Union’s CO2 emissions targets for heavy-duty vehicles will require manufacturers to reduce average fleet emissions by 15% by 2025 and 30% by 2030 (compared to 2019 levels), directly incentivizing the adoption of hybridization hardware across OEM fleets (DAF Trucks; Volvo Trucks). Similarly, the United States’ EPA Phase 2 GHG regulations and California’s Advanced Clean Trucks rule are expected to boost demand for hybrid systems in the coming years (Cummins).
Leading manufacturers and suppliers are scaling up investments and partnerships to meet projected demand. Major OEMs such as Daimler Truck, PACCAR, and Navistar are introducing new generations of hybridized vehicle platforms and collaborating with specialized component suppliers. Technology providers like Allison Transmission, Robert Bosch GmbH, and ZF Friedrichshafen AG are expanding their heavy-duty hybrid hardware portfolios, targeting both factory-fit and retrofit opportunities.
Forecasts for the 2025–2030 period indicate a compound annual growth rate (CAGR) in the high single digits to low double digits for the heavy vehicle hybrid hardware market, with the global addressable market value potentially reaching several billion USD by 2030. Adoption is expected to be most rapid in urban delivery fleets, transit buses, and vocational vehicles, where hybrid systems deliver clear benefits in fuel savings and emissions reduction. Supply chain localization and modularization of hybrid components—such as battery packs, control systems, and e-axles—will further accelerate cost reductions and market penetration.
In summary, the next five years are expected to see robust market expansion, supported by a convergence of policy mandates, technological advancements, and ongoing investment from both OEMs and Tier 1 suppliers.
Regulatory Drivers: Global Emissions Mandates and Incentives
In 2025 and the years immediately following, regulatory pressures are a primary catalyst for the adoption of hybridization hardware in heavy vehicles. Governments worldwide are tightening emissions standards for commercial transportation, prompting OEMs and suppliers to accelerate the integration of hybrid systems. The European Union’s “Fit for 55” package mandates a 90% reduction in CO₂ emissions from new heavy-duty vehicles by 2040, a target that effectively requires widespread electrification and hybridization of fleets. In the near term, the Euro VII standards, expected to be finalized in 2025, will further limit nitrogen oxides (NOx) and particulate matter, reinforcing the need for advanced powertrain hardware such as electric drive modules, high-voltage batteries, and regenerative braking systems (Daimler Truck).
In the United States, the Environmental Protection Agency (EPA) has introduced the “Clean Trucks Plan,” which phases in stringent NOx and greenhouse gas (GHG) requirements for model years 2027 and beyond. California’s Advanced Clean Trucks regulation, being adopted by other states, mandates increasing sales of zero-emission and hybrid trucks, accelerating the market for hybridization components such as power electronics and electric axles (PACCAR). Federal and state-level incentives, such as the U.S. Inflation Reduction Act, provide tax credits and grants for hybrid vehicle and component production, supporting manufacturing scale-up and component innovation (Navistar).
In China, where heavy-duty vehicle electrification is a national priority, the Ministry of Ecology and Environment continues to roll out tougher pollutant limits and offers subsidies for hybrid and new energy commercial vehicles. This regulatory environment has pushed domestic manufacturers to invest heavily in hybrid powertrain hardware, including advanced energy storage and power management systems (FAW Group).
Incentive programs across all key regions are driving investment in hybridization hardware. European Union funding mechanisms such as the Connecting Europe Facility and the Innovation Fund support fleet retrofits and new hybrid truck deployments. In North America and China, government and utility incentives lower the total cost of ownership and accelerate the transition to cleaner technologies.
Looking ahead to the late 2020s, the regulatory landscape is expected to become more stringent, with further reductions in allowable emissions and expanded zones restricting internal combustion vehicles. These trends ensure continued demand for hybridization hardware—ranging from electric motors and inverters to control software—as fleets seek compliance and operational cost savings, positioning hybrid technology as a key bridge in the transition to zero-emission heavy transport.
Competitive Landscape: Leading Manufacturers and Innovators
The competitive landscape for heavy vehicle hybridization hardware in 2025 is characterized by rapid innovation, strategic partnerships, and expanding global footprints among established automotive manufacturers and specialized component suppliers. The segment is driven by tightening emissions regulations, rising fuel costs, and growing demand for sustainable logistics solutions, particularly in North America, Europe, and Asia-Pacific.
Among the global leaders, Volvo Group continues to set benchmarks with its hybrid truck and bus solutions, leveraging proprietary electric drivetrains and energy storage systems. Volvo’s hybrid trucks and buses are being deployed in both urban and long-haul applications, with continual improvements in battery capacity and power electronics to reduce emissions and improve fuel economy.
Daimler Truck maintains a prominent position with its Mercedes-Benz and FUSO hybrid offerings, focusing on modular hybrid systems that allow for scalability across different vehicle classes. Daimler’s commitment to electrification is evident in its investments in hybrid transmission technology and integration of advanced power electronics to optimize energy recovery and utilization.
Cummins has emerged as a major force in hybrid powertrains, offering complete hybrid solutions that combine advanced diesel engines with electric drive modules, battery packs, and control systems. Their hybrid systems are widely adopted in transit buses and vocational trucks, aided by partnerships with chassis OEMs and fleet operators to ensure seamless integration.
Component suppliers such as Robert Bosch GmbH and ZF Friedrichshafen AG play crucial roles by delivering sophisticated hybrid modules, inverters, and energy management systems. Bosch’s scalable hybrid drives and ZF’s modular electric axle systems are incorporated into multiple OEM platforms, enabling flexible adaptation to regional requirements and vehicle types.
Asian manufacturers, notably Toyota Motor Corporation and Hino Motors, maintain strong momentum in hybrid heavy vehicle technology. Their focus on parallel and series hybrid architectures has resulted in high-volume deployments in regions prioritizing emissions reductions, particularly in commercial buses and urban delivery trucks.
Looking ahead, the competitive landscape is expected to intensify as new entrants and technology startups enter the market, fostering further advances in battery technology, power electronics, and integration. Strategic collaborations between truck OEMs, tier-one suppliers, and energy storage specialists are anticipated to accelerate the rollout of next-generation hybridization hardware, positioning the sector for significant growth through the remainder of the decade.
Supply Chain and Materials: Sourcing, Costs, and Constraints
The supply chain for heavy vehicle hybridization hardware is undergoing significant transformation as demand accelerates in 2025 and is expected to grow through the latter half of the decade. Key components such as high-voltage batteries, electric motors, power electronics, and control systems form the backbone of hybrid drivetrains for trucks, buses, and construction vehicles. Sourcing these materials and components involves a complex network of tiered suppliers, with increasing emphasis on localization and resilience in response to recent global disruptions.
One of the most critical supply chain constraints involves lithium-ion batteries, which dominate current hybrid and plug-in hybrid architectures. Battery cell manufacturing is concentrated among a few major players, such as CATL, LG Energy Solution, and Panasonic. These companies have announced expansions in North America and Europe, aiming to alleviate long lead times and mitigate geopolitical risks. However, material sourcing—especially for lithium, cobalt, and nickel—remains a bottleneck, with price volatility and ESG concerns impacting procurement strategies.
Electric motor production, often reliant on rare earth magnets, faces its own set of challenges. Major suppliers like Bosch and Siemens are investing in alternative magnet technologies and diversifying sourcing to reduce reliance on single regions. Power electronics, such as inverters and DC/DC converters, increasingly use silicon carbide (SiC) semiconductors, whose supply is limited by wafer production capacity and long equipment lead times. Companies like Infineon Technologies and STMicroelectronics are expanding fabrication facilities to address this constraint.
Cost pressures remain high in 2025, as raw material prices for batteries and semiconductors have yet to return to pre-pandemic levels. OEMs are responding by entering long-term contracts and investing directly in upstream supply, as seen in recent announcements from Volvo Group and Daimler Truck. Additionally, hybrid system integration requires specialized components—such as compact transmissions, high-voltage wiring, and advanced cooling systems—frequently supplied by firms like Dana Incorporated and ZF Friedrichshafen. Ensuring consistent quality and availability of these components is a growing priority as hybrid volumes scale up.
Looking ahead, supply chain resilience and sustainable sourcing are expected to shape procurement strategies. OEMs and suppliers are increasingly emphasizing recycled materials, closed-loop battery processes, and greater transparency to meet regulatory and customer expectations. While near-term constraints persist, ongoing investment and collaboration across the value chain are likely to gradually ease bottlenecks and support the broader adoption of heavy vehicle hybridization hardware.
Fleet Operator Adoption: Barriers, Incentives, and Case Studies
Fleet operators are increasingly evaluating hybrid hardware solutions for heavy vehicles as a means to reduce fuel costs, comply with emissions regulations, and future-proof their fleets. However, adoption in 2025 faces a complex mix of barriers and incentives, with notable case studies providing insight into trends and strategies.
Barriers: The principal challenges for fleet operators include the higher upfront costs of hybridization kits and new hybrid vehicles, integration complexity with existing fleets, and concerns over maintenance infrastructure. For example, retrofitting hybrid systems into legacy diesel trucks can involve significant engineering adjustments, which may disrupt operational schedules and require specialized technician training. Additionally, the availability of hybrid-specific components—such as high-voltage batteries, power electronics, and electric drive modules—remains uneven globally, posing logistical hurdles for operators outside major markets. Some operators express concern about the residual value and lifecycle cost savings of hybrid hardware, especially as battery technology and regulatory landscapes rapidly evolve.
Incentives: Governments in North America, Europe, and parts of Asia are offering direct financial incentives, such as purchase grants and tax benefits, to offset initial costs. For instance, “Clean Truck” programs subsidize the integration of hybrid technologies in commercial fleets. Regulatory frameworks, including stricter urban emissions zones and medium- and heavy-duty vehicle CO2 standards, are pushing fleets to adopt cleaner technologies. OEMs and suppliers are responding by expanding hybrid hardware offerings; major industry players like Volvo Group and Daimler Truck have introduced advanced hybrid drivetrains for both new vehicle sales and aftermarket retrofits. Some component manufacturers, such as Bosch and Allison Transmission, now provide modular hybrid systems that simplify integration into diverse platforms, reducing technical barriers for fleet operators.
Case Studies: Leading logistics and transit operators have begun large-scale hybrid vehicle deployments. DHL has incorporated hybrid trucks into its European fleets, reporting reductions in both fuel consumption and emissions. Similarly, municipal transit agencies in the United States and Europe, in partnership with Volvo Group and Allison Transmission, have documented operational cost savings and positive driver feedback following hybrid bus rollouts.
Outlook: Over the next few years, wider adoption is likely as hybrid hardware matures and total cost of ownership advantages become clearer. Expanded support from OEMs and suppliers, along with ongoing policy incentives, are expected to help lower adoption barriers. Fleet operator experience from early deployments will continue to shape best practices, guiding others through the transition to hybridized heavy vehicles.
Integration Challenges: Retrofitting and New Build Strategies
The integration of hybridization hardware into heavy vehicles—both through retrofitting existing fleets and incorporating systems in new builds—poses significant technical and operational challenges. As of 2025, the sector is witnessing increased attention to these integration hurdles, driven by the dual pressures of decarbonization mandates and total cost of ownership (TCO) optimization.
For retrofitting, one major challenge is the variability in legacy vehicle architectures. Existing heavy-duty trucks and buses often lack the standardized interfaces or space allocations needed to accommodate hybrid systems, such as battery packs, electric motors, or power electronics. Companies like Daimler Truck and Volvo Trucks have noted the complexity of integrating high-voltage components into chassis originally designed for conventional internal combustion engines. Moreover, ensuring compatibility with vehicle control systems and safety protocols remains a persistent obstacle, as does certification to meet regulatory standards.
Retrofitting also faces economic challenges: the initial capital outlay for hardware and installation can be high, and operational downtime during the conversion process is a significant concern for fleet operators. To address these issues, some manufacturers and specialized retrofit firms are developing modularized kits with standardized interfaces, aiming to reduce both installation complexity and time. However, as of 2025, widespread adoption is still limited, with most retrofit projects focused on pilot fleets or urban transit applications where operational profiles are predictable and infrastructure support is available.
In contrast, new build strategies offer greater flexibility for integrating hybrid hardware from the outset. OEMs such as PACCAR and CNH Industrial are designing platforms specifically optimized for hybrid—and in some cases, fully electric—drivetrains. These purpose-built architectures allow for optimal placement of batteries, cooling systems, and ancillary components, improving performance, reliability, and maintainability. The shift toward modular, scalable electric drive platforms is expected to accelerate in the coming years, enabling manufacturers to offer a broader range of hybridized models with varying degrees of electrification.
Looking ahead, integration challenges are likely to persist but diminish in severity as industry standards mature and economies of scale develop. Collaboration across the value chain—including component suppliers, system integrators, and regulatory bodies—will be critical to overcoming technical and economic barriers. By the late 2020s, it is expected that advances in battery energy density, power electronics, and digital vehicle controls will further streamline both retrofit and new-build hybridization efforts, supporting the broader transition to low- and zero-emission heavy vehicles.
Emerging Technologies: Battery, Supercapacitor, and Powertrain Advances
The landscape of heavy vehicle hybridization hardware is rapidly advancing as manufacturers and suppliers focus on improving efficiency, reducing emissions, and meeting tightening regulatory standards. In 2025, the convergence of battery, supercapacitor, and powertrain technologies is driving the hybridization of heavy-duty trucks, buses, and off-highway vehicles, aiming to bridge the gap between conventional diesel vehicles and fully electric alternatives.
Key hardware components in heavy vehicle hybrid systems include high-capacity lithium-ion batteries, advanced supercapacitors, power electronics, and hybrid-specific transmission units. The latest generation of lithium-ion batteries offers greater energy density, faster charging capabilities, and improved cycle life, making them better suited for the demanding duty cycles of heavy vehicles. Leading battery manufacturers such as CATL and Samsung SDI are actively supplying battery packs specifically engineered for commercial and off-highway hybrid applications, supporting both plug-in and non-plug-in architectures.
Supercapacitors are also gaining traction, particularly for regenerative braking and rapid energy discharge during acceleration. Companies like Maxwell Technologies (a subsidiary of Tesla) have developed robust supercapacitor modules that can be integrated into hybrid powertrains to complement batteries, enhance peak power delivery, and extend system lifespan.
On the powertrain side, integrated electric drive modules, high-voltage inverters, and hybrid transmissions are being tailored for heavy-duty requirements. Allison Transmission and ZF Friedrichshafen AG are among the established suppliers developing hybrid transmission solutions that seamlessly blend engine and electric motor power, optimizing fuel economy and drivability. These systems often include advanced control units and software to manage energy flows and maximize operational efficiency.
Original equipment manufacturers (OEMs) such as Volvo Trucks and Daimler Truck are rolling out new hybrid heavy vehicle models in 2025, leveraging these hardware advances to offer fleets lower total cost of ownership and compliance with upcoming emissions zones. In addition, regulatory incentives and infrastructure investments are accelerating adoption, with pilot deployments of hybrid refuse trucks, transit buses, and construction vehicles already underway in major markets.
Looking ahead, further improvements in battery chemistry, supercapacitor integration, and power electronics miniaturization are expected to enhance system performance and reduce costs. As hybridization solutions become more modular and scalable, uptake across a broader range of heavy vehicle classes is anticipated over the next few years, positioning hybrid hardware as a critical bridge in the transition to zero-emission transport.
Future Outlook: Long-Term Trends, Opportunities, and Risks
As 2025 approaches, the long-term outlook for heavy vehicle hybridization hardware is shaped by tightening emissions regulations, advances in component technology, and evolving market demands. Heavy-duty sectors—including trucking, transit, and construction—are increasingly turning to hybrid systems as a pragmatic bridge between traditional internal combustion and full electrification.
A primary driver is global emissions policy: the European Union’s “Euro VII” and the United States’ EPA Phase 3 GHG standards, both coming into force in the next few years, are pushing manufacturers to adopt hybrid solutions that can deliver immediate reductions in fuel consumption and CO2 output. Hybridization hardware—spanning electric motors, high-voltage battery packs, power electronics, and advanced transmissions—is being integrated into new models and retrofitted to existing fleets by leading OEMs such as Daimler Truck, Volvo Trucks, and PACCAR.
Recent commercial deployments demonstrate rapid progress. Dana Incorporated and Allison Transmission have both introduced scalable hybrid driveline solutions that integrate seamlessly with conventional diesel powertrains, offering up to 30% fuel savings in urban duty cycles and significant NOx reductions. ZF Friedrichshafen AG has expanded its modular e-mobility platforms for buses and trucks, targeting flexible hybridization from mild to plug-in systems, with production ramping up through 2025.
Looking further ahead, several trends are likely to shape the sector:
- Component Innovation: Continued cost and performance improvements in batteries and power electronics—supported by investments from companies like Cummins—will make hybrid systems more competitive and accessible, especially for medium-duty and vocational vehicles.
- System Integration: OEMs and Tier 1 suppliers are emphasizing modularity, allowing hybrid hardware to be tailored for diverse applications, from refuse collection to regional haulage. This flexibility is key to accelerating market penetration.
- Risks: Market uptake could be constrained by total cost of ownership uncertainties, battery raw material sourcing challenges, and the potential for regulatory shifts favoring full electrification over hybrids. Supply chains for critical components such as high-power inverters and lithium-ion cells remain vulnerable to global disruptions.
Overall, hybridization hardware is set to play a vital transitional role in decarbonizing heavy transport through the late 2020s. While some risk of technology obsolescence exists, ongoing collaboration between hardware suppliers and vehicle manufacturers positions the sector for resilient growth as regulatory and operational pressures mount.
Sources & References
- Daimler Truck
- Volvo Trucks
- PACCAR
- Allison Transmission
- BorgWarner
- Dana Incorporated
- Robert Bosch GmbH
- Danfoss
- Contemporary Amperex Technology Co., Limited (CATL)
- Schneider Electric
- Infineon Technologies
- ZF Friedrichshafen AG
- DAF Trucks
- Daimler Truck
- Navistar
- FAW Group
- Volvo Group
- Robert Bosch GmbH
- ZF Friedrichshafen AG
- Toyota Motor Corporation
- LG Energy Solution
- Siemens
- STMicroelectronics
- Volvo Group
- Volvo Group
- CNH Industrial
- Maxwell Technologies