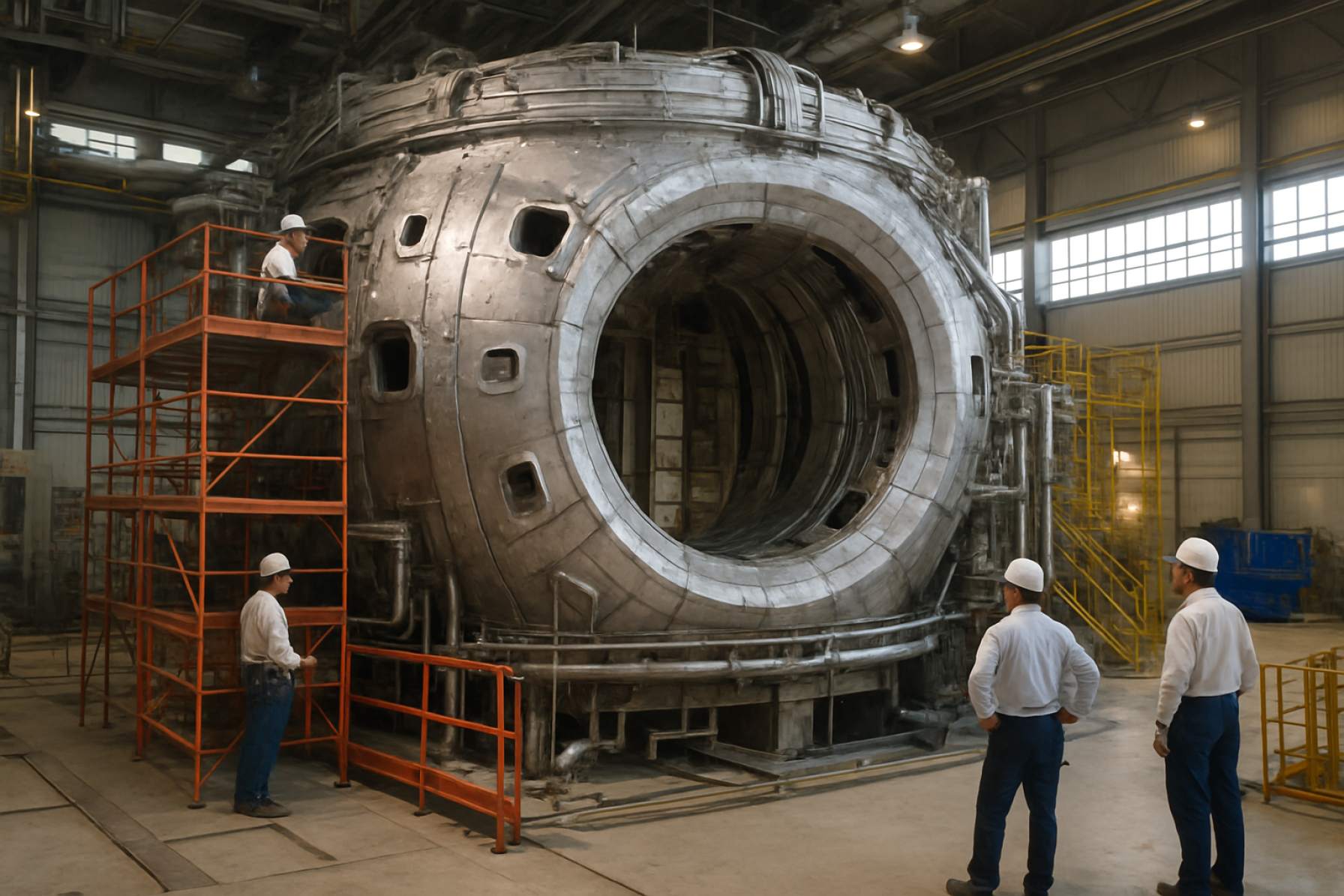
Table of Contents
- Executive Summary: 2025 at the Crossroads of Fusion Engineering
- Market Size & Growth Forecast: 2025–2030
- Key Players and Industry Consortia
- Innovations in Vacuum Vessel Materials and Manufacturing
- Advanced Sealing and Welding Technologies
- Integration with Cryogenic and Magnetic Systems
- Safety, Regulatory, and Standards Landscape
- Supply Chain Dynamics and Strategic Partnerships
- Case Studies: ITER, EAST, and Global Tokamak Projects
- Future Outlook: Next-Gen Designs and Commercialization Pathways
- Sources & References
Executive Summary: 2025 at the Crossroads of Fusion Engineering
In 2025, tokamak vacuum vessel engineering stands at a pivotal juncture, reflecting both the culmination of decades-long innovation and the emergence of new industrial standards. The vacuum vessel, a double-walled, toroidal chamber, is the linchpin of magnetic confinement fusion, providing a high-vacuum environment essential for plasma stability and sustaining the extreme conditions required for fusion reactions. This year marks a significant phase for flagship projects such as ITER, where construction and integration of the vacuum vessel’s final sectors are underway, a process involving global supply chains and unprecedented engineering precision.
Recent achievements include the near-completion of ITER’s 1,200-tonne vacuum vessel sectors, representing some of the largest and most complex stainless steel structures ever fabricated. These sectors, engineered to withstand neutron flux, thermal stresses, and electromagnetic loads, are delivered by industrial leaders such as DOJINDO (Japan), Ansaldo Energia (Italy), and Hyundai Heavy Industries (South Korea), in partnership with European and Asian fusion agencies. The integration efforts in 2025 focus on alignment tolerances within millimeters, leak-testing at ultra-high vacuum, and the installation of in-vessel components that interface with plasma-facing materials and diagnostics.
Technological progress in vessel fabrication centers on advanced welding, non-destructive testing, and real-time digital monitoring, facilitated by automation and robotics. New materials, including low-activation ferritic steels and innovative composite coatings, are being validated to enhance vessel longevity and minimize radioactive waste, aligning with evolving regulatory and sustainability standards set forth by organizations such as Fusion for Energy. Industry-wide, there is a push for digital twin modeling and lifecycle data management to optimize maintenance and enable predictive diagnostics throughout the vessel’s operational life.
Looking forward, the next several years will see the transition from assembly to commissioning and initial plasma operations in ITER, with lessons directly informing the design and procurement strategies for demonstration reactors (DEMO) and national pilot plants. Emerging players—particularly in East Asia—are ramping up domestic tokamak programs, leveraging industrial experience gained from ITER participation. The collaborative model among manufacturers, research institutes, and government agencies is expected to intensify, driving standardization and cost efficiencies across the sector.
In summary, 2025 is a watershed moment for tokamak vacuum vessel engineering, with tangible milestones achieved and a clear trajectory toward scalable, commercially viable fusion energy systems. The sector’s outlook is shaped by a blend of proven industrial capability and ongoing innovation, setting the stage for the next phase of fusion power realization.
Market Size & Growth Forecast: 2025–2030
The market for Tokamak vacuum vessel engineering is poised for steady growth between 2025 and 2030, driven by ongoing international fusion energy projects and the need for increasingly sophisticated containment systems. As of 2025, the sector is primarily propelled by large-scale endeavors such as the ITER project in France, where the vacuum vessel is a critical component for plasma containment and overall reactor safety. ITER’s vacuum vessel, manufactured and assembled through a global collaboration, represents one of the largest and most complex stainless-steel pressure chambers ever built, with a weight of approximately 5,200 tonnes and a volume of 1,400 m³. Major industry participants include United States Department of Energy, Fusion for Energy (the EU’s ITER Domestic Agency), and Hitachi Zosen Corporation, all of whom are actively engaged in vacuum vessel engineering, manufacturing, or component supply.
From 2025 onward, additional growth is expected as new tokamak initiatives progress from conceptual design to construction phases. The Chinese CFETR (China Fusion Engineering Test Reactor) and South Korea’s K-DEMO projects are entering advanced engineering and procurement stages, signaling increased demand for vacuum vessel expertise and supply chain expansion. Korea Institute of Fusion Energy and Institute of Plasma Physics, Chinese Academy of Sciences are key organizations channeling investments into advanced manufacturing techniques, such as precision welding, remote handling, and non-destructive evaluation, to meet strict safety and performance standards.
The market outlook through 2030 is characterized by several emerging trends:
- Adoption of digital engineering and lifecycle management tools to optimize vessel design, monitoring, and maintenance, led by collaborative efforts among fusion agencies and industrial partners.
- Increasing participation from heavy industry manufacturers, particularly in Europe and Asia, who are expanding their fusion engineering portfolios to include vacuum vessel fabrication, integration, and quality assurance.
- Growing collaboration between public-sector research organizations and private fusion ventures, such as those developing compact spherical tokamaks, which is anticipated to diversify technology requirements and market opportunities.
While precise market size figures are proprietary and difficult to disaggregate amidst broader fusion R&D spending, the value of contracts for ITER’s vacuum vessel alone has exceeded €600 million in recent years, with further multi-year procurement opportunities expected across global demonstration and pilot plant programs (Fusion for Energy). As new projects approach the construction phase and as operational experience with first-of-a-kind vessels accumulates, the Tokamak vacuum vessel engineering market is set for measured but robust expansion through 2030.
Key Players and Industry Consortia
The landscape of tokamak vacuum vessel engineering in 2025 is defined by the collaborative efforts of major industrial players, specialized manufacturers, and international consortia that are advancing fusion energy projects worldwide. The engineering and fabrication of vacuum vessels—critical for containing the plasma and maintaining ultra-high vacuum conditions—remains a technologically demanding task, involving large-scale precision manufacturing, advanced welding techniques, and stringent quality assurance.
A central focus in 2025 is the ongoing construction and integration of vacuum vessel sectors for the ITER Organization project in France, currently the world’s largest tokamak. The ITER vacuum vessel, standing at 19.4 meters in diameter and weighing over 5,000 tonnes, has its sectors fabricated by a consortium of suppliers, primarily in South Korea and Europe. Doosan Enerbility (formerly Doosan Heavy Industries & Construction) is a principal contractor, responsible for manufacturing several of the vessel’s massive stainless steel sectors, employing advanced robotic welding and non-destructive examination technologies to meet ITER’s stringent specifications. European efforts are coordinated by Ansaldo Energia and its affiliates, who have played a leading role in the delivery and assembly of European-manufactured vessel segments.
In parallel, the Fusion for Energy (F4E) organization, as the European Union’s body managing Europe’s contribution to ITER, continues to oversee contracts and supply chains, ensuring that complex vessel components—such as port structures, in-wall shielding, and support systems—are delivered on schedule. F4E collaborates closely with a network of European companies, fostering knowledge transfer and industrial capacity for future fusion reactors.
Beyond ITER, private sector entrants are also shaping the field. Companies such as Tokamak Energy in the UK are developing smaller, spherical tokamaks with innovative vacuum vessel designs that emphasize modularity, rapid assembly, and the use of advanced materials to withstand neutron flux. These private initiatives often partner with established heavy engineering companies to prototype next-generation vessel concepts.
Industry consortia, including the EUROfusion consortium, play a pivotal role in coordinating research, design standardization, and pre-commercialization activities across member states. Their coordinated approach to vacuum vessel R&D is expected to accelerate the transition from demonstration-scale projects like ITER to commercial fusion prototypes in the late 2020s and early 2030s.
Looking forward, the global network of tokamak vacuum vessel engineering stakeholders is poised to expand, with new entrants from Asia and North America anticipated as national fusion demonstration projects move from design to construction. The sector’s collaborative model—centered on shared risk, pooled expertise, and joint industrial capacity—will be a critical factor in meeting the technical and logistical challenges of next-generation fusion reactors.
Innovations in Vacuum Vessel Materials and Manufacturing
Innovations in vacuum vessel materials and manufacturing play a critical role in advancing tokamak vacuum vessel engineering, especially as fusion projects worldwide intensify their efforts toward first plasma and beyond. In 2025, significant progress is being made in both material selection and advanced fabrication techniques to address the demanding operational environment inside a tokamak, characterized by extreme temperatures, neutron flux, and structural stresses.
Stainless steel alloys, particularly austenitic grades such as 316LN, continue to be the baseline material for vacuum vessel construction due to their favorable mechanical properties, corrosion resistance, and weldability. However, the need for improved neutron irradiation resistance and reduced activation post-operation has driven research into alternative alloys and optimized compositions. For example, low-cobalt and low-impurity variants are increasingly utilized to minimize long-term radioactive waste, aligning with safety and environmental requirements established by international fusion projects such as ITER and DEMO (ITER Organization).
Manufacturing innovations are equally pivotal. Recent years have seen the adoption of advanced forming and joining techniques, including high-precision electron beam welding and robotic TIG/MIG welding, which ensure the vacuum vessel’s structural integrity and leak tightness at a scale previously unattainable. These technologies are now being deployed at major fusion construction sites, enabling the production of large, complex double-walled vessel segments with integrated cooling channels and diagnostic ports. Notably, additive manufacturing (AM) for specific subcomponents is gaining traction, particularly for intricate cooling passages and support brackets, promising reduced lead times and material waste (EUROfusion).
Another area of innovation is the use of advanced non-destructive evaluation (NDE) methods. Real-time radiography, phased array ultrasonics, and digital twin modeling are increasingly integrated into the quality assurance process, allowing for early detection of micro-defects and continuous monitoring during operation. This is crucial for ensuring the long-term performance of vacuum vessels under cyclic thermal and mechanical loads.
Looking ahead to the next few years, fusion demonstration projects such as ITER and the European DEMO are expected to further accelerate the adoption of these innovations. Collaboration with specialized manufacturers is intensifying, with companies investing in dedicated production lines for large-scale, high-precision vacuum vessel components (Danfysik, Toshiba Energy Systems & Solutions Corporation). The outlook for 2025 and beyond points to increased standardization, digitalization of manufacturing workflows, and broader integration of smart materials tailored for fusion environments, all aimed at supporting the reliable and scalable construction of next-generation tokamaks.
Advanced Sealing and Welding Technologies
The integrity of the vacuum vessel is central to the safety and performance of tokamak fusion reactors. As of 2025, advanced sealing and welding technologies are being prioritized to address the increasing demands for leak-tightness, radiation resistance, and maintainability in next-generation tokamaks. The vacuum vessel for ITER, one of the world’s most ambitious fusion projects, is a prime example: its double-walled, D-shaped structure, weighing over 5,000 tonnes, comprises 9 sectors and hundreds of ports, all requiring precise, high-integrity welding and sealing solutions to sustain ultra-high vacuum and withstand neutron fluxes over decades of operation (Fusion for Energy).
Recent progress has focused on the deployment and refinement of advanced welding methods such as narrow gap TIG (Tungsten Inert Gas) welding, electron beam welding, and laser welding. These techniques are favored for their precision, deep penetration, and low distortion, which are essential for the thick, austenitic stainless steel sections used in vacuum vessels. In the ITER project, narrow gap TIG welding has achieved welds up to 60 mm thick with minimal defects, while remote-operated welding heads are used extensively to access and repair difficult-to-reach seams (ITER Organization). The ongoing development of automated and robotic welding systems is expected to improve both quality assurance and productivity in upcoming projects, such as DEMO and the Chinese CFETR facility.
On the sealing front, metallic seals—particularly Helicoflex and double-convoluted metal gaskets—are now standard, offering superior resistance to outgassing and radiation compared to elastomeric seals. For port and flange connections, the use of all-metal seals is reinforced by rigorous helium leak testing procedures, targeting leak rates below 10-9 mbar·l/s. Suppliers and manufacturers specializing in these sealing systems are collaborating closely with fusion organizations to accelerate testing and qualification for larger-diameter and more complex interfaces anticipated in future reactors (Ansaldo Energia).
Looking forward, the integration of real-time, in-situ inspection methods—such as phased array ultrasonic testing and laser-based metrology—is set to enhance the reliability of welds and seals during vessel assembly and maintenance. As fusion demonstration plants approach construction, the adoption of advanced material joining and sealing technologies will be critical to meeting the operational and regulatory standards necessary for commercial deployment. Collaborative international R&D efforts will continue to drive innovation in this vital aspect of tokamak engineering.
Integration with Cryogenic and Magnetic Systems
The integration of the tokamak vacuum vessel with cryogenic and magnetic systems represents a critical engineering frontier as the fusion industry advances toward commercial viability in 2025 and the near future. The vacuum vessel acts as the primary containment for the plasma, but its successful operation is interdependent with cryogenic cooling required for superconducting magnets, as well as the direct forces imparted by these powerful magnetic systems. In 2025, international flagship projects such as ITER are setting the benchmark for large-scale integration, with lessons directly informing emerging private-sector tokamaks.
Recent milestones include the completion of the ITER vacuum vessel sector assembly and its ongoing integration with the cryostat and poloidal/toroidal field magnets. The vessel must maintain ultra-high vacuum standards while being thermally isolated from the 4 K environment of superconducting magnet windings. This necessitates multi-layer insulation, actively cooled thermal shields, and bellows junctions capable of accommodating differential thermal contraction—a challenge magnified by ITER’s 830 m³ internal vessel volume and the complexity of its port penetrations. The integration is further complicated by the need for remote handling compatibility, as well as neutron shielding and tritium containment requirements (Fusion for Energy).
Looking ahead, the next generation of tokamaks—including projects from companies such as Tokamak Energy and ITER Organization—will increasingly rely on high-temperature superconductors (HTS), which operate at higher cryogenic temperatures (20–77 K). This shift reduces the thermal gradient between magnets and vessel, potentially easing some integration constraints but introducing new engineering variables, such as different thermal cycling behaviors and support structure requirements. HTS adoption also allows for more compact device geometries, amplifying the importance of precise alignment between the vessel, magnets, and cryogenic supports to maintain magnetic field uniformity and plasma stability.
- In 2025, focus remains on robust, leak-tight vessel-to-cryostat interfaces using advanced welding and real-time ultrasonic inspection.
- Enhanced thermal shield designs, frequently utilizing actively cooled stainless steel and aluminum, are being deployed to minimize cryogenic load and protect vessel instrumentation.
- Digital twin models and integrated system simulations are now routinely employed by industry leaders to predict structural deformation and optimize cryogenic-magnetic-vessel interaction under both routine and off-normal events (ITER Organization).
As tokamak demonstrations and pilot plants move forward, the successful integration of vacuum vessels with cryogenic and magnetic systems will remain central to their reliability and economic competitiveness, influencing both capital cost and operational efficiency for fusion power plants in the latter 2020s and beyond.
Safety, Regulatory, and Standards Landscape
The safety, regulatory, and standards landscape for tokamak vacuum vessel engineering is evolving rapidly as large-scale fusion projects approach critical milestones in 2025 and beyond. The vacuum vessel, as the primary containment barrier for plasma and radioactive materials, is subject to stringent safety requirements, with oversight from both national nuclear authorities and international bodies. For example, the International Thermonuclear Experimental Reactor (ITER) project remains the benchmark, setting precedents in its compliance with French nuclear safety regulations (given its location at Cadarache) and harmonizing with international codes such as RCC-MR and ASME standards. ITER’s vacuum vessel has been classified as a nuclear pressure equipment (ESPN), demanding rigorous conformity assessments, extensive material traceability, and comprehensive testing before operation (ITER Organization).
In 2025, regulatory frameworks are being influenced by operational feedback from ITER’s assembly phase and component testing, with particular attention to leak tightness, structural integrity under seismic and thermal loads, and remote handling considerations for maintenance. These requirements are shaping the design and fabrication standards for a new generation of devices, including the UK’s STEP (Spherical Tokamak for Energy Production) and China’s CFETR (China Fusion Engineering Test Reactor), both of which are aligning their safety cases with international best practices while adapting to their respective national regulatory landscapes (United Kingdom Atomic Energy Authority; China Institute of Atomic Energy).
The International Atomic Energy Agency (IAEA) continues to play a central role in fostering harmonization of safety standards, publishing updated guidance on the licensing and regulation of fusion facilities and vacuum pressure boundary components. These guidelines emphasize the importance of deterministic and probabilistic safety analyses, material qualification, and in-service inspection protocols tailored to the unique challenges of fusion environments (International Atomic Energy Agency).
Looking ahead, the next few years will witness increased collaboration between regulatory authorities, fusion research organizations, and major engineering firms such as Framatome and ROSATOM, who provide key components and safety expertise. The emphasis will be on iterative refinement of standards based on operational data, non-destructive testing innovations, and digital twin technologies to support real-time monitoring and predictive maintenance. This evolving landscape is expected to accelerate licensing timelines while maintaining high safety margins, an essential step toward the commercialization of fusion energy.
Supply Chain Dynamics and Strategic Partnerships
The supply chain supporting tokamak vacuum vessel engineering is entering a period of heightened complexity and strategic collaboration as projects like ITER, SPARC, and DEMO drive large-scale demand for high-precision manufacturing and specialized materials. In 2025, the focus is shifting from one-off prototype fabrication to serial production, quality assurance, and risk mitigation for supply disruptions. The ITER project, with its multinational procurement structure, continues to set benchmarks for supply chain integration and engineering standards. Key components, such as the double-walled stainless steel vacuum vessel sectors, are being produced through coordinated efforts between leading heavy industry firms in Europe and Asia, including DOOSAN, Ansaldo Energia, and Siemens.
Strategic partnerships have become essential to ensuring timely delivery and compliance with exacting nuclear-grade specifications. For example, DOOSAN has collaborated with European engineering groups to co-develop advanced welding and non-destructive testing methods, critical for the vessel’s structural integrity. Meanwhile, Ansaldo Energia has leveraged its expertise in large-scale component assembly and logistics to streamline cross-border transport and installation of massive vacuum vessel segments. These alliances are supported by formal agreements and shared quality management frameworks, such as those coordinated by the Fusion for Energy agency, which manages Europe’s contribution to ITER.
Recent years have also witnessed the entry of specialized suppliers for high-performance alloys, precision machining, and advanced sealing technologies. Companies in Japan and South Korea have been instrumental in delivering ultra-low-carbon stainless steel and complex forging products, while European firms provide bespoke vacuum and cryogenic components. The need for redundancy and resilience in the supply chain has prompted initiatives to diversify suppliers and invest in digital traceability, ensuring that critical path items are monitored in real time from fabrication to on-site assembly.
Looking ahead to the next few years, the sector anticipates further consolidation of strategic partnerships and the integration of digital supply chain management platforms. The adoption of advanced simulation, remote inspection, and automated welding technologies is expected to enhance both productivity and quality assurance. As follow-on projects like DEMO and commercial pilot plants ramp up, the lessons learned from ITER’s multinational supply chain are likely to incentivize early engagement between technology developers, heavy industry, and specialist suppliers—setting a new standard for global collaboration in tokamak vacuum vessel engineering.
Case Studies: ITER, EAST, and Global Tokamak Projects
The period from 2025 onward marks a pivotal phase in tokamak vacuum vessel engineering, with significant case studies underway at flagship projects such as ITER, EAST, and emerging global tokamaks. These projects collectively represent the state-of-the-art in vacuum vessel design, manufacturing, and integration—each facing unique challenges due to scale, operational requirements, and the drive for efficient assembly and maintenance.
ITER, the world’s largest tokamak under construction in France, continues to set benchmarks in vacuum vessel engineering. As of 2025, the assembly of ITER’s 9-segment stainless steel vacuum vessel nears completion, with emphasis on precision manufacturing and high-integrity welds to withstand operational pressures and neutron flux. Each sector, weighing approximately 440 tonnes, is manufactured by industrial consortia in Europe, Korea, and India, requiring advanced transport and alignment solutions for integration. The vessel’s double-walled structure, with built-in cooling channels for nuclear heating mitigation, is a milestone in fusion engineering. Leak-tightness and dimensional accuracy remain under constant verification as ITER moves toward its First Plasma milestone, targeted for late 2025 or early 2026 (Fusion for Energy; ITER Organization).
In China, the Experimental Advanced Superconducting Tokamak (EAST) continues to pioneer operational advancements in vacuum vessel design, focusing on long-pulse plasma scenarios. EAST’s vessel, a D-shaped, fully welded structure, has successfully supported 1,000+ second plasma discharges, demonstrating the importance of robust water-cooling and remote handling features for in-vessel component maintenance. The vessel’s adaptability—accommodating upgrades such as advanced first wall and divertor modules—serves as a reference for future projects like CFETR (China Fusion Engineering Test Reactor), which will demand even larger, more complex vacuum vessel assemblies (Institute of Plasma Physics, Chinese Academy of Sciences).
Globally, projects such as JT-60SA in Japan and SPARC in the United States are advancing vacuum vessel methodologies tailored for rapid assembly and high-performance operation. JT-60SA, commissioned in 2023, has validated modular vessel construction and integrated diagnostics, providing valuable lessons for the European DEMO and other next-generation reactors. Meanwhile, private-sector initiatives are collaborating with established suppliers for advanced materials, high-precision welding, and digital twin integration to accelerate vessel fabrication and reduce commissioning timelines (National Institutes for Quantum Science and Technology; Commonwealth Fusion Systems).
Looking ahead, the next few years will see the refinement of manufacturing automation, real-time monitoring, and remote maintenance technologies in vacuum vessel engineering. These advances, driven by lessons from ITER, EAST, and global collaborators, will be crucial for scaling up to demonstration and commercial fusion plants.
Future Outlook: Next-Gen Designs and Commercialization Pathways
The outlook for tokamak vacuum vessel engineering in 2025 and the subsequent years is shaped by the convergence of advanced materials science, manufacturing innovation, and the drive toward commercial fusion energy. As flagship projects like ITER move closer to first plasma, the lessons learned and breakthroughs achieved are informing the design philosophy of next-generation commercial reactors.
One of the most significant recent trends is the adoption of modular design principles and advanced manufacturing techniques, such as precision robotic welding and large-scale additive manufacturing. These approaches aim to reduce both the complexity and cost of future vacuum vessel fabrication. For instance, major suppliers are actively developing automated welding and inspection systems to meet the stringent tolerances and safety requirements of double-walled, actively cooled vacuum vessel structures envisioned for DEMO-class reactors.
Material innovation also continues to play a central role. While ITER employs 316L(N) stainless steel with optimized low-cobalt content for neutron activation resistance, research is intensifying into reduced activation ferritic-martensitic steels and novel alloys to further extend vessel lifetime and support higher neutron fluxes expected in commercial plants. Organizations such as EUROfusion are coordinating multi-national R&D programs for next-gen vessel materials and joining techniques, targeting the specific demands of DEMO and beyond.
The path to commercialization is also prompting greater collaboration between public fusion initiatives and industrial partners. Leading engineering firms and pressure vessel manufacturers are expanding their capabilities to meet the scale and quality requirements for fusion applications. Companies like Ansaldo Energia and Damen are contributing expertise in heavy component fabrication and systems integration, anticipating the transition from prototype to serial production as commercial fusion projects emerge in the late 2020s.
Key challenges for the coming years include ensuring regulatory harmonization for fusion-specific vessel codes and developing robust, scalable quality assurance regimes. International forums, under the coordination of organizations such as the International Atomic Energy Agency, are facilitating the exchange of best practices and standards harmonization.
Overall, the next several years will witness rapid evolution in vacuum vessel engineering, driven by the imperative to enable safe, cost-effective, and scalable commercial fusion. The interplay of advanced manufacturing, improved materials, and expanded industrial participation is expected to position the sector for key milestones on the path to practical fusion power.
Sources & References
- DOJINDO
- Ansaldo Energia
- Hyundai Heavy Industries
- Fusion for Energy
- Hitachi Zosen Corporation
- Korea Institute of Fusion Energy
- ITER Organization
- Doosan Enerbility
- Tokamak Energy
- EUROfusion
- EUROfusion
- Danfysik
- Fusion for Energy
- Tokamak Energy
- ITER Organization
- International Atomic Energy Agency
- Framatome
- Siemens
- National Institutes for Quantum Science and Technology
- Commonwealth Fusion Systems
- Damen