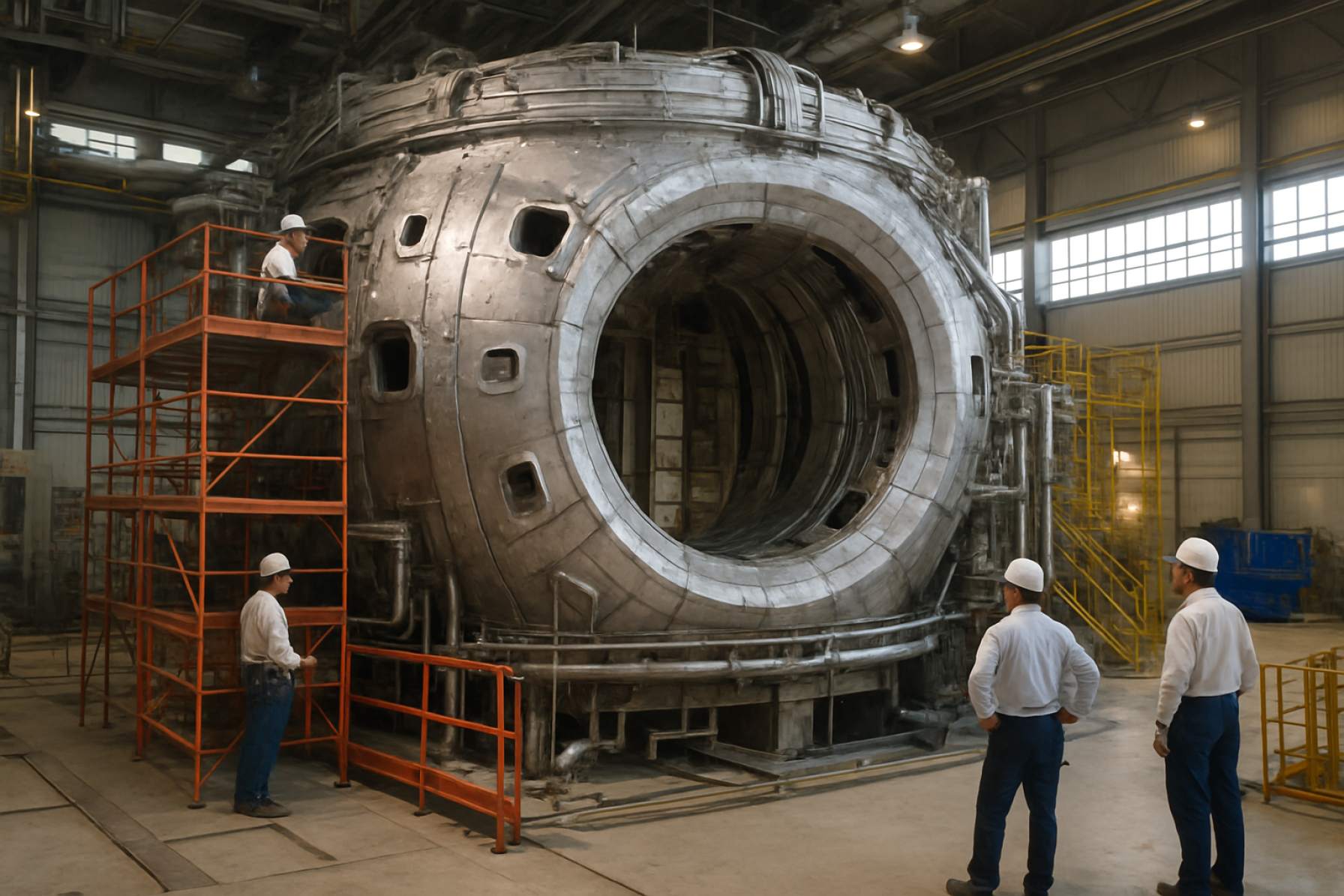
Inhaltsverzeichnis
- Zusammenfassung: 2025 an der Wegscheide der Fusionsengineering
- Marktgröße & Wachstumsprognose: 2025–2030
- Wichtige Akteure und Branchenkonsortien
- Innovationen in Vakuumgefäßmaterialien und -fertigung
- Fortgeschrittene Dichtungs- und Schweißtechnologien
- Integration mit kryogenen und magnetischen Systemen
- Sicherheits-, Regulierungs- und Normenlandschaft
- Lieferketten-Dynamik und strategische Partnerschaften
- Fallstudien: ITER, EAST und globale Tokamak-Projekte
- Zukunftsausblick: Nächste Generation Designs und Kommerzialisierungspfade
- Quellen & Referenzen
Zusammenfassung: 2025 an der Wegscheide der Fusionsengineering
Im Jahr 2025 steht das Engineering von Tokamak-Vakuumgefäßen an einem entscheidenden Punkt, der sowohl den Höhepunkt jahrzehntelanger Innovation als auch das Entstehen neuer industrieweiter Standards widerspiegelt. Das Vakuumgefäß, eine doppelwandige, toroidale Kammer, ist das Bindeglied der magnetischen Einschlussfusion und bietet ein Hochvakuumumfeld, das für die Plasmastabilität und die extreme Bedingungen, die für Fusionsreaktionen erforderlich sind, unerlässlich ist. Dieses Jahr markiert eine bedeutende Phase für Flagship-Projekte wie ITER, bei denen der Bau und die Integration der finalen Sektoren des Vakuumgefäßes im Gange sind, ein Prozess, der globale Lieferketten und beispiellose Ingenieursgenauigkeit erfordert.
Zu den jüngsten Errungenschaften gehört die nahezu vollständige Fertigstellung der 1.200 Tonnen schweren Sektoren des ITER-Vakuumgefäßes, die einige der größten und komplexesten Edelstahlstrukturen darstellen, die je gefertigt wurden. Diese Sektoren, die so konzipiert sind, dass sie Neutronenfluss, thermischen Spannungen und elektromagnetischen Belastungen standhalten, werden von Industriegrößen wie DOJINDO (Japan), Ansaldo Energia (Italien) und Hyundai Heavy Industries (Südkorea) in Partnerschaft mit europäischen und asiatischen Fusionsbehörden geliefert. Die Integrationsbemühungen im Jahr 2025 konzentrieren sich auf Ausrichtungs-Toleranzen im Millimeterbereich, Leckage-Tests im Ultra-Hochvakuum und die Installation von Komponenten im Gefäß, die mit plasma-beständigen Materialien und Diagnosen interagieren.
Der technologische Fortschritt in der Gefäßfertigung konzentriert sich auf fortschrittliches Schweißen, zerstörungsfreie Prüfung und digitales Monitoring in Echtzeit, unterstützt durch Automatisierung und Robotik. Neue Materialien, einschließlich niedrig aktivierender ferritischer Stähle und innovativer Verbundbeschichtungen, werden validiert, um die Langlebigkeit des Gefäßes zu erhöhen und radioaktiven Abfall zu minimieren, im Einklang mit sich entwickelnden regulatorischen und Nachhaltigkeitsstandards, die von Organisationen wie Fusion for Energy festgelegt wurden. Branchenweit gibt es einen Push für digitale Zwillingsmodellierung und Lebenszyklus-Datenmanagement, um Wartung zu optimieren und prädiktive Diagnosen während der Betriebszeit des Gefäßes zu ermöglichen.
Insgesamt wird in den nächsten Jahren der Übergang von der Montage zur Inbetriebnahme und zu den anfänglichen Plasma-Betriebsphasen bei ITER zu beobachten sein, wobei die daraus gewonnenen Erkenntnisse direkt das Design und die Beschaffungsstrategien für Demonstrationsreaktoren (DEMO) und nationale Pilotanlagen beeinflussen werden. Aufstrebende Akteure, insbesondere in Ostasien, verstärken ihre inländischen Tokamak-Programme, indem sie die industrielle Erfahrung aus der ITER-Teilnahme nutzen. Das kollaborative Modell zwischen Herstellern, Forschungsinstituten und Regierungsbehörden wird voraussichtlich intensiver werden und die Standardisierung und Kosteneffizienz im gesamten Sektor vorantreiben.
Zusammenfassend lässt sich sagen, dass 2025 ein Wendepunkt für das Engineering von Tokamak-Vakuumgefäßen ist, mit greifbaren Meilensteinen und einem klaren Weg hin zu skalierbaren, kommerziell tragfähigen Fusionsenergieträgersystemen. Die Perspektiven des Sektors sind geprägt von einer Mischung aus bewährter industrieller Fähigkeit und fortlaufender Innovation, die die Bühne für die nächste Phase der Realisierung der Fusionskraft bereitet.
Marktgröße & Wachstumsprognose: 2025–2030
Der Markt für Tokamak-Vakuumgefäßengineering ist von 2025 bis 2030 auf stetiges Wachstum ausgerichtet, getrieben von laufenden internationalen Fusionsenergieprojekten und dem Bedarf an immer anspruchsvolleren Einschlusssystemen. Ab 2025 wird der Sektor hauptsächlich durch groß angelegte Vorhaben wie das ITER-Projekt in Frankreich angetrieben, bei dem das Vakuumgefäß ein kritischer Bestandteil für die Plasmasicherung und die allgemeine Reaktorsicherheit ist. Das Vakuumgefäß von ITER, das durch eine globale Zusammenarbeit hergestellt und assembliert wird, stellt eine der größten und komplexesten Edelstahl-Druckkammern dar, die je gebaut wurde, mit einem Gewicht von etwa 5.200 Tonnen und einem Volumen von 1.400 m³. Zu den Hauptakteuren der Branche gehören das US-Energieministerium, Fusion for Energy (die nationale Behörde der EU für ITER) und Hitachi Zosen Corporation, die alle aktiv im Bereich Vakuumgefäßengineering, -fertigung oder -komponentenzulieferung tätig sind.
Von 2025 an wird ein zusätzliches Wachstum erwartet, da neue Tokamak-Initiativen von der konzeptionellen Design- in die Bauphasen übergehen. Die chinesischen CFETR (China Fusion Engineering Test Reactor) und Südkoreas K-DEMO-Projekte treten in fortgeschrittene Ingenieur- und Beschaffungsphasen ein, was auf eine steigende Nachfrage nach Fachwissen und eine Erweiterung der Lieferkette für Vakuumgefäße hinweist. Korea Institute of Fusion Energy und das Institut für Plasmaphysik der Chinesischen Akademie der Wissenschaften sind Schlüsselorganisationen, die Investitionen in fortschrittliche Fertigungstechniken, wie präzises Schweißen, Fernhandling und zerstörungsfreie Bewertung, lenken, um strengen Sicherheits- und Leistungsstandards gerecht zu werden.
Der Marktausblick bis 2030 wird von mehreren aufkommenden Trends geprägt sein:
- Einführung digitaler Ingenieuranwendungen und Lebenszyklusmanagement-Tools zur Optimierung des Gefäßdesigns, der Überwachung und der Wartung, angeführt durch kooperative Bemühungen zwischen Fusionsbehörden und Industriepartnern.
- Zunehmende Beteiligung von Herstellern aus der Schwerindustrie, insbesondere in Europa und Asien, die ihre Portfolios im Bereich Fusionsengineering um die Herstellung, Integration und Qualitätssicherung von Vakuumgefäßen erweitern.
- Wachsende Zusammenarbeit zwischen öffentlich-rechtlichen Forschungseinrichtungen und privaten Fusionsunternehmen, wie beispielsweise solche, die kompakte sphärische Tokamaks entwickeln, was voraussichtlich die Technologieforderungen und Marktchancen diversifizieren wird.
Obwohl genaue Marktgrößenangaben proprietär und schwer zu differenzieren sind angesichts breiterer Fusions-F&E-Ausgaben, hat der Wert der Verträge für das ITER-Vakuumgefäß allein in den letzten Jahren die 600 Millionen Euro-Grenze überschritten, wobei weitere mehrjährige Beschaffungsmöglichkeiten bei globalen Demonstrations- und Pilotprogrammen erwartet werden (Fusion for Energy). Da neue Projekte die Bauphasen erreichen und operative Erfahrungen mit einzigartigen Gefäßen gesammelt werden, wird der Markt für Tokamak-Vakuumgefäßengineering voraussichtlich bis 2030 ein gemessenes, aber robustes Wachstum erfahren.
Wichtige Akteure und Branchenkonsortien
Die Landschaft des Tokamak-Vakuumgefäßengineering im Jahr 2025 wird durch die gemeinsamen Anstrengungen bedeutender Industriekonzerne, spezialisierter Hersteller und internationaler Konsortien geprägt, die Fusionsenergieprojekte weltweit vorantreiben. Das Engineering und die Fertigung von Vakuumgefäßen – die für die Eindämmung des Plasmas und die Aufrechterhaltung von ultrahohen Vakuumbedingungen von entscheidender Bedeutung sind – bleibt eine technologisch anspruchsvolle Aufgabe, die groß angelegte Präzisionsfertigung, fortgeschrittene Schweißtechniken und strenge Qualitätssicherung umfasst.
Ein zentrales Augenmerk im Jahr 2025 liegt auf dem ongoing Bau und der Integration von Vakuumgefäßsektoren für das ITER-Organisationsprojekt in Frankreich, derzeit der weltweit größte Tokamak. Das ITER-Vakuumgefäß, das einen Durchmesser von 19,4 Metern hat und über 5.000 Tonnen wiegt, wird von einem Konsortium von Lieferanten, hauptsächlich in Südkorea und Europa, hergestellt. Doosan Enerbility (ehemals Doosan Heavy Industries & Construction) ist ein Hauptauftragnehmer, der für die Herstellung mehrerer großer Edelstahlsektoren des Gefäßes verantwortlich ist und dabei fortschrittliche Roboter-Schweiß- und zerstörungsfreie Untersuchungstechnologien einsetzt, um den strengen Spezifikationen von ITER gerecht zu werden. Die europäischen Bemühungen werden von Ansaldo Energia und seinen Tochtergesellschaften koordiniert, die eine führende Rolle bei der Lieferung und Montage der in Europa gefertigten Gehäuseteile spielen.
Parallel sorgt die Fusion for Energy (F4E)-Organisation, als das Organ der Europäischen Union, das den Beitrag Europas zu ITER verwaltet, weiterhin dafür, dass komplexe Gefäßkomponenten – wie Portstrukturen, Wandabschirmungen und Unterstützungssysteme – termingerecht geliefert werden. F4E arbeitet eng mit einem Netzwerk europäischer Unternehmen zusammen und fördert den Wissenstransfer und die industrielle Fähigkeit für zukünftige Fusionsreaktoren.
Über ITER hinaus gestalten auch private Sektoren das Feld. Unternehmen wie Tokamak Energy im Vereinigten Königreich entwickeln kleinere, sphärische Tokamaks mit innovativen Vakuumgefäßdesigns, die Modularität, schnelle Montage und den Einsatz fortschrittlicher Materialien zur Widerstandsfähigkeit gegenüber Neutronenfluss betonen. Diese privaten Initiativen arbeiten häufig mit etablierten Schwerbauunternehmen zusammen, um Prototypen der Gefäßkonzepte der nächsten Generation zu entwickeln.
Branchenkonsortien, darunter das EUROfusion-Konsortium, spielen eine entscheidende Rolle bei der Koordination von Forschung, Normierung des Designs und vorkommerziellen Aktivitäten in den Mitgliedsstaaten. Ihr koordinierter Ansatz zur Forschung und Entwicklung von Vakuumgefäßen wird voraussichtlich den Übergang von Demonstrationsprojekten wie ITER zu kommerziellen Fusionsprototypen Ende der 2020er und Anfang der 2030er Jahre beschleunigen.
In Zukunft wird das globale Netzwerk von Akteuren im Tokamak-Vakuumgefäßengineering voraussichtlich wachsen, wobei neue Teilnehmer aus Asien und Nordamerika erwartet werden, da nationale Fusionsdemonstrationsprojekte vom Design in den Bau übergehen. Das kollaborative Modell des Sektors – zentriert auf gemeinsames Risiko, gebündeltes Fachwissen und gemeinsame industrielle Kapazitäten – wird ein entscheidender Faktor bei der Bewältigung der technischen und logistischen Herausforderungen der Reaktoren der nächsten Generation sein.
Innovationen in Vakuumgefäßmaterialien und -fertigung
Innovationen in Vakuumgefäßmaterialien und -fertigung spielen eine entscheidende Rolle bei der Weiterentwicklung des Tokamak-Vakuumgefäßengineering, insbesondere da Fusionsprojekte weltweit ihre Anstrengungen in Richtung des ersten Plasmas und darüber hinaus intensivieren. Im Jahr 2025 werden erhebliche Fortschritte sowohl bei der Materialauswahl als auch bei fortschrittlichen Fertigungstechniken erzielt, um das anspruchsvolle Betriebsumfeld in einem Tokamak, das durch extreme Temperaturen, Neutronenfluss und strukturelle Spannungen gekennzeichnet ist, anzugehen.
Edelstahllegierungen, insbesondere austenitische Sorten wie 316LN, bleiben das Basis-Material für den Bau von Vakuumgefäßen aufgrund ihrer vorteilhaften mechanischen Eigenschaften, ihrer Korrosionsbeständigkeit und ihrer Schweißbarkeit. Der Bedarf an verbesserter Neutronenstrahlung Beständigkeit und verringerter Aktivierung nach dem Betrieb hat jedoch die Forschung in Richtung alternativer Legierungen und optimierter Zusammensetzungen vorangetrieben. Beispielsweise werden zunehmend legierungsarme und reinheitsarme Varianten verwendet, um langlebigen radioaktiven Abfall zu minimieren, was mit den Sicherheits- und Umweltanforderungen übereinstimmt, die von internationalen Fusionsprojekten wie ITER und DEMO festgelegt wurden (ITER-Organisation).
Fertigungsinnovationen sind ebenso entscheidend. In den letzten Jahren wurden fortschrittliche Formen- und Verbindungstechniken eingeführt, einschließlich hochpräziser Elektronenstrahlschweiß- und robotergeführter TIG/MIG-Schweißverfahren, die die strukturelle Integrität und Dichtheit des Vakuumgefäßes in einem bisher unerreichten Maß sicherstellen. Diese Technologien werden jetzt an großen Fusionsbaustellen eingesetzt, um große, komplexe doppelwandige Gefäßsegmente mit integrierten Kühlkanälen und Diagnoseanschlüssen zu produzieren. Insbesondere gewinnt die additive Fertigung (AM) für spezifische Unterkomponenten an Bedeutung, insbesondere für komplizierte Kühlkanäle und Tragstrukturen, was verspricht, die Vorlaufzeiten und Materialabfälle zu reduzieren (EUROfusion).
Ein weiterer Innovationsbereich ist der Einsatz fortschrittlicher zerstörungsfreier Prüfverfahren (NDE). Echtzeitradiografie, Phased Array-Ultraschall und digitale Zwillingsmodellierung werden zunehmend in den Qualitätssicherungsprozess integriert, um frühzeitige Mikrodefekte zu erkennen und kontinuierliches Monitoring während des Betriebs zu ermöglichen. Dies ist entscheidend, um die langfristige Leistung von Vakuumgefäßen unter zyklischen thermischen und mechanischen Lasten sicherzustellen.
Blickt man in die nächsten Jahre, wird erwartet, dass Fusionsdemonstrationsprojekte wie ITER und das europäische DEMO die Einführung dieser Innovationen weiter beschleunigen werden. Die Zusammenarbeit mit spezialisierten Herstellern intensiviert sich, wobei Unternehmen in spezielle Produktionslinien für großangelegte, hochpräzise Vakuumgefäßkomponenten investieren (Danfysik, Toshiba Energy Systems & Solutions Corporation). Die Perspektiven für 2025 und darüber hinaus deuten auf eine erhöhte Standardisierung, Digitalisierung von Fertigungsabläufen und breitere Integration von intelligenten Materialien hin, die auf Fusionsumgebungen abgestimmt sind, alles zielt darauf ab, den zuverlässigen und skalierbaren Aufbau zukünftiger Tokamaks zu unterstützen.
Fortgeschrittene Dichtungs- und Schweißtechnologien
Die Integrität des Vakuumgefäßes ist zentral für die Sicherheit und Leistung von Tokamak-Fusionsreaktoren. Im Jahr 2025 stehen fortschrittliche Dichtungs- und Schweißtechnologien im Vordergrund, um den steigenden Anforderungen an Dichtheit, Strahlungsbeständigkeit und Wartungsfreundlichkeit in Tokamaks der nächsten Generation gerecht zu werden. Das Vakuumgefäß für ITER, eines der weltweit ehrgeizigsten Fusionsprojekte, ist ein herausragendes Beispiel: Seine doppelwandige, D-förmige Struktur, die mehr als 5.000 Tonnen wiegt, besteht aus 9 Sektoren und Hunderten von Anschlüssen, die alle präzise, hochintegrierte Schweiß- und Dichtungslösungen benötigen, um ein ultrahohes Vakuum aufrechtzuerhalten und über Jahrzehnte Neutronenfluss standzuhalten (Fusion for Energy).
Jüngste Fortschritte haben sich auf die Einführung und Verfeinerung fortschrittlicher Schweißmethoden wie Schweißen mit engem Spalt-TIG (Tungsten Inert Gas), Elektronenstrahlschweißen und Laserschweißen konzentriert. Diese Techniken werden wegen ihrer Präzision, tiefen Durchdringungen und geringen Verzerrungen geschätzt, die für die dicken austenitischen Edelstahlabschnitte, die in Vakuumgefäßen verwendet werden, von entscheidender Bedeutung sind. Im ITER-Projekt hat das Schweißen mit engem Spalt-TIG Schweißnähte von bis zu 60 mm Dicke mit minimalen Fehlern erreicht, während fernbediente Schweißköpfe ausgiebig eingesetzt werden, um schwer zugängliche Nähte zu erreichen und zu reparieren (ITER-Organisation). Die laufende Entwicklung automatisierter und robotergeführter Schweißsysteme wird erwartet, um sowohl die Qualitätssicherung als auch die Produktivität in kommenden Projekten wie DEMO und der chinesischen CFETR-Anlage zu verbessern.
Im Bereich Dichtungen sind metallische Dichtungen – insbesondere Helicoflex und doppelt gewickelte Metallgasketten – jetzt Standard und bieten im Vergleich zu elastomerischen Dichtungen überlegene Beständigkeit gegenüber Ausgasung und Strahlung. Bei Port- und Flanschverbindungen wird der Einsatz von Vollmetall-Dichtungen durch strenge Helium-Leckagetests verstärkt, die auf Leckraten unter 10-9 mbar·l/s abzielen. Anbieter und Hersteller, die auf diese Dichtungssysteme spezialisiert sind, arbeiten eng mit Fusionsorganisationen zusammen, um Tests und Qualifizierungen für größere Durchmesser und komplexere Schnittstellen zu beschleunigen, die in zukünftigen Reaktoren erwartet werden (Ansaldo Energia).
Blickt man in die Zukunft, werden die Integration von Echtzeit-, in-situ Inspektionsmethoden – wie Phased Array-Ultraschallprüfungen und laserbasierter Messtechnik – die Zuverlässigkeit von Schweißnähte und Dichtungen während der Gefäßmontage und Wartung weiter erhöhen. Wenn Fusionsdemonstrationsanlagen den Bau erreichen, wird die Einführung fortschrittlicher Materialverbindungen und Dichtungstechnologien entscheidend sein, um die Betriebs- und Regulierungsstandards für die kommerzielle Bereitstellung zu erfüllen. Collaborative internationale F&E-Bemühungen werden weiterhin Innovationen in diesem wichtigen Aspekt des Tokamak-Engineering vorantreiben.
Integration mit kryogenen und magnetischen Systemen
Die Integration des Tokamak-Vakuumgefäßes mit kryogenen und magnetischen Systemen stellt eine kritische Ingenieursgrenze dar, während die Fusionsindustrie 2025 und in der nahen Zukunft in Richtung kommerzieller Machbarkeit voranschreitet. Das Vakuumgefäß fungiert als primäre Eindämmung für das Plasma, jedoch ist sein erfolgreicher Betrieb abhängig von der kryogenen Kühlung, die für supraleitende Magnete erforderlich ist, sowie von den direkten Kräften, die von diesen leistungsstarken magnetischen Systemen ausgeübt werden. Im Jahr 2025 setzen internationale Flagship-Projekte wie ITER Maßstäbe für die großangelegte Integration, wobei Erkenntnisse direkt die aufkommenden Tokamaks im privaten Sektor informieren.
Zu den jüngsten Meilensteinen gehört der Abschluss der Montage des ITER-Vakuumgefäßsektors und dessen fortlaufende Integration mit dem Kryostaten und den poloidalen/torroidalen Feldmagneten. Das Gefäß muss ultrahohes Vakuumniveau aufrechterhalten, während es thermisch von der 4 K-Umgebung der supraleitenden Magnetwicklungen isoliert ist. Dies erfordert mehrlagige Isolierung, aktiv gekühlte thermische Abschirmungen und Balgverbindungen, die in der Lage sind, unterschiedliche thermische Kontraktionen auszugleichen – eine Herausforderung, die durch das 830 m³ große Innenvolumen des Gefäßes und die Komplexität seiner Portdurchdringungen verschärft wird. Die Integration wird weiter kompliziert durch die Notwendigkeit der Kompatibilität mit Fernbedienung sowie Anforderungen an Neutronenabschirmung und Tritiumeindämmung (Fusion for Energy).
In den kommenden Jahren wird die nächste Generation von Tokamaks – einschließlich Projekte von Unternehmen wie Tokamak Energy und ITER-Organisation – zunehmend auf hochempfindliche Hochtemperatursupraleiter (HTS) angewiesen sein, die bei höheren kryogenen Temperaturen (20–77 K) betrieben werden. Dieser Wechsel reduziert den Temperaturgradienten zwischen Magneten und Gefäß, was möglicherweise einige Integrationsbeschränkungen erleichtert, jedoch neue Ingenieurvariablen wie unterschiedliche thermische Zyklen und Unterstützungsgestellanforderungen einführt. Die Einführung von HTS ermöglicht auch kompaktere Gerätestrukturen, wodurch die genaue Ausrichtung zwischen dem Gefäß, den Magneten und den kryogenen Unterstützungen, um die Homogenität des Magnetfeldes und die Plasmastabilität aufrechtzuerhalten, an Bedeutung gewinnt.
- Im Jahr 2025 bleibt der Fokus auf robusten, dichten Gefäß-zu-Kryostaten-Schnittstellen unter Verwendung fortschrittlicher Schweiß- und Echtzeitsulfurinspektion.
- Verstärkte thermische Abdichtungsdesigns, die häufig aktiv gekühlten Edelstahl und Aluminium verwenden, werden eingesetzt, um die kryogene Belastung zu minimieren und die Instrumentierung des Gefäßes zu schützen.
- Digitale Zwillingsmodelle und integrierte Systemsimulationen werden jetzt routinemäßig von Branchenführern eingesetzt, um strukturelle Verformungen vorherzusagen und die Interaktion zwischen kryogenen, magnetischen und Gefäßsystemen unter normalen und außerordentlichen Bedingungen zu optimieren (ITER-Organisation).
Wenn Tokamak-Demonstrationen und Pilotanlagen voranschreiten, wird die erfolgreiche Integration von Vakuumgefäßen mit kryogenen und magnetischen Systemen zentral für ihre Zuverlässigkeit und wirtschaftliche Wettbewerbsfähigkeit bleiben und sowohl die Investitionskosten als auch die Betriebseffizienz von Fusionskraftwerken in den späten 2020er Jahren und darüber hinaus beeinflussen.
Sicherheits-, Regulierungs- und Normenlandschaft
Die Sicherheits-, Regulierungs- und Normenlandschaft für Tokamak-Vakuumgefäßengineering entwickelt sich rasant weiter, während großangelegte Fusionsprojekte im Jahr 2025 und darüber hinaus kritische Meilensteine erreichen. Das Vakuumgefäß, das die primäre Eindämmungsbarriere für Plasma und radioaktive Materialien darstellt, unterliegt strengen Sicherheitsanforderungen, die sowohl von nationalen Atomaufsichtsbehörden als auch von internationalen Gremien überwacht werden. Zum Beispiel bleibt das Projekt International Thermonuclear Experimental Reactor (ITER) der Maßstab, wobei es Präzedenzfälle hinsichtlich der Einhaltung französischer nuklearer Sicherheitsvorschriften (angesichts seines Standorts in Cadarache) und in Einklang mit internationalen Normen wie RCC-MR und ASME-Standards schafft. Das Vakuumgefäß von ITER wurde als nukleares Druckequipment (ESPN) klassifiziert, was anspruchsvolle Konformitätsbewertungen, umfassende Materialnachverfolgbarkeit und umfassende Tests vor dem Betrieb erfordert (ITER-Organisation).
Im Jahr 2025 werden die regulatorischen Rahmenbedingungen durch operationale Rückmeldungen aus der Assemblierungsphase und der Komponentenprüfung von ITER beeinflusst, wobei besonderes Augenmerk auf Dichtheit, strukturelle Integrität unter seismischen und thermischen Lasten und Fernhandhabungskriterien für die Wartung gelegt wird. Diese Anforderungen prägen die Design- und Fertigungsstandards für eine neue Generation von Geräten, einschließlich des UK’s STEP (Spherical Tokamak for Energy Production) und Chinas CFETR (China Fusion Engineering Test Reactor), die beide ihre Sicherheitskonzepte an internationalen Best Practices orientieren, während sie sich gleichzeitig an ihre jeweiligen nationalen Regulierungslandschaften anpassen (UK Atomic Energy Authority; China Institute of Atomic Energy).
Die Internationale Atomenergie-Organisation (IAEA) spielt weiterhin eine zentrale Rolle bei der Förderung der Harmonisierung von Sicherheitsstandards und veröffentlicht aktualisierte Richtlinien zur Lizenzierung und Regulierung von Fusionsanlagen und Vakuum-Druckgrenzkomponenten. Diese Richtlinien betonen die Wichtigkeit von deterministischen und probabilistischen Sicherheitsanalysen, Materialqualifikationen und In-Service-Prüfungen, die speziell auf die einzigartigen Herausforderungen von Fusionsumgebungen abgestimmt sind (Internationale Atomenergie-Organisation).
Blickt man in die nächsten Jahre, wird eine verstärkte Zusammenarbeit zwischen Regulierungsbehörden, Fusionsforschungsorganisationen und großen Ingenieurunternehmen wie Framatome und ROSATOM, die Schlüsselkomponenten und Sicherheitsexpertise bereitstellen, zu erwarten sein. Der Fokus wird auf der iterativen Verfeinerung von Standards basierend auf operationalen Daten, Innovationen in der zerstörungsfreien Prüfung und digitalen Zwillings-Technologien liegen, um Echtzeit-Überwachung und prädiktive Wartung zu unterstützen. Diese sich weiterentwickelnde Landschaft wird voraussichtlich die Lizenzierungsfristen beschleunigen, während hohe Sicherheitsmargen gewährleistet werden, ein wesentlicher Schritt in Richtung Kommerzialisierung der Fusionsenergie.
Lieferketten-Dynamik und strategische Partnerschaften
Die Lieferkette, die das Tokamak-Vakuumgefäßengineering unterstützt, befindet sich in einer Phase erhöhter Komplexität und strategischer Zusammenarbeit, da Projekte wie ITER, SPARC und DEMO eine groß angelegte Nachfrage nach hochpräziser Fertigung und spezialisierten Materialien erzeugen. Im Jahr 2025 verlagert sich der Fokus von einmaliger Prototypenfertigung hin zu Serienproduktion, Qualitätssicherung und Risikominderung bei Lieferunterbrechungen. Das ITER-Projekt, mit seiner multinationalen Beschaffungsstruktur, setzt weiterhin Maßstäbe für die Integration der Lieferkette und Ingenieurstandards. Wichtige Komponenten wie die doppelwandigen Edelstahl-Vakuumgefäßsektoren werden durch koordinierte Bemühungen zwischen führenden Schwerindustriefirmen in Europa und Asien hergestellt, einschließlich DOOSAN, Ansaldo Energia und Siemens.
Strategische Partnerschaften sind unerlässlich geworden, um rechtzeitige Lieferung und Einhaltung strenger nuklearer Spezifikationen zu gewährleisten. Beispielsweise hat DOOSAN mit europäischen Ingenieuregruppen zusammengearbeitet, um fortgeschrittene Schweiß- und zerstörungsfreie Prüfmethoden zu entwickeln, die für die strukturelle Integrität des Gefäßes entscheidend sind. Unterdessen hat Ansaldo Energia sein Fachwissen in der Großkomponentenmontage und Logistik genutzt, um den grenzüberschreitenden Transport und die Installation von massiven Vakuumgefäßsegmenten zu optimieren. Diese Allianzen werden durch formale Vereinbarungen und gemeinsame Qualitätsmanagement-Rahmen unterstützt, wie sie von der Fusion for Energy-Behörde koordiniert werden, die Europas Beitrag zu ITER verwaltet.
In den letzten Jahren haben auch spezialisierte Zulieferer für Hochleistungslegierungen, Präzisionsmechanik und fortschrittliche Dichtungstechnologien an Bedeutung gewonnen. Unternehmen in Japan und Südkorea haben eine Schlüsselrolle bei der Lieferung von ultraniedrigem Kohlenstoff-Edelstahl und komplexen Schmiedewaren gespielt, während europäische Firmen maßgeschneiderte Vakuum- und kryogene Komponenten bereitstellen. Der Bedarf an Redundanz und Resilienz in der Lieferkette hat Initiativen angestoßen, um Lieferanten zu diversifizieren und in digitale Nachverfolgbarkeit zu investieren, um sicherzustellen, dass kritische Prozess-Elemente in Echtzeit von der Fertigung bis zur Montage vor Ort überwacht werden.
Blickt man in die nächsten Jahre, rechnet der Sektor mit einer weiteren Konsolidierung strategischer Partnerschaften und der Integration digitaler Lieferkettenmanagement-Plattformen. Die Einführung fortschrittlicher Simulation, Ferninspektions- und automatisierter Schweißtechnologien wird voraussichtlich sowohl die Produktivität als auch die Qualitätssicherung verbessern. Sobald Folgeprojekte wie DEMO und kommerzielle Pilotanlagen starten, werden die Lehren aus der multinationalen Lieferkette von ITER voraussichtlich Anreize für eine frühe Einbindung zwischen Technologieträgern, Schwerindustrie und Spezialzulieferern schaffen – und einen neuen Standard für globale Zusammenarbeit im Tokamak-Vakuumgefäßengineering setzen.
Fallstudien: ITER, EAST und globale Tokamak-Projekte
Der Zeitraum von 2025 an markiert eine entscheidende Phase im Tokamak-Vakuumgefäßengineering, mit bedeutenden Fallstudien, die bei Flagship-Projekten wie ITER, EAST und aufstrebenden globalen Tokamaks durchgeführt werden. Diese Projekte repräsentieren gemeinsam den Stand der Technik im Design, der Herstellung und Integration von Vakuumgefäßen – jedes bringt aufgrund von Größe, Betriebsanforderungen und dem Streben nach effizienter Montage und Wartung einzigartige Herausforderungen mit sich.
ITER, der größte Tokamak der Welt, der derzeit in Frankreich gebaut wird, setzt weiterhin Maßstäbe im Engineering von Vakuumgefäßen. Ab 2025 steht die Montage des 9-Segment-Edelstahl-Vakuumgefäßes von ITER kurz vor dem Abschluss, wobei der Fokus auf präziser Fertigung und hochintegren Schweißverbindungen liegt, um Betriebdruck und Neutronenfluss standzuhalten. Jeder Sektor, der etwa 440 Tonnen wiegt, wird von Industriekonsortien in Europa, Korea und Indien hergestellt, was fortgeschrittene Transport- und Ausrichtungslösungen für die Integration erfordert. Die doppelwandige Struktur des Gefäßes, die integrierte Kühlkanäle zur Minderung der nuklearen Wärmeabsorption integriert, ist ein Meilenstein im Fusionsengineering. Dichtheit und dimensionaler Genauigkeit werden ständig überprüft, während ITER auf den Meilenstein „Erstes Plasma“ zusteuert, der für Ende 2025 oder Anfang 2026 geplant ist (Fusion for Energy; ITER-Organisation).
In China entwickelt der Experimental Advanced Superconducting Tokamak (EAST) weiterhin operationale Fortschritte im Design von Vakuumgefäßen und konzentriert sich auf Langzeit-Plasma-Szenarien. Das Gefäß von EAST, eine D-förmige, vollgeschweißte Struktur, hat erfolgreich über 1.000 Sekunden Plasmaentladungen unterstützt und demonstriert die Bedeutung robuster Wasser-Kühl- und Fernhandhabungsfunktionen für die Wartung von In-Vessel-Komponenten. Die Anpassungsfähigkeit des Gefäßes — Anpassungen wie fortschrittliche erste Wand und Divertormodule sind berücksichtigt — dient als Referenz für zukünftige Projekte wie CFETR (China Fusion Engineering Test Reactor), die sogar größere, komplexere Vakuumgefäßmontagen erfordern werden (Institut für Plasmaphysik, Chinesische Akademie der Wissenschaften).
Weltweit treiben Projekte wie JT-60SA in Japan und SPARC in den USA die Methoden von Vakuumgefäßen voran, die auf schnelle Montage und Hochleistungsbetrieb zugeschnitten sind. JT-60SA, die 2023 in Betrieb genommen wurden, haben die modulare Gefäßkonstruktion und integrierte Diagnostik validiert und wertvolle Lehren für das europäische DEMO und andere Reaktoren der nächsten Generation geliefert. Inzwischen arbeiten private Initiativen mit etablierten Zulieferern für fortschrittliche Materialien, hochpräzises Schweißen und die Integration digitaler Zwillinge zusammen, um die Gefäßfertigung zu beschleunigen und die Inbetriebnahmezeiten zu verkürzen (Nationale Institute für Quantenwissenschaft und Technologie; Commonwealth Fusion Systems).
In der Zukunft erwarten wir in den nächsten Jahren die Verfeinerung von Automatisierung in der Fertigung, Echtzeitüberwachung und Technologien zur Fernwartung im Vakuumgefäßengineering. Diese Fortschritte, die aus den Erfahrungen mit ITER, EAST und globalen Partnern hervorgehen, werden entscheidend sein, um den Maßstab für Demonstrations- und kommerzielle Fusionskraftanlagen zu erhöhen.
Zukunftsausblick: Nächste Generation Designs und Kommerzialisierungspfade
Die Perspektiven für das Tokamak-Vakuumgefäßengineering im Jahr 2025 und den folgenden Jahren werden durch die Zusammenführung von fortschrittlicher Materialwissenschaft, Fertigungsinnovation und dem Streben nach kommerzieller Fusionsenergie geprägt. Während Flagship-Projekte wie ITER näher an das erste Plasma rücken, informieren die gewonnenen Erkenntnisse und erreichten Durchbrüche die Designphilosophie künftiger kommerzieller Reaktoren.
Einer der bedeutendsten jüngsten Trends ist die Übernahme modularer Entwurfsprinzipien und fortschrittlicher Fertigungstechniken, wie präzises robotergeführtes Schweißen und großangelegte additive Fertigung. Diese Ansätze zielen darauf ab, sowohl die Komplexität als auch die Kosten der zukünftigen Fertigung von Vakuumgefäßen zu reduzieren. Beispielsweise entwickeln große Zulieferer aktiv automatisierte Schweiß- und Inspektionssysteme, um den strengen Toleranzen und Sicherheitsanforderungen der doppelwandigen, aktiv gekühlten Vakuumgefäßstrukturen, die für DEMO-Klasse-Reaktoren vorgesehen sind, gerecht zu werden.
Materialsinnovationen spielen ebenfalls eine zentrale Rolle. Während ITER 316L(N)-Edelstahl mit optimierter niedriger Kobaltgehalt zur Neutronenaktivierungsbeständigkeit verwendet, intensiviert sich die Forschung in Richtung reduzierter Aktivierung ferritisch-martensitischer Stähle und neuartiger Legierungen, um die Lebensdauer des Gefäßes weiter zu verlängern und höhere Neutronenflüsse zu unterstützen, die in kommerziellen Anlagen erwartet werden. Organisationen wie EUROfusion koordinieren multinationalen F&E-Programme für die Materialanforderungen und Verbindungstechniken der nächsten Generation, die speziell auf die Anforderungen von DEMO und darüber hinaus abzielen.
Der Weg zur Kommerzialisierung fördert auch eine größere Zusammenarbeit zwischen öffentlichen Fusionsinitiativen und industriellen Partnern. Führende Ingenieure und Druckbehälterhersteller erweitern ihre Fähigkeiten, um den Maßstab und die Qualitätsanforderungen für Fusionsanwendungen zu erfüllen. Unternehmen wie Ansaldo Energia und Damen bringen Expertise in der Fertigung schwerer Komponenten und Systemintegration ein und erwarten den Übergang von Prototypen zu Serienproduktionen, da kommerzielle Fusionsprojekte in den späten 2020er Jahren auftauchen.
Schlüsselherausforderungen für die kommenden Jahre bestehen darin, die regulatorische Harmonisierung für fusionsspezifische Gefäßcodes sicherzustellen und robuste, skalierbare Qualitätsüberprüfungsregime zu entwickeln. Internationale Foren, unter der Koordination von Organisationen wie der International Atomic Energy Agency, erleichtern den Austausch von Best Practices und die Harmonisierung von Standards.
Insgesamt werden die kommenden Jahre eine rasche Entwicklung im Vakuumgefäßengineering mit sich bringen, angetrieben von der Notwendigkeit, eine sichere, kosteneffektive und skalierbare kommerzielle Fusion zu ermöglichen. Das Zusammenspiel von fortschrittlicher Fertigung, verbesserten Materialien und erweiteter industrieller Beteiligung wird voraussichtlich den Sektor auf wichtige Meilensteine auf dem Weg zur praktischen Fusionskraft positionieren.
Quellen & Referenzen
- DOJINDO
- Ansaldo Energia
- Hyundai Heavy Industries
- Fusion for Energy
- Hitachi Zosen Corporation
- Korea Institute of Fusion Energy
- ITER Organisation
- Doosan Enerbility
- Tokamak Energy
- EUROfusion
- EUROfusion
- Danfysik
- Fusion for Energy
- Tokamak Energy
- ITER Organisation
- Internationale Atomenergie-Organisation
- Framatome
- Siemens
- Nationale Institute für Quantenwissenschaft und Technologie
- Commonwealth Fusion Systems
- Damen