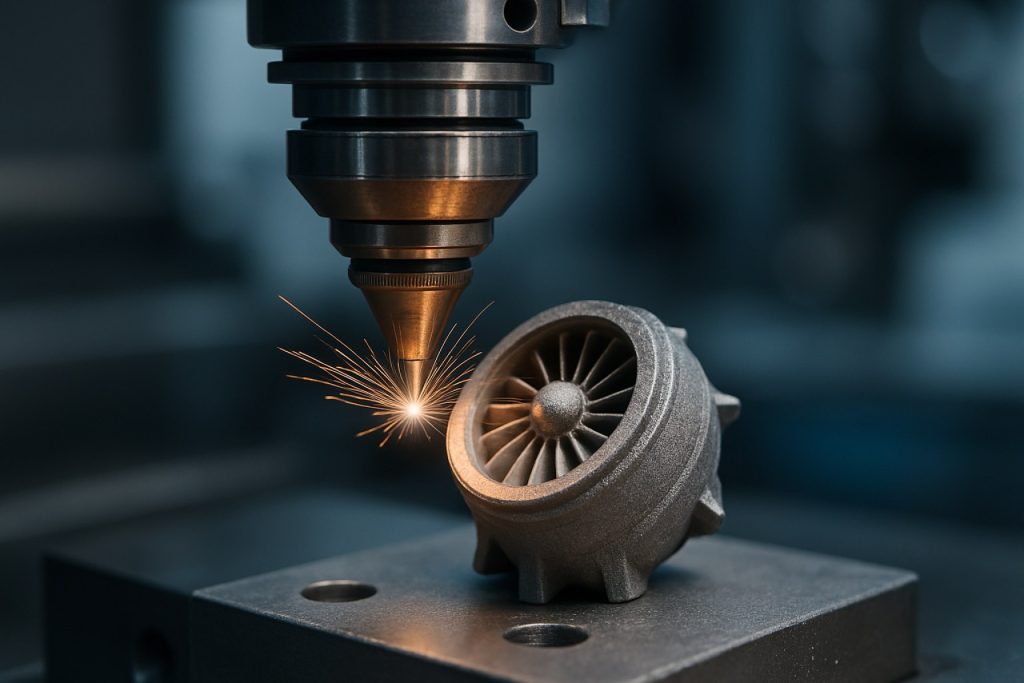
Table of Contents
- Executive Summary: Aerojet Engine Microfabrication in 2025
- Market Size and Growth Forecast: 2025–2030
- Key Players and Industry Collaborations
- Microfabrication Technologies Revolutionizing Aerojet Engines
- Material Science Advances: Alloys, Ceramics, and Composites
- Manufacturing Challenges and Solutions
- Applications in Commercial, Defense, and Space Sectors
- Regulatory Landscape and Industry Standards
- Investment Trends and Funding Insights
- Future Outlook: Disruptive Innovations and Competitive Dynamics
- Sources & References
Executive Summary: Aerojet Engine Microfabrication in 2025
Aerojet engine microfabrication is rapidly reshaping the aerospace propulsion landscape in 2025, driven by the demand for higher efficiency, reduced weight, and improved reliability in both commercial and defense sectors. Microfabrication—encompassing techniques such as micro-electrical discharge machining (micro-EDM), laser ablation, and advanced additive manufacturing—enables the creation of intricate engine components at the micron scale, which were previously impossible or highly cost-prohibitive with traditional manufacturing methods.
The year 2025 marks a significant inflection point for adoption, with major propulsion system OEMs and suppliers accelerating investments in microfabrication facilities and processes. Companies such as GE Aerospace and Rolls-Royce continue to develop and implement microfabrication for next-generation jet engine parts, particularly turbine blades, fuel injectors, and microchannel heat exchangers. These advancements not only enhance engine performance and efficiency but also extend component lifespans and reduce maintenance intervals.
Adoption is further propelled by successful pilot programs and production runs that have demonstrated significant performance gains. For example, microfabricated cooling channels in turbine blades have allowed for higher operating temperatures, directly translating to improved thrust-to-weight ratios and lower fuel consumption. Such innovations are closely tied to stringent emissions targets and sustainability mandates from regulatory bodies, compelling manufacturers to adopt microfabrication to meet future environmental standards.
The supply chain for microfabricated aerojet engine parts is becoming increasingly robust, with key material suppliers such as Honeywell investing in specialized alloys and ceramic composites tailored for micro-scale features. Concurrently, machine tool manufacturers and process technology firms are rolling out new platforms designed specifically for aerospace microfabrication, emphasizing precision, repeatability, and scalability.
Looking ahead to the next few years, the outlook for aerojet engine microfabrication is highly positive. Industry forecasts and ongoing R&D suggest that by 2027–2028, microfabricated components will become commonplace in both commercial and military engine programs, with production volumes expected to rise as cost barriers continue to fall. Collaborative efforts between engine OEMs, material specialists, and academic institutions are also accelerating the pace of innovation, with a focus on digital design integration, real-time process monitoring, and automated quality assurance.
In summary, 2025 stands as a pivotal year for aerojet engine microfabrication, with industry leaders and suppliers committed to scaling up these transformative technologies, setting the stage for a new era of propulsion efficiency, durability, and sustainability.
Market Size and Growth Forecast: 2025–2030
The global market for aerojet engine microfabrication is poised for significant growth between 2025 and 2030, driven by increasing demand for fuel-efficient, lower-emission propulsion systems in both commercial and defense aerospace sectors. Microfabrication techniques—such as advanced additive manufacturing, micro-electro-mechanical systems (MEMS) integration, and precision laser machining—are being integrated into the core manufacturing processes of next-generation jet engines to enable lightweight, high-performance components. Key industry players are investing in scaling up production capacities and developing new material systems to meet the evolving requirements of aerospace propulsion.
As of 2025, leading aeroengine manufacturers including GE Aerospace, Rolls-Royce, and Pratt & Whitney are leveraging microfabrication to enhance component miniaturization, improve cooling channel geometries, and optimize fuel nozzle designs. For example, microfabricated components in fuel injection systems and turbine blades have yielded measurable improvements in thermal efficiency and emissions reduction. These advances are supported by collaborations with specialist suppliers such as Safran and MTU Aero Engines, who are also expanding their microfabrication capabilities.
Market expansion is closely linked to the wider adoption of additive manufacturing and laser-based micro-drilling for producing precision engine features at scale. According to statements from GE Aerospace and Rolls-Royce, a growing proportion of new engine parts—especially for narrowbody and regional aircraft—will incorporate microfabricated elements by 2030. This is expected to drive a compound annual growth rate (CAGR) in the high single digits for the aerojet engine microfabrication segment throughout the period.
- North America and Europe will remain the principal markets, supported by ongoing fleet renewals and stringent emissions regulations.
- Asia-Pacific is anticipated to see the fastest uptake, as regional aircraft production and defense modernization programs expand.
- Investments in R&D and new production lines by major OEMs and suppliers are forecast to accelerate throughout the forecast period, with high-value contracts already reported for microfabricated turbine and combustor components.
Looking ahead, the market outlook for 2025–2030 is robust, with microfabrication poised to become a standard in aerojet engine design and production. The convergence of regulatory pressure, material innovation, and maturing manufacturing technologies is expected to sustain growth and intensify competition among established and emerging industry participants.
Key Players and Industry Collaborations
The landscape of aerojet engine microfabrication in 2025 is shaped by a combination of established aerospace manufacturers, innovative suppliers, and cross-sector collaborations. Key players are investing in advanced microfabrication to enhance propulsion efficiency, reduce emissions, and enable new engine architectures for both commercial and defense aerospace markets.
Among the global leaders, GE Aerospace continues to spearhead microfabrication initiatives, leveraging additive manufacturing (AM) and micro-electromechanical systems (MEMS) for turbine components and fuel injectors. Their sustained investment in AM technology enables the production of intricate cooling channels and optimized geometries at micron scales, supporting both large engine lines and emerging small-scale propulsion systems. Rolls-Royce is similarly active, with its ongoing collaborations with materials technology firms and research institutions to refine micro-scale manufacturing processes for high-temperature alloys and ceramic matrix composites. These efforts are critical for next-generation engines emphasizing fuel efficiency and reduced weight.
On the supplier front, Oxford Instruments and Precision Micro are prominent in providing microfabrication tools and photochemical etching services, respectively. Their technologies enable engine OEMs to realize ultra-fine tolerances in miniaturized components such as micro-nozzles, sensors, and heat exchangers. Honeywell Aerospace, another major player, integrates MEMS-based sensors fabricated at micro-scales into their engine control and health monitoring systems, signaling a trend toward digitalization and data-driven maintenance.
Industry collaborations are gaining momentum as companies seek to accelerate innovation and share the high costs associated with microfabrication R&D. For example, joint ventures between prime engine manufacturers and semiconductor foundries are emerging to transfer microelectronics fabrication expertise into the aerospace sector. Additionally, partnerships with national research labs and universities—such as those fostered by NASA—are facilitating the transfer of microfabrication techniques from the laboratory to commercial engine platforms.
Looking forward, the next few years are likely to witness increasing investment in integrated supply chains, with OEMs deepening relationships with microfabrication specialists to enable mass production of complex, miniaturized engine parts. As environmental regulations tighten, the role of microfabrication in achieving higher fuel efficiency and emissions compliance will further incentivize collaboration and technological advancement across the industry.
Microfabrication Technologies Revolutionizing Aerojet Engines
The rapid evolution of microfabrication technologies is fundamentally transforming the development and performance of aerojet engines as the aerospace sector enters 2025. Traditional manufacturing methods are increasingly being supplanted by advanced micro-scale processes that enable the production of highly complex, precise, and lightweight engine components. A major driver of this shift is the adoption of additive manufacturing (AM), commonly known as 3D printing, particularly through techniques such as selective laser melting (SLM) and electron beam melting (EBM). These processes allow for the fabrication of intricate fuel injectors, turbine blades, and cooling channels with internal geometries that were previously impossible to realize using conventional subtractive methods.
Leading propulsion companies are now deploying microfabrication to reduce weight and improve thermal efficiencies. For instance, GE Aerospace has successfully integrated AM-produced fuel nozzles into its LEAP engines, achieving a 25% weight reduction and a fivefold increase in durability compared to traditionally manufactured counterparts. The company continues to expand its use of microfabrication for next-generation components, focusing on tighter tolerances and reduced lead times. Similarly, Rolls-Royce is investing in microfabricated turbine parts, leveraging lattice structures and advanced cooling channels to push the boundaries of engine efficiency and lifespan.
The role of micro-electromechanical systems (MEMS) in aerojet engines is also growing, with component miniaturization enabling improved sensing, monitoring, and actuation within harsh engine environments. Companies like Safran are advancing MEMS-based sensor arrays for real-time data acquisition, driving predictive maintenance and greater operational safety. The integration of MEMS into propulsion systems is anticipated to become more widespread as production scalability and reliability improve in the next few years.
Looking ahead, the continued maturation of microfabrication technologies is expected to accelerate innovation in aerojet engine design and manufacturing through 2025 and beyond. The emergence of novel materials, such as heat-resistant superalloys and ceramic matrix composites, in conjunction with precision microfabrication, will further enhance performance metrics. Industry analysts predict a growing ecosystem of dedicated suppliers and partners specializing in micro-scale aerospace components, with sustained investment from major players like Pratt & Whitney and MTU Aero Engines poised to drive adoption across both commercial and defense aviation sectors.
Material Science Advances: Alloys, Ceramics, and Composites
In 2025, the microfabrication of aerojet engine components is experiencing significant advancements in material science, particularly with the integration of novel alloys, ceramics, and composite materials. The continual push for higher efficiency, reduced weight, and enhanced thermal resilience in aerojet propulsion systems has driven research and industrial adoption of cutting-edge materials and innovative manufacturing techniques.
Advanced nickel-based superalloys remain the backbone of turbine section fabrication due to their exceptional mechanical strength and resistance to high-temperature degradation. However, ongoing developments are focusing on improving creep resistance and oxidation protection at operating temperatures exceeding 1200°C. Companies such as GE Aerospace and Rolls-Royce are actively developing new alloy formulations with tailored microstructures enabled by additive manufacturing. Electron beam melting and laser powder bed fusion are now routinely used to produce turbine blades and vanes with complex internal cooling passages at the microscale, enhancing thermal performance while reducing component mass.
Ceramic matrix composites (CMCs) have transitioned from experimental to commercial application in hot-section components. Silicon carbide-based CMCs, for example, offer weight savings of up to 30% over traditional alloys and can operate at temperatures 200–300°C higher than their metallic counterparts. In 2025, Safran and GE Aerospace continue to expand the deployment of CMCs in combustor liners and turbine shrouds, enabled by advances in fiber architecture, interfacial coatings, and scalable fabrication techniques such as chemical vapor infiltration and slurry infiltration.
Composites reinforced with nanomaterials—such as carbon nanotubes and graphene—are also under active investigation for their potential to further reduce weight while improving mechanical and thermal properties. Manufacturers are collaborating with materials science institutes to optimize dispersion and alignment of nanoreinforcements within metal and ceramic matrices, aiming for commercial maturity within the next several years.
Looking ahead, the outlook for aerojet engine microfabrication is centered on the convergence of advanced materials and digital manufacturing. Real-time process monitoring, in-line quality control, and AI-driven microstructural optimization are expected to accelerate the qualification and integration of next-generation alloys, CMCs, and hybrid composites. This synergy will not only enable engines with higher thrust-to-weight ratios and fuel efficiency but also support the aviation industry’s sustainability goals through longer component lifespans and reduced raw material usage. As these technologies mature, leading industry players such as GE Aerospace, Rolls-Royce, and Safran are poised to set new standards in aerojet propulsion performance and reliability.
Manufacturing Challenges and Solutions
Aerojet engine microfabrication is at the forefront of propulsion innovation, enabling heightened efficiency, reduced emissions, and lower weight in next-generation aerospace systems. As 2025 approaches, the sector faces both persistent and emerging manufacturing challenges, notably in achieving high-precision fabrication, material compatibility, thermal management, and scalable production.
One of the most significant hurdles involves the precise machining of micro-scale features for components such as fuel injectors, turbine blades, and microchannel heat exchangers. Tolerances at the micron level are required to ensure optimal combustion and efficiency, but traditional subtractive manufacturing methods reach their limits in accuracy and repeatability. In response, advanced additive manufacturing (AM) techniques—such as laser powder bed fusion (LPBF) and electron beam melting—are being deployed by companies including GE Aerospace and Rolls-Royce, allowing for the production of intricate geometries previously unattainable. In 2023, GE Aerospace reported success in printing turbine blade tips with integrated cooling channels, reducing part counts and improving lifecycle performance.
Material selection and compatibility present another ongoing challenge. Aerojet engines demand superalloys and ceramic matrix composites that withstand extreme temperatures and corrosive environments while maintaining microstructural integrity during microfabrication processes. Safran continues to invest in advanced powder metallurgy and hybrid manufacturing techniques, aiming to combine the thermal resilience of ceramics with the mechanical strength of metals for microfabricated engine parts.
Thermal management is critical at the micro-scale, as heat concentration can lead to microcracks or material warping. To address this, manufacturers are integrating real-time thermal monitoring and closed-loop feedback systems during fabrication. Siemens is developing digital twins and in-situ process controls that predict and compensate for thermal distortions, improving yield and repeatability.
Scalability remains a central concern as demand for advanced aerojet engines grows, particularly in commercial aviation and space exploration. Collaborative efforts like the Airbus “Wing of Tomorrow” program are fostering knowledge-sharing and standardization in microfabrication processes, aiming to accelerate the transition from prototyping to full-scale production.
Looking ahead to the next few years, the outlook is optimistic. Continued convergence of digital manufacturing, advanced materials, and process automation is expected to further mitigate current challenges. As these technologies mature, industry leaders anticipate reductions in both cost and cycle time, paving the way for broader adoption of microfabricated aerojet engine components in mainstream aerospace applications.
Applications in Commercial, Defense, and Space Sectors
Aerojet engine microfabrication is experiencing rapid advancements across commercial aviation, defense, and space sectors, driven by the demand for higher efficiency, reduced component weight, and greater design complexity. As of 2025, industry leaders are leveraging microfabrication techniques such as additive manufacturing, laser-based micromachining, and advanced etching to create intricate engine parts with unprecedented precision and reliability. These methods allow for the production of micro-scale features, including cooling channels, fuel injectors, and turbine blades, which are critical for improving thermal management and combustion efficiency in modern aerojet engines.
In the commercial aviation sector, manufacturers are adopting microfabrication to support the development of next-generation engines aimed at reducing fuel consumption and emissions. For example, companies like GE Aerospace and Rolls-Royce Holdings are actively integrating microengineered components into their new engine platforms. These efforts are aligned with industry-wide goals to meet stricter environmental regulations and improve overall fleet performance. Microfabricated parts, such as fuel nozzles and microchannel heat exchangers, are being validated for durability and performance, with initial production runs anticipated to scale up through the latter half of the decade.
In the defense sector, microfabrication is enhancing the agility and survivability of military aircraft and missile systems. Programs led by organizations like Northrop Grumman and RTX Corporation are employing miniaturized propulsion systems and micro-thrusters for precision-guided munitions and unmanned aerial vehicles (UAVs). These components benefit from microfabrication’s ability to deliver lightweight, compact designs without compromising power or reliability. The U.S. Department of Defense is expected to expand contracts focused on microfabricated propulsion solutions, aiming for field deployment in late 2020s.
The space sector is also capitalizing on microfabrication to advance the design of satellite propulsion systems and deep-space exploration vehicles. Companies such as Aerojet Rocketdyne are developing micro-propulsion units that enable precise maneuvering of small satellites and CubeSats. These systems, which rely on microfabricated thrusters and fluidic control devices, are set for commercial launches and constellation deployments beginning in 2025 and continuing to expand in the following years.
Looking ahead, the integration of microfabricated aerojet engine components is projected to accelerate as material science innovations and digital manufacturing platforms mature. Industry collaborations and public-private partnerships will likely play a vital role in scaling up these technologies for widespread application, ensuring that commercial, defense, and space stakeholders maintain a competitive edge in propulsion performance and sustainability.
Regulatory Landscape and Industry Standards
The regulatory landscape for aerojet engine microfabrication is evolving rapidly as the aerospace industry increasingly adopts advanced manufacturing techniques such as micro-electro-mechanical systems (MEMS), additive manufacturing, and precision micro-machining. In 2025, oversight is guided by a combination of established aerospace standards and emerging frameworks tailored to address the unique challenges and risks presented by micro-scale fabrication processes.
Key regulatory bodies such as the Federal Aviation Administration (FAA) and the European Union Aviation Safety Agency (EASA) continue to set baseline safety and quality standards for aircraft engines, which now encompass components produced by microfabrication. Both organizations require that manufacturers demonstrate the reliability and repeatability of microfabricated parts through rigorous testing, documentation, and traceability protocols. As microfabrication enables the production of intricate cooling channels, fuel nozzles, and sensor arrays with unprecedented precision, these agencies are updating certification guidelines to address potential new failure modes and inspection challenges unique to micro-scale structures.
The SAE International continues to play a central role in standardizing microfabrication processes. Recent updates to standards such as AS9100 and AS9110 now include specific provisions for additive and microfabrication process control, material traceability, and inspection requirements. In 2025, efforts are underway to harmonize these standards globally to facilitate international supply chains and certification reciprocity. Industry groups are also collaborating with regulatory agencies to establish new test methods for microfabricated engine components, focusing on fatigue life, thermal cycling, and defect detection at micro scales.
Leading aerojet engine manufacturers, including GE Aerospace and Rolls-Royce, are actively engaging with regulators and standard bodies to shape requirements that support innovation while maintaining safety. These companies have invested in digital quality management systems and in-house certification expertise, anticipating that regulatory scrutiny will intensify as microfabricated components become increasingly mission-critical. Notably, as these manufacturers push the boundaries of design with micro-scale features, they are supporting the creation of new non-destructive evaluation (NDE) protocols and qualification procedures tailored to the unique geometries and material properties of microfabricated parts.
Looking ahead, the next several years are expected to see the introduction of more granular process certification pathways, increased emphasis on digital twins and process simulation for regulatory compliance, and the adoption of real-time monitoring and traceability tools. The dynamic regulatory landscape will require ongoing collaboration between OEMs, suppliers, and standards organizations to ensure safe, repeatable, and economically viable deployment of aerojet engine microfabrication technologies.
Investment Trends and Funding Insights
Aerojet engine microfabrication—encompassing advanced manufacturing approaches like additive manufacturing, laser micromachining, and precision etching—has seen a notable influx of investment activity as the aerospace sector pushes for lighter, more efficient propulsion systems. In 2025, the field is characterized by a blend of government-backed initiatives, strategic corporate funding, and venture capital targeting both established aerospace primes and agile startups.
A significant driver of current investment is the increasing demand for high-thrust, compact propulsion units in both commercial and defense applications. Major engine manufacturers are scaling their microfabrication capabilities to reduce part count, improve fuel efficiency, and enable complex cooling geometries previously unachievable with traditional methods. GE Aerospace and RTX are among the most active, channeling R&D budgets to expand microfabrication lines and partner with specialist suppliers. In parallel, governmental funding—especially from agencies such as the U.S. Department of Defense and European Space Agency—continues to underwrite advances in miniaturized propulsion for satellites and hypersonic vehicles.
The trend toward public-private partnerships is accelerating. In 2025, co-investment models have become common, with entities like NASA supporting demonstration projects that de-risk novel microfabrication techniques for aerojet components. These collaborations are not only fostering technical breakthroughs but also catalyzing private follow-on funding. Emerging players, including university spinouts and microfabrication specialists, are benefiting from seed and Series A rounds provided by aerospace-focused venture funds and corporate venture arms of major primes.
Data from ongoing funding rounds suggests that capital is flowing into areas such as high-temperature ceramics, microchannel heat exchangers, and integrated thrust vectoring nozzles—key components enabled by advanced microfabrication. Suppliers specializing in laser and electron-beam additive processes are reporting order backlogs and expansion plans, driven by multi-year procurement agreements from OEMs and Tier 1 suppliers. For example, Safran and Rolls-Royce have both announced increased investment in in-house and partner-led microfabrication capability to support next-generation engine programs.
Looking ahead to the next several years, the investment outlook remains robust. The convergence of digital design, automation, and real-time process monitoring is expected to further reduce development cycles and manufacturing costs. As regulatory bodies move toward certifying microfabricated aerojet engine parts for broader flight applications, the sector is likely to see sustained, diversified investment—positioning microfabrication as a central pillar of propulsion innovation through the late 2020s.
Future Outlook: Disruptive Innovations and Competitive Dynamics
The landscape of aerojet engine microfabrication in 2025 is poised for significant transformation, driven by disruptive innovations in additive manufacturing, advanced materials, and digital twin technologies. A key trend is the integration of microfabrication techniques—such as laser powder bed fusion and micro-electrical discharge machining (micro-EDM)—into the serial production of engine components with complex geometries and enhanced performance characteristics. Leading engine manufacturers and suppliers are intensifying investments in these microfabrication capabilities to achieve lighter, more fuel-efficient engines with reduced emissions.
Companies like GE Aerospace and Rolls-Royce plc are at the forefront of developing microfabricated jet engine parts, including micro-nozzles, fuel injectors, and cooling channels. In 2025, ongoing projects in these organizations emphasize precision manufacturing at sub-millimeter scales, leveraging in-situ monitoring and AI-driven process controls to ensure quality and repeatability. The adoption of additively manufactured micro-components is expected to expand across both commercial and defense aviation sectors, offering up to 30% reductions in part count and significant improvements in engine thermodynamic efficiency.
Material science breakthroughs are also shaping the future outlook. The introduction of high-temperature ceramic matrix composites and novel superalloys, enabled by microfabrication, is allowing for thinner walls and more intricate internal cooling passages—key to withstanding higher operating temperatures. Safran and Pratt & Whitney are actively advancing research partnerships to scale up production of such components, aiming to deliver engines with improved durability and lower lifecycle costs by 2027.
The competitive dynamics are intensifying as OEMs and key suppliers race to secure intellectual property and qualification for new microfabricated parts. There is growing collaboration between engine manufacturers and specialized fabrication firms, such as Siemens, which is leveraging its expertise in digital manufacturing and process automation to support rapid prototyping and certification of critical engine structures. Simultaneously, the emergence of start-ups and university spin-offs focusing on novel microfabrication processes is expected to further disrupt supply chains and push innovation cycles.
Looking ahead, the next few years will be marked by accelerated certification pathways for microfabricated aerojet engine components, spurred by digital twin validation and real-time inspection systems. Industry stakeholders anticipate that by 2030, microfabrication will underpin the majority of next-generation aerojet engine architectures, fundamentally altering design possibilities and driving a new era of sustainable, high-performance flight.