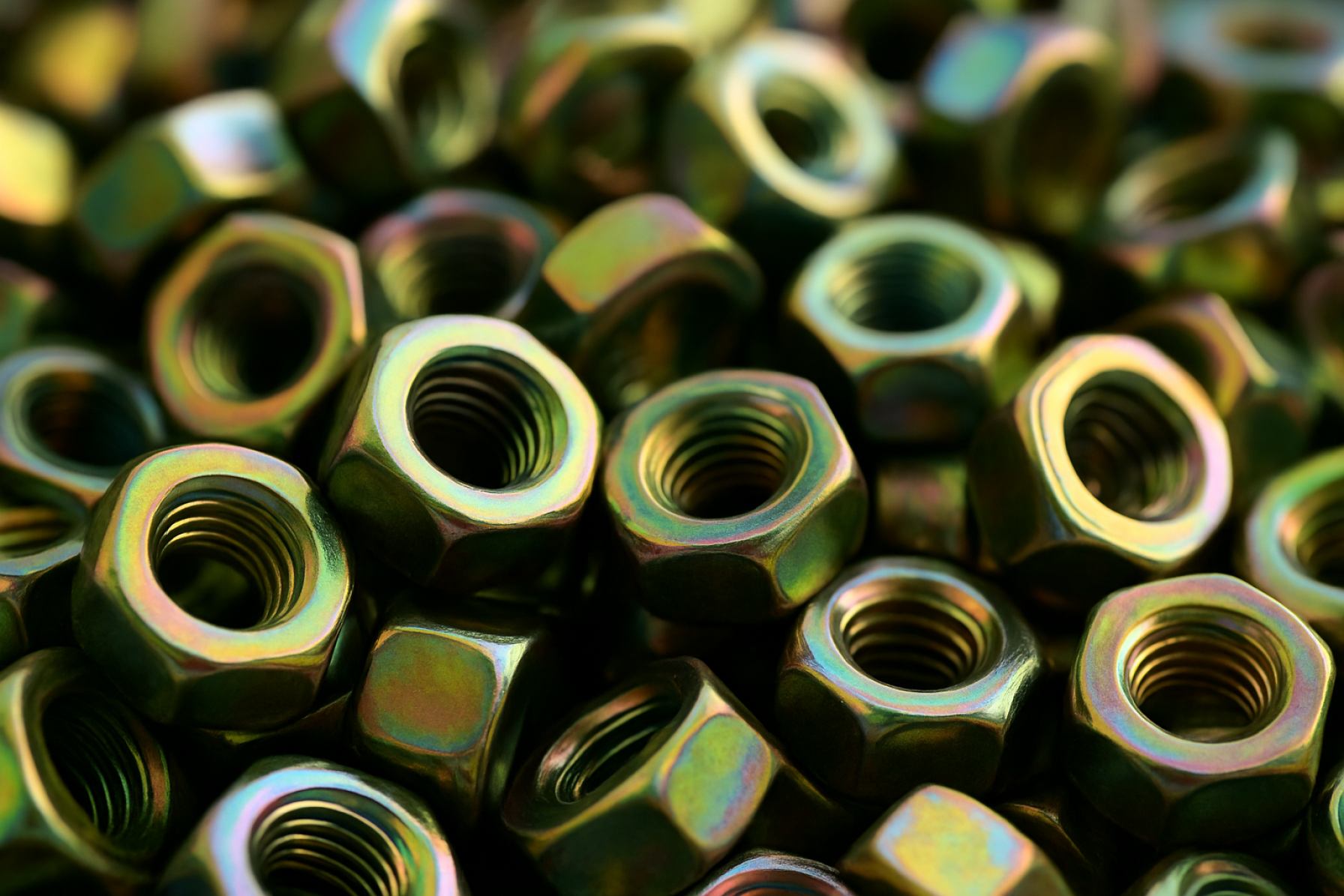
Table des matières
- Résumé exécutif : tendances clés 2025-2029 dans les revêtements en zinc-nickel multicouches
- Aperçu technologique : état actuel et avancées en ingénierie de prochaine génération
- Taille du marché et prévisions : demande mondiale et régionale jusqu’en 2029
- Paysage concurrentiel : entreprises leaders et partenariats stratégiques
- Demande automobile et aérospatiale : moteurs de croissance spécifiques aux secteurs
- Pipeline d’innovation : brevets, R&D et processus émergents
- Durabilité et changements réglementaires : facteurs environnementaux et de conformité
- Chaîne d’approvisionnement et défis des matières premières
- Adoption par les clients : perspectives des OEM, des fournisseurs de niveau 1 et du secteur de rechange
- Perspectives futures : technologies perturbatrices et recommandations stratégiques
- Sources et références
Résumé exécutif : tendances clés 2025-2029 dans les revêtements en zinc-nickel multicouches
L’ingénierie des revêtements en zinc-nickel multicouches est sur le point d’évoluer de manière significative entre 2025 et 2029, alors que les secteurs industriels intensifient leur focus sur une résistance à la corrosion améliorée, la conformité environnementale et l’efficacité des coûts. Les revêtements en zinc-nickel, reconnus pour leur protection supérieure contre la corrosion—particulièrement dans les applications automobiles, aérospatiales et de machines lourdes—devraient connaître une demande robuste alors que les industries passent d’alternatives traditionnelles à base de zinc pur ou de cadmium.
Ces dernières années, des fabricants leaders, tels que MacDermid Alpha et Atotech, ont conduit des innovations dans la composition des alliages et les techniques de dépôt. Ces entreprises avancent des technologies de galvanoplastie en zinc-nickel alcalin et acide pour améliorer l’uniformité, réduire l’embrittlement par l’hydrogène et répondre à des normes réglementaires mondiales plus strictes. Notamment, l’accent mis sur les passivations sans chrome hexavalent, en alignement avec les directives REACH et RoHS, transforme les formulations de revêtements et les processus de post-traitement.
Les données du secteur indiquent un changement clair vers des revêtements à haute teneur en nickel (12–15% Ni), qui offrent jusqu’à 10 fois la résistance à la corrosion des revêtements en zinc standard dans les tests de brouillard salin. Cela est particulièrement critique pour les fixations automobiles, les composants de châssis et les connecteurs électriques, où des fabricants tels qu’Automotive Racing Products et Norm Fasteners spécifient de plus en plus le zinc-nickel pour les pièces OEM et du marché de rechange.
L’automatisation et la digitalisation devraient également transformer le paysage des revêtements en zinc-nickel. Des fournisseurs majeurs de lignes de galvanoplastie comme AWA intègrent des contrôles de processus avancés, une surveillance de la qualité en temps réel et des analyses de données intégrées. Ces améliorations technologiques devraient entraîner un taux de production plus élevé, des déchets réduits et une meilleure traçabilité—des exigences clés des OEM automobiles et électroniques cherchant à optimiser les coûts de cycle de vie et l’assurance qualité.
En regardant vers 2025-2029, l’optimisme du marché reste robuste. La transition vers des véhicules électriques et des systèmes d’énergie renouvelable stimulera davantage les besoins d’une protection fiable contre la corrosion dans des environnements difficiles. En même temps, les pressions sur la chaîne d’approvisionnement mondiale incitent à des opérations de revêtement localisées et flexibles, avec des entreprises en Europe, en Amérique du Nord et en Asie-Pacifique augmentant leur capacité et leurs partenariats régionaux.
En résumé, les prochaines années verront l’ingénierie des revêtements en zinc-nickel multicouches caractérisée par une innovation pilotée par la réglementation, une adoption accrue des alliages haute performance et l’intégration de technologies de fabrication intelligente. Les parties prenantes de la chaîne de valeur—from chemical suppliers and coating service providers to end-users in automotive and industrial sectors—sont prêtes à bénéficier de ces avancées alors que l’industrie se dirige vers la durabilité et l’excellence opérationnelle.
Aperçu technologique : état actuel et avancées en ingénierie de prochaine génération
Les revêtements en zinc-nickel multicouches ont émergé comme une technologie critique dans la protection avancée contre la corrosion, en particulier pour les applications automobiles, aérospatiales et industrielles. En 2025, ce secteur connaît des avancées en ingénierie notables, motivées par des réglementations environnementales de plus en plus strictes et la demande pour des traitements de surface plus performants. Le principal avantage des revêtements en zinc-nickel—contenant généralement 12-16% de nickel—réside dans leur résistance à la corrosion améliorée, qui peut surpasser celle des revêtements en zinc conventionnels par un facteur allant jusqu’à cinq dans les tests de brouillard salin. Cette performance a stimulé une adoption généralisée parmi les OEM et les fournisseurs de niveau 1.
Des fabricants leaders tels qu’Atotech et DuPont ont investi pour affiner les chimies de bain et les contrôles de processus, permettant des épaisseurs de couche plus précises et une composition d’alliage uniforme sur des géométries complexes. L’automatisation récente des processus, y compris la surveillance en temps réel de la composition de l’électrolyte et la modulation de courant avancée, permet des tolérances de qualité plus strictes et une meilleure efficacité énergétique dans les lignes de galvanoplastie. De plus, l’introduction des systèmes de passivation au chrome trivalent—portée par des entreprises comme MacDermid Alpha—répond à un mouvement mondial visant à éliminer le chrome hexavalent pour le post-traitement, s’alignant ainsi sur les tendances réglementaires.
Du point de vue de l’ingénierie des matériaux, le processus de superposition et les techniques de dépôt multi-étapes évoluent. Les approches de prochaine génération impliquent non seulement des couches d’alliage en zinc-nickel, mais aussi des systèmes duplex et même triplex, où un revêtement organique ou céramique supplémentaire est appliqué pour prolonger la durée de vie et ajouter des propriétés fonctionnelles, telles que l’auto-réparation ou des effets hydrophobes. Atotech et ses pairs développent des systèmes de revêtements modulaires compatibles à la fois avec le placage sur rack et le placage en baril, permettant une fabrication flexible et des délais de livraison réduits.
Dans un avenir proche, la digitalisation et l’optimisation des processus basées sur les données devraient jouer un rôle plus important. L’intégration du retour d’information sur les processus guidée par l’IA, actuellement testée dans des usines pilotes par plusieurs fournisseurs mondiaux, devrait encore améliorer la cohérence et le débit. Les prochaines années devraient également voir une adoption plus large de revêtements conçus pour être compatibles avec des alliages légers et des aciers haute résistance, conformément à l’évolution de l’industrie automobile vers l’électrification et la durabilité.
Globalement, les revêtements en zinc-nickel multicouches sont positionnés pour rester à l’avant-garde des solutions anticorrosion en 2025 et au-delà, soutenus à la fois par des impératifs environnementaux et une innovation technologique continue de la part de leaders du secteur tels qu’Atotech, MacDermid Alpha et DuPont.
Taille du marché et prévisions : demande mondiale et régionale jusqu’en 2029
Le marché de l’ingénierie des revêtements en zinc-nickel multicouches connaît une croissance robuste, alimentée par une demande croissante dans les secteurs de l’automobile, de l’électronique, de l’énergie et des machines lourdes cherchant une résistance à la corrosion supérieure et une conformité environnementale. À l’horizon 2025, les capacités de production et les taux d’adoption s’élargissent en Amérique du Nord, en Europe et en Asie-Pacifique, avec des acteurs clés de l’industrie investissant dans des technologies de fabrication et de finition avancées pour répondre à l’évolution des exigences réglementaires et des normes de performance.
En Europe, le passage des finitions traditionnelles au cadmium et au chrome hexavalent, en raison des réglementations REACH, continue d’accélérer l’adoption des revêtements en zinc-nickel. Des fournisseurs de premier plan tels qu’Atotech et MacDermid Alpha investissent dans de nouvelles mises à niveau d’installations et des innovations de processus visant un plus haut rendement et un impact environnemental réduit. Le marché européen devrait connaître un taux de croissance annuel composé (CAGR) dans les chiffres à un chiffre jusqu’en 2029, témoignant d’une demande soutenue des OEM automobiles et des fournisseurs de composants axés sur l’allègement et les intervalles de service prolongés.
L’Amérique du Nord reste un marché significatif, avec les États-Unis et le Mexique entraînant l’adoption dans les secteurs automobile, des équipements agricoles et des fixations industrielles. Des fabricants majeurs tels que A+ Industrial Coatings et Prestige Coating développent leurs lignes de revêtements en zinc-nickel, répondant aux exigences des OEM pour une protection anticorrosion améliorée dans les composants et infrastructures des véhicules électriques (EV). La région devrait maintenir une trajectoire de croissance stable mais modérée, soutenue par des investissements dans les infrastructures et des politiques environnementales strictes.
La région Asie-Pacifique, menée par la Chine, le Japon et la Corée du Sud, devrait afficher les taux de croissance les plus élevés jusqu’en 2029. La région bénéficie d’une production automobile en plein essor, de bases de fabrication modernisées rapidement et d’une production électronique élargie. Des entreprises comme Nippon Paint Holdings et Tokyo Kinzoku Industry augmentent leurs capacités de revêtement en zinc-nickel, en se concentrant sur des lignes de plaquage automatisées et à volume élevé pour desservir à la fois les marchés nationaux et d’exportation.
À l’échelle mondiale, le marché de l’ingénierie des revêtements en zinc-nickel multicouches devrait dépasser des repères de volume significatifs d’ici 2029, alimenté par une réglementation de plus en plus stricte sur les substances dangereuses, une sensibilisation croissante aux coûts de cycle de vie et des avancées techniques continues dans les techniques de dépôt. À l’avenir, les prochaines années devraient voir des expansions de capacité continues, une intégration plus large des contrôles de processus numériques et de nouvelles formulations d’alliage offrant des performances sur mesure pour des besoins spécifiques à chaque secteur.
Paysage concurrentiel : entreprises leaders et partenariats stratégiques
Le paysage concurrentiel de l’ingénierie des revêtements en zinc-nickel multicouches en 2025 est caractérisé par la présence de spécialistes reconnus du traitement de surface, de fabricants de produits chimiques mondiaux et de leaders de la chaîne d’approvisionnement automobile. Ces entreprises stimulent l’innovation par des formulations d’alliage avancées, des processus de galvanoplastie automatisés et des partenariats axés sur l’amélioration de la durabilité et de la résistance à la corrosion. Alors que les réglementations environnementales se durcissent et que les secteurs automobile et industriel lourd demandent des revêtements plus durables et performants, les acteurs de l’industrie investissent de plus en plus dans la R&D et les collaborations stratégiques pour consolider leurs positions.
Des leaders de l’industrie tels qu’Atotech, MacDermid Alpha, et otech restent à l’avant-garde, fournissant des chimies en zinc-nickel propriétaires et des solutions de galvanoplastie clés en main aux OEM et aux fournisseurs de niveau 1 à l’échelle mondiale. Atotech, par exemple, continue d’élargir ses gammes de produits Tricotect et Zintek, en mettant l’accent sur une efficacité de dépôt élevée et la conformité aux normes de performance de corrosion des OEM automobiles. Pendant ce temps, MacDermid Alpha tire parti de sa présence mondiale pour fournir des systèmes de revêtements en zinc-nickel intégrés adaptés aux fixations automobiles et aux composants de châssis.
Les partenariats stratégiques et les alliances techniques sont essentiels dans cet environnement concurrentiel. Notamment, les collaborations entre fournisseurs de solutions chimiques et fabricants d’équipements d’automatisation rationalisent le déploiement de lignes de zinc-nickel à haut débit et respectueuses de l’environnement. Par exemple, Galvatek, un spécialiste des usines de traitement de surface automatisées, s’associe fréquemment à des fournisseurs de produits chimiques pour fournir des systèmes de galvanoplastie en zinc-nickel pour des clients dans l’aérospatiale et la défense.
La demande croissante de solutions durables a également poussé les alliances visant à répondre aux critères de conformité sans chrome, REACH et de processus à faible déchet. Des fabricants automobiles mondiaux leaders, tels que Volkswagen AG, s’engagent activement auprès des fournisseurs de technologies de revêtement pour co-développer des solutions en zinc-nickel de nouvelle génération qui prolongent la durée de vie des composants tout en réduisant l’impact environnemental.
À l’avenir, le marché est prêt pour une consolidation supplémentaire alors que les entreprises cherchent à sécuriser la propriété intellectuelle, accéder à de nouveaux marchés régionaux et diversifier leurs champs d’application. L’entrée des fournisseurs asiatiques et l’expansion des acteurs européens et nord-américains dans les chaînes d’approvisionnement de véhicules électriques et d’énergie renouvelable devraient intensifier la concurrence dans les prochaines années. Un investissement continu dans l’automatisation, la surveillance numérique de la qualité et des chimies de processus plus respectueuses de l’environnement est anticipé, les leaders de l’industrie formant de nouveaux partenariats pour répondre aux exigences techniques et réglementaires évolutives des utilisateurs finaux.
Demande automobile et aérospatiale : moteurs de croissance spécifiques aux secteurs
Les industries automobile et aérospatiale sont prêtes à rester des moteurs clés pour l’ingénierie des revêtements en zinc-nickel multicouches jusqu’en 2025 et dans les années à venir. L’accent mis sur la construction légère, l’électrification et la résistance à la corrosion améliorée continue de fixer des normes élevées pour les technologies de traitement de surface. Les revêtements en zinc-nickel, en particulier ceux avec des architectures multicouches ou duplex, sont de plus en plus privilégiés en raison de leur protection supérieure contre la corrosion—jusqu’à huit fois plus grande que le plaquage en zinc traditionnel—tout en répondant aux exigences de résistance à haute température et chimique.
Au sein du secteur automobile, les fabricants d’équipements d’origine (OEM) et les fournisseurs intensifient leur adoption des revêtements en zinc-nickel pour les fixations critiques, les composants de frein, les pièces du système de carburant et les boîtiers de batteries de véhicules électriques (EV). Les pressions réglementaires, telles que la directive sur les véhicules hors d’usage (ELV) de l’Union européenne et les restrictions croissantes sur le chrome hexavalent, propulsent le passage à des revêtements électroplaqués plus respectueux de l’environnement et plus durables. De grands fournisseurs automobiles—y compris ZF Friedrichshafen AG et Robert Bosch GmbH—se sont publiquement engagés à remplacer les revêtements traditionnels par des solutions avancées en zinc-nickel pour répondre aux garanties de corrosion à long terme et aux normes de durabilité.
Les applications aérospatiales, où l’économie de poids, la compatibilité galvanique et la fiabilité dans des conditions extrêmes sont primordiales, illustrent également la demande croissante pour des couches en zinc-nickel conçues. Les fabricants d’avions et leurs fournisseurs de niveau 1 spécifient le zinc-nickel pour les fixations, les composants de train d’atterrissage et les raccords hydrauliques, souvent dans le cadre de systèmes multicouches combinant passivation et couches supérieures pour améliorer les performances. Des entreprises telles que Galvatek et Socomore développent en outre des systèmes d’automatisation des processus et de contrôle de la qualité adaptés aux tolérances serrées et à la traçabilité exigées par les clients du secteur aérospatial.
Du point de vue technologique, les avancées dans la chimie des bains, le plaquage par impulsion et le micro-dépôt permettent des dépôts plus uniformes et des compositions d’alliage sur mesure. Les investissements en cours d’équipements comme Atotech soutiennent des installations évolutives et à haut rendement pour les lignes de production automobile et aérospatiale. Notamment, les efforts de R&D collaboratives entre fournisseurs de revêtements et OEM accélèrent la transition vers des passivations trivalentes et des chimies sans plomb, reflétant à la fois les objectifs de durabilité réglementaire et d’entreprise.
À l’avenir, les perspectives pour l’ingénierie des revêtements en zinc-nickel sont robustes. L’électrification continue dans la mobilité, la nécessité d’une durée de vie plus longue des composants et des cadres réglementaires plus stricts devraient alimenter de nouveaux développements de processus et des expansions de capacité. Les leaders de l’industrie anticipent que la part du zinc-nickel dans les revêtements anticorrosion continuera de croître, avec une adoption s’étendant à des segments de mobilité adjacents tels que les véhicules commerciaux et les plateformes de mobilité électrique.
Pipeline d’innovation : brevets, R&D et processus émergents
Le pipeline d’innovation pour l’ingénierie des revêtements en zinc-nickel multicouches en 2025 est caractérisé par des activités de recherche et développement robustes, un paysage de brevets dynamique et l’émergence de processus avancés optimisés pour la fois performances et conformité réglementaire. Les secteurs automobile, de la construction et de l’électronique continuent de stimuler la demande pour des revêtements anticorrosion haute performance, incitant les scientifiques des matériaux et les fabricants de revêtements à intensifier leurs efforts en formulation d’alliages, automatisation des processus et responsabilité environnementale.
L’une des tendances les plus marquantes est l’accent mis sur les systèmes de passivation trivalents et les bains de plaquage sans cyanure. En réponse à des réglementations environnementales plus strictes—particulièrement en Europe et en Amérique du Nord—des fabricants tels qu’Atotech et MacDermid Alpha développent des processus en zinc-nickel propriétaires qui allient haute résistance à la corrosion et génération de déchets dangereux réduite. Par exemple, les innovations d’Atotech se concentrent sur des alliages à haute teneur en nickel (12–16%) pour les fixations automobiles, avec une résistance aux tests de brouillard salin dépassant 1 000 heures jusqu’à la corrosion par rouille rouge, tout en restant conformes aux directives REACH et RoHS.
Le paysage des brevets connaît un afflux constant de dépôts liés aux revêtements en zinc-nickel multicouches et composites. Les divulgations récentes mettent en avant des approches multicouches—telles que des revêtements fonctionnellement gradés ou des structures duplex—qui combinent séquentiellement des couches ductiles et riches en zinc avec des barrières de diffusion plus dures et riches en nickel. Cette ingénierie permet d’obtenir des performances sur mesure pour des contraintes d’application spécifiques, allant des environnements marins aux ensembles automobiles sous capot. Des entreprises comme OC Oerlikon et Nippon Paint Holdings poursuivent activement des droits de propriété intellectuelle dans ce domaine, soulignant l’intensité concurrentielle du secteur.
Les efforts de R&D s’étendent également à l’automatisation des processus et à la digitalisation. La surveillance de la qualité en ligne, l’analyse de la composition des bains en temps réel et le contrôle des processus guidé par l’IA deviennent standards dans les lignes de galvanoplastie à la pointe de la technologie, comme on le voit dans les offres technologiques d’Elaqua et d’Atotech. Ces technologies devraient accélérer l’adoption commerciale de revêtements multicouches complexes en assurant la reproductibilité et l’efficacité des coûts.
En regardant vers les prochaines années, les perspectives de l’industrie sont façonnées par la nécessité de normes de performance encore plus élevées—telles qu’une protection anticorrosion prolongée pour les composants de véhicules électriques et les alliages légers. Les collaborations en cours entre OEM, fournisseurs de produits chimiques et laboratoires universitaires devraient aboutir à de nouveaux dépôts de brevets et à des lancements commerciaux de revêtements en zinc-nickel nanostructurés, de couches intelligentes auto-réparatrices, et de revêtements compatibles avec les substrats de fabrication additive. Avec la durabilité et la fabrication numérique comme moteurs centraux, l’ingénierie des revêtements en zinc-nickel est prête à évoluer rapidement jusqu’en 2025 et au-delà.
Durabilité et changements réglementaires : facteurs environnementaux et de conformité
Les revêtements en zinc-nickel multicouches sont devenus un point focal dans l’ingénierie de surface en raison de leur résistance à la corrosion supérieure et de leur profil environnemental favorable comparé aux alternatives traditionnelles à base de cadmium ou à haute teneur en zinc. À l’horizon 2025, la durabilité et la conformité réglementaire sont des moteurs définis dans ce secteur, influencés par le resserrement des normes mondiales sur les substances dangereuses et les émissions de cycle de vie.
L’application continue par l’Union européenne de la réglementation REACH et de la directive sur les véhicules hors d’usage (ELV) continue de restreindre l’utilisation du chrome hexavalent et d’autres substances dangereuses dans la fabrication automobile et électronique. En conséquence, les OEM et les fournisseurs de niveau 1 accélèrent l’adoption des revêtements en zinc-nickel, qui offrent des performances élevées sans les risques de conformité associés aux chimies plus anciennes. De grands fournisseurs de revêtements, tels qu’Atotech et MacDermid Alpha, rapportent des portefeuilles élargis de processus de passivation trivalente et de zinc-nickel conformes à la directive RoHS, visant à servir à la fois les marchés des fixations automobiles et industrielles.
En Amérique du Nord, le changement est parallèle à la mise à jour des normes ASTM et à l’augmentation des exigences des clients pour une durée de vie prolongée en brouillard salin et un impact environnemental réduit. DuPont et Aker BP ont souligné le rôle critique des revêtements durables pour les applications offshore et énergétiques, où les évaluations du cycle de vie et les empreintes carbone sont désormais couramment prises en compte dans les décisions d’approvisionnement.
Les données des dernières années montrent une augmentation généralisée de l’utilisation de revêtements en zinc-nickel avec des systèmes de passivation trivalents ou sans chrome, réduisant la dépendance aux métaux lourds et améliorant la sécurité des travailleurs lors de l’application. Par exemple, les dernières gammes de produits d’Atotech mettent l’accent sur l’efficacité énergétique, la réduction des déchets et le recyclage de l’eau en circuit fermé, en s’alignant sur les directives environnementales de l’UE et des États-Unis.
À l’avenir, une dynamique réglementaire accrue devrait intensifier son cours, avec la Convention de Minamata sur le mercure des Nations Unies et de probables restrictions supplémentaires sur les PFAS et d’autres produits chimiques persistants poussant le secteur vers des formulations encore plus écologiques. L’essor de l’économie circulaire et des passeports de produits numériques dans l’UE nécessitera également un suivi transparent des chimies de revêtement tout au long de la chaîne de valeur, incitant davantage au passage à des systèmes de zinc-nickel durables.
Dans l’ensemble, l’ingénierie des revêtements en zinc-nickel est positionnée pour une croissance robuste, soutenue par l’harmonisation réglementaire, les mandats de durabilité des clients et l’innovation continue des fournisseurs leaders. Les entreprises investissant dans des technologies éco-responsables et conformes devraient maintenir un avantage concurrentiel à mesure que les attentes environnementales mondiales continuent d’augmenter.
Chaîne d’approvisionnement et défis des matières premières
La chaîne d’approvisionnement et le paysage des matières premières pour les revêtements en zinc-nickel multicouches subissent des changements significatifs à l’approche de 2025. Les intrants principaux—zinc et nickel de haute pureté—ont connu des fluctuations de disponibilité et de prix en raison de facteurs géopolitiques, des coûts énergétiques et de l’évolution des réglementations environnementales. Ces dernières années, les marchés du nickel ont été particulièrement volatils, influencés par une demande croissante du secteur des batteries et des contraintes d’approvisionnement chez de grands producteurs. Cette volatilité impacte directement la structure des coûts des revêtements en zinc-nickel, où le nickel constitue généralement 10–15% de l’alliage, mais jusqu’à 60% du coût matériel.
Plusieurs fournisseurs leaders, y compris Umicore et BASF, ont publiquement noté des défis pour assurer un approvisionnement constant en nickel pour les technologies de surface, avec des investissements en cours pour améliorer le recyclage et la circularité dans leurs chaînes de valeur. Ces efforts devraient permettre de réduire partiellement les pressions sur les matières premières, mais un découplage complet des sources de nickel primaire reste insaisissable à l’horizon 2025.
Les réglementations environnementales exercent une pression supplémentaire sur les opérations d’exploitation minière et de raffinage traditionnelles. Le Green Deal de l’Union européenne et la loi sur la réduction de l’inflation des États-Unis accélèrent les changements en faveur d’une approvisionnement responsable et d’un contrôle accru de la transparence de la chaîne d’approvisionnement. Par conséquent, les OEM et les applicateurs de revêtements recherchent de plus en plus des certifications et des documents de conformité de chaîne d’approvisionnement de la part de leurs fournisseurs de matières premières, comme l’ont souligné les mises à jour politiques d’Aker Solutions et de Technip Energies dans leurs récents rapports de durabilité.
Un autre défi émergent est la concurrence pour le nickel entre les applications de revêtement et le secteur des batteries de véhicules électriques, en plein essor. Cette concurrence a entraîné des pénuries d’approvisionnement périodiques et a poussé certaines entreprises de traitement de surface à explorer des compositions d’alliage alternatives ou des systèmes de revêtement multicouches qui réduisent la dépendance globale au nickel. Par exemple, Atotech a indiqué un R&D actif dans des revêtements à faible teneur en nickel et hybrides pour répondre aux contraintes attendues des matières premières jusqu’en 2026 et au-delà.
Les perspectives à court terme suggèrent une continuité de la tension sur l’approvisionnement en nickel, le zinc restant relativement plus stable en raison d’une base de producteurs plus large et d’une concurrence moins intense des autres secteurs industriels. Cependant, des stratégies de résilience de la chaîne d’approvisionnement—telles que la double source, l’augmentation du recyclage et des partenariats fournisseurs plus étroits—sont prioritaires dans l’industrie des revêtements en zinc-nickel. Les entreprises qui investissent dans la traçabilité numérique et les initiatives d’économie circulaire devraient être mieux positionnées pour naviguer dans le paysage évolutif des matières premières dans les prochaines années.
Adoption par les clients : perspectives des OEM, des fournisseurs de niveau 1 et du secteur de rechange
L’adoption des revêtements en zinc-nickel multicouches connaît une nette hausse dans les secteurs automobile, des machines lourdes et industrielles, stimulée par des normes de résistance à la corrosion de plus en plus strictes et des mandats de durabilité en évolution. Les fabricants d’équipements d’origine (OEM), les fournisseurs de niveau 1 et le secteur de rechange abordent chacun les revêtements zinc-nickel avec des priorités uniques, mais tous convergent vers cette technologie en raison de ses performances démontrées et de son alignement réglementaire.
Les OEM mènent le mouvement en faveur des revêtements en zinc-nickel, notamment dans les régions où les réglementations environnementales et de performance se resserrent. Les OEM européens sont particulièrement proactifs, comme en témoigne l’adoption généralisée parmi les grandes marques automobiles et les producteurs de composants. Cela est largement dû à la protection anticorrosion supérieure—dépassant souvent 720 heures dans les tests de brouillard salin—et au passage des processus au chrome hexavalent. Des entreprises telles que DuPont et ZEISS (pour l’inspection qualité et le contrôle des processus) soutiennent les OEM avec des capacités d’intégration des processus avancées. Alors que l’allègement des véhicules et l’électrification se poursuivent jusqu’en 2025, la compatibilité des revêtements en zinc-nickel avec les métaux mixtes et sa sensibilité à l’embrittlement par l’hydrogène sont des avantages majeurs.
Les fournisseurs de niveau 1, responsables des assemblages complexes et des sous-composants, s’alignent étroitement sur les exigences des OEM en intégrant des lignes de galvanoplastie en zinc-nickel automatisées et en investissant dans la traçabilité des processus. Des entreprises telles que Atotech fournissent des systèmes de plaquage clés en main et des solutions chimiques pour aider les fournisseurs de niveau 1 à répondre aux spécifications et exigences de durabilité des OEM. Les fournisseurs de niveau 1 tirent également parti de l’augmentation de la constance des processus des bains de zinc-nickel modernes, leur permettant de délivrer des revêtements hautement uniformes même sur des géométries complexes—une considération essentielle pour les composants de châssis et de transmission électrisés.
Dans le secteur de rechange, l’adoption est plus variée mais devrait croître régulièrement jusqu’en 2025 et au-delà, notamment dans les régions où la longévité des produits et les réclamations de garantie liées à la corrosion sont des préoccupations primordiales. Les acteurs du marché de rechange spécifient de plus en plus des finitions en zinc-nickel pour les fixations critiques, les composants de frein et les éléments de suspension, reflétant les pratiques des OEM. Les réseaux de fournisseurs tels que Wynn’s et Bosch élargissent leur gamme de produits revêtus en réponse à la demande des utilisateurs finaux et des opérateurs de flotte pour des intervalles de maintenance plus longs.
À l’avenir, les perspectives pour l’ingénierie des revêtements en zinc-nickel demeurent robustes. À mesure que les pressions réglementaires s’intensifient et que les principes de l’économie circulaire prennent de l’ampleur, la courbe d’adoption devrait s’accentuer dans tous les segments de clients. Les principaux organismes de l’industrie, tels que le Automotive Industry Action Group (AIAG), mettent à jour les pratiques recommandées et les normes de la chaîne d’approvisionnement pour faciliter davantage la mise en œuvre de revêtements de surface à haute performance et respectueux de l’environnement.
Perspectives futures : technologies perturbatrices et recommandations stratégiques
Les revêtements en zinc-nickel multicouches sont prêts pour une évolution significative en 2025 et les années suivantes, alimentée par des pressions réglementaires, l’évolution vers l’électrification de l’industrie automobile et un accent croissant sur la durabilité. Ces revêtements—déjà établis pour leur résistance supérieure à la corrosion par rapport à la galvanoplastie traditionnelle en zinc—sont de plus en plus intégrés dans les secteurs automobile, aérospatial et des machines lourdes en raison de leur capacité à répondre à des exigences de performance stricts dans des conditions environnementales difficiles.
Une tendance perturbatrice clé est l’adoption de systèmes de passivation trivalents et de systèmes d’étanchéité sans chrome, qui répondent aux préoccupations environnementales et sanitaires associées au chrome hexavalent. Des fournisseurs de traitement de surface de premier plan tels qu’Atotech et DuPont ont investi dans des chimies de bain en zinc-nickel de nouvelle génération qui suppriment non seulement les substances dangereuses, mais améliorent également l’efficacité du plaquage et l’uniformité de la couche. Ces avancées devraient devenir courantes à mesure que les constructeurs automobiles et les OEM exigent la conformité aux directives REACH et ELV.
Un autre domaine d’innovation est l’intégration de la fabrication intelligente et du contrôle des processus numériques. Des entreprises comme AZ Electronic Materials et ZEISS développent des outils de surveillance de précision et des systèmes d’assurance qualité automatisés, permettant des ajustements en temps réel des processus de dépôt. Ce changement améliore non seulement la cohérence des revêtements mais réduit également les déchets et la consommation d’énergie, en s’alignant sur les objectifs de durabilité mondiaux.
Les tendances d’électrification, en particulier dans le secteur automobile, devraient influencer les spécifications des revêtements en zinc-nickel jusqu’en 2025 et au-delà. L’utilisation croissante d’assemblages de matériaux mixtes et d’alliages légers nécessite des revêtements offrant une adhérence robuste, une faible résistance au contact et une haute compatibilité avec l’aluminium. Cela se reflète dans les collaborations en cours entre les OEM et des fournisseurs tels que Bosch et Schaeffler, qui spécifient activement des solutions avancées en zinc-nickel pour les applications de groupe motopropulseur et de châssis destinées à la mobilité électrique.
En regardant vers l’avenir, les recommandations stratégiques pour les parties prenantes de l’industrie incluent : investir dans la R&D pour des systèmes de revêtement multifonctionnels (par exemple, combinant la protection de la corrosion avec des couches auto-lubrifiantes ou antimicrobiennes) ; élargir les programmes pilotes de gestion chimique en boucle fermée pour réduire l’impact environnemental ; et favoriser des partenariats intersectoriels pour accélérer l’adoption de lignes de plaquage numérique. À mesure que le paysage réglementaire continue de se resserrer et que les exigences des utilisateurs finaux évoluent, ceux qui intègrent proactivement l’ingénierie avancée du zinc-nickel sécuriseront un avantage concurrentiel sur le marché des revêtements tout au long de la seconde moitié de cette décennie.
Sources et références
- Atotech
- Norm Fasteners
- AWA
- DuPont
- Nippon Paint Holdings
- otech
- Volkswagen AG
- ZF Friedrichshafen AG
- Robert Bosch GmbH
- Socomore
- Aker BP
- Umicore
- BASF
- Technip Energies
- ZEISS
- Automotive Industry Action Group (AIAG)
- Schaeffler