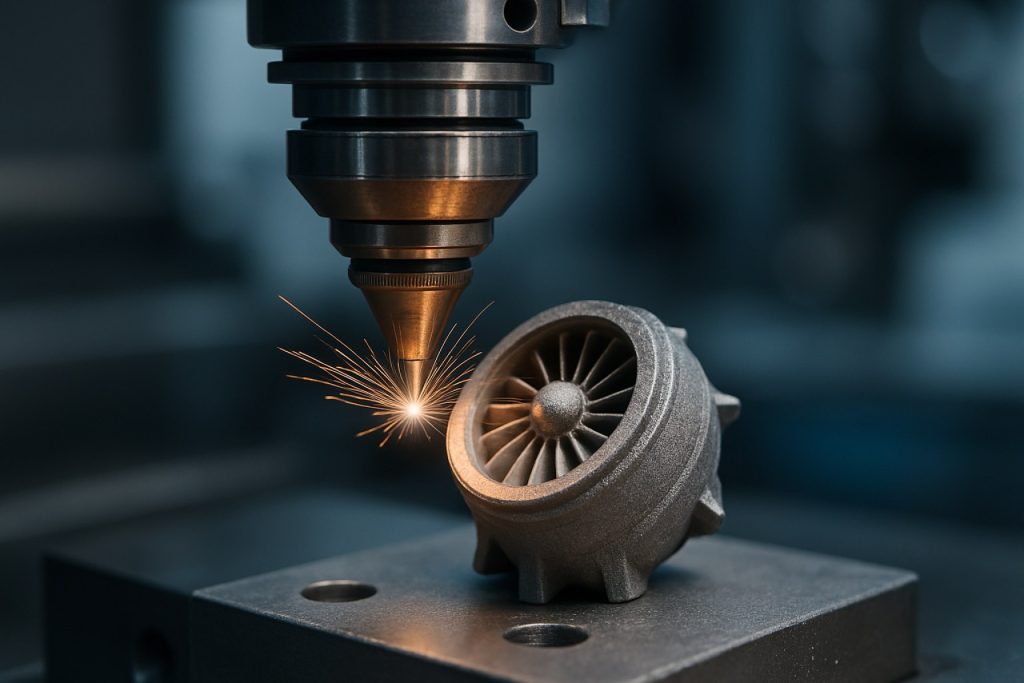
Indholdsfortegnelse
- Ledelsesresumé: Aerojet Motor Mikrofabrikation i 2025
- Markedsstørrelse og Vækstprognose: 2025–2030
- Nøglespillere og Branche-samarbejder
- Mikrofabrikationsteknologier, der Revolutionerer Aerojet Motorer
- Materialevidenskabsfremskridt: Legeringer, Keramikk og Kompositter
- Fremstillingsudfordringer og Løsninger
- Anvendelser i Kommercielle, Forsvars- og Rumsektorer
- Regulatorisk Landskab og Branche-standarder
- Investeringsmuligheder og Finansieringsindsigt
- Fremtidsudsigter: Disruptive Innovationer og Konkurrence Dynamik
- Kilder & Referencer
Ledelsesresumé: Aerojet Motor Mikrofabrikation i 2025
Aerojet motor mikrofabrikation omformer hurtigt aerospace fremdriftslandskabet i 2025, drevet af efterspørgslen efter højere effektivitet, reduceret vægt og forbedret pålidelighed i både kommercielle og forsvarssektorer. Mikrofabrikation—som omfatter teknikker såsom mikro-elektrisk afladningsbearbejdning (mikro-EDM), laserablation og avanceret additiv fremstilling—muliggør skabelsen af indviklede motor komponenter på mikronskala, som tidligere var umulige eller meget kostbare med traditionelle fremstillingsmetoder.
Året 2025 markerer et betydeligt vendepunkt for adoption, med store fremdrivningssystem OEM’er og leverandører, der intensiverer investeringer i mikrofabrikation faciliteter og processer. Virksomheder som GE Aerospace og Rolls-Royce fortsætter med at udvikle og implementere mikrofabrikation til næste generations jetmotorer, særligt turbineblade, brændstofindsprøjtningssystemer og mikrokanal varmevekslere. Disse fremskridt forbedrer ikke blot motorens ydelse og effektivitet, men forlænger også komponenternes levetid og reducerer vedligeholdelsesintervaller.
Adoptionen fremmes yderligere af succesfulde pilotprogrammer og produktionskørsler, der har vist betydelige præstationsgevinster. For eksempel har mikro-fabrikerede kølekanaler i turbineblade gjort det muligt at have højere driftstemperaturer, hvilket direkte oversættes til forbedrede skub-til-vægt-forhold og lavere brændstofforbrug. Sådanne innovationer er nært knyttet til strenge emissionsmål og bæredygtighedsmandater fra regulerende organer, hvilket tvang producenter til at adoptere mikrofabrikation for at opfylde fremtidige miljøstandarder.
Forsyningskæden for mikrofabrikerede aerojet motor dele bliver stadig mere robust, med nøglematerialeleverandører som Honeywell, der investerer i specialiserede legeringer og keramiske kompositer tilpasset mikroskala funktioner. Samtidig ruller maskinværktøjsproducenter og proces teknologi virksomheder nye platforme, der er designet specifikt til aerospace mikrofabrikation, med fokus på præcision, gentagelighed og skalerbarhed.
Ser man frem mod de kommende år, er udsigterne for aerojet motor mikrofabrikation meget positive. Brancheprognoser og igangværende F&U tyder på, at mikrofabrikerede komponenter vil blive almindelige i både kommercielle og militære motorprogrammer mellem 2027 og 2028, med forventede produktionsvolumener, der stiger, efterhånden som omkostningsbarriererne fortsætter med at falde. Samarbejde mellem motor OEM’er, materialespecialister og akademiske institutioner accelererer også innovationshastigheden, med fokus på digital designintegration, realtids procesovervågning og automatiseret kvalitetskontrol.
Sammenfattende står 2025 som et afgørende år for aerojet motor mikrofabrikation, hvor branchens ledere og leverandører er forpligtet til at optrappe disse transformative teknologier og bane vejen for en ny æra af fremdriftseffektivitet, holdbarhed og bæredygtighed.
Markedsstørrelse og Vækstprognose: 2025–2030
Det globale marked for aerojet motor mikrofabrikation er klar til betydelig vækst mellem 2025 og 2030, drevet af den stigende efterspørgsel efter brændstofeffektive, lav-emissions fremdrivningssystemer i både kommercielle og forsvars aerospace sektorer. Mikrofabrikationsteknikker—som avanceret additiv fremstilling, integration af mikro-elektro-mekaniske systemer (MEMS) og præcisions laserbearbejdning—integreres i kernefremstillingsprocesserne for næste generations jetmotorer for at muliggøre letvægts, højtydende komponenter. Nøglebrancheaktører investerer i at skalere produktionskapaciteter og udvikle nye materialesystemer for at imødekomme de skiftende krav inden for aerospace fremdrift.
Fra 2025 vil førende aerojet producenter, herunder GE Aerospace, Rolls-Royce og Pratt & Whitney, udnytte mikrofabrikation til at forbedre komponentminiaturisering, forbedre kølekanalsgeometrier og optimere brændstofdyse designs. For eksempel har mikrofabrikerede komponenter i brændstofindsprøjtningssystemer og turbineblade resulteret i målbare forbedringer i termisk effektivitet og emissionsreduktion. Disse fremskridt støttes af samarbejder med specialleverandører som Safran og MTU Aero Engines, der også udvider deres mikrofabrikation kapabiliteter.
Markedsudvidelse er nært beslægtet med den bredere anvendelse af additiv fremstilling og laser-baseret mikro-bore til produktion af præcise motorfunktioner i storskala. Ifølge erklæringer fra GE Aerospace og Rolls-Royce vil en stigende andel af nye motor dele—især til smalprofil og regionale fly—inkorporere mikrofabrikerede elementer inden 2030. Dette forventes at drive en sammensat årlig vækstrate (CAGR) i høje enkeltcifrede tal for segmentet af aerojet motor mikrofabrikation gennem perioden.
- Nordamerika og Europa vil forblive de vigtigste markeder, understøttet af igangværende flådefornyelser og strenge emissionsreguleringer.
- Asien-Stillehavsområdet forventes at se den hurtigste optagelse, da produktionen af regionale fly og opdateringsprogrammer inden for forsvaret udvides.
- Investeringer i F&U og nye produktionslinjer fra store OEM’er og leverandører forventes at accelerere i hele prognoseperioden, med højværdikontrakter allerede rapporteret for mikrofabrikerede turbine- og forbrændingskomponenter.
Ser man fremad, er markedsudsigterne for 2025–2030 robuste, med mikrofabrikation på vej til at blive en standard i design og produktion af aerojet motorer. Sammenfaldet af reguleringspres, materialeinnovation og modnende fremstillingsteknologier forventes at opretholde væksten og intensivere konkurrencen blandt etablerede og nye aktører inden for branchen.
Nøglespillere og Branche-samarbejder
Landskabet for aerojet motor mikrofabrikation i 2025 er præget af en kombination af etablerede aerospace producenter, innovative leverandører og tværsektorielle samarbejder. Nøglespillere investerer i avanceret mikrofabrikation for at forbedre fremdriftseffektivitet, reducere emissioner og muliggøre nye motorarkitekturer for både kommercielle og forsvars aerospace markeder.
Blandt de globale ledere fortsætter GE Aerospace med at føre an i mikrofabrikationsinitiativer, der udnytter additiv fremstilling (AM) og mikro-elektromekaniske systemer (MEMS) til turbinekomponenter og brændstofindsprøjtningssystemer. Deres vedholdende investering i AM teknologi muliggør produktion af indviklede kølekanaler og optimerede geometrier på mikronskala, der støtter både store motorlinjer og nystartede småskala fremdriftssystemer. Rolls-Royce er ligeledes aktiv med løbende samarbejder med materialeteknologivirksomheder og forskningsinstitutioner for at forfine mikroskala produktionsteknikker til højtemperaturlegeringer og keramiske matrixkompositter. Disse bestræbelser er afgørende for næste generations motorer, der fokuserer på brændstofeffektivitet og reduceret vægt.
På leverandørsiden er Oxford Instruments og Precision Micro fremtrædende i at levere mikrofabrikationsværktøjer og fotokemisk ætsningstjenester, henholdsvis. Deres teknologier gør det muligt for motor OEM’er at realisere ultrafine tolerancer i miniaturiserede komponenter som mikrodyser, sensorer og varmevekslere. Honeywell Aerospace, en anden stor spiller, integrerer MEMS-baserede sensorer, der er fabrikere på mikroskala, i deres motor kontrol- og sundhedsovervågningssystemer, hvilket signalerer en tendens mod digitalisering og datadrevet vedligeholdelse.
Branche-samarbejder vinder momentum, da virksomheder søger at accelerere innovation og dele de høje omkostninger forbundet med mikrofabrikation F&U. For eksempel udvikles joint ventures mellem primære motorproducenter og halvlederfabrikker for at overføre mikroelektronik fremstillingskompetencer til aerospace-sektoren. Derudover fremmer partnerskaber med nationale forskningslaboratorier og universiteter—som dem sponsoreret af NASA—overførslen af mikrofabrikationsteknikker fra laboratoriet til kommercielle motorplatforme.
Ser man frem, vil de kommende år sandsynligvis se stigende investering i integrerede forsyningskæder, hvor OEM’er uddyber forholdet med mikrofabrikation specialister for at muliggøre masseproduktion af komplekse, miniaturiserede motor dele. Efterhånden som miljøreguleringerne strammes, vil mikrofabrikationens rolle i at opnå højere brændstofeffektivitet og emissionssamsvar yderligere tilskynde til samarbejde og teknologisk fremskridt på tværs af branchen.
Mikrofabrikationsteknologier, der Revolutionerer Aerojet Motorer
Den hurtige udvikling af mikrofabrikationsteknologier transformerar fundamentalt udviklingen og ydeevnen af aerojet motorer, når aerospace sektoren går ind i 2025. Traditionelle fremstillingsmetoder erstattes i stigende grad af avancerede mikroskala processer, der muliggør produktion af meget komplekse, præcise og letvægts motor komponenter. En vigtig drivkraft bag dette skift er adoptionen af additiv fremstilling (AM), almindeligvis kendt som 3D-udskrivning, især gennem teknikker såsom selektiv laser smeltning (SLM) og elektronstrålesmeltning (EBM). Disse processer muliggør fremstillingen af indviklede brændstofindsprøjtere, turbineblade og kølekanaler med interne geometrier, der tidligere var umulige at realisere ved konventionelle subtraktive metoder.
Førende fremdrivningsvirksomheder anvender nu mikrofabrikation for at reducere vægt og forbedre termisk effektivitet. For eksempel har GE Aerospace med succes integreret AM-fremstillede brændstofdyser i sine LEAP-motorer og opnået en vægtreduktion på 25% og en femfoldig forøgelse af holdbarheden sammenlignet med traditionelt fremstillede modparter. Virksomheden fortsætter med at udvide sin brug af mikrofabrikation til næste generations komponenter, med fokus på tættere tolerancer og kortere leveringstider. Tilsvarende investerer Rolls-Royce i mikrofabrikerede turbine dele, der udnytter gitterstrukturer og avancerede kølekanaler for at presse grænserne for motorens effektivitet og levetid.
Rollen af mikro-elektromekaniske systemer (MEMS) i aerojet motorer vokser også, idet komponentminiaturisering muliggør forbedret sensing, overvågning og aktivering inden for barske motormiljøer. Virksomheder som Safran har fremskridt med MEMS-baserede sensorarrayer til realtids dataindsamling, hvilket driver forudsigende vedligeholdelse og større driftsikkerhed. Integrationen af MEMS i fremdrivningssystemer forventes at blive mere udbredt, efterhånden som produktionens skalerbarhed og pålidelighed forbedres i de kommende år.
Ser man frem, forventes den fortsatte modning af mikrofabrikationsteknologier at accelerere innovationen i design og fremstilling af aerojet motorer gennem 2025 og fremad. Fremkomsten af nye materialer, såsom varmebestandige superlegeringer og keramiske matrixkompositter, i kombination med præcisions mikrofabrikation, vil yderligere forbedre præstationsmetrikker. Brancheanalytikere forudsiger en voksende økosystem af dedikerede leverandører og partnere, der specialiserer sig i mikroskala aerospace komponenter, med vedvarende investering fra store aktører som Pratt & Whitney og MTU Aero Engines, som er klar til at drive adoption på tværs af både kommercielle og forsvars luftfartssektorer.
Materialevidenskabsfremskridt: Legeringer, Keramikk og Kompositter
I 2025 oplever mikrofabrikation af aerojet motor komponenter betydelige fremskridt inden for materialevidenskab, især med integrationen af nye legeringer, keramik og kompositmaterialer. Den kontinuerlige stræben efter højere effektivitet, reduceret vægt og forbedret termisk modstandsdygtighed i aerojet fremdrivningssystemer har drevet forskning og industriel adoption af banebrydende materialer og innovative fremstillingsteknikker.
Avancerede nikkellegeringer forbliver rygraden i fremstillingen af turbine sektioner på grund af deres exceptionelle mekaniske styrke og modstand mod højtemperatur nedbrydning. Dog fokuserer de igangværende udviklinger på at forbedre krypebestandighed og oxidationsbeskyttelse ved driftstemperaturer, der overstiger 1200°C. Virksomheder såsom GE Aerospace og Rolls-Royce udvikler aktivt nye legeringsformuleringer med skræddersyede mikrostrukturer muliggivet af additiv fremstilling. Elektronstrålesmeltning og laserpulverbedfusion anvendes nu rutinemæssigt til at producere turbineblade og skovle med komplekse interne kølekanaler på mikroskala, hvilket forbedrer den termiske ydeevne samtidigt med reducering af komponentmassen.
Keramiske matrixkompositter (CMCs) er gået fra eksperimentelle til kommercielle anvendelser i varmeafsnit komponenter. Siliciumcarbid-baserede CMC’er, for eksempel, tilbyder vægtbesparelser på op til 30% i forhold til traditionelle legeringer og kan fungere ved temperaturer 200–300°C højere end deres metalliske modparter. I 2025 fortsætter Safran og GE Aerospace med at udvide implementeringen af CMC’er i forbrændingskammerlinser og turbine skjolde, muliggjort af fremskridt i fiberarkitektur, grænsefladebelægninger og skalerbare fremstillingsteknikker såsom kemisk dampsugning og slurryinfusion.
Kompositter, der er forstærket med nanomaterialer—som carbon nanotubes og grafen—er også under aktiv undersøgelse for deres potentiale til yderligere at reducere vægten, samtidig med at de forbedrer mekaniske og termiske egenskaber. Producenter samarbejder med materialevidenskabsinstitutter for at optimere spredningen og justeringen af nanoforsterkninger inden for metal- og keramiske matricer med henblik på at opnå kommerciel modenhed inden for de næste par år.
Ser man frem, er udsigterne for mikrofabrikation af aerojet motorer centreret om sammenfaldet af avancerede materialer og digital fremstilling. Realtids procesovervågning, inline kvalitetskontrol og AI-drevet mikroskala optimering forventes at accelerere kvalifikationen og integrationen af næste generations legeringer, CMC’er og hybridkompositter. Dette samarbejde vil ikke kun muliggøre motorer med højere skub-til-vægt-forhold og brændstofeffektivitet, men også understøtte luftfartsindustriens bæredygtighedsmål gennem længere komponentlevetider og reduceret forbrug af råmaterialer. Efterhånden som disse teknologier modnes, er førende aktører i branchen som GE Aerospace, Rolls-Royce og Safran klar til at sætte nye standarder inden for aerojet fremdrivningsydelse og pålidelighed.
Fremstillingsudfordringer og Løsninger
Aerojet motor mikrofabrikation er i fronten af fremdriftsinnovation, som muliggør højere effektivitet, reducerede emissioner og lavere vægt i næste generations aerospace systemer. I takt med at 2025 nærmer sig, står sektoren over for både vedholdende og nye fremstillingsudfordringer, især i opnåelsen af højpræcision fremstillings-, materialekompatibilitet, termisk styring og skalerbar produktion.
En af de mest betydningsfulde udfordringer involverer præcis bearbejdning af mikroskala funktioner til komponenter som brændstofindsprøjtere, turbineblade og mikrokanal varmevekslere. Tolerancer på mikroniveau kræves for at sikre optimal forbrænding og effektivitet, men traditionelle subtraktive fremstillingsteknikker når deres grænser i nøjagtighed og gentagelighed. Som svar anvendes avancerede additiv fremstillings (AM) teknikker—såsom laser pulverbed fusion (LPBF) og elektronstrålesmeltning af virksomheder inkluderet GE Aerospace og Rolls-Royce, hvilket muliggør produktion af indviklede geometrier, der tidligere ikke kunne opnås. I 2023 rapporterede GE Aerospace succes med at printe turbinebladstoppe med integrerede kølekanaler, hvilket reducerede antallet af dele og forbedrede livscyklussen.
Materialevalg og kompatibilitet præsenterer en anden vedvarende udfordring. Aerojet motorer kræver superlegeringer og keramiske matrixkompositter, der modstår ekstreme temperaturer og ætsemiljøer, samtidig med at de opretholder mikrostrukturens integritet under mikrofabrikationsprocesser. Safran fortsætter med at investere i avanceret pulvermetallurgi og hybrids fremstillingsteknikker, med henblik på at kombinere den termiske modstandsdygtighed ved keramik med den mekaniske styrke ved metaller til mikrofabrikerede motor dele.
Termisk styring er kritisk på mikroskala, da varme koncentration kan føre til mikrorevner eller materialeforringelse. For at imødekomme dette integrerer producenter nu realtids termisk overvågning og closed-loop feedback systemer under fremstillingen. Siemens udvikler digitale tvillinger og in situ proceskontroller, der forudsiger og kompensere for termiske forvrængninger, hvilket forbedrer udbyttet og gentagelighed.
Skalerbarhed forbliver en central bekymring, efterhånden som efterspørgslen efter avancerede aerojet motorer stiger, særligt inden for kommerciel luftfart og rumforskning. Samarbejder som Airbus “Wing of Tomorrow”-programmet fremmer vidensdeling og standardisering inden for mikrofabrikationsprocesser, hvor målet er at accelerere overgangen fra prototyper til fuldskala produktion.
Ser man frem mod de kommende år, er udsigterne optimistiske. Den fortsatte konvergens af digital fremstilling, avancerede materialer og procesautomatisering forventes at mitigere nuværende udfordringer. Efterhånden som disse teknologier modnes, forventer brancheledere reduktioner i både omkostninger og cyklustid, hvilket baner vejen for bredere adoption af mikrofabrikerede aerojet motor komponenter i mainstream aerospace anvendelser.
Anvendelser i Kommercielle, Forsvars- og Rumsektorer
Aerojet motor mikrofabrikation oplever hurtige fremskridt på tværs af kommerciel luftfart, forsvar og rumsektorer, drevet af efterspørgslen efter højere effektivitet, reduceret komponentvægt og større designkompleksitet. Fra 2025 udnytter brancheledere mikrofabrikationsteknikker som additiv fremstilling, laser-baseret mikrobearbejdning og avanceret ætsning til at skabe indviklede motor dele med hidtil uset præcision og pålidelighed. Disse metoder tillader produktion af mikroskala funktioner, herunder kølekanaler, brændstofindsprøjtere og turbineblade, som er kritiske for at forbedre termisk styring og forbrændingseffektivitet i moderne aerojet motorer.
I den kommercielle luftfartssektor adopterer producenter mikrofabrikation for at støtte udviklingen af næste generations motorer, der sigter mod at reducere brændstofforbrug og emissioner. For eksempel integrerer virksomheder som GE Aerospace og Rolls-Royce Holdings aktivt mikroengineerede komponenter i deres nye motorplatforme. Disse bestræbelser er i overensstemmelse med branchens overordnede mål om at imødekomme strengere miljøreguleringer og forbedre den samlede flådes ydeevne. Mikrofabrikerede dele, såsom brændstofdyser og mikrokanal varmevekslere, valideres for holdbarhed og ydeevne, med de første produktionskørsler, der forventes at skalere op gennem det sene årti.
I forsvarssektoren forbedrer mikrofabrikation smidigheden og overlevelsesevnen af militære fly og missilsystemer. Programmer ledet af organisationer som Northrop Grumman og RTX Corporation anvender miniaturiserede fremdrivningssystemer og mikro-thrusters til præcisionsstyrede ammunition og ubemandede luftfartøjer (UAV’er). Disse komponenter drager fordel af mikrofabrikationens evne til at levere letvægts, kompakte designs uden at gå på kompromis med kraft eller pålidelighed. Det amerikanske forsvarsministerium forventes at udvide kontrakter, der fokuserer på mikrofabrikerede fremdrivningsløsninger, med sigte på feltdistribuering i slutningen af 2020’erne.
Rummsektoren drager også fordel af mikrofabrikation til at fremme designet af satellit fremdrivningssystemer og dybderumtsektorbiler. Virksomheder som Aerojet Rocketdyne udvikler mikro-fremdrivningsenheder, der muliggør præcise manøvredygtighed af småsatellitter og CubeSats. Disse systemer, der er afhængige af mikrofabrikerede thrusters og fluidiske kontrol enheder, er sat til kommercielle lanceringer og konstellationsudrulning begyndende i 2025 og fortsætter med at udvide i de følgende år.
Ser man frem, forventes integrationen af mikrofabrikerede aerojet motor komponenter at accelerere, efterhånden som innovation inden for materialevidenskab og digitale fremstillingsplatforme modnes. Branchesamarbejder og offentlige-private partnerskaber vil sandsynligvis spille en vigtig rolle i at skalere disse teknologier til bred anvendelse, hvilket sikrer, at kommercielle, forsvars- og rumaktører opretholder en konkurrencemæssig fordel inden for fremdriftsydelse og bæredygtighed.
Regulatorisk Landskab og Branche-standarder
Det regulatoriske landskab for aerojet motor mikrofabrikation udvikler sig hurtigt, efterhånden som luftfartsindustrien i stigende grad adopterer avancerede fremstillingsteknikker som mikro-elektromekaniske systemer (MEMS), additiv fremstilling og præcisions mikro-bearbejdning. I 2025 styres tilsynet af en kombination af etablerede luftfartsstandarder og nye rammer, der er skræddersyet til at imødekomme de unikke udfordringer og risici, der præsenteres af mikroskala behandlingsprocesser.
Nøgleregulatoriske organer som Federal Aviation Administration (FAA) og European Union Aviation Safety Agency (EASA) fortsætter med at fastsætte baseline sikkerheds- og kvalitetsstandarder for flymotorer, som nu omfatter komponenter produceret ved mikrofabrikation. Begge organisationer kræver, at producenter demonstrerer pålideligheden og gentageligheden af mikrofabrikerede dele gennem strenge test, dokumentation og sporbarhedsprotokoller. Efterhånden som mikrofabrikation muliggør produktionen af indviklede kølekanaler, brændstofdyser og sensorarrayer med hidtil uset præcision, opdaterer disse myndigheder certificeringsretningslinjer for at imødekomme potentielle nye fejlmetoder og inspektionsudfordringer, der er unikke for mikroskala strukturer.
SAE International fortsætter med at spille en central rolle i standardiseringen af mikrofabrikationsprocesser. Nylige opdateringer til standarder som AS9100 og AS9110 inkluderer nu specifikke bestemmelser for additiv og mikrofabrikationsproceskontrol, materialesporbarhed og inspektionskrav. I 2025 er der igangværende bestræbelser på at harmonisere disse standarder globalt for at lette internationale forsyningskæder og certificeringsreciprocitet. Branchegrupper samarbejder også med regulatoriske organer for at etablere nye testmetoder for mikrofabrikerede motor komponenter, med fokus på udmattelseslevetid, termisk cykling og defektdetektion på mikroskala.
Førende aerojet motor producenter, herunder GE Aerospace og Rolls-Royce, engagerer sig aktivt med regulatorerne og standardorganisationerne for at forme krav, der understøtter innovation samtidig med at de opretholder sikkerhed. Disse virksomheder har investeret i digitale kvalitetsstyringssystemer og interne certificeringskompetencer, idet de forudser, at den regulatoriske granskning vil intensiveres, efterhånden som mikrofabrikerede komponenter bliver stadig mere mission-kritiske. Bemærkelsesværdigt er det, at mens disse producenter skubber grænserne for design med mikroskala funktioner, støtter de oprettelsen af nye ikke-destruktive evalueringsprotokoller (NDE) og kvalifikationsprocedurer, der er skræddersyet til de unikke geometriske og materialeegenskaber ved mikrofabrikerede dele.
Ser man frem, forventes de kommende år at se indførelsen af mere granulære procescertificeringsveje, øget fokus på digitale tvillinger og proces simulering for regulatorisk overholdelse, samt vedtagelse af realtids overvågnings- og sporbarhedsværktøjer. Det dynamiske regulatoriske landskab vil kræve løbende samarbejde mellem OEM’er, leverandører og standardorganisationer for at sikre sikker, gentagelig og økonomisk rentabel implementering af aerojet motor mikrofabrikationsteknologier.
Investeringsmuligheder og Finansieringsindsigt
Aerojet motor mikrofabrikation—som omfatter avancerede fremstillingsmetoder som additiv fremstilling, laser mikrobearbejdning og præcisions ætning—har set en markant tilstrømning af investeringsaktiviteter, da luftfartssektoren presser på for lettere, mere effektive fremdrivningssystemer. I 2025 er området præget af en blanding af offentligt understøttede initiativer, strategisk virksomhedsinvestering og venturekapital, der retter sig mod både etablerede luftfarts-prime og smidige startups.
En væsentlig drivkraft for den nuværende investering er den voksende efterspørgsel efter højthårde, kompakte fremdrivningsenheder i både kommercielle og forsvarsansøgninger. Store motorproducenter skalerer deres mikrofabrikationsevner for at reducere deleantal, forbedre brændstofeffektivitet og muliggøre komplekse kølegeometrier, der tidligere ikke kunne opnås med traditionelle metoder. GE Aerospace og RTX er blandt de mest aktive, der kanaliserer R&D budgetter til at udvide mikrofabrikationslinjer og samarbejde med specialistleverandører. Samtidig fortsætter offentlig finansiering—især fra agenturer som det amerikanske forsvarsministerium og European Space Agency—med at støtte fremskridt inden for miniaturiseret fremdrivning til satellitter og hypersoniske køretøjer.
Tendensen mod offentligt-private partnerskaber accelererer. I 2025 er co-investering modeller blevet almindelige, hvor enheder som NASA støtter demonstrationsprojekter, der reducerer risikoen ved nye mikrofabrikationsteknikker til aerojet komponenter. Disse samarbejder fremmer ikke alene tekniske gennembrud, men stimulerer også privat efterfølgende finansiering. Nye aktører, herunder universitetspartnere og mikrofabrikation specialister, drager fordel af frø- og serie A-runder, som tilbydes af luftfartsfokuserede venturefonde og virksomheders venturearme fra større producenter.
Data fra igangværende finansieringsrunder tyder på, at kapital strømmer ind i områder som højtemperaturkeramisk, mikrokanal varmevekslere og integrerede skubvektornåse—nøglekomponenter, der muliggøres af avanceret mikrofabrikation. Leverandører, der specialiserer sig i laser- og elektronstråle additiv processer, rapporterer ordrebacklogs og ekspansionsplaner, drevet af flerårige indkøbsaftaler fra OEM’er og Tier 1 leverandører. For eksempel har Safran og Rolls-Royce begge annonceret øgede investeringer i in-house og partnerledede mikrofabrikationsevner for at støtte næste generations motorprogrammer.
Ser man frem mod de kommende år, forbliver investeringsudsigterne robuste. Sammenfaldet af digital design, automatisering og realtids procesovervågning forventes at reducere udviklingscyklusser og produktionsomkostninger yderligere. Efterhånden som regulatoriske organer bevæger sig mod at certificere mikrofabrikerede aerojet motor dele til bredere flyapplications, forventes sektoren at se vedvarende og diversificeret investering—positionering af mikrofabrikation som en central søjle i fremdriftsinnovation gennem slutningen af 2020’erne.
Fremtidsudsigter: Disruptive Innovationer og Konkurrence Dynamik
Landskabet for aerojet motor mikrofabrikation i 2025 er klar til betydelig transformation, drevet af disruptive innovationer inden for additiv fremstilling, avancerede materialer og digitale tvillingeteknologier. En vigtig tendens er integrationen af mikrofabrikationsteknikker—som laser pulverbed fusion og mikro-elektrisk afladningsbearbejdning (mikro-EDM)—i serieproduktionen af motor komponenter med komplekse geometrier og forbedrede præstationsegenskaber. Førende motorproducenter og leverandører intensiverer investeringerne i disse mikrofabrikationsevner for at opnå lettere, mere brændstofeffektive motorer med reducerede emissioner.
Virksomheder som GE Aerospace og Rolls-Royce plc er i front med at udvikle mikrofabrikerede jetmotor dele, herunder mikrodyser, brændstofindsprøjtere og kølekanaler. I 2025 lægger igangværende projekter i disse organisationer vægt på præcisionsfremstilling på sub-millimeter skala, der udnytter in-situ overvågning og AI-drevne proceskontroller for at sikre kvalitet og gentagelighed. Adoptionen af additivt fremstillede mikrokoponer forventes at udvide sig på tværs af både kommercielle og forsvars luftfartssektorer med op til 30% reduktioner i deleantal og betydelige forbedringer i motorens termodynamiske effektivitet.
Materialevidenskabsfremskridt former også fremtidsudsigterne. Introduktionen af højtemperatur keramiske matrixkompositter og nye superlegeringer, muliggjort ved mikrofabrikation, tillader tyndere vægge og mere indviklede interne kølekanaler—nøgle til at holde til højere driftstemperaturer. Safran og Pratt & Whitney arbejder aktivt på at fremme forskningspartnerskaber for at skalere produktionen af sådanne komponenter med henblik på at levere motorer med forbedret holdbarhed og lavere livscyklusomkostninger inden 2027.
Konkurrencedynerne intensiveres, da OEM’er og nøgleleverandører konkurrerer om at sikre intellektuel ejendom og kvalifikation for nye mikrofabrikerede dele. Der er voksende samarbejde mellem motorproducenter og specialiserede fabrikanter, såsom Siemens, som bruger deres ekspertise inden for digital fremstilling og procesautomatisering til at støtte hurtig prototyping og certificering af kritiske motorstrukturer. Samtidig forventes fremkomsten af startups og universitetspartnere, der fokuserer på nye mikrofabrikation processer, at yderligere forstyrre forsyningskæder og skubbe innovationscykler.
Ser man frem, vil de næste par år blive præget af accelererede certificeringsveje for mikrofabrikerede aerojet motor komponenter, drevet af digitale tvillingeverifikation og realtidsinspektionssystemer. Branchen forventer, at mikrofabrikation vil understøtte størstedelen af næste generations aerojet motorarkitekturer inden 2030, hvilket fundamentalt ændrer designmulighederne og driver en ny æra af bæredygtig, højtydende flyvning.
Kilder & Referencer
- GE Aerospace
- Honeywell
- GE Aerospace
- MTU Aero Engines
- Oxford Instruments
- Precision Micro
- NASA
- Siemens
- Airbus
- Northrop Grumman
- RTX Corporation
- GE Aerospace