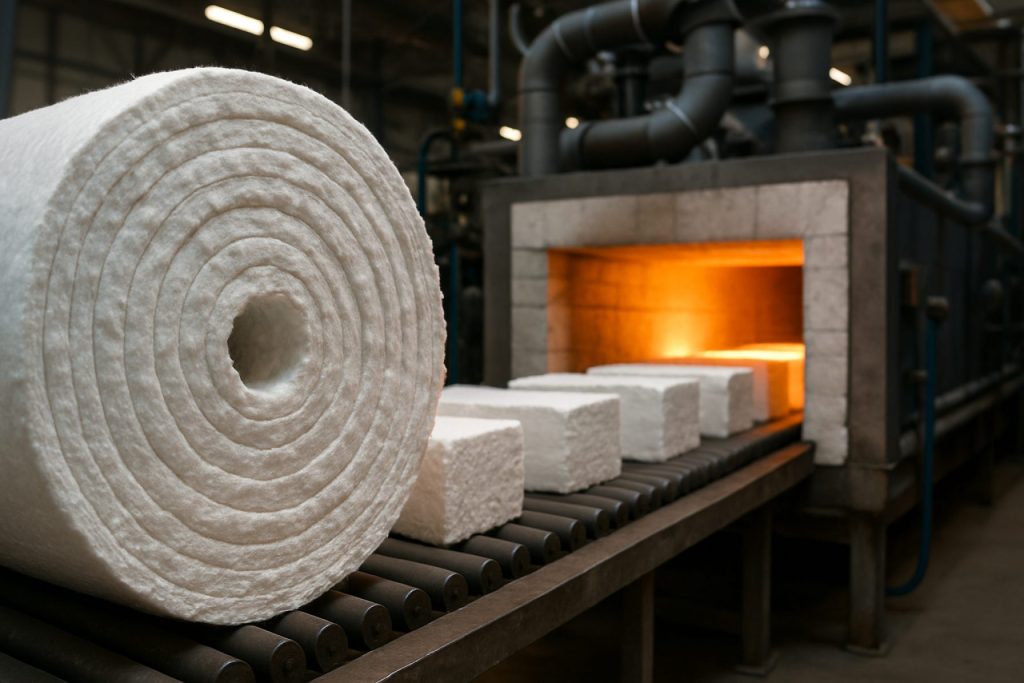
Refractory Ceramic Fiber Manufacturing in 2025: Navigating Explosive Growth, Regulatory Shifts, and Next-Gen Innovations. Discover How Industry Leaders Are Shaping the Future of High-Temperature Insulation.
- Executive Summary: 2025 and Beyond
- Global Market Size, Growth Rate & Forecasts (2025–2030)
- Key Manufacturers and Industry Leaders
- Emerging Technologies and Product Innovations
- Sustainability, Health, and Regulatory Developments
- Regional Analysis: North America, Europe, Asia-Pacific, and ROW
- End-Use Sectors: Steel, Petrochemicals, Power, and More
- Competitive Landscape and Strategic Initiatives
- Supply Chain, Raw Materials, and Pricing Trends
- Future Outlook: Opportunities, Challenges, and Disruptors
- Sources & References
Executive Summary: 2025 and Beyond
The refractory ceramic fiber (RCF) manufacturing sector is entering 2025 with a focus on technological innovation, regulatory adaptation, and global supply chain resilience. RCFs, prized for their high-temperature insulation properties, remain essential in industries such as petrochemicals, power generation, and metallurgy. The market is shaped by evolving environmental standards, increasing demand for energy efficiency, and the ongoing need for advanced thermal management solutions.
Key manufacturers, including Morgan Advanced Materials, Unifrax (now part of Alkegen), and Isolite Insulating Products, continue to invest in R&D to enhance fiber performance and reduce environmental impact. These companies are expanding their product portfolios to include low-bio-persistence fibers and eco-friendly alternatives, responding to stricter occupational health and safety regulations in North America, Europe, and parts of Asia. For example, Morgan Advanced Materials has developed a range of low-biopersistent fibers to address regulatory requirements and customer sustainability goals.
In 2025, the industry is witnessing a shift toward automation and digitalization in manufacturing processes. Leading producers are implementing advanced process controls and real-time monitoring to improve product consistency and reduce energy consumption. Unifrax has highlighted its commitment to sustainable manufacturing, including energy-efficient production lines and waste minimization initiatives, which are expected to become industry benchmarks in the coming years.
Geographically, Asia-Pacific remains the largest and fastest-growing market for RCFs, driven by robust industrialization in China, India, and Southeast Asia. Local manufacturers, such as Isolite Insulating Products and other regional players, are expanding capacity to meet rising domestic and export demand. Meanwhile, European and North American producers are focusing on high-value applications and compliance with increasingly stringent environmental and workplace safety standards.
Looking ahead, the RCF manufacturing sector is expected to see moderate growth through the late 2020s, with innovation centered on safer, more sustainable fiber chemistries and process efficiencies. Strategic partnerships, capacity expansions, and continued regulatory adaptation will define the competitive landscape. The sector’s outlook remains positive, underpinned by the essential role of RCFs in high-temperature industrial processes and the global push for energy efficiency and emissions reduction.
Global Market Size, Growth Rate & Forecasts (2025–2030)
The global refractory ceramic fiber (RCF) manufacturing sector is poised for steady growth from 2025 through 2030, driven by robust demand in high-temperature industrial applications such as petrochemicals, iron and steel, power generation, and ceramics. RCFs are valued for their exceptional thermal insulation, low thermal conductivity, and resistance to chemical attack, making them indispensable in furnace linings, kiln insulation, and fire protection systems.
As of 2025, the global RCF market is estimated to be valued in the low single-digit billions (USD), with leading manufacturers reporting strong order books and capacity expansions. The sector is expected to register a compound annual growth rate (CAGR) in the range of 4–6% through 2030, reflecting both organic growth in traditional end-use industries and emerging applications in energy transition technologies, such as hydrogen production and battery manufacturing.
Key players in the RCF manufacturing landscape include Morgan Advanced Materials, Unifrax (now part of Alkegen), Isolite Insulating Products, RATH Group, and 3M. These companies operate globally, with manufacturing facilities and R&D centers in North America, Europe, and Asia-Pacific. Morgan Advanced Materials and Unifrax are particularly notable for their extensive product portfolios and ongoing investments in next-generation fiber technologies, including low-bio-persistence and eco-friendly alternatives to traditional RCFs.
Regional growth dynamics are shaped by industrialization trends and regulatory environments. Asia-Pacific, led by China, India, and Southeast Asia, continues to be the largest and fastest-growing market, fueled by expansion in steel, cement, and petrochemical sectors. Europe and North America maintain steady demand, with a growing emphasis on compliance with occupational health and safety regulations regarding fiber emissions and worker exposure. This regulatory focus is prompting manufacturers to innovate and diversify their product offerings, including the development of safer, more sustainable fiber compositions.
Looking ahead, the RCF manufacturing sector is expected to benefit from increased infrastructure spending, decarbonization initiatives, and the modernization of industrial assets. However, the industry also faces challenges related to raw material costs, energy prices, and evolving environmental standards. Leading companies are responding with investments in process efficiency, recycling, and the development of advanced fiber solutions tailored to new market requirements.
Key Manufacturers and Industry Leaders
The refractory ceramic fiber (RCF) manufacturing sector in 2025 is characterized by a concentrated group of global leaders, ongoing technological innovation, and a strong focus on regulatory compliance and sustainability. RCFs are widely used for high-temperature insulation in industries such as petrochemicals, steel, power generation, and ceramics, making the sector strategically important for energy efficiency and emissions reduction.
Among the most prominent manufacturers, Morgan Advanced Materials stands out as a pioneer and one of the largest global producers of RCFs. The company operates advanced manufacturing facilities across Europe, North America, and Asia, and continues to invest in product development to address evolving regulatory requirements, particularly concerning the classification of RCFs as hazardous materials in some jurisdictions. Morgan’s product lines include bulk fibers, blankets, boards, and modules, serving a broad industrial customer base.
Another key player is Unifrax, which has a significant global footprint and a diversified portfolio of high-temperature insulation materials, including RCFs and next-generation low bio-persistent fibers. Unifrax has been at the forefront of developing safer alternatives to traditional RCFs, responding to increasing regulatory scrutiny in the European Union and other regions. The company’s focus on innovation is evident in its investments in new fiber chemistries and manufacturing processes aimed at reducing environmental and health impacts.
In Asia, Isolite Insulating Products Co., Ltd. is a leading manufacturer, particularly strong in the Japanese and broader Asian markets. Isolite produces a wide range of ceramic fiber products and has expanded its R&D efforts to develop fibers with improved thermal performance and reduced health risks. The company collaborates with industrial partners to tailor solutions for specific high-temperature applications.
Other notable manufacturers include RATH Group, which specializes in refractory solutions and ceramic fiber products for demanding industrial environments, and Ibiden Co., Ltd., which supplies advanced ceramic materials, including RCFs, to the global market.
Looking ahead, the RCF manufacturing industry is expected to see continued consolidation among major players, increased investment in sustainable and regulatory-compliant fiber technologies, and a gradual shift toward low bio-persistent and alternative fiber products. The drive for energy efficiency in heavy industry, coupled with tightening occupational health standards, will shape product development and market dynamics through 2025 and beyond.
Emerging Technologies and Product Innovations
The refractory ceramic fiber (RCF) manufacturing sector is experiencing a wave of technological advancements and product innovations as it adapts to evolving industrial demands and regulatory pressures in 2025. RCFs, prized for their high-temperature resistance and insulating properties, are critical in industries such as steel, petrochemicals, and power generation. However, the sector faces increasing scrutiny over environmental and health concerns, driving manufacturers to invest in safer, more sustainable solutions.
One of the most significant trends is the development of low-bio-persistence (LBP) fibers, which are designed to reduce potential health risks associated with traditional RCFs. Leading manufacturers such as Morgan Advanced Materials and Unifrax have expanded their portfolios to include LBP fiber products that meet stringent regulatory standards in Europe, North America, and Asia. These fibers are engineered to dissolve more rapidly in biological fluids, minimizing long-term health impacts while maintaining thermal performance.
Automation and digitalization are also reshaping RCF manufacturing processes. Companies are integrating advanced process controls, real-time monitoring, and data analytics to optimize fiber production, improve product consistency, and reduce energy consumption. For example, RATH Group has invested in smart manufacturing systems that enable precise control over fiber diameter and composition, resulting in higher-quality, application-specific products.
Product innovation is evident in the introduction of next-generation RCF modules and blanket systems with enhanced thermal efficiency and mechanical strength. These new products are tailored for demanding applications such as high-efficiency furnaces and emission control systems. Isolite Insulating Products Co., Ltd., a major Asian producer, has launched advanced fiber modules that offer improved installation speed and reduced heat loss, supporting energy-saving initiatives in heavy industry.
Sustainability is another key focus area. Manufacturers are exploring the use of recycled raw materials and cleaner production technologies to lower the environmental footprint of RCF manufacturing. Efforts to develop hybrid fiber systems—combining RCFs with alternative materials like polycrystalline wool—are gaining traction, offering a balance between performance, safety, and regulatory compliance.
Looking ahead, the RCF sector is expected to see continued investment in research and development, with a strong emphasis on health, safety, and environmental stewardship. As global industries pursue decarbonization and stricter workplace safety standards, demand for innovative, compliant refractory ceramic fiber solutions is set to grow through 2025 and beyond.
Sustainability, Health, and Regulatory Developments
The manufacturing of refractory ceramic fibers (RCFs) is undergoing significant transformation in 2025, driven by intensifying sustainability imperatives, evolving health standards, and tightening regulatory frameworks. RCFs, prized for their high-temperature resistance and insulation properties, are widely used in industries such as steel, petrochemicals, and power generation. However, concerns over their potential health risks—particularly their classification as possible carcinogens—have placed the sector under increasing scrutiny.
In 2025, regulatory agencies in North America, Europe, and Asia are advancing stricter controls on RCF production and use. The European Union continues to enforce its Registration, Evaluation, Authorisation and Restriction of Chemicals (REACH) regulations, which require manufacturers to implement rigorous exposure controls and labeling for RCFs. The EU’s focus on worker safety and environmental impact is prompting manufacturers to invest in advanced dust collection, filtration, and fiber encapsulation technologies. Major European producers such as Morgan Advanced Materials and Saint-Gobain are at the forefront, integrating best practices for emissions reduction and workplace safety.
In the United States, the Occupational Safety and Health Administration (OSHA) and the Environmental Protection Agency (EPA) are maintaining stringent permissible exposure limits for airborne fibers, with ongoing reviews to potentially lower thresholds further. U.S.-based manufacturers like Unifrax (now part of Alkegen) are responding by enhancing process automation, improving fiber containment, and developing alternative fiber chemistries with lower bio-persistence. These efforts are not only regulatory-driven but also reflect growing customer demand for safer, more sustainable insulation materials.
Asia-Pacific, led by China and Japan, is also seeing regulatory tightening, though implementation varies by country. Chinese manufacturers, including Shandong Minye Refractory Fibre, are increasingly aligning with international standards to maintain export competitiveness. Japanese firms, such as Isolite Insulating Products, are investing in R&D to create next-generation fibers with reduced health risks and improved recyclability.
Sustainability is a growing priority, with leading manufacturers setting ambitious targets for energy efficiency, waste reduction, and circularity. The development of low-bio-persistence (LBP) fibers—engineered to dissolve more rapidly in biological fluids—continues to accelerate, with several companies expanding their LBP product lines in 2025. These innovations are expected to gradually replace traditional RCFs in many applications, especially where regulatory or customer requirements are most stringent.
Looking ahead, the RCF manufacturing sector is poised for further evolution as global regulations tighten and sustainability expectations rise. Companies that proactively invest in safer chemistries, advanced manufacturing controls, and transparent supply chains are likely to maintain market leadership and regulatory compliance in the coming years.
Regional Analysis: North America, Europe, Asia-Pacific, and ROW
The global landscape for refractory ceramic fiber (RCF) manufacturing in 2025 is shaped by regional regulatory frameworks, industrial demand, and technological advancements. North America, Europe, Asia-Pacific, and the Rest of the World (ROW) each present distinct dynamics influencing production and market growth.
North America remains a significant producer and consumer of RCF, driven by robust demand from petrochemical, power generation, and metal processing industries. The United States, in particular, is home to major manufacturers such as Morgan Advanced Materials and Unifrax, both of which operate advanced facilities and invest in R&D for safer, more energy-efficient fiber products. Regulatory oversight by agencies such as OSHA and the EPA continues to shape manufacturing practices, with a focus on worker safety and emissions control. In 2025, North American producers are expected to further invest in low-bio-persistence fiber alternatives to comply with evolving health standards.
Europe is characterized by stringent environmental and occupational health regulations, particularly under REACH and the European Chemicals Agency (ECHA). This has led to a gradual shift from traditional RCFs to safer, eco-friendly alternatives. Leading European manufacturers, including Morgan Advanced Materials and Isolite, are at the forefront of this transition, focusing on the development of low-bio-persistent and alkaline earth silicate (AES) fibers. The region’s emphasis on decarbonization and energy efficiency in heavy industries is expected to sustain demand for advanced refractory solutions through 2025 and beyond.
Asia-Pacific is the fastest-growing region for RCF manufacturing, propelled by rapid industrialization in China, India, and Southeast Asia. China, in particular, dominates both production and consumption, with numerous domestic manufacturers such as Zircar Zirconia and Shandong Minye Refractory Fibre expanding capacity to meet rising demand from steel, cement, and glass industries. While regulatory standards are tightening, especially in China’s major industrial hubs, the region still faces challenges in harmonizing safety and environmental practices with Western counterparts. Nevertheless, Asia-Pacific’s cost advantages and growing technical expertise are expected to reinforce its leadership in global RCF output through the next several years.
Rest of the World (ROW) encompasses emerging markets in Latin America, the Middle East, and Africa. While these regions currently represent a smaller share of global RCF manufacturing, investments in infrastructure and energy projects are gradually increasing demand. International players such as Unifrax and Morgan Advanced Materials are expanding their presence through partnerships and localized production to capture growth opportunities in these developing markets.
Overall, the outlook for refractory ceramic fiber manufacturing in 2025 and the coming years is shaped by regional regulatory trends, industrial modernization, and the ongoing shift toward safer, more sustainable fiber technologies.
End-Use Sectors: Steel, Petrochemicals, Power, and More
Refractory ceramic fiber (RCF) manufacturing is closely tied to the performance and evolution of several heavy industrial sectors, notably steel, petrochemicals, and power generation. As of 2025, these end-use industries continue to drive demand for RCF products due to their need for high-temperature insulation, energy efficiency, and operational safety.
The steel industry remains the largest consumer of refractory ceramic fibers, utilizing them in applications such as furnace linings, ladle covers, and heat shields. The ongoing modernization of steel plants, particularly in Asia and the Middle East, is expected to sustain robust demand for RCF. Major steel producers are increasingly focused on reducing energy consumption and emissions, which further incentivizes the adoption of advanced insulation materials like RCF. Companies such as Tata Steel and ArcelorMittal have highlighted the importance of refractory solutions in their sustainability strategies.
In the petrochemical sector, RCFs are essential for lining reactors, reformers, and other high-temperature process equipment. The sector’s expansion in regions such as the United States, China, and the Middle East is expected to bolster RCF consumption through 2025 and beyond. Leading RCF manufacturers, including Morgan Advanced Materials and Unifrax, supply a range of fiber-based products tailored for the chemical processing industry, emphasizing both thermal performance and regulatory compliance.
Power generation, particularly in thermal and waste-to-energy plants, is another significant end-use sector. RCFs are used for insulating boilers, turbines, and exhaust systems, contributing to improved thermal efficiency and reduced maintenance costs. The global shift toward cleaner energy sources is prompting upgrades and retrofits in existing power infrastructure, which is expected to support steady RCF demand. Companies like RATH Group and Isolite are active in supplying RCF solutions for power sector applications.
Beyond these core sectors, RCFs are also finding increased use in industries such as ceramics, glass, and aerospace, where high-temperature stability and lightweight insulation are critical. The outlook for 2025 and the following years suggests continued growth in RCF manufacturing, driven by industrial expansion, stricter energy efficiency standards, and ongoing innovation in fiber technology. However, regulatory scrutiny regarding the health and environmental impacts of RCFs may influence product development and market dynamics, prompting manufacturers to invest in safer, next-generation fiber materials.
Competitive Landscape and Strategic Initiatives
The competitive landscape of refractory ceramic fiber (RCF) manufacturing in 2025 is characterized by a concentrated group of global players, ongoing capacity expansions, and a strategic pivot toward sustainable and regulatory-compliant solutions. The sector is dominated by a handful of multinational corporations with vertically integrated operations, robust R&D capabilities, and extensive distribution networks. Key players include Morgan Advanced Materials, Unifrax (now part of Alkegen), Isolite Insulating Products, RATH Group, and IBIDEN. These companies are recognized for their global manufacturing footprints and their ability to serve high-temperature industrial markets such as petrochemicals, power generation, and metallurgy.
In 2025, strategic initiatives are increasingly shaped by tightening environmental and occupational health regulations, particularly in North America, Europe, and parts of Asia. Companies are investing in the development of low-bio-persistence (LBP) fibers and alternative high-temperature insulation materials to address regulatory restrictions on traditional RCFs, which are classified as possible carcinogens in some jurisdictions. For example, Morgan Advanced Materials has expanded its product portfolio to include Superwool® low-bio-persistent fibers, which are designed to meet stringent EU and US standards while maintaining thermal performance. Similarly, Unifrax (Alkegen) continues to invest in its FyreWrap® and Insulfrax® product lines, emphasizing both regulatory compliance and energy efficiency.
Capacity expansion and localization of production are also prominent strategies. In response to supply chain disruptions and rising transportation costs, manufacturers are increasing investments in regional production facilities. Isolite Insulating Products and RATH Group have announced plans to enhance their manufacturing capabilities in Asia and Europe, respectively, to better serve local markets and reduce lead times.
Strategic partnerships and acquisitions are further shaping the competitive landscape. Companies are collaborating with end-users and technology providers to co-develop next-generation fiber solutions with improved safety profiles and performance characteristics. For instance, IBIDEN has focused on joint R&D initiatives with automotive and electronics manufacturers to tailor RCF products for emerging applications, such as battery thermal management and advanced ceramics.
Looking ahead, the RCF manufacturing sector is expected to see continued consolidation, with leading players leveraging scale, innovation, and regulatory expertise to maintain competitive advantage. The shift toward sustainable and compliant fiber solutions is likely to accelerate, driven by both customer demand and evolving global standards.
Supply Chain, Raw Materials, and Pricing Trends
The supply chain for refractory ceramic fiber (RCF) manufacturing in 2025 is shaped by evolving raw material sourcing, regulatory pressures, and shifting global demand. RCFs are primarily produced from high-purity alumina and silica, with kaolin clay and other additives sometimes used depending on the fiber grade. The availability and price of these raw materials are influenced by mining output, energy costs, and environmental regulations, particularly in major producing countries such as China and the United States.
China remains the dominant supplier of both raw materials and finished RCF products, with companies like ZIRCAR Refractory Composites and RATH Group maintaining significant production capacities. However, ongoing environmental crackdowns and stricter emissions standards in China have led to periodic supply disruptions and increased costs for alumina and silica, which are reflected in the pricing of RCFs globally. In the United States, manufacturers such as Morgan Advanced Materials and Unifrax (now part of Alkegen) continue to invest in domestic supply chains to reduce reliance on imports and mitigate volatility.
The RCF market in 2025 is also affected by logistics challenges, including container shortages and fluctuating freight rates, which have persisted since the COVID-19 pandemic. These factors contribute to longer lead times and higher landed costs, particularly for customers in Europe and North America. To address these issues, some manufacturers are expanding regional production and warehousing, as seen with Morgan Advanced Materials’s recent investments in North American facilities.
Pricing trends for RCFs in 2025 reflect both supply-side constraints and robust demand from high-temperature industries such as steel, petrochemicals, and power generation. While prices stabilized somewhat after the sharp increases of 2021–2023, they remain elevated compared to pre-pandemic levels. Industry sources report that the average price of high-purity RCF blankets and modules is up 10–15% year-on-year, driven by higher energy and raw material costs as well as compliance with stricter occupational health regulations.
Looking ahead, the outlook for RCF supply chains is mixed. On one hand, ongoing investments in automation and recycling of ceramic fibers are expected to improve efficiency and reduce waste. On the other, regulatory scrutiny—especially in the European Union, where RCFs are classified as carcinogenic—may prompt further shifts toward alternative fiber types, such as alkaline earth silicate (AES) fibers. Nevertheless, established players like Unifrax and Morgan Advanced Materials are well-positioned to adapt, leveraging their global networks and R&D capabilities to ensure supply continuity and competitive pricing in the coming years.
Future Outlook: Opportunities, Challenges, and Disruptors
The refractory ceramic fiber (RCF) manufacturing sector is poised for significant transformation in 2025 and the coming years, shaped by evolving regulatory landscapes, technological advancements, and shifting market demands. As a critical material for high-temperature insulation in industries such as petrochemicals, steel, and power generation, RCF continues to be indispensable, yet faces mounting scrutiny over health and environmental concerns.
One of the most prominent challenges for RCF manufacturers is the tightening of occupational health and safety regulations, particularly in North America and Europe. Regulatory bodies are increasingly classifying certain RCFs as potential carcinogens, prompting stricter exposure limits and driving demand for safer alternatives. Leading producers such as Morgan Advanced Materials and Unifrax (now part of Alkegen) are investing heavily in research and development to create low-bio-persistence fibers and next-generation materials that meet both performance and safety standards.
Opportunities are emerging from the global push for energy efficiency and decarbonization. As industries seek to reduce energy consumption and emissions, demand for advanced thermal insulation solutions is expected to rise. RCFs, with their superior insulating properties, are well-positioned to benefit, provided manufacturers can address regulatory and sustainability concerns. Companies like Isolite Insulating Products and RATH Group are expanding their product portfolios to include eco-friendly and high-performance fiber solutions tailored for new energy and hydrogen applications.
However, the sector faces disruptors in the form of alternative materials, such as polycrystalline wool and bio-soluble fibers, which offer similar thermal performance with improved health profiles. The adoption of these alternatives is accelerating, especially in regions with stringent regulations. To remain competitive, established RCF manufacturers are diversifying their offerings and investing in process innovations, such as automated fiber production and digital quality control systems.
Geopolitical factors and supply chain dynamics also play a crucial role in shaping the outlook. The concentration of raw material sources and manufacturing capacity in Asia, particularly China, introduces both opportunities for cost-effective production and risks related to trade policies and export controls. Major Chinese producers, including Shandong Minye Refractory Fibre, are expanding their global reach, intensifying competition and driving further innovation.
In summary, the future of refractory ceramic fiber manufacturing will be defined by the industry’s ability to adapt to regulatory pressures, embrace sustainable innovation, and respond to the evolving needs of high-temperature industrial applications. Companies that proactively address these challenges and capitalize on emerging opportunities are likely to maintain a competitive edge in the years ahead.
Sources & References
- Morgan Advanced Materials
- Unifrax
- Isolite Insulating Products
- RATH Group
- Ibiden Co., Ltd.
- Shandong Minye Refractory Fibre
- Isolite
- Zircar Zirconia
- Tata Steel
- ArcelorMittal