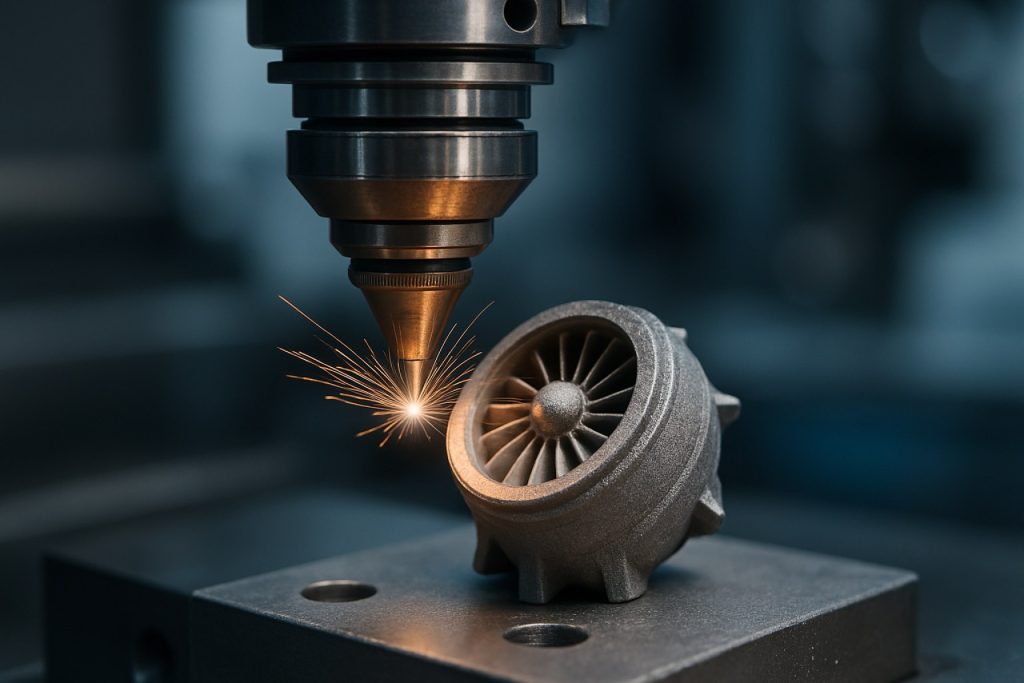
Inhaltsverzeichnis
- Zusammenfassung: Mikrofabrikation von Aerojet-Motoren im Jahr 2025
- Marktgröße und Wachstumsprognose: 2025–2030
- Wichtige Akteure und Branchenkooperationen
- Mikrofabrikationstechnologien, die Aerojet-Motoren revolutionieren
- Fortschritte in der Materialwissenschaft: Legierungen, Keramiken und Verbundstoffe
- Herausforderungen und Lösungen in der Fertigung
- Anwendungen in den Bereichen Kommerzielle, Verteidigung und Raumfahrt
- Regulatorische Rahmenbedingungen und Branchenstandards
- Investitionstrends und Finanzierungsinformationen
- Zukunftsausblick: Disruptive Innovationen und Wettbewerbskräfte
- Quellen & Referenzen
Zusammenfassung: Mikrofabrikation von Aerojet-Motoren im Jahr 2025
Die Mikrofabrikation von Aerojet-Motoren gestaltet im Jahr 2025 die Landschaft der Luftfahrtantriebe schnell um, angetrieben von der Nachfrage nach höherer Effizienz, geringerem Gewicht und verbesserter Zuverlässigkeit in den Bereichen Kommerzielle und Verteidigung. Mikrofabrikation – einschließlich Techniken wie mikro-elektrische Entladungsspannungsmachining (micro-EDM), Laserablation und fortschrittliche additive Fertigung – ermöglicht die Herstellung komplexer Motorenkomponenten im Mikrometerbereich, die zuvor mit traditionellen Fertigungsmethoden unmöglich oder sehr kostenintensiv waren.
Das Jahr 2025 markiert einen bedeutenden Wendepunkt für die Akzeptanz, da große Hersteller von Antriebssystemen und Zulieferer ihre Investitionen in Mikrofabrikationseinrichtungen und -prozesse beschleunigen. Unternehmen wie GE Aerospace und Rolls-Royce entwickeln und implementieren weiterhin Mikrofabrikation für Teile von nächsten Generationen von Triebwerken, insbesondere Turbinenschaufeln, Kraftstoffeinspritzern und Mikrokanalwärmetauschern. Diese Fortschritte verbessern nicht nur die Leistung und Effizienz der Motoren, sondern verlängern auch die Lebensdauer der Komponenten und reduzieren die Wartungsintervalle.
Die Akzeptanz wird zusätzlich durch erfolgreiche Pilotprojekte und Produktionsläufe vorangetrieben, die erhebliche Leistungsgewinne gezeigt haben. Beispielsweise haben mikrostrukturiert Kühlkanäle in Turbinenschaufeln höhere Betriebstemperaturen ermöglicht, was sich direkt in verbesserten Schub-Gewicht-Verhältnissen und geringerem Kraftstoffverbrauch niederschlägt. Solche Innovationen stehen in engem Zusammenhang mit strengen Emissionszielen und Nachhaltigkeitsmandaten von Regulierungsbehörden, die die Hersteller zwingen, Mikrofabrikation zu übernehmen, um zukünftige Umweltstandards zu erfüllen.
Die Lieferkette für mikrofabrizierte Aerojet-Motorenteile wird immer robuster, da wichtige Materialzulieferer wie Honeywell in spezialisierte Legierungen und keramische Verbundstoffe investieren, die auf mikrostrukturierte Merkmale abgestimmt sind. Gleichzeitig bringen Werkzeughersteller und Prozess-technologiefirmen neue Plattformen auf den Markt, die speziell für die Mikrofabrikation in der Luftfahrt konzipiert sind und dabei Präzision, Wiederholbarkeit und Skalierbarkeit betonen.
Blickt man auf die kommenden Jahre, ist die Aussichten für die Mikrofabrikation von Aerojet-Motoren sehr positiv. Branchenprognosen und laufende F&E-Daten deuten darauf hin, dass bis 2027–2028 mikrofabrizierte Komponenten in sowohl kommerziellen als auch militärischen Motorenprogrammen alltäglich werden, wobei die Produktionsmengen voraussichtlich steigen werden, da die Kostenbarrieren weiter sinken. Kooperative Bemühungen zwischen Motorherstellern, Materialspezialisten und akademischen Institutionen beschleunigen ebenfalls das Innovationstempo, mit einem Fokus auf digitale Designintegration, Echtzeitprozessüberwachung und automatisierte Qualitätskontrolle.
Zusammenfassend lässt sich sagen, dass 2025 ein entscheidendes Jahr für die Mikrofabrikation von Aerojet-Motoren darstellt, in dem Branchenführer und Zulieferer sich verpflichtet haben, diese transformierenden Technologien zu skalieren und den Grundstein für eine neue Ära der Antriebseffizienz, Langlebigkeit und Nachhaltigkeit zu legen.
Marktgröße und Wachstumsprognose: 2025–2030
Der globale Markt für die Mikrofabrikation von Aerojet-Motoren steht zwischen 2025 und 2030 vor erheblichem Wachstum, getrieben von der steigenden Nachfrage nach kraftstoffeffizienten, emissionsarmen Antriebssystemen sowohl in der kommerziellen als auch in der Verteidigungs-Luftfahrtbranche. Mikrofabrikationstechniken – wie fortschrittliche additive Fertigung, Integration mikroelektromechanischer Systeme (MEMS) und präzise Lasermachining – werden in die Kernfertigungsprozesse neuer Generationen von Triebwerken integriert, um leichte, leistungsstarke Komponenten zu ermöglichen. Wichtige Branchenakteure investieren in den Ausbau der Produktionskapazitäten und die Entwicklung neuer Materialsysteme, um den sich wandelnden Anforderungen der Luftfahrtantriebe gerecht zu werden.
Ab 2025 nutzen führende Triebwerkshersteller wie GE Aerospace, Rolls-Royce und Pratt & Whitney Mikrofabrikation, um die Miniaturisierung der Komponenten zu verbessern, die Geometrien der Kühlkanäle zu optimieren und die Designs der Kraftstoffdüsen zu optimieren. Beispielsweise haben mikrofabrizierte Komponenten in Kraftstoffeinspritzsystemen und Turbinenschaufeln messbare Verbesserungen bei der thermischen Effizienz und der Emissionsreduzierung erzielt. Diese Fortschritte werden durch Kooperationen mit spezialisierten Zulieferern wie Safran und MTU Aero Engines unterstützt, die ebenfalls ihre Mikrofabrikation-Fähigkeiten erweitern.
Die Marktexpansion steht in engem Zusammenhang mit der weiteren Akzeptanz der additiven Fertigung und der laserbasierten Mikrobohrungen zur Herstellung präziser Triebwerksmerkmale im großen Maßstab. Laut Aussagen von GE Aerospace und Rolls-Royce wird ein wachsender Anteil neuer Triebwerks Teile – insbesondere für Narrowbody- und Regionalflugzeuge – bis 2030 mikro-fabrizierte Elemente enthalten. Dies wird voraussichtlich zu einer durchschnittlichen jährlichen Wachstumsrate (CAGR) im hohen einstelligen Bereich für den Sektor der Mikrofabrikation von Aerojet-Motoren während des gesamten Zeitraums führen.
- Nordamerika und Europa werden die Hauptmärkte bleiben, unterstützt durch laufende Flottenrenovierungen und strenge Emissionsvorschriften.
- Asien-Pazifik wird voraussichtlich die schnellste Akzeptanz erleben, da die Produktion regionaler Flugzeuge und Verteidigungsmodernisierungsprogramme zunimmt.
- Investitionen in F&E und neue Produktionslinien von Haupt-OEMs und Zulieferern werden voraussichtlich während des Prognosezeitraums zunehmen, wobei bereits hohe Verträge für mikrofabrizierte Turbine- und Verbrennungs-Komponenten gemeldet wurden.
Mit Blick auf die Zukunft ist der Marktausblick für 2025–2030 robust, wobei die Mikrofabrikation voraussichtlich zum Standard in der Konstruktion und Produktion von Aerojet-Motoren werden wird. Die Konvergenz von regulatorischem Druck, Materialinnovationen und reifenden Fertigungstechnologien wird voraussichtlich das Wachstum aufrechterhalten und den Wettkampf zwischen etablierten und aufstrebenden Branchenakteuren verstärken.
Wichtige Akteure und Branchenkooperationen
Die Landschaft der Mikrofabrikation von Aerojet-Motoren im Jahr 2025 wird durch eine Kombination aus etablierten Herstellern der Luftfahrtindustrie, innovativen Zulieferern und sektorübergreifenden Kooperationen geprägt. Wichtige Akteure investieren in fortschrittliche Mikrofabrikation, um die Effizienz der Antriebssysteme zu verbessern, Emissionen zu reduzieren und neue Motorarchitekturen für die kommerzielle und militärische Luftfahrt zu ermöglichen.
Zu den globalen Führern gehört GE Aerospace, das weiterhin Mikrofabrikation-Initiativen anführt und additive Fertigung (AM) sowie mikroelektromechanische Systeme (MEMS) für Turbinenkomponenten und Kraftstoffeinspritzer nutzt. Ihre fortwährenden Investitionen in AM-Technologie ermöglichen die Herstellung komplizierter Kühlkanäle und optimierter Geometrien auf Mikrometerskala, die sowohl großen Motorenlinien als auch emerging kleinen Antriebssystemen zugutekommen. Rolls-Royce ist ähnlich aktiv und arbeitet kontinuierlich mit Materialtechnologiefirmen und Forschungsinstitutionen zusammen, um mikrostrukturierte Fertigungsprozesse für hochtemperaturbeständige Legierungen und keramische Matrixverbundstoffe zu verfeinern. Diese Bemühungen sind entscheidend für die nächsten Generationen von Triebwerken, die auf Kraftstoffeffizienz und geringeres Gewicht setzen.
Auf der Zuliefererseite sind Oxford Instruments und Precision Micro prominent in der Bereitstellung von Mikrofabrikationstools und photochemischen Ätzdiensten. Ihre Technologien ermöglichen es Motor-OEMs, ultrafeine Toleranzen in miniaturisierten Komponenten wie Mikro-Düsen, Sensoren und Wärmetauschern zu erreichen. Honeywell Aerospace, ein weiterer wichtiger Akteur, integriert MEMS-basierte Sensoren, die auf Mikrometerskala gefertigt sind, in ihre Motorsteuerungs- und Gesundheitsüberwachungssysteme und signalisiert damit einen Trend hin zu Digitalisierungs- und datenbasierten Wartung.
Branchenkooperationen nehmen an Dynamik zu, da Unternehmen bestrebt sind, Innovationen zu beschleunigen und die hohen Kosten, die mit der Mikrofabrikations-F&E verbunden sind, zu teilen. Beispielsweise entstehen Joint Ventures zwischen primären Motorherstellern und Halbleiterfabriken, um Fachwissen in der Mikroechnik in den Luftfahrtsektor zu übertragen. Zudem erleichtern Partnerschaften mit nationalen Forschungslabors und Universitäten – wie sie von NASA gefördert werden – den Transfer von Mikrofabrikationstechniken von Laboren zu kommerziellen Motorenplattformen.
Mit Blick in die Zukunft wird erwartet, dass die kommenden Jahre eine zunehmende Investition in integrierte Lieferketten mit sich bringen, bei denen OEMs die Beziehungen zu Mikrofabrikation-Spezialisten vertiefen, um die Massenproduktion komplexer, miniaturisierter Motorenteile zu ermöglichen. Angesichts strengerer Umweltschutzvorschriften wird die Rolle der Mikrofabrikation bei der Erreichung einer höheren Kraftstoffeffizienz und der Einhaltung von Emissionsstandards zudem eine verstärkte Zusammenarbeit und technologische Fortschritte in der gesamten Branche anregen.
Mikrofabrikationstechnologien, die Aerojet-Motoren revolutionieren
Die rasante Entwicklung von Mikrofabrikationstechnologien verwandelt grundlegend die Entwicklung und Leistung von Aerojet-Motoren, während der Luftfahrtsektor im Jahr 2025 voranschreitet. Traditionelle Fertigungsmethoden werden zunehmend durch fortschrittliche mikro-skalierten Prozesse ersetzt, die die Produktion von hochkomplexen, präzisen und leichten Motorenteilen ermöglichen. Ein Haupttreiber dieses Wandels ist die Übernahme der additiven Fertigung (AM), allgemein bekannt als 3D-Druck, insbesondere durch Techniken wie selektives Laserschmelzen (SLM) und Elektronenstrahlschmelzen (EBM). Diese Prozesse ermöglichen die Fertigung von komplexen Kraftstoffeinspritzern, Turbinenschaufeln und Kühlkanälen mit inneren Geometrien, die zuvor mit konventionellen subtraktiven Methoden nicht realisierbar waren.
Führende Antriebsgesellschaften setzen nun Mikrofabrikation ein, um das Gewicht zu reduzieren und die thermischen Effizienzen zu verbessern. Zum Beispiel hat GE Aerospace erfolgreich AM-hergestellte Kraftstoffdüsen in seinen LEAP-Motoren integriert und eine Gewichtsreduzierung von 25 % sowie eine fünffache Erhöhung der Haltbarkeit im Vergleich zu traditionell hergestellten Varianten erreicht. Das Unternehmen setzt seine Nutzung von Mikrofabrikation für Komponenten der nächsten Generation fort und konzentriert sich auf engere Toleranzen und kürzere Vorlaufzeiten. Ebenso investiert Rolls-Royce in mikrofabrizierte Turbinenkomponenten und nutzt Gitterstrukturen und fortschrittliche Kühlkanäle, um die Grenzen der Effizienz und Lebensdauer von Motoren zu erweitern.
Die Rolle von mikroelektromechanischen Systemen (MEMS) in Aerojet-Motoren wächst ebenfalls, wobei die Miniaturisierung von Komponenten verbesserte Sensorik, Überwachung und Aktuation in rauen Motorenbedingungen ermöglicht. Unternehmen wie Safran entwickeln MEMS-basierte Sensorarrays für die Echtzeit-Datenakquisition, welche die vorausschauende Wartung und eine höhere Betriebssicherheit vorantreiben. Die Integration von MEMS in Antriebssysteme wird voraussichtlich verbreiteter, da die Produktionsskalierbarkeit und Zuverlässigkeit in den kommenden Jahren verbessert werden.
Mit Blick auf die Zukunft wird erwartet, dass die fortschreitende Reifung von Mikrofabrikationstechnologien die Innovation in der Konstruktion und Herstellung von Aerojet-Motoren bis 2025 und darüber hinaus beschleunigt. Das Aufkommen neuartiger Materialien, wie hitzebeständige Superlegierungen und keramische Matrixverbundstoffe, in Verbindung mit präziser Mikrofabrikation wird die Leistungskennzahlen weiter steigern. Branchenanalysten prognostizieren ein wachsendes Ökosystem spezialisierter Zulieferer und Partner, die sich auf Mikro-Skalen-Luftfahrtkomponenten konzentrieren, und bedeutende Investitionen von großen Akteuren wie Pratt & Whitney und MTU Aero Engines werden voraussichtlich die Akzeptanz sowohl im kommerziellen als auch im Verteidigungsflugsektor vorantreiben.
Fortschritte in der Materialwissenschaft: Legierungen, Keramiken und Verbundstoffe
Im Jahr 2025 erlebt die Mikrofabrikation von Aerojet-Motorenteilen erhebliche Fortschritte in der Materialwissenschaft, insbesondere durch die Integration neuartiger Legierungen, Keramiken und Verbundstoffe. Der kontinuierliche Druck für höhere Effizienz, geringeres Gewicht und bessere thermische Resilienz in Aerojet-Antriebssystemen hat zur Forschung und industriellen Einführung von modernsten Materialien und innovativen Fertigungstechniken geführt.
Fortschrittliche nickelbasierte Superlegierungen bleiben das Rückgrat der Fertigung im Turbinenbereich aufgrund ihrer hervorragenden mechanischen Festigkeit und der Widerstandsfähigkeit gegenüber Hochtemperatur-Abbau. Allerdings konzentrieren sich die laufenden Entwicklungen darauf, die Kriechbeständigkeit und den Oxidationsschutz bei Betriebstemperaturen über 1200 °C zu verbessern. Unternehmen wie GE Aerospace und Rolls-Royce entwickeln aktiv neue Legierungsformulierungen mit maßgeschneiderten Mikrostrukturen, die durch additive Fertigung ermöglicht werden. Elektronenstrahlschmelzen und laserstrahlgeführte Pulverbettschmelze werden nun routinemäßig eingesetzt, um Turbinenschaufeln und -flügel mit komplexen inneren Kühlkanälen im Mikrometerskala herzustellen, um die thermische Leistung zu verbessern und das Gewicht der Komponenten zu verringern.
Keramische Matrixverbundstoffe (CMCs) haben den Übergang von der experimentellen zur kommerziellen Anwendung in Hot-Section-Komponenten vollzogen. Siliziumcarbid-basierte CMCs beispielsweise bieten Gewichtseinsparungen von bis zu 30 % im Vergleich zu herkömmlichen Legierungen und können bei Temperaturen 200–300 °C höher betrieben werden als ihre metallischen Pendants. Im Jahr 2025 erweitern Safran und GE Aerospace weiterhin den Einsatz von CMCs in Verbrennungslinern und Turbinenkappen, unterstützt durch Fortschritte in der Faserarchitektur, Schnittstellenbeschichtungen und skalierbaren Fertigungstechniken wie chemischer Dampfablagerung und Schlicker-Infiltration.
Verbundstoffe, die mit Nanomaterialien – wie Kohlenstoffnanoröhren und Graphen – verstärkt sind, sind ebenfalls Gegenstand aktiver Untersuchungen, um ihr Potenzial zur weiteren Gewichtseinsparung bei gleichzeitig verbesserten mechanischen und thermischen Eigenschaften zu prüfen. Hersteller arbeiten mit Materialwissenschaftsinstituten zusammen, um die Dispersion und Ausrichtung von Nanoverstärkungen innerhalb metallischer und keramischer Matrices zu optimieren, mit dem Ziel der kommerziellen Reife in den nächsten Jahren.
Blickt man in die Zukunft, konzentriert sich der Ausblick für die Mikrofabrikation von Aerojet-Motoren auf die Konvergenz fortschrittlicher Materialien und digitaler Fertigung. Echtzeit-Prozessüberwachung, inline-Qualitätskontrolle und KI-gesteuerte Mikrostruktur-Optimierung sollen die Qualifizierung und Integration von Legierungen, CMCs und hybriden Verbundstoffen der nächsten Generation beschleunigen. Diese Synergie ermöglicht nicht nur Motoren mit höheren Schub-Gewicht-Verhältnissen und Kraftstoffeffizienz, sondern unterstützt auch die Nachhaltigkeitsziele der Luftfahrtindustrie durch eine längere Lebensdauer der Komponenten und einen reduzierten Rohstoffverbrauch. Während sich diese Technologien weiterentwickeln, sind führende Branchenakteure wie GE Aerospace, Rolls-Royce und Safran bereit, neue Standards in der Leistung und Zuverlässigkeit von Aerojet-Antrieben zu setzen.
Herausforderungen und Lösungen in der Fertigung
Die Mikrofabrikation von Aerojet-Motoren steht an der Schnittstelle von Antriebstechnologie-Innovation und ermöglicht eine höhere Effizienz, reduzierte Emissionen und ein geringeres Gewicht in zukünftigen Luftfahrtantriebssystemen. Mit dem Herannahen des Jahres 2025 sieht sich der Sektor sowohl anhaltenden als auch aufkommenden Herausforderungen in der Fertigung gegenüber, insbesondere in Bezug auf die Erreichung von hochpräziser Verarbeitung, Materialkompatibilität, thermisches Management und skalierbare Produktion.
Eine der größten Hürden besteht darin, mikroskalierte Merkmale für Komponenten wie Kraftstoffeinspritzer, Turbinenschaufeln und Mikrokanalwärmetauscher präzise zu bearbeiten. Toleranzen auf Mikrometerskala sind erforderlich, um eine optimale Verbrennung und Effizienz sicherzustellen, doch traditionelle subtraktive Fertigungsmethoden stoßen in Bezug auf Genauigkeit und Wiederholbarkeit an ihre Grenzen. Als Reaktion darauf werden fortschrittliche additive Fertigungstechniken (AM) – wie laserstrahlgeführte Pulverbettschmelze (LPBF) und Elektronenstrahlschmelzen – von Unternehmen wie GE Aerospace und Rolls-Royce eingesetzt, die die Produktion komplexer Geometrien ermöglichen, die zuvor nicht erreichbar waren. Im Jahr 2023 berichtete GE Aerospace über Erfolge beim Drucken von Turbinenschaufelspitzen mit integrierten Kühlkanälen, die die Anzahl der Teile reduzieren und die Lebenszyklusleistung verbessern.
Die Materialauswahl und -kompatibilität stellt eine weitere anhaltende Herausforderung dar. Aerojet-Motoren erfordern Superlegierungen und keramische Matrixverbundstoffe, die extremen Temperaturen und korrosiven Umgebungen standhalten können, während sie während der Mikrofabrikation die mikrostrukturelle Integrität bewahren. Safran investiert weiterhin in fortschrittliche Pulvermetallurgie und hybride Fertigungstechniken, um die thermische Resilienz von Keramiken mit der mechanischen Festigkeit von Metallen für mikrofabrizierte Motorenteile zu verbinden.
Das thermische Management ist im Mikromaßstab kritisch, da Hitzeansammlung zu Mikrorissen oder Materialverformungen führen kann. Um dem entgegenzuwirken, integrieren Hersteller Echtzeit-Überwachungssysteme und geschlossene Regelkreise während der Fertigung. Siemens entwickelt digitale Zwillinge und in-situ-Prozesskontrollen, die thermische Verzerrungen vorhersagen und kompensieren, um die Ausbeute und Wiederholbarkeit zu verbessern.
Die Skalierbarkeit bleibt ein zentrales Anliegen, da die Nachfrage nach fortschrittlichen Aerojet-Motoren wächst, insbesondere in der kommerziellen Luftfahrt und Raumfahrt. Zusammenarbeit wie das Airbus „Wing of Tomorrow“-Programm fördert den Wissensaustausch und die Standardisierung von Mikrofabrikationstechniken mit dem Ziel, den Übergang von der Prototypenentwicklung zur Serienproduktion zu beschleunigen.
Mit Blick auf die kommenden Jahre ist die Aussicht optimistisch. Die fortwährende Konvergenz von digitaler Fertigung, fortschrittlichen Materialien und Prozessautomatisierung wird voraussichtlich die aktuellen Herausforderungen weiter mildern. Wenn sich diese Technologien weiterentwickeln, erwarten Branchenführer Einsparungen bei Kosten und Zykluszeiten, was den Weg für eine breitere Akzeptanz von mikrofabrizierten Aerojet-Motorenteilen in den gängigen Anwendungen der Luftfahrt ebnen wird.
Anwendungen in den Bereichen Kommerzielle, Verteidigung und Raumfahrt
Die Mikrofabrikation von Aerojet-Motoren erlebt in der kommerziellen Luftfahrt, der Verteidigung und der Raumfahrtbranche rasante Fortschritte, die durch die Nachfrage nach höherer Effizienz, reduziertem Komponenten Gewicht und größerer Designkomplexität angetrieben wird. Ab 2025 nutzen Branchenführer Mikrofabrikationstechniken wie additive Fertigung, laserbasierte Mikroverarbeitung und fortschrittliches Ätzen, um komplexe Motorenteile mit bisher unerreichter Präzision und Zuverlässigkeit herzustellen. Diese Methoden ermöglichen die Herstellung von mikroskaligen Merkmalen, einschließlich Kühlkanälen, Kraftstoffeinspritzern und Turbinenschaufeln, die entscheidend zur Verbesserung des thermischen Managements und der Verbrennungseffizienz in modernen Aerojet-Motoren beitragen.
Im kommerziellen Luftfahrtsektor setzen Hersteller Mikrofabrikation ein, um die Entwicklung von Triebwerken der nächsten Generation zu unterstützen, die auf eine Verringerung des Kraftstoffverbrauchs und der Emissionen abzielen. Beispielsweise integrieren Unternehmen wie GE Aerospace und Rolls-Royce Holdings aktiv mikroauseinandergestellte Komponenten in ihre neuen Triebwerksplattformen. Diese Bemühungen sind mit den branchenweiten Zielen verbunden, strengere Umweltvorschriften einzuhalten und die Gesamtleistung der Flotte zu verbessern. Mikrofabrizierte Teile, wie Kraftstoffdüsen und Mikrokanalwärmetauscher, werden bereits auf Haltbarkeit und Leistung validiert, wobei erste Produktionsläufe voraussichtlich in der zweiten Hälfte des Jahrzehnts zunehmen werden.
Im Verteidigungssektor verbessert Mikrofabrikation die Agilität und Überlebensfähigkeit von Militärflugzeugen und Raketensystemen. Programme, die von Organisationen wie Northrop Grumman und RTX Corporation geleitet werden, nutzen miniaturisierte Antriebssysteme und Mikrothruster für präzisionsgeführte Munition und unbemannte Luftfahrzeuge (UAVs). Diese Komponenten profitieren von der Fähigkeit der Mikrofabrikation, leichte, kompakte Designs zu liefern, ohne Leistung oder Zuverlässigkeit zu beeinträchtigen. Das US-Verteidigungsministerium wird voraussichtlich Verträge für mikrofabrizierte Antriebslösungen ausweiten, mit dem Ziel, Ende der 2020er Jahre auf dem Feld eingesetzt zu werden.
Der Raumfahrtsektor nutzt ebenfalls Mikrofabrikation, um das Design von Satelliten-Antriebssystemen und Raumfahrzeugen für die tiefen Weltraumforschung voranzutreiben. Unternehmen wie Aerojet Rocketdyne entwickeln Mikroantriebseinheiten, die präzise Manövrieren von kleinen Satelliten und CubeSats ermöglichen. Diese Systeme, die auf mikrofabrizierten Thruster- und fluidischen Kontrolldevices basieren, sind für kommerzielle Starts und Konstellations-Deployments ab 2025 und in den folgenden Jahren vorgesehen.
Mit Blick auf die Zukunft wird erwartet, dass die Integration von mikrofabrizierten Aerojet-Motorenteilen beschleunigt wird, da Fortschritte in der Materialwissenschaft und digitale Fertigungsplattformen reifen. Branchenkooperationen und öffentlich-private Partnerschaften werden voraussichtlich eine entscheidende Rolle bei der Skalierung dieser Technologien für die Anwendung in großem Maßstab spielen und sicherstellen, dass die Akteure in den Bereichen Kommerzielle, Verteidigung und Raumfahrt einen Wettbewerbsvorteil in Bezug auf Leistung und Nachhaltigkeit in der Antriebstechnik behalten.
Regulatorische Rahmenbedingungen und Branchenstandards
Die regulatorische Landschaft für die Mikrofabrikation von Aerojet-Motoren entwickelt sich schnell, da die Luftfahrtindustrie zunehmend fortschrittliche Fertigungstechniken wie mikroelektromechanische Systeme (MEMS), additive Fertigung und präzise Mikromachining einführt. Im Jahr 2025 wird die Aufsicht durch eine Kombination aus etablierten Luftfahrtstandards und neuen Rahmenbedingungen geleitet, die darauf abzielen, die einzigartigen Herausforderungen und Risiken der mikro-skalierten Fertigungsprozesse zu adressieren.
Wichtige Regulierungsbehörden wie die Federal Aviation Administration (FAA) und die Europäische Agentur für Flugsicherheit (EASA) setzen weiterhin Basis-Sicherheits- und Qualitätsstandards für Flugzeugmotoren, die nun auch Komponenten umfassen, die durch Mikrofabrikation hergestellt wurden. Beide Organisationen verlangen von den Herstellern, die Zuverlässigkeit und Wiederholbarkeit von mikrofabrizierten Teilen durch umfassende Tests, Dokumentationen und Rückverfolgbarkeitsprotokolle zu demonstrieren. Da die Mikrofabrikation die Produktion komplexer Kühlkanäle, Kraftstoffeinspritzer und Sensorarrays mit bisher unerreichter Präzision ermöglicht, aktualisieren diese Behörden die Zertifizierungsrichtlinien, um potenzielle neue Ausfallmodi und Inspektionsherausforderungen zu berücksichtigen, die einzigartig für mikro-skalierten Strukturen sind.
Die SAE International spielt eine zentrale Rolle bei der Standardisierung von Mikrofabrikationsprozessen. Jüngste Aktualisierungen von Standards wie AS9100 und AS9110 enthalten jetzt spezifische Bestimmungen für additive und Mikrofabrikation-Prozesskontrollen, Materialnachverfolgbarkeit und Inspektionsanforderungen. Im Jahr 2025 laufen Bemühungen, diese Standards global zu harmonisieren, um internationale Lieferketten und Zertifizierungskosten zu erleichtern. Branchenverbände arbeiten auch mit Regulierungsbehörden zusammen, um neue Testmethoden für mikrofabrizierte Motorenteile zu etablieren, die sich auf Ermüdung, thermische Zyklen und Fehlererkennung im Mikromaßstab konzentrieren.
Führende Hersteller von Aerojet-Motoren, darunter GE Aerospace und Rolls-Royce, engagieren sich aktiv bei Regulierungsbehörden und Normungsstellen, um Anforderungen zu gestalten, die Innovationen unterstützen und gleichzeitig die Sicherheit gewährleisten. Diese Unternehmen haben in digitale Qualitätsmanagementsysteme und firmeninterne Zertifizierungsexpertise investiert und erwarten, dass die regulatorischen Anforderungen intensiver werden, da mikrofabrizierte Komponenten immer kritischer für Missionen werden. Bemerkenswert ist, dass diese Hersteller, während sie die Grenzen des Designs mit mikro-strukturierten Merkmalen erweitern, die Schaffung neuer Verfahren zur zerstörungsfreien Prüfung (NDE) und Qualifizierungsverfahren unterstützen, die auf die einzigartigen Geometrien und Materialeigenschaften von mikrofabrizierten Teilen zugeschnitten sind.
Blickt man in die Zukunft, wird in den nächsten Jahren erwartet, dass detailliertere Prozesszertifizierungspfade, eine verstärkte Betonung von digitalen Zwillingen und Prozesssimulationen zur Einhaltung von Vorschriften sowie die Einführung von Echtzeitüberwachungs- und Rückverfolgbarkeitstools umgesetzt werden. Die dynamische regulatorische Landschaft erfordert eine ständige Zusammenarbeit zwischen OEMs, Zulieferern und Normierungsorganisationen, um eine sichere, wiederholbare und wirtschaftlich tragfähige Einführung von Mikrofabrikationstechnologien für Aerojet-Motoren zu gewährleisten.
Investitionstrends und Finanzierungsinformationen
Die Mikrofabrikation von Aerojet-Motoren – einschließlich fortschrittlicher Fertigungsansätze wie additive Fertigung, laserbasierte Mikromachining und präzises Ätzen – hat einen bemerkenswerten Anstieg der Investitionstätigkeit erlebt, da der Luftfahrtsektor nach leichteren, effizienteren Antriebssystemen strebt. Im Jahr 2025 wird das Feld durch eine Kombination aus staatlich geförderten Initiativen, strategischen Unternehmensfinanzierungen und Risikokapital, das sowohl etablierte Luftfahrt-Riesen als auch agile Start-ups anvisiert, geprägt.
Ein wesentlicher Treiber der aktuellen Investitionen ist die steigende Nachfrage nach leistungsstarken, kompakten Antriebseinheiten sowohl im kommerziellen als auch im Verteidigungsbereich. Große Triebwerkshersteller erweitern ihre Mikrofabrikationskapazitäten, um die Teileanzahl zu reduzieren, die Kraftstoffeffizienz zu verbessern und komplexe Kühlgeometrien zu ermöglichen, die mit traditionellen Methoden zuvor nicht erreichbar waren. GE Aerospace und RTX sind unter den aktivsten, die F&E-Budgets aufwenden, um Mikrofabrikationslinien auszubauen und mit spezialisierten Zulieferern zu kooperieren. Parallel dazu unterstützt staatliche Finanzierung – insbesondere durch Agenturen wie das US-Verteidigungsministerium und die Europäische Weltraumorganisation – weiterhin Fortschritte in der miniaturisierten Antriebstechnik für Satelliten und hyperschallschnelle Fahrzeuge.
Der Trend zu öffentlich-privaten Partnerschaften beschleunigt sich. Im Jahr 2025 sind Co-Investitionsmodelle üblich geworden, wobei Einrichtungen wie NASA Demonstrationsprojekte unterstützen, die neuartige Mikrofabrikationstechniken für Aerojet-Komponenten entschärfen. Diese Kooperationen fördern nicht nur technische Durchbrüche, sondern wirken auch als Katalysatoren für private Nachfolgefonds. Neu auftretende Akteure, einschließlich Universitätsgründungen und Mikrofabrikationsspezialisten, profitieren von Seed- und Series-A-Runden, die von luftfahrtfokussierten Risikokapitalfonds und Unternehmensrisikokapital von großen Akteuren zur Verfügung gestellt werden.
Daten aus laufenden Finanzierungsrunden zeigen, dass Kapital in Bereiche wie hochtemperaturkeramische, Mikrokanalwärmetauscher und integrierte Schubvektor-Düsen fließt – Schlüsselkomponenten, die durch fortschrittliche Mikrofabrikation ermöglicht werden. Zulieferer, die sich auf Laser- und Elektronenstrahl-Additionsverfahren spezialisiert haben, berichten von Auftragsrückständen und Expansionsplänen, die durch mehrjährige Beschaffungsvereinbarungen von OEMs und Tier-1-Zulieferern angeregt werden. Zum Beispiel haben Safran und Rolls-Royce beide angekündigt, die Investitionen in interne und partnergeführte Mikrofabrikationsfähigkeiten zur Unterstützung von Triebwerken der nächsten Generation zu erhöhen.
Mit Blick auf die nächsten Jahre bleibt der Investitionsausblick robust. Die Konvergenz von digitalem Design, Automatisierung und Echtzeit-Prozessüberwachung wird voraussichtlich die Entwicklungszyklen und Herstellkosten weiter senken. Sobald Regulierungsbehörden begonnen haben, mikrofabrizierte Aerojet-Motorenteile für breitere Fluganwendungen zu zertifizieren, wird der Sektor voraussichtlich nachhaltig und diversifiziert investiert werden – und die Mikrofabrikation als zentrale Säule der Antriebstechnologie-innovation durch die späten 2020er Jahre positionieren.
Zukunftsausblick: Disruptive Innovationen und Wettbewerbskräfte
Die Landschaft der Mikrofabrikation von Aerojet-Motoren im Jahr 2025 steht vor einer erheblichen Transformation, die durch disruptive Innovationen in der additiven Fertigung, fortschrittlichen Materialien und digitalen Twin-Technologien vorangetrieben wird. Ein wichtiger Trend ist die Integration von Mikrofabrikationstechniken – wie laserstrahlgeführtes Pulverbettschmelzen und mikro-elektrische Entladungsspannungsmachining (micro-EDM) – in die Serienproduktion von Motorenteilen mit komplexen Geometrien und verbesserten Leistungseigenschaften. Führende Motorenhersteller und Zulieferer intensivieren die Investitionen in diese Mikrofabrikationsfähigkeiten, um leichtere, kraftstoffeffizientere Motoren mit reduzierten Emissionen zu erreichen.
Unternehmen wie GE Aerospace und Rolls-Royce plc stehen an der Spitze der Entwicklung von mikrofabrizierten Triebwerkskomponenten, darunter Mikrodüsen, Kraftstoffeinspritzer und Kühlkanäle. Im Jahr 2025 betonen laufende Projekte in diesen Organisationen die präzise Herstellung im submillimetergenauem Maßstab und nutzen In-Situ-Überwachung und KI-gesteuerte Prozesskontrollen, um Qualität und Wiederholbarkeit sicherzustellen. Die Übernahme additiv hergestellter Mikrokomponenten wird voraussichtlich in den Bereichen der kommerziellen und militärischen Luftfahrt weiterhin zunehmen, wobei Einsparungen von bis zu 30 % bei der Teileanzahl und erhebliche Verbesserungen der thermodynamischen Effizienz des Motors erzielt werden.
Durchbrüche in der Materialwissenschaft prägen ebenfalls den Zukunftsausblick. Die Einführung hochtemperaturbeständiger keramischer Matrixverbundstoffe und neuartiger Superlegierungen, die durch Mikrofabrikation ermöglicht werden, erlauben dünnere Wände und komplexere interne Kühlkanäle – entscheidend, um höheren Betriebstemperaturen standzuhalten. Safran und Pratt & Whitney fördern aktiv Forschungskooperationen, um die Produktion solcher Komponenten zu skalieren und bis 2027 Motoren mit verbesserter Haltbarkeit und geringeren Lebenszykluskosten zu liefern.
Die wettbewerbspolitischen Dynamiken verschärfen sich, da OEMs und wichtige Zulieferer darum kämpfen, geistiges Eigentum und Qualifikationen für neue mikrofabrizierte Teile zu sichern. Die Zusammenarbeit zwischen Motorenherstellern und spezialisierten Fertigungsunternehmen, wie Siemens, die ihre Fachkenntnisse in digitaler Fertigung und Prozessautomatisierung nutzen, um die schnelle Prototyp-erstellung und Zertifizierung kritischer Motorstrukturen zu unterstützen, nimmt zu. Gleichzeitig wird erwartet, dass das Aufkommen von Start-ups und Universitätsausgründungen, die sich auf neuartige Mikrofabrikationsprozesse konzentrieren, die Lieferketten weiter stören und die Innovationszyklen vorantreiben werden.
Mit Blick in die Zukunft sind die kommenden Jahre durch beschleunigte Zertifizierungspfade für mikrofabrizierte Aerojet-Motorenteile gekennzeichnet, die durch die Validierung von digitalen Zwillingen und Systeme zur Echtzeitinspektion angestoßen werden. Branchenakteure erwarten, dass bis 2030 die Mikrofabrikation der Mehrheit der Architekturen von Aerojet-Motoren der nächsten Generation zugrunde liegt, was die Designmöglichkeiten grundlegend verändert und eine neue Ära nachhaltigen, leistungsstarken Flugs einleitet.
Quellen & Referenzen
- GE Aerospace
- Honeywell
- GE Aerospace
- MTU Aero Engines
- Oxford Instruments
- Precision Micro
- NASA
- Siemens
- Airbus
- Northrop Grumman
- RTX Corporation
- GE Aerospace