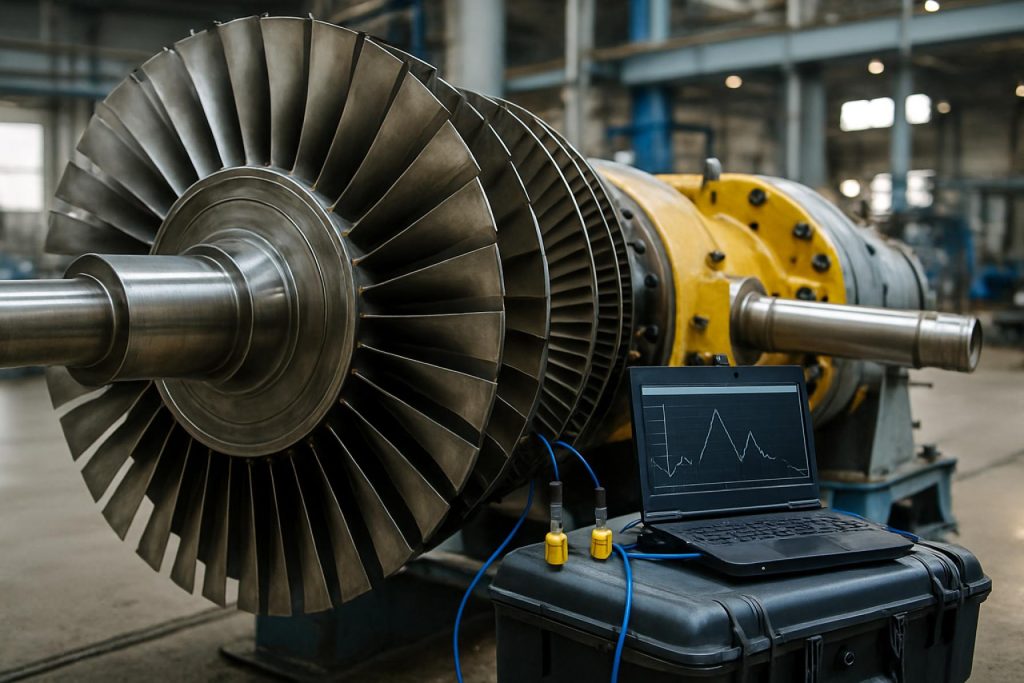
Déverrouiller la prochaine ère des diagnostics de turbomachinerie à flux axial : Ce que 2025 nous réserve, qui est en tête, et où seront réalisés les investissements les plus intelligents. Découvrez les données et les technologies émergentes qui redéfiniront la performance et la fiabilité.
- Résumé Exécutif : Principaux enseignements et aperçu de 2025
- Taille du Marché & Prévisions jusqu’en 2030 : Croissance, Segments et Moteurs de Valeur
- Paysage Concurrentiel : Acteurs Principaux, Partenariats Récents, et Mouvements Stratégiques
- Technologies de Diagnostic Révolutionnaires : Capteurs, IA et Jumeaux Numériques
- Tendances Réglementaires et Normes Industrielles : Conformité et Atténuation des Risques
- Études de Cas : Déploiements Réussis dans la Production d’Énergie et l’Aérospatiale
- Défis et Obstacles : Intégration des Données, Cybersécurité et Systèmes Hérités
- Opportunités Émergentes : Maintenance Prédictive, Surveillance à Distance et Analyse Cloud
- Analyse Régionale : Nord-Amérique, Europe, Asie-Pacifique, et Points Chauds du Moyen-Orient
- Perspectives Futures : Projections d’Experts, Feuilles de Route de l’Innovation, et Priorités d’Investissement
- Sources & Références
Résumé Exécutif : Principaux enseignements et aperçu de 2025
La turbomachinerie à flux axial—englobant les compresseurs et les turbines dans les secteurs de l’énergie, de l’aérospatiale et de l’industrie—reste centrale pour l’infrastructure mondiale. Les diagnostics de ces machines ont pénétré une phase transformative en 2025, alimentée par des demandes croissantes d’efficacité opérationnelle, de maintenance prédictive et de durabilité. Les principales tendances mettent en évidence la convergence du déploiement de capteurs avancés, de l’analyse de données en temps réel et de l’apprentissage machine, toutes priorisées par les OEM et les opérateurs cherchant à minimiser les temps d’arrêt imprévus et à prolonger la durée de vie des actifs.
Un développement significatif est l’intégration plus large de réseaux de capteurs sans fil de haute fidélité, permettant une surveillance continue et non intrusive des vibrations, de la température et de la pression dans les compresseurs et turbines axiaux. Les principaux OEM tels que Siemens Energy, GE Vernova (anciennement partie de General Electric), et Safran intègrent des capacités de diagnostic dans les nouvelles machines ainsi que dans les solutions de rétrofit. L’accent est mis sur la détection précoce des défauts—en particulier pour les dommages aux pales, l’encrassement, et les événements de suralimentation—en utilisant l’analyse des données directement sur le site pour réduire la latence et les besoins en bande passante.
- Jumeaux Numériques et Diagnostics Prédictifs : La technologie des jumeaux numériques est désormais un élément essentiel des diagnostics de turbomachinerie à flux axial, permettant la simulation en temps réel des états des machines sur la base des entrées de capteurs. Siemens Energy et GE Vernova ont étendu leurs plates-formes de jumeaux numériques pour inclure des modules de diagnostic pilotés par IA qui identifient non seulement les anomalies mais recommandent également des actions de maintenance, optimisant les cycles de révision et réduisant les coûts de cycle de vie.
- Diagnostics à Distance et Intégration Cloud : Les centres de surveillance à distance, tels que ceux opérés par Siemens Energy et GE Vernova, exploitent des plates-formes cloud pour analyser les données de l’ensemble de la flotte, comparant les unités individuelles aux métriques de performance globale. Cette approche améliore l’analyse des causes profondes et soutient la diffusion rapide des mises à jour logicielles et des algorithmes de diagnostic à travers les flottes mondiales.
- Moteurs Réglementaires et de Durabilité : Des normes d’émissions plus strictes et des mandats d’efficacité, en particulier en Europe et en Asie, accélèrent l’investissement dans des diagnostics avancés. Des entreprises comme Rolls-Royce et Safran collaborent avec des utilisateurs finaux pour adapter des solutions de diagnostic soutenant des objectifs de décarbonisation et de fonctionnement durable.
À l’avenir, les perspectives pour 2025 et au-delà présentent une automatisation accrue des diagnostics, un déploiement plus important de l’IA pour les prognostics, et une intégration plus étroite avec les workflows de gestion des actifs. Les OEM et les opérateurs devraient approfondir leurs partenariats avec les fabricants de capteurs et les fournisseurs de logiciels, brouillant davantage les frontières entre matériel et services numériques. Cette convergence est prête à redéfinir la création de valeur dans le secteur de la turbomachinerie à flux axial au cours des prochaines années.
Taille du Marché & Prévisions jusqu’en 2030 : Croissance, Segments et Moteurs de Valeur
Le marché des diagnostics de turbomachinerie à flux axial est prêt pour une croissance significative jusqu’en 2030, alimentée par des investissements soutenus dans les infrastructures énergétiques, la modernisation continue des centrales électriques, et un accent mondial sur l’efficacité et la fiabilité des équipements rotatifs. En 2025, le marché connaît une demande robuste dans les secteurs de la production d’énergie, du pétrole et gaz, et de l’aviation, où les turbines et compresseurs à flux axial sont des actifs critiques. Les moteurs de valeur clés comprennent l’adoption croissante de la maintenance prédictive, l’intégration de technologies de capteurs avancées, et la transition vers des jumeaux numériques pour le suivi des conditions en temps réel.
Les principaux fabricants et fournisseurs de services tels que GE, Siemens Energy, et Sulzer sont à l’avant-garde, offrant des solutions de diagnostic complètes qui combinent matériel (capteurs de vibrations, acoustiques, et de température) avec des plates-formes d’analyse sophistiquées. Ces entreprises élargissent leurs portefeuilles de diagnostics, en utilisant l’intelligence artificielle et l’apprentissage machine pour détecter des anomalies, prédire des pannes, et optimiser les calendriers de maintenance. Le déploiement d’analytique basée sur le cloud et de surveillance à distance s’accélère, facilitant le diagnostic en temps réel même dans des opérations géographiquement dispersées.
La segmentation du marché indique que la production d’énergie reste le plus grand secteur d’utilisation finale, soutenue par la modernisation des centrales thermiques, à gaz, et à cycle combiné, en particulier en Asie-Pacifique et en Amérique du Nord. Le secteur pétrolier et gazier continue d’être un contributeur significatif, les installations en milieu et en aval investissant dans la fiabilité des actifs pour minimiser les temps d’arrêt et se conformer aux réglementations de sécurité strictes. L’aérospatiale est un autre segment en forte croissance, avec les fabricants de moteurs d’avions et les opérateurs adoptant des diagnostics avancés pour améliorer la disponibilité de la flotte et réduire les coûts de maintenance.
Les initiatives sectorielles poussent vers la normalisation et l’interopérabilité des systèmes de diagnostic, les organisations comme l’American Petroleum Institute et l’International Energy Agency promouvant les meilleures pratiques pour la surveillance des actifs et le partage des données. La tendance vers la numérisation, y compris l’utilisation de l’informatique de bord et l’intégration avec les systèmes de gestion d’actifs d’entreprise (EAM), devrait encore stimuler les taux d’adoption.
En regardant vers 2030, le marché des diagnostics de turbomachinerie à flux axial est en voie d’expansion soutenue, soutenue par des efforts continus de décarbonisation, l’essor des turbines prêtes pour l’hydrogène, et la prolifération des actifs d’énergie renouvelable nécessitant une alimentation de secours fiable. À mesure que la base installée de turbomachinerie vieillissante croît et que la transformation numérique s’accélère, la demande pour des diagnostics avancés devrait rester forte, avec de grands OEM et fournisseurs de technologie investissant massivement dans la R&D pour rester en tête dans ce paysage dynamique.
Paysage Concurrentiel : Acteurs Principaux, Partenariats Récents, et Mouvements Stratégiques
Le paysage concurrentiel des diagnostics de turbomachinerie à flux axial est caractérisé par la présence d’OEM établis, de fournisseurs de diagnostics spécialisés, et de nouveaux entrants tirant parti de la numérisation. Les principaux fabricants tels que Siemens Energy, General Electric (GE), et Mitsubishi Heavy Industries (MHI) maintiennent une position dominante, intégrant des diagnostics avancés dans leurs portefeuilles de turbomachinerie. Ces entreprises investissent massivement dans la surveillance des conditions, l’analyse en temps réel, et la maintenance prédictive pour améliorer la fiabilité opérationnelle et réduire les temps d’arrêt imprévus.
Ces dernières années ont vu une montée en puissance des partenariats stratégiques et des coentreprises pour accélérer la transformation numérique. Par exemple, en 2024, Baker Hughes a élargi ses collaborations avec des spécialistes du cloud et de l’IA pour offrir des capacités de diagnostic et de gestion des performances des actifs améliorées pour les compresseurs et turbines axiaux. ABB et Schneider Electric ont également approfondi leurs relations avec les utilisateurs finaux dans les secteurs du pétrole & gaz et de l’énergie, fournissant des paquets de capteurs et d’analytique intégrés pour les nouvelles installations et les projets de rétrofit.
Des fournisseurs tels que Emerson et Honeywell se sont concentrés sur l’informatique de bord et les plates-formes IIoT (Internet Industriel des Objets) pour fournir des informations sur la santé des turbomachines en temps réel. Leurs offres incluent désormais des capteurs de vibrations sans fil, une acquisition de données haute fréquence, et des diagnostics basés sur le cloud conçus pour les compresseurs et turbines à flux axial. En 2025, ils devraient déployer des mises à jour qui automatisent encore davantage l’analyse des causes profondes et optimisent les intervalles de maintenance.
De plus petites entreprises spécialisées font également leur chemin en se concentrant sur des solutions de diagnostic de niche. Des entreprises telles que Wood (via sa division d’optimisation des performances des actifs) et Sulzer (connue pour ses services après-vente en turbomachinerie) ont élargi leurs portefeuilles de services de surveillance, proposant des diagnostics à distance, une analyse avancée des vibrations, et une gestion du cycle de vie adaptées aux machines à flux axial.
À l’avenir, la dynamique concurrentielle devrait s’intensifier à mesure que la surveillance à distance, les diagnostics basés sur l’IA, et les jumeaux numériques deviennent des normes industrielles. Les leaders du marché devraient augmenter leurs investissements en R&D et en alliances stratégiques, en particulier avec des développeurs de logiciels et des entreprises d’automatisation. Les prochaines années devraient voir une convergence encore plus poussée de l’expertise matérielle et logicielle, les solutions de diagnostic étant de plus en plus intégrées dans les offres des OEM et disponibles sous forme de services par abonnement.
Technologies de Diagnostic Révolutionnaires : Capteurs, IA et Jumeaux Numériques
Le domaine des diagnostics de turbomachinerie à flux axial connaît une transformation significative en 2025, alimentée par le déploiement rapide de technologies de capteurs avancés, d’intelligence artificielle (IA), et de plates-formes de jumeaux numériques. Ces technologies permettent des niveaux de surveillance en temps réel, de maintenance prédictive et d’optimisation des performances sans précédent dans des équipements critiques tels que les turbines à gaz, les compresseurs, et les moteurs à réaction.
L’innovation en matière de capteurs reste un pilier de cette évolution. Les principaux OEM et fournisseurs de composants avancent dans l’intégration des systèmes de capteurs à fibre optique et sans fil, permettant une mesure continue et de haute fidélité de paramètres tels que les vibrations, la pression, la température, et le décalage de la pointe des pales. Par exemple, General Electric utilise des capteurs intégrés avancés dans ses turbines à gaz de classe HA, facilitant la capture continue de données pour l’évaluation de la santé et la détection précoce des anomalies. De même, Siemens Energy et Rolls-Royce Holdings plc ont élargi leurs gammes de capteurs pour inclure des dispositifs distribués et miniaturisés, permettant des diagnostics plus granulaires dans les turbomachineries industrielles et aérospatiales.
L’IA et l’apprentissage machine sont désormais centraux dans les stratégies de diagnostic. Les algorithmes analysent les volumes massifs de données des capteurs pour reconnaître des schémas subtils indiquatifs de défauts naissants, tels que la fatigue des pales, l’usure des roulements, ou des instabilités aérodynamiques. Baker Hughes et Safran déploient activement des plates-formes de surveillance de condition pilotées par IA, qui soutiennent les opérateurs avec des alertes d’avertissement anticipées et des recommandations de maintenance exploitables. Ces systèmes réduisent non seulement les temps d’arrêt imprévus, mais permettent également un passage d’une maintenance programmée à une maintenance réellement prédictive, réduisant les coûts de cycle de vie et améliorant la fiabilité.
La technologie des jumeaux numériques—répliques virtuelles des actifs physiques de turbomachinerie—atteint de nouveaux niveaux de maturité en 2025. Des entreprises telles que Siemens AG et Ansys, Inc. fournissent des jumeaux numériques de haute fidélité qui ingèrent des données opérationnelles en temps réel, simulent le comportement des composants dans diverses conditions, et prédisent l’évolution des défauts ou la dégradation des performances. Cette capacité permet des diagnostics et une optimisation basés sur des scénarios, y compris l’évaluation des impacts des changements opérationnels ou des fluctuations environnementales, soutenant ainsi des décisions de gestion des actifs plus intelligentes.
En regardant vers les années à venir, la convergence de ces technologies devrait s’accélérer. Les principaux acteurs de l’industrie investissent dans des écosystèmes de diagnostic intégrés, combinant réseaux de capteurs, analyses basées sur l’IA, et jumeaux numériques en plates-formes unifiées. À mesure que les normes d’interopérabilité s’améliorent et que la puissance de calcul augmente, les diagnostics deviendront encore plus automatisés, adaptatifs et accessibles à travers la flotte mondiale de turbomachinerie. Cette transformation numérique est prête à apporter des avantages tangibles en matière d’efficacité, de sécurité, et de durabilité pour des secteurs allant de l’énergie et de l’aviation aux industries de processus.
Tendances Réglementaires et Normes Industrielles : Conformité et Atténuation des Risques
En 2025, les tendances réglementaires et les normes industriels pour les diagnostics de turbomachinerie à flux axial sont façonnées par des exigences de sécurité, environnementales et de fiabilité de plus en plus strictes. Les secteurs mondiaux de l’aviation, de la production d’énergie, et du pétrole & gaz sont sous pression accrue pour s’assurer que les turbomachineries—telles que les compresseurs et turbines axiaux—fonctionnent avec une efficacité optimale et un risque minimal de défaillance. Cela pousse à la fois les régulateurs et les organismes industriels à développer et à faire respecter des exigences complètes en matière de diagnostic et de surveillance.
Un moteur critique est l’évolution des normes d’organisations telles que l’Organisation internationale de normalisation (ISO) et de la Société américaine des ingénieurs mécaniques (ASME), qui continuent de mettre à jour les directives pour la surveillance des conditions, l’évaluation des performances, et la détection des défauts dans les turbomachineries. Par exemple, des normes comme l’ISO 13379 et l’ASME PTC 10 sont de plus en plus souvent référencées pour établir des protocoles de diagnostic et des critères d’acceptation. Ces normes influencent les spécifications d’approvisionnement et de maintenance à travers les industries, alors que les opérateurs cherchent à démontrer leur conformité et à réduire les risques opérationnels.
Parallèlement, les agences réglementaires sur les principaux marchés—including la Federal Aviation Administration (FAA) des États-Unis pour l’aérospatiale et l’Environmental Protection Agency (EPA) des États-Unis pour les émissions—incrémentent leurs attentes en matière de surveillance en temps réel et de pratiques de maintenance basées sur les données. Par exemple, la volonté continue de la FAA de se concentrer sur les diagnostics prédictifs mène à une plus grande adoption des systèmes de surveillance de santé continue dans les moteurs d’avion, y compris ceux produits par des fabricants tels que GE Aerospace et Rolls-Royce. Les deux entreprises ont investi dans des analyses numériques avancées et des diagnostics activés par IoT qui soutiennent la conformité avec les directives de navigabilité en évolution et les objectifs d’émissions.
Dans les industries de l’énergie et de la transformation, des OEM tels que Siemens Energy et Solar Turbines mettent en œuvre des solutions de diagnostic qui s’intègrent parfaitement aux cadres de conformité réglementaire. Ces systèmes capturent des données de vibrations, de température et de pression pour satisfaire aux exigences de reporting opérationnel et environnemental, ainsi qu’aux seuils d’alerte précoce imposés par les assureurs et les organismes réglementaires.
À l’avenir, les perspectives du secteur pour 2025 et les années à venir se caractérisent par un passage d’inspections périodiques à des diagnostics continus et automatisés. Cette évolution est renforcée par l’adoption de l’Internet industriel des objets (IIoT) et d’analyses avancées, qui devraient devenir des piliers centraux des normes réglementaires à venir. Des consortiums industriels et des organismes de normalisation collaborent sur de nouveaux cadres qui exigeront probablement des diagnostics en temps réel, des rapports basés sur le cloud, et des journaux de conformité traçables—intégrant encore davantage l’atténuation des risques dans le cœur des opérations de turbomachinerie.
Études de Cas : Déploiements Réussis dans la Production d’Énergie et l’Aérospatiale
Le déploiement de diagnostics avancés dans la turbomachinerie à flux axial est devenu de plus en plus critique dans les secteurs de la production d’énergie et de l’aérospatiale, surtout alors que les opérateurs cherchent à améliorer la fiabilité, l’efficacité, et la maintenance prédictive. En 2025, plusieurs études de cas médiatisées soulignent l’impact transformateur des systèmes de diagnostic modernes.
Dans l’industrie de la production d’énergie, Siemens Energy a été à l’avant-garde de l’intégration de plates-formes de diagnostic dans ses flottes de turbines à gaz et à vapeur. Tirant parti de ses « Omnivise Digital Services », Siemens Energy a permis la surveillance en temps réel et la détection avancée des défauts sur des centaines de turbines à flux axial installées à travers le monde. Un déploiement récent dans une centrale à cycle combiné en Europe a démontré comment l’analyse des vibrations et des images thermiques a détecté une fatigue naissante des pales, permettant aux équipes de maintenance d’intervenir avant une défaillance coûteuse—augmentant finalement la disponibilité des unités et réduisant les pannes imprévues.
De même, GE Vernova (la division énergie rebranded de GE) a mis en œuvre sa suite « Predix Asset Performance Management » dans plusieurs centrales électriques à travers l’Amérique du Nord et l’Asie. Dans un cas de 2024, une unité de turbine à gaz de 700 MW a présenté des anomalies de performance subtiles. Utilisant des données de capteurs haute fréquence et la reconnaissance de motifs pilotée par l’IA, le système de GE Vernova a localisé un encrassement précoce dans la section du compresseur. L’alerte prédictive a permis de programmer un nettoyage optimisé, améliorant l’efficacité de 1,2 % et générant d’importantes économies de carburant sur l’année.
Dans l’aérospatial, Rolls-Royce continue d’établir des références avec son système de « Surveillance de la Santé du Moteur »—maintenant standard sur tous les nouveaux moteurs de la série Trent. En 2025, un partenaire aérien de premier plan a signalé une détection réussie en vol d’un évènement d’instabilité mineure du compresseur. La télémétrie en temps réel du système, alimentée par des analyses cloud, a entraîné un arrêt contrôlé du moteur et une déviation sécurisée, évitant une éventuelle urgence en vol. L’analyse post-incident a conduit à une identification rapide de la cause profonde, rationalisant l’action corrective et minimisant le temps d’arrêt de l’avion.
De plus, Pratt & Whitney a élargi sa suite de diagnostics « EngineWise » à travers ses flottes militaires et commerciales. Notamment, en 2025, un important opérateur de l’armée de l’air a crédité le système d’une réduction de 20 % des retours moteur non programmés, attribuant cela directement à une meilleure détection de l’usure du compresseur axial et des dommages causés par des objets étrangers.
Les perspectives demeurent robustes : avec des avancées continues en matière de fidélité des capteurs, d’apprentissage machine, et de connectivité cloud, on s’attend à une prolifération des études de cas dans le monde réel. Les leaders de l’industrie sont prêts à réduire davantage les coûts de cycle de vie et à améliorer les marges de sécurité, consolidant ainsi les diagnostics comme une pierre angulaire de l’exploitation des turbomachineries dans les années à venir.
Défis et Obstacles : Intégration des Données, Cybersécurité et Systèmes Hérités
Les diagnostics de turbomachinerie à flux axial connaissent des avancées rapides, mais l’industrie continue de faire face à des défis significatifs liés à l’intégration des données, à la cybersécurité, et à la gestion des systèmes hérités—des défis qui devraient rester présents jusqu’en 2025 et dans les prochaines années. Alors que la numérisation et la surveillance à distance deviennent omniprésentes, les opérateurs et les OEM doivent naviguer dans des barrières techniques et organisationnelles complexes.
Intégration des Données : L’intégration des données de diagnostic provenant de sources diverses—including capteurs de vibrations, moniteurs de performance, et systèmes de contrôle—reste un défi central. La plupart des flottes de turbomachinerie contiennent des équipements de plusieurs générations et fabricants, souvent avec des formats de données propriétaires. Atteindre une interopérabilité transparente pour des diagnostics en temps réel nécessite des middleware robustes et des protocoles de communication standardisés. Les principaux OEM tels que Siemens Energy et GE Vernova investissent dans des plates-formes numériques qui agrègent des données provenant à la fois d’actifs hérités et modernes. Cependant, les progrès de l’industrie sont entravés par des architectures de données fragmentées et une adoption limitée des normes ouvertes. À partir de 2025, les efforts de collaboration—tels que le développement des cadres de Gestion de la Performance des Actifs (APM)—sont en cours mais pas encore mis en œuvre universellement.
Cybersécurité : Avec la prolifération des diagnostics basés sur le cloud et la connectivité à distance, la turbomachinerie à flux axial est de plus en plus exposée aux cybermenaces. Le secteur est sous pression pour se conformer à des cadres réglementaires plus stricts, y compris le Cadre de Cybersécurité NIST et les mandats d’infrastructure critique régionaux. Les OEM et les opérateurs priorisent la transmission sécurisée des données, l’authentification multi-facteur, et la détection d’intrusions. Des entreprises comme Baker Hughes et ABB intègrent la cybersécurité dans leurs offres de surveillance et de diagnostic, collaborant souvent avec des spécialistes de la cybersécurité pour des solutions de bout en bout. Néanmoins, l’expansion rapide des dispositifs de l’Internet industriel des objets (IIoT) continue d’élargir la surface d’attaque, et la mise à jour des sécurités pour les systèmes hérités reste une préoccupation persistante.
Systèmes Hérités : Une portion significative de la flotte mondiale de turbomachinerie à flux axial est constituée d’unités datant d’avant l’ère numérique. La mise à niveau de ces actifs pour des diagnostics modernes présente à la fois des barrières techniques et économiques. Le rétrofit de capteurs et de passerelles est souvent contraint par des limitations de design physique, un manque de documentation détaillée, ou un risque de perturbation opérationnelle. Bien que des entreprises telles que Siemens Energy et GE Vernova proposent des packages de rétrofit et des jumeaux numériques pour prolonger la durée de vie des actifs, de nombreux opérateurs peinent à justifier l’investissement sans un retour sur investissement clair. Au cours des prochaines années, le secteur devrait connaître des progrès incrementaux alors que de nouvelles technologies de capteurs modulaires et des solutions d’informatique à la périphérie réduisent les coûts et la complexité de déploiement.
À l’avenir, la capacité de l’industrie à surmonter ces obstacles façonnera le rythme de la transformation numérique dans les diagnostics de turbomachinerie à flux axial. Une plus grande adoption des normes ouvertes, de meilleures postures de cybersécurité, et des solutions d’intégration évolutives devraient être des domaines de focus clés jusqu’en 2025 et au-delà.
Opportunités Émergentes : Maintenance Prédictive, Surveillance à Distance et Analyse Cloud
Les diagnostics de turbomachinerie à flux axial entrent dans une phase transformative, alimentée par des avancées dans la maintenance prédictive, la surveillance à distance, et les analyses basées sur le cloud. En 2025, les OEM et les opérateurs investissent de plus en plus dans des outils numériques pour améliorer la fiabilité, minimiser les pannes non planifiées, et optimiser les coûts de cycle de vie des actifs tels que les turbines à gaz et à vapeur, les compresseurs axiaux, et les équipements aérodérivés.
La maintenance prédictive évolue rapidement grâce à l’intégration d’algorithmes d’IA et d’apprentissage machine, qui analysent les données des capteurs en temps réel pour prévoir les pannes avant qu’elles ne se produisent. Les principaux OEM tels que Siemens Energy et GE ont élargi leurs portefeuilles de services numériques, offrant des plates-formes de diagnostic avancées qui agrègent les données de vibrations, de température, et de pression pour identifier les défauts à un stade précoce dans les composants à flux axial. Ces solutions prolongent non seulement les intervalles entre les révisions mais soutiennent également des calendriers de maintenance basés sur les conditions, réduisant les interventions inutiles et les coûts associés.
La surveillance à distance est désormais une fonctionnalité standard pour les nouvelles installations et les rétrofits. Des entreprises comme Ansaldo Energia et Mitsubishi Power fournissent une connectivité sécurisée et en temps réel entre l’équipement de terrain et les centres de surveillance centralisés. Cela permet aux équipes d’experts de superviser des flottes à l’échelle mondiale, de fournir des informations de diagnostic rapides, et de guider les techniciens sur site à travers les procédures de dépannage. L’accès à distance améliore le temps de fonctionnement et la sécurité, en particulier pour les unités déployées dans des lieux éloignés ou dangereux.
Les plates-formes d’analyse cloud deviennent essentielles pour gérer les vastes quantités de données opérationnelles générées par les turbomachineries modernes. Les OEM et les fournisseurs de services indépendants tirent parti de l’infrastructure cloud pour traiter, stocker, et visualiser les données de milliers de capteurs en temps réel. GE et Siemens Energy sont des acteurs importants dans ce domaine, offrant des solutions qui s’intègrent avec les systèmes de gestion d’actifs d’entreprise et soutiennent des diagnostics avancés, la détection d’anomalies, et le benchmarking de performances à travers de grandes flottes.
À l’avenir, les perspectives pour les diagnostics de turbomachinerie à flux axial seront marquées par l’adoption croissante de l’informatique de périphérie, des jumeaux numériques, et des améliorations en cybersécurité. Les dispositifs de bord devraient permettre des diagnostics plus rapides et localisés, tandis que les jumeaux numériques—répliques virtuelles d’actifs physiques—fournissent une fondation pour simuler les performances et prédire la dégradation dans divers scénarios opérationnels. Les collaborations à l’échelle de l’industrie, y compris celles impliquant des organisations telles que Siemens Energy, GE, et Mitsubishi Power, devraient accélérer le développement des normes et des meilleures pratiques pour les écosystèmes de diagnostics interopérables et sécurisés.
D’ici 2025 et au-delà, ces technologies émergentes sont prêtes à offrir des gains d’efficacité importants, des économies de coûts, et des améliorations de fiabilité pour les opérateurs de turbomachinerie à flux axial à travers les secteurs de l’énergie, de l’aviation, et des processus industriels.
Analyse Régionale : Nord-Amérique, Europe, Asie-Pacifique, et Points Chauds du Moyen-Orient
Le paysage mondial des diagnostics de turbomachinerie à flux axial est façonné par les priorités distinctes et les profils industriels de l’Amérique du Nord, de l’Europe, de l’Asie-Pacifique, et du Moyen-Orient. En 2025 et en regardant vers les prochaines années, ces régions déploient des diagnostics avancés pour améliorer l’efficacité, la fiabilité et la durabilité dans des secteurs tels que la production d’énergie, l’aérospatiale, le pétrole et le gaz, et le traitement industriel.
Nord-Amérique reste un leader dans l’adoption de diagnostics haut de gamme, avec de grands OEM et fournisseurs de services intégrant des jumeaux numériques, une maintenance prédictive pilotée par IA, et une surveillance des conditions en temps réel dans leurs compresseurs et turbines à flux axial. Des entreprises comme GE et Siemens Energy maintiennent des opérations significatives de R&D et de fabrication aux États-Unis et au Canada, se concentrant sur les diagnostics à distance et la gestion du cycle de vie. L’environnement réglementaire fort de la région et l’accent mis sur la décarbonisation stimulent également les investissements dans la surveillance avancée pour les flottes de turbomachineries anciennes et nouvelles.
Europe se caractérise par une base industrielle mature et des normes environnementales strictes. L’accent est mis sur les diagnostics pouvant soutenir l’intégration de l’hydrogène et des combustibles alternatifs, ainsi que la conformité aux réglementations sur les émissions. Des entreprises de premier plan telles que Rolls-Royce et Siemens Energy déploient des plates-formes d’analytique sophistiquées pour les turbomachineries de production d’énergie et d’aérospatiale. Les initiatives de numérisation de l’Union européenne et le financement des projets de transition énergétique devraient accélérer l’adoption de diagnostics intelligents à travers le continent.
Dans la région Asie-Pacifique, l’industrialisation rapide et l’expansion des infrastructures électriques et pétrochimiques stimulent la demande de diagnostics robustes. Des pays comme la Chine, le Japon, et la Corée du Sud investissent massivement tant dans la fabrication domestique que dans l’importation de solutions de turbomachinerie avancées. Des entreprises telles que Mitsubishi Heavy Industries avancent les services de surveillance à distance, tandis que des acteurs locaux et multinationaux forment des partenariats pour localiser la technologie de diagnostic et le support après-vente. La pression pour la stabilité et la fiabilité du réseau dans des économies en forte croissance rend les diagnostics avancés prioritaires.
Le Moyen-Orient reste un point chaud en raison de sa concentration d’actifs dans le secteur pétrolier & gaz et de la production d’énergie. Les opérateurs adoptent des diagnostics pour maximiser le temps de fonctionnement et prolonger la durée de vie des actifs sous des conditions d’exploitation difficiles. Des entreprises comme Baker Hughes et Siemens Energy sont des acteurs majeurs dans le déploiement de plates-formes de surveillance et d’analytique adaptées aux exigences uniques de la région. À mesure que les pays diversifient leur mix énergétique, y compris les investissements dans les énergies renouvelables et l’hydrogène, le rôle des diagnostics dans l’assurance de l’excellence opérationnelle est destiné à croître.
Dans toutes les régions, les perspectives pour les diagnostics de turbomachinerie à flux axial sont robustes, avec la numérisation, les services à distance, et les insights pilotés par l’IA devenant la norme. La convergence de la pression réglementaire, des infrastructures vieillissantes, et de la transition énergétique continue de créer de nouvelles opportunités et défis pour les OEM et les utilisateurs finaux.
Perspectives Futures : Projections d’Experts, Feuilles de Route de l’Innovation, et Priorités d’Investissement
Les perspectives pour les diagnostics de turbomachinerie à flux axial jusqu’en 2025 et dans la seconde moitié de la décennie sont façonnées par une numérisation accélérée, un accent mis sur la maintenance prédictive, et un paysage réglementaire en évolution. Les parties prenantes de l’industrie—OEM, opérateurs, et intégrateurs de technologies—priorisent les investissements dans des technologies de capteurs avancées, des analyses en temps réel, et des plates-formes de diagnostic pilotées par l’IA pour améliorer la fiabilité, l’efficacité, et la durabilité dans les secteurs de la production d’énergie, de l’aviation, et de l’industrie.
Un moteur clé est l’intégration de solutions de diagnostic basées sur le cloud et de cadres de l’Internet industriel des objets (IIoT). Les principaux fabricants de turbomachinerie tels que Siemens Energy et General Electric élargissent leurs portefeuilles de services numériques, tirant parti de l’informatique de bord et de l’apprentissage machine pour permettre une surveillance continue de la santé et la détection précoce des anomalies. Ces plates-formes agrègent des données de vibrations, acoustiques, et thermiques à haute fréquence provenant de compresseurs et turbines à flux axial, soutenant des diagnostics à distance et réduisant les temps d’arrêt imprévus. Par exemple, les offres numériques de Siemens Energy mettent l’accent sur des mises à niveau modulaires et des diagnostics interopérables, tandis que la suite de Gestion de la Performance des Actifs de General Electric est adoptée pour rationaliser la maintenance et prolonger les cycles de vie des composants.
Les feuilles de route d’innovation pour les prochaines années mettent en évidence la transition de la maintenance réactive et basée sur le calendrier vers des régimes entièrement prédictifs et prescriptifs. Des entreprises telles que Rolls-Royce investissent dans des jumeaux numériques—représentations virtuelles des actifs physiques de turbomachinerie—pour simuler dynamiquement l’usure, l’encrassement, et la dégradation des performances, permettant ainsi aux opérateurs d’optimiser les interventions et de maximiser la disponibilité. De plus, la miniaturisation des capteurs et l’avènement de dispositifs de surveillance sans fil et autonomes devraient réduire les obstacles aux rétrofits d’équipements anciens, élargissant le marché adressable.
Du point de vue des investissements, le secteur connaît une collaboration accrue entre OEM, entreprises d’automatisation, et spécialistes de l’analyse des données. Honeywell et ABB, par exemple, alignent leurs écosystèmes numériques avec ceux des OEM de turbomachinerie pour fournir des capacités de diagnostic et de prognostic de bout en bout adaptées aux objectifs de transition énergétique et de conformité aux émissions. Les priorités d’investissement sont également façonnées par des initiatives de décarbonisation—les solutions de diagnostic qui minimisent les pertes d’énergie et optimisent la flexibilité opérationnelle sont en forte demande alors que les entreprises se préparent à des réglementations CO2 plus strictes d’ici 2030.
Dans l’ensemble, les prochaines années verront les diagnostics de turbomachinerie à flux axial s’orienter davantage vers des modèles autonomes centrés sur les données. Le déploiement généralisé de capteurs intelligents, de mesures de cybersécurité améliorées, et de solutions intégrées de gestion du cycle de vie devraient définir l’agenda de l’innovation, les leaders du marché plaçant des paris stratégiques sur des diagnostics renforcés par l’IA et des modèles de service durables et numériquement habilités.
Sources & Références
- Siemens Energy
- GE Vernova
- Rolls-Royce
- Siemens Energy
- Sulzer
- American Petroleum Institute
- International Energy Agency
- Mitsubishi Heavy Industries
- Baker Hughes
- ABB
- Emerson
- Honeywell
- Wood
- ISO
- ASME
- Ansaldo Energia