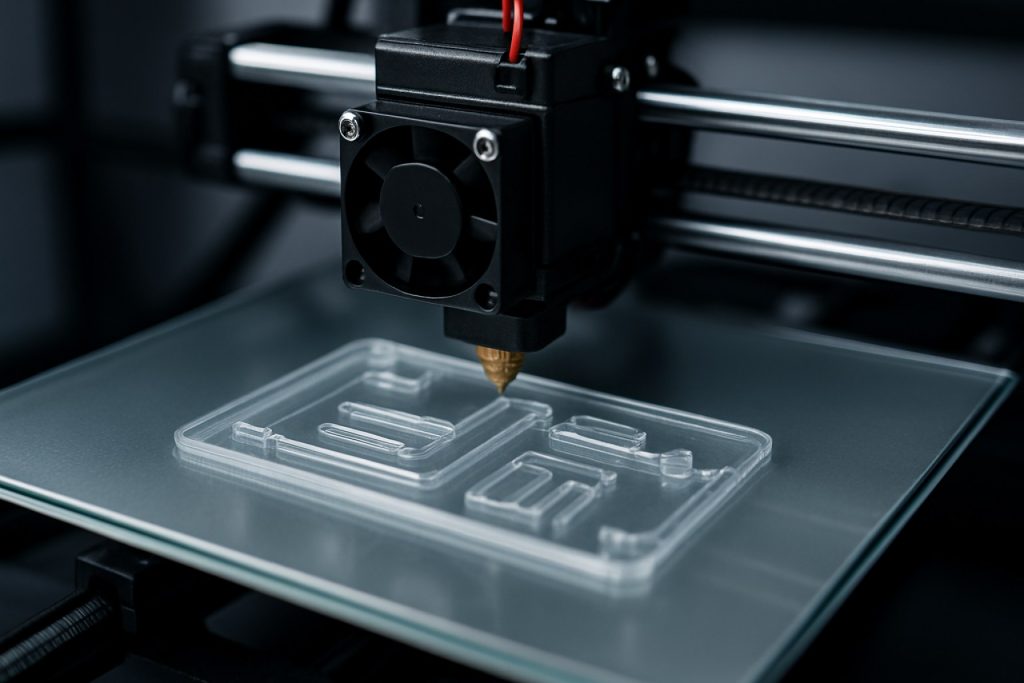
Comment l’impression 3D FDM transforme la microfluidique : Unlocking Rapid Prototyping, Customization, et Innovation Abordable pour les dispositifs Lab-on-a-Chip. Découvrez la synergie révolutionnaire entre la fabrication additive et la recherche microfluidique. (2025)
- Introduction : L’intersection de l’impression 3D FDM et de la microfluidique
- Fondamentaux de la modélisation par dépôt fondu (FDM)
- Conception de dispositifs microfluidiques : Opportunités et défis avec le FDM
- Sélection des matériaux et biocompatibilité dans les microfluidiques FDM
- Résolution, précision et qualité de surface : surmonter les limitations du FDM
- Études de cas : Applications microfluidiques FDM imprimées avec succès
- Analyse comparative : FDM vs. autres méthodes d’impression 3D pour la microfluidique
- Tendances du marché et prévisions de croissance : FDM en microfluidique (CAGR estimé de 20 à 30 % d’ici 2030)
- Innovations émergentes : Fabrication hybride et intégration fonctionnelle
- Perspectives d’avenir : Montée en puissance, standardisation et expansion de l’intérêt public
- Sources et références
Introduction : L’intersection de l’impression 3D FDM et de la microfluidique
La modélisation par dépôt fondu (FDM) en impression 3D a émergé comme une technologie transformative dans le domaine de la microfluidique, offrant de nouvelles avenues pour le prototypage rapide, la personnalisation et la fabrication de dispositifs économiques. La microfluidique, qui implique la manipulation de fluides à l’échelle submillimétrique, est fondamentale pour les avancées dans les diagnostics biomédicaux, la synthèse chimique et la surveillance environnementale. Traditionnellement, les dispositifs microfluidiques étaient fabriqués à l’aide de photolithographie et de lithographie douce, des processus souvent longs, coûteux et nécessitant des installations spécialisées. L’intégration de l’impression 3D FDM dans la microfluidique redessine ce paysage, en particulier à mesure que la technologie mûrit en 2025 et au-delà.
L’impression 3D FDM fonctionne en extrudant des matériaux thermoplastiques couche par couche pour construire des objets tridimensionnels. Son accessibilité, son coût abordable et sa compatibilité avec une gamme de polymères en ont fait un choix populaire pour les groupes de recherche académiques et industriels. Ces dernières années, les améliorations de la résolution de l’imprimante, des propriétés des matériaux et du contrôle logiciel ont permis la fabrication de canaux microfluidiques avec des dimensions approchant les 100 micromètres, une avancée significative pour le domaine. Des organisations telles que le National Institute of Standards and Technology (NIST) et les National Institutes of Health (NIH) ont souligné le potentiel des technologies d’impression 3D, y compris le FDM, pour démocratiser l’accès au développement de dispositifs microfluidiques et accélérer l’innovation dans les diagnostics au point de soin et les systèmes lab-on-a-chip.
L’année 2025 marque une période d’adoption rapide et de perfectionnement de la fabrication microfluidique basée sur le FDM. Des initiatives de matériel open-source et des plateformes collaboratives favorisent la diffusion de fichiers de conception et des meilleures pratiques, abaissant les barrières à l’entrée et favorisant une communauté mondiale de praticiens. Les universités et centres de recherche de premier plan publient des protocoles et des études de cas démontrant l’application réussie de la microfluidique imprimée en FDM dans des domaines tels que la culture cellulaire, la génération de gouttelettes et l’analyse chimique. La National Science Foundation (NSF) continue de financer des recherches interdisciplinaires qui exploitent l’impression 3D FDM pour l’innovation microfluidique, soulignant l’importance de la reproductibilité, de l’échelle et de l’intégration avec des composants électroniques et optiques.
En regardant vers l’avenir, l’intersection de l’impression 3D FDM et de la microfluidique devrait engendrer d’autres percées en complexité des dispositifs, intégration multi-matériaux et fonctionnalisation. À mesure que la science des matériaux progresse et que les capacités d’impression s’améliorent, le FDM est prêt à jouer un rôle central dans la prochaine génération de technologies microfluidiques, soutenant à la fois la recherche fondamentale et les applications réelles dans les soins de santé, la science de l’environnement et au-delà.
Fondamentaux de la modélisation par dépôt fondu (FDM)
La modélisation par dépôt fondu (FDM) est une technique de fabrication additive largement adoptée qui a gagné une traction significative dans le domaine de la microfluidique, surtout à mesure que la technologie mûrit en 2025. Le FDM fonctionne en extrudant des filaments thermoplastiques à travers une buse chauffée, déposant le matériau couche par couche pour construire des objets tridimensionnels. Le processus est régulé par un contrôle précis de la température, du taux d’extrusion et du mouvement le long des axes X, Y et Z, permettant la fabrication de géomÉtries complexes avec une précision et une répétabilité raisonnables.
Dans la microfluidique, la demande de prototypage rapide et de fabrication de dispositifs économiques a stimulé l’adoption du FDM. Les méthodes de microfabrication traditionnelles, telles que la lithographie douce, nécessitent des installations en salle blanche et prennent beaucoup de temps, tandis que le FDM offre une alternative de bureau capable de produire des dispositifs microfluidiques fonctionnels en quelques heures. Les récentes avancées dans le matériel et les matériaux FDM ont amélioré la résolution et la compatibilité chimique des dispositifs imprimés, les rendant de plus en plus adaptés aux applications en diagnostics, en synthèse chimique et en essais biologiques.
Un aspect clé de l’application du FDM en microfluidique est la capacité d’imprimer des canaux et des chambres avec des dimensions de l’ordre de quelques centaines de micromètres. Bien que le FDM soit intrinsèquement limité par le diamètre de la buse et la hauteur de couche—généralement entraînant des tailles de caractéristiques minimales de 200 à 400 μm—les recherches en cours repoussent ces limites. En 2025, plusieurs groupes de recherche et entreprises expérimentent des buses plus fines, des paramètres d’impression optimisés et des techniques de post-traitement pour obtenir des canaux plus petits et plus lisses. Par exemple, l’utilisation de matériaux de soutien solubles dans l’eau permet la création de microcanaux fermés, qui sont ensuite dégagés en dissolvant le support, une méthode de plus en plus adoptée dans les milieux académiques et industriels.
La sélection des matériaux est un autre aspect critique. Les matériaux FDM courants tels que l’acide polylactique (PLA) et le styrène acrylonitrile butadiène (ABS) sont appréciés pour leur facilité d’utilisation et leur biocompatibilité, mais de nouveaux filaments avec une résistance chimique améliorée et une transparence optique sont en cours de développement pour répondre aux besoins spécifiques des applications microfluidiques. Des organisations comme le National Institute of Standards and Technology (NIST) participent activement à la normalisation des propriétés des matériaux et des protocoles d’impression pour garantir la reproductibilité et la fiabilité dans la fabrication de dispositifs microfluidiques.
En regardant vers l’avenir, les perspectives pour le FDM en microfluidique sont prometteuses. La convergence d’une résolution d’imprimante améliorée, de matériaux avancés et de dépôts de conception open-source devrait encore démocratiser l’accès à la technologie microfluidique. À mesure que les imprimantes FDM deviennent plus abordables et performantes, leur rôle dans le prototypage rapide et même la production à petite échelle de dispositifs microfluidiques est appelé à s’élargir, soutenant l’innovation dans les diagnostics au point de soin, la surveillance environnementale et les outils éducatifs jusqu’en 2025 et au-delà.
Conception de dispositifs microfluidiques : Opportunités et défis avec le FDM
La modélisation par dépôt fondu (FDM) en impression 3D a émergé comme une technologie transformative dans la conception et le prototypage de dispositifs microfluidiques, offrant une fabrication rapide, économique et accessible. En 2025, la communauté microfluidique exploite de plus en plus le FDM pour relever des défis de longue date dans le développement de dispositifs, notamment pour des applications en diagnostics, synthèse chimique et tests au point de soin.
Une des principales opportunités que présente le FDM est la démocratisation de la fabrication de dispositifs microfluidiques. Les méthodes traditionnelles, telles que la lithographie douce, nécessitent des installations en salle blanche et une expertise spécialisée, limitant l’accessibilité. En revanche, les imprimantes FDM sont largement accessibles et abordables, permettant aux chercheurs et aux petits laboratoires d’itérer rapidement les conceptions. Cela a conduit à une hausse des projets microfluidiques open-source et à l’innovation collaborative, comme le montrent les initiatives soutenues par des organisations telles que le National Institute of Standards and Technology (NIST), qui promeut activement des normes et meilleures pratiques pour la fabrication additive en recherche scientifique.
Les avancées récentes dans le matériel et les matériaux FDM ont encore élargi son utilité. L’introduction de buses plus fines, de moteurs pas à pas améliorés et de systèmes de contrôle de température a permis l’impression de canaux de dimensions approchant les 200 micromètres, une amélioration significative par rapport aux générations précédentes. Les développements en science des matériaux, y compris la disponibilité de filaments transparents et chimiquement résistants, ont résolu certains des problèmes de compatibilité qui limitaient auparavant l’utilisation du FDM en microfluidique. Par exemple, le National Institute of Standards and Technology a publié des directives sur la caractérisation des polymères imprimés en 3D pour des applications fluidiques, soutenant la reproductibilité et la fiabilité.
Malgré ces avancées, des défis subsistent. Réaliser de véritables caractéristiques microscale (<100 micromètres) reste difficile en raison des limitations inhérentes au dépôt couche par couche du FDM et à la taille de l'orifice. La rugosité de surface et la fidélité des canaux peuvent affecter le flux de fluide et la performance des dispositifs, nécessitant des étapes de post-traitement telles que le lissage par solvant ou le revêtement. De plus, la gamme de matériaux biocompatibles et optiquement clairs adaptés au FDM est encore limitée par rapport à d'autres méthodes d'impression 3D comme la stéréolithographie (SLA).
À l’avenir, des recherches sont en cours sur des approches de fabrication hybrides, combinant le FDM avec d’autres techniques pour surmonter les limitations actuelles. Le développement de nouveaux filaments composites et des capacités d’impression multi-matériaux devraient encore améliorer la fonctionnalité des dispositifs microfluidiques fabriqués en FDM. Des organisations comme le National Institute of Standards and Technology et la National Science Foundation devraient jouer un rôle clé dans la normalisation des processus et le soutien à l’innovation dans ce domaine en rapide évolution. À mesure que ces efforts mûrissent, le FDM est prêt à devenir un outil encore plus essentiel dans le paysage de conception de la microfluidique jusqu’en 2025 et au-delà.
Sélection des matériaux et biocompatibilité dans les microfluidiques FDM
La sélection des matériaux et la biocompatibilité sont des considérations cruciales dans l’avancement de l’impression 3D par modélisation par dépôt fondu (FDM) pour les applications microfluidiques, surtout maintenant que le domaine progresse vers 2025 et au-delà. Le choix des matériaux thermoplastiques impacte directement la performance des dispositifs, leur compatibilité chimique et leur adéquation pour les essais biologiques. Traditionnellement, le FDM s’est appuyé sur des polymères tels que l’acide polylactique (PLA), le styrène acrylonitrile butadiène (ABS), et le polyéthylène téréphtalate glycol (PETG). Ces matériaux sont appréciés pour leur imprimabilité et leurs propriétés mécaniques, mais leur biocompatibilité et leur résistance chimique varient considérablement.
Les dernières années ont vu une montée en flèche de la recherche et du développement visant à élargir la palette de matériaux pour les microfluidiques FDM. Le PLA, un polymère biodégradable dérivé de ressources renouvelables, reste populaire en raison de sa facilité d’utilisation et de sa biocompatibilité générale, ce qui le rend adapté à certaines applications de culture cellulaire et de diagnostic. Cependant, sa résistance chimique limitée et sa stabilité thermique modérée restreignent son utilisation dans des environnements microfluidiques plus exigeants. Le PETG, en revanche, offre une meilleure résistance chimique et une transparence, ce qui est avantageux pour la détection optique et l’imagerie dans les dispositifs microfluidiques. L’ABS, bien que robuste, nécessite souvent un post-traitement pour éliminer les additifs toxiques et améliorer les propriétés de surface pour les applications biologiques.
Une tendance clé pour 2025 est le développement et la commercialisation de filaments FDM spécialisés adaptés à la microfluidique. Cela inclut des polymères de qualité médicale et certifiés biocompatibles, ainsi que des matériaux composites avec une meilleure lisse de surface et des leachables réduits. Par exemple, des groupes de recherche et des entreprises explorent l’utilisation de copolymères d’oléfine cyclique (COC) et de mélanges de polycarbonate (PC), qui offrent une clarté optique supérieure et une inertie chimique. L’intégration d’additifs antimicrobiens et de traitements de surface est également à l’étude pour réduire le bio-encrassement et améliorer la durabilité des dispositifs.
Les tests de biocompatibilité deviennent de plus en plus standardisés, avec des protocoles s’alignant sur des normes internationales telles que l’ISO 10993 pour l’évaluation biologique des dispositifs médicaux. Des organisations comme l’Organisation internationale de normalisation et des organismes réglementaires tels que la Food and Drug Administration (FDA) des États-Unis fournissent des orientations plus claires sur les exigences relatives aux matériaux utilisés dans la microfluidique biomédicale. Cette clarté réglementaire devrait accélérer l’adoption des dispositifs microfluidiques imprimés en FDM dans des milieux cliniques et de recherche.
À l’avenir, les perspectives pour la sélection des matériaux dans les microfluidiques FDM sont prometteuses. Les collaborations en cours entre scientifiques des matériaux, ingénieurs de dispositifs et agences réglementaires devraient donner naissance à de nouveaux filaments aux propriétés adaptées pour des applications microfluidiques spécifiques. La convergence du développement de matériaux open-source et de l’innovation commerciale devrait en outre démocratiser l’accès à l’impression FDM biocompatible, soutenant le prototypage rapide et le déploiement de dispositifs microfluidiques de prochaine génération.
Résolution, précision et qualité de surface : surmonter les limitations du FDM
La modélisation par dépôt fondu (FDM) en impression 3D est devenue un outil de plus en plus accessible pour le prototypage et la fabrication de dispositifs microfluidiques. Cependant, son adoption dans la microfluidique a historiquement été limitée par des défis en matière de résolution, de précision et de qualité de surface—des paramètres critiques pour le fonctionnement fiable des canaux fluidiques à échelle microscopique. En 2025, des avancées significatives sont réalisées pour remédier à ces limitations, grâce à l’innovation matérielle et à l’optimisation des processus.
La taille minimale des caractéristiques réalisables par les imprimantes FDM standard varie généralement de 200 à 400 micromètres, ce qui est supérieur aux caractéristiques sub-100 micromètres souvent requises dans les applications microfluidiques avancées. Les avancées récentes dans la conception de buses, le contrôle de l’extrusion et les systèmes de mouvement repoussent ces limites. Par exemple, les fabricants introduisent des buses plus fines (jusqu’à 0,1 mm) et des moteurs pas à pas plus précis, permettant une meilleure exactitude dimensionnelle et une répétabilité accrue. Des entreprises telles que Ultimaker et Prusa Research sont à la pointe de ces développements matériels, offrant des plateformes open-source qui facilitent l’itération rapide et la personnalisation pour les besoins de la recherche.
La rugosité de surface demeure un défi clé, car le dépôt couche par couche inhérent au FDM crée des stries qui peuvent perturber l’écoulement laminaire et favoriser un mélange ou une adsorption indésirable dans les canaux microfluidiques. En 2025, les chercheurs utilisent de plus en plus des techniques de post-traitement telles que le lissage aux vapeurs de solvant, le polissage mécanique et l’infiltration de résine pour réduire la rugosité de surface en dessous de 10 micromètres Ra, ce qui approche le seuil pour de nombreuses applications microfluidiques. De plus, l’utilisation de nouveaux filaments thermoplastiques avec des caractéristiques d’écoulement améliorées et des points de fusion plus bas est explorée pour améliorer la fidélité d’impression et la finition de surface.
La précision de la géométrie des canaux est également améliorée grâce à la surveillance des processus en temps réel et aux systèmes de retour d’information en boucle fermée. L’intégration de la vision artificielle et de la métrologie in-situ permet la détection et la correction des défauts d’impression pendant la fabrication, une tendance soutenue par des efforts collaboratifs entre groupes de recherche académiques et partenaires industriels. Des organisations telles que le National Institute of Standards and Technology (NIST) développent activement des normes et des meilleures pratiques pour la fabrication additive en microfluidique, ce qui devrait accélérer l’adoption du FDM pour la fabrication de dispositifs fonctionnels.
À l’avenir, les perspectives pour le FDM en microfluidique sont optimistes. La convergence des améliorations matérielles, des avancées en sciences des matériaux et du contrôle numérique des processus devrait encore réduire l’écart entre le FDM et des techniques de plus haute résolution telles que la stéréolithographie (SLA) et la polymérisation par deux photons. À mesure que les communautés open-source et les organismes de normalisation continuent de stimuler l’innovation, le FDM est prêt à devenir une option viable et économique pour le prototypage rapide et même la production en petites séries de dispositifs microfluidiques dans les années à venir.
Études de cas : Applications microfluidiques FDM imprimées avec succès
Ces dernières années, la modélisation par dépôt fondu (FDM) en impression 3D a émergé comme une méthode pratique et accessible pour fabriquer des dispositifs microfluidiques, avec plusieurs études de cas réussies démontrant son potentiel dans des contextes tant de recherche qu’appliqués. En 2025, le domaine a connu des progrès notables en matière de résolution, de compatibilité des matériaux et d’intégration fonctionnelle des systèmes microfluidiques imprimés en FDM.
Un exemple marquant est l’utilisation de puces microfluidiques imprimées en FDM pour des diagnostics au point de soin. Des chercheurs d’institutions académiques de premier plan ont développé des flux de travail de prototypage rapide et à faible coût utilisant des imprimantes FDM pour créer des dispositifs pour la séparation de plasma sanguin et la détection de pathogènes. Ces dispositifs, fabriqués à partir de thermoplastiques biocompatibles tels que l’acide polylactique (PLA) et le polyéthylène téréphtalate glycol (PETG), ont démontré une manipulation des fluides fiable et une compatibilité avec des essais de laboratoire standards. Les National Institutes of Health ont soutenu plusieurs projets explorant les microfluidiques imprimées en FDM pour le dépistage rapide de maladies, notamment dans des environnements limités en ressources.
Une autre application réussie concerne la surveillance environnementale. En 2024, un projet collaboratif entre des centres de recherche européens et des agences environnementales a utilisé des plateformes microfluidiques imprimées en FDM pour l’analyse de la qualité de l’eau sur site. Ces dispositifs intégraient des capteurs et des réservoirs de réactifs directement dans la structure imprimée, permettant la détection en temps réel de contaminants tels que les métaux lourds et les nitrates. Les Laboratoires fédéraux suisses pour les sciences et technologies des matériaux (Empa) ont publié des données sur la durabilité et la résistance chimique des dispositifs microfluidiques imprimés en FDM dans des conditions de terrain, mettant en évidence leur adéquation aux applications robustes.
Dans le secteur pharmaceutique, des réacteurs microfluidiques imprimés en FDM ont été utilisés pour la synthèse en flux continu et le dépistage de médicaments. Des entreprises et des groupes de recherche ont rapporté la fabrication réussie de réacteurs modulaires et personnalisables qui peuvent être rapidement itérés pour optimiser les conditions de réaction. La Food and Drug Administration (FDA) des États-Unis a reconnu le rôle croissant de l’impression 3D dans la fabrication pharmaceutique, y compris l’utilisation du FDM pour le prototypage et le développement de processus.
À l’avenir, les prochaines années devraient apporter une intégration encore plus poussée des microfluidiques imprimées en FDM avec l’électronique et les capteurs, permettant des systèmes lab-on-a-chip intelligents. Les améliorations continues de la résolution d’impression et de la science des matériaux, soutenues par des organisations telles que le National Institute of Standards and Technology (NIST), devraient élargir la gamme d’applications et améliorer les performances des dispositifs. Ces études de cas soulignent la polyvalence et l’impact de l’impression 3D FDM dans l’avancement de la technologie microfluidique à travers des domaines diversifiés.
Analyse comparative : FDM vs. autres méthodes d’impression 3D pour la microfluidique
La modélisation par dépôt fondu (FDM) a émergé comme une technologie d’impression 3D largement accessible pour la fabrication de dispositifs microfluidiques, mais ses performances comparatives par rapport à d’autres méthodes de fabrication additive—telles que la stéréolithographie (SLA), le traitement par lumière numérique (DLP) et PolyJet—demeurent un sujet de recherche et de développement actif. En 2025, la communauté microfluidique se concentre de plus en plus sur l’évaluation de ces technologies en termes de résolution, de compatibilité des matériaux, de coût et d’évolutivité.
L’avantage principal du FDM réside dans son accessibilité et sa disponibilité généralisée. Les matériels open-source et une large gamme de filaments thermoplastiques ont fait des imprimantes FDM un élément de base dans les environnements académiques et de prototypage. Cependant, le processus d’extrusion couche par couche de la technologie limite généralement sa taille de caractéristique minimale à environ 200 à 400 micromètres, ce qui est moins précis que les caractéristiques sub-100 micromètres réalisables avec la SLA ou la DLP. Cette limitation est significative pour les applications microfluidiques qui nécessitent des géométries de canaux fines et des surfaces internes lisses pour garantir un écoulement laminaire et prévenir la perte d’échantillons.
Les avancées récentes dans le FDM, telles que l’utilisation de buses plus fines et de paramètres d’impression optimisés, ont réduit l’écart de résolution. Les groupes de recherche expérimentent également des techniques de post-traitement—comme le lissage par vapeurs de solvant et les revêtements de surface—pour améliorer la fidélité des canaux et réduire la rugosité de surface. Néanmoins, la SLA et la DLP, qui utilisent la photopolymérisation pour durcir la résine couche par couche, continuent d’offrir un meilleur fini de surface et une résolution de caractéristiques supérieure. Ces méthodes sont de plus en plus adoptées pour le prototypage microfluidique, surtout dans des applications exigeant une haute précision, telles que l’analyse de cellules uniques et la génération de gouttelettes.
La compatibilité des matériaux est un autre critère de différenciation. Le FDM prend en charge une variété de thermoplastiques, y compris des options biocompatibles et chimiquement résistantes comme l’acide polylactique (PLA) et le styrène acrylonitrile butadiène (ABS). Cependant, les résines SLA et DLP peuvent être conçues pour des propriétés optiques, mécaniques ou chimiques spécifiques, élargissant leur utilité dans des applications microfluidiques spécialisées. La technologie PolyJet, offerte par des entreprises telles que Stratasys, permet l’impression multi-matériaux avec une haute résolution, mais à un coût plus élevé et avec un post-traitement plus complexe.
Le coût et l’accessibilité demeurent des atouts majeurs pour le FDM. Les imprimantes FDM d’entrée de gamme sont significativement moins chères que les systèmes SLA, DLP ou PolyJet, ce qui les rend attrayantes pour le prototypage rapide et l’utilisation éducative. Le mouvement open-source, défendu par des organisations comme le RepRap Project, continue de stimuler l’innovation et de démocratiser l’accès à la technologie FDM.
À l’avenir, les prochaines années devraient voir davantage d’améliorations de la résolution d’impression du FDM et de la diversité des matériaux, réduisant l’écart avec les méthodes basées sur des photopolymères. Les approches hybrides—combinant le FDM avec des post-traitements ou intégrant des composants imprimés en FDM avec d’autres techniques de fabrication—devraient élargir la gamme d’applications microfluidiques. À mesure que le domaine mûrit, le choix entre FDM et d’autres méthodes d’impression 3D dépendra de plus en plus des exigences spécifiques de chaque dispositif microfluidique, trouvant un équilibre entre coût, résolution et besoins en matériaux.
Tendances du marché et prévisions de croissance : FDM en microfluidique (CAGR estimé de 20 à 30 % d’ici 2030)
L’impression 3D par modélisation par dépôt fondu (FDM) a rapidement gagné du terrain dans le secteur de la microfluidique, soutenue par son accessibilité, son efficacité et les améliorations continues de la résolution d’impression et de la compatibilité des matériaux. En 2025, le marché de l’impression 3D FDM en microfluidique connaît une croissance robuste, avec des analystes industriels et des institutions de recherche projetant un taux de croissance annuel composé (CAGR) dans la fourchette de 20 à 30 % d’ici 2030. Cette expansion est alimentée par l’adoption croissante dans la recherche académique, le prototypage, et même dans la production commerciale précoce de dispositifs microfluidiques.
Les principaux moteurs de cette croissance incluent la démocratisation de la fabrication des dispositifs microfluidiques, alors que les imprimantes FDM deviennent plus abordables et conviviales. Des fabricants majeurs tels que Ultimaker et Stratasys ont introduit des systèmes FDM avec une précision améliorée et une gamme plus large de thermoplastiques biocompatibles et chimiquement résistants, les rendant adaptés aux applications microfluidiques. Le mouvement open-source pour le matériel et le logiciel, défendu par des organisations comme le RepRap Project, continue de réduire les barrières d’entrée, permettant à davantage de laboratoires et de startups de concevoir et de fabriquer en interne des puces microfluidiques personnalisées.
Les dernières années ont vu une augmentation des recherches publiées et des dépôts de brevets liés aux dispositifs microfluidiques fabriqués en FDM, en particulier dans les domaines des diagnostics au point de soin, de la surveillance environnementale et des systèmes organ-on-chip. Des consortiums académiques et des organismes de recherche publics, tels que les National Institutes of Health (NIH), ont financé des initiatives visant à normaliser les protocoles de fabrication microfluidique basés sur le FDM, légitimant davantage la technologie pour des applications biomédicales et analytiques.
À l’avenir, les perspectives de l’impression 3D FDM en microfluidique restent très positives. Les avancées continues en matière de technologie de tête d’impression, d’impression multi-matériaux et de techniques de post-traitement devraient encore rétrécir l’écart entre le FDM et les méthodes de fabrication additive à haute résolution. Les parties prenantes de l’industrie anticipent qu’en 2030, le FDM dominera non seulement le prototypage rapide mais jouera également un rôle significatif dans la production à faible volume de dispositifs microfluidiques fonctionnels, en particulier pour des applications personnalisées et décentralisées.
- On s’attend à une adoption plus large dans les environnements éducatifs et limités en ressources, alors que les imprimantes FDM deviennent encore plus accessibles.
- Les collaborations entre fabricants d’imprimantes, scientifiques des matériaux et chercheurs en microfluidique devraient donner naissance à de nouveaux polymères imprimables adaptés à la performance microfluidique.
- Les organismes réglementaires, y compris la Food and Drug Administration (FDA) des États-Unis, devraient élaborer des directives plus claires pour l’utilisation des dispositifs microfluidiques imprimés en 3D dans les milieux cliniques et diagnostiques.
En résumé, le marché de l’impression 3D FDM dans la microfluidique est prêt pour une croissance durable à deux chiffres, soutenue par l’innovation technologique, l’expansion des domaines d’application et le soutien institutionnel croissant.
Innovations émergentes : Fabrication hybride et intégration fonctionnelle
L’impression 3D par modélisation par dépôt fondu (FDM) a rapidement évolué en tant que catalyseur clé dans la fabrication de dispositifs microfluidiques, surtout alors que le domaine se dirige vers la fabrication hybride et l’intégration fonctionnelle. En 2025, la convergence du FDM avec d’autres techniques de fabrication—telles que l’écriture directe d’encre, le micromachinage laser et la lithographie douce—conduit à une nouvelle ère de complexité et de performances des dispositifs. Cette approche hybride permet l’intégration de plusieurs matériaux, de capteurs intégrés et de composants actifs directement dans les puces microfluidiques, s’attaquant ainsi aux défis de longue date liés à la miniaturisation des dispositifs et à leur multifonctionnalité.
Les dernières années ont vu émerger des filaments compatibles FDM avec des propriétés améliorées, notamment une meilleure transparence, une résistance chimique et une biocompatibilité. Ces matériaux sont en cours de développement et de validation par des institutions de recherche de premier plan et des acteurs de l’industrie, permettant la fabrication de dispositifs microfluidiques adaptés aux diagnostics biomédicaux, aux systèmes organ-on-chip et à la surveillance environnementale. Par exemple, le National Institute of Standards and Technology (NIST) a été activement impliqué dans la normalisation des matériaux et des processus pour la microfluidique imprimée en 3D, garantissant la reproductibilité et la fiabilité dans des applications critiques.
Les flux de travail de fabrication hybride exploitent désormais les forces du FDM—telles que le prototypage rapide et l’économie de coût—tout en surmontant ses limitations en matière de résolution et de qualité de surface en le combinant avec des post-traitements de haute précision ou des techniques additives complémentaires. Cela a permis la création de dispositifs microfluidiques avec des électrodes intégrées, des guides d’ondes optiques et même des microvalves, élargissant le répertoire fonctionnel des plateformes lab-on-a-chip. Des organisations comme le Nature Publishing Group et Elsevier ont documenté une augmentation des publications évaluées par des pairs détaillant ces stratégies hybrides, reflétant un consensus croissant sur leur potentiel transformateur.
À l’avenir, les prochaines années devraient témoigner d’une intégration accrue du FDM avec les écosystèmes de fabrication numérique, y compris l’optimisation automatisée des conceptions et le contrôle qualité en ligne. L’adoption de plateformes matérielles et logicielles open-source s’accélère également, démocratisant l’accès à la fabrication microfluidique avancée et favorisant la collaboration mondiale. Des initiatives des National Institutes of Health (NIH) et de la National Science Foundation (NSF) soutiennent la recherche interdisciplinaire dans ce domaine, avec un accent sur les applications translationales en santé et en science environnementale.
En résumé, l’impression 3D FDM est prête à jouer un rôle central dans la prochaine génération de dispositifs microfluidiques, avec la fabrication hybride et l’intégration fonctionnelle au premier plan de l’innovation. À mesure que la science des matériaux, l’ingénierie des processus et le design numérique continuent de progresser, les limites de ce qui est possible en microfluidique devraient s’étendre de manière significative jusqu’en 2025 et au-delà.
Perspectives d’avenir : Montée en puissance, standardisation et expansion de l’intérêt public
L’avenir de l’impression 3D par modélisation par dépôt fondu (FDM) en microfluidique est prêt pour une transformation significative alors que le domaine se dirige vers une adoption plus large, la standardisation et l’engagement public. En 2025, le FDM reste l’une des techniques de fabrication additive les plus accessibles et économiques, en faisant un pilier pour démocratiser la fabrication de dispositifs microfluidiques tant dans des contextes académiques qu’industriels.
Une tendance clé est la montée en puissance de la production microfluidique basée sur le FDM. Les récentes avancées en matière de résolution d’imprimante, d’extrusion multi-matériaux et de formulation de filaments permettent de fabriquer des architectures microfluidiques plus complexes et fonctionnelles. Des fabricants leaders tels que Ultimaker et Prusa Research développent activement des améliorations matérielles et logicielles open-source qui soutiennent des tailles de caractéristiques plus fines et une meilleure étanchéité des canaux, qui sont critiques pour les applications microfluidiques. Ces développements devraient abaisser la barrière pour le prototypage et la production à petite échelle, surtout dans des environnements limités en ressources.
La standardisation émerge comme un axe central pour le domaine. Des organisations comme l’Organisation internationale de normalisation (ISO) et le National Institute of Standards and Technology (NIST) sont de plus en plus impliquées dans l’établissement de directives pour les dispositifs microfluidiques imprimés en 3D, y compris les tolérances dimensionnelles, la biocompatibilité des matériaux et les métriques de performance des dispositifs. De telles normes sont cruciales pour garantir la reproductibilité et l’interopérabilité, en particulier alors que les microfluidiques imprimées en FDM passent de prototypes de recherche à des produits commerciaux et cliniques.
L’intérêt public pour la microfluidique, alimenté par le projecteur sur les diagnostics rapides et les tests au point de soin pendant la pandémie de COVID-19, devrait croître davantage à mesure que l’impression FDM rend la fabrication des dispositifs plus accessible. Les initiatives éducatives et les projets open-source, tels que ceux promus par les National Institutes of Health (NIH), élargissent la sensibilisation et la formation au design numérique et à la fabrication. Cette démocratisation devrait favoriser une nouvelle génération de citoyens scientifiques et d’entrepreneurs, accélérant l’innovation dans des domaines allant de la surveillance environnementale à la médecine personnalisée.
À l’avenir, les prochaines années devraient voir l’impression 3D FDM dans la microfluidique se diriger vers une plus grande automatisation, une intégration avec des outils de design numérique et l’adoption de matériaux durables. À mesure que l’écosystème mûrit, des collaborations entre l’industrie, le monde académique et les organismes réglementaires seront essentielles pour relever les défis de l’assurance qualité et de l’approbation réglementaire, ouvrant la voie à un déploiement généralisé des solutions microfluidiques imprimées en FDM.
Sources et références
- National Institute of Standards and Technology
- National Institutes of Health
- National Science Foundation
- Organisation internationale de normalisation
- Ultimaker
- Prusa Research
- National Institute of Standards and Technology (NIST)
- Laboratoires fédéraux suisses pour les sciences et technologies des matériaux (Empa)
- Stratasys
- RepRap Project
- National Institutes of Health
- Nature Publishing Group
- Elsevier
- Organisation internationale de normalisation