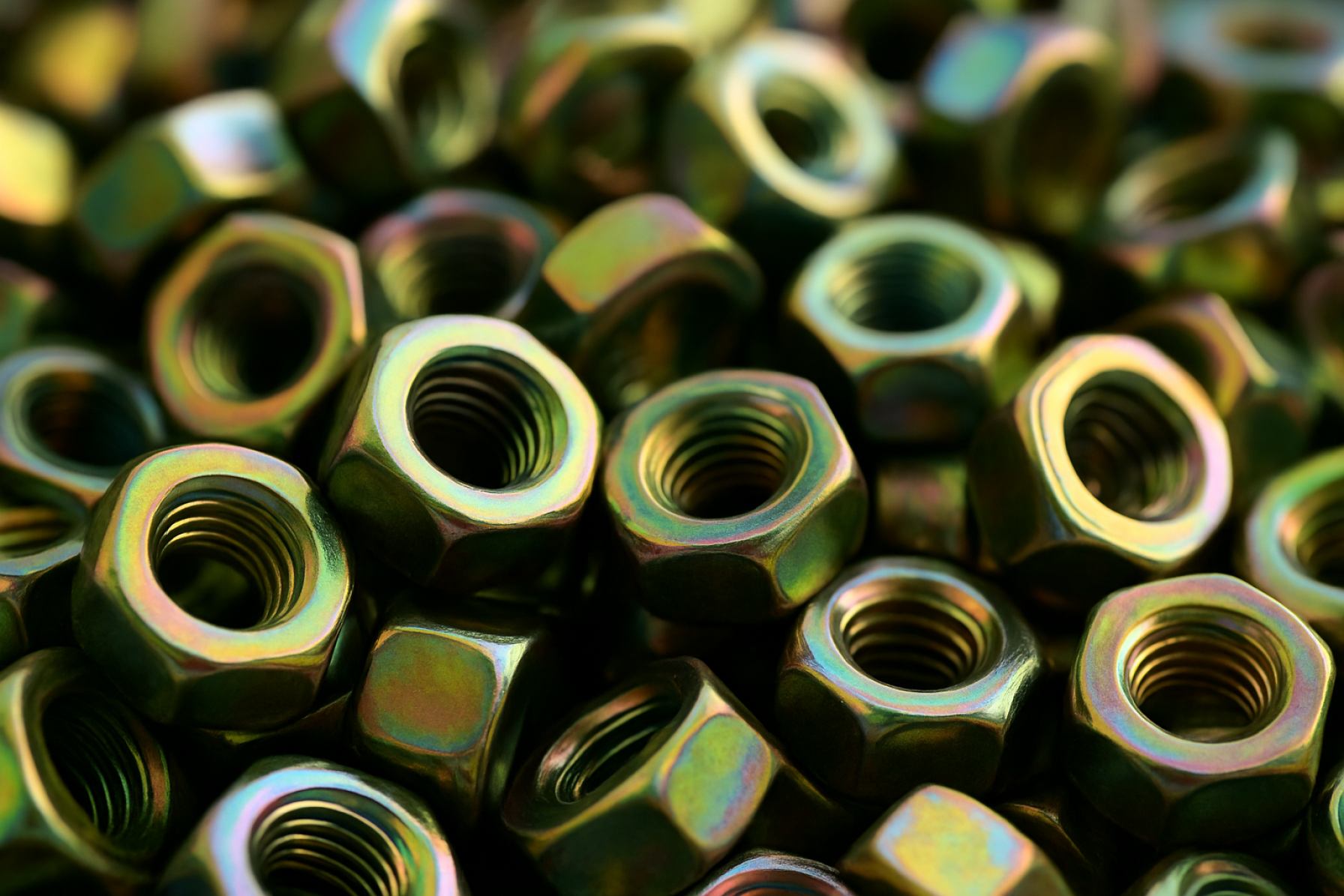
目次
- エグゼクティブサマリー:2025-2029年における亜鉛-ニッケル層状コーティングの主要トレンド
- 技術概要:現在の状況と次世代のエンジニアリングの進展
- 市場規模と予測:2029年までの世界的および地域的需要
- 競争環境:主要企業と戦略的パートナーシップ
- 自動車および航空宇宙の需要:セクター特有の成長要因
- イノベーションパイプライン:特許、R&D、出現するプロセス
- 持続可能性と規制の変化:環境およびコンプライアンス要因
- サプライチェーンと原材料の課題
- 顧客の採用:OEM、Tier 1、およびアフターマーケットの視点
- 今後の展望:破壊的技術と戦略的推奨事項
- 出典および参考文献
エグゼクティブサマリー:2025-2029年における亜鉛-ニッケル層状コーティングの主要トレンド
亜鉛-ニッケル層状コーティングのエンジニアリングは、2025年から2029年にかけて大きな進化を遂げようとしており、産業セクターは耐腐食性の向上、環境規制の遵守、コスト効率の向上にますます焦点を当てています。亜鉛-ニッケルコーティングは、自動車、航空宇宙、重機などの応用において優れた腐食保護が認められており、伝統的な純亜鉛やカドミウムベースの代替品からの移行が進む中で、堅調な需要が予想されています。
最近の数年間では、MacDermid AlphaやAtotechのような主要メーカーが合金組成や堆積技術の革新を推進しています。これらの企業は、亜鉛-ニッケルの電気メッキ技術を進化させ、均一性の向上、水素脆化の低減、そして世界的に厳しくなっている規制基準の遵守を目指しています。特に、REACHおよびRoHS指令に沿った六価クロムフリーのパッシベーションへの移行が、コーティングの配合や後処理プロセスを再構築しています。
この分野からのデータは、高ニッケル含有コーティング(ニッケル12~15%)への明確な移行を示しており、これにより塩霧試験において通常の亜鉛コーティングよりも最大10倍の腐食抵抗を提供します。これは、自動車用ファスナー、シャシー部品、電気コネクタなどでは特に重要であり、自動車レーシング製品やNorm Fastenersのようなメーカーが、OEMおよびアフターマーケットの部品に対して亜鉛-ニッケルを指定する傾向が高まっています。
自動化とデジタル化も亜鉛-ニッケルコーティングの状況を変えることが期待されています。AWAのような主要なメッキラインプロバイダーは、高度なプロセス制御、リアルタイムの品質監視、統合データ分析を組み込んでいます。これらの技術的向上は、生産性の向上、廃棄物削減、トレーサビリティの向上など、ライフサイクルコストと品質保証を最適化しようとする自動車および電子OEMからの需要に応えるものです。
2025-2029年の市場展望は依然として堅調です。電気自動車および再生可能エネルギーシステムへの移行は、厳しい環境での信頼できる腐食保護の必要性をさらに助長するでしょう。同時に、グローバルなサプライチェーンの圧力は、柔軟で地域的なコーティング業務の促進を促し、ヨーロッパ、北米、アジア太平洋の企業が設備能力を拡大し、地域のパートナーシップを強化しています。
要するに、今後数年間は、亜鉛-ニッケル層状コーティングのエンジニアリングが、規制主導の革新、高機能合金の採用の増加、スマート製造技術の統合によって特徴づけられるでしょう。バリューチェーンの関係者、すなわち化学供給業者、コーティングサービスプロバイダー、自動車および産業セクターのエンドユーザーは、持続可能性および業務の卓越性に向けた産業の移行においてこれらの進展から恩恵を受ける準備が整っています。
技術概要:現在の状況と次世代のエンジニアリングの進展
亜鉛-ニッケル層状コーティングは、特に自動車、航空宇宙、産業用途における高度な耐腐食保護の重要な技術として浮上しています。2025年現在、この分野は、ますます厳しくなる環境規制と高性能の表面処理への需要によって駆動される顕著なエンジニアリングの進展を経験しています。亜鉛-ニッケルコーティングの中核的な利点は、通常12~16%のニッケルを含んでおり、ニュートラルな塩霧テストで従来の亜鉛コーティングに比べて最大で5倍の耐腐食性を発揮することです。このパフォーマンスは、OEMやTierサプライヤーの間で広く採用されています。
AtotechやDuPontのような主要な製造業者は、浴槽の化学物質やプロセス制御の精緻化に投資し、複雑な形状に対してより正確な層の厚さと均一な合金組成を可能にしています。最近のプロセスオートメーションには、電解質の組成のリアルタイム監視や高度な電流変調が含まれており、電気メッキラインでのより厳しい品質許容基準とエネルギー効率の向上を可能にしています。さらに、MacDermid Alphaのような企業が推進する三価クロムパッシベーションシステムの導入は、六価クロムからのグローバルな移行に応じたものであり、これも規制の動向に合わせたものです。
材料工学の観点から、層堆積および複数段階の堆積技術が進化しています。次世代アプローチでは、亜鉛-ニッケル合金層だけでなく、デュプレックスおよびトリプレックスシステムも含まれており、これにより追加の有機またはセラミックのトップコートが適用されてサービス寿命を延ばし、自己修復または撥水効果のような機能的な特性を付加することが可能です。Atotechなどの企業は、ラックおよびバレルメッキの両方に適応可能なモジュラーコーティングシステムを開発しています。これにより、柔軟な製造とリードタイムの短縮が実現されています。
近い将来、デジタル化とデータ駆動のプロセス最適化がより大きな役割を果たすと期待されています。複数の国際的な供給者によるパイロットプラントで試行されたAIガイドのプロセスフィードバックの統合は、さらに一貫性と生産性を高めることが見込まれています。今後数年間では、軽量合金や高強度鋼との互換性を考慮して設計されたコーティングの採用が広がることが予想され、これは自動車産業の電動化と持続可能性へのシフトに呼応したものです。
全体として、亜鉛-ニッケル層状コーティングは、環境的な必然性と、Atotech、MacDermid Alpha、DuPontのような業界リーダーからの技術革新の進行によって、2025年以降も対腐食ソリューションの最前線であり続けることが期待されています。
市場規模と予測:2029年までの世界的および地域的需要
亜鉛-ニッケル層状コーティングエンジニアリングの市場は、優れた耐腐食性と環境規制の遵守を求める自動車、電子機器、エネルギー、および重機部門の需要の高まりにより、堅調な成長を見せています。2025年現在、北米、ヨーロッパ、アジア太平洋地域全体で生産能力と採用率が拡大しており、主要な業界プレイヤーは、進化する規制要件や性能基準に応じて高度な製造および仕上げ技術に投資しています。
ヨーロッパでは、REACH規制による伝統的なカドミウムおよび六価クロム仕上げからの移行が進み、亜鉛-ニッケルコーティングの採用が加速しています。AtotechやMacDermid Alphaのような主要供給者は、より高いスループットと環境影響の低減を目的とした新しい施設のアップグレードやプロセス革新に投資しています。ヨーロッパ市場は、今年から2029年までの中位数桁の複合年間成長率(CAGR)の予測され、軽量化や延長されたサービス間隔を重視する自動車OEMや部品供給者からの安定した需要を反映しています。
北米は主要市場の一つであり、アメリカ合衆国とメキシコが自動車、農業機器、産業ファスナーのセクターでの採用を促進しています。A+ Industrial CoatingsやPrestige Coatingなどの主要メーカーは、電気自動車(EV)部品やインフラにおける腐食保護の改善を求めるOEMの指示に応じて、亜鉛-ニッケルコーティングラインの拡張を進めています。この地域は、インフラ投資と厳しい環境政策によって、安定した成長の軌道を保つと予測されています。
アジア太平洋地域は、中国、日本、韓国主導で、2029年までに最も高い成長率を記録すると期待されています。この地域は急成長する自動車生産、急速に近代化を進める製造基盤、及び拡大するエレクトロニクス生産から恩恵を受けています。Nippon Paint Holdingsや東京金属工業のような企業は、国内市場および輸出市場を対象とした自動化された高ボリュームのメッキラインを提供する亜鉛-ニッケルコーティング機能を拡大しています。
世界的に、亜鉛-ニッケル層状コーティングエンジニアリング市場は、2029年までに重要なボリュームのベンチマークを超えると予測されており、これには有害物質に関する規制の厳格化、ライフサイクルコストに対する意識の高まり、堆積技術に関する継続的な技術革新が寄与しています。今後数年間では、能力拡張の継続、デジタルプロセス制御のより広範な統合、および特定の業界ニーズに合わせた新しい合金配合が見られるでしょう。
競争環境:主要企業と戦略的パートナーシップ
2025年の亜鉛-ニッケル層状コーティングエンジニアリングの競争環境は、確立された表面処理の専門家、グローバルな化学メーカー、自動車サプライチェーンのリーダーが存在することによって特徴付けられています。これらの企業は、高度な合金の配合、自動メッキプロセス、持続可能性や腐食抵抗の改善を目指すパートナーシップを通じて革新を推進しています。環境規制の厳格化に伴い、自動車や重工業セクターがより長持ちする高性能のコーティングを求めていることから、業界のプレイヤーは、研究開発や戦略的な提携にますます投資しています。
Atotech、MacDermid Alpha、otechのような主要業界リーダーは、OEMやTierサプライヤーに対して独自の亜鉛-ニッケルの化学物質やターンキーのメッキソリューションを提供し続けています。例えば、Atotechは、そのTricotectおよびZintek製品ラインを拡張し、腐食性能に関する自動車OEM基準を遵守するとともに、高い堆積効率を強調しています。一方、MacDermid Alphaは、グローバルなプレゼンスを活かし、自動車用ファスナーやシャシー部品に特化した統合型亜鉛-ニッケルコーティングシステムを提供しています。
戦略的パートナーシップや技術的提携は、この競争環境において不可欠です。特に、化学ソリューションプロバイダーと自動化設備メーカーとの協力が進んでおり、高スループットかつ環境に優しい亜鉛-ニッケルラインの展開がスムーズになっています。例えば、Galvatekは、自動化された表面処理プラントの専門家として、航空宇宙や防衛のクライアント向けにターンキー亜鉛-ニッケルメッキシステムを提供するために、化学供給者としばしば提携しています。
持続可能なソリューションに対する需要の高まりは、六価クロムフリー、REACH準拠、低廃棄プロセス基準を満たすことを目的とした提携を促進しています。Volkswagen AGのような大手自動車メーカーは、環境への影響を軽減しつつ部品の寿命を延ばす次世代亜鉛-ニッケルソリューションの共同開発に向けて、コーティング技術プロバイダーと積極的に連携しています。
今後は、企業が知的財産を確保し、新しい地域市場へのアクセスを獲得し、応用分野を多様化しようとする中で、市場はさらなる統合へ向かうことが予想されます。アジアのサプライヤーの参入や、ヨーロッパおよび北米のプレーヤーが電気自動車や再生可能エネルギーのサプライチェーンへ進出することで、今後数年で競争が激化する可能性があります。自動化、デジタル品質監視、環境に優しいプロセス化学への継続的な投資が見込まれ、業界リーダーが変化する技術的および規制要件に対処するための新たなパートナーシップを形成することが期待されています。
自動車および航空宇宙の需要:セクター特有の成長要因
自動車および航空宇宙産業は、2025年から今後数年間にわたり、亜鉛-ニッケル層状コーティングエンジニアリングの重要な駆動要因であり続けます。軽量構造、電動化、および耐腐食性能の向上が、表面処理技術の基準を引き上げ続けています。特に層状またはデュプレックス構造の亜鉛-ニッケルコーティングは、従来の亜鉛メッキよりも最大8倍優れた腐食保護を提供し、高温および化学に対する耐性を高めながら、ますます好まれるようになっています。
自動車セクター内では、OEMやサプライヤーが重要なファスナー、ブレーキ部品、燃料系部品、電気自動車(EV)バッテリーケースに亜鉛-ニッケルコーティングの採用を強化しています。EUの廃棄物としての自動車指令や六価クロムに関する規制の高まりが、環境に優しく、耐久性のある電気メッキコーティングへの移行を促進しています。ZF Friedrichshafen AGやRobert Bosch GmbHなどの主要自動車サプライヤーは、耐腐食保証や持続可能性の基準を満たすために、従来のコーティングを先進的な亜鉛-ニッケルソリューションに置き換えることを公言しています。
航空宇宙用途では、重量削減、ガルバニック互換性、過酷な条件下での信頼性が重要であり、エンジニアリングされた亜鉛-ニッケル層の需要が高まっています。航空機メーカーやそのTierサプライヤーは、ファスナー、着陸装置部品、油圧フィッティングに対して亜鉛-ニッケルを指定し、通常はパッシベーションやトップコートを組み合わせた多層システムの一部として使用されます。GalvatekやSocomoreなどの企業は、航空宇宙クライアントに要求される厳しい許容誤差やトレーサビリティに対応するために、プロセスオートメーションや品質管理システムをさらに開発しています。
技術の観点からは、浴槽化学、パルスメッキ、およびマイクロ層の進展が、より均一な堆積や適応した合金組成を可能にしています。Atotechのような設備プロバイダーによる持続的な投資は、自動車および航空宇宙生産ラインでのスケーラブルな高スループットの設置を支援しています。特に、コーティング供給者とOEM間の共同研究開発の取り組みが、三価のパッシベーションや鉛フリー化学の移行を加速させており、これは規制および企業の持続可能性の目標を反映しています。
今後も、亜鉛-ニッケル層状コーティングエンジニアリングの見通しは堅調です。モビリティの電動化の継続、部品の寿命延長の必要性、厳しい規制枠組みが新たなプロセス開発や能力拡張を促進すると期待されています。業界リーダーは、亜鉛-ニッケルの対腐食コーティングのシェアが徐々に増加し、商業車両やe-モビリティプラットフォームなど、隣接したモビリティセグメントへの採用が広がると予想しています。
イノベーションパイプライン:特許、R&D、出現するプロセス
2025年の亜鉛-ニッケル層状コーティングエンジニアリングにおけるイノベーションパイプラインは、活発な研究開発活動、動的な特許環境、性能および規制遵守のために最適化された高度なプロセスの出現によって特徴付けられています。自動車、建設、電子機器セクターは、高性能で耐腐食性のコーティングの需要を引き続き推進しており、材料科学者やコーティングメーカーは合金配合、プロセスオートメーション、環境管理の取り組みに注力しています。
最も注目されるトレンドの一つは、三価パッシベーションシステムおよびシアン化物フリーのメッキ浴への移行です。特に欧州および北米における厳しい環境規制への対応として、AtotechやMacDermid Alphaなどのメーカーは、高い耐腐食性と低危険廃棄物の生成を兼ね備えた独自の亜鉛-ニッケルプロセスを開発しています。例えば、Atotechの革新は、自動車用ファスナー向けに高ニッケル(12~16%)合金に焦点を当てており、塩霧試験で赤錆に対して1,000時間を超える耐性を示し、REACHおよびRoHS指令を遵守しています。
特許環境には、層状および複合亜鉛-ニッケルコーティングに関連する出願が steadily 繁忙を感じています。最近の開示は、多層アプローチ ─ 機能的にグレーディングされたコーティングやデュプレックス構造 ─ などを強調し、柔軟な犠牲亜鉛層を硬いニッケルリッチ拡散バリアと組み合わせることによって、特定の応用における応力からの耐性を提供しています。この工学は、海洋環境から自動車アセンブリの下回りまでの特定の適用ストレスに合わせた性能を実現します。OC OerlikonやNippon Paint Holdingsのような企業がこの分野の知的財産を追求しており、業界の競争の激しさを象徴しています。
研究開発の取り組みは、プロセスオートメーションやデジタル化にも及んでいます。インライン品質監視、リアルタイムの浴槽組成分析、AI駆動のプロセス制御が、最先端のメッキラインにおいて標準化されつつあり、ElaquaやAtotechからの技術提供に見られる通りです。これらの技術は、再現性やコスト効率を保証することによって、複雑な層状コーティングの商業導入を加速させることが期待されています。
今後数年間を見込むと、業界の見通しは、さらに高いパフォーマンス基準 ─ 例えば電動車両部品や軽量合金への耐腐食保護 ─ を求める必要性によって形成されます。OEM、化学供給者、大学の研究所間の継続的な共同作業により、ナノ構造亜鉛-ニッケルコーティング、スマート自己修復層、そして添加製造基板と互換性のあるコーティングに関する新しい特許出願や商業化が期待されています。持続可能性とデジタル製造を中心に据えた中で、亜鉛-ニッケル層状コーティングエンジニアリングは、2025年以降も急速に進化する準備が整っています。
持続可能性と規制の変化:環境およびコンプライアンス要因
亜鉛-ニッケル層状コーティングは、その優れた耐腐食性と、従来のカドミウムや高亜鉛の代替品に比べて環境に優しい特性から、表面工学の焦点となっています。2025年現在、持続可能性と規制の遵守は、この分野の主要な駆動要因となっており、有害物質やライフサイクル排出に関する世界基準が厳格化されている影響を受けています。
欧州連合によるREACH規制および廃棄物としての自動車指令(ELV)の施行は、現在も進行中であり、自動車や電子機器製造における六価クロムやその他の有害物質の使用を制限しています。そのため、OEMやTierサプライヤーは、古い化学物質に関連するコンプライアンスリスクなしに高性能を提供する亜鉛-ニッケルコーティングの採用を加速させています。主要なコーティングプロバイダーであるAtotechやMacDermid Alphaは、亜鉛-ニッケルプロセスのポートフォリオを拡大しており、両者を自動車および産業ファスナー市場に適応させようとしています。
北米では、最新のASTM基準や、塩霧寿命の延長、環境影響の低減に対する顧客要件の高まりにより、状況が似ています。DuPontやAker BPは、ライフサイクル評価やカーボンフットプリントが調達決定に通常取り入れられるようになった offshore やエネルギー用途における持続可能なコーティングの重要性を強調しています。
最近のデータは、トリバレントクロメートまたはクロムフリーのパッシベーションシステムを使用した亜鉛-ニッケルコーティングの市場全体での増加を示しており、重金属への依存を減らし、適用中の労働者の安全性を向上させています。例えば、Atotechの最新の製品ラインは、エネルギー効率、廃棄物生成の低減、閉ループ水再利用を強調しており、EUおよび米国の環境指令にaligned しています。
今後数年間では、国連の水銀に関する水俣条約やPFASやその他の持続性のある化学物質に対する制限の強化が予想されており、業界はさらなる環境に優しい配合へと進むことになります。また、欧州連合における循環型経済やデジタル製品パスポートの台頭は、バリューチェーン全体でコーティング化学の透明な追跡を要求し、持続可能な亜鉛-ニッケルシステムへの移行をさらに促進することになるでしょう。
全体として、亜鉛-ニッケル層状コーティングエンジニアリングは、規制の統一、顧客の持続可能性の義務、および主要な供給者による継続的な革新によって堅調な成長の位置にあります。環境に優しい、法令遵守の技術に投資する企業は、世界的な環境期待の高まりに応じて競争優位を維持する可能性が高いでしょう。
サプライチェーンと原材料の課題
亜鉛-ニッケル層状コーティングのサプライチェーンと原材料の状況は、業界が2025年に入るにつれて重要な変化を迎えています。主な原材料である高純度亜鉛とニッケルは、地政学的要因、エネルギーコスト、変化する環境規制のために、供給と価格が変動しています。最近の数年間、特にニッケル市場は、バッテリーセクターからの需要の増加や主要生産者からの供給制約により、特に不安定です。この変動は、通常亜鉛-ニッケルコーティング全体のコスト構造に直接影響を与えます。ニッケルは合金の10~15%を構成しますが、材料費の60%を占める場合もあります。
UmicoreやBASFなどの主要供給者は、表面技術におけるニッケルの安定供給を確保することの課題を公に認めており、バリューチェーンのリサイクルと循環性の改善に向けた継続的な投資を行っています。これらの取り組みは、原材料の圧力を部分的に緩和することが期待されていますが、2025年時点での主要ニッケル源からの完全な切り離しは難しい状況です。
環境規制は、従来の鉱山および精製業務にさらなる圧力を加えています。EUのグリーンディールや米国のインフレ抑制法は、責任ある調達へと向かう動きを加速させ、サプライチェーンの透明性に対する監視を強化しています。このため、OEMやコーティング施工業者は、原材料供給者からのサプライチェーン遵守の証明や書類を求めるようになっています。これは、Aker SolutionsやTechnip Energiesの最近の持続可能性報告での政策更新によって強調されています。
新たな課題として、コーティング用途と急成長する電気自動車バッテリーセクターとの間におけるニッケルの競争が挙げられます。この競争は周期的な供給不足を引き起こすことがあり、一部の表面工学企業は、全体的なニッケル依存度を減らすために代替合金の配合や多層コーティングシステムを探求しています。例えば、Atotechは、原材料制約に対する対応として、ニッケル含有量の少ないハイブリッドコーティングにおける積極的な研究開発を行っています。
今年の短期見通しは、ニッケル供給は引き続き厳しく、亜鉛はより安定しているものの、その他の産業セクターからの競争が激しくないためより安定しているというものです。ただし、デュアルソーシングやリサイクルの増加、サプライヤーとの関係を密接にするなど、サプライチェーンの弾力性を高める戦略が亜鉛-ニッケルコーティング業界全体で優先されることが期待されています。デジタルトレーサビリティや循環型経済に関する取り組みに投資する企業は、今後数年にわたって進化する原材料状況をうまく切り抜けられる可能性が高いでしょう。
顧客の採用:OEM、Tier 1、およびアフターマーケットの視点
亜鉛-ニッケル層状コーティングの採用は、自動車、重機および産業セクターにおいて顕著な増加を見せており、これはますます厳しくなる耐腐食基準および進化する持続可能性義務によって推進されています。原材料製造者(OEM)、Tier 1サプライヤー、およびアフターマーケットはそれぞれ異なる優先事項を持って亜鉛-ニッケルコーティングにアプローチしていますが、すべてはそのパフォーマンスと規制への整合性を評価しています。
OEMは、特に環境および性能規制が厳しい地域で亜鉛-ニッケルコーティングの推進の先頭に立っています。特にヨーロッパのOEMは、それが大手自動車ブランドや部品メーカー間で広がる様子が顕著であり、これは通常720時間を超える耐腐食保護と、六価クロムプロセスからの移行によるものです。DuPontやZEISS(品質検査とプロセス制御)のような企業は、OEMの高度なプロセス統合能力を支援しています。軽量化および電動化が2025年まで続くにつれて、亜鉛-ニッケルコーティングの混合金属との互換性や水素脆化に対する感受性は大きな利点です。
Tier 1サプライヤーは、複雑な組立品やサブコンポーネントを担当した上で、製品のエコシステムをOEMの要求に緊密に整合させるため、亜鉛-ニッケルの自動メッキラインを統合し、プロセスのトレーサビリティに投資しています。Atotechのような企業は、Tier 1がOEMの仕様や持続可能性の要件を満たすために、ターンキーのメッキシステムや化学ソリューションを提供しています。Tier 1はまた、最新の亜鉛-ニッケル浴のプロセスの一貫性を活用し、複雑な幾何学においても高い均一性のコーティングを実現できるため、電動ドライブトレインやシャシーコンポーネントにおいて重要な要素となります。
アフターマーケットにおいては、採用はより多様ですが、特に延長された製品ライフサイクルと腐食に関連する保証請求が主要な関心事である地域では、2025年まで安定して成長すると見込まれています。アフターマーケットのプレイヤーは、OEM慣行を模倣する形で重要なファスナー、ブレーキ部品、サスペンション要素に亜鉛-ニッケルの仕上げを指定する傾向が高まりつつあります。Wynn’sやBoschなどのサプライヤーネットワークは、エンドユーザーやフリートオペレーターの長いメンテナンスインターバルに対する需要に応じて、コーティングされた製品ラインを拡大しています。
今後、亜鉛-ニッケル層状コーティングエンジニアリングの見通しは堅調です。規制の圧力が強まる中、循環経済の原則が広がることで、すべての顧客セグメントでの採用曲線は急勾配になると予測されています。自動車業界動作グループ(AIAG)などの主要業界団体は、高性能かつ環境に優しい表面コーティングの実装をさらに促進するために、推奨プラクティスやサプライチェーン基準を更新しています。
今後の展望:破壊的技術と戦略的推奨事項
亜鉛-ニッケル層状コーティングは、2025年およびその後の数年間で、規制圧力、自動車業界の電動化への移行、そして持続可能性への重視という要因によって大きな進化を遂げることが期待されています。これらのコーティングは、従来の亜鉛メッキと比較して優れた耐腐食性が確立されており、自動車、航空宇宙、重機の分野で重要な役割を果たしています。
鍵となる破壊的なトレンドは、三価パッシベーションおよびクロムフリーシーリングシステムの採用であり、これは六価クロムに関連する環境および健康上の懸念を解決するためのものです。AtotechやDuPontなどの主要な表面処理プロバイダーは、有害物質を排除し、メッキ効率および層の均一性を向上させる次世代の亜鉛-ニッケル浴化学に投資しています。これらの進歩は、メーカーやOEMがREACHおよびELVの指令に準拠することを求める中で、主流化することが期待されています。
別のイノベーションの領域は、スマート製造とデジタルプロセス制御の統合です。AZ Electronic MaterialsやZEISSのような企業は、プロセスのリアルタイムの調整を可能にする精密監視ツールや自動化された品質保証システムを開発しています。この変化は、コーティングの一貫性を向上させるだけでなく、廃棄物やエネルギー消費を最小限に抑え、世界的な持続可能性の目標に合わせたものです。
特に自動車分野での電動化トレンドは、2025年以降の亜鉛-ニッケルコーティングの仕様を形作ると予想されます。混合材料アセンブリや軽量合金の使用が増加する中で、堅牢な接着、低接触抵抗、およびアルミニウムとの高い互換性を提供するコーティングが求められています。これは、OEMやBosch、Schaefflerなどのサプライヤーと活発に連携して、e-モビリティのパワートレインやシャシーアプリケーション向けに先進的な亜鉛-ニッケルソリューションを指定していることにも表れています。
今後の業界のステークホルダーに対する戦略的推奨事項としては、腐食保護を自己潤滑や抗菌層と組み合わせた多機能コーティングシステムのための研究開発に投資すること、環境影響を低減するためのクローズドループ化学管理のためのパイロットプログラムを拡大すること、デジタル化されたメッキラインの導入を加速するための産業間パートナーシップを促進することが挙げられます。規制環境が厳しさを増し、最終ユーザーの要求が進化していく中で、先進的な亜鉛-ニッケル工学を積極的に統合する企業は、この十年の後半においてコーティング市場で競争優位を確保することになるでしょう。
出典および参考文献
- Atotech
- Norm Fasteners
- AWA
- DuPont
- Nippon Paint Holdings
- otech
- Volkswagen AG
- ZF Friedrichshafen AG
- Robert Bosch GmbH
- Socomore
- Aker BP
- Umicore
- BASF
- Technip Energies
- ZEISS
- Automotive Industry Action Group (AIAG)
- Schaeffler