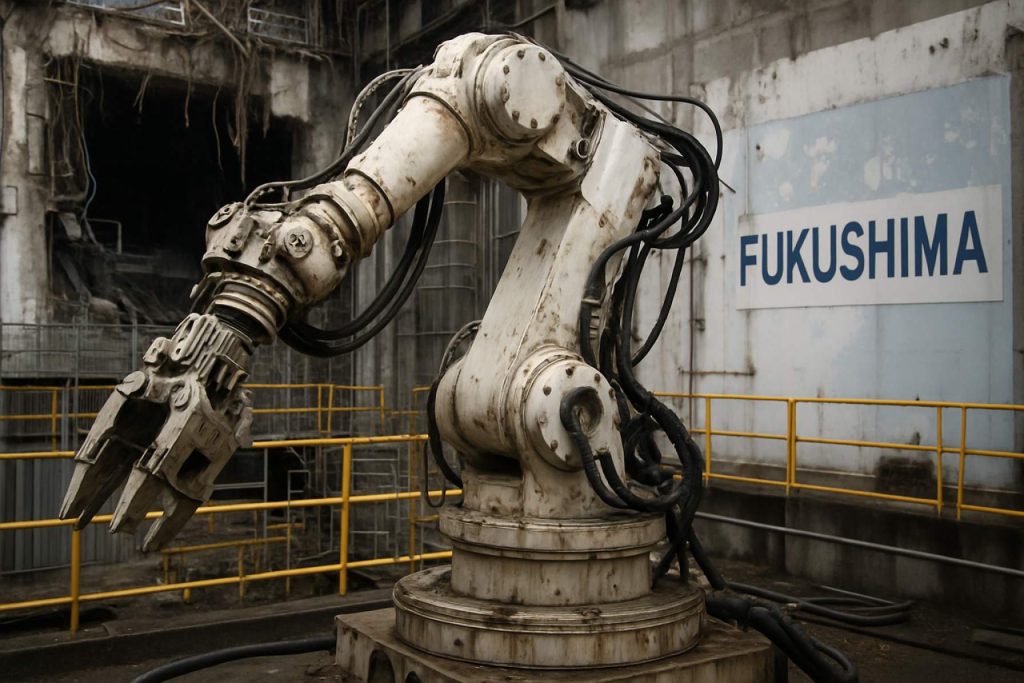
- The Fukushima Daiichi clean-up faces its toughest challenge: removing 880 tons of melted nuclear fuel debris from beneath destroyed reactors.
- A massive 22-meter robotic arm was engineered for this task, but repeated technical setbacks and delays have raised doubts about its effectiveness.
- Despite over $53 million invested, simpler alternative methods have outperformed the robot in crucial test runs.
- Persistent problems, like mechanical failures and cable damage, have slowed progress, emphasizing the complexities of nuclear decommissioning technology.
- The situation highlights a key lesson: successful disaster recovery depends on adaptability, humility, and the willingness to change strategies—not just advanced machinery.
A cavernous gloom lingers beneath the No. 5 reactor at the battered Fukushima Daiichi nuclear complex—where a machine, both monumental in size and weight, idles in hope and uncertainty. This robotic arm, stretching 22 meters long and flexing through 18 intricate joints, stands as the latest, most audacious attempt by engineers to exhume the dangerous legacy of the 2011 nuclear meltdown.
In the bowels of the plant, a space barely taller than a crouching adult offers a grueling obstacle course for this high-tech lifeline. To begin its mission, operators must guide the 4.6-ton behemoth—its tip only 40 centimeters tall—through an opening barely wider than a car tire. Even a minor miscalculation could send it colliding with fragile equipment, risking irreparable setbacks in a process watched with global attention.
The stakes could not be higher: beneath three destroyed reactors, an estimated 880 tons of melted fuel debris awaits retrieval, the most intractable hurdle in a clean-up that has captured the world’s concern. Engineers, supported by more than $53 million of public funds, and the expertise of Mitsubishi Heavy Industries and leading British nuclear specialists, spent years crafting the machine. Yet, for all its promise, the arm remains untested in the most challenging conditions—beset by cable failures, mechanical stumbles, and the unpredictable toll of high radiation.
Delays and doubts have mounted. Despite the years and investment, the robotic arm has missed deadline after deadline. During trial runs, simpler, reliable alternatives took over, successfully collecting debris samples where the hulking mechanical marvel could not. Each test revealed fresh complications—aged wiring, misfiring mechanisms, a structure that swayed unsteadily at full stretch.
Yet, hope persists. Team leaders attack each new challenge with methodical determination. When the arm grazed structures during tests, subtle adjustments followed. When cables frayed from long dormancy, they disassembled the machine, resolved to learn and adapt. Insiders track every wire and joint with the persistent, almost ritualistic patience that has come to define post-disaster recovery in Japan.
As 2025 approaches, the question looms: Will this robotic giant finally break its cycle of delay, or be left to gather dust, eclipsed by nimbler solutions? Industry voices warn against blind faith in plans that no longer serve the urgent realities. In crisis management—a lesson Fukushima has taught the world repeatedly—bravery sometimes means knowing when to rewrite the playbook.
The saga of the Fukushima robotic arm tells a broader story. Under the shadow of catastrophe, innovation is forced to wrestle with imperfection. Japan’s ongoing struggle with decommissioning its reactors is not just a feat of engineering, but an enduring test of humility and resolve. Whatever the future holds for this mechanical titan, one truth prevails: successful recovery from disaster is found not in stubborn adherence to plans, but in the courage to keep learning, adjusting, and—when needed—changing direction.
For more on the world’s evolving energy challenges and advances, visit Reuters or BBC.
Key insight: At the heart of Fukushima’s cleanup is not just technology, but a testament to adaptability—reminding us that human ingenuity finds progress in each patient, corrective step forward.
Inside Fukushima’s High-Stakes Clean-Up: Why a Giant Robot Arm Might Not Be the Ultimate Solution
Deep Dive: Uncovering What Fukushima’s Robot Arm Story Missed
The ambitious robotic arm developed for the Fukushima Daiichi nuclear plant is emblematic of Japan’s struggle to tame one of the world’s most hazardous decommissioning challenges. While the original article captured the robot’s daunting task and setbacks, much remains beneath the surface, both technically and contextually. Here’s what experts, industry observers, and global trends tell us about the fate of the Fukushima clean-up—and what it means for the future of nuclear decommissioning.
—
Additional Facts & Industry Context
1. Extreme Radiation Remains a Major Limitation
– The robotic arm must operate in environments with radiation levels that would incapacitate conventional machinery within hours or days (source: [World Nuclear Association]World Nuclear Association).
– Engineers use shielded electronics, lead barriers, and remotely operated systems to extend functionality in these conditions.
2. Why Can’t People Just Go In?
– Human entry into areas beneath reactors 1, 2, and 3 is physically impossible due to lethal radiation doses—exposure for even a few minutes could be fatal.
– Past attempts at inspection relied on small robots, or even drones, many of which failed after brief use due to the hostile environment.
3. Variety of Robotics in Play—Not Just One Arm
– TEPCO, Japan’s power utility, has tested various robots: snake-like probes, crawler bots, and even submersible ROVs to scout, sample, and map radioactive fuel debris.
– No single machine is expected to complete the job; most experts predict a suite of modular robots will work together, each specialized for task (Reuters, 2024).
4. International Collaboration and Lessons Learned
– British, French, and American nuclear experts have regularly consulted on the project, sharing decommissioning know-how from other reactor disasters (like Chernobyl and Three Mile Island).
– Industry insiders agree that only by sharing data transparently—and admitting missteps—can similar crises be better managed in the future ([BBC]BBC).
5. Cost and Timeline Escalation
– Initial projections suggested most melted debris would be removed by 2040–2051; however, recent reports warn these targets may slip by years or decades due to technical bottlenecks and safety checks.
– The total cost for decommissioning and compensation is expected to exceed $200 billion USD, making this the most expensive nuclear clean-up ever attempted (Asahi Shimbun, 2023).
—
How-To & Life Hacks: What Makes a Successful Nuclear Clean-Up Robot?
Key Features in an Effective Nuclear Decommissioning Robot:
– Radiation-hardened electronics: Ensures longer operational lifetime in high-radiation zones.
– Highly flexible joints: Allows navigation in cramped, debris-filled spaces.
– Remote manual override: Critical for intervention if autonomy fails.
– Modular construction: Easy in-place repairs and adaptation with new tools or sensors.
Safety Tips for Robotic Operation:
1. Continuous remote monitoring for anomalous readings.
2. Redundant data links to prevent communication dropouts.
3. Scheduled inspection/maintenance after each mission inside reactor.
—
Market & Industry Insights
– Decommissioning robotics is a fast-expanding sector: Global nuclear clean-up robotics market expected to surpass $2.8 billion by 2030 (Statista, 2023).
– Japan has become the world’s foremost testbed for disaster robotics, driving R&D not just for nuclear, but for future applications in oil, gas, mining, and space exploration.
– Policy Shift: Japanese public’s concern with nuclear energy safety is driving demand for more transparency and proactive safety technology investments (World Nuclear News, 2024).
—
Reviews & Comparisons
| System | Strengths | Weaknesses | Cost |
|——————–|————————————–|—————————|—————|
| Mitsubishi Arm | Large payload, flexible joints | Bulky, maintenance-heavy | $53 million+ |
| Crawler ‘Scorpion’ | Compact, agile | Limited reach, fragile | $7 million |
| Submersible Drone | Good for underwater debris | Limited manipulation | $3M–$8M |
Expert Opinion: “Fukushima’s clean-up will ultimately require a hybrid approach—including tried-and-true remote handlers and newer, smarter robots, not just one mega-machine.” (Dr. Naoko Iwata, University of Tokyo Robotics Lab)
—
Controversies & Limitations
– Delays Spark Public Criticism: Repeated timeline extensions and technical mishaps have raised questions about government oversight and transparency.
– Sustainability Concerns: Safe disposal of retrieved radioactive debris remains unresolved—temporary storage fills up faster than anticipated.
– Security Considerations: Proper cybersecurity protocols must protect remote robotic operations from hacking or sabotage.
—
Real-World Use Cases & Pros and Cons Overview
Pros:
– Reduces human risk.
– Can work in environments where nothing else survives.
– Advances technology for future disasters.
Cons:
– Expensive to build and maintain.
– Prone to failure in ultra-radiated, cluttered spaces.
– Delays impede overall site recovery and local revitalization.
—
Most Pressing Reader Questions, Answered
Q: Will the robotic arm ever be used for widespread debris removal?
A: Experts now believe it’s unlikely to be the sole solution. Instead, its technology will inform the next generation of hybrid, task-specific robots.
Q: What happens to the retrieved melted fuel?
A: It’s stored onsite in shielded, dry casks until a long-term waste repository is operational—a challenge Japan has not solved.
Q: Is there a risk of another major radioactive leak?
A: Current containment is stable, but risks remain—especially if unplanned events (natural disasters) disrupt debris removal.
—
Actionable Recommendations & Quick Tips
– For policymakers and engineers: Plan for modularity and adaptability; overdesigning for one task can delay the overall mission.
– For communities near nuclear sites: Demand regular, transparent reporting from government and plant operators.
– For the public: Stay informed through reliable outlets like [Reuters](https://www.reuters.com) and [BBC](https://www.bbc.com); Japan’s experience will shape nuclear policy worldwide.
Final Word
Fukushima’s robotic recovery drives home a vital lesson: In the face of disaster, adaptability, collaboration, and realistic planning matter more than technical bravado. As nuclear decommissioning becomes a global necessity, future solutions will likely be more agile, integrated, and—critically—open to change.
Key takeaway: Robotics is transforming nuclear safety, but human adaptability and learning remain the ultimate tools in any crisis.