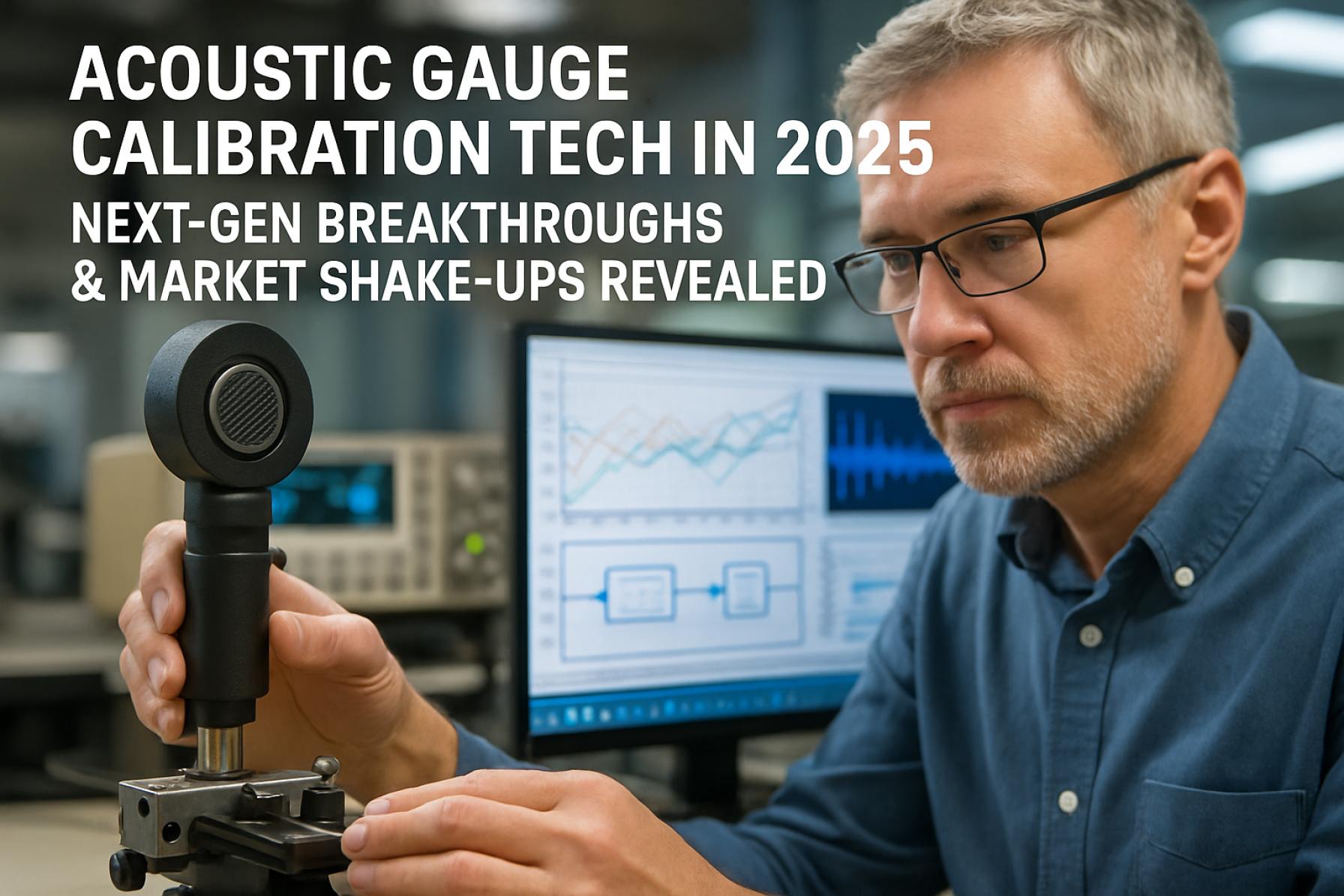
Table of Contents
- Executive Overview: Market Size and 2025–2030 Forecasts
- Emerging Acoustic Calibration Technologies: Trends and Innovations
- Regulatory Landscape and Industry Standards (ASME, IEEE, ISO)
- Key Manufacturers and Technology Providers: Competitive Analysis
- Integration with IoT, AI, and Automation in Calibration Workflows
- Sector Applications: Oil & Gas, Power Generation, Chemicals, and More
- Sustainability and Energy Efficiency in Calibration Solutions
- Regional Market Dynamics: North America, Europe, Asia-Pacific, and Beyond
- Investment, M&A, and R&D Pipelines: 2025 and Future Outlook
- Challenges, Disruptors, and Opportunities Shaping the Next 5 Years
- Sources & References
Executive Overview: Market Size and 2025–2030 Forecasts
The global market for Acoustic Gauge Calibration Technologies is experiencing steady growth, driven by increased adoption across sectors such as oil and gas, environmental monitoring, and industrial process control. As of 2025, the demand for precise and reliable calibration of acoustic gauges—used to measure parameters such as liquid level, flow, and well integrity—has surged due to regulatory pressures and the need for higher operational efficiency. Major industry players are expanding their service portfolios, integrating advanced digital calibration tools and automated processes to enhance accuracy and reduce downtime.
Notable manufacturers and calibration service providers, including Baker Hughes and Halliburton, have invested in developing next-generation calibration solutions, leveraging IoT connectivity and cloud-based data management to enable real-time monitoring and remote diagnostics. These innovations align with broader trends in digital transformation and predictive maintenance, providing operators with actionable insights and minimizing risks associated with instrument drift or failure.
The market’s expansion is further supported by organizations such as the American Petroleum Institute (API), which continues to update calibration standards and best practices, prompting end users to upgrade legacy systems. In 2025, increased capital expenditure from upstream and midstream oil and gas operators is expected to fuel market growth, especially in North America, the Middle East, and Asia-Pacific. Additionally, manufacturers like Emerson and Siemens are focusing on modular calibration platforms that can be rapidly deployed and customized for diverse industrial environments.
Looking ahead to 2030, the outlook remains positive. Industry adoption of automated calibration and self-diagnostic technologies is projected to accelerate, supported by ongoing R&D and collaboration between equipment manufacturers and standards organizations. The integration of AI-driven analytics and enhanced sensor miniaturization are anticipated to open new application areas, particularly in remote or hazardous locations where traditional calibration methods are impractical.
Overall, the Acoustic Gauge Calibration Technologies market is forecast to achieve a compound annual growth rate (CAGR) in the mid-single digits over the next five years. Growth will likely be strongest in sectors with stringent regulatory requirements and where digitalization initiatives are well advanced, positioning leading suppliers—including Baker Hughes, Halliburton, Emerson, and Siemens—at the forefront of innovation and market share expansion.
Emerging Acoustic Calibration Technologies: Trends and Innovations
Acoustic gauge calibration technologies are rapidly evolving in response to the increasing demands for higher precision, automation, and traceability in industrial and research applications. As of 2025, several key developments are shaping the landscape of acoustic calibration, particularly in sectors such as environmental monitoring, medical diagnostics, and non-destructive testing.
One of the most notable trends is the advancement of automated and digital calibration systems. Companies such as Brüel & Kjær have introduced integrated calibration workstations capable of automating the entire process, from signal generation to data logging. These systems reduce human error and significantly improve throughput, addressing the needs of laboratories handling high volumes of acoustic sensors or microphones. The push toward automation is further supported by the adoption of cloud-based data management, ensuring secure record-keeping and facilitating remote audits for compliance purposes.
Recent years have also seen the integration of digital signal processing and AI-driven algorithms to enhance the accuracy and repeatability of calibration routines. For example, NTi Audio has implemented advanced calibration algorithms in their solutions that compensate for environmental variations such as temperature and humidity, ensuring consistent results across different operating conditions. This is particularly beneficial in emerging fields like wearable medical devices and smart infrastructure, where sensors are deployed in diverse and sometimes unpredictable environments.
In parallel, the industry is focusing on the traceability of acoustic calibration to international standards. Organizations such as Physikalisch-Technische Bundesanstalt (PTB) are collaborating with manufacturers to establish primary and secondary calibration methods that support the latest IEC and ISO standards. This collaboration ensures that new calibration instruments are not only technologically advanced but also compliant with the rigorous requirements of regulatory bodies.
Looking ahead, the next few years are expected to bring further miniaturization and integration of calibration modules directly into measurement devices, enabling real-time, self-calibrating systems. The adoption of MEMS-based acoustic sensors, along with digital calibration protocols, is likely to accelerate, driven by manufacturers such as GRAS Sound & Vibration. These innovations will play a crucial role in meeting the evolving demands of applications ranging from autonomous vehicles to smart city monitoring, solidifying acoustic gauge calibration as a foundational technology for the digital age.
Regulatory Landscape and Industry Standards (ASME, IEEE, ISO)
The regulatory landscape for acoustic gauge calibration technologies in 2025 is increasingly shaped by the adoption of rigorous international and industry-specific standards. Organizations such as the American Society of Mechanical Engineers (ASME), the Institute of Electrical and Electronics Engineers (IEEE), and the International Organization for Standardization (ISO) play a pivotal role in defining the calibration methodologies and ensuring consistent measurement accuracy across sectors.
ASME continues to update its standards related to pressure and flow measurement, which often reference the calibration of acoustic gauges used in industrial applications. In 2024, ASME reaffirmed the importance of traceable calibration for acoustic devices as outlined in their Boiler and Pressure Vessel Code and the PTC 19.3 TW-2016 standard for thermowell testing, which influences the use and verification of acoustic gauges in harsh environments (ASME).
IEEE, through its Instrumentation and Measurement Society, regularly reviews and updates standards that impact the calibration of acoustic sensors and gauges. IEEE Standard 1451, for example, provides a framework for smart transducer interface, which includes recommendations for calibration data formats and protocols for acoustic instruments. In 2025, the working groups are focusing on interoperability and cybersecurity in sensor calibration systems, acknowledging the growing use of digital and remote calibration services (IEEE Instrumentation and Measurement Society).
ISO standards, particularly ISO/IEC 17025:2017, remain the global benchmark for calibration laboratories. This accreditation ensures that labs performing acoustic gauge calibration adhere to strict quality management and technical requirements. In 2023 and 2024, ISO technical committees have launched initiatives to address traceability and uncertainty quantification for acoustic measurements, anticipating stricter requirements for calibration documentation and data integrity by 2026 (International Organization for Standardization).
Manufacturers and accredited laboratories are rapidly aligning with these evolving standards. Leading suppliers such as Brüel & Kjær and Norsonic AS have updated their calibration procedures and software tools to comply with the latest ISO and ASME requirements. These companies are also participating in international round-robin tests and proficiency programs to demonstrate the reliability and repeatability of their calibration processes.
Looking ahead to 2026 and beyond, the industry expects tighter integration of digital calibration certificates and real-time compliance auditing, leveraging cloud-based platforms for traceability and remote verification. Standards bodies are also preparing to introduce guidelines that address the calibration of new classes of smart and wireless acoustic gauges, ensuring continued alignment with technological advancements and regulatory expectations.
Key Manufacturers and Technology Providers: Competitive Analysis
The landscape of acoustic gauge calibration technologies in 2025 is characterized by robust competition among established measurement specialists and a wave of innovation driven by increased demand for precision and automation across sectors such as oil and gas, aerospace, and industrial manufacturing. Key manufacturers and technology providers are focusing on integrating digital solutions, automated calibration processes, and advanced acoustic sensor technologies to enhance accuracy, reduce downtime, and support compliance with evolving international standards.
Among the leading players, Brüel & Kjær (a part of HBK) continues to be a dominant force, offering a comprehensive range of acoustic calibrators and reference microphones for both laboratory and field applications. In 2024–2025, Brüel & Kjær has expanded its digital calibration suite, introducing new models with improved environmental compensation and wireless data transfer features, addressing the needs of remote monitoring and IoT integration.
Larson Davis, a division of PCB Piezotronics, remains a key competitor, particularly in portable and automated calibration systems. Its CAL200 and CAL150 acoustic calibrators are widely recognized for their compliance with IEC and ANSI standards. Recent product updates emphasize traceability, ease of use, and integration with cloud-based asset management systems, reflecting broader trends in digital transformation within metrology.
Another significant provider, Grelco, has increased its focus on accredited calibration laboratory services, supporting OEMs and end-users with ISO/IEC 17025-compliant calibration of acoustic gauges. Grelco’s investments in automated calibration rigs and high-precision reference standards signal a move toward higher throughput and reduced human error in routine gauge verification.
In the Asia-Pacific region, Norsonic has advanced its portfolio of sound calibrators, emphasizing compatibility with a wide array of third-party sensors and data acquisition systems. Their recent models incorporate self-diagnostic features and guided calibration workflows, catering to both field engineers and laboratory technicians.
- Brüel & Kjær: Expanded digital calibration tools and wireless data transfer.
- Larson Davis: Cloud-ready, portable calibrators with compliance to global standards.
- Grelco: Automated ISO/IEC 17025-compliant calibration services.
- Norsonic: Self-diagnosing and multi-sensor compatible calibrators.
Looking ahead, competition is expected to intensify as the adoption of AI-driven analytics, remote calibration, and real-time sensor diagnostics becomes mainstream. Manufacturers are likely to pursue further integration with enterprise asset management platforms and expand their service offerings to meet the growing demand for traceable, high-precision acoustic gauge calibration across emerging industrial and environmental applications.
Integration with IoT, AI, and Automation in Calibration Workflows
Acoustic gauge calibration technologies are undergoing significant transformation as they integrate with Internet of Things (IoT), Artificial Intelligence (AI), and automation within calibration workflows. In 2025, this convergence is being driven by the need for higher precision, real-time monitoring, and reduced manual intervention in sectors such as oil & gas, environmental monitoring, and industrial automation.
Leading manufacturers are embedding IoT connectivity directly into acoustic calibration instruments, enabling remote diagnostics, status monitoring, and predictive maintenance. For example, Brüel & Kjær offers digital sound calibrators that can interface with asset management platforms, facilitating automated calibration records and compliance tracking. Such integration helps minimize human error and delivers actionable data to operators in real-time.
The use of AI in acoustic calibration is also gaining momentum. Machine learning algorithms are being applied to historical calibration data to predict drift, optimize recalibration intervals, and flag anomalies before they affect measurement integrity. Companies like NTi Audio are piloting AI-driven analytics in their sound measurement systems, enhancing diagnostics and reducing downtime in calibration processes.
Automation is further streamlining workflows through robotic calibration stations and automated test sequences. Norsonic has introduced solutions where multiple acoustic sensors and gauges can be calibrated simultaneously with minimal operator input, leveraging automated handling and test routines. This improves throughput and ensures consistent calibration quality across large fleets of sensors.
Looking forward, the sector is expected to further integrate cloud-based data storage and digital twins with acoustic calibration systems. This will allow users to model real-world performance, simulate calibration needs, and synchronize field devices with central databases. The trend aligns with broader digital transformation initiatives in process industries and environmental agencies, who are seeking to maximize operational efficiency and regulatory compliance.
By 2026 and beyond, the adoption of standardized IoT protocols and interoperable APIs is anticipated, fostering greater compatibility between calibration devices from different manufacturers. Industry organizations such as OIML are already advocating for harmonized data formats in metrological instrumentation, which will further accelerate the deployment of smart, interconnected acoustic calibration ecosystems.
Sector Applications: Oil & Gas, Power Generation, Chemicals, and More
Acoustic gauge calibration technologies are increasingly integral to critical industrial sectors such as oil & gas, power generation, and chemicals, where precise measurement and monitoring of fluids and gases are essential for operational safety, regulatory compliance, and process optimization. In 2025, adoption and innovation in calibration methodologies are shaped by industry demands for higher accuracy, automation, and digital integration.
Within the oil & gas sector, acoustic calibration is pivotal for downhole measurement tools, including reservoir monitoring and pipeline integrity testing. Leading providers like Halliburton and SLB (formerly Schlumberger) have advanced acoustic calibration solutions for wireline tools, facilitating real-time adjustments and verification of acoustic sensors used in well logging and leak detection. In 2024 and 2025, focus has shifted to remote and automated calibration systems, reducing the need for manual intervention in hazardous environments and enabling predictive maintenance based on acoustic signal analysis.
In power generation, especially in thermal and nuclear plants, the accurate calibration of acoustic flow meters and leak detection systems is crucial for heat rate optimization and early fault detection in steam and gas pipelines. Companies like Emerson are developing digital calibration platforms that utilize cloud connectivity, allowing for routine verification and remote diagnostics of installed acoustic sensors. This trend is forecasted to expand as regulatory scrutiny over emissions and operational safety intensifies globally through 2025 and beyond.
The chemical industry relies on acoustic level gauges and flow meters for process control in high-pressure and corrosive environments. Manufacturers such as Siemens have incorporated AI-driven calibration routines into their acoustic measurement products, enabling adaptive calibration cycles that account for process variations and material buildup. This reduces downtime and enhances measurement reliability, a crucial factor for continuous chemical processing.
Across sectors, there is a marked shift towards smart calibration technologies—including self-diagnosing sensors and automated recalibration protocols. Major instrumentation suppliers like Endress+Hauser are introducing calibration platforms that use digital twins and advanced analytics to simulate sensor drift and schedule proactive maintenance. These innovations are expected to become standard as part of broader digital transformation initiatives in industrial operations through 2026.
Overall, the outlook for acoustic gauge calibration technologies in these industries is one of rapid technological integration, greater automation, and enhanced reliability, with emphasis on remote operation and real-time data analytics to support critical decision-making and compliance goals.
Sustainability and Energy Efficiency in Calibration Solutions
Acoustic gauge calibration technologies are undergoing significant advancements in sustainability and energy efficiency as industry demand grows for more environmentally responsible and cost-effective solutions. In 2025, leading manufacturers and calibration service providers are prioritizing innovations that reduce resource consumption, lower emissions, and enhance operational longevity of acoustic devices.
Modern acoustic calibration systems increasingly utilize closed-loop test chambers and automated signal processing to minimize energy usage while maintaining high precision. For example, Brüel & Kjær has developed calibration solutions that employ highly efficient microphones and power management systems, resulting in lower operational power requirements and less waste heat. The use of advanced digital signal processing (DSP) allows for faster, more accurate calibrations, reducing the need for repeated measurements and thus conserving both time and resources.
Additionally, manufacturers are transitioning toward modular and upgradable calibration hardware. This approach, championed by companies like GRAS Sound & Vibration, extends product lifecycles and reduces the environmental impact associated with frequent equipment replacements. Modular design enables individual components—such as reference microphones or preamplifiers—to be swapped or upgraded without discarding the entire system, aligning with principles of circular economy and e-waste reduction.
Energy-efficient calibration environments are also an area of focus. Many laboratories are implementing smart facility controls and low-energy lighting, while calibration baths and climate chambers are being designed for optimized thermal insulation and minimal standby power consumption. Organizations such as National Institute of Standards and Technology (NIST) are actively researching and publishing on best practices for energy management in metrology facilities, further driving adoption of sustainable practices across the sector.
Looking forward, the adoption of cloud-based calibration management platforms is expected to further enhance sustainability. Remote monitoring and digital record-keeping, as provided by several leading suppliers, eliminate the need for paper-based documentation and reduce travel requirements for on-site service, contributing to lower carbon footprints.
Collectively, these trends indicate a robust outlook for sustainability and energy efficiency within acoustic gauge calibration technologies. As regulatory and customer pressures mount, manufacturers and service providers are expected to accelerate the integration of green technologies and circular economy principles, ensuring that acoustic calibration not only meets technical standards but also aligns with global environmental goals.
Regional Market Dynamics: North America, Europe, Asia-Pacific, and Beyond
The global market for acoustic gauge calibration technologies is evolving rapidly across North America, Europe, Asia-Pacific, and other regions, driven by increasing regulatory demands, advances in sensor technology, and the expansion of industrial applications. As of 2025, regional market dynamics reflect both shared trends and unique local drivers.
North America remains a leader in acoustic gauge calibration, supported by a robust oil and gas sector and stringent safety standards. Major manufacturers and calibration service providers such as Baker Hughes and SLB (Schlumberger) continue to innovate with integrated digital calibration solutions, offering real-time analytics and wireless data transfer. The region’s focus on pipeline integrity and environmental compliance is leading to increased demand for highly accurate and automated calibration systems. The adoption of cloud-based calibration management platforms is also accelerating, enhancing traceability and audit-readiness for clients.
Europe is witnessing growth in acoustic gauge calibration driven largely by the region’s push toward decarbonization and stricter environmental regulations. Companies such as Siemens and Endress+Hauser are integrating smart calibration technologies with IoT connectivity, enabling remote diagnostics and predictive maintenance. The European Union’s emphasis on energy efficiency and industrial digitalization is encouraging the deployment of advanced calibration systems in both process industries and renewable energy sectors. Additionally, collaborations between research institutes and industry are fostering the development of novel calibration standards and automated verification protocols.
Asia-Pacific is experiencing rapid expansion in acoustic gauge calibration, particularly in China, India, and Southeast Asia, fueled by rising investments in infrastructure, energy, and manufacturing. Key regional players such as Yokogawa Electric Corporation are developing cost-effective and scalable calibration solutions tailored for emerging markets. Government initiatives to improve industrial safety and quality standards are also stimulating demand for certified calibration services. Furthermore, the region is seeing increased localization of production and service capabilities to meet the needs of a diverse and expanding industrial base.
Beyond these regions, the Middle East and Latin America present growth opportunities as energy and petrochemical industries modernize. As global industries move toward digital transformation and sustainability, the outlook for acoustic gauge calibration technologies is positive, with continued innovation in automation, remote monitoring, and regulatory compliance solutions expected through 2025 and beyond.
Investment, M&A, and R&D Pipelines: 2025 and Future Outlook
The landscape for investment, mergers and acquisitions (M&A), and research and development (R&D) in acoustic gauge calibration technologies is poised for notable activity in 2025 and the subsequent years. Driven by tightening industry standards, digital transformation, and increasing demand for high-accuracy measurement in sectors such as oil & gas, utilities, and environmental monitoring, stakeholders are strategically repositioning to address evolving technical requirements and capture growth opportunities.
On the investment front, key manufacturers are channeling resources into expanding production capabilities and advancing digital calibration solutions. Notably, Fluke Corporation has announced ongoing investments in smart acoustic calibration platforms, incorporating wireless connectivity and data analytics to streamline workflows and facilitate remote diagnostics. Similarly, Brüel & Kjær (a part of HBK) continues to prioritize R&D efforts into automated calibration benches and AI-assisted error detection, aiming to reduce human intervention and increase calibration throughput.
In terms of M&A, the sector has seen increasing consolidation as established players seek to integrate specialized acoustic calibration providers. For example, Norsonic AS has recently completed the acquisition of a UK-based calibration laboratory, thereby strengthening its footprint in the European market and expanding its portfolio of accredited calibration services. This trend is expected to persist as large instrumentation firms look to offer end-to-end acoustic measurement and calibration packages.
R&D pipelines are robust, with a focus on meeting emerging regulatory standards and supporting next-generation sensor technologies such as MEMS-based and ultrasonic transducers. National Instruments is actively collaborating with academic partners to develop precision acoustic calibration algorithms for use in automated test systems, targeting applications in automotive and aerospace sectors. Meanwhile, RION Co., Ltd. is advancing the miniaturization and ruggedization of portable acoustic calibrators, with field trials ongoing for use in harsh industrial environments.
Looking ahead, the outlook for 2025 and beyond points to continued growth in investment, strategic acquisitions, and R&D innovation. Regulatory drivers—such as the anticipated tightening of IEC and ISO standards for acoustic calibration—are expected to accelerate product development cycles and increase demand for accredited laboratories. As digitalization becomes further entrenched in metrology, companies that integrate software-driven calibration, remote access, and advanced data analytics will be well-positioned to lead the market.
Challenges, Disruptors, and Opportunities Shaping the Next 5 Years
The landscape of acoustic gauge calibration technologies is undergoing significant transformation as industries seek greater accuracy, automation, and digital integration. Several challenges, disruptors, and opportunities are shaping the sector as it moves through 2025 and beyond.
Challenges:
- Stringent Accuracy Demands: Sectors such as energy, pharmaceuticals, and aerospace are imposing tighter calibration tolerances. Meeting these requirements is complicated by environmental noise interference and the need to calibrate across broader frequency ranges. Manufacturers are being pressured to innovate in both hardware and software signal processing.
- Regulatory Compliance: Evolving standards from organizations like the International Electrotechnical Commission (IEC) and regional authorities require regular updates to calibration protocols and documentation. Ensuring compliance while maintaining operational efficiency is a recurring challenge for calibration labs and device manufacturers.
Disruptors:
- Digitalization and IoT: The integration of IoT-enabled gauges and remote calibration capabilities is disrupting traditional manual calibration workflows. Companies like Brüel & Kjær and GRAS Sound & Vibration are advancing smart calibrator products that enable remote monitoring, automated diagnostics, and cloud-based calibration records.
- Automated Calibration Systems: The move towards fully automated, robotic calibration benches is reducing human error, increasing throughput, and enabling 24/7 operations. Trescal is expanding its automated calibration service offerings globally, highlighting a trend that is expected to gain momentum in the next several years.
- AI and Advanced Analytics: Integration of artificial intelligence for error detection, predictive maintenance, and performance optimization is beginning to emerge in calibration solutions. This is facilitating adaptive calibration routines that can respond to changing acoustic environments in real time.
Opportunities:
- Remote and Cloud-Based Calibration: There is increasing demand for calibration systems that support remote operation, data sharing, and cloud-based documentation. This is particularly relevant for organizations managing distributed assets or operating under hybrid work models.
- Expansion into New Markets: The proliferation of acoustic sensors in smart cities, automotive (e.g., electric and autonomous vehicles), and health monitoring devices is opening new application areas for calibration technologies. Manufacturers are positioning themselves to provide scalable solutions adapted to these emerging markets.
- Sustainability and Green Practices: Organizations such as Norsonic are incorporating energy-efficient designs and environmentally friendly materials in their calibration products, aligning with broader industry trends towards sustainability.
Looking ahead, the acoustic gauge calibration sector is poised for rapid innovation driven by digitalization, automation, and the expansion of acoustic measurement applications. Early adopters of smart and automated calibration technologies are expected to benefit from improved efficiency, compliance, and access to new markets over the next five years.
Sources & References
- Baker Hughes
- Halliburton
- American Petroleum Institute (API)
- Emerson
- Siemens
- Brüel & Kjær
- NTi Audio
- Physikalisch-Technische Bundesanstalt (PTB)
- GRAS Sound & Vibration
- ASME
- IEEE Instrumentation and Measurement Society
- International Organization for Standardization
- Norsonic AS
- Larson Davis
- NTi Audio
- OIML
- SLB
- Endress+Hauser
- National Institute of Standards and Technology
- Yokogawa Electric Corporation
- Fluke Corporation
- Trescal