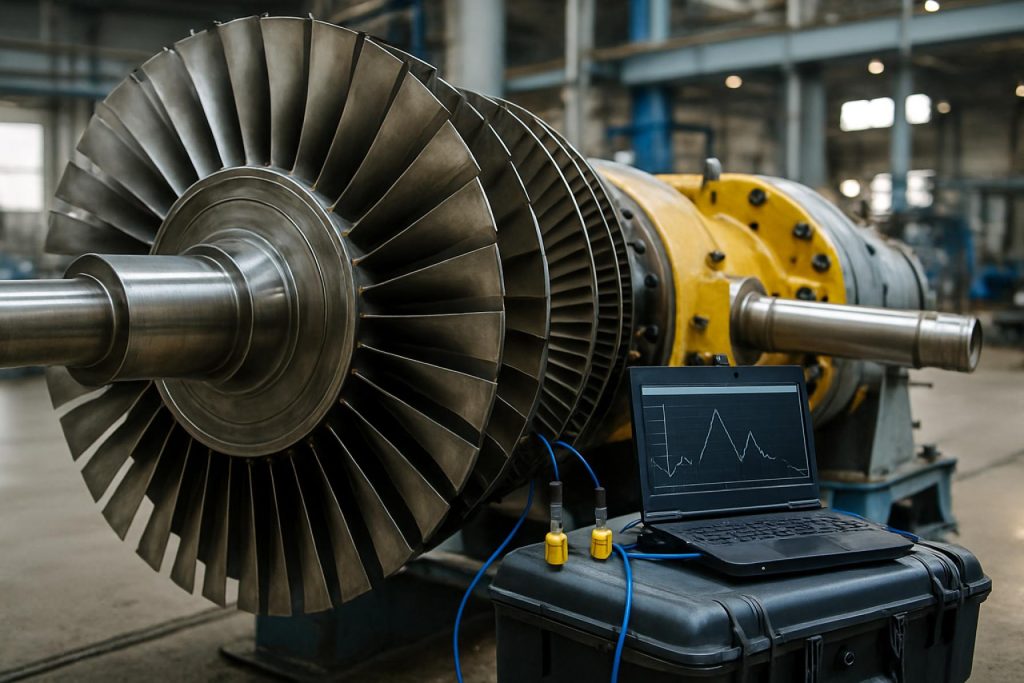
Unlocking the Next Era in Axial Flow Turbomachinery Diagnostics: What 2025 Holds, Who’s Winning, and Where the Smartest Investments Will Be Made. Discover the Data and Emerging Technologies Set to Redefine Performance and Reliability.
- Executive Summary: Key Insights and 2025 Overview
- Market Size & Forecast Through 2030: Growth, Segments, and Value Drivers
- Competitive Landscape: Leading Players, Recent Partnerships, and Strategic Moves
- Breakthrough Diagnostic Technologies: Sensors, AI, and Digital Twins
- Regulatory Trends and Industry Standards: Compliance and Risk Mitigation
- Case Studies: Successful Deployments in Power Generation and Aerospace
- Challenges and Barriers: Data Integration, Cybersecurity, and Legacy Systems
- Emerging Opportunities: Predictive Maintenance, Remote Monitoring, and Cloud Analytics
- Regional Analysis: North America, Europe, Asia-Pacific, and Middle East Hotspots
- Future Outlook: Expert Projections, Innovation Roadmaps, and Investment Priorities
- Sources & References
Executive Summary: Key Insights and 2025 Overview
Axial flow turbomachinery—spanning compressors and turbines in energy, aerospace, and industrial sectors—remains central to global infrastructure. Diagnostics for these machines has entered a transformative phase in 2025, driven by increasing demands for operational efficiency, predictive maintenance, and sustainability. Key trends highlight the convergence of advanced sensor deployment, real-time data analytics, and machine learning, all prioritized by OEMs and operators seeking to minimize unplanned downtime and extend asset life.
A significant development is the wider integration of high-fidelity, wireless sensor networks, enabling continuous, non-intrusive monitoring of vibration, temperature, and pressure in axial compressors and turbines. Leading OEMs such as Siemens Energy, GE Vernova (formerly part of General Electric), and Safran are embedding diagnostic capabilities in both new machines and retrofit solutions. The focus is on early fault detection—especially for blade damage, fouling, and surge events—using edge analytics directly at the site to reduce latency and bandwidth needs.
- Digital Twins and Predictive Diagnostics: Digital twin technology is now a staple in axial flow turbomachinery diagnostics, allowing for real-time simulation of machine states based on sensor inputs. Siemens Energy and GE Vernova have expanded their digital twin platforms to include AI-driven diagnostic modules that not only identify anomalies but also recommend maintenance actions, optimizing overhaul cycles and reducing lifecycle costs.
- Remote Diagnostics and Cloud Integration: Remote monitoring centers, such as those operated by Siemens Energy and GE Vernova, are leveraging cloud-based platforms to analyze fleet-wide data, benchmarking individual units against global performance metrics. This approach improves root-cause analysis and supports the rapid dissemination of software updates and diagnostic algorithms across global fleets.
- Regulatory and Sustainability Drivers: Stricter emissions standards and efficiency mandates, particularly in Europe and Asia, are accelerating investment in advanced diagnostics. Companies like Rolls-Royce and Safran are collaborating with end-users to tailor diagnostic solutions that support decarbonization targets and sustainable operation.
Looking ahead, the outlook for 2025 and beyond features increased automation of diagnostics, greater deployment of AI for prognostics, and tighter integration with asset management workflows. OEMs and operators are expected to deepen partnerships with sensor manufacturers and software providers, further blurring the lines between hardware and digital services. This convergence is set to redefine value creation in the axial flow turbomachinery sector over the next several years.
Market Size & Forecast Through 2030: Growth, Segments, and Value Drivers
The market for axial flow turbomachinery diagnostics is poised for significant growth through 2030, driven by sustained investments in energy infrastructure, the ongoing modernization of power plants, and a global focus on efficiency and reliability in rotating equipment. In 2025, the market is experiencing robust demand across power generation, oil & gas, and aviation sectors, where axial flow turbines and compressors are critical assets. Key value drivers include the increasing adoption of predictive maintenance, the integration of advanced sensor technologies, and the transition toward digital twins for real-time condition monitoring.
Major manufacturers and service providers such as GE, Siemens Energy, and Sulzer are at the forefront, offering comprehensive diagnostic solutions that combine hardware (vibration, acoustic, and temperature sensors) with sophisticated analytics platforms. These companies are expanding their diagnostics portfolios, leveraging artificial intelligence and machine learning to detect anomalies, predict failures, and optimize maintenance schedules. The deployment of cloud-based analytics and remote monitoring is accelerating, facilitating real-time diagnostics even in geographically dispersed operations.
Market segmentation indicates that power generation remains the largest end-use sector, supported by the modernization of existing thermal, gas, and combined-cycle plants, particularly in Asia-Pacific and North America. The oil & gas sector continues to be a significant contributor, with midstream and downstream facilities investing in asset reliability to minimize downtime and comply with stringent safety regulations. Aerospace is another rapidly growing segment, with aircraft engine manufacturers and operators adopting advanced diagnostics to improve fleet availability and reduce maintenance costs.
Industry initiatives are pushing toward standardization and interoperability of diagnostic systems, with organizations such as the American Petroleum Institute and the International Energy Agency promoting best practices for asset monitoring and data sharing. The trend toward digitalization, including the use of edge computing and integration with enterprise asset management (EAM) systems, is expected to further drive adoption rates.
Looking ahead to 2030, the axial flow turbomachinery diagnostics market is set for sustained expansion, supported by ongoing decarbonization efforts, the rise of hydrogen-ready turbines, and the proliferation of renewable energy assets requiring reliable backup power. As the installed base of aging turbomachinery grows and digital transformation accelerates, the demand for advanced diagnostics is expected to remain strong, with major OEMs and technology providers investing heavily in R&D to stay ahead in this dynamic landscape.
Competitive Landscape: Leading Players, Recent Partnerships, and Strategic Moves
The competitive landscape of axial flow turbomachinery diagnostics is characterized by the presence of established OEMs, specialized diagnostics providers, and new entrants leveraging digitalization. Leading manufacturers such as Siemens Energy, General Electric (GE), and Mitsubishi Heavy Industries (MHI) maintain a dominant position, integrating advanced diagnostics into their turbomachinery portfolios. These companies invest heavily in condition monitoring, real-time analytics, and predictive maintenance to enhance operational reliability and reduce unplanned downtime.
Recent years have seen a surge in strategic partnerships and joint ventures to accelerate digital transformation. For example, in 2024, Baker Hughes expanded collaborations with cloud and AI specialists to offer enhanced diagnostics and asset performance management for axial compressors and turbines. ABB and Schneider Electric have also deepened relationships with end-users in the oil & gas and power sectors, providing integrated sensor and analytics packages for both new installations and retrofit projects.
Suppliers such as Emerson and Honeywell have focused on edge computing and IIoT (Industrial Internet of Things) platforms to deliver real-time turbomachinery health insights. Their offerings now include wireless vibration sensors, high-frequency data acquisition, and cloud-based diagnostics designed for axial flow compressors and turbines. In 2025, they are expected to roll out updates that further automate root cause analysis and optimize maintenance intervals.
Smaller, specialized firms are also making inroads by focusing on niche diagnostic solutions. Companies like Wood (through its Asset Performance Optimization division) and Sulzer (known for aftermarket turbomachinery services) have expanded their monitoring service portfolios, offering remote diagnostics, advanced vibration analysis, and lifecycle management tailored for axial flow machines.
Looking forward, competitive dynamics are likely to intensify as remote monitoring, AI-driven diagnostics, and digital twins become industry standards. Market leaders are expected to increase investment in R&D and strategic alliances, particularly with software developers and automation companies. The next few years will likely see further convergence of hardware and software expertise, with diagnostics solutions increasingly embedded into OEM offerings and available as subscription-based services.
Breakthrough Diagnostic Technologies: Sensors, AI, and Digital Twins
The field of axial flow turbomachinery diagnostics is experiencing a significant transformation in 2025, fueled by the rapid deployment of advanced sensor technologies, artificial intelligence (AI), and digital twin platforms. These technologies are enabling unprecedented levels of real-time monitoring, predictive maintenance, and performance optimization in critical equipment such as gas turbines, compressors, and jet engines.
Sensor innovation continues to be a cornerstone of this evolution. Leading OEMs and component suppliers are advancing the integration of fiber-optic and wireless sensor systems, enabling high-fidelity, continuous measurement of parameters such as vibration, pressure, temperature, and blade tip clearance. For example, General Electric leverages advanced embedded sensors in its HA-class gas turbines, facilitating continuous data capture for health assessment and early anomaly detection. Similarly, Siemens Energy and Rolls-Royce Holdings plc have expanded their sensor suites to include distributed and miniaturized devices, allowing for more granular diagnostics in both industrial and aerospace turbomachinery.
AI and machine learning are now central to diagnostic strategies. Algorithms analyze the vast volumes of sensor data to recognize subtle patterns indicative of incipient faults, such as blade fatigue, bearing wear, or aerodynamic instabilities. Baker Hughes and Safran are actively deploying AI-driven condition monitoring platforms, which support operators with early warning alerts and actionable maintenance recommendations. These systems not only reduce unplanned downtime but also enable a shift from scheduled to truly predictive maintenance, reducing lifecycle costs and improving reliability.
Digital twin technology—virtual replicas of physical turbomachinery assets—has reached new levels of maturity in 2025. Companies such as Siemens AG and Ansys, Inc. provide high-fidelity digital twins that ingest real-time operational data, simulate component behavior under a variety of conditions, and predict the evolution of faults or performance degradation. This capability allows for scenario-based diagnostics and optimization, including the assessment of impacts from operational changes or environmental fluctuations, thus supporting smarter asset management decisions.
Looking ahead into the next several years, the convergence of these technologies is expected to accelerate. Key industry stakeholders are investing in integrated diagnostic ecosystems, combining sensor networks, AI analytics, and digital twins into unified platforms. As interoperability standards improve and computational power increases, diagnostics will become even more automated, adaptive, and accessible across the global turbomachinery fleet. This digital transformation is set to deliver tangible benefits in efficiency, safety, and sustainability for sectors ranging from energy and aviation to process industries.
Regulatory Trends and Industry Standards: Compliance and Risk Mitigation
In 2025, regulatory trends and industry standards for axial flow turbomachinery diagnostics are being shaped by increasingly stringent safety, environmental, and reliability demands. Global aviation, power generation, and oil & gas sectors are under mounting pressure to ensure that turbomachinery—such as axial compressors and turbines—operates with optimal efficiency and minimal risk of failure. This is prompting both regulators and industry bodies to develop and enforce comprehensive diagnostic and monitoring requirements.
A critical driver is the evolution of standards from organizations like the International Organization for Standardization (ISO) and the American Society of Mechanical Engineers (ASME), which continue to update guidelines for condition monitoring, performance assessment, and fault detection in turbomachinery. For example, standards such as ISO 13379 and ASME PTC 10 are being referenced more frequently for establishing diagnostic protocols and acceptance criteria. These standards are influencing procurement and maintenance specifications across industries, as operators seek to demonstrate compliance and reduce operational risk.
In parallel, regulatory agencies in major markets—including the U.S. Federal Aviation Administration (FAA) for aerospace and the U.S. Environmental Protection Agency (EPA) for emissions—are increasing expectations for real-time monitoring and data-driven maintenance practices. For example, the FAA’s continued focus on predictive diagnostics is leading to greater adoption of continuous health monitoring systems in aircraft engines, including those produced by manufacturers like GE Aerospace and Rolls-Royce. Both companies have invested in advanced digital analytics and IoT-enabled diagnostics that support compliance with evolving airworthiness directives and emission targets.
In the power and process industries, OEMs such as Siemens Energy and Solar Turbines are implementing diagnostic solutions that integrate seamlessly with regulatory compliance frameworks. These systems capture vibration, temperature, and pressure data to satisfy operational and environmental reporting requirements, as well as early warning thresholds mandated by insurance providers and regulatory bodies.
Looking ahead, industry outlook for 2025 and the coming years is characterized by a shift from periodic inspections to continuous, automated diagnostics. This evolution is being reinforced by the adoption of the Industrial Internet of Things (IIoT) and advanced analytics, which are expected to become central pillars of forthcoming regulatory standards. Industry consortia and standards bodies are collaborating on new frameworks that will likely require real-time diagnostics, cloud-based reporting, and traceable compliance logs—further embedding risk mitigation into the core of turbomachinery operations.
Case Studies: Successful Deployments in Power Generation and Aerospace
The deployment of advanced diagnostics in axial flow turbomachinery has become increasingly critical across power generation and aerospace sectors, especially as operators seek to enhance reliability, efficiency, and predictive maintenance. In 2025, several high-profile case studies underscore the transformative impact of modern diagnostic systems.
In the power generation industry, Siemens Energy has been at the forefront of integrating diagnostic platforms into its gas and steam turbine fleets. Leveraging its “Omnivise Digital Services,” Siemens Energy has enabled real-time monitoring and advanced fault detection on hundreds of installed axial flow turbines worldwide. A recent deployment at a European combined-cycle plant demonstrated how vibration and thermal imaging analytics detected incipient blade fatigue, allowing maintenance teams to intervene before a costly failure—ultimately increasing unit availability and reducing unplanned outages.
Similarly, GE Vernova (the rebranded energy division of GE) has implemented its “Predix Asset Performance Management” suite in several power stations across North America and Asia. In a 2024 case, a 700 MW gas turbine unit exhibited subtle performance anomalies. Using high-frequency sensor data and AI-driven pattern recognition, GE Vernova’s system pinpointed early-stage fouling in the compressor section. The predictive alert enabled optimized cleaning scheduling, improving efficiency by 1.2% and yielding substantial fuel savings over the annual cycle.
Within aerospace, Rolls-Royce continues to set benchmarks with its “Engine Health Monitoring” system—now standard on all new Trent series engines. In 2025, a flagship airline partner reported a successful in-flight detection of a minute compressor instability event. The system’s real-time telemetry, powered by cloud analytics, prompted a controlled engine shutdown and safe diversion, averting a potential in-flight emergency. Post-incident analysis led to rapid root-cause identification, streamlining corrective action and minimizing aircraft downtime.
Additionally, Pratt & Whitney has expanded its “EngineWise” diagnostics suite across both military and commercial fleets. Notably, in 2025, a major air force operator credited the system with a 20% reduction in unscheduled engine removals, attributing this directly to improved detection of axial compressor wear and foreign object damage.
The outlook remains robust: with continued advances in sensor fidelity, machine learning, and cloud connectivity, real-world case studies are expected to proliferate. Industry leaders are poised to further reduce lifecycle costs and enhance safety margins, cementing diagnostics as a cornerstone of turbomachinery operation in the years to come.
Challenges and Barriers: Data Integration, Cybersecurity, and Legacy Systems
Axial flow turbomachinery diagnostics are experiencing rapid advancements, but the industry continues to face significant challenges related to data integration, cybersecurity, and the management of legacy systems—challenges that are expected to remain prominent through 2025 and the next few years. As digitalization and remote monitoring become ubiquitous, operators and OEMs must navigate complex technical and organizational barriers.
Data Integration: The integration of diagnostic data from diverse sources—including vibration sensors, performance monitors, and control systems—remains a central challenge. Most turbomachinery fleets contain equipment from multiple generations and manufacturers, often with proprietary data formats. Achieving seamless interoperability for real-time diagnostics requires robust middleware and standardized communication protocols. Leading OEMs such as Siemens Energy and GE Vernova are investing in digital platforms that aggregate data from both legacy and modern assets. However, industry progress is hindered by fragmented data architectures and limited adoption of open standards. As of 2025, collaboration efforts—such as the development of the Asset Performance Management (APM) frameworks—are ongoing but not yet universally implemented.
Cybersecurity: With the proliferation of cloud-based diagnostics and remote connectivity, axial flow turbomachinery is increasingly exposed to cyber threats. The sector is under pressure to comply with stricter regulatory frameworks, including the NIST Cybersecurity Framework and regional critical infrastructure mandates. OEMs and operators are prioritizing secure data transmission, multi-factor authentication, and intrusion detection. Companies like Baker Hughes and ABB are embedding cybersecurity into their monitoring and diagnostic offerings, often collaborating with cybersecurity specialists for end-to-end solutions. Nonetheless, the rapid expansion of Industrial Internet of Things (IIoT) devices continues to enlarge the attack surface, and security patching for legacy systems remains a persistent concern.
Legacy Systems: A significant portion of the global axial turbomachinery fleet consists of units that predate the digital era. Upgrading these assets for modern diagnostics presents both technical and economic barriers. Retrofitting sensors and gateways is often constrained by physical design limitations, lack of detailed documentation, or risk of operational disruption. While companies like Siemens Energy and GE Vernova offer retrofit packages and digital twins to extend asset life, many operators struggle to justify the investment without clear ROI. Over the next few years, the sector is anticipated to see incremental progress as new modular sensor technologies and edge computing solutions lower costs and deployment complexity.
Looking ahead, the industry’s ability to surmount these barriers will shape the pace of digital transformation in axial flow turbomachinery diagnostics. Greater adoption of open standards, enhanced cybersecurity postures, and scalable integration solutions are expected to be key focus areas through 2025 and beyond.
Emerging Opportunities: Predictive Maintenance, Remote Monitoring, and Cloud Analytics
Axial flow turbomachinery diagnostics are entering a transformative phase, driven by advances in predictive maintenance, remote monitoring, and cloud-based analytics. As of 2025, OEMs and operators are increasingly investing in digital tools to improve reliability, minimize unplanned outages, and optimize lifecycle costs for assets such as gas and steam turbines, axial compressors, and aero-derivative equipment.
Predictive maintenance is evolving rapidly through the integration of AI and machine learning algorithms, which analyze real-time sensor data to forecast failures before they occur. Major OEMs such as Siemens Energy and GE have expanded their digital service portfolios, offering advanced diagnostic platforms that aggregate vibration, temperature, and pressure data to identify early-stage faults in axial flow components. These solutions not only extend intervals between overhauls but also support condition-based maintenance schedules, reducing unnecessary interventions and associated costs.
Remote monitoring is now a standard feature for new installations and retrofits. Companies like Ansaldo Energia and Mitsubishi Power provide secure, real-time connectivity between field equipment and centralized monitoring centers. This enables expert teams to oversee fleets globally, deliver rapid diagnostic insights, and guide on-site technicians through troubleshooting procedures. Remote access enhances uptime and safety, especially for units deployed in remote or hazardous locations.
Cloud analytics platforms are becoming essential for handling the vast quantities of operational data generated by modern turbomachinery. OEMs and independent service providers leverage cloud infrastructure to process, store, and visualize data from thousands of sensors in real time. GE and Siemens Energy are prominent in this space, offering solutions that integrate with enterprise asset management systems and support advanced diagnostics, anomaly detection, and performance benchmarking across large fleets.
Looking ahead, the outlook for axial flow turbomachinery diagnostics is shaped by increasing adoption of edge computing, digital twins, and cybersecurity enhancements. Edge devices are expected to enable faster, localized diagnostics, while digital twins—virtual replicas of physical assets—provide a foundation for simulating performance and predicting degradation under varying operational scenarios. Industry-wide collaborations, including those involving organizations such as Siemens Energy, GE, and Mitsubishi Power, are likely to accelerate standards development and best practices for secure, interoperable diagnostic ecosystems.
By 2025 and beyond, these emerging technologies are poised to deliver significant efficiency gains, cost savings, and reliability improvements for operators of axial flow turbomachinery across the energy, aviation, and process industries.
Regional Analysis: North America, Europe, Asia-Pacific, and Middle East Hotspots
The global landscape for axial flow turbomachinery diagnostics is shaped by the distinct priorities and industrial profiles of North America, Europe, Asia-Pacific, and the Middle East. As of 2025 and looking into the next several years, these regions are deploying advanced diagnostics to enhance efficiency, reliability, and sustainability in sectors such as power generation, aerospace, oil and gas, and industrial processing.
North America remains a leader in the adoption of high-end diagnostics, with major OEMs and service providers integrating digital twins, AI-driven predictive maintenance, and real-time condition monitoring into their axial flow compressors and turbines. Companies like GE and Siemens Energy maintain significant R&D and manufacturing operations in the US and Canada, focusing on remote diagnostics and lifecycle management. The region’s strong regulatory environment and emphasis on decarbonization further drive investment in advanced monitoring for both legacy and new turbomachinery fleets.
Europe is characterized by a mature industrial base and stringent environmental standards. The focus is on diagnostics that can support the integration of hydrogen and alternative fuels, as well as compliance with emissions regulations. Leading firms such as Rolls-Royce and Siemens Energy are deploying sophisticated analytics platforms for both power generation and aerospace turbomachinery. The European Union’s digitalization initiatives and funding for energy transition projects are expected to accelerate the uptake of smart diagnostics across the continent.
In the Asia-Pacific region, rapid industrialization and expansion of power and petrochemical infrastructure are driving demand for robust diagnostics. Countries like China, Japan, and South Korea are investing heavily in both domestic manufacturing and the import of advanced turbomachinery solutions. Companies such as Mitsubishi Heavy Industries are advancing remote monitoring services, while local and multinational players are forming partnerships to localize diagnostic technology and aftersales support. The push for grid stability and reliability in fast-growing economies makes advanced diagnostics a priority.
The Middle East remains a hotspot due to its concentration of oil & gas and power generation assets. Operators are adopting diagnostics to maximize uptime and extend asset life under harsh operating conditions. Firms like Baker Hughes and Siemens Energy are prominent in deploying monitoring and analytics platforms tailored for the region’s unique requirements. As countries diversify their energy mix, including investments in renewables and hydrogen, the role of diagnostics in ensuring operational excellence is set to grow.
Across all regions, the outlook for axial flow turbomachinery diagnostics is robust, with digitization, remote services, and AI-driven insights becoming the norm. The convergence of regulatory pressure, aging infrastructure, and the energy transition continues to create new opportunities and challenges for OEMs and end-users alike.
Future Outlook: Expert Projections, Innovation Roadmaps, and Investment Priorities
The outlook for axial flow turbomachinery diagnostics through 2025 and into the latter part of the decade is shaped by accelerating digitalization, a heightened focus on predictive maintenance, and an evolving regulatory landscape. Industry stakeholders—OEMs, operators, and technology integrators—are prioritizing investments in advanced sensor technologies, real-time analytics, and AI-driven diagnostic platforms to enhance reliability, efficiency, and sustainability across power generation, aviation, and industrial sectors.
A key driver is the integration of cloud-based diagnostic solutions and Industrial Internet of Things (IIoT) frameworks. Leading turbomachinery manufacturers such as Siemens Energy and General Electric are expanding their digital service portfolios, leveraging edge computing and machine learning to enable continuous health monitoring and early anomaly detection. These platforms aggregate high-frequency vibration, acoustic, and thermal data from axial flow compressors and turbines, supporting remote diagnostics and reducing unplanned downtime. For example, Siemens Energy’s digital offerings emphasize modular upgrades and interoperable diagnostics, while General Electric’s Asset Performance Management suite is being adopted to streamline maintenance and extend component life cycles.
Innovation roadmaps for the next few years highlight the transition from reactive and calendar-based maintenance to fully predictive and prescriptive regimes. Companies such as Rolls-Royce are investing in digital twins—virtual representations of physical turbomachinery assets—to dynamically simulate wear, fouling, and performance degradation, thereby enabling operators to optimize interventions and maximize availability. Additionally, sensor miniaturization and the advent of wireless, self-powered monitoring devices are expected to reduce retrofit barriers for legacy equipment, broadening the addressable market.
From an investment perspective, the sector is witnessing increased collaboration between OEMs, automation firms, and data analytics specialists. Honeywell and ABB, for instance, are aligning their digital ecosystems with turbomachinery OEMs to deliver end-to-end diagnostic and prognostic capabilities tailored for energy transition goals and emissions compliance. Investment priorities are also being shaped by decarbonization initiatives—diagnostic solutions that minimize energy losses and optimize operational flexibility are in high demand as companies prepare for tighter CO2 regulations through 2030.
Overall, the next few years will see axial flow turbomachinery diagnostics shift further toward autonomous, data-centric models. Widespread deployment of smart sensors, enhanced cybersecurity measures, and integrated lifecycle management solutions are projected to define the innovation agenda, with market leaders placing strategic bets on AI-enhanced diagnostics and sustainable, digitally enabled service models.
Sources & References
- Siemens Energy
- GE Vernova
- Rolls-Royce
- Siemens Energy
- Sulzer
- American Petroleum Institute
- International Energy Agency
- Mitsubishi Heavy Industries
- Baker Hughes
- ABB
- Emerson
- Honeywell
- Wood
- ISO
- ASME
- Ansaldo Energia