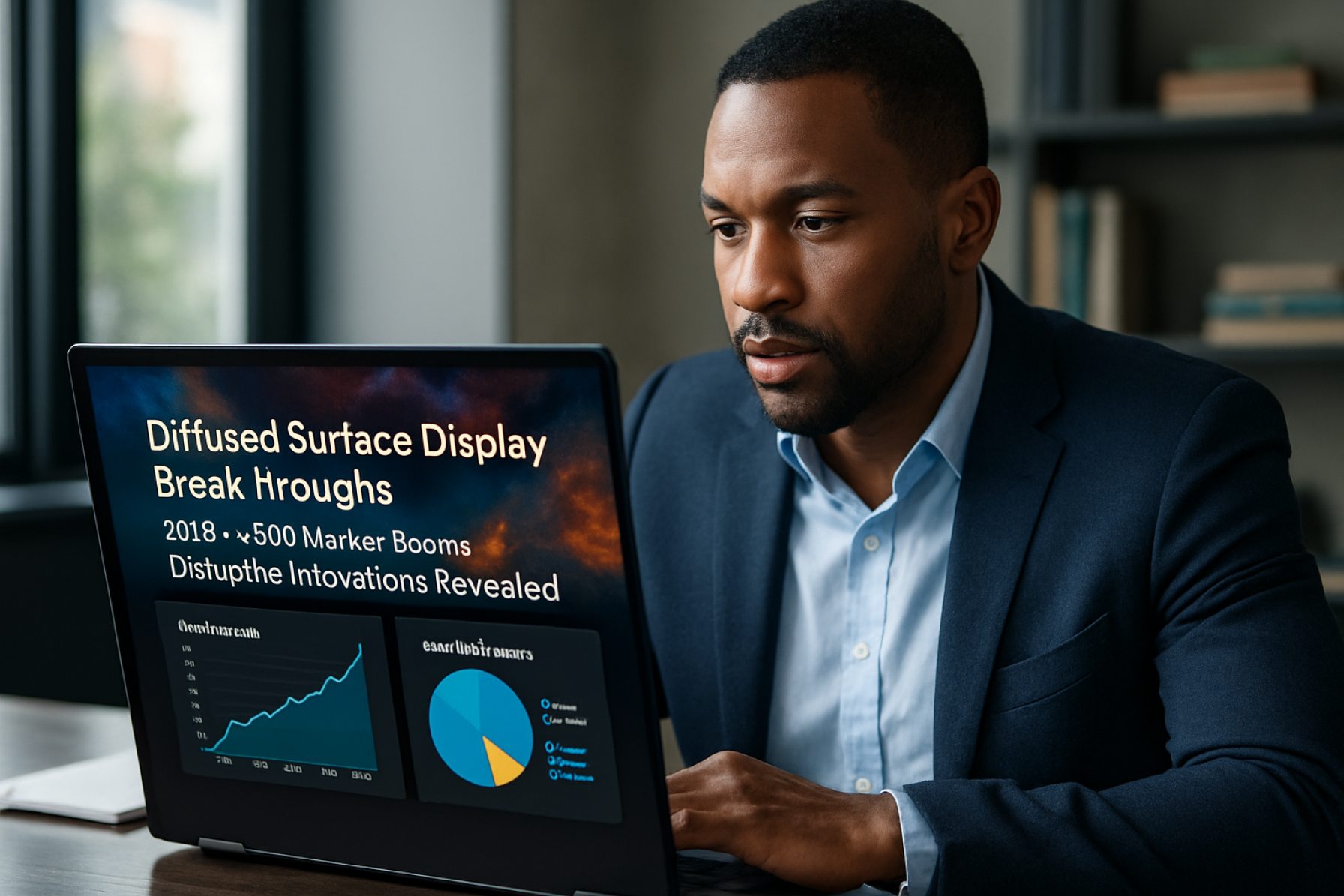
Table of Contents
- Executive Summary: Key Trends Shaping Diffused Surface Display in 2025–2030
- Technology Overview: Principles and Recent Advances in Diffused Surface Display Fabrication
- Major Players and Strategic Partnerships (e.g., samsung.com, corning.com, lgdisplay.com)
- Market Size and Forecast: Global Growth Projections Through 2030
- Emerging Applications: Automotive, Consumer Electronics, and Smart Environments
- Materials Science: Innovations in Substrates, Coatings, and Light Diffusion
- Manufacturing Techniques: Automation, Precision, and Scalability Challenges
- Competitive Landscape: Patents, IP Activity, and Regional Hubs
- Sustainability and Regulatory Drivers in Fabrication Processes
- Future Outlook: Disruptive Opportunities and Risks for Stakeholders
- Sources & References
Executive Summary: Key Trends Shaping Diffused Surface Display in 2025–2030
The landscape of diffused surface display fabrication is undergoing significant transformation in 2025, driven by technological innovation, material advances, and the growing demand for immersive visual experiences across sectors. Diffused surface displays—characterized by their ability to scatter light uniformly, minimizing glare and enhancing visibility from wide viewing angles—are now central to next-generation applications in retail, automotive, and architectural integration.
A key trend is the adoption of advanced micro- and nano-patterning techniques to achieve unprecedented levels of light diffusion. Leading manufacturers such as 3M are leveraging precision-engineered surface textures and optical films, enabling displays that deliver both high brightness and energy efficiency. In 2025, 3M continues to expand its line of diffusive films, providing enhanced performance for large-format displays and digital signage.
Material innovation is another critical driver. The incorporation of functional polymers and hybrid glass-polymer substrates is allowing for thinner, lighter, and more flexible diffused displays. Kuraray and AGC Inc. have both reported advancements in specialty interlayers and coatings that maintain optical clarity while offering robust diffusion properties, supporting seamless integration in automotive heads-up displays and interactive kiosks.
Manufacturing scalability is improving with the adoption of roll-to-roll processing and laser-assisted patterning, facilitating higher throughput and cost-effectiveness. For example, DuPont is developing scalable fabrication techniques for optical films, aiming to meet the surging demand for both consumer and commercial display installations.
Sustainability considerations are now shaping fabrication processes. Companies like Covestro are introducing eco-friendly diffusive materials that reduce reliance on traditional plastics and support recycling initiatives—addressing regulatory pressures and customer preferences for greener solutions. These sustainable materials are expected to gain momentum through 2030 as environmental regulations tighten.
Looking ahead, the convergence of smart manufacturing, automation, and advanced materials science will further accelerate the evolution of diffused surface displays. Integration with sensor technologies and adaptive lighting is anticipated, with suppliers such as SCHOTT exploring intelligent glass solutions that dynamically adjust diffusion based on ambient conditions.
In summary, from 2025 through the end of the decade, diffused surface display fabrication will be defined by precision patterning, material innovation, sustainable practices, and integration with intelligent systems, positioning the sector for robust growth and diversification across industries.
Technology Overview: Principles and Recent Advances in Diffused Surface Display Fabrication
Diffused surface display fabrication revolves around creating display panels that scatter incident light to achieve uniform luminance, reduce glare, and enhance visual comfort. The underlying principle leverages engineered micro- or nano-structured surfaces, diffusive coatings, or embedded particles to scatter light emitted from underlying sources, such as LEDs or OLEDs. This approach is particularly critical in applications requiring wide viewing angles, minimal specular reflection, and high readability—such as automotive dashboards, signage, and next-generation consumer electronics.
Recent years have seen significant progress in both materials and manufacturing processes for diffused surface displays. Companies like 3M have advanced their light management films, integrating micro-replicated patterns that enable tailored diffusion profiles while maintaining high optical clarity. Their latest optical films for displays in 2024 incorporate proprietary microstructures designed for enhanced energy efficiency and reduced thickness, supporting slimmer device form factors.
In the automotive and public information display sectors, AGC Inc. has introduced chemically strengthened glass with integrated diffusive layers, optimizing both durability and light scattering. Their 2025 product lines focus on combining anti-glare surface treatments with controlled haze levels to meet evolving standards for outdoor readability and ambient light adaptation.
On the manufacturing front, roll-to-roll (R2R) nanoimprinting has emerged as a scalable method for producing large-area diffused films. Nippon Electric Glass Co., Ltd. has deployed precision R2R processes to embed sub-micron diffusive patterns directly into display cover glass, achieving high uniformity and throughput suitable for mass-market displays. Such advancements are lowering costs and expanding the availability of diffused surface technologies in mid-range and entry-level devices.
OLED and miniLED display manufacturers are also integrating advanced diffusers to overcome issues of hotspotting and color non-uniformity. LG Display has developed hybrid diffusive layers specifically optimized for their transparent and automotive OLED panels, targeting both daylight readability and style-conscious industrial design. Meanwhile, Kuraray is commercializing specialty diffusive PVA films for flexible and curved display applications, supporting the trend toward novel form factors.
Looking ahead to 2025 and beyond, the sector is expected to see further convergence of diffusive technologies with smart functionality—such as tunable haze, dynamic privacy modes, and integrated touch sensitivity. Leading suppliers are investing in material innovations and digital manufacturing tools to enable rapid customization and high-volume production. As display performance requirements become more demanding across industries, advances in diffused surface display fabrication will play a pivotal role in enabling the next generation of immersive, energy-efficient, and user-friendly screens.
Major Players and Strategic Partnerships (e.g., samsung.com, corning.com, lgdisplay.com)
The fabrication of diffused surface displays—a key technology for ambient, glare-free, and high-contrast visual outputs—is rapidly advancing, led by major players in the display and materials industries. In 2025, strategic partnerships are accelerating innovation, integrating advanced surface treatments, nanostructured coatings, and novel substrate materials to enhance both performance and manufacturability.
Samsung Display continues to invest heavily in diffused surface OLED and QD-display technologies, focusing on anti-reflection and anti-glare layers for improved readability and energy efficiency. In early 2025, the company expanded its partnership with leading material suppliers to co-develop next-generation diffusion films, aiming to integrate these solutions across its large-size display panels and emerging automotive applications (Samsung Display).
Corning Incorporated, a global leader in specialty glass and ceramics, has maintained its pivotal role by supplying advanced glass substrates featuring engineered surface textures. These substrates underpin many diffused surface displays by optimizing light scattering and minimizing unwanted reflections. In 2024–2025, Corning announced collaborations with tier-one display manufacturers to jointly develop new glass compositions and scalable surface etching processes, targeting consumer electronics and high-end professional displays (Corning Incorporated).
LG Display is leveraging its expertise in both OLED and LCD fabrication to push the boundaries of diffused surface treatments. The company’s 2025 roadmap includes the deployment of proprietary micro-patterned films and advanced surface lamination techniques, which significantly reduce screen glare in large-format displays. LG Display’s ongoing alliances with equipment manufacturers and chemical suppliers are focused on enhancing production scalability and environmental sustainability (LG Display).
In parallel, BOE Technology Group and AUO are actively investing in R&D for diffused surface technologies, particularly for commercial signage, automotive, and industrial displays. BOE’s 2025 initiatives include pilot lines for roll-to-roll fabrication of diffusive layers, while AUO is exploring hybrid surface structures to maximize both clarity and ambient light performance (BOE Technology Group, AUO).
Looking forward, cross-industry collaborations—spanning substrate manufacturers, display panel makers, and specialty chemical companies—are expected to deepen. The next several years will likely see further integration of advanced nano-coatings, sustainable materials, and digital fabrication methods, positioning these major players at the forefront of diffused surface display innovation and commercialization.
Market Size and Forecast: Global Growth Projections Through 2030
The global market for diffused surface display fabrication, a segment encompassing technologies such as light-diffusing OLEDs, micro-LEDs, and projection-based displays, is poised for robust expansion through 2030. As of 2025, growth is largely propelled by rapid advancements in display manufacturing, increasing demand for seamless digital signage, automotive interior displays, and next-generation consumer electronics. Key manufacturers are scaling up their fabrication capabilities to enable larger, more flexible, and visually uniform displays that utilize diffused surface architectures for improved viewing angles and reduced glare.
Current data from leading industry players indicate a surge in investment in both R&D and production capacity. LG Display and Samsung Display, for instance, have announced expanded fabrication lines dedicated to advanced OLED and micro-LED panels, with a focus on diffused surface enhancements for automotive and commercial applications. Similarly, Japan Display Inc. is directing resources towards innovative light management films and new substrate materials that improve diffusion efficiency while maintaining high color fidelity.
On the materials and equipment front, suppliers like Mitsubishi Electric and Konica Minolta are driving improvements in optical film coatings and precision deposition technologies, essential for high-yield, high-uniformity diffused displays. The integration of nanostructured diffusers and quantum dot films is expected to further enhance performance, supporting broader adoption across sectors.
Geographically, Asia-Pacific continues to lead both production volume and technological innovation, with China, South Korea, and Japan hosting major fabrication hubs. However, North America and Europe are rapidly increasing investments, particularly in automotive, public information, and architectural display applications. For example, Continental AG and Bosch Mobility are collaborating with display manufacturers to integrate diffused surface displays into next-generation vehicle cockpits, aiming for mass deployment by 2026-2027.
Looking ahead, industry forecasts from primary display manufacturers anticipate that the global diffused surface display fabrication market will maintain a compound annual growth rate (CAGR) exceeding 10% through 2030, driven by continued innovation and expanding end-use cases. The next few years will likely see accelerated adoption of fabrication techniques that enable ultra-thin, energy-efficient, and highly diffusive displays, positioning the sector for significant value creation and technological leadership.
Emerging Applications: Automotive, Consumer Electronics, and Smart Environments
Diffused surface display fabrication is rapidly advancing as a foundational technology for next-generation interfaces across automotive, consumer electronics, and smart environments. In 2025, the adoption of diffused surface displays is being driven by the demand for seamless integration, enhanced aesthetic appeal, and improved user interaction.
In the automotive sector, diffused displays are increasingly embedded into vehicle interiors, transforming dashboards, center consoles, and even door panels into interactive surfaces. Recent product launches emphasize invisible-until-lit interfaces, enabled by advanced backlighting and diffusion layers. For example, Continental AG is integrating diffused surface displays into its Human-Machine Interface (HMI) solutions, offering customizable lighting and interactive controls that blend smoothly with interior surfaces. Similarly, LG Display is supplying large-area OLED and LCD panels with diffused layers for next-gen automotive cockpits, supporting features like ambient displays and heads-up interfaces.
Consumer electronics are also leveraging diffused surface display fabrication to realize minimalist product designs and immersive user experiences. Smart home devices—such as speakers, thermostats, and lighting controls—are increasingly featuring diffused LED matrices or transparent OLEDs beneath touch-sensitive surfaces, enabling information to appear or disappear as needed. Samsung Display has showcased OLED panel prototypes with embedded diffusers, targeting applications in foldable devices and smart appliances. Meanwhile, Konica Minolta is developing flexible light-diffusing films for integration into compact consumer electronics, supporting both functional and decorative illumination.
Smart environments—encompassing retail, hospitality, and architecture—are adopting diffused surface display fabrication to deliver dynamic, interactive surfaces at scale. Hotels and retail stores are deploying large-area, seamless LED diffused panels for ambiance and wayfinding. ams OSRAM is supplying high-efficiency LEDs and optical diffusers for architectural lighting and interactive signage, while Covestro provides specialty polymers for light-diffusing panels used in interior design and smart building applications.
Looking forward to the next few years, advances in micro-LEDs, flexible substrates, and optical diffusion materials are expected to further enhance the performance and versatility of diffused surface displays. Industry players are focusing on improving energy efficiency, transparency, and touch sensitivity, anticipating broader deployment across mobility, home automation, and adaptive workspaces.
Materials Science: Innovations in Substrates, Coatings, and Light Diffusion
The fabrication of diffused surface displays is witnessing significant advancements in materials science, particularly in the development of innovative substrates, advanced coatings, and engineered light diffusion layers. As of 2025, global display manufacturers are prioritizing these innovations to address demands for higher brightness, improved viewing angles, and energy efficiency in both large-format and wearable displays.
A core focus is the refinement of diffusion layers. Companies such as Kuraray have been developing specialty polymers with controlled microstructures, enabling precise light scattering critical for uniform brightness and color consistency. These polymers, often fabricated via extrusion or casting methods, are integrated as films or embedded within glass substrates.
Simultaneously, substrate innovation is accelerating. AGC Inc. and Corning Incorporated are advancing ultra-thin glass and flexible glass solutions with optimized surface roughness and transmission characteristics. For instance, Corning’s ultra-slim glass enables tighter integration of diffusion elements without compromising display thinness or flexibility, supporting the proliferation of foldable and rollable OLED displays.
In coatings, anti-reflective and light-diffusing nanostructures are being adopted at scale. 3M has commercialized optical films with embedded micro-lens arrays and surface texturing that enhance ambient light diffusion while minimizing glare, a crucial factor for outdoor and automotive displays. Wet-coating and vacuum deposition techniques are being fine-tuned to produce these micro- and nano-scale features with high uniformity across large panels.
Hybrid approaches combining inorganic and organic materials are also emerging. Saint-Gobain is integrating silica-based diffusers with polymer substrates, leveraging the high durability of glass and the processing flexibility of plastics. This fusion supports the production of robust, lightweight panels for digital signage and public information displays.
Looking forward to the next several years, the outlook for diffused surface display fabrication is marked by increased automation and precision. Inline metrology and AI-driven quality control are being adopted to monitor the uniformity of diffusion features during manufacturing, ensuring consistent optical performance. Moreover, sustainable materials—such as bio-based polymers and recyclable coatings—are gaining traction as manufacturers respond to regulatory pressures and consumer demand for greener electronics.
These material and process innovations collectively position diffused surface displays for broader application, from immersive retail environments to next-generation automotive dashboards, reflecting a dynamic interplay between scientific advancement and market-driven requirements.
Manufacturing Techniques: Automation, Precision, and Scalability Challenges
The fabrication of diffused surface displays—used in products ranging from premium automotive dashboards to advanced retail signage—has witnessed significant evolution in recent years, with a growing emphasis on automation, precision, and scalability. In 2025, manufacturers are accelerating the deployment of automated production lines to keep up with rising demand for seamless, high-uniformity displays. Robotic handling, laser microfabrication, and advanced inspection systems are now integral to modern production environments.
For instance, Konica Minolta has invested in automated roll-to-roll processing lines, enabling continuous fabrication of microstructured diffusing films. This technology ensures consistent optical quality and minimizes surface defects, critical for automotive and large-area display applications. Similarly, 3M continues to refine its microreplication and multi-layer lamination techniques, leveraging proprietary equipment to achieve precise control over diffusion characteristics and layer uniformity.
Precision challenges remain at the forefront, especially as display manufacturers pursue thinner, lighter, and more flexible form factors. Companies like AGC Inc. are deploying advanced metrology and inline monitoring solutions that enable real-time feedback during fabrication, reducing yield loss due to minor surface variations or particulate contamination. Recent technical developments also include adaptive laser patterning, pioneered by Coherent Corp., which enables the fabrication of highly controlled micro- and nano-structured diffusion features directly onto glass and polymer substrates with sub-micron precision.
One major scalability challenge is the transition from lab-scale or pilot production to high-throughput, cost-effective mass manufacturing. Merck KGaA (EMD Electronics) is among those investing in modular, scalable coating and curing systems designed to support large-area diffused displays for architectural and commercial applications. The supply chain for specialized raw materials—such as high-purity polymers and surface modifiers—is also tightening, prompting collaborative efforts between material suppliers and OEMs to secure consistent quality and supply.
Looking ahead to the next few years, the outlook for diffused surface display fabrication is shaped by the convergence of digital manufacturing and materials innovation. Integration of AI-driven process control and predictive maintenance is expected to further reduce downtime and improve yield. Industrial alliances and standardization efforts, such as those led by SEMI, aim to harmonize quality benchmarks and process protocols, supporting rapid scaling as new applications for diffused surface displays emerge in mobility, smart infrastructure, and immersive retail environments.
Competitive Landscape: Patents, IP Activity, and Regional Hubs
The competitive landscape in diffused surface display fabrication is intensifying as global demand rises for advanced display technologies in automotive, architectural, and consumer electronics sectors. In 2025, key industry players are ramping up patent filings and strategic IP activities, seeking to secure technological leadership and market share.
Patent activity is particularly pronounced among established display manufacturers and materials companies. LG Display has significantly expanded its patent portfolio focused on microstructure diffusion layers, a critical aspect of achieving uniform light distribution in next-generation OLED and MicroLED panels. Similarly, Samsung Display has filed patents related to novel surface texturing and nanomaterial integration, aiming to enhance ambient light performance and viewing angles for large-format and transparent displays.
In Europe, Merck KGaA continues to invest in IP covering liquid crystal and polymer-based diffusive films, supporting the region’s robust automotive and architectural display sectors. Japanese firms such as Nitto Denko Corporation are also notable for their patenting of optical adhesive and multilayer diffusion film technologies, which are increasingly vital for flexible and curved display applications.
Regional innovation hubs are emerging, with significant R&D clusters in East Asia (South Korea, Japan, Taiwan), Germany, and select U.S. states (notably California and Massachusetts). These regions benefit from proximity to advanced materials suppliers, precision manufacturing infrastructure, and collaborative research ecosystems. For example, 3M in the U.S. is advancing light management film innovations, leveraging its proprietary microreplication and optical coating capabilities to support diffused surface displays in automotive and consumer markets.
The next few years are expected to see an escalation in cross-licensing agreements and defensive patent strategies, as companies seek to navigate the increasingly crowded IP landscape. Collaborative consortia, such as those supported by SEMI, are fostering pre-competitive research and establishing interoperability standards for diffused display components. This collaborative environment may help mitigate litigation risk and accelerate commercialization cycles.
Looking ahead, the interplay between proprietary materials, process innovation, and regional specialization will likely define the industry’s competitive dynamics. Firms that can rapidly translate patented advances in diffusion layer materials and manufacturing methods into scalable, reliable products will be best positioned in the evolving global market for diffused surface displays.
Sustainability and Regulatory Drivers in Fabrication Processes
The fabrication of diffused surface displays is increasingly shaped by stringent sustainability goals and evolving regulatory frameworks in 2025 and the coming years. As display technologies continue to permeate a wide range of applications—from automotive dashboards to architectural installations—manufacturers are under intensifying pressure to reduce the environmental impact of both their materials and production processes.
A primary sustainability focus is the reduction of hazardous substances in display manufacturing, particularly those outlined by directives like the European Union’s RoHS (Restriction of Hazardous Substances) and REACH (Registration, Evaluation, Authorisation and Restriction of Chemicals). Leading display makers such as LG Display and Samsung Display are accelerating the transition towards halogen-free flame retardants and phasing out cadmium-based quantum dots, fostering compliance and environmental responsibility.
Recent process innovations emphasize resource efficiency and energy reduction. For example, Sharp Corporation has publicly committed to adopting low-temperature fabrication techniques for thin-film transistor (TFT) backplanes, which significantly cut greenhouse gas emissions and lower energy consumption compared to conventional high-temperature processes. Meanwhile, Kyocera is investing in water recycling systems within its display production facilities, aiming to minimize water usage and improve waste management.
Recyclability and end-of-life strategies are also at the forefront of regulatory and corporate agendas. Organizations like Acer are integrating circular economy principles by designing displays with modular architectures, enabling easier disassembly and material recovery. This approach aligns with extended producer responsibility (EPR) policies being adopted or expanded in several regions, mandating manufacturers to take greater accountability for post-consumer waste.
Looking ahead, regulatory pressure is expected to intensify, especially concerning carbon footprint disclosures and lifecycle assessments for display products. Industry bodies such as the VDMA (German Mechanical Engineering Industry Association) are working on developing standardized sustainability metrics and certifications specific to electronic display fabrication. These initiatives are set to influence procurement decisions and supply chain collaborations across the industry.
In summary, sustainability and regulatory drivers are fundamentally reshaping how diffused surface displays are fabricated. The sector is witnessing a convergence of innovative eco-friendly processes, stricter compliance measures, and a growing emphasis on circularity—trends that will define competitive advantage and compliance in the next several years.
Future Outlook: Disruptive Opportunities and Risks for Stakeholders
The field of diffused surface display fabrication stands at a pivotal juncture in 2025, poised for rapid evolution as both opportunities and risks emerge for stakeholders across the value chain. Driven by advances in materials science, manufacturing techniques, and integration with smart systems, the next few years are likely to see disruptive developments that reshape market dynamics and technological possibilities.
One major opportunity lies in the integration of diffused surface displays into automotive interiors, where demand for seamless, non-distracting interfaces is surging. Companies like Continental AG and LG Display are actively developing and showcasing large-area, flexible displays that utilize diffused surface technologies to improve visibility and reduce glare, enhancing driver safety and experience. Similarly, the architectural and retail sectors are adopting diffused surface displays for dynamic signage and ambient communication, as evidenced by product launches from AGC Inc. and Saint-Gobain that embed display capability directly into glass and composite surfaces.
From a fabrication standpoint, 2025 brings ongoing refinement of nanoimprinting and roll-to-roll manufacturing processes, which promise cost-effective scalability for producing large diffused display panels. Companies such as Mitsubishi Electric are pioneering automated assembly lines capable of embedding micro-optical structures at high speed, while Covestro is advancing polymer formulations that offer improved light diffusion without compromising mechanical strength or transparency. These developments are expected to lower barriers to entry and foster broader adoption across new application areas.
However, these disruptive opportunities are counterbalanced by several emerging risks. Intellectual property (IP) disputes over micro-patterning techniques and proprietary materials remain a significant concern, as seen in ongoing litigation between major display manufacturers. Additionally, the need for standardized testing and certification protocols has become acute, with industry bodies such as the Display Alliance and Society for Information Display (SID) working to establish guidelines for performance, safety, and environmental impact.
Looking ahead, stakeholders must navigate potential supply chain disruptions, particularly for rare-earth dopants and specialty polymers, which could be exacerbated by geopolitical tensions and resource constraints. Proactive investment in circularity and recycling solutions—championed by firms like Dow—will be crucial for mitigating long-term risks and meeting regulatory demands. In sum, while the future of diffused surface display fabrication is rich with promise, it will require strategic collaboration and innovation to fully realize its potential and manage attendant risks.