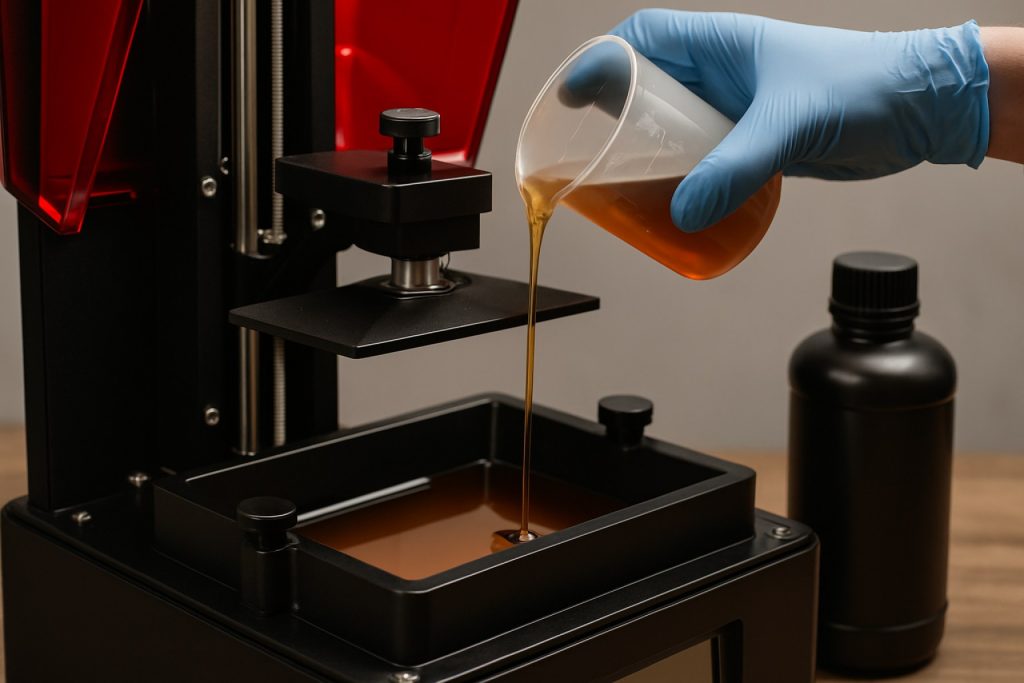
Digital Light Processing (DLP) 3D Printer Resin Formulation in 2025: Innovations, Market Dynamics, and the Road Ahead. Explore how advanced chemistries and application demands are reshaping the future of additive manufacturing.
- Executive Summary: Key Trends and Market Drivers
- Technology Overview: DLP 3D Printing and Resin Chemistry Fundamentals
- Current State of DLP Resin Formulation (2025)
- Major Players and Strategic Initiatives
- Emerging Materials: Bio-based, High-Performance, and Functional Resins
- Regulatory Landscape and Industry Standards
- Market Forecasts: Volume, Value, and Regional Growth (2025–2030)
- Application Spotlight: Dental, Jewelry, Prototyping, and Industrial Uses
- Challenges and Opportunities: Sustainability, Cost, and Performance
- Future Outlook: Innovation Pipelines and Next-Gen DLP Resin Technologies
- Sources & References
Executive Summary: Key Trends and Market Drivers
The Digital Light Processing (DLP) 3D printer resin formulation sector is experiencing rapid innovation and expansion in 2025, driven by advances in photopolymer chemistry, increasing demand for high-performance materials, and the growing adoption of DLP technology across industries. Key trends shaping the market include the development of specialized resins for end-use applications, sustainability initiatives, and the integration of smart material functionalities.
A major driver is the push for higher resolution and faster print speeds, which has led to the formulation of resins with optimized viscosity, reactivity, and mechanical properties. Leading manufacturers such as Stratasys and 3D Systems are investing in proprietary resin chemistries that enable finer feature detail and improved surface finish, catering to sectors like dental, jewelry, and electronics. The demand for biocompatible and medical-grade resins is also surging, with companies like Formlabs and EnvisionTEC (now part of Desktop Metal) expanding their portfolios to include materials certified for medical and dental use.
Sustainability is emerging as a significant trend, with resin formulators focusing on bio-based and recyclable photopolymers. Companies such as BASF and Evonik are developing eco-friendly resin solutions, responding to regulatory pressures and customer demand for greener manufacturing. These efforts are complemented by initiatives to reduce hazardous substances and improve the recyclability of printed parts.
Another key trend is the customization of resins for specific industrial applications. For example, Henkel and Liqcreate are collaborating with OEMs to tailor resin formulations for automotive, aerospace, and consumer goods, focusing on properties such as heat resistance, flexibility, and impact strength. The integration of functional additives—such as conductive, flame-retardant, or antimicrobial agents—is expanding the utility of DLP-printed parts in demanding environments.
Looking ahead, the DLP resin market is expected to benefit from ongoing R&D in photoinitiator systems, pigment dispersion, and post-processing techniques. The convergence of digital manufacturing and material science is likely to yield new classes of smart resins with tunable properties, further broadening the scope of DLP 3D printing. As the ecosystem matures, partnerships between resin suppliers, printer manufacturers, and end-users will be crucial in driving innovation and meeting the evolving needs of the market.
Technology Overview: DLP 3D Printing and Resin Chemistry Fundamentals
Digital Light Processing (DLP) 3D printing is a vat photopolymerization technology that utilizes a digital light projector to selectively cure liquid photopolymer resins layer by layer, producing highly detailed and accurate parts. The core of DLP’s performance lies in the formulation of its resins, which are engineered to respond rapidly and precisely to specific wavelengths of light, typically in the 385–405 nm range. As of 2025, advances in both projector technology and resin chemistry are driving significant improvements in print speed, resolution, and material properties.
DLP resins are complex mixtures, generally composed of oligomers, monomers, photoinitiators, and various additives. The oligomers and monomers form the backbone of the cured polymer, determining mechanical properties such as strength, flexibility, and heat resistance. Photoinitiators are critical for initiating polymerization upon exposure to light, and their selection is closely matched to the projector’s emission spectrum for optimal efficiency. Additives may include pigments, stabilizers, and fillers to tailor color, viscosity, and performance characteristics.
Recent years have seen a shift toward more specialized and high-performance resin formulations. For example, Formlabs and EnvisionTEC (now part of Desktop Metal) have introduced engineering-grade resins with enhanced mechanical and thermal properties, suitable for end-use parts and functional prototypes. Biocompatible and dental resins are also a major focus, with companies like Dentsply Sirona and Kulzer developing materials certified for medical and dental applications.
A key trend in 2025 is the development of low-viscosity, fast-curing resins that enable higher throughput without sacrificing detail. This is facilitated by new photoinitiator systems and oligomer blends, as well as improved projector light engines. Additionally, sustainability is becoming a priority, with manufacturers such as Carbon and Stratasys exploring bio-based and recyclable resin components to reduce environmental impact.
Looking ahead, the outlook for DLP resin formulation is marked by continued innovation in material diversity and performance. The integration of functional additives—such as ceramics, conductive fillers, or flame retardants—is expected to expand the range of applications in automotive, aerospace, and electronics. Furthermore, open material platforms and partnerships between printer manufacturers and chemical companies are likely to accelerate the pace of resin development, making DLP 3D printing increasingly versatile and accessible across industries.
Current State of DLP Resin Formulation (2025)
As of 2025, Digital Light Processing (DLP) 3D printer resin formulation stands at a pivotal point, driven by rapid advancements in photopolymer chemistry, increasing application diversity, and growing demand for high-performance materials. DLP technology, which utilizes projected light to cure liquid resin layer by layer, relies heavily on the quality and properties of its photopolymer resins. The current state of DLP resin formulation is characterized by a focus on improved mechanical properties, biocompatibility, and sustainability, as well as the expansion of functional and specialty resins.
Leading manufacturers such as Formlabs, 3D Systems, and EnvisionTEC (now part of Desktop Metal) have significantly expanded their resin portfolios in recent years. These companies offer a wide range of resins tailored for specific applications, including dental, jewelry, engineering, and medical devices. For example, Formlabs has introduced resins with enhanced toughness, flexibility, and temperature resistance, while 3D Systems continues to develop biocompatible and castable materials for healthcare and manufacturing sectors.
Material innovation is also being driven by the need for faster print speeds and higher resolution. The development of low-viscosity resins with optimized photoinitiator systems allows for rapid layer curing and finer feature reproduction. Additionally, the integration of ceramic and composite fillers into photopolymer matrices is enabling the production of parts with improved strength, heat resistance, and functional properties. Companies like EnvisionTEC and Formlabs have both released composite and ceramic-filled resins targeting industrial and dental applications.
Sustainability is an emerging priority in resin formulation. Efforts are underway to reduce the environmental impact of DLP resins by incorporating bio-based monomers and developing recyclable or less toxic formulations. While fully biodegradable DLP resins remain in early stages, several manufacturers are actively researching greener alternatives to conventional acrylate-based systems.
Looking ahead, the DLP resin market is expected to see continued diversification, with a strong emphasis on application-specific materials and regulatory compliance, especially in medical and dental fields. The ongoing collaboration between resin formulators, printer manufacturers, and end-users is likely to accelerate the pace of innovation, ensuring that DLP 3D printing remains at the forefront of additive manufacturing technology.
Major Players and Strategic Initiatives
The landscape of Digital Light Processing (DLP) 3D printer resin formulation in 2025 is shaped by a dynamic interplay of established chemical giants, specialized additive manufacturing firms, and emerging innovators. These major players are driving advancements in resin chemistry, sustainability, and application-specific performance, responding to the growing demand for high-resolution, functional, and environmentally conscious materials.
Among the most influential companies, BASF continues to leverage its extensive chemical expertise to develop photopolymer resins tailored for DLP applications. Its subsidiary, Forward AM, has expanded its portfolio with engineering-grade resins targeting automotive, dental, and industrial prototyping sectors. Similarly, Evonik Industries is investing in specialty monomers and oligomers, focusing on biocompatible and high-strength formulations for medical and dental use. Both companies are emphasizing low-viscosity, fast-curing resins to improve print speed and part accuracy.
In the dedicated 3D printing space, Formlabs stands out for its vertically integrated approach, developing proprietary DLP resins optimized for its printers. The company’s 2025 initiatives include expanding its dental and engineering resin lines, with a focus on biocompatibility and regulatory compliance. Stratasys, through its Origin One platform, is collaborating with material partners to co-develop open-platform resins, accelerating the adoption of DLP in end-use part production.
Asian manufacturers are also asserting a strong presence. Shining 3D and Anycubic are scaling up their resin R&D, targeting affordability and improved mechanical properties for consumer and professional markets. These companies are increasingly focusing on low-odor, low-toxicity formulations to address user safety and regulatory trends.
Strategic initiatives across the sector include partnerships between resin formulators and printer manufacturers to ensure material-printer compatibility and certification. Sustainability is a growing priority, with companies like BASF and Evonik Industries investing in bio-based and recyclable resin chemistries. Additionally, open material platforms are gaining traction, enabling third-party resin development and fostering innovation.
Looking ahead, the next few years are expected to see accelerated development of high-performance, application-specific DLP resins, particularly for dental, medical, and industrial end-use parts. The convergence of material science, regulatory compliance, and sustainability will continue to shape strategic initiatives among the sector’s leading players.
Emerging Materials: Bio-based, High-Performance, and Functional Resins
The landscape of Digital Light Processing (DLP) 3D printer resin formulation is rapidly evolving in 2025, driven by the demand for sustainable, high-performance, and functionally enhanced materials. The industry is witnessing a marked shift toward bio-based resins, advanced engineering polymers, and smart materials that expand the application scope of DLP technology.
Bio-based resins are gaining traction as environmental regulations tighten and end-users seek greener alternatives. Leading manufacturers such as Arkema and Covestro are investing in the development of photopolymer resins derived from renewable feedstocks, including plant-based acrylates and epoxies. These materials aim to reduce the carbon footprint of additive manufacturing while maintaining the mechanical and optical properties required for DLP processes. For instance, Covestro has announced ongoing research into partially bio-based polyurethane acrylates, targeting both prototyping and end-use part production.
Simultaneously, the demand for high-performance resins is accelerating, particularly in sectors such as dental, medical, and aerospace. Companies like Stratasys and 3D Systems are expanding their portfolios with engineering-grade photopolymers that offer enhanced heat resistance, toughness, and chemical stability. These resins are tailored for functional prototypes and short-run manufacturing, enabling DLP printers to produce parts that meet stringent industry standards. Notably, 3D Systems has introduced new dental and biocompatible resins, reflecting the growing importance of regulatory compliance and patient safety in resin formulation.
Functional resins—those with added properties such as conductivity, flexibility, or responsiveness to external stimuli—are also emerging as a key innovation area. Formlabs and EnvisionTEC (now part of Desktop Metal) are actively developing resins with embedded nanoparticles, elastomeric behavior, or tailored optical characteristics. These materials enable applications ranging from flexible electronics to microfluidic devices and optical components, broadening the utility of DLP printing beyond traditional prototyping.
Looking ahead, the next few years are expected to see further integration of bio-based content, improved recyclability, and the introduction of smart resins capable of self-healing or environmental sensing. Collaboration between resin formulators, printer manufacturers, and end-users will be crucial to accelerate the adoption of these advanced materials and to ensure compatibility with evolving DLP hardware platforms.
Regulatory Landscape and Industry Standards
The regulatory landscape and industry standards for Digital Light Processing (DLP) 3D printer resin formulation are evolving rapidly in 2025, reflecting the technology’s growing adoption in sectors such as healthcare, dental, automotive, and consumer goods. As DLP 3D printing moves from prototyping to end-use part production, regulatory scrutiny and standardization efforts are intensifying, particularly regarding resin safety, biocompatibility, and environmental impact.
In the United States, the U.S. Food and Drug Administration (FDA) continues to play a pivotal role in regulating DLP resins used for medical and dental applications. The FDA’s 510(k) clearance process and guidance on additive manufacturing of medical devices require manufacturers to demonstrate the biocompatibility and safety of photopolymer resins, including cytotoxicity, sensitization, and chemical leachables. Companies such as Stratasys and 3D Systems have developed medical-grade DLP resins that comply with these requirements, supporting their use in surgical guides, dental models, and custom implants.
In Europe, the International Organization for Standardization (ISO) and the European Committee for Standardization (CEN) are central to harmonizing standards for additive manufacturing materials. ISO/ASTM 52900 and related standards provide terminology and general principles, while ISO 10993 series addresses biological evaluation of medical devices, directly impacting resin formulation for healthcare. The new EU Medical Device Regulation (MDR), fully enforced since 2021, continues to influence resin manufacturers, requiring more rigorous clinical and material data for DLP-printed medical products.
Environmental and occupational safety regulations are also tightening. The U.S. Environmental Protection Agency (EPA) and the European Chemicals Agency (ECHA) are increasing oversight of photopolymer resin ingredients, particularly acrylates and photoinitiators, due to concerns about toxicity and environmental persistence. Resin manufacturers such as Formlabs and EnvisionTEC are responding by developing low-VOC, less hazardous, and recyclable resin formulations, and by providing detailed safety data sheets (SDS) and guidance for safe handling and disposal.
Looking ahead, industry groups like America Makes and the Additive Manufacturing UK are collaborating with regulatory bodies to establish best practices and certification pathways for DLP resin materials. The next few years are expected to see further alignment of global standards, increased transparency in resin composition, and the emergence of eco-labels or certifications for sustainable 3D printing materials. This evolving regulatory environment will drive innovation in resin chemistry and quality assurance, ensuring safer and more reliable DLP 3D printing across industries.
Market Forecasts: Volume, Value, and Regional Growth (2025–2030)
The market for Digital Light Processing (DLP) 3D printer resin formulation is poised for robust growth from 2025 through 2030, driven by expanding industrial adoption, advances in photopolymer chemistry, and increasing demand for high-performance, application-specific materials. As DLP technology matures, resin manufacturers are scaling up production and diversifying their portfolios to address the needs of sectors such as dental, medical, jewelry, and industrial prototyping.
In terms of volume, the global consumption of DLP-compatible resins is expected to rise steadily, with North America and Europe maintaining leading positions due to their established additive manufacturing ecosystems and strong presence of key players. Asia-Pacific, particularly China and South Korea, is anticipated to experience the fastest growth, fueled by investments in manufacturing infrastructure and the rapid expansion of local 3D printing industries. Companies such as Formlabs (USA), EnvisionTEC (now part of Desktop Metal, USA), and Photocentric (UK) are expanding their resin lines and production capacities to meet this rising demand.
From a value perspective, the DLP 3D printer resin market is projected to see a compound annual growth rate (CAGR) in the high single digits through 2030, with premium, specialty, and biocompatible resins commanding higher price points. The dental and medical sectors, in particular, are driving value growth due to stringent regulatory requirements and the need for certified, high-performance materials. 3D Systems and Stratasys are notable for their investments in medical-grade and dental resins, while Carbon (USA) continues to innovate in high-strength and elastomeric formulations for industrial and consumer applications.
Regionally, Europe is expected to maintain a strong market share, supported by initiatives to promote advanced manufacturing and sustainability in materials. Meanwhile, the Asia-Pacific region is likely to close the gap, with local resin producers such as Anycubic (China) and Creality (China) increasing their presence in both consumer and professional segments.
Looking ahead, the outlook for DLP 3D printer resin formulation is characterized by continued innovation in photopolymer chemistry, the emergence of recyclable and bio-based resins, and the integration of smart materials with enhanced mechanical and functional properties. As end-users demand greater customization and performance, resin manufacturers are expected to invest in R&D and regional production hubs, further accelerating market growth and diversification through 2030.
Application Spotlight: Dental, Jewelry, Prototyping, and Industrial Uses
Digital Light Processing (DLP) 3D printer resin formulation has rapidly evolved to meet the stringent requirements of specialized applications, notably in dental, jewelry, prototyping, and industrial sectors. As of 2025, the convergence of advanced photopolymer chemistry and precise light-based curing is enabling new levels of performance, accuracy, and material diversity across these fields.
Dental Applications: The dental sector remains a primary driver for DLP resin innovation. Dental resins must meet biocompatibility standards, high dimensional accuracy, and mechanical strength for crowns, bridges, surgical guides, and aligners. Companies such as Formlabs and 3D Systems have expanded their dental resin portfolios, offering Class IIa and Class I biocompatible materials certified for intraoral use. In 2025, the focus is on faster post-processing, improved translucency for lifelike aesthetics, and resins tailored for permanent restorations. The integration of antimicrobial additives and enhanced wear resistance is also being reported, addressing the longevity and hygiene demands of dental prosthetics.
Jewelry Manufacturing: DLP’s high resolution and smooth surface finish make it ideal for jewelry casting patterns. Leading suppliers like EnvisionTEC (now part of Desktop Metal) and B9Creations have introduced castable resins with low ash content and clean burnout properties, critical for investment casting. In 2025, the trend is toward resins that support ultra-fine detail, minimal shrinkage, and compatibility with a broader range of precious metal alloys. The ability to print intricate filigree and micro-pavé settings directly from digital designs is streamlining custom jewelry workflows and reducing lead times.
Prototyping: Rapid prototyping remains a core application for DLP, with resin formulations now offering a balance of speed, detail, and mechanical properties. Stratasys and Carbon are notable for their engineering-grade resins, which simulate ABS, polypropylene, and elastomers. In 2025, the emphasis is on multi-material printing, color accuracy, and functional prototyping—enabling iterative design cycles for consumer products, electronics, and automotive components. The adoption of tough, impact-resistant, and heat-stable resins is expanding the scope of DLP prototyping beyond visual models to functional testing.
Industrial Uses: Industrial users are leveraging DLP for end-use parts, jigs, fixtures, and tooling. Resin manufacturers such as Henkel (Loctite) and BASF (Forward AM) are developing photopolymers with enhanced chemical resistance, thermal stability, and mechanical strength. In 2025, the outlook includes the introduction of resins for electronics encapsulation, automotive under-the-hood components, and even aerospace-grade parts. The push for sustainability is also evident, with bio-based and recyclable resin options entering the market.
Across all sectors, the next few years will see continued collaboration between printer manufacturers and resin formulators, driving application-specific innovation and regulatory compliance. The result is a rapidly expanding palette of DLP resins, each engineered for the unique demands of dental, jewelry, prototyping, and industrial applications.
Challenges and Opportunities: Sustainability, Cost, and Performance
The formulation of resins for Digital Light Processing (DLP) 3D printers in 2025 is shaped by a dynamic interplay of sustainability, cost, and performance imperatives. As the DLP 3D printing market matures, resin manufacturers and end-users are increasingly focused on addressing environmental concerns, reducing material costs, and enhancing the mechanical and functional properties of printed parts.
Sustainability is a central challenge and opportunity. Traditional DLP resins are predominantly based on petroleum-derived acrylates and methacrylates, which raise concerns about environmental impact and end-of-life disposal. In response, leading resin producers are investing in bio-based and recyclable alternatives. For example, BASF and Evonik are developing photopolymer resins incorporating renewable raw materials, aiming to reduce carbon footprints and improve biodegradability. However, these sustainable formulations often face hurdles in matching the mechanical strength, resolution, and curing speed of conventional resins, necessitating ongoing research and optimization.
Cost remains a significant barrier to broader adoption of DLP 3D printing, particularly in industrial and consumer markets. The high price of specialty photoinitiators, oligomers, and monomers used in DLP resins contributes to the overall expense. Companies such as Formlabs and Stratasys are working to streamline supply chains and scale up production, which is expected to gradually lower costs over the next few years. Additionally, the emergence of open-material platforms and third-party resin suppliers is fostering competition and price reductions, though this also introduces challenges in ensuring consistent print quality and printer-resin compatibility.
Performance demands are intensifying as DLP 3D printing expands into sectors such as dental, medical, and industrial manufacturing. Users require resins with tailored properties—such as high heat resistance, biocompatibility, and flexibility—without sacrificing print speed or resolution. 3D Systems and EnvisionTEC (now part of Desktop Metal) are at the forefront of developing application-specific resins, including those for dental prosthetics and engineering-grade components. The integration of nanomaterials and hybrid chemistries is a promising avenue for enhancing performance, though it introduces new complexities in formulation and regulatory approval.
Looking ahead, the DLP resin sector is poised for significant innovation, driven by regulatory pressures, customer demand for greener solutions, and the need for cost-effective, high-performance materials. Collaboration between chemical companies, printer manufacturers, and end-users will be crucial in overcoming current limitations and unlocking the full potential of DLP 3D printing in the coming years.
Future Outlook: Innovation Pipelines and Next-Gen DLP Resin Technologies
The future of Digital Light Processing (DLP) 3D printer resin formulation is poised for significant transformation as the industry enters 2025 and beyond. Key players are intensifying research and development efforts to address the evolving demands of industrial, dental, medical, and consumer applications. The innovation pipeline is characterized by a focus on advanced material properties, sustainability, and process optimization.
One of the most prominent trends is the development of high-performance resins with enhanced mechanical, thermal, and chemical resistance. Companies such as Stratasys and 3D Systems are investing in photopolymer chemistries that enable end-use parts with properties rivaling traditional thermoplastics. These next-generation resins are expected to expand DLP’s reach into functional prototyping and low-volume manufacturing, particularly in automotive and aerospace sectors.
Biocompatibility and regulatory compliance are also driving innovation, especially in dental and medical markets. Formlabs and Dentsply Sirona are advancing resin formulations that meet stringent ISO and FDA standards, enabling the direct production of dental prosthetics, surgical guides, and hearing aids. The push for faster curing times and improved accuracy is leading to the integration of novel photoinitiators and oligomer blends, which are expected to become mainstream in the next few years.
Sustainability is another critical area of focus. Companies like BASF and Evonik are developing bio-based and recyclable photopolymers, aiming to reduce the environmental footprint of DLP printing. These efforts align with broader industry goals to minimize waste and enable circular material flows, a trend likely to accelerate as regulatory pressures mount.
Process optimization is being addressed through the formulation of low-viscosity resins that enable faster print speeds and higher resolution. EnvisionTEC (now part of Desktop Metal) and Carbon are at the forefront, leveraging proprietary resin chemistries and hardware-software integration to push the boundaries of DLP throughput and part quality.
Looking ahead, the convergence of smart materials—such as self-healing or stimuli-responsive resins—and digital manufacturing workflows is anticipated. Industry leaders are collaborating with academic institutions to accelerate the commercialization of these advanced materials. As a result, the next few years are expected to see DLP resin formulations that not only meet but exceed the requirements of demanding applications, solidifying DLP’s role in the additive manufacturing landscape.
Sources & References
- Stratasys
- 3D Systems
- Formlabs
- BASF
- Evonik
- Henkel
- Liqcreate
- Formlabs
- Dentsply Sirona
- Kulzer
- Carbon
- Stratasys
- 3D Systems
- BASF
- Shining 3D
- Anycubic
- Arkema
- Covestro
- International Organization for Standardization
- European Committee for Standardization
- Anycubic
- Creality
- Henkel
- BASF
- Dentsply Sirona
- Carbon