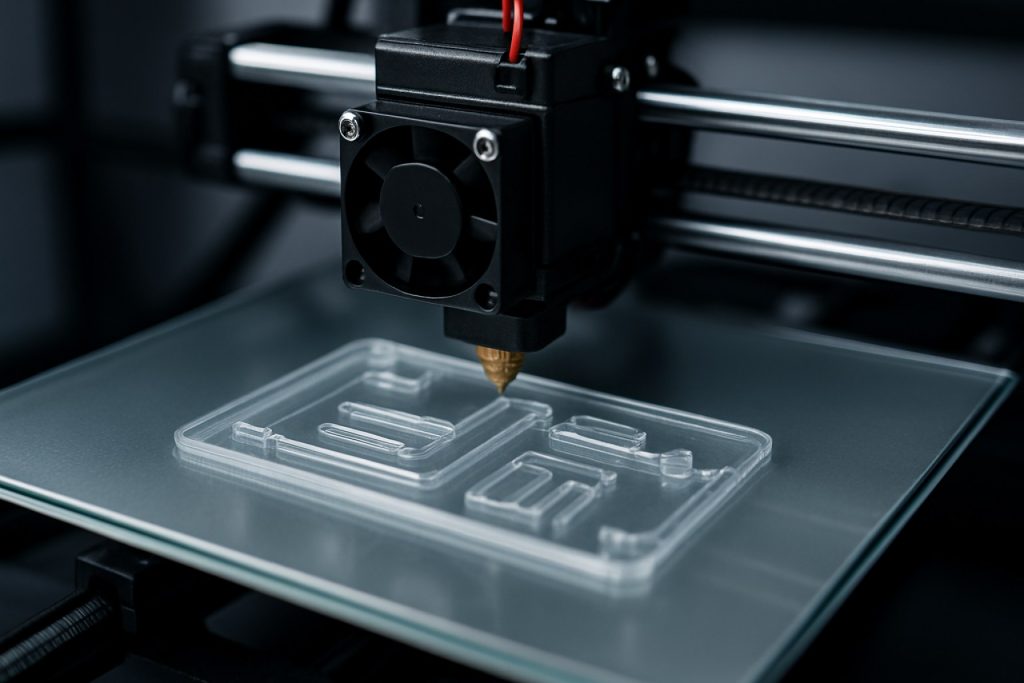
How FDM 3D Printing is Transforming Microfluidics: Unlocking Rapid Prototyping, Customization, and Affordable Innovation for Lab-on-a-Chip Devices. Discover the Game-Changing Synergy Between Additive Manufacturing and Microfluidic Research. (2025)
- Introduction: The Intersection of FDM 3D Printing and Microfluidics
- Fundamentals of Fused Deposition Modeling (FDM) Technology
- Microfluidic Device Design: Opportunities and Challenges with FDM
- Material Selection and Biocompatibility in FDM Microfluidics
- Resolution, Accuracy, and Surface Quality: Overcoming FDM Limitations
- Case Studies: Successful FDM-Printed Microfluidic Applications
- Comparative Analysis: FDM vs. Other 3D Printing Methods for Microfluidics
- Market Trends and Growth Forecast: FDM in Microfluidics (Estimated 20–30% CAGR through 2030)
- Emerging Innovations: Hybrid Manufacturing and Functional Integration
- Future Outlook: Scaling Up, Standardization, and Expanding Public Interest
- Sources & References
Introduction: The Intersection of FDM 3D Printing and Microfluidics
Fused Deposition Modeling (FDM) 3D printing has emerged as a transformative technology in the field of microfluidics, offering new avenues for rapid prototyping, customization, and cost-effective device fabrication. Microfluidics, which involves the manipulation of fluids at the sub-millimeter scale, is foundational to advancements in biomedical diagnostics, chemical synthesis, and environmental monitoring. Traditionally, microfluidic devices have been fabricated using photolithography and soft lithography, processes that are often time-consuming, expensive, and require specialized facilities. The integration of FDM 3D printing into microfluidics is reshaping this landscape, particularly as the technology matures in 2025 and beyond.
FDM 3D printing operates by extruding thermoplastic materials layer by layer to build three-dimensional objects. Its accessibility, affordability, and compatibility with a range of polymers have made it a popular choice for academic and industrial research groups. In recent years, improvements in printer resolution, material properties, and software control have enabled the fabrication of microfluidic channels with dimensions approaching 100 micrometers, a significant milestone for the field. Organizations such as National Institute of Standards and Technology (NIST) and National Institutes of Health (NIH) have highlighted the potential of 3D printing technologies, including FDM, to democratize access to microfluidic device development and accelerate innovation in point-of-care diagnostics and lab-on-a-chip systems.
The year 2025 marks a period of rapid adoption and refinement of FDM-based microfluidic fabrication. Open-source hardware initiatives and collaborative platforms are driving the dissemination of design files and best practices, lowering barriers for entry and fostering a global community of practitioners. Leading universities and research centers are publishing protocols and case studies demonstrating the successful application of FDM-printed microfluidics in areas such as cell culture, droplet generation, and chemical analysis. The National Science Foundation (NSF) continues to fund interdisciplinary research that leverages FDM 3D printing for microfluidic innovation, emphasizing the importance of reproducibility, scalability, and integration with electronic and optical components.
Looking ahead, the intersection of FDM 3D printing and microfluidics is expected to yield further breakthroughs in device complexity, multi-material integration, and functionalization. As material science advances and printer capabilities improve, FDM is poised to play a central role in the next generation of microfluidic technologies, supporting both fundamental research and real-world applications in healthcare, environmental science, and beyond.
Fundamentals of Fused Deposition Modeling (FDM) Technology
Fused Deposition Modeling (FDM) is a widely adopted additive manufacturing technique that has gained significant traction in the field of microfluidics, especially as the technology matures into 2025. FDM operates by extruding thermoplastic filaments through a heated nozzle, depositing material layer by layer to build three-dimensional objects. The process is governed by precise control of temperature, extrusion rate, and movement along the X, Y, and Z axes, enabling the fabrication of complex geometries with reasonable accuracy and repeatability.
In microfluidics, the demand for rapid prototyping and cost-effective device fabrication has driven the adoption of FDM. Traditional microfabrication methods, such as soft lithography, require cleanroom facilities and are time-consuming, whereas FDM offers a desktop alternative that can produce functional microfluidic devices within hours. Recent advances in FDM hardware and materials have improved the resolution and chemical compatibility of printed devices, making them increasingly suitable for applications in diagnostics, chemical synthesis, and biological assays.
Key to FDM’s application in microfluidics is the ability to print channels and chambers with dimensions on the order of hundreds of micrometers. While FDM is inherently limited by nozzle diameter and layer height—typically resulting in minimum feature sizes of 200–400 μm—ongoing research is pushing these boundaries. In 2025, several research groups and companies are experimenting with finer nozzles, optimized print parameters, and post-processing techniques to achieve smaller, smoother channels. For example, the use of water-soluble support materials allows for the creation of enclosed microchannels, which are subsequently cleared by dissolving the support, a method increasingly adopted in academic and industrial settings.
Material selection is another critical aspect. Common FDM materials such as polylactic acid (PLA) and acrylonitrile butadiene styrene (ABS) are valued for their ease of use and biocompatibility, but new filaments with enhanced chemical resistance and optical transparency are being developed to meet the specific needs of microfluidic applications. Organizations like National Institute of Standards and Technology (NIST) are actively involved in standardizing material properties and print protocols to ensure reproducibility and reliability in microfluidic device fabrication.
Looking ahead, the outlook for FDM in microfluidics is promising. The convergence of improved printer resolution, advanced materials, and open-source design repositories is expected to further democratize access to microfluidic technology. As FDM printers become more affordable and capable, their role in rapid prototyping and even small-scale production of microfluidic devices is set to expand, supporting innovation in point-of-care diagnostics, environmental monitoring, and educational tools through 2025 and beyond.
Microfluidic Device Design: Opportunities and Challenges with FDM
Fused Deposition Modeling (FDM) 3D printing has emerged as a transformative technology in the design and prototyping of microfluidic devices, offering rapid, cost-effective, and accessible fabrication. As of 2025, the microfluidics community is increasingly leveraging FDM to address longstanding challenges in device development, particularly for applications in diagnostics, chemical synthesis, and point-of-care testing.
One of the primary opportunities FDM presents is the democratization of microfluidic device fabrication. Traditional methods, such as soft lithography, require cleanroom facilities and specialized expertise, limiting accessibility. In contrast, FDM printers are widely available and affordable, enabling researchers and small laboratories to iterate designs quickly. This has led to a surge in open-source microfluidic projects and collaborative innovation, as seen in initiatives supported by organizations like the National Institute of Standards and Technology (NIST), which actively promotes standards and best practices for additive manufacturing in scientific research.
Recent advances in FDM hardware and materials have further expanded its utility. The introduction of finer nozzles, improved stepper motors, and temperature control systems has enabled the printing of channels with dimensions approaching 200 micrometers, a significant improvement over earlier generations. Material science developments, including the availability of transparent and chemically resistant filaments, have addressed some of the compatibility issues that previously limited FDM’s use in microfluidics. For example, the National Institute of Standards and Technology has published guidelines on the characterization of 3D-printed polymers for fluidic applications, supporting reproducibility and reliability.
Despite these advances, challenges remain. Achieving truly microscale features (<100 micrometers) is still difficult due to the inherent limitations of FDM’s layer-by-layer deposition and nozzle size. Surface roughness and channel fidelity can impact fluid flow and device performance, necessitating post-processing steps such as solvent smoothing or coating. Additionally, the range of biocompatible and optically clear materials suitable for FDM is still limited compared to other 3D printing methods like stereolithography (SLA).
Looking ahead, ongoing research is focused on hybrid fabrication approaches, combining FDM with other techniques to overcome current limitations. The development of new composite filaments and multi-material printing capabilities is expected to further enhance the functionality of FDM-fabricated microfluidic devices. Organizations such as the National Institute of Standards and Technology and the National Science Foundation are anticipated to play key roles in standardizing processes and supporting innovation in this rapidly evolving field. As these efforts mature, FDM is poised to become an even more integral tool in the microfluidics design landscape through 2025 and beyond.
Material Selection and Biocompatibility in FDM Microfluidics
Material selection and biocompatibility are pivotal considerations in the advancement of Fused Deposition Modeling (FDM) 3D printing for microfluidic applications, especially as the field moves into 2025 and beyond. The choice of thermoplastic materials directly impacts device performance, chemical compatibility, and suitability for biological assays. Traditionally, FDM has relied on polymers such as polylactic acid (PLA), acrylonitrile butadiene styrene (ABS), and polyethylene terephthalate glycol (PETG). These materials are favored for their printability and mechanical properties, but their biocompatibility and chemical resistance vary significantly.
Recent years have seen a surge in research and development aimed at expanding the material palette for FDM microfluidics. PLA, a biodegradable polymer derived from renewable resources, remains popular due to its ease of use and general biocompatibility, making it suitable for certain cell culture and diagnostic applications. However, its limited chemical resistance and moderate thermal stability restrict its use in more demanding microfluidic environments. PETG, on the other hand, offers improved chemical resistance and transparency, which are advantageous for optical detection and imaging in microfluidic devices. ABS, while robust, often requires post-processing to remove toxic additives and improve surface properties for biological applications.
A key trend for 2025 is the development and commercialization of specialty FDM filaments tailored for microfluidics. These include medical-grade and certified biocompatible polymers, as well as composite materials with enhanced surface smoothness and reduced leachables. For example, research groups and companies are exploring the use of cyclic olefin copolymer (COC) and polycarbonate (PC) blends, which offer superior optical clarity and chemical inertness. The integration of antimicrobial additives and surface treatments is also being investigated to reduce biofouling and improve device longevity.
Biocompatibility testing is increasingly standardized, with protocols aligning to international standards such as ISO 10993 for biological evaluation of medical devices. Organizations like the International Organization for Standardization and regulatory bodies such as the U.S. Food and Drug Administration are providing clearer guidance on the requirements for materials used in biomedical microfluidics. This regulatory clarity is expected to accelerate the adoption of FDM-printed microfluidic devices in clinical and research settings.
Looking ahead, the outlook for material selection in FDM microfluidics is promising. Ongoing collaborations between material scientists, device engineers, and regulatory agencies are likely to yield new filaments with tailored properties for specific microfluidic applications. The convergence of open-source material development and commercial innovation is expected to further democratize access to biocompatible FDM printing, supporting the rapid prototyping and deployment of next-generation microfluidic devices.
Resolution, Accuracy, and Surface Quality: Overcoming FDM Limitations
Fused Deposition Modeling (FDM) 3D printing has become an increasingly accessible tool for prototyping and fabricating microfluidic devices. However, its adoption in microfluidics has been historically limited by challenges in resolution, accuracy, and surface quality—critical parameters for the reliable function of micro-scale fluidic channels. As of 2025, significant progress is being made to address these limitations, driven by both hardware innovation and process optimization.
The minimum feature size achievable by standard FDM printers typically ranges from 200 to 400 micrometers, which is larger than the sub-100 micrometer features often required in advanced microfluidic applications. Recent advances in nozzle design, extrusion control, and motion systems are pushing these boundaries. For example, manufacturers are introducing finer nozzles (down to 0.1 mm) and more precise stepper motors, enabling improved dimensional accuracy and repeatability. Companies such as Ultimaker and Prusa Research are at the forefront of these hardware developments, offering open-source platforms that facilitate rapid iteration and customization for research needs.
Surface roughness remains a key challenge, as the layer-by-layer deposition inherent to FDM creates striations that can disrupt laminar flow and promote unwanted mixing or adsorption in microfluidic channels. In 2025, researchers are increasingly employing post-processing techniques such as solvent vapor smoothing, mechanical polishing, and resin infiltration to reduce surface roughness to below 10 micrometers Ra, which is approaching the threshold for many microfluidic applications. Additionally, the use of new thermoplastic filaments with improved flow characteristics and lower melting points is being explored to enhance print fidelity and surface finish.
Accuracy in channel geometry is also being improved through real-time process monitoring and closed-loop feedback systems. Integration of machine vision and in-situ metrology allows for the detection and correction of print defects during fabrication, a trend supported by collaborative efforts between academic research groups and industry partners. Organizations such as the National Institute of Standards and Technology (NIST) are actively developing standards and best practices for additive manufacturing in microfluidics, which is expected to accelerate the adoption of FDM for functional device fabrication.
Looking ahead, the outlook for FDM in microfluidics is optimistic. The convergence of hardware improvements, material science advances, and digital process control is expected to further close the gap between FDM and higher-resolution techniques such as stereolithography (SLA) and two-photon polymerization. As open-source communities and standards bodies continue to drive innovation, FDM is poised to become a viable, cost-effective option for rapid prototyping and even small-batch production of microfluidic devices in the coming years.
Case Studies: Successful FDM-Printed Microfluidic Applications
In recent years, Fused Deposition Modeling (FDM) 3D printing has emerged as a practical and accessible method for fabricating microfluidic devices, with several successful case studies demonstrating its potential in both research and applied settings. As of 2025, the field has seen notable advancements in the resolution, material compatibility, and functional integration of FDM-printed microfluidic systems.
One prominent example is the use of FDM-printed microfluidic chips for point-of-care diagnostics. Researchers at leading academic institutions have developed low-cost, rapid-prototyping workflows using FDM printers to create devices for blood plasma separation and pathogen detection. These devices, fabricated from biocompatible thermoplastics such as polylactic acid (PLA) and polyethylene terephthalate glycol (PETG), have demonstrated reliable fluid handling and compatibility with standard laboratory assays. The National Institutes of Health has supported several projects exploring FDM-printed microfluidics for rapid disease screening, particularly in resource-limited settings.
Another successful application involves environmental monitoring. In 2024, a collaborative project between European research centers and environmental agencies utilized FDM-printed microfluidic platforms for on-site water quality analysis. These devices integrated sensors and reagent reservoirs directly into the printed structure, enabling real-time detection of contaminants such as heavy metals and nitrates. The Swiss Federal Laboratories for Materials Science and Technology (Empa) has published data on the durability and chemical resistance of FDM-printed microfluidic devices in field conditions, highlighting their suitability for rugged applications.
In the pharmaceutical sector, FDM-printed microfluidic reactors have been employed for continuous-flow synthesis and drug screening. Companies and research groups have reported the successful fabrication of modular, customizable reactors that can be rapidly iterated to optimize reaction conditions. The U.S. Food and Drug Administration has acknowledged the growing role of 3D printing in pharmaceutical manufacturing, including the use of FDM for prototyping and process development.
Looking ahead, the next few years are expected to bring further integration of FDM-printed microfluidics with electronics and sensors, enabling smart lab-on-a-chip systems. Ongoing improvements in printer resolution and material science, supported by organizations such as the National Institute of Standards and Technology (NIST), are likely to expand the range of applications and enhance device performance. These case studies underscore the versatility and impact of FDM 3D printing in advancing microfluidic technology across diverse fields.
Comparative Analysis: FDM vs. Other 3D Printing Methods for Microfluidics
Fused Deposition Modeling (FDM) has emerged as a widely accessible 3D printing technology for microfluidic device fabrication, but its comparative performance against other additive manufacturing methods—such as Stereolithography (SLA), Digital Light Processing (DLP), and PolyJet—remains a subject of active research and development. As of 2025, the microfluidics community is increasingly focused on evaluating these technologies in terms of resolution, material compatibility, cost, and scalability.
FDM’s primary advantage lies in its affordability and widespread availability. Open-source hardware and a broad range of thermoplastic filaments have made FDM printers a staple in academic and prototyping environments. However, the technology’s layer-by-layer extrusion process typically limits its minimum feature size to around 200–400 micrometers, which is less precise than the sub-100 micrometer features achievable with SLA or DLP. This limitation is significant for microfluidic applications that require fine channel geometries and smooth internal surfaces to ensure laminar flow and prevent sample loss.
Recent advances in FDM, such as the use of finer nozzles and optimized printing parameters, have narrowed the resolution gap. Research groups are also experimenting with post-processing techniques—like solvent vapor smoothing and surface coatings—to improve channel fidelity and reduce surface roughness. Nevertheless, SLA and DLP, which use photopolymerization to cure resin layer-by-layer, continue to offer superior surface finish and feature resolution. These methods are increasingly adopted for microfluidic prototyping, especially in applications demanding high precision, such as single-cell analysis and droplet generation.
Material compatibility is another differentiator. FDM supports a variety of thermoplastics, including biocompatible and chemically resistant options like polylactic acid (PLA) and acrylonitrile butadiene styrene (ABS). However, SLA and DLP resins can be engineered for specific optical, mechanical, or chemical properties, expanding their utility in specialized microfluidic applications. PolyJet technology, offered by companies such as Stratasys, enables multi-material printing with high resolution, but at a higher cost and with more complex post-processing.
Cost and accessibility remain strong points for FDM. Entry-level FDM printers are significantly less expensive than SLA, DLP, or PolyJet systems, making them attractive for rapid prototyping and educational use. The open-source movement, championed by organizations like the RepRap Project, continues to drive innovation and democratize access to FDM technology.
Looking ahead, the next few years are expected to see further improvements in FDM print resolution and material diversity, narrowing the gap with photopolymer-based methods. Hybrid approaches—combining FDM with post-processing or integrating FDM-printed components with other fabrication techniques—are likely to expand the range of microfluidic applications. As the field matures, the choice between FDM and alternative 3D printing methods will increasingly depend on the specific requirements of each microfluidic device, balancing cost, resolution, and material needs.
Market Trends and Growth Forecast: FDM in Microfluidics (Estimated 20–30% CAGR through 2030)
Fused Deposition Modeling (FDM) 3D printing has rapidly gained traction in the microfluidics sector, driven by its accessibility, cost-effectiveness, and ongoing improvements in print resolution and material compatibility. As of 2025, the market for FDM 3D printing in microfluidics is experiencing robust growth, with industry analysts and research institutions projecting a compound annual growth rate (CAGR) in the range of 20–30% through 2030. This expansion is fueled by increasing adoption in academic research, prototyping, and even early-stage commercial production of microfluidic devices.
Key drivers of this growth include the democratization of microfluidic device fabrication, as FDM printers become more affordable and user-friendly. Major manufacturers such as Ultimaker and Stratasys have introduced FDM systems with enhanced precision and a broader range of biocompatible and chemically resistant thermoplastics, making them suitable for microfluidic applications. The open-source hardware and software movement, championed by organizations like the RepRap Project, continues to lower barriers for entry, enabling more laboratories and startups to design and fabricate custom microfluidic chips in-house.
Recent years have seen a surge in published research and patent filings related to FDM-fabricated microfluidic devices, particularly in the fields of point-of-care diagnostics, environmental monitoring, and organ-on-chip systems. Academic consortia and public research bodies, such as the National Institutes of Health (NIH), have funded initiatives to standardize FDM-based microfluidic fabrication protocols, further legitimizing the technology for biomedical and analytical applications.
Looking ahead, the outlook for FDM 3D printing in microfluidics remains highly positive. Ongoing advancements in printhead technology, multi-material printing, and post-processing techniques are expected to further close the gap between FDM and higher-resolution additive manufacturing methods. Industry stakeholders anticipate that by 2030, FDM will not only dominate rapid prototyping but also play a significant role in the low-volume production of functional microfluidic devices, especially for custom and decentralized applications.
- Wider adoption in educational and resource-limited settings is expected, as FDM printers become even more accessible.
- Collaborations between printer manufacturers, material scientists, and microfluidics researchers are likely to yield new printable polymers tailored for microfluidic performance.
- Regulatory bodies, including the U.S. Food and Drug Administration (FDA), are anticipated to develop clearer guidelines for the use of 3D-printed microfluidic devices in clinical and diagnostic settings.
In summary, the FDM 3D printing market in microfluidics is poised for sustained double-digit growth, underpinned by technological innovation, expanding application domains, and increasing institutional support.
Emerging Innovations: Hybrid Manufacturing and Functional Integration
Fused Deposition Modeling (FDM) 3D printing has rapidly evolved as a key enabler in the fabrication of microfluidic devices, particularly as the field moves toward hybrid manufacturing and functional integration. As of 2025, the convergence of FDM with other manufacturing techniques—such as direct ink writing, laser micromachining, and soft lithography—is driving a new era of device complexity and performance. This hybrid approach allows for the integration of multiple materials, embedded sensors, and active components directly into microfluidic chips, addressing longstanding challenges in device miniaturization and multifunctionality.
Recent years have seen the emergence of FDM-compatible filaments with enhanced properties, including improved transparency, chemical resistance, and biocompatibility. These materials are being developed and validated by leading research institutions and industry players, enabling the fabrication of microfluidic devices suitable for biomedical diagnostics, organ-on-chip systems, and environmental monitoring. For example, the National Institute of Standards and Technology (NIST) has been actively involved in standardizing materials and processes for 3D-printed microfluidics, ensuring reproducibility and reliability in critical applications.
Hybrid manufacturing workflows are now leveraging the strengths of FDM—such as rapid prototyping and cost-effectiveness—while overcoming its limitations in resolution and surface finish by combining it with high-precision post-processing or complementary additive techniques. This has enabled the creation of microfluidic devices with integrated electrodes, optical waveguides, and even microvalves, expanding the functional repertoire of lab-on-a-chip platforms. Organizations like the Nature Publishing Group and Elsevier have documented a surge in peer-reviewed publications detailing these hybrid strategies, reflecting a growing consensus on their transformative potential.
Looking ahead, the next few years are expected to witness further integration of FDM with digital manufacturing ecosystems, including automated design optimization and in-line quality control. The adoption of open-source hardware and software platforms is also accelerating, democratizing access to advanced microfluidic fabrication and fostering global collaboration. Initiatives by the National Institutes of Health (NIH) and the National Science Foundation (NSF) are supporting interdisciplinary research in this area, with a focus on translational applications in healthcare and environmental science.
In summary, FDM 3D printing is poised to play a central role in the next generation of microfluidic devices, with hybrid manufacturing and functional integration at the forefront of innovation. As material science, process engineering, and digital design continue to advance, the boundaries of what is possible in microfluidics are set to expand significantly through 2025 and beyond.
Future Outlook: Scaling Up, Standardization, and Expanding Public Interest
The future of Fused Deposition Modeling (FDM) 3D printing in microfluidics is poised for significant transformation as the field moves toward broader adoption, standardization, and public engagement. As of 2025, FDM remains one of the most accessible and cost-effective additive manufacturing techniques, making it a cornerstone for democratizing microfluidic device fabrication in both academic and industrial settings.
A key trend is the scaling up of FDM-based microfluidic production. Recent advances in printer resolution, multi-material extrusion, and filament formulation are enabling the fabrication of more complex and functional microfluidic architectures. Leading manufacturers such as Ultimaker and Prusa Research are actively developing hardware and open-source software improvements that support finer feature sizes and more reliable channel sealing, which are critical for microfluidic applications. These developments are expected to lower the barrier for prototyping and small-batch production, especially in resource-limited environments.
Standardization is emerging as a central focus for the field. Organizations like the International Organization for Standardization (ISO) and the National Institute of Standards and Technology (NIST) are increasingly involved in establishing guidelines for 3D-printed microfluidic devices, including dimensional tolerances, material biocompatibility, and device performance metrics. Such standards are crucial for ensuring reproducibility and interoperability, particularly as FDM-printed microfluidics transition from research prototypes to commercial and clinical products.
Public interest in microfluidics, fueled by the COVID-19 pandemic’s spotlight on rapid diagnostics and point-of-care testing, is expected to grow further as FDM 3D printing makes device fabrication more accessible. Educational initiatives and open-source projects, such as those promoted by the National Institutes of Health (NIH), are expanding awareness and training in digital design and fabrication. This democratization is likely to foster a new generation of citizen scientists and entrepreneurs, accelerating innovation in fields ranging from environmental monitoring to personalized medicine.
Looking ahead, the next few years will likely see FDM 3D printing in microfluidics move toward greater automation, integration with digital design tools, and adoption of sustainable materials. As the ecosystem matures, collaborations between industry, academia, and regulatory bodies will be essential to address challenges in quality assurance and regulatory approval, paving the way for widespread deployment of FDM-printed microfluidic solutions.
Sources & References
- National Institute of Standards and Technology
- National Institutes of Health
- National Science Foundation
- International Organization for Standardization
- Ultimaker
- Prusa Research
- National Institute of Standards and Technology (NIST)
- Swiss Federal Laboratories for Materials Science and Technology (Empa)
- Stratasys
- RepRap Project
- National Institutes of Health
- Nature Publishing Group
- Elsevier
- International Organization for Standardization