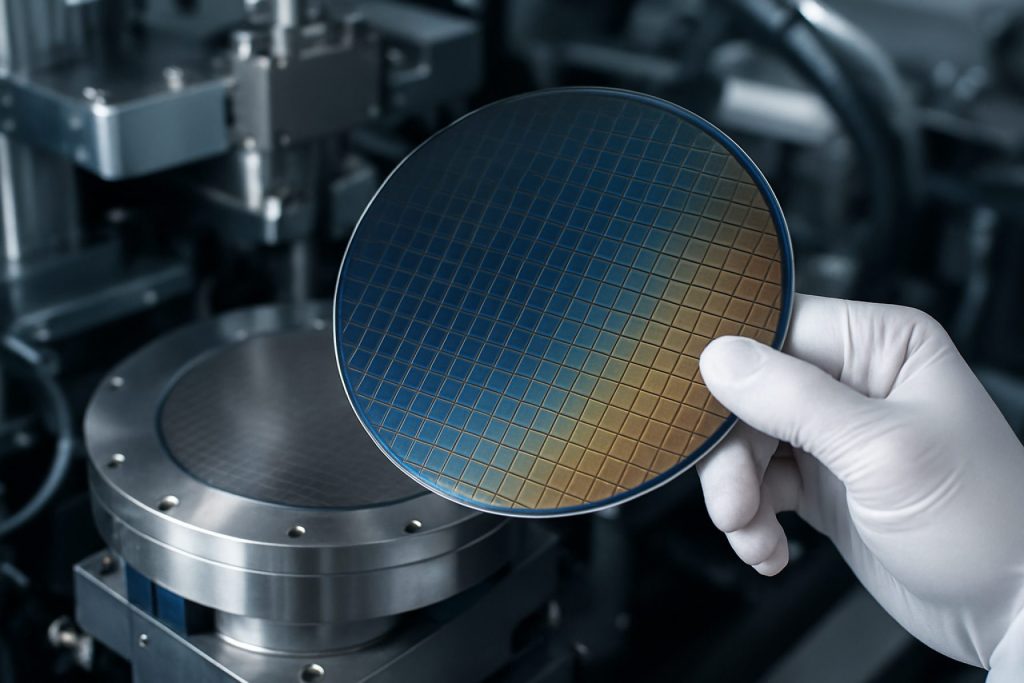
Gallium Nitride Semiconductor Fabrication in 2025: Unleashing High-Efficiency Power and RF Solutions for a Rapidly Evolving Electronics Landscape. Explore Market Growth, Technological Breakthroughs, and Strategic Opportunities Shaping the Next Five Years.
- Executive Summary: Key Trends and 2025 Outlook
- Market Size, Growth Forecasts, and Regional Hotspots (2025–2030)
- Core Technologies: GaN Substrates, Epitaxy, and Device Architectures
- Manufacturing Innovations: Process Advances and Yield Optimization
- Major Players and Strategic Partnerships (Citing infineon.com, navitassemi.com, gan.com, ieee.org)
- GaN vs. Silicon: Performance, Cost, and Adoption Barriers
- Applications: Power Electronics, RF, Automotive, and Data Centers
- Supply Chain Dynamics and Raw Material Sourcing
- Regulatory, Environmental, and Industry Standards (Referencing ieee.org, semiconductors.org)
- Future Outlook: Disruptive Trends, Investment Hotspots, and Roadmap to 2030
- Sources & References
Executive Summary: Key Trends and 2025 Outlook
Gallium Nitride (GaN) semiconductor fabrication is entering a pivotal phase in 2025, driven by surging demand for high-efficiency power electronics, radio frequency (RF) devices, and next-generation optoelectronics. GaN’s superior material properties—such as wide bandgap, high electron mobility, and thermal stability—are enabling rapid advancements in electric vehicles (EVs), 5G infrastructure, data centers, and renewable energy systems. The global transition toward electrification and digitalization is accelerating the adoption of GaN-based devices, with fabrication technologies evolving to meet stringent performance and scalability requirements.
Key industry players are scaling up their GaN manufacturing capabilities. Infineon Technologies AG has expanded its GaN-on-silicon production lines, targeting automotive and industrial power conversion markets. STMicroelectronics is investing in dedicated GaN wafer fabs, aiming to deliver discrete and integrated solutions for consumer and industrial applications. NXP Semiconductors is advancing GaN RF technology for 5G base stations and aerospace, while Wolfspeed, Inc. continues to ramp up its Mohawk Valley Fab, the world’s largest 200mm GaN and SiC facility, to address power and RF device demand.
On the supply chain front, substrate innovation and wafer scaling are critical trends. The shift from 150mm to 200mm GaN-on-silicon wafers is underway, promising higher yields and lower costs per device. ams OSRAM and KYOCERA Corporation are among those developing advanced GaN substrates and epitaxy processes to support mass production. Meanwhile, foundry services from Taiwan Semiconductor Manufacturing Company (TSMC) and GLOBALFOUNDRIES are making GaN fabrication accessible to fabless design houses, accelerating innovation cycles.
Looking ahead, the 2025 outlook for GaN semiconductor fabrication is robust. Industry forecasts anticipate double-digit annual growth rates, with automotive electrification, fast-charging infrastructure, and 5G/6G deployments as primary drivers. Strategic partnerships, vertical integration, and government-backed initiatives—especially in the US, Europe, and Asia—are expected to further strengthen the GaN ecosystem. As process maturity improves and economies of scale are realized, GaN is poised to capture a larger share of the power and RF semiconductor markets, reshaping the competitive landscape for years to come.
Market Size, Growth Forecasts, and Regional Hotspots (2025–2030)
The global market for gallium nitride (GaN) semiconductor fabrication is poised for robust expansion between 2025 and 2030, driven by surging demand in power electronics, radio frequency (RF) devices, and optoelectronics. GaN’s superior properties—such as high electron mobility, wide bandgap, and thermal stability—are catalyzing its adoption in electric vehicles, 5G infrastructure, data centers, and renewable energy systems.
In 2025, the GaN semiconductor sector is expected to see significant investments in both substrate and device manufacturing. Leading wafer suppliers such as Ammono (now part of OSRAM), Sumitomo Chemical, and Kyocera are scaling up production of high-quality GaN substrates, while device manufacturers like Infineon Technologies, NXP Semiconductors, STMicroelectronics, and onsemi are expanding their GaN device portfolios for automotive and industrial applications.
Asia-Pacific remains the dominant regional hotspot, with countries such as Japan, Taiwan, South Korea, and China investing heavily in GaN fabrication infrastructure. Japanese firms, including Panasonic and ROHM Semiconductor, are advancing GaN-on-Si and GaN-on-SiC technologies, while Taiwan’s TSMC and WIN Semiconductors are ramping up foundry services for GaN RF and power devices. In China, state-backed initiatives are accelerating domestic GaN wafer and device production, with companies like Sanan Optoelectronics and Changelight expanding capacity.
In North America, the United States is witnessing increased activity from both established players and startups. Wolfspeed (formerly Cree) is investing in large-scale GaN and SiC wafer fabs, while Navitas Semiconductor and GaN Systems (now part of Infineon Technologies) are pushing innovations in GaN power ICs. Europe is also emerging as a key region, with Infineon Technologies and STMicroelectronics leading R&D and manufacturing efforts.
Looking ahead to 2030, the GaN semiconductor fabrication market is projected to experience double-digit annual growth, underpinned by the electrification of transport, expansion of 5G/6G networks, and the proliferation of high-efficiency power conversion systems. Regional competition is expected to intensify, with Asia-Pacific maintaining its lead but with notable capacity expansions in North America and Europe as governments and industry seek to localize supply chains and secure strategic semiconductor capabilities.
Core Technologies: GaN Substrates, Epitaxy, and Device Architectures
Gallium Nitride (GaN) semiconductor fabrication is undergoing rapid evolution in 2025, driven by advances in substrate technology, epitaxial growth, and device architectures. The industry’s focus is on scaling production, improving material quality, and enabling new device classes for power electronics, RF, and optoelectronics.
A critical bottleneck in GaN device performance and cost has been the availability of high-quality native GaN substrates. Historically, most GaN devices have been fabricated on foreign substrates such as silicon (Si), silicon carbide (SiC), or sapphire, due to the high cost and limited size of native GaN wafers. However, in 2025, several manufacturers are scaling up production of larger-diameter native GaN substrates. Ammono and Sumitomo Chemical are among the leaders in bulk GaN crystal growth, with Sumitomo Chemical offering 2-inch and 4-inch GaN wafers for high-performance applications. These native substrates reduce dislocation densities and enable higher breakdown voltages and efficiency in power devices.
Epitaxial growth remains a cornerstone of GaN fabrication. Metal-Organic Chemical Vapor Deposition (MOCVD) is the dominant technique, with equipment suppliers such as AIXTRON and Veeco Instruments providing advanced reactors capable of uniform, high-throughput deposition on 6-inch and even 8-inch wafers. In 2025, the industry is seeing increased adoption of advanced in-situ monitoring and automation to improve yield and reproducibility. Innovations in buffer layer engineering and strain management are further reducing defect densities, especially for GaN-on-Si and GaN-on-SiC platforms.
Device architectures are also advancing rapidly. Lateral High Electron Mobility Transistors (HEMTs) remain the workhorse for RF and power switching, but vertical GaN devices are gaining traction due to their superior voltage handling and current capability. Companies like Panasonic and NexGen Power Systems are developing vertical GaN power devices targeting automotive and industrial markets. Meanwhile, Infineon Technologies and STMicroelectronics are expanding their GaN device portfolios, leveraging proprietary process technologies to enhance performance and reliability.
Looking ahead, the next few years are expected to bring further scaling of native GaN substrate production, broader adoption of 8-inch GaN-on-Si epitaxy, and commercialization of vertical GaN devices. These advances will underpin the expansion of GaN semiconductors into mainstream power conversion, 5G/6G communications, and emerging applications such as electric vehicles and data centers.
Manufacturing Innovations: Process Advances and Yield Optimization
The fabrication of gallium nitride (GaN) semiconductors is undergoing rapid innovation in 2025, driven by the demand for high-performance power electronics, RF devices, and next-generation optoelectronics. Key advances are centered on process integration, substrate engineering, and yield optimization, as leading manufacturers and equipment suppliers invest in scaling up production and improving device reliability.
A major trend is the transition from traditional sapphire and silicon carbide (SiC) substrates to large-diameter silicon wafers for GaN epitaxy. This shift enables compatibility with existing CMOS fabs and leverages mature 200 mm and 300 mm wafer processing lines, significantly reducing costs and improving throughput. Companies such as Infineon Technologies AG and NXP Semiconductors have announced expanded GaN-on-Si production, with Infineon commissioning new 200 mm GaN lines in Austria and Malaysia. This move is expected to double GaN device output by 2026, while also improving process uniformity and yield.
Epitaxial growth techniques are also evolving. Metal-organic chemical vapor deposition (MOCVD) remains the dominant method, but recent innovations focus on in-situ monitoring and advanced precursor delivery systems to minimize defects and improve layer uniformity. ams OSRAM and KYOCERA Corporation are investing in proprietary MOCVD reactor designs and real-time process control, targeting higher yields for both power and optoelectronic GaN devices.
Yield optimization is further supported by the adoption of advanced metrology and inspection tools. Inline defect inspection, atomic force microscopy, and X-ray diffraction are increasingly integrated into production lines to detect and mitigate dislocations, cracks, and contamination at early stages. Advantest Corporation and KLA Corporation are supplying next-generation inspection systems tailored for GaN’s unique material properties, enabling rapid feedback and process correction.
Looking ahead, the industry is also exploring vertical device architectures and novel etching techniques to further enhance device performance and manufacturing efficiency. Collaborative efforts, such as those led by STMicroelectronics and ROHM Co., Ltd., are expected to yield new process flows that reduce defect densities and improve scalability for automotive and industrial applications.
Overall, the next few years will see GaN fabrication processes become more standardized, with a strong emphasis on yield, cost reduction, and integration with mainstream semiconductor manufacturing. These innovations are poised to accelerate the adoption of GaN devices across a broad range of high-growth markets.
Major Players and Strategic Partnerships (Citing infineon.com, navitassemi.com, gan.com, ieee.org)
The landscape of Gallium Nitride (GaN) semiconductor fabrication in 2025 is defined by the activities of several major players and a growing web of strategic partnerships. As demand for high-efficiency power electronics and RF devices accelerates, companies are scaling up production, investing in new facilities, and collaborating to address supply chain and technology challenges.
One of the most prominent companies in the GaN sector is Infineon Technologies AG. Infineon has made significant investments in GaN-on-silicon technology, targeting automotive, industrial, and consumer applications. In recent years, Infineon has expanded its GaN product portfolio and manufacturing capabilities, including the integration of GaN devices into its power electronics solutions. The company’s strategy includes both in-house fabrication and partnerships with foundries to ensure supply resilience and scalability.
Another key player is Navitas Semiconductor, which specializes exclusively in GaN power ICs. Navitas has pioneered the development of monolithically integrated GaN power solutions, enabling higher efficiency and smaller form factors for fast chargers, data centers, and renewable energy systems. The company has established manufacturing partnerships with leading foundries to ramp up production and meet growing global demand. Navitas’ focus on vertical integration and close collaboration with supply chain partners positions it as a leader in the commercialization of GaN technology.
Vertically integrated manufacturers such as GaN Systems are also shaping the market. GaN Systems has developed proprietary GaN transistor designs and works closely with partners across the automotive, industrial, and consumer electronics sectors. The company’s approach includes strategic alliances with module makers and OEMs to accelerate the adoption of GaN-based solutions in high-growth markets.
Industry organizations like the IEEE play a crucial role in fostering collaboration and standardization within the GaN ecosystem. Through conferences, technical committees, and working groups, IEEE brings together manufacturers, researchers, and end-users to address technical challenges, share best practices, and develop industry standards that support the reliable and scalable fabrication of GaN semiconductors.
Looking ahead to the next few years, the GaN fabrication sector is expected to see further consolidation and deeper partnerships, as companies seek to secure supply chains, optimize manufacturing processes, and accelerate innovation. The interplay between established semiconductor giants, specialized GaN firms, and collaborative industry bodies will be central to the continued growth and maturation of the GaN semiconductor market.
GaN vs. Silicon: Performance, Cost, and Adoption Barriers
Gallium nitride (GaN) semiconductors have emerged as a disruptive technology, challenging the long-standing dominance of silicon (Si) in power electronics, RF devices, and optoelectronics. As of 2025, the performance advantages of GaN over silicon are well established: GaN devices offer higher breakdown voltages, faster switching speeds, and greater efficiency, particularly in high-frequency and high-power applications. These characteristics make GaN highly attractive for sectors such as electric vehicles, 5G infrastructure, data centers, and renewable energy systems.
In terms of fabrication, GaN presents unique challenges and opportunities compared to silicon. While silicon benefits from decades of process optimization and a vast, mature supply chain, GaN fabrication is still evolving. Most commercial GaN devices are produced using heteroepitaxy, typically growing GaN layers on silicon, silicon carbide (SiC), or sapphire substrates. Each substrate choice impacts cost, yield, and device performance. For example, GaN-on-Si is favored for its compatibility with existing silicon fabs and lower substrate costs, but GaN-on-SiC offers superior thermal conductivity and device reliability, albeit at a higher price point.
Leading manufacturers such as Infineon Technologies AG, NXP Semiconductors N.V., and STMicroelectronics N.V. have expanded their GaN portfolios, investing in both discrete devices and integrated solutions. Infineon Technologies AG has ramped up production of GaN-on-Si power devices, targeting automotive and industrial markets. NXP Semiconductors N.V. focuses on GaN RF solutions for 5G and aerospace, while STMicroelectronics N.V. is developing GaN power transistors for consumer and industrial applications. Additionally, Wolfspeed, Inc. (formerly Cree) is a major supplier of both GaN and SiC materials and devices, leveraging its expertise in wide bandgap semiconductors.
Despite these advances, cost remains a significant barrier to widespread GaN adoption. GaN wafers and epitaxial processes are more expensive than their silicon counterparts, and yield challenges persist, especially for larger wafer diameters. However, the industry is making progress: 6-inch and even 8-inch GaN-on-Si wafers are entering production, promising improved economies of scale. Companies like imec are collaborating with foundries to optimize GaN process integration on standard silicon lines, aiming to reduce costs and accelerate adoption.
Looking ahead, the next few years are expected to see continued cost reductions, higher yields, and broader adoption of GaN devices, particularly as automotive and data center sectors demand higher efficiency and power density. However, silicon’s entrenched infrastructure and lower cost will ensure its continued relevance, especially in cost-sensitive, high-volume applications. The GaN vs. silicon dynamic will thus remain a central theme in semiconductor fabrication, with GaN steadily gaining ground where its performance advantages justify the investment.
Applications: Power Electronics, RF, Automotive, and Data Centers
Gallium Nitride (GaN) semiconductor fabrication is rapidly transforming several high-impact application domains, notably power electronics, radio frequency (RF) systems, automotive electronics, and data center infrastructure. As of 2025, the industry is witnessing accelerated adoption of GaN devices, driven by their superior efficiency, high breakdown voltage, and fast switching capabilities compared to traditional silicon-based semiconductors.
In power electronics, GaN transistors and diodes are increasingly deployed in applications such as power supplies, inverters, and fast chargers. Major manufacturers like Infineon Technologies AG and NXP Semiconductors have expanded their GaN product portfolios, targeting consumer electronics, industrial automation, and renewable energy systems. For instance, Infineon’s CoolGaN™ technology is being integrated into high-efficiency power conversion systems, enabling smaller, lighter, and more energy-efficient devices. The trend is expected to intensify through 2025 and beyond, as OEMs seek to meet stringent energy efficiency standards and reduce system footprints.
In RF applications, GaN’s high electron mobility and power density make it the material of choice for 5G base stations, satellite communications, and radar systems. Qorvo, Inc. and Cree, Inc. (now operating its semiconductor business as Wolfspeed) are at the forefront, supplying GaN-on-SiC and GaN-on-Silicon RF devices to telecom and defense sectors. Qorvo’s GaN RF solutions are integral to next-generation wireless infrastructure, supporting higher frequencies and greater bandwidths. Wolfspeed, meanwhile, continues to scale up its 200mm GaN wafer fabrication, aiming to meet surging demand for high-power RF components.
The automotive sector is another key growth area. GaN-based power devices are being adopted in electric vehicle (EV) onboard chargers, DC-DC converters, and traction inverters, offering higher efficiency and reduced cooling requirements. STMicroelectronics and ROHM Semiconductor have announced collaborations with leading automotive OEMs to integrate GaN technology into next-generation EV platforms. These partnerships are expected to yield commercial deployments by 2025, as automakers prioritize range extension and system miniaturization.
Data centers, facing mounting pressure to improve energy efficiency, are turning to GaN power ICs for server power supplies and high-density power distribution units. Navitas Semiconductor and Transphorm, Inc. are notable players, with both companies ramping up production of GaN-based solutions tailored for hyperscale and enterprise data centers. Their devices enable significant reductions in power loss and thermal management costs, supporting the sector’s sustainability goals.
Looking ahead, the GaN semiconductor fabrication ecosystem is poised for robust growth, with ongoing investments in 200mm wafer technology, vertical integration, and automotive-grade reliability. As fabrication yields improve and costs decline, GaN is set to become a mainstream technology across power, RF, automotive, and data center applications through the latter half of the decade.
Supply Chain Dynamics and Raw Material Sourcing
The supply chain for gallium nitride (GaN) semiconductor fabrication is undergoing significant transformation as global demand for high-performance power electronics and RF devices accelerates into 2025. GaN’s unique properties—such as high electron mobility and wide bandgap—make it a critical material for applications in electric vehicles, 5G infrastructure, and renewable energy systems. However, the supply chain for GaN devices is complex, involving the sourcing of high-purity gallium, advanced substrate materials, and specialized epitaxial growth processes.
Gallium, the primary raw material for GaN, is typically obtained as a byproduct of aluminum and zinc production. The majority of global gallium production is concentrated in a few countries, with Alcoa Corporation and United Company RUSAL among the notable producers of alumina from which gallium is extracted. China remains the dominant supplier of primary gallium, accounting for over 90% of global output, which has raised concerns about supply security and price volatility. In response, several semiconductor manufacturers are seeking to diversify their sourcing strategies and invest in recycling technologies to recover gallium from industrial waste streams.
The fabrication of GaN devices also relies on high-quality substrates. While native GaN substrates offer superior performance, they are expensive and limited in availability. As a result, most commercial GaN devices are grown on silicon carbide (SiC) or sapphire substrates. Companies such as Wolfspeed, Inc. (formerly Cree) and Kyocera Corporation are leading suppliers of SiC substrates, while Saint-Gobain and Sumitomo Chemical provide sapphire wafers. The ongoing expansion of substrate manufacturing capacity is expected to alleviate some supply constraints by 2025, but the industry remains sensitive to fluctuations in raw material availability and pricing.
Epitaxial growth, typically performed using metal-organic chemical vapor deposition (MOCVD), is another critical step in the GaN supply chain. Equipment suppliers such as AIXTRON SE and Veeco Instruments Inc. are scaling up production to meet the growing demand for GaN epitaxy tools. Meanwhile, integrated device manufacturers like Infineon Technologies AG and NXP Semiconductors are investing in vertical integration and long-term supply agreements to secure access to both raw materials and advanced manufacturing equipment.
Looking ahead, the GaN semiconductor supply chain is expected to become more resilient as new sources of gallium are developed, recycling initiatives mature, and substrate production expands. However, geopolitical factors and the concentration of gallium refining capacity remain potential risks. Industry stakeholders are likely to continue pursuing diversification and strategic partnerships to ensure stable supply and support the rapid growth of GaN-based technologies through 2025 and beyond.
Regulatory, Environmental, and Industry Standards (Referencing ieee.org, semiconductors.org)
The regulatory, environmental, and industry standards landscape for Gallium Nitride (GaN) semiconductor fabrication is evolving rapidly as the technology matures and adoption accelerates in power electronics, RF, and automotive sectors. In 2025, regulatory frameworks are increasingly focused on both the unique material properties of GaN and the broader sustainability goals of the semiconductor industry.
Key industry standards for GaN device performance, reliability, and safety are being developed and refined by organizations such as the IEEE. The IEEE has established working groups dedicated to standardizing test methods and qualification procedures for GaN power devices, addressing issues such as high-voltage operation, thermal management, and long-term reliability. These standards are critical for ensuring interoperability and safety as GaN devices are integrated into electric vehicles, data centers, and renewable energy systems.
Environmental regulations are also shaping GaN fabrication processes. The Semiconductor Industry Association (SIA) and its global partners are advocating for responsible sourcing of gallium and nitrogen precursors, as well as the reduction of hazardous byproducts in metal-organic chemical vapor deposition (MOCVD) and other epitaxial growth techniques. In 2025, manufacturers are increasingly required to comply with international directives such as RoHS (Restriction of Hazardous Substances) and REACH (Registration, Evaluation, Authorisation and Restriction of Chemicals), which limit the use of toxic materials and mandate transparent supply chains.
Industry-wide initiatives are underway to improve the energy efficiency and environmental footprint of GaN fabrication. Leading companies are investing in closed-loop water systems, advanced abatement technologies for process gases, and recycling of gallium-containing waste streams. These efforts align with the semiconductor sector’s broader commitment to net-zero emissions and resource conservation, as outlined by the Semiconductor Industry Association.
Looking ahead, the next few years will see further harmonization of global standards for GaN device qualification and environmental compliance. Collaborative efforts between industry, academia, and regulatory bodies are expected to accelerate the adoption of best practices, ensuring that GaN semiconductor fabrication remains both innovative and sustainable. As GaN technology becomes more pervasive, adherence to rigorous standards will be essential for market access, customer trust, and long-term industry growth.
Future Outlook: Disruptive Trends, Investment Hotspots, and Roadmap to 2030
The future of gallium nitride (GaN) semiconductor fabrication is poised for significant transformation as the industry approaches 2025 and looks toward 2030. GaN’s superior material properties—such as high electron mobility, wide bandgap, and thermal stability—are driving its adoption in power electronics, RF devices, and next-generation optoelectronics. Several disruptive trends are shaping the sector, with major investments and strategic roadmaps emerging from both established players and new entrants.
One of the most notable trends is the rapid scaling of GaN-on-silicon (GaN-on-Si) technology, which enables cost-effective, high-volume manufacturing using existing silicon foundry infrastructure. Leading companies such as Infineon Technologies AG and NXP Semiconductors N.V. are expanding their GaN portfolios, targeting automotive, industrial, and consumer applications. Infineon Technologies AG has announced significant investments in expanding its GaN production capacity in Europe, aiming to meet the surging demand for efficient power conversion in electric vehicles and renewable energy systems.
Another disruptive trend is the integration of GaN devices into advanced packaging and heterogeneous integration platforms. STMicroelectronics and Renesas Electronics Corporation are actively developing GaN-based power modules and system-in-package (SiP) solutions, which are expected to accelerate the adoption of GaN in data centers, 5G infrastructure, and AI hardware. These efforts are complemented by collaborations with foundry partners and equipment suppliers to optimize process yields and reliability.
Investment hotspots are emerging in Asia, Europe, and North America, with government-backed initiatives and public-private partnerships fueling R&D and pilot production lines. For example, ROHM Co., Ltd. and Panasonic Holdings Corporation are expanding their GaN device manufacturing in Japan, while Wolfspeed, Inc. is ramping up its Mohawk Valley Fab in the United States, which is dedicated to wide bandgap semiconductors including GaN.
Looking ahead to 2030, the GaN fabrication roadmap is expected to focus on further scaling wafer sizes (moving from 6-inch to 8-inch and beyond), improving defect densities, and developing vertical GaN device architectures for higher voltage and current handling. Industry bodies such as Semiconductor Industry Association are forecasting robust growth in GaN adoption, driven by electrification, digitalization, and the global push for energy efficiency. As the ecosystem matures, strategic alliances and supply chain investments will be critical to overcoming technical and economic barriers, positioning GaN as a cornerstone of next-generation semiconductor technology.
Sources & References
- Infineon Technologies AG
- STMicroelectronics
- NXP Semiconductors
- Wolfspeed, Inc.
- ams OSRAM
- KYOCERA Corporation
- OSRAM
- Sumitomo Chemical
- ROHM Semiconductor
- GaN Systems
- AIXTRON
- Veeco Instruments
- NexGen Power Systems
- Advantest Corporation
- KLA Corporation
- IEEE
- imec
- Cree, Inc.
- Alcoa Corporation
- United Company RUSAL
- IEEE
- Semiconductor Industry Association
- Semiconductor Industry Association