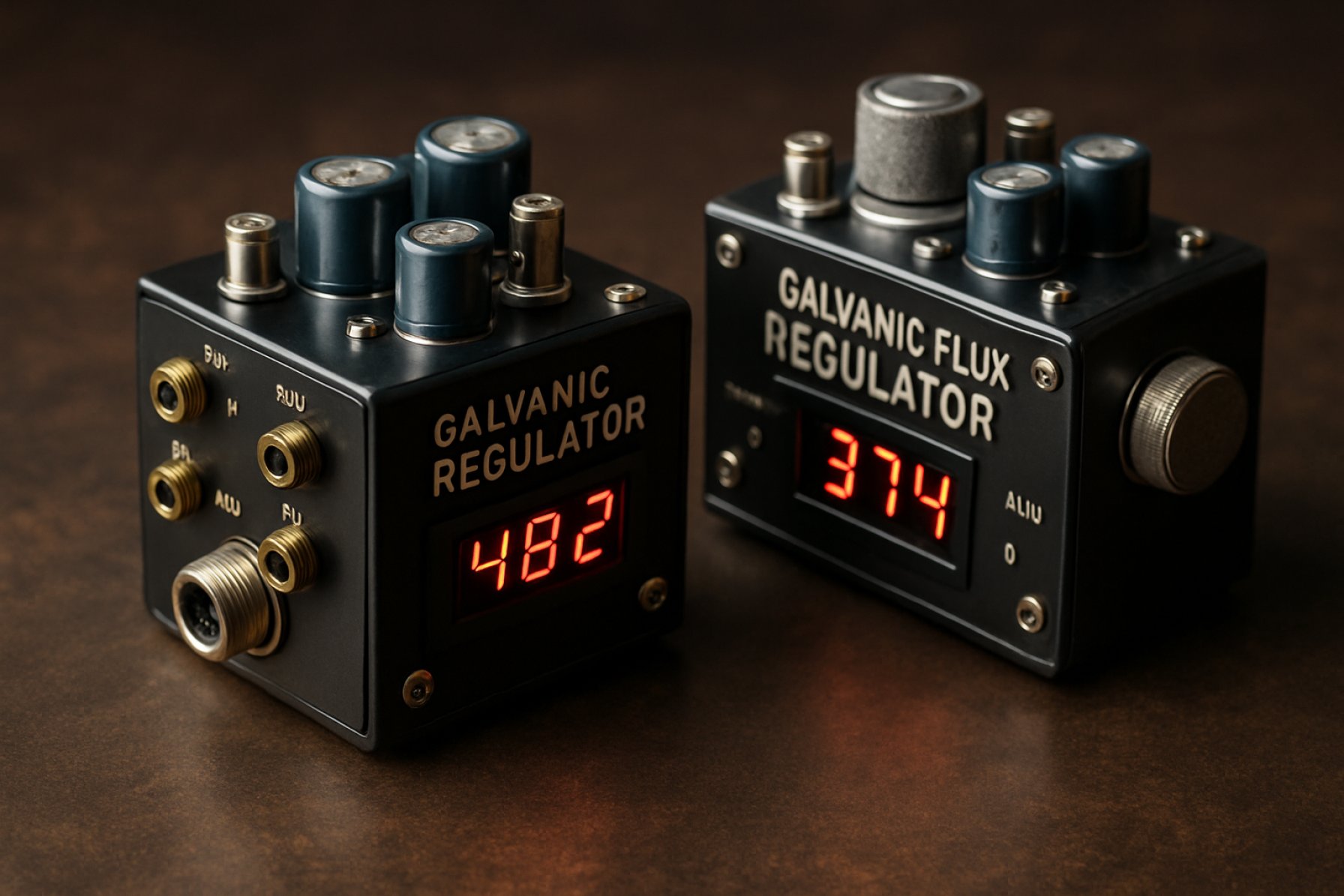
Table of Contents
- Executive Summary: Key Trends Shaping 2025
- Galvanic Flux Regulator Technology Overview
- Global Market Sizing & 3-Year Forecast (2025–2028)
- Major Players & Industry Leaders (Official Sources Only)
- Cutting-Edge Applications Across Sectors
- Regulatory Landscape and Standards (Referencing IEEE, ASME)
- Breakthrough Innovations Shaping the Future
- Supply Chain, Manufacturing, and Sustainability Factors
- Challenges, Risks, and Competitive Dynamics
- Future Outlook: Opportunities and Strategic Recommendations
- Sources & References
Executive Summary: Key Trends Shaping 2025
Galvanic flux regulators are emerging as a pivotal component in advanced manufacturing, power electronics, and energy storage systems, with 2025 marking a significant inflection point for both technological innovation and market adoption. These devices, which manage and stabilize ionic and electronic flows in electrochemical systems, are increasingly critical for next-generation battery management, fuel cell optimization, and precision electroplating processes.
Key trends shaping the sector in 2025 include the integration of galvanic flux regulators into high-performance lithium-ion and solid-state batteries to enhance charge/discharge efficiency and prolong cycle life. Leading battery manufacturers, such as Panasonic Corporation and LG Energy Solution, are investing in advanced flux regulation technologies to address issues of electrode degradation and thermal runaway, aiming to meet the surging demand for electric vehicles (EVs) and grid-scale energy storage. These regulators are also being incorporated into fuel cell stacks, with companies like Ballard Power Systems exploring their application for improved ionic control and efficiency in both stationary and mobile hydrogen applications.
The rise of automated manufacturing lines and Industry 4.0 frameworks is pushing for smarter, real-time flux regulation solutions. Automation leaders such as Siemens AG are collaborating with component suppliers to embed IoT-enabled galvanic regulators capable of predictive maintenance and fault detection. This digitalization trend is expected to drive operational cost savings and production yield improvements across sectors including automotive, aerospace, and microelectronics.
Materials innovation is another key trend, with suppliers like Umicore advancing high-stability alloy and ceramic interfaces for regulators, improving device lifespan and compatibility with aggressive electrolytes. In parallel, regulatory bodies such as the IEEE are developing updated standards for safety and interoperability, which are anticipated to influence procurement and integration strategies starting in 2025.
Looking ahead, the market outlook for galvanic flux regulators remains robust, underpinned by global decarbonization policies and the electrification of transport and industry. Ongoing R&D, led by both established manufacturers and new entrants, is expected to yield more compact, energy-efficient, and AI-compatible regulator modules, positioning this technology as a cornerstone of the next wave of industrial electrification.
Galvanic Flux Regulator Technology Overview
Galvanic flux regulators are specialized devices engineered to control and stabilize the flow of electric current between galvanic cells or within electrochemical systems, playing a crucial role in industries such as electronics manufacturing, corrosion protection, and advanced battery management. As of 2025, current developments in galvanic flux regulator technology are marked by a shift towards miniaturization, digital integration, and enhanced materials, reflecting broader trends in the electronics and energy storage sectors.
One of the major advancements in recent years is the integration of real-time monitoring and feedback systems. Leading manufacturers have begun incorporating microcontrollers and IoT connectivity into their galvanic flux regulators, allowing for remote adjustment and predictive maintenance. For example, AMETEK has introduced high-precision controllers that enable automated regulation of current flux, supporting both increased operational efficiency and data-driven process optimization in plating and surface treatment applications.
Material science advancements have also shaped the landscape of galvanic flux regulators. The adoption of corrosion-resistant alloys and advanced ceramic components has improved device longevity and accuracy. Companies like Sartorius have invested in the development of robust sensors that offer reliable current regulation even in aggressive chemical environments, addressing the needs of pharmaceutical and semiconductor manufacturers.
In parallel, the demand for higher energy efficiency and sustainability has pushed suppliers to design regulators with lower energy consumption and reduced thermal losses. SABIC has announced new polymer-based encapsulation solutions, aiming to minimize leakage currents and enhance the safety profile of galvanic flux regulation systems used in battery packs and fuel cells.
Looking ahead to the next few years, the outlook for galvanic flux regulator technology is focused on further digitalization and interoperability. The adoption of open communication protocols is expected to facilitate seamless integration into smart manufacturing environments and digital twins, enabling more granular control and diagnostics. Additionally, the growth in electric vehicle (EV) and renewable energy markets is anticipated to drive innovation in high-capacity, scalable flux regulation solutions tailored for large-format batteries and grid-level energy storage. Industry consortia such as IEEE are actively working on defining new standards to ensure safety, reliability, and cross-compatibility of advanced galvanic regulation devices.
Global Market Sizing & 3-Year Forecast (2025–2028)
The global market for galvanic flux regulators is poised for measured growth in the 2025–2028 period, driven by escalating demand for advanced process control in electronics manufacturing, renewable energy systems, and industrial automation. As of 2025, the market size is estimated to be in the lower hundreds of millions USD, with North America, Europe, and East Asia comprising the principal regions of demand due to their well-established electronics and energy sectors.
Leading suppliers and manufacturers, such as KYOCERA Corporation and Honeywell International Inc., have reported increasing order volumes from both printed circuit board (PCB) fabrication and battery management system (BMS) integrators. These sectors rely on precise galvanic flux regulation to ensure product reliability and efficiency, particularly as device miniaturization and energy density requirements intensify.
Recent updates from Schneider Electric and Siemens AG indicate that the integration of digital twins and predictive analytics into flux regulation systems is becoming a market differentiator. These advancements enable real-time monitoring and adaptive control, which major electronics assemblers and energy storage manufacturers increasingly specify in their procurement criteria. In 2025, several large-scale projects in automotive battery gigafactories and semiconductor foundries have initiated pilot deployments of integrated galvanic flux regulators, setting a precedent for mainstream adoption in the coming years.
From a regional perspective, Panasonic Corporation and TDK Corporation in Japan are expanding their galvanic flux regulator portfolios, targeting both domestic and overseas markets. Meanwhile, European companies are aligning product developments with sustainability regulations, enhancing the recyclability and energy efficiency of their flux management technologies.
Looking ahead to 2028, the global market for galvanic flux regulators is forecast to grow at a compound annual growth rate (CAGR) of 6–8%. This trajectory is underpinned by ongoing electrification trends, stricter quality standards, and the proliferation of automated manufacturing lines. Strategic partnerships between equipment manufacturers and system integrators—such as recent collaborations highlighted by ABB Ltd.—are expected to accelerate the deployment of next-generation flux regulation solutions globally, especially in fast-growing Asian markets.
Major Players & Industry Leaders (Official Sources Only)
The market for Galvanic Flux Regulators is characterized by a concentration of established manufacturers and technology innovators serving sectors such as electronics manufacturing, battery systems, and advanced materials. As of 2025, the industry’s major players are advancing production capabilities to meet the rising demand for precise flux control in both traditional and emerging applications.
- Nordson Corporation continues to be a leading supplier of precision dispensing and control technologies, including galvanic flux regulators for electronics assembly. The company’s systems are widely used in surface mount technology (SMT) lines, with recent product updates targeting enhanced process control and reduced waste. Their ongoing investment in R&D is geared toward increasing automation and integration with Industry 4.0 systems, as highlighted in their annual technology review (Nordson Corporation).
- ITW EAE (a division of Illinois Tool Works) remains at the forefront with its Electrovert and Camalot brands, delivering advanced fluxing and galvanic regulation systems. Their latest offerings emphasize real-time monitoring and adaptive control for high-reliability electronics, as outlined in their 2025 product roadmap (ITW EAE).
- Balver Zinn, a global supplier of soldering materials and flux systems, has expanded its portfolio in response to stricter environmental and reliability standards. Their galvanic flux regulators are frequently integrated into automated production lines for automotive and renewable energy electronics, reflecting a shift toward higher efficiency and sustainability (Balver Zinn).
- Yamaha Motor Co., Ltd.’s robotics and SMT division is leveraging its expertise in factory automation to enhance its flux regulation modules. In 2025, Yamaha is focusing on modular, scalable solutions compatible with smart manufacturing platforms (Yamaha Motor Co., Ltd.).
Looking ahead, these industry leaders are likely to drive further innovation, especially as demand grows for miniaturized electronics and more stringent process standards. Collaborations with semiconductor and electric vehicle manufacturers are expected to shape product development through 2027, with a focus on digitalization, sustainability, and real-time data analytics.
Cutting-Edge Applications Across Sectors
Galvanic flux regulators (GFRs) are rapidly expanding their footprint across multiple sectors, propelled by their unique ability to precisely control ionic flow in electrochemical environments. In 2025, several industries are leveraging GFRs to enhance efficiency, reliability, and miniaturization in both established and emerging applications.
- Semiconductor Manufacturing: GFRs are integral to next-generation wafer fabrication, where precise electroplating and etching processes demand atomic-scale control of material deposition. Companies such as Lam Research Corporation are integrating advanced GFR modules within their electrochemical deposition systems, enabling finer interconnects and reducing defect rates in advanced node devices.
- Energy Storage and Conversion: Battery manufacturers, notably Panasonic Corporation and Tesla, Inc., are evaluating GFRs to optimize lithium-ion cell manufacturing and extend battery life. GFR-enabled electrolyte management is showing promise in mitigating dendrite formation, a leading cause of battery failure, and in supporting the development of solid-state batteries.
- Corrosion Control in Infrastructure: The oil and gas, as well as marine industries, are deploying GFRs in smart cathodic protection systems. Saudi Arabian Oil Company (Aramco) is piloting GFR-based solutions to dynamically regulate protective currents on pipelines and offshore platforms, reducing maintenance costs and extending asset life.
- Biomedical Devices: The precise modulation of ionic currents by GFRs is unlocking advances in neurostimulation and implantable devices. Medtronic plc is exploring GFR-integrated platforms for adaptive deep brain stimulation, aiming for real-time response to patient neural activity with improved safety profiles.
- Water Treatment and Desalination: GFRs are being trialed in capacitive deionization and electrochemical water purification systems. Xylem Inc. is conducting field tests on GFR-driven modules for selective ion removal, enhancing efficiency while lowering operational costs in municipal and industrial water treatment.
Looking ahead, the outlook for GFRs is buoyed by ongoing miniaturization, improved material science, and integration with AI-driven control systems. As 2025 progresses, deeper adoption is expected in fields requiring granular electrochemical control, with collaborative projects between device manufacturers and end-users accelerating real-world deployments. The next few years are likely to see GFRs become a standard component in high-precision electrochemical systems across sectors.
Regulatory Landscape and Standards (Referencing IEEE, ASME)
The regulatory landscape for Galvanic Flux Regulators (GFRs) is evolving rapidly as these devices become increasingly integral to advanced power management systems, smart grids, and precision industrial processes. As of 2025, the primary frameworks guiding the development and deployment of GFRs stem from international standards organizations such as the Institute of Electrical and Electronics Engineers (IEEE) and the American Society of Mechanical Engineers (ASME).
Within the IEEE, the most relevant standards for GFRs are encompassed in the Power and Energy Society’s guidelines for electrical equipment interoperability and grid integration. The IEEE Standard 1547 series, which covers interconnection and interoperability of distributed energy resources with power systems, has recently been updated to include more granular requirements for galvanic isolation and flux regulation in decentralized grids. This update reflects the growing use of GFRs for precise control of current and voltage in renewable energy applications and microgrids (IEEE).
ASME, traditionally focused on mechanical systems, has expanded its codes related to electro-mechanical devices. The ASME A17 series, related to safety code for elevators and escalators, now includes provisions for advanced flux regulators used in elevator drive systems, enforcing stricter requirements for galvanic isolation, electromagnetic compatibility, and system resilience (ASME). The ASME’s recent collaboration with electrical standards bodies aims to harmonize mechanical and electrical safety requirements, directly impacting manufacturers of GFRs targeting industrial automation and transport sectors.
Looking ahead, the next few years are expected to see even more stringent benchmarking for GFRs, especially as the electrification of infrastructure accelerates. Both IEEE and ASME are working on harmonized standards that address cybersecurity for flux regulation devices, grid stability, and integration with IoT platforms. Several manufacturers and industry consortia are currently participating in pilot programs to validate compliance with anticipated 2026 and 2027 standards, reflecting a proactive approach to regulatory alignment (IEEE).
In summary, the regulatory framework for Galvanic Flux Regulators is becoming increasingly rigorous, with both IEEE and ASME at the forefront of standardization. Manufacturers and users should monitor updates from these organizations closely, as forthcoming standards will likely shape product development, certification processes, and market access in the years ahead.
Breakthrough Innovations Shaping the Future
Galvanic flux regulators, pivotal in controlling electrochemical processes and ensuring the efficiency and safety of galvanic cells, are undergoing significant innovation as industry demands for precision, sustainability, and digital integration accelerate into 2025. A central trend shaping the sector is the advancement of adaptive control algorithms embedded in regulators, enabling real-time response to fluctuations in current density, temperature, and electrolyte composition. For example, Sartorius AG has introduced next-generation galvanic probes with built-in flux regulation and automated diagnostics, dramatically reducing calibration cycles and operational downtime in industrial electrolysis and plating lines.
Another key area is the integration of Internet of Things (IoT) connectivity and digital twins into galvanic flux regulation systems. Siemens AG has begun piloting cloud-based platforms that visualize and optimize flux regulation parameters across distributed manufacturing sites, allowing for predictive maintenance and remote troubleshooting. This shift is expected to drive greater process transparency and data-driven efficiency, with early field data indicating up to 15% reduction in energy consumption and significant enhancements in product quality consistency.
Materials innovation is also reshaping the sector. The adoption of advanced ceramic and polymer composites in regulator components is improving chemical resistance and operational lifespans. Metso Corporation is evaluating novel membrane technologies for flux regulation in harsh electrochemical environments, aimed at reducing contamination and extending maintenance intervals. These developments are particularly relevant for battery manufacturing and metal refining, industries projected to see double-digit growth rates through the mid-2020s.
Looking ahead, the convergence of galvanic flux regulators with artificial intelligence (AI) and machine learning is anticipated to unlock further breakthroughs. AI-driven control systems, now in prototype stages at firms like ABB Ltd., promise self-optimizing flux regulation that dynamically adapts to process drift and raw material variability. Industry experts forecast that by 2027, such technologies could become standard in high-throughput electrochemical manufacturing, supporting both sustainability goals and stringent quality standards.
Together, these innovations are positioning galvanic flux regulators as key enablers for the next generation of efficient, sustainable, and intelligent manufacturing processes, with rapid adoption expected across electroplating, energy storage, and specialty chemical sectors in the coming years.
Supply Chain, Manufacturing, and Sustainability Factors
The supply chain and manufacturing landscape for galvanic flux regulators is poised for notable transformation in 2025 and the coming years, as the electronics and electroplating industries demand greater precision, integration, and sustainability. Galvanic flux regulators, crucial for maintaining optimal current distribution and chemical stability during electrochemical processes, are seeing increased adoption in battery manufacturing, PCB fabrication, and emerging green technologies.
Manufacturers such as Umicore and Technic Inc. continue to invest in advanced production lines for galvanic process controls, including flux regulators, to serve expanding markets in Asia, Europe, and North America. In 2025, supply chains are expected to benefit from regional diversification, with new facilities and supplier partnerships reducing the risk of single-source disruptions. For example, Atotech has expanded its manufacturing footprint in Asia to address both local and international demand for electroplating systems and components, which directly include galvanic flux regulators.
Material sourcing for key components—such as specialty alloys and chemical sensors—remains a focal point. Companies like Umicore are prioritizing the use of recycled metals and certified supply chains for critical inputs, aligning with increasing regulatory and customer expectations around sustainability. Furthermore, the adoption of digital inventory management and transparent supplier auditing, as seen in initiatives by Technic Inc., is expected to streamline the procurement and tracking of flux regulator components.
Sustainability considerations are increasingly shaping manufacturing practices. Leading producers are deploying eco-efficient production techniques, waste minimization processes, and closed-loop water systems to reduce their environmental footprint. Atotech has highlighted the integration of resource-efficient processes in their new facilities, aiming to lower emissions and energy consumption associated with galvanic equipment production.
Looking ahead, the outlook for galvanic flux regulators is closely tied to broader trends in electrification, miniaturization, and environmental compliance. As OEMs and end-users require more stringent quality and sustainability standards, suppliers are expected to accelerate investments in greener manufacturing and resilient supply chains. The continued rollout of digital manufacturing and real-time monitoring systems will further boost both efficiency and traceability across the value chain, reinforcing supply security and sustainability for galvanic flux regulators through 2025 and beyond.
Challenges, Risks, and Competitive Dynamics
The landscape for Galvanic Flux Regulators (GFRs) in 2025 is shaped by several evolving challenges, risks, and intensifying competitive dynamics. As industries such as electronics manufacturing, renewable energy, and advanced materials continue to demand higher precision in flux regulation, the performance expectations for GFRs are rising. One of the primary technical challenges centers on maintaining regulator stability and accuracy in the face of fluctuating process variables, especially as miniaturization and integration with IoT systems become more prevalent. Companies like Sensata Technologies and Schneider Electric are investing in advanced sensor integration and adaptive control algorithms to address these concerns, but the complexity of such solutions raises both development costs and barriers to entry for smaller competitors.
Risks related to supply chain volatility remain prominent. The ongoing global shortage of high-purity metals and specialized semiconductors, crucial for the manufacture of precise galvanic components, has led to price fluctuations and delivery delays. Consequently, manufacturers like ABB Ltd and Honeywell International Inc. are pursuing greater vertical integration and diversified supplier relationships to mitigate these risks, while also investing in recycling and material recovery processes to secure raw material streams.
Another important risk factor is regulatory compliance, especially in the context of global environmental and safety standards. The increasing stringency of directives such as RoHS and REACH in Europe, and comparable frameworks in North America and Asia, require companies to continuously audit and update their GFR product lines for hazardous substance management and lifecycle traceability. For example, Phoenix Contact reports regular product updates to ensure ongoing compliance, which adds to operational overhead but is essential for market access.
The competitive landscape is also shifting as established automation and control firms face competition from agile startups leveraging digital twins, AI-driven maintenance, and cloud-based diagnostics to offer differentiated GFR solutions. Strategic partnerships are emerging, with companies like Siemens AG collaborating with software providers to embed advanced analytics and remote management capabilities into their GFR offerings. This trend is likely to intensify over the next few years, as end-users prioritize future-proof, interoperable solutions that can seamlessly integrate into broader Industry 4.0 architectures.
Looking ahead, the sector is expected to see further consolidation, with leading GFR suppliers acquiring niche technology firms to enhance their competitive positions. Companies that can balance innovation, supply chain resilience, and compliance will be best positioned to capture growing demand—especially in high-growth regions and sectors emphasizing energy efficiency and process digitization.
Future Outlook: Opportunities and Strategic Recommendations
The future outlook for Galvanic Flux Regulators (GFRs) in 2025 and beyond is shaped by accelerating trends in electronics miniaturization, green manufacturing, and advanced materials innovation. As the electronics and semiconductor industries continue to scale down device geometries, the demands for precise and dynamic flux control in soldering and surface finishing processes are poised to intensify. GFRs are increasingly recognized for their ability to provide real-time regulation of galvanic processes, helping manufacturers achieve tighter tolerances and higher product consistency.
From a market perspective, strategic investments in R&D and production capacity for GFRs are underway among leading suppliers. For example, Entegris and Kyocera are expanding their process control portfolios to integrate advanced flux regulation solutions, targeting the semiconductor packaging and printed circuit board (PCB) sectors. These companies are developing GFR modules that are compatible with Industry 4.0 frameworks, enabling remote monitoring and predictive diagnostics for enhanced throughput and yield.
Sustainability pressures are also shaping the strategic direction of GFR technologies. Environmental regulations, especially in the EU and Asia-Pacific, are prompting electronics manufacturers to adopt flux regulators that minimize waste and reduce the use of hazardous substances in soldering baths. Henkel, a major supplier of assembly materials, is collaborating with equipment manufacturers to develop GFRs that support closed-loop flux management and traceability, contributing to greener production lines.
In terms of technological innovation, the next few years are expected to witness the emergence of AI-enhanced GFRs. These systems will leverage machine learning algorithms to optimize flux delivery parameters in real-time, responding to subtle variations in process conditions and material properties. Companies such as ASMPT are piloting smart control systems that integrate GFRs with broader manufacturing execution systems, providing end-to-end data visibility and feedback loops for continuous improvement.
Strategically, manufacturers are advised to:
- Invest in GFR solutions compatible with digital manufacturing and Industry 4.0 standards.
- Prioritize suppliers with strong commitments to sustainability and compliance with evolving environmental regulations.
- Explore partnerships with GFR innovators to co-develop custom solutions that address specific production challenges.
- Develop in-house expertise in data analytics and AI to maximize the value of next-generation GFR platforms.
Overall, the adoption of Galvanic Flux Regulators is set to accelerate, underpinned by both regulatory drivers and the need for higher manufacturing precision. Companies proactively embracing these technologies are likely to gain competitive advantages in terms of quality, efficiency, and sustainability.