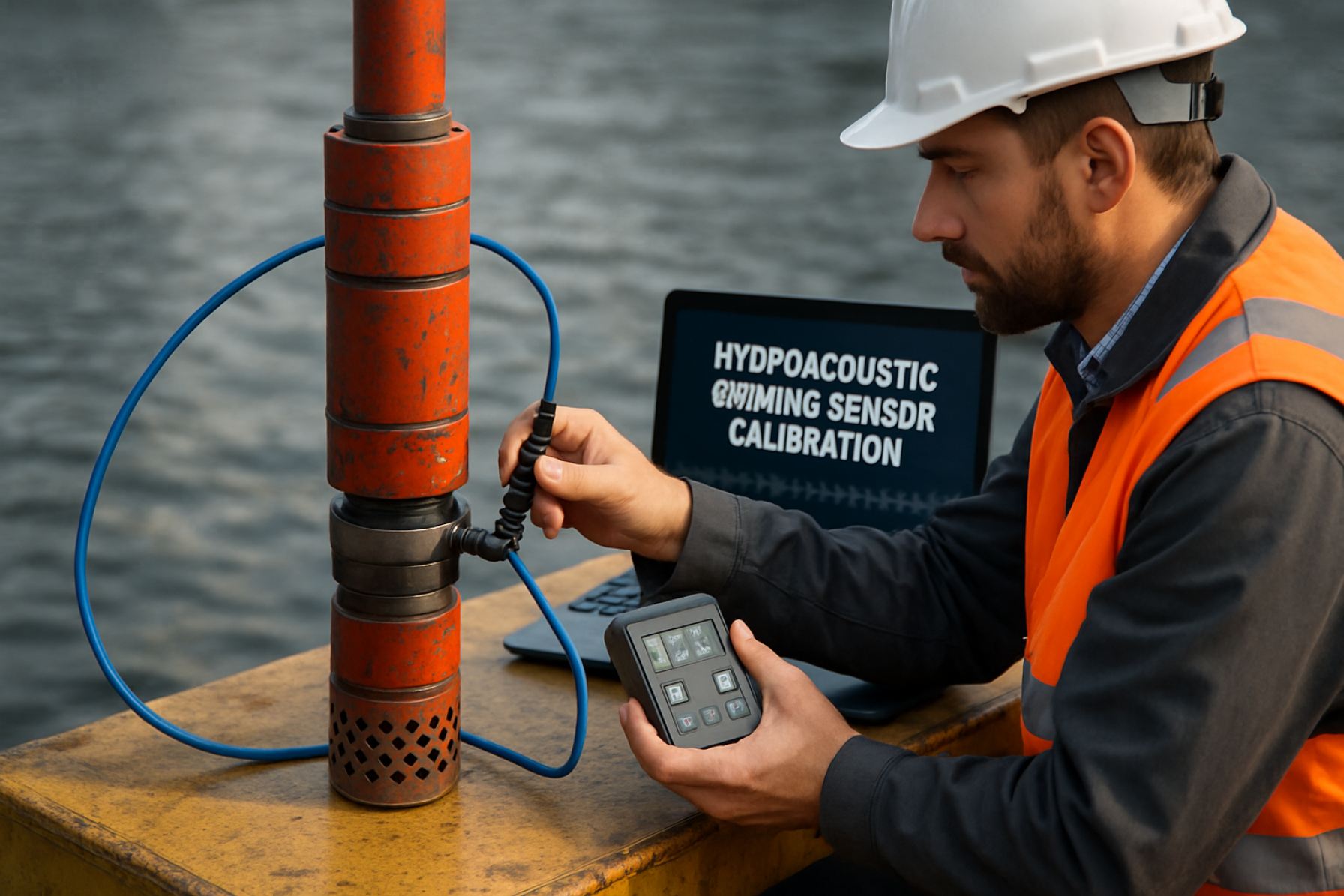
Table of Contents
- Executive Summary & 2025 Market Outlook
- Key Industry Drivers and Regulatory Developments
- Hydroacoustic Sensor Technologies: Innovations and Trends
- Calibration Techniques: Current Best Practices and Breakthroughs
- Major Players and Strategic Partnerships (e.g. slb.com, bakerhughes.com, ieee.org)
- Emerging Applications in Oil, Gas, and Geothermal Drilling
- Global Market Forecast: 2025–2030 by Region and Segment
- Challenges: Accuracy, Data Integration, and Harsh Environments
- Sustainability, Compliance, and Environmental Impact
- Future Outlook: Next-Gen Calibration and Competitive Landscapes
- Sources & References
Executive Summary & 2025 Market Outlook
Hydroacoustic drilling sensors are increasingly critical for precise subsurface characterization, real-time drilling optimization, and ensuring operational safety in offshore and onshore drilling environments. Calibration of these sensors remains a technical and commercial priority as operators demand higher data accuracy and reliability in complex geophysical settings. In 2025, this sector is witnessing significant momentum driven by technological advancements, regulatory requirements, and the integration of digital calibration workflows.
Key industry players, including SLB (Schlumberger), Halliburton, and Baker Hughes, are actively investing in advanced hydroacoustic sensor calibration capabilities. These companies are deploying automated calibration rigs and leveraging machine learning algorithms to correct for environmental noise, sensor drift, and coupling errors in real-time. For example, SLB has integrated digital twins and cloud-based calibration management into its sensor platforms, improving diagnostics and reducing downtime for offshore calibration campaigns.
In 2025, the adoption of remote and in situ calibration solutions is accelerating. Kongsberg Maritime and Sonardyne International are pioneering remote diagnostics and automated verification routines, minimizing the need for manual intervention and vessel-based recalibration. This trend is particularly important for deepwater and ultra-deepwater projects, where accessibility and operational costs are critical concerns. These solutions help operators comply with evolving standards set by organizations such as the International Association of Oil & Gas Producers (IOGP), which now emphasize traceable, repeatable calibration for hydroacoustic positioning and logging sensors.
Emerging data from recent field operations highlights the commercial value of precise calibration. Operators report marked reductions in non-productive time (NPT) and improved drilling accuracy, translating to lower well costs and fewer environmental incidents. As a result, sensor manufacturers are expanding their calibration offerings to include predictive maintenance analytics and cloud-based audit trails, ensuring sustained compliance and performance over the sensor lifecycle.
Looking ahead to the next few years, the hydroacoustic drilling sensor calibration market is set for further growth. Key drivers will include increasing adoption in offshore wind and carbon capture projects, heightened environmental scrutiny, and the integration of AI-driven calibration workflows. As digitalization deepens, the sector will likely see further collaboration between sensor OEMs, software providers, and energy operators to deliver more autonomous, resilient, and scalable calibration solutions.
Key Industry Drivers and Regulatory Developments
Hydroacoustic drilling sensor calibration is emerging as a critical segment in drilling operations, driven by stringent industry demands for precision, reliability, and compliance with evolving standards. In 2025, several key industry drivers and regulatory developments are shaping the calibration landscape for hydroacoustic sensors used in oil & gas, mining, and geotechnical drilling.
- Enhanced Accuracy Requirements: The need for high-resolution subsurface imaging and precise borehole positioning has intensified, particularly in offshore and deepwater drilling. Operators increasingly rely on hydroacoustic sensors—such as Doppler velocity logs, multibeam echosounders, and acoustic positioning systems—that require regular and traceable calibration. Companies like Kongsberg Maritime and Sonardyne International are at the forefront, offering calibration solutions and referencing the importance of maintaining sensor fidelity to support drilling accuracy and safety.
- Digitalization and Remote Calibration: As the energy sector embraces digital transformation, remote monitoring and digital twin technologies increasingly incorporate hydroacoustic sensor data. This shift is driving demand for automated, in situ calibration techniques and digital calibration certificates, as seen in pilot projects by Teledyne Marine. Such advancements streamline compliance and minimize costly downtime associated with traditional, manual calibration routines.
- Regulatory Alignment and Certification: National and international regulatory bodies, including the International Association of Oil & Gas Producers (IOGP), are updating standards to address the growing use of hydroacoustic technologies. Recent years have seen the adoption of stricter calibration traceability requirements and periodic recertification mandates, compelling sensor manufacturers and service providers to invest in accredited calibration facilities. Organizations like Fugro have expanded their calibration service offerings to ensure customers meet these evolving regulatory expectations.
- Environmental Monitoring Integration: The integration of hydroacoustic sensors for both drilling operations and environmental monitoring (such as marine mammal detection and subsea leak identification) has led to new calibration protocols. Regulatory agencies, including the International Maritime Organization (IMO), are expected to formalize these dual-use calibration standards within the next few years, reflecting a broader focus on operational sustainability and environmental stewardship.
Looking ahead, the next few years will likely see continued convergence of calibration standards across sectors, increased automation, and a stronger regulatory emphasis on traceability, accuracy, and environmental compliance. Industry leaders are actively investing in R&D and cross-sector collaborations to anticipate and address these evolving requirements, positioning hydroacoustic sensor calibration as a foundational element of safe and sustainable drilling operations.
Hydroacoustic Sensor Technologies: Innovations and Trends
Hydroacoustic drilling sensor calibration has become a focal point of innovation in subsurface exploration as accuracy requirements intensify for both energy and geoscience applications. In 2025, calibration methodologies are undergoing rapid refinement to support increasingly complex drilling environments, such as ultra-deepwater and high-temperature geothermal wells. Leading equipment manufacturers and service companies are investing in automated calibration systems and digital twins to ensure reliability and repeatability in sensor output under dynamic operating conditions.
One significant trend in 2025 is the adoption of real-time, in-situ calibration technologies. Rather than relying solely on pre-deployment laboratory calibration, sensor arrays—such as hydrophones and piezoelectric transducers—are now equipped with embedded reference sources. These allow self-checks during operation, compensating for drift and environmental noise. For example, Schlumberger has expanded its portfolio with downhole hydroacoustic modules capable of autonomous calibration cycles, enhancing the precision of acoustic velocity and attenuation measurements that are crucial for formation evaluation.
Automated test rigs and calibration tanks with programmable acoustic fields are now standard among top-tier calibration facilities. Teledyne Marine has advanced its hydroacoustic sensor calibration labs by integrating digital control of water temperature, salinity, and pressure. This enables simulation of extreme subsea environments and produces traceable calibration certificates aligned with ISO/IEC 17025 standards. Similarly, system integrators such as Kongsberg Maritime have established mobile calibration platforms, which allow on-site verification of sensor performance aboard offshore rigs, reducing downtime and logistics costs.
Data integrity is further enhanced by the integration of AI-based quality assurance tools. These systems analyze calibration data in real time, flagging anomalies and recommending corrective actions. Industry-wide, there is a move toward standardized calibration protocols, with organizations such as the IEEE and the Oceanology International community working to harmonize procedures across equipment suppliers.
Looking ahead to the next few years, ongoing R&D is focused on miniaturized calibration hardware for downhole deployment and the use of digital twins for predictive sensor maintenance. These advances are expected to facilitate broader adoption of hydroacoustic monitoring for carbon capture and storage (CCS) and offshore wind, where sensor reliability underpins both safety and regulatory compliance. As sensor networks proliferate, calibration traceability and automation will remain central to the sector’s evolution.
Calibration Techniques: Current Best Practices and Breakthroughs
Hydroacoustic drilling sensor calibration is a critical process ensuring accurate subsurface data acquisition, particularly as drilling operations extend into more complex and challenging environments. As of 2025, calibration techniques are being shaped by both incremental improvements in established methods and the introduction of novel technologies, aiming to improve accuracy, efficiency, and operational reliability.
Current best practices for hydroacoustic sensor calibration revolve around controlled laboratory settings and in-situ verification. In the laboratory, reference tanks with precisely known acoustic properties are used to benchmark sensor responses against traceable standards. This includes calibrating for pressure, temperature, and salinity, all of which affect acoustic wave propagation. Leading manufacturers such as Teledyne Marine and Kongsberg Maritime provide specialized calibration facilities and protocols for their hydroacoustic products, ensuring compliance with international standards and repeatability across deployments.
Recent breakthroughs are focused on automating in-situ calibration routines. For example, self-calibrating sensor arrays have been introduced, employing internal reference signals and real-time environmental compensation algorithms. Sonardyne has pioneered embedded diagnostic systems that continually monitor sensor health and calibration drift, alerting operators to potential deviations before critical thresholds are crossed. These systems leverage advanced digital signal processing to distinguish between sensor anomalies and genuine environmental changes.
Data-driven calibration is also gaining traction. Machine learning algorithms are being developed to analyze large volumes of acoustic data, identifying subtle patterns of sensor drift or bias that might be missed by conventional calibration checks. iXblue and other industry innovators are integrating AI-based analytics into their hydroacoustic sensor suites, enabling predictive maintenance and reducing the risk of unplanned downtime.
Looking ahead to the next few years, the outlook includes further integration of remote and autonomous calibration technologies. As offshore and unmanned drilling operations expand, the need for sensors capable of self-verification and adjustment in real time is paramount. Initiatives such as digital twins—virtual replicas of physical sensor systems—are being developed to simulate sensor behavior under varying conditions, facilitating continuous online calibration and performance optimization (Kongsberg Maritime).
In summary, hydroacoustic drilling sensor calibration is rapidly evolving, with industry leaders focusing on automation, data analytics, and remote capabilities. These advances are expected to set new standards for reliability and data quality in drilling operations through 2025 and beyond.
Major Players and Strategic Partnerships (e.g. slb.com, bakerhughes.com, ieee.org)
In 2025, the hydroacoustic drilling sensor calibration sector is shaped by leading companies and strategic alliances focused on precision, reliability, and digital integration. Prominent industry players such as SLB (Schlumberger) and Baker Hughes continue to drive innovation in hydroacoustic sensor technology, leveraging their extensive experience in downhole measurement and data acquisition. These companies prioritize advanced calibration protocols to ensure the accuracy of real-time data used for geosteering, formation evaluation, and well integrity assessments.
SLB has been actively expanding its hydroacoustic sensor portfolio, emphasizing digital calibration workflows that integrate cloud-based analytics and automated diagnostics. Their recent collaborations with digital solution providers facilitate seamless sensor performance monitoring and remote recalibration, reducing non-productive time and improving data fidelity (SLB). Similarly, Baker Hughes is investing in modular sensor platforms with embedded self-calibration features, enabling operators to maintain high measurement accuracy even under challenging drilling conditions. Their partnerships with sensor manufacturers and software developers are accelerating the deployment of AI-driven calibration routines that minimize human intervention and adapt to varying subsurface environments (Baker Hughes).
Industry standards and best practices for hydroacoustic drilling sensor calibration are also being shaped by organizations such as the IEEE. The IEEE is involved in developing technical standards, such as IEEE 1451, which address smart sensor interoperability and calibration protocol harmonization. These standards are crucial for enabling cross-vendor compatibility and streamlining field deployment of multi-sensor arrays in drilling operations (IEEE).
Strategic partnerships are further emerging between major oilfield service providers and technology startups specializing in hydroacoustic analytics. These collaborations focus on the co-development of miniaturized, high-sensitivity hydroacoustic sensors and the refinement of automated calibration algorithms. Looking ahead to the next few years, the sector is expected to witness increased integration of Internet of Things (IoT) connectivity and machine learning in calibration processes, enabling predictive maintenance and more agile responses to sensor drift or failure.
In summary, the calibration of hydroacoustic drilling sensors in 2025 is characterized by technological advancements and a collaborative approach among industry leaders, standards bodies, and innovators, paving the way for improved drilling efficiency and operational safety in increasingly complex subsurface environments.
Emerging Applications in Oil, Gas, and Geothermal Drilling
Hydroacoustic sensor systems are increasingly integral to modern drilling operations, providing real-time measurements critical for downhole navigation, reservoir characterization, and equipment diagnostics. In the oil, gas, and geothermal sectors, the demand for accurate and reliable hydroacoustic data has grown considerably, prompting a renewed focus on sensor calibration methods as these industries contend with more complex subsurface environments in 2025 and beyond.
Recent advancements in hydroacoustic sensor design—such as high-frequency transducers, multi-channel arrays, and digital signal processing—have driven the need for more rigorous calibration protocols. Calibration ensures that hydroacoustic sensors accurately translate acoustic signals into meaningful measurements, unaffected by environmental noise, pressure, or temperature fluctuations encountered at depth. In 2025, manufacturers such as Kongsberg Maritime and Teledyne Marine are leading efforts to standardize calibration services, offering in-house pressure tanks and field-deployable calibration kits tailored to the high-pressure, high-temperature (HPHT) conditions typical of deep drilling.
A major event influencing calibration standards is the industry-wide move toward autonomous drilling systems. These systems require hydroacoustic sensors with traceable, repeatable calibrations to ensure safe operation and data integrity (Baker Hughes). New calibration facilities, such as those being developed by SLB, include automated test loops and environmental simulation chambers, allowing for simultaneous multi-sensor calibration under dynamic fluid flow and real-world acoustic interference scenarios.
On the data side, real-time calibration validation is becoming more commonplace. Companies are integrating embedded reference sources and self-diagnostic routines within hydroacoustic tools to monitor drift and signal fidelity during operation. Halliburton has demonstrated adaptive calibration algorithms capable of adjusting sensor baselines in response to changing borehole fluid properties, a feature particularly relevant to geothermal wells with variable thermal gradients.
Looking forward, the outlook for hydroacoustic drilling sensor calibration includes broader adoption of digital twins for calibration traceability and regulatory compliance. Collaboration between manufacturers, industry bodies, and operators is expected to yield new calibration standards, especially as deepwater and geothermal projects expand globally. The next few years will likely see an emphasis on rapid, remote calibration methods, reducing downtime and supporting the deployment of next-generation hydroacoustic sensor arrays in increasingly challenging drilling environments.
Global Market Forecast: 2025–2030 by Region and Segment
The global market for hydroacoustic drilling sensor calibration is poised for notable advancements and moderate growth between 2025 and 2030, as offshore energy development, deepwater exploration, and digitalization efforts intensify across key regions. Calibration ensures the accuracy and reliability of hydroacoustic sensors used in drilling operations, which is crucial for subsea positioning, borehole evaluation, and real-time monitoring in challenging environments.
- North America: The United States and Canada are expected to maintain leadership in sensor calibration demand due to ongoing offshore activity in the Gulf of Mexico and Arctic regions. Leading calibration service providers such as Teledyne Marine and Sonardyne International Ltd are investing in advanced laboratory calibration and in-situ verification methods. The implementation of digital twins and remote calibration support is expected to accelerate, aligning with regional digital oilfield strategies.
- Europe: The North Sea, Mediterranean, and emerging offshore wind sectors are driving regional requirements for precise sensor calibration. Companies like Kongsberg Maritime and Fugro are expanding their calibration solutions, focusing on enhanced traceability and compliance with international standards such as ISO/IEC 17025. The integration of AI-driven diagnostics and predictive maintenance is anticipated to influence the segment outlook.
- Asia-Pacific: Growth in deepwater projects offshore China, Australia, and Southeast Asia is increasing demand for robust sensor calibration services. Regional players, including Silversea (China), are strengthening collaborations with international sensor manufacturers to localize calibration capabilities and reduce operational downtime. The adoption of portable calibration systems is projected to rise, especially for remote or mobile rigs.
- Middle East & Africa: While the region’s focus remains on traditional hydrocarbon production, investments in ultra-deepwater exploration (e.g., off the coasts of Angola and Mozambique) are expected to boost the calibration market. Partnerships between local service providers and global technology companies such as SLB (Schlumberger) are facilitating the transfer of advanced calibration technologies and best practices.
- Latin America: Offshore developments in Brazil and Guyana are driving sensor calibration demand, with operators emphasizing real-time data quality and compliance with environmental regulations. Regional calibration centers—supported by firms like Oceaneering International—are anticipated to expand their capacity and service offerings over the forecast period.
Across all regions, the next five years will likely see a shift toward automation, remote calibration verification, and cloud-based data management for hydroacoustic drilling sensors. As the sector responds to deeper, more complex drilling environments and regulatory scrutiny, calibration will remain a critical enabler of operational safety and efficiency.
Challenges: Accuracy, Data Integration, and Harsh Environments
Hydroacoustic drilling sensor calibration faces a unique set of challenges in 2025, primarily focused on accuracy, data integration, and the capacity to withstand harsh drilling environments. These challenges are critical as the oil & gas and geothermal sectors increasingly rely on real-time hydroacoustic data for downhole navigation, reservoir characterization, and wellbore stability monitoring.
A persistent issue is the maintenance of calibration accuracy under dynamic conditions. Hydroacoustic sensors are sensitive to temperature, pressure, and fluid composition changes, all of which are prevalent in deep drilling environments. Even minor deviations in calibration can cause significant errors in depth or formation evaluation. Companies such as Teledyne Marine and Kongsberg Maritime have advanced their sensor lines with in-situ calibration routines and temperature-compensation algorithms. However, the industry continues to report challenges in maintaining performance over extended drilling campaigns where sensor drift and fouling can degrade signal quality.
Data integration is another major hurdle. Hydroacoustic sensors typically operate alongside a suite of other downhole instruments—such as resistivity, gamma ray, and pressure sensors—within Measurement-While-Drilling (MWD) or Logging-While-Drilling (LWD) systems. Harmonizing hydroacoustic data streams with other sensor outputs requires robust calibration protocols and data fusion algorithms. In 2025, leading service providers like SLB and Halliburton are developing unified sensor frameworks that facilitate real-time data integration while flagging calibration anomalies through onboard diagnostics.
Environmental harshness remains a defining challenge. Downhole sensors must withstand high vibration, rapid pressure fluctuations, abrasive drilling fluids, and extreme temperatures. This environment accelerates sensor wear and can cause calibration drift. Manufacturers such as Baker Hughes are investing in ruggedized sensor housings and self-cleaning transducer surfaces to mitigate fouling and extend calibration intervals. In parallel, remote calibration verification—enabled by cloud connectivity and edge computing—is being piloted to allow surface operators to assess sensor health and recalibrate as needed without interrupting drilling operations.
Looking forward, the next few years are expected to see further advancements in autonomous calibration systems and AI-driven data quality monitoring, as well as greater adoption of digital twins to simulate calibration drift scenarios. Industry collaborations and new standards from bodies such as the International Association of Oil & Gas Producers (IOGP) will likely play a pivotal role in establishing best practices for calibration under increasingly complex drilling conditions.
Sustainability, Compliance, and Environmental Impact
Hydroacoustic drilling sensor calibration plays a pivotal role in ensuring both the precision of subsurface measurements and the environmental responsibility of drilling operations. As the industry moves further into 2025, the integration of sustainability and compliance requirements into calibration processes has become increasingly central to the development and deployment of hydroacoustic sensors.
A key development in recent years is the shift towards in-situ and remote calibration techniques, which minimize the need for physical intervention and reduce the carbon footprint associated with traditional calibration methods. Manufacturers such as Kongsberg Maritime have introduced sensor systems featuring automated self-calibration and health monitoring capabilities, allowing for continuous operation with reduced environmental disruption. These systems are designed to maintain high accuracy while aligning with the latest international environmental standards.
Regulatory frameworks are also evolving. In 2024 and 2025, agencies like the United States Environmental Protection Agency (EPA) and the International Organization for Standardization (ISO) have updated their recommendations for underwater acoustic measurements, emphasizing the importance of minimizing acoustic pollution and ensuring the calibration of sensors to avoid inadvertent harm to marine life. Compliance with these guidelines is now a key consideration for manufacturers and operators alike.
Recent data from sensor suppliers such as Teledyne Marine and Sonardyne International Ltd indicate a growing adoption of environmentally friendly calibration fluids and the use of biodegradable materials in sensor housings. These changes not only reduce the risk of introducing contaminants into marine environments but also facilitate compliance with stricter disposal and recycling regulations expected in the next few years.
Looking forward, the hydroacoustic sensor sector is poised to benefit from ongoing research into low-impact calibration signals and the integration of digital twins for remote performance verification. Leading organizations are investing in these technologies to meet both operational efficiency and sustainability targets. As a result, the outlook for hydroacoustic drilling sensor calibration in 2025 and beyond is characterized by a strong alignment with global sustainability goals, increased regulatory scrutiny, and rapid technological innovation aimed at minimizing environmental impact while maintaining measurement integrity.
Future Outlook: Next-Gen Calibration and Competitive Landscapes
The future of hydroacoustic drilling sensor calibration is poised for significant transformation as both technological innovation and competitive dynamics accelerate into 2025 and the ensuing years. Calibration accuracy and reliability are becoming paramount as hydroacoustic sensors, such as those used for measuring borehole parameters and subsurface imaging, are increasingly deployed in complex, data-intensive drilling projects.
Key industry players are investing in automation and advanced digitalization to streamline calibration procedures. For instance, Kongsberg Maritime is actively enhancing its calibration systems, integrating advanced machine learning algorithms that enable real-time drift compensation and adaptive recalibration during drilling operations. These advancements are directly addressing the need for reduced manual intervention and minimizing downtime, which is essential for offshore and remote installations.
Another major trend is the shift toward remote and cloud-based calibration management. Sonardyne International and Teledyne Marine are both developing platforms that allow operators to monitor sensor health, track calibration history, and initiate recalibration protocols from centralized control centers. This approach not only improves responsiveness but also supports large-scale drilling operations with distributed sensor arrays.
Interoperability and standardization are also receiving increased attention. Industry working groups, such as those convened by the International Association of Oil & Gas Producers (IOGP), are developing calibration best practices and standardized data formats. These initiatives aim to enable seamless integration of sensors from multiple manufacturers within unified drilling systems, reducing friction in multi-vendor environments and allowing for more flexible procurement strategies.
From a competitive perspective, companies with in-house calibration expertise and proprietary algorithms are gaining a distinct edge. Enhanced calibration capabilities are becoming a key differentiator, especially as drilling projects move into deeper, more technically challenging environments where sensor accuracy is mission-critical. Partnerships and collaborations between sensor manufacturers and drilling services firms are also expected to intensify, fostering rapid development and deployment of next-generation calibration technologies.
Looking ahead, the calibration landscape will likely see the introduction of autonomous self-testing sensors, leveraging AI for predictive maintenance and calibration needs. This evolution will further reduce operational risks and costs, while supporting the sector’s ongoing digital transformation. The companies that successfully integrate these innovations will be best positioned to lead in a highly competitive global market.