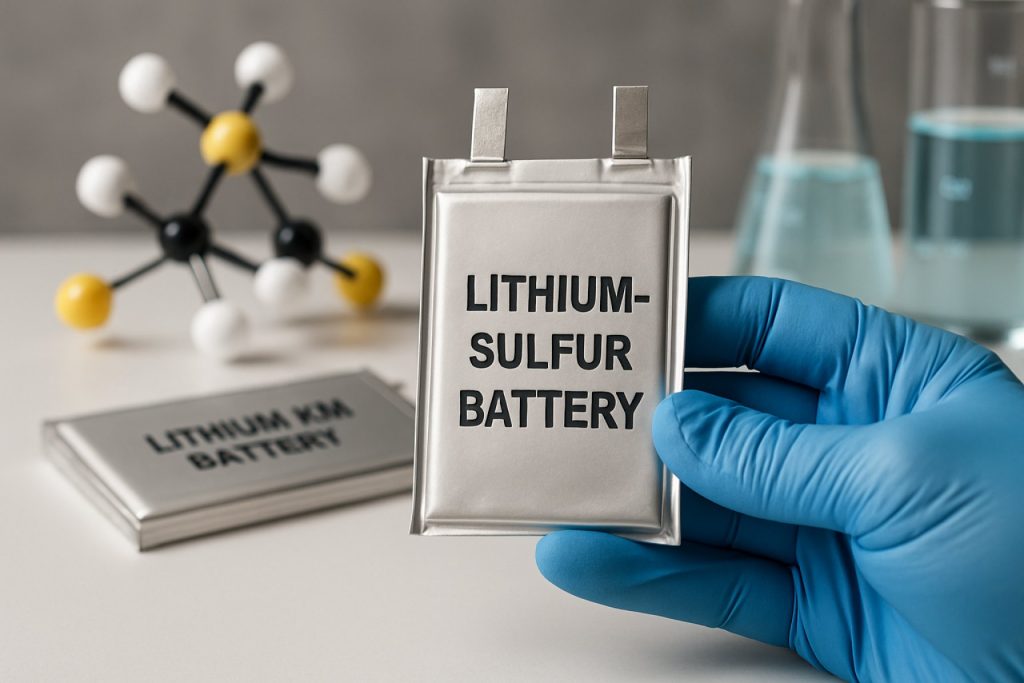
Revolutionizing Energy Storage: How Lithium-Sulfur Cathode Engineering in 2025 Is Shaping the Next Generation of High-Performance Batteries. Explore the Innovations, Market Surge, and Future Roadmap for This Transformative Technology.
- Executive Summary: 2025 Market Landscape and Key Drivers
- Lithium-Sulfur Cathode Technology: Fundamentals and Recent Breakthroughs
- Competitive Analysis: Leading Companies and Research Initiatives (e.g., saftbatteries.com, sionpower.com, basf.com)
- Manufacturing Advances: Scaling Up Sulfur Cathode Production
- Performance Metrics: Energy Density, Cycle Life, and Safety Improvements
- Market Forecast 2025–2030: CAGR, Volume, and Revenue Projections
- Application Spotlight: Electric Vehicles, Aerospace, and Grid Storage
- Supply Chain and Raw Material Challenges
- Regulatory, Environmental, and Sustainability Considerations (e.g., batteryassociation.org)
- Future Outlook: Next-Gen Cathode Materials and Commercialization Timeline
- Sources & References
Executive Summary: 2025 Market Landscape and Key Drivers
The lithium-sulfur (Li-S) battery sector is poised for significant transformation in 2025, driven by advances in cathode engineering and a growing demand for next-generation energy storage. Li-S batteries offer theoretical energy densities up to 500 Wh/kg—substantially higher than conventional lithium-ion systems—making them attractive for electric vehicles (EVs), aviation, and grid storage. The primary challenge remains the development of robust sulfur cathodes that can overcome issues such as polysulfide shuttle, low conductivity, and volume expansion during cycling.
In 2025, several industry leaders and innovators are accelerating the commercialization of Li-S technology. OXIS Energy, a UK-based pioneer, has been instrumental in developing advanced sulfur cathode formulations and proprietary electrolyte systems, although the company faced financial difficulties in recent years. Their legacy technology continues to influence ongoing projects and partnerships in Europe and Asia. Meanwhile, Sion Power in the United States is actively scaling up its Licerion-S platform, which integrates engineered sulfur cathodes with high-loading designs to achieve cycle life and energy density targets suitable for aerospace and automotive applications.
In Asia, China National Petroleum Corporation (CNPC) and its affiliates are investing in sulfur cathode research, leveraging their expertise in materials processing and large-scale manufacturing. These efforts are complemented by collaborations with academic institutions and government-backed initiatives aimed at establishing a domestic supply chain for Li-S batteries. Additionally, Samsung Electronics has disclosed ongoing research into sulfur-based cathode materials, with a focus on improving cycle stability and safety for consumer electronics and mobility sectors.
Key drivers for the 2025 market include the push for higher energy density to extend EV range, regulatory pressure to reduce reliance on critical minerals like cobalt and nickel, and the need for safer, lighter batteries in aviation. The European Union’s Battery Regulation and the U.S. Department of Energy’s funding for advanced battery manufacturing are catalyzing investment in Li-S cathode engineering. Industry roadmaps suggest that by 2027, Li-S batteries could achieve commercial viability in niche markets, with broader adoption contingent on further improvements in cathode durability and cost reduction.
In summary, 2025 marks a pivotal year for lithium-sulfur battery cathode engineering, with major players and new entrants intensifying R&D and pilot-scale production. The sector’s outlook is optimistic, underpinned by technological breakthroughs, supportive policy frameworks, and a clear trajectory toward commercialization in high-value applications.
Lithium-Sulfur Cathode Technology: Fundamentals and Recent Breakthroughs
Lithium-sulfur (Li-S) battery cathode engineering has emerged as a focal point in next-generation energy storage, driven by the promise of high theoretical energy density (up to 2,600 Wh/kg) and the abundance of sulfur. The fundamental challenge in Li-S cathode design lies in mitigating the polysulfide shuttle effect, which leads to rapid capacity fading and poor cycle life. Recent years have seen significant advances in cathode materials, architectures, and manufacturing approaches, with 2025 marking a period of accelerated progress toward commercialization.
A key breakthrough has been the development of nanostructured carbon-sulfur composites, which physically confine polysulfides and enhance electrical conductivity. Companies such as Sion Power and OXIS Energy (prior to its 2021 administration) have pioneered proprietary cathode formulations, focusing on encapsulating sulfur within porous carbon matrices or polymer hosts. These approaches have enabled laboratory-scale cells to achieve cycle lives exceeding 500 cycles at moderate capacities, a substantial improvement over earlier generations.
In 2025, attention has shifted toward scalable manufacturing and the integration of advanced binders and coatings. For instance, Sion Power has reported progress in roll-to-roll cathode fabrication, targeting automotive and aerospace applications. Their Licerion® technology leverages engineered cathode interfaces to suppress polysulfide migration, with prototype cells demonstrating energy densities above 400 Wh/kg. Meanwhile, The Faraday Institution in the UK coordinates collaborative research, supporting the translation of academic breakthroughs into industrially relevant processes.
Another area of innovation is the use of solid-state electrolytes and functional interlayers to further stabilize the cathode. Companies like Solid Power are exploring hybrid solid-state Li-S architectures, aiming to combine the safety and longevity of solid electrolytes with the high capacity of sulfur cathodes. Early prototypes have shown promise, but challenges remain in achieving uniform sulfur utilization and maintaining interface stability over extended cycling.
Looking ahead to the next few years, the outlook for Li-S cathode engineering is optimistic. Industry roadmaps anticipate pilot-scale production lines and the first commercial deployments in niche sectors such as high-altitude drones and electric aviation, where weight savings are critical. Continued collaboration between material suppliers, cell manufacturers, and end-users will be essential to address remaining hurdles in cycle life, manufacturability, and cost. As of 2025, the field is poised for transition from laboratory innovation to real-world impact, with leading companies and research consortia driving the pace of progress.
Competitive Analysis: Leading Companies and Research Initiatives (e.g., saftbatteries.com, sionpower.com, basf.com)
The competitive landscape for lithium-sulfur (Li-S) battery cathode engineering in 2025 is marked by a dynamic interplay between established battery manufacturers, innovative startups, and major chemical suppliers. The focus is on overcoming the intrinsic challenges of Li-S chemistry—namely, the polysulfide shuttle effect, limited cycle life, and low conductivity of sulfur cathodes—while capitalizing on the technology’s promise of high energy density and reduced reliance on critical minerals like cobalt and nickel.
Among the most prominent players, Saft, a subsidiary of TotalEnergies, has been at the forefront of industrializing Li-S technology. Saft’s research and pilot-scale production lines are targeting aviation and defense applications, leveraging proprietary cathode architectures that incorporate conductive carbon matrices and advanced binders to stabilize sulfur and suppress polysulfide migration. Their recent collaborations with aerospace partners underscore the near-term commercial potential of Li-S batteries in sectors where weight and energy density are paramount.
Another key innovator, Sion Power, is advancing its Licerion® technology, which integrates engineered sulfur cathodes with protected lithium metal anodes. Sion Power’s approach involves nano-structured cathode composites and electrolyte additives designed to extend cycle life and improve safety. The company has announced partnerships with electric vehicle and drone manufacturers, aiming for commercial deployment in the second half of the decade. Sion Power’s pilot cells have demonstrated energy densities exceeding 500 Wh/kg, a significant leap over conventional lithium-ion batteries.
On the materials supply side, BASF is investing in the development of high-purity sulfur and conductive additives tailored for Li-S cathode formulations. BASF’s expertise in chemical engineering and large-scale production is expected to play a crucial role in scaling up Li-S battery manufacturing, ensuring consistent quality and supply of critical cathode materials. The company is also collaborating with cell manufacturers to optimize cathode slurry processing and electrode coating techniques.
In addition to these leaders, several startups and research consortia in Europe and Asia are pursuing novel cathode designs, such as encapsulated sulfur nanoparticles, hybrid polymer-sulfur composites, and solid-state electrolytes to further mitigate the shuttle effect. The European Union’s Battery 2030+ initiative and various national programs in China and Japan are providing funding and infrastructure for pilot lines and demonstration projects, accelerating the path to commercialization.
Looking ahead, the next few years will likely see the first commercial deployments of Li-S batteries in niche markets, with ongoing cathode engineering innovations driving improvements in cycle life, safety, and manufacturability. As leading companies refine their processes and scale up production, Li-S technology is poised to become a competitive alternative to lithium-ion in applications demanding ultra-high energy density and sustainability.
Manufacturing Advances: Scaling Up Sulfur Cathode Production
The transition from laboratory-scale lithium-sulfur (Li-S) battery research to commercial-scale production hinges on significant advances in sulfur cathode manufacturing. As of 2025, the industry is witnessing a concerted push to overcome the inherent challenges of sulfur cathode engineering—namely, sulfur’s low electrical conductivity, volumetric expansion during cycling, and the polysulfide shuttle effect. These issues have historically limited the practical energy density and cycle life of Li-S batteries, but recent manufacturing innovations are beginning to address them at scale.
Key players in the battery sector are investing in scalable cathode fabrication techniques. For instance, Sion Power, a U.S.-based advanced battery manufacturer, has developed proprietary methods for integrating sulfur into composite cathodes, focusing on uniform sulfur distribution and robust conductive matrices. Their approach leverages roll-to-roll coating processes compatible with existing lithium-ion battery manufacturing lines, which is critical for cost-effective scale-up.
In Europe, OXIS Energy (now part of Johnson Matthey) previously pioneered water-based slurry processing for sulfur cathodes, which reduces environmental impact and improves process safety. Although OXIS Energy ceased operations in 2021, their intellectual property and pilot-scale manufacturing assets have been acquired and are being further developed by Johnson Matthey, a global leader in sustainable technologies. Johnson Matthey is now advancing these processes, aiming to deliver high-loading sulfur cathodes with improved cycle stability and manufacturability.
Asian manufacturers are also making significant strides. China National Energy and Contemporary Amperex Technology Co. Limited (CATL) are reportedly investing in pilot lines for Li-S batteries, with a focus on optimizing cathode slurry formulation and calendaring techniques to achieve high sulfur content (>70% by weight) while maintaining electrode integrity. These efforts are supported by automation and in-line quality control systems, which are essential for consistent large-scale production.
Looking ahead, the next few years are expected to see further integration of advanced materials—such as carbon nanotube networks and polymer binders—into cathode manufacturing. These materials enhance electronic conductivity and suppress polysulfide migration, enabling higher areal capacities and longer cycle life. Industry collaborations, such as those fostered by Batteries Europe, are accelerating the transfer of these innovations from research to industrial implementation.
Overall, the outlook for scaling up sulfur cathode production is increasingly positive. With major manufacturers refining scalable, environmentally friendly processes and integrating advanced materials, Li-S batteries are poised to move closer to commercial viability in the latter half of the 2020s, particularly for applications demanding high specific energy and lower raw material costs.
Performance Metrics: Energy Density, Cycle Life, and Safety Improvements
Lithium-sulfur (Li-S) battery cathode engineering has seen significant advancements in recent years, with a strong focus on improving key performance metrics such as energy density, cycle life, and safety. As of 2025, the industry is witnessing a transition from laboratory-scale breakthroughs to early-stage commercialization, driven by both established battery manufacturers and innovative startups.
Energy density remains a primary advantage of Li-S technology, with theoretical values approaching 2,600 Wh/kg—substantially higher than conventional lithium-ion batteries. In practice, recent prototypes and pre-commercial cells have demonstrated gravimetric energy densities in the range of 400–500 Wh/kg, with some companies reporting even higher values in controlled settings. For example, Sion Power has announced Li-S cells targeting over 500 Wh/kg, aiming to address the needs of electric aviation and long-range electric vehicles. Similarly, OXIS Energy (prior to its 2021 administration and subsequent technology transfer) had developed pouch cells with energy densities exceeding 400 Wh/kg, setting a benchmark for the sector.
Cycle life, historically a challenge for Li-S batteries due to polysulfide shuttle effects and cathode degradation, has seen marked improvements through advanced cathode engineering. Techniques such as encapsulating sulfur in porous carbon matrices, using conductive polymers, and incorporating solid-state electrolytes have extended cycle life to over 500 cycles at high capacities in recent demonstrations. LioNano and Sion Power are among the companies reporting significant progress in mitigating capacity fade, with ongoing efforts to reach the 1,000-cycle threshold required for mainstream automotive and grid applications.
Safety is another critical metric, especially as Li-S batteries move toward commercialization. The absence of oxygen release during thermal runaway and the use of non-flammable electrolytes in some designs contribute to improved safety profiles compared to traditional lithium-ion chemistries. Companies such as Sion Power and LioNano are actively developing cathode and electrolyte systems that minimize dendrite formation and thermal risks, with several prototypes undergoing rigorous safety testing in 2025.
Looking ahead, the next few years are expected to bring further gains in all three performance metrics as cathode engineering matures. Industry collaborations, pilot-scale manufacturing, and integration into niche markets such as aerospace and specialty vehicles are anticipated, with the potential for broader adoption as cycle life and safety continue to improve. The ongoing efforts of companies like Sion Power and LioNano will be pivotal in shaping the commercial landscape of Li-S batteries through 2025 and beyond.
Market Forecast 2025–2030: CAGR, Volume, and Revenue Projections
The market for lithium-sulfur (Li-S) battery cathode engineering is poised for significant growth between 2025 and 2030, driven by the urgent demand for next-generation energy storage solutions in electric vehicles (EVs), aviation, and grid-scale applications. Li-S batteries offer a theoretical energy density up to five times higher than conventional lithium-ion batteries, and recent advances in cathode engineering are addressing key challenges such as polysulfide shuttling and limited cycle life.
By 2025, the global Li-S battery market is expected to transition from pilot-scale to early commercial deployment, with several industry leaders and startups scaling up production. Companies such as Sion Power and OXIS Energy (noting OXIS’s recent insolvency but ongoing technology licensing) have been at the forefront of cathode material innovation, focusing on sulfur-carbon composites and advanced electrolyte formulations. Sion Power has demonstrated Li-S cells with energy densities exceeding 400 Wh/kg, targeting aviation and heavy-duty transport sectors.
Volume projections for Li-S battery cathodes are expected to rise sharply as automakers and aerospace manufacturers seek lighter, higher-capacity batteries. By 2030, annual global production of Li-S batteries could reach several gigawatt-hours (GWh), with cathode material demand scaling accordingly. Sion Power and LioNano are among the companies investing in pilot lines and semi-commercial facilities to meet this anticipated demand.
Revenue forecasts for the Li-S battery market vary, but industry consensus points to a compound annual growth rate (CAGR) of 25–30% from 2025 to 2030, outpacing traditional lithium-ion segments. This growth is underpinned by ongoing partnerships between battery developers and end-users in the automotive and aerospace sectors. For example, Sion Power has announced collaborations with major OEMs to integrate Li-S technology into next-generation vehicles.
Looking ahead, the market outlook for Li-S battery cathode engineering remains robust, contingent on continued improvements in cycle life, safety, and manufacturability. Industry players are expected to accelerate R&D and scale-up activities, with government funding and strategic alliances playing a pivotal role. As the technology matures, Li-S batteries are positioned to capture a growing share of the advanced battery market, particularly in applications where weight and energy density are critical.
Application Spotlight: Electric Vehicles, Aerospace, and Grid Storage
Lithium-sulfur (Li-S) battery cathode engineering is rapidly advancing, with significant implications for electric vehicles (EVs), aerospace, and grid storage applications in 2025 and the coming years. The promise of Li-S technology lies in its high theoretical energy density—up to 500 Wh/kg, far surpassing conventional lithium-ion batteries. This makes Li-S particularly attractive for sectors where weight and energy density are critical.
In the electric vehicle sector, several companies are actively developing Li-S batteries to address range and weight limitations. OXIS Energy, a UK-based pioneer, has focused on sulfur cathode optimization, achieving energy densities above 400 Wh/kg in prototype cells. Although OXIS Energy entered administration in 2021, its intellectual property and technology have been acquired and are being further developed by other industry players, with a focus on commercializing Li-S for EVs by mid-decade. Sion Power, based in the US, is also advancing Li-S cathode engineering, targeting the automotive market with its Licerion technology, which aims for high cycle life and safety.
Aerospace applications are another key focus, as the weight savings from Li-S batteries can significantly extend flight times for electric aircraft and drones. Sion Power and LiONANO are both working on cathode materials and cell designs tailored for high-altitude and long-endurance missions. In 2025, demonstration projects are underway with aerospace partners to validate Li-S performance under extreme conditions, with the goal of commercial deployment in the next few years.
For grid storage, the scalability and cost-effectiveness of sulfur as a cathode material are major advantages. Enerpoly and Sion Power are exploring large-format Li-S cells for stationary storage, aiming to deliver longer-duration storage at a lower cost per kWh than lithium-ion. These efforts are supported by collaborations with utility companies and government agencies, with pilot installations expected to expand in 2025 and beyond.
Despite these advances, challenges remain in cathode engineering, particularly in mitigating the polysulfide shuttle effect and improving cycle life. Companies are investing in novel cathode architectures, such as encapsulated sulfur particles and conductive carbon matrices, to address these issues. The outlook for Li-S battery cathode engineering is optimistic, with industry leaders projecting that commercial-scale adoption in EVs, aerospace, and grid storage could begin as early as 2026, contingent on continued progress in material stability and manufacturing scalability.
Supply Chain and Raw Material Challenges
The supply chain and raw material landscape for lithium-sulfur (Li-S) battery cathode engineering is rapidly evolving as the technology approaches commercial viability in 2025 and beyond. Unlike conventional lithium-ion batteries, Li-S batteries utilize sulfur as the primary cathode material, which is both abundant and low-cost compared to cobalt and nickel. However, the transition to large-scale Li-S production introduces new challenges in sourcing, processing, and integrating sulfur and advanced carbon materials, as well as ensuring the purity and consistency required for high-performance cathodes.
Sulfur, while plentiful as a byproduct of petroleum refining and natural gas processing, must meet stringent purity standards for battery applications. The global sulfur supply is dominated by major chemical and energy companies, with Shell and ExxonMobil among the largest producers. These companies are increasingly exploring partnerships with battery manufacturers to supply high-purity sulfur tailored for energy storage applications. In parallel, the development of advanced carbon hosts—such as graphene and carbon nanotubes—remains a critical factor for cathode performance, with companies like Cabot Corporation and Orion Engineered Carbons expanding their specialty carbon offerings to meet battery sector demand.
A key supply chain challenge is the integration of sulfur and carbon materials into scalable, high-performance cathode composites. This requires not only reliable raw material sources but also advanced processing capabilities. Companies such as OXIS Energy (now part of Johnson Matthey) and Sion Power have invested in proprietary cathode engineering processes to optimize sulfur utilization and cycle life, though the sector continues to face hurdles in achieving consistent large-scale production yields.
Geopolitical factors and environmental regulations are also shaping the Li-S supply chain. As sulfur is often sourced from oil and gas operations, fluctuations in fossil fuel markets and tightening emissions standards could impact availability and pricing. Battery manufacturers are therefore seeking to diversify supply, including exploring sulfur recovery from alternative sources such as mining and waste streams.
Looking ahead to the next few years, the outlook for Li-S cathode supply chains is cautiously optimistic. Industry collaborations are intensifying, with major chemical and battery firms forming alliances to secure raw materials and develop standardized processing protocols. As pilot-scale Li-S battery production ramps up in 2025, the sector’s ability to address raw material purity, supply stability, and sustainable sourcing will be pivotal in determining the pace of commercial adoption.
Regulatory, Environmental, and Sustainability Considerations (e.g., batteryassociation.org)
The regulatory, environmental, and sustainability landscape for lithium-sulfur (Li-S) battery cathode engineering is rapidly evolving as the technology approaches commercial viability in 2025 and beyond. Regulatory bodies and industry associations are increasingly focused on ensuring that the next generation of batteries, including Li-S, align with global sustainability goals and responsible sourcing practices.
One of the primary regulatory drivers is the European Union’s Battery Regulation, which came into force in 2023 and will be fully implemented over the next few years. This regulation mandates strict requirements for carbon footprint disclosure, recycled content, and responsible sourcing of raw materials for all batteries placed on the EU market. For Li-S batteries, this means cathode materials—primarily sulfur and lithium—must be sourced and processed in compliance with these standards. The regulation also sets ambitious targets for end-of-life collection and recycling, which will directly impact the design and engineering of Li-S cathodes to facilitate recyclability and minimize environmental impact (Battery Association).
From an environmental perspective, Li-S batteries offer several advantages over conventional lithium-ion chemistries. Sulfur is abundant, inexpensive, and non-toxic, reducing reliance on critical minerals such as cobalt and nickel, which are associated with significant environmental and social concerns. Companies like OXIS Energy (now part of Johnson Matthey) and Sion Power have highlighted the potential for Li-S cathodes to lower the overall carbon footprint of battery production. However, the use of lithium metal anodes in many Li-S designs still raises questions about lithium sourcing and the environmental impact of extraction, particularly as demand scales up.
Sustainability considerations are also driving innovation in cathode engineering. Manufacturers are exploring the use of recycled sulfur from industrial byproducts and closed-loop recycling systems for both lithium and sulfur components. Industry groups such as the Battery Association are working with stakeholders to develop best practices and certification schemes for sustainable battery materials, which are expected to become increasingly important as Li-S batteries enter mass production.
Looking ahead, regulatory frameworks are likely to become more stringent, with increased scrutiny on supply chain transparency and lifecycle impacts. Companies investing in Li-S battery technology will need to prioritize eco-design, recyclability, and responsible sourcing to meet both regulatory requirements and growing consumer expectations for sustainable energy storage solutions. The next few years will be critical in establishing industry standards and ensuring that Li-S cathode engineering contributes positively to the global transition toward cleaner energy.
Future Outlook: Next-Gen Cathode Materials and Commercialization Timeline
The outlook for lithium-sulfur (Li-S) battery cathode engineering in 2025 and the following years is marked by rapid advancements in material science and a growing push toward commercialization. Li-S batteries are widely recognized for their high theoretical energy density—up to 2,600 Wh/kg, significantly surpassing conventional lithium-ion batteries. However, the path to market has been hindered by challenges such as the polysulfide shuttle effect, limited cycle life, and cathode degradation. Recent years have seen a surge in research and pilot-scale production aimed at overcoming these barriers.
In 2025, several companies are expected to transition from laboratory-scale breakthroughs to pre-commercial and early commercial deployments. OXIS Energy, a UK-based pioneer in Li-S technology, has been developing advanced sulfur cathodes with proprietary electrolyte formulations to suppress polysulfide migration. Although OXIS Energy entered administration in 2021, its intellectual property and assets have been acquired and are being leveraged by other industry players, indicating continued momentum in the sector.
Another key player, Sion Power, is actively developing Li-S batteries for electric vehicle (EV) and aerospace applications. Sion Power’s Licerion-S platform focuses on engineered cathode architectures and protective coatings to enhance cycle life and energy density. The company has announced plans to scale up production and target commercial partnerships in the 2025–2027 timeframe, with prototypes already undergoing field testing.
In Asia, China National Petroleum Corporation (CNPC) and its affiliates are investing in sulfur cathode research, leveraging their expertise in sulfur chemistry and large-scale manufacturing. These efforts are complemented by collaborations with academic institutions and battery manufacturers to accelerate the transition from pilot lines to mass production.
The next few years are expected to see the introduction of Li-S batteries in niche markets such as high-altitude drones, aviation, and specialty vehicles, where weight savings and high energy density are critical. As cathode engineering matures—incorporating nanostructured carbon hosts, solid-state electrolytes, and advanced binders—cycle life and safety are projected to improve, making Li-S batteries increasingly viable for mainstream EVs and grid storage by the late 2020s.
Overall, the commercialization timeline for next-generation Li-S cathode materials is accelerating, with 2025 marking a pivotal year for pilot deployments and strategic partnerships. Continued investment from established energy and materials companies, combined with advances in cathode design, is expected to drive the sector toward broader adoption and cost competitiveness within the decade.
Sources & References
- Sion Power
- BASF
- Contemporary Amperex Technology Co. Limited (CATL)
- LioNano
- Enerpoly
- Shell
- ExxonMobil
- Cabot Corporation
- Orion Engineered Carbons