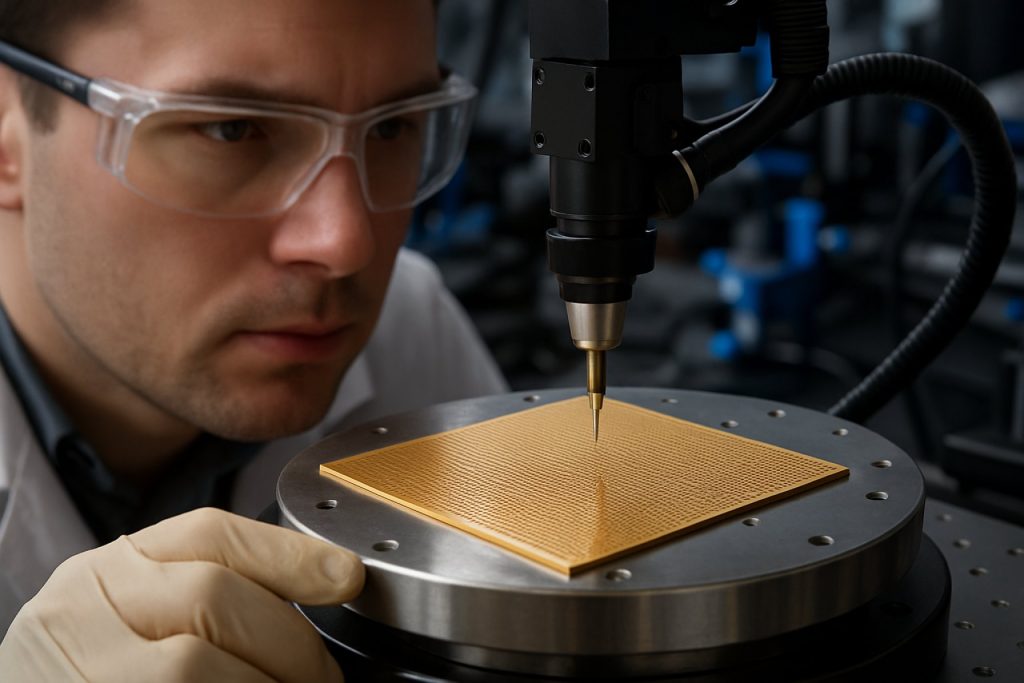
Revolutionizing Terahertz Imaging: How Metamaterial Fabrication in 2025 Is Shaping the Next Wave of High-Resolution Sensing. Explore the Market Forces, Innovations, and Strategic Opportunities Driving This Transformative Sector.
- Executive Summary: 2025 Market Landscape and Key Takeaways
- Metamaterial Fundamentals: Principles and Relevance to Terahertz Imaging
- Current Fabrication Techniques: Advances and Limitations
- Emerging Materials and Nanofabrication Innovations
- Market Size, Segmentation, and 2025–2030 Growth Forecasts
- Key Industry Players and Strategic Partnerships
- Application Spotlight: Security, Medical, and Industrial Use Cases
- Regulatory Environment and Standardization Efforts
- Investment Trends, Funding, and M&A Activity
- Future Outlook: Technology Roadmap and Competitive Opportunities
- Sources & References
Executive Summary: 2025 Market Landscape and Key Takeaways
The metamaterial fabrication sector for terahertz (THz) imaging is poised for significant advancements and market expansion in 2025, driven by rapid technological progress and increasing demand across security, medical, and industrial inspection applications. Metamaterials—engineered structures with unique electromagnetic properties—are enabling breakthroughs in THz imaging by overcoming traditional material limitations, such as low sensitivity and high losses at terahertz frequencies.
In 2025, the market landscape is characterized by a shift from laboratory-scale prototypes to scalable, commercially viable fabrication processes. Key players are investing in advanced lithography, nanoimprint, and additive manufacturing techniques to produce large-area, high-uniformity metamaterial films and devices. For instance, Metamaterial Inc. (META®), a leading developer of functional materials and photonic solutions, has expanded its manufacturing capabilities to support volume production of metamaterial-based THz components. Their focus on roll-to-roll and sheet-to-sheet processes is expected to lower costs and accelerate adoption in imaging systems.
Another notable company, NKT Photonics, is advancing the integration of metamaterial structures with THz sources and detectors, aiming to enhance imaging resolution and sensitivity. Meanwhile, TOPTICA Photonics AG continues to collaborate with research institutions to develop tunable THz sources and metamaterial-enabled sensors, targeting applications in non-destructive testing and biomedical diagnostics.
The sector is also witnessing increased collaboration between material suppliers, device manufacturers, and end-users. For example, Oxford Instruments provides deposition and etching equipment tailored for precise metamaterial patterning, supporting both established companies and startups in the THz imaging space. Such partnerships are crucial for scaling up production and ensuring device reliability.
Looking ahead, the next few years will likely see further improvements in fabrication throughput, cost efficiency, and device performance. The adoption of AI-driven design tools and in-line quality control is expected to streamline manufacturing and reduce defect rates. As regulatory standards for THz imaging in security and healthcare become more defined, companies with robust, scalable fabrication capabilities will be well-positioned to capture emerging opportunities.
In summary, 2025 marks a pivotal year for metamaterial fabrication in terahertz imaging, with the market transitioning toward industrial-scale production and broader commercial deployment. The competitive landscape is shaped by innovation in manufacturing processes, strategic partnerships, and a focus on end-user requirements, setting the stage for sustained growth and technological leadership in the coming years.
Metamaterial Fundamentals: Principles and Relevance to Terahertz Imaging
Metamaterial fabrication for terahertz (THz) imaging is advancing rapidly, driven by the demand for high-performance, cost-effective devices in security screening, medical diagnostics, and industrial inspection. Metamaterials—engineered composites with tailored electromagnetic properties—enable unprecedented control over THz waves, including negative refractive index, cloaking, and superlensing effects. The fabrication of these materials for THz applications in 2025 is characterized by a convergence of micro- and nanofabrication techniques, scalable manufacturing, and integration with semiconductor processes.
Current fabrication methods include electron-beam lithography, photolithography, nanoimprint lithography, and direct laser writing. These techniques allow for the precise patterning of sub-wavelength structures essential for manipulating THz radiation. For instance, Nanoscribe is recognized for its two-photon polymerization 3D printing systems, which enable the creation of complex metamaterial geometries with feature sizes down to the hundreds of nanometers, suitable for THz frequencies. Similarly, Oxford Instruments provides advanced plasma etching and deposition tools widely used in the fabrication of metamaterial layers on silicon and other substrates.
In 2025, there is a notable shift toward scalable and cost-effective production. Roll-to-roll nanoimprint lithography is being adopted for large-area metamaterial films, enabling the mass production of flexible and conformal THz devices. Companies such as NIL Technology are at the forefront, offering nanoimprint solutions that support high-throughput manufacturing of metamaterial patterns for THz imaging arrays. Additionally, integration with CMOS-compatible processes is a key trend, as it allows for the co-fabrication of metamaterial structures with conventional electronic and photonic components, paving the way for compact, on-chip THz imaging systems.
Material innovation is also a focus, with research and development into low-loss dielectrics, high-conductivity metals, and novel 2D materials like graphene to enhance THz performance. Graphenea is a leading supplier of high-quality graphene, which is being explored for tunable and reconfigurable THz metamaterials due to its unique electronic properties.
Looking ahead, the outlook for metamaterial fabrication in THz imaging is promising. The next few years are expected to see further improvements in fabrication resolution, throughput, and integration, driven by collaborations between equipment manufacturers, material suppliers, and end-users. As these advances mature, they will enable the deployment of high-sensitivity, real-time THz imaging systems in a broader range of applications, from non-destructive testing to biomedical imaging.
Current Fabrication Techniques: Advances and Limitations
The fabrication of metamaterials for terahertz (THz) imaging has seen significant progress in recent years, driven by the demand for high-performance, scalable, and cost-effective solutions. As of 2025, several advanced techniques are being employed and refined to meet the stringent requirements of THz imaging systems, including high spatial resolution, low loss, and tunability.
Photolithography remains the cornerstone for fabricating planar metamaterial structures, particularly for frequencies in the lower THz range. This technique, widely adopted by semiconductor manufacturers, enables precise patterning of sub-micron features on substrates such as silicon and quartz. Companies like ASML and Canon provide the photolithography equipment that underpins much of the current research and commercial development in this area. However, the cost and complexity of photolithography, especially for large-area or flexible substrates, remain significant limitations.
Electron-beam lithography (EBL) offers even finer resolution, making it suitable for prototyping and research-scale production of THz metamaterials with intricate geometries. While EBL is indispensable for pushing the boundaries of feature size, its low throughput and high operational costs restrict its use to small-scale fabrication. Companies such as JEOL and Thermo Fisher Scientific are leading suppliers of EBL systems.
Nanoimprint lithography (NIL) is gaining traction as a promising alternative for large-area, high-throughput fabrication of THz metamaterials. NIL enables the replication of nanoscale patterns over substantial areas at relatively low cost, making it attractive for commercial-scale production. Equipment providers like Nanonex and SÜSS MicroTec are actively advancing NIL technology for metamaterial applications.
Additive manufacturing, particularly two-photon polymerization and direct laser writing, is emerging as a flexible approach for fabricating complex three-dimensional metamaterial architectures. These methods allow for rapid prototyping and the creation of novel structures that are challenging to realize with traditional lithography. Companies such as Nanoscribe are at the forefront of commercializing these techniques for photonic and THz applications.
Despite these advances, several challenges persist. Achieving uniformity and reproducibility over large areas, integrating active materials for tunable THz response, and reducing fabrication costs are ongoing concerns. In the next few years, the field is expected to benefit from further automation, hybrid fabrication approaches, and the integration of novel materials such as graphene and phase-change compounds. Industry collaborations and investments from major photonics and semiconductor equipment manufacturers are likely to accelerate the transition from laboratory-scale demonstrations to scalable, commercial THz imaging systems.
Emerging Materials and Nanofabrication Innovations
The field of metamaterial fabrication for terahertz (THz) imaging is experiencing rapid innovation, driven by the demand for high-resolution, non-invasive imaging in security, medical diagnostics, and industrial inspection. As of 2025, the focus is on scalable nanofabrication techniques and the integration of novel materials to overcome the traditional limitations of THz devices, such as low sensitivity and high production costs.
Recent advances in nanofabrication have enabled the production of metamaterials with sub-wavelength features, essential for manipulating THz waves. Electron-beam lithography (EBL) and nanoimprint lithography (NIL) remain the primary methods for fabricating these intricate structures, with companies like Nanoscribe GmbH and Raith GmbH providing state-of-the-art direct laser writing and EBL systems, respectively. These tools allow for the creation of three-dimensional (3D) metamaterial architectures with feature sizes down to the tens of nanometers, which is critical for achieving the desired electromagnetic responses in the THz regime.
Material innovation is another key trend. Researchers and manufacturers are increasingly turning to two-dimensional (2D) materials such as graphene and transition metal dichalcogenides (TMDs) for their tunable electronic and optical properties. Companies like Graphenea are supplying high-quality graphene, which is being integrated into metamaterial designs to enable active modulation of THz waves. Additionally, flexible substrates and polymers are being explored to produce conformal and wearable THz imaging devices, with suppliers such as DuPont offering advanced polymer films suitable for these applications.
In 2025, there is a notable push towards scalable, cost-effective manufacturing. Roll-to-roll nanoimprint lithography and large-area self-assembly techniques are being developed to facilitate mass production of metamaterial films. Obducat AB is among the companies advancing NIL for high-throughput fabrication, targeting both research and industrial markets.
Looking ahead, the next few years are expected to see further convergence of material science and nanofabrication, with hybrid metamaterials—combining metals, dielectrics, and 2D materials—poised to deliver tunable, high-performance THz imaging components. Industry collaborations and pilot production lines are anticipated to accelerate commercialization, particularly as end-users in security and healthcare demand compact, affordable THz imaging systems. The ongoing evolution of fabrication tools and materials supply chains, led by companies like Nanoscribe GmbH, Graphenea, and DuPont, will be pivotal in shaping the THz metamaterial landscape through 2025 and beyond.
Market Size, Segmentation, and 2025–2030 Growth Forecasts
The global market for metamaterial fabrication tailored to terahertz (THz) imaging is poised for significant expansion between 2025 and 2030, driven by advances in material science, increasing demand for high-resolution imaging, and the proliferation of security, medical, and industrial applications. As of 2025, the market is characterized by a growing number of specialized manufacturers and research-driven startups, with a focus on scalable, cost-effective production methods for complex metamaterial structures.
Segmentation within the market is primarily based on application (security screening, medical diagnostics, non-destructive testing, and scientific research), fabrication technique (lithography, 3D printing, nanoimprint, and self-assembly), and end-user (government, healthcare, industrial, and academic sectors). Security and defense remain the largest application segment, leveraging THz metamaterials for advanced imaging systems capable of detecting concealed threats with high sensitivity. Medical imaging is rapidly emerging, with metamaterial-based THz devices offering non-ionizing, high-contrast imaging for early disease detection.
Key players in the metamaterial fabrication landscape include Metamaterial Inc., a pioneer in commercializing functional metamaterials for electromagnetic applications, and NKT Photonics, which integrates advanced photonic components into THz imaging systems. TeraView Limited is notable for its proprietary THz imaging platforms, often incorporating custom-fabricated metamaterial components. Additionally, ams-OSRAM AG and Thorlabs, Inc. supply critical photonic and optoelectronic components that enable the integration of metamaterials into commercial THz imaging devices.
From 2025 to 2030, the market is expected to witness a compound annual growth rate (CAGR) in the double digits, fueled by ongoing miniaturization, improved fabrication throughput, and the transition from laboratory-scale prototypes to mass-produced devices. The adoption of roll-to-roll nanoimprint lithography and additive manufacturing is anticipated to lower production costs and enable large-area metamaterial films, further broadening the addressable market. Strategic collaborations between material suppliers, device manufacturers, and end-users are likely to accelerate commercialization and standardization efforts.
Looking ahead, the outlook for metamaterial fabrication in THz imaging is robust, with increasing investment in R&D and pilot production lines. The convergence of advanced materials, photonics, and semiconductor manufacturing is expected to yield new device architectures and unlock novel applications, particularly in real-time security screening and portable medical diagnostics. As industry standards mature and supply chains stabilize, the sector is positioned for sustained growth through 2030 and beyond.
Key Industry Players and Strategic Partnerships
The landscape of metamaterial fabrication for terahertz (THz) imaging is rapidly evolving, with several industry leaders and innovative startups driving advancements through strategic partnerships and technology development. As of 2025, the sector is characterized by a blend of established photonics and materials companies, as well as specialized metamaterial firms, all vying to commercialize scalable, high-performance THz imaging solutions.
A prominent player in this space is Metamaterial Inc., a company specializing in the design and manufacture of functional materials and nanostructures. Their focus on scalable fabrication methods, such as roll-to-roll nanoimprinting and advanced lithography, positions them at the forefront of supplying metamaterial components for THz imaging systems. The company has announced collaborations with leading photonics and defense contractors to integrate their metamaterial films into next-generation security and medical imaging devices.
Another key contributor is TeraView Limited, recognized for its expertise in terahertz technology and imaging systems. TeraView has established partnerships with semiconductor manufacturers and research institutions to co-develop metamaterial-based THz sources and detectors, aiming to enhance sensitivity and resolution in industrial inspection and biomedical imaging applications.
In the United States, Northrop Grumman Corporation is actively investing in metamaterial research for defense and security applications, including THz imaging for concealed threat detection. The company collaborates with academic institutions and government agencies to accelerate the transition of laboratory-scale metamaterial fabrication techniques to mass production, focusing on reliability and cost-effectiveness.
On the materials supply side, Oxford Instruments plc provides advanced deposition and etching equipment crucial for the precise fabrication of metamaterial structures at terahertz frequencies. Their systems are widely adopted by both commercial and academic R&D labs, supporting the development of novel THz imaging components.
Strategic partnerships are increasingly shaping the sector’s outlook. For example, alliances between metamaterial developers and established imaging system integrators are expediting the commercialization of THz imaging platforms for security screening, non-destructive testing, and medical diagnostics. These collaborations are expected to intensify over the next few years, as the demand for high-throughput, cost-effective THz imaging solutions grows.
Looking ahead, the industry is poised for further consolidation and cross-sector partnerships, particularly as end-users in healthcare, aerospace, and manufacturing seek to leverage the unique capabilities of metamaterial-enabled THz imaging. The next few years will likely see increased investment in pilot production lines, joint ventures, and technology licensing agreements, accelerating the path from prototype to market-ready systems.
Application Spotlight: Security, Medical, and Industrial Use Cases
Metamaterial fabrication for terahertz (THz) imaging is rapidly advancing, with 2025 marking a pivotal year for the deployment of these technologies in security, medical, and industrial sectors. The unique electromagnetic properties of metamaterials—engineered structures with sub-wavelength features—enable unprecedented control over THz waves, which are non-ionizing and can penetrate materials opaque to visible light. This makes them ideal for imaging concealed objects, biological tissues, and industrial components.
In security, THz imaging systems based on metamaterials are being integrated into airport scanners and checkpoint devices, offering high-resolution, non-invasive detection of weapons, explosives, and contraband. Companies such as Toyota Industries Corporation and Lockheed Martin have invested in research and pilot deployments of THz scanners, leveraging metamaterial-based antennas and filters to enhance sensitivity and reduce false positives. These systems are expected to see broader adoption in 2025, particularly as governments seek to modernize critical infrastructure.
In the medical field, metamaterial-enabled THz imaging is being explored for early cancer detection, burn assessment, and dental diagnostics. The non-ionizing nature of THz radiation allows for safe, repeated imaging, while metamaterial components improve spatial resolution and contrast. Thorlabs, a leading photonics manufacturer, has developed prototype THz imaging modules incorporating metamaterial lenses and waveguides, targeting both research and clinical markets. Additionally, Carl Zeiss AG is collaborating with academic partners to refine metamaterial-based THz endoscopes for minimally invasive procedures.
Industrial applications are also expanding, with THz imaging systems used for non-destructive testing (NDT) of composite materials, quality control in pharmaceuticals, and detection of defects in semiconductor wafers. Oxford Instruments and HORIBA are actively developing turnkey THz imaging solutions that incorporate metamaterial filters and modulators, enabling faster and more accurate inspection processes. These systems are being piloted in automotive and electronics manufacturing plants, with commercial rollouts anticipated in the next few years.
Looking ahead, the outlook for metamaterial fabrication in THz imaging is robust. Advances in scalable nanofabrication—such as nanoimprint lithography and roll-to-roll processing—are reducing costs and enabling mass production of complex metamaterial structures. As a result, industry leaders and new entrants alike are poised to deliver compact, affordable THz imaging devices across security, medical, and industrial domains, with significant market growth expected through 2025 and beyond.
Regulatory Environment and Standardization Efforts
The regulatory environment and standardization efforts surrounding metamaterial fabrication for terahertz (THz) imaging are rapidly evolving as the technology matures and moves toward broader commercial deployment. In 2025, the focus is on harmonizing safety, performance, and interoperability standards to facilitate adoption in sectors such as security screening, medical diagnostics, and industrial inspection.
Globally, regulatory bodies are beginning to address the unique challenges posed by THz metamaterials, particularly regarding electromagnetic emissions, device reliability, and material safety. The International Electrotechnical Commission (IEC) and the International Organization for Standardization (ISO) are actively developing guidelines for THz device characterization, including standardized test methods for metamaterial-based components. These efforts aim to ensure that devices meet minimum performance thresholds and can be reliably integrated into existing imaging systems.
In the United States, the Federal Communications Commission (FCC) continues to regulate the electromagnetic spectrum, including the THz band, to prevent interference with other wireless technologies. The FCC is working with industry stakeholders to define emission limits and compliance procedures for new THz imaging devices, which often incorporate metamaterial-based antennas and modulators. Meanwhile, the National Institute of Standards and Technology (NIST) is collaborating with manufacturers and research institutions to develop reference materials and calibration protocols specific to metamaterial-enabled THz systems.
In Europe, the European Committee for Electrotechnical Standardization (CENELEC) and the European Telecommunications Standards Institute (ETSI) are leading initiatives to align THz imaging standards with broader EU directives on radio equipment and electromagnetic compatibility. These organizations are also considering the environmental impact of advanced metamaterial fabrication processes, including the use of novel nanomaterials and potential recycling requirements.
Industry consortia, such as the Semiconductor Industry Association (SIA), are increasingly involved in shaping best practices for the fabrication and integration of metamaterials in THz devices. Leading manufacturers, including Northrop Grumman and TeraView, are participating in pilot programs to validate compliance with emerging standards and to provide feedback on manufacturability and scalability.
Looking ahead, the next few years are expected to bring greater regulatory clarity and the publication of comprehensive standards for metamaterial-based THz imaging. This will likely accelerate commercialization, reduce barriers to market entry, and foster international collaboration, ensuring that safety and performance benchmarks keep pace with rapid technological advances.
Investment Trends, Funding, and M&A Activity
The investment landscape for metamaterial fabrication in terahertz (THz) imaging is experiencing notable momentum as of 2025, driven by the convergence of advanced manufacturing, semiconductor innovation, and the expanding application base in security, medical diagnostics, and industrial inspection. Venture capital and strategic corporate investments are increasingly targeting startups and scale-ups that demonstrate scalable fabrication techniques and integration with existing THz systems.
A key player in this space is Meta Materials Inc., a publicly traded company specializing in functional materials and nanofabrication. The company has attracted significant funding rounds in recent years, leveraging its proprietary roll-to-roll and lithography-based processes to produce large-area metamaterials suitable for THz imaging. Their partnerships with defense and aerospace primes have further catalyzed investment, as these sectors seek to enhance non-destructive testing and concealed object detection capabilities.
Another notable entity is NKT Photonics, which, while primarily known for photonic crystal fibers and lasers, has expanded its portfolio to include THz components and metamaterial-enabled devices. The company’s ongoing collaborations with European research consortia and industrial partners have attracted both public and private funding, particularly from innovation programs focused on next-generation imaging technologies.
Mergers and acquisitions (M&A) activity is also intensifying. In 2024, Meta Materials Inc. completed the acquisition of a UK-based nanofabrication startup, consolidating its intellectual property and expanding its manufacturing footprint in Europe. This move reflects a broader trend of established photonics and materials companies acquiring niche metamaterial fabricators to accelerate time-to-market and secure supply chains for THz imaging modules.
On the funding front, government-backed initiatives in the US, EU, and Asia are providing non-dilutive grants and co-investment opportunities for companies developing scalable metamaterial fabrication for THz applications. For example, the European Commission’s Horizon Europe program continues to support collaborative projects involving THz metamaterials, with several consortia including industrial partners such as NKT Photonics and leading academic institutions.
Looking ahead, the next few years are expected to see further consolidation as larger photonics and semiconductor companies seek to vertically integrate metamaterial capabilities. The influx of capital is likely to accelerate the transition from laboratory-scale fabrication to high-throughput manufacturing, with a focus on cost reduction and reliability for commercial THz imaging systems. As the market matures, strategic investments and M&A will remain central to shaping the competitive landscape and driving innovation in this rapidly evolving sector.
Future Outlook: Technology Roadmap and Competitive Opportunities
The future of metamaterial fabrication for terahertz (THz) imaging is poised for significant advancements in 2025 and the following years, driven by both technological innovation and increasing commercial interest. The THz frequency range (0.1–10 THz) offers unique imaging capabilities for security screening, medical diagnostics, and industrial inspection, but widespread adoption has been limited by fabrication challenges, cost, and scalability.
Recent years have seen a shift from laboratory-scale demonstrations to early-stage commercialization, with several companies and research institutions focusing on scalable, cost-effective manufacturing methods. Key players such as Metamaterial Inc. are actively developing proprietary fabrication techniques, including roll-to-roll nanoimprint lithography and large-area patterning, to produce metamaterial films and components suitable for THz applications. These methods promise to reduce production costs and enable integration into existing imaging systems.
In 2025, the technology roadmap is expected to emphasize the following areas:
- Scalable Manufacturing: Companies are investing in high-throughput fabrication processes, such as nanoimprint lithography and advanced photolithography, to produce metamaterial structures over large areas. Metamaterial Inc. and other industry leaders are targeting wafer-scale and flexible substrate production, which is critical for commercial THz imaging devices.
- Material Innovation: The development of new polymers, hybrid composites, and 2D materials is expected to enhance the performance and durability of THz metamaterials. Research collaborations with academic institutions and material suppliers are accelerating the discovery of materials with tailored electromagnetic properties.
- Integration with Electronics: The next few years will see increased efforts to integrate metamaterial components with THz sources, detectors, and readout electronics. This integration is essential for compact, robust, and user-friendly imaging systems.
- Standardization and Certification: As the market matures, industry bodies and consortia are likely to establish standards for THz metamaterial components, ensuring interoperability and reliability across applications.
Competitive opportunities are emerging for companies that can deliver high-performance, cost-effective metamaterial solutions at scale. Early movers such as Metamaterial Inc. are positioning themselves as key suppliers for security, healthcare, and industrial imaging markets. Meanwhile, established photonics and semiconductor manufacturers are exploring partnerships and acquisitions to accelerate their entry into the THz metamaterial space.
Looking ahead, the convergence of scalable fabrication, material innovation, and system integration is expected to drive rapid growth in THz imaging applications. Companies that invest in advanced manufacturing capabilities and strategic collaborations will be well-placed to capture emerging opportunities as the technology transitions from research to real-world deployment.
Sources & References
- Metamaterial Inc.
- NKT Photonics
- TOPTICA Photonics AG
- Oxford Instruments
- Nanoscribe
- ASML
- Canon
- JEOL
- Thermo Fisher Scientific
- Nanonex
- SÜSS MicroTec
- Raith GmbH
- DuPont
- Obducat AB
- TeraView Limited
- ams-OSRAM AG
- Thorlabs, Inc.
- Northrop Grumman Corporation
- Toyota Industries Corporation
- Lockheed Martin
- Carl Zeiss AG
- Oxford Instruments
- HORIBA
- International Organization for Standardization
- National Institute of Standards and Technology
- European Committee for Electrotechnical Standardization
- Semiconductor Industry Association