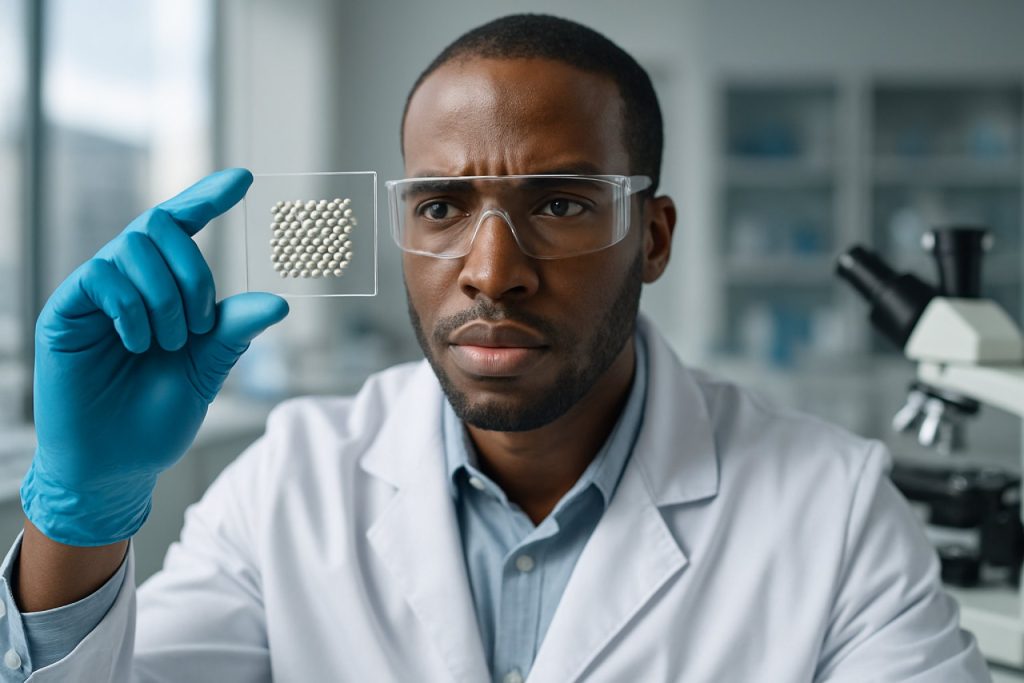
Nanomaterials Synthesis Engineering in 2025: Unleashing Next-Gen Manufacturing, Market Expansion, and Disruptive Technologies. Explore How Advanced Synthesis is Shaping the Future of Materials Science.
- Executive Summary: Key Trends and Market Drivers in 2025
- Global Market Size, Segmentation, and 2025–2029 Growth Forecasts
- Emerging Synthesis Techniques: From Bottom-Up to Green Chemistry
- Key Applications: Electronics, Energy, Healthcare, and Beyond
- Leading Players and Strategic Initiatives (e.g., nano.gov, basf.com, dupont.com)
- Supply Chain Innovations and Raw Material Sourcing
- Regulatory Landscape and Industry Standards (e.g., iso.org, ieee.org)
- Investment, Funding, and M&A Activity in Nanomaterials Engineering
- Challenges: Scalability, Safety, and Environmental Impact
- Future Outlook: Disruptive Technologies and Market Opportunities Through 2029
- Sources & References
Executive Summary: Key Trends and Market Drivers in 2025
Nanomaterials synthesis engineering is poised for significant advancements in 2025, driven by escalating demand across sectors such as electronics, energy storage, healthcare, and advanced manufacturing. The field is characterized by rapid innovation in scalable, cost-effective, and environmentally sustainable synthesis methods, as well as the integration of automation and digitalization in production processes.
A key trend is the transition from laboratory-scale to industrial-scale nanomaterial production. Companies are investing in continuous flow reactors, plasma-based synthesis, and green chemistry approaches to meet the growing requirements for high-purity, uniform nanomaterials. For instance, BASF and Evonik Industries—both global leaders in specialty chemicals—are expanding their nanomaterials portfolios, focusing on scalable synthesis routes for nanoparticles and nanostructured materials used in coatings, batteries, and catalysis.
Automation and digital process control are becoming central to nanomaterials engineering. The adoption of artificial intelligence (AI) and machine learning for process optimization is accelerating, enabling real-time monitoring and quality control. Oxford Instruments, a prominent supplier of nanotechnology tools, is advancing automated synthesis and characterization platforms, which are expected to reduce production costs and improve reproducibility.
Sustainability is another major driver. The industry is under pressure to minimize environmental impact by reducing solvent use, energy consumption, and hazardous byproducts. Companies such as Nanophase Technologies are pioneering eco-friendly synthesis techniques, including aqueous-phase and low-temperature processes, to align with global regulatory trends and customer expectations.
In the energy sector, the push for high-performance batteries and supercapacitors is fueling demand for engineered nanomaterials like graphene, carbon nanotubes, and silicon nanostructures. Samsung and LG Chem are actively developing advanced nanomaterial synthesis for next-generation energy storage devices, aiming for higher energy densities and longer lifespans.
Looking ahead, the outlook for nanomaterials synthesis engineering remains robust. The convergence of digital manufacturing, green chemistry, and end-user demand is expected to drive double-digit growth in the sector over the next few years. Strategic collaborations between material suppliers, equipment manufacturers, and end-users will be crucial in overcoming scale-up challenges and accelerating commercialization of novel nanomaterials.
Global Market Size, Segmentation, and 2025–2029 Growth Forecasts
The global market for nanomaterials synthesis engineering is poised for robust expansion through 2025 and into the latter part of the decade, driven by accelerating demand across electronics, energy, healthcare, and advanced materials sectors. As of 2025, the nanomaterials market is estimated to be valued in the tens of billions of US dollars, with leading industry participants reporting double-digit annual growth rates in both production capacity and revenue. The market is broadly segmented by material type (carbon-based, metal-based, dendrimers, composites), synthesis method (physical, chemical, biological), and end-use industry (electronics, energy, healthcare, automotive, coatings, and others).
Key players in nanomaterials synthesis engineering include BASF, a global chemical giant with extensive nanomaterials R&D and manufacturing capabilities, and Arkema, which has invested heavily in carbon nanotube and nanocomposite production. Evonik Industries is another major supplier, focusing on silica and metal oxide nanoparticles for industrial and consumer applications. In Asia, Showa Denko and Mitsui Chemicals are prominent, with significant investments in nanomaterials for batteries, coatings, and electronics. North American firms such as Chemours and Cabot Corporation are also expanding their nanomaterials portfolios, particularly in conductive additives and specialty carbons.
Segmentation by synthesis method reveals a growing preference for scalable, environmentally friendly processes. Chemical vapor deposition (CVD), sol-gel, and hydrothermal synthesis remain dominant for high-purity nanomaterials, while green synthesis methods—using biological agents or low-energy processes—are gaining traction, especially in Europe and Japan. The electronics and energy storage sectors are the largest consumers, with nanomaterials enabling next-generation batteries, supercapacitors, and flexible electronics. Healthcare applications, including drug delivery and diagnostics, are also expanding rapidly, supported by regulatory advances and increased investment in nanomedicine.
Looking ahead to 2029, industry forecasts anticipate a compound annual growth rate (CAGR) in the high single to low double digits, with the Asia-Pacific region outpacing other geographies due to aggressive manufacturing expansion and government support. Companies are expected to invest in both capacity and process innovation, with a focus on cost reduction, quality control, and sustainability. Strategic partnerships between material suppliers, device manufacturers, and research institutions are likely to accelerate commercialization of novel nanomaterials and synthesis techniques, further broadening the market’s scope and impact.
Emerging Synthesis Techniques: From Bottom-Up to Green Chemistry
In 2025, nanomaterials synthesis engineering is witnessing a dynamic shift, driven by the convergence of advanced bottom-up fabrication methods and the imperative for sustainable, green chemistry approaches. The bottom-up synthesis paradigm—where nanostructures are assembled atom-by-atom or molecule-by-molecule—remains central to the production of high-purity, precisely controlled nanomaterials. Techniques such as chemical vapor deposition (CVD), atomic layer deposition (ALD), and solution-phase synthesis are being refined for scalability and reproducibility. For instance, Oxford Instruments continues to advance ALD and CVD systems, enabling the controlled growth of 2D materials and complex nanostructures for electronics and energy applications.
Simultaneously, the industry is responding to environmental and regulatory pressures by integrating green chemistry principles into nanomaterials synthesis. This includes the use of benign solvents, renewable feedstocks, and energy-efficient processes. Companies like MilliporeSigma (the U.S. and Canada life science business of Merck KGaA, Darmstadt, Germany) are expanding their portfolios of eco-friendly reagents and offering protocols for solvent-free or aqueous-phase nanomaterial synthesis, reducing hazardous waste and improving safety profiles.
A notable trend in 2025 is the adoption of bio-inspired and biogenic synthesis routes. These methods leverage biological systems—such as plant extracts, bacteria, or enzymes—to mediate the formation of nanoparticles under mild conditions. Nanophase Technologies Corporation, a key supplier of engineered nanomaterials, is exploring such approaches to produce metal oxide nanoparticles with reduced environmental impact, targeting applications in personal care and advanced coatings.
Automation and digitalization are also transforming synthesis engineering. Modular, automated reactors equipped with real-time analytics are being deployed to optimize reaction conditions and scale up production efficiently. The Chemours Company, known for its titanium dioxide and advanced materials, is investing in process intensification and digital process control to enhance product consistency and resource efficiency.
Looking ahead, the next few years are expected to see further integration of machine learning and artificial intelligence in synthesis process design, enabling predictive control over nanomaterial properties and accelerating the discovery of novel materials. The convergence of bottom-up precision, green chemistry, and digital innovation is poised to redefine nanomaterials manufacturing, with industry leaders and emerging players alike focusing on scalable, sustainable, and high-performance solutions.
Key Applications: Electronics, Energy, Healthcare, and Beyond
Nanomaterials synthesis engineering is rapidly advancing, with 2025 marking a pivotal year for the translation of laboratory-scale innovations into industrial-scale applications. The precision control over nanomaterial properties—such as size, morphology, and surface chemistry—has enabled breakthroughs across electronics, energy, healthcare, and other sectors.
In electronics, the demand for smaller, faster, and more energy-efficient devices is driving the adoption of engineered nanomaterials. Companies like Samsung Electronics and Intel Corporation are actively integrating nanostructured materials into next-generation transistors, memory devices, and sensors. For instance, the use of carbon nanotubes and 2D materials such as graphene and transition metal dichalcogenides is enabling the development of sub-3nm node transistors, which are expected to enter commercial production in the next few years. These materials offer superior electron mobility and thermal conductivity, addressing the scaling limitations of traditional silicon-based devices.
In the energy sector, nanomaterials synthesis is central to the advancement of high-performance batteries, supercapacitors, and solar cells. Tesla, Inc. and LG Energy Solution are investing in nanostructured electrode materials to enhance lithium-ion battery capacity, charging speed, and cycle life. Nanostructured silicon and graphene composites are being scaled up for commercial battery anodes, with pilot production lines operational in 2025. Meanwhile, companies like First Solar are leveraging engineered quantum dots and perovskite nanomaterials to boost photovoltaic efficiency and stability, aiming for large-scale deployment in the coming years.
Healthcare applications are also witnessing significant progress. Engineered nanoparticles are being developed for targeted drug delivery, diagnostics, and imaging. Thermo Fisher Scientific and F. Hoffmann-La Roche AG are among the leaders in commercializing nanoparticle-based assays and contrast agents. In 2025, clinical trials are underway for nanomaterial-enabled cancer therapies and mRNA delivery systems, with regulatory approvals anticipated in the near term. The scalability and reproducibility of nanomaterials synthesis remain key challenges, but advances in automated and continuous-flow synthesis are improving quality control and throughput.
Beyond these sectors, nanomaterials are being engineered for use in water purification, advanced coatings, and smart textiles. Companies such as DuPont are scaling up nanostructured membranes for industrial water treatment, while Toray Industries, Inc. is developing nanofiber-based filtration and functional fabrics. As synthesis engineering matures, the next few years are expected to see broader commercialization, with sustainability and cost-effectiveness as guiding priorities.
Leading Players and Strategic Initiatives (e.g., nano.gov, basf.com, dupont.com)
The landscape of nanomaterials synthesis engineering in 2025 is shaped by a combination of established chemical giants, innovative startups, and government-backed initiatives, all driving advancements in scalable, sustainable, and application-specific nanomaterial production. Key players are leveraging their R&D capabilities, global manufacturing networks, and strategic partnerships to address the growing demand for nanomaterials in sectors such as electronics, energy storage, healthcare, and advanced coatings.
Among the most influential organizations is the National Nanotechnology Initiative (NNI), a U.S. government program that continues to coordinate federal investments and foster collaboration across academia, industry, and government agencies. In 2025, NNI’s focus includes supporting the development of standardized synthesis protocols, promoting responsible manufacturing practices, and facilitating technology transfer to accelerate commercialization.
On the industrial front, BASF remains a global leader in nanomaterials synthesis, with ongoing investments in process intensification and green chemistry approaches. BASF’s recent initiatives include scaling up the production of functionalized nanoparticles for battery electrodes and catalysis, as well as developing safer, more energy-efficient synthesis routes for nanostructured coatings and additives. The company’s global R&D centers are increasingly collaborating with academic institutions to fast-track the translation of lab-scale discoveries into industrial-scale processes.
DuPont is another major player, focusing on engineered nanomaterials for advanced electronics, flexible displays, and high-performance membranes. In 2025, DuPont is expanding its portfolio of nanostructured materials through both in-house innovation and strategic acquisitions, aiming to meet the stringent purity and performance requirements of next-generation semiconductor and filtration applications.
Other significant contributors include Evonik Industries, which is advancing the synthesis of silica and metal oxide nanoparticles for use in pharmaceuticals, 3D printing, and lightweight composites. Evonik’s emphasis on continuous flow synthesis and digital process optimization is expected to enhance both scalability and reproducibility in nanomaterial manufacturing.
Looking ahead, the sector is witnessing increased collaboration between industry and government, with initiatives such as the European Union’s Horizon Europe program and the U.S. Department of Energy’s nanomaterials consortia supporting pilot-scale demonstrations and the development of robust supply chains. As regulatory frameworks evolve and demand for sustainable solutions intensifies, leading players are expected to prioritize eco-friendly synthesis methods, lifecycle analysis, and transparent supply chain management, setting new benchmarks for the nanomaterials industry in the coming years.
Supply Chain Innovations and Raw Material Sourcing
The nanomaterials synthesis engineering sector is experiencing significant transformation in its supply chain and raw material sourcing strategies as of 2025. This evolution is driven by the need for scalability, sustainability, and resilience in response to both market demand and regulatory pressures. Key players are increasingly focusing on vertical integration, localizing supply chains, and adopting green chemistry principles to ensure a stable and ethical supply of raw materials.
A notable trend is the strategic investment in upstream raw material sources. For example, BASF, a global leader in chemical manufacturing, has expanded its partnerships with mining and mineral processing companies to secure a reliable supply of high-purity precursors essential for nanomaterial synthesis, such as titanium dioxide and silicon nanoparticles. This approach not only mitigates supply disruptions but also allows for greater control over material quality and traceability.
Sustainability is another major driver. Companies like DuPont are pioneering the use of recycled and bio-based feedstocks in nanomaterial production, reducing reliance on virgin raw materials and lowering the environmental footprint of their supply chains. These initiatives are supported by the adoption of closed-loop manufacturing systems, where waste streams are minimized and byproducts are repurposed, aligning with circular economy principles.
In 2025, digitalization and advanced analytics are being leveraged to enhance supply chain transparency and efficiency. Dow has implemented blockchain-based tracking systems to monitor the provenance and movement of raw materials used in nanomaterial synthesis. This technology enables real-time verification of material origin, compliance with regulatory standards, and rapid response to potential disruptions.
Geopolitical factors and the push for regional self-sufficiency are also shaping sourcing strategies. The European Union’s focus on critical raw materials has prompted companies like Evonik Industries to diversify their supplier base and invest in local extraction and processing facilities for key inputs such as rare earth elements and specialty metals. This reduces exposure to global supply shocks and aligns with regional industrial policies.
Looking ahead, the nanomaterials synthesis engineering sector is expected to further integrate sustainable sourcing, digital supply chain management, and regionalization. These innovations will be crucial for meeting the growing demand for advanced nanomaterials in electronics, energy, and healthcare, while ensuring ethical and resilient supply chains in the years beyond 2025.
Regulatory Landscape and Industry Standards (e.g., iso.org, ieee.org)
The regulatory landscape and industry standards for nanomaterials synthesis engineering are evolving rapidly as the sector matures and applications proliferate across electronics, energy, healthcare, and advanced manufacturing. In 2025, regulatory bodies and standards organizations are intensifying efforts to address the unique challenges posed by nanomaterials, particularly regarding safety, environmental impact, and quality assurance.
The International Organization for Standardization (ISO) remains at the forefront, with its Technical Committee ISO/TC 229 dedicated to nanotechnologies. This committee has developed and continues to update a suite of standards covering terminology, measurement, characterization, and risk management for nanomaterials. Notably, ISO 9001:2015 for quality management and ISO/TS 80004 for vocabulary are widely referenced in the industry. In 2025, new work items are focusing on harmonizing protocols for the synthesis and scale-up of engineered nanomaterials, reflecting the sector’s shift from laboratory to industrial production.
The Institute of Electrical and Electronics Engineers (IEEE) is also active, particularly in standardizing nanomaterial applications in electronics and photonics. The IEEE Nanotechnology Council is collaborating with industry to develop standards for the integration of nanomaterials in semiconductors, sensors, and flexible electronics, with several working groups targeting reliability and interoperability benchmarks for nanomaterial-enabled devices.
On the regulatory front, the European Union’s Registration, Evaluation, Authorisation and Restriction of Chemicals (REACH) framework continues to set stringent requirements for nanomaterial registration and safety data, influencing global practices. The European Chemicals Agency (ECHA) has updated guidance for nanomaterial dossiers, emphasizing detailed characterization and lifecycle analysis. In the United States, the U.S. Environmental Protection Agency (EPA) is expanding its oversight under the Toxic Substances Control Act (TSCA), requiring more comprehensive pre-manufacture notifications and risk assessments for new nanoscale materials.
Industry leaders such as BASF and DuPont are actively participating in standards development and regulatory consultations, leveraging their experience in large-scale nanomaterial synthesis. These companies are also implementing internal protocols that often exceed regulatory minimums, focusing on traceability, worker safety, and environmental stewardship.
Looking ahead, the next few years will likely see increased convergence between international standards and national regulations, driven by the need for global supply chain consistency and public trust. The ongoing collaboration between industry, regulators, and standards bodies is expected to yield more robust frameworks for nanomaterials synthesis, supporting both innovation and responsible commercialization.
Investment, Funding, and M&A Activity in Nanomaterials Engineering
The nanomaterials synthesis engineering sector is experiencing robust investment and M&A activity as global demand for advanced materials accelerates in 2025. This momentum is driven by the expanding applications of nanomaterials in electronics, energy storage, healthcare, and environmental solutions. Major industry players and emerging startups alike are attracting significant funding to scale up production, enhance synthesis technologies, and secure intellectual property.
In 2025, leading chemical and materials companies are intensifying their focus on nanomaterials. BASF, one of the world’s largest chemical producers, continues to invest in nanomaterials R&D, particularly in the development of advanced catalysts and battery materials. Dow is similarly expanding its nanomaterials portfolio, targeting high-performance polymers and coatings. Both companies have announced capital expenditures aimed at modernizing synthesis facilities and integrating automation and AI-driven process controls.
On the startup front, venture capital and corporate investors are backing companies with novel synthesis methods and scalable production platforms. For example, Nanoco Technologies (UK) has secured new funding rounds to expand its quantum dot manufacturing capacity, responding to increased demand from the display and medical imaging sectors. In the United States, Oxford Instruments is supporting early-stage ventures through partnerships and technology licensing, particularly in atomic layer deposition and nanoparticle synthesis.
Mergers and acquisitions are also shaping the competitive landscape. In late 2024 and early 2025, Evonik Industries completed the acquisition of a specialty nanomaterials firm to strengthen its position in high-purity silica and functionalized nanoparticles. This move aligns with Evonik’s strategy to expand its advanced materials segment and leverage synergies in process engineering. Meanwhile, SABIC has announced joint ventures with Asian partners to co-develop nanocomposites for automotive and packaging applications, reflecting the globalization of nanomaterials supply chains.
Looking ahead, the outlook for investment and M&A in nanomaterials synthesis engineering remains positive. The sector is expected to see continued inflows from both strategic and financial investors, with a focus on sustainable synthesis methods, green chemistry, and circular economy solutions. As regulatory frameworks evolve and end-user industries demand higher performance materials, companies with advanced synthesis capabilities and robust IP portfolios are likely to be prime targets for acquisition or partnership.
Challenges: Scalability, Safety, and Environmental Impact
The rapid advancement of nanomaterials synthesis engineering in 2025 is accompanied by significant challenges related to scalability, safety, and environmental impact. As the demand for nanomaterials in sectors such as electronics, energy storage, and healthcare continues to grow, the industry faces mounting pressure to transition from laboratory-scale synthesis to industrial-scale production while maintaining product consistency and minimizing risks.
Scalability remains a primary hurdle. Many nanomaterial synthesis methods, such as chemical vapor deposition (CVD) and sol-gel processes, are well-established at the laboratory level but present difficulties when scaled up. Issues include maintaining uniform particle size, purity, and morphology across large batches. Companies like Oxford Instruments and nanoComposix are actively developing scalable synthesis platforms, focusing on continuous flow reactors and automated process controls to address these challenges. However, the transition to mass production often requires significant capital investment and process optimization, which can slow commercialization timelines.
Safety is another critical concern, particularly regarding occupational exposure and the potential toxicity of nanomaterials. The unique properties that make nanomaterials valuable—such as high surface area and reactivity—can also pose health risks if inhaled or absorbed through the skin. Industry leaders like Evonik Industries and BASF have implemented rigorous safety protocols, including closed-system manufacturing and real-time monitoring of airborne nanoparticles, to protect workers and the environment. Regulatory bodies are also updating guidelines to reflect the latest scientific understanding of nanomaterial hazards, but harmonization across regions remains a work in progress.
Environmental impact is increasingly scrutinized as nanomaterial production scales up. Concerns include the release of nanoparticles into water and soil, energy-intensive synthesis processes, and the lifecycle impacts of nanomaterial-enabled products. Companies such as Arkema are investing in greener synthesis routes, including solvent-free processes and the use of renewable feedstocks, to reduce their environmental footprint. Additionally, industry consortia and organizations like National Nanotechnology Initiative are promoting best practices for waste management and environmental monitoring.
Looking ahead, the next few years will likely see increased collaboration between industry, academia, and regulatory agencies to develop standardized protocols for safe and sustainable nanomaterial synthesis. Advances in process automation, real-time monitoring, and green chemistry are expected to play pivotal roles in overcoming current challenges, enabling the broader adoption of nanomaterials across multiple industries while safeguarding human health and the environment.
Future Outlook: Disruptive Technologies and Market Opportunities Through 2029
The landscape of nanomaterials synthesis engineering is poised for significant transformation through 2029, driven by disruptive technologies and expanding market opportunities. As of 2025, the sector is witnessing rapid advancements in scalable, cost-effective, and environmentally sustainable synthesis methods. Key players are investing in automation, artificial intelligence (AI)-driven process optimization, and green chemistry approaches to meet the growing demand for high-performance nanomaterials across industries.
One of the most notable trends is the integration of AI and machine learning into nanomaterials synthesis. Companies such as BASF and Dow are leveraging data-driven platforms to accelerate the discovery and optimization of nanomaterial properties, reducing development cycles and enabling tailored solutions for applications in energy storage, electronics, and healthcare. These digital tools are expected to become standard in R&D pipelines, enhancing reproducibility and scalability.
Sustainability is another major driver shaping the future of nanomaterials synthesis. Leading manufacturers like Evonik Industries are prioritizing green synthesis routes, such as solvent-free processes and the use of renewable feedstocks, to minimize environmental impact and comply with tightening regulations. The adoption of continuous flow reactors and plasma-based synthesis is also gaining traction, offering improved control over particle size and morphology while reducing waste.
Market opportunities are expanding as nanomaterials find new applications in sectors such as batteries, semiconductors, and biomedicine. For instance, Samsung is actively developing nanomaterial-enabled components for next-generation electronics and energy storage devices, aiming to enhance performance and longevity. In the healthcare sector, companies like Thermo Fisher Scientific are advancing the synthesis of biocompatible nanoparticles for targeted drug delivery and diagnostics, with several products expected to reach commercialization by 2027.
Looking ahead, the convergence of advanced manufacturing, digitalization, and sustainability will likely define the competitive landscape. Strategic partnerships between material suppliers, technology developers, and end-users are expected to accelerate innovation and market adoption. As regulatory frameworks evolve, companies with robust, transparent, and eco-friendly synthesis processes will be best positioned to capture emerging opportunities. By 2029, nanomaterials synthesis engineering is anticipated to be a cornerstone of multiple high-growth industries, underpinned by continuous technological disruption and a strong emphasis on responsible manufacturing.
Sources & References
- BASF
- Evonik Industries
- Oxford Instruments
- Nanophase Technologies
- Arkema
- Cabot Corporation
- LG Energy Solution
- First Solar
- Thermo Fisher Scientific
- F. Hoffmann-La Roche AG
- DuPont
- National Nanotechnology Initiative (NNI)
- International Organization for Standardization (ISO)
- Institute of Electrical and Electronics Engineers (IEEE)
- Oxford Instruments
- National Nanotechnology Initiative