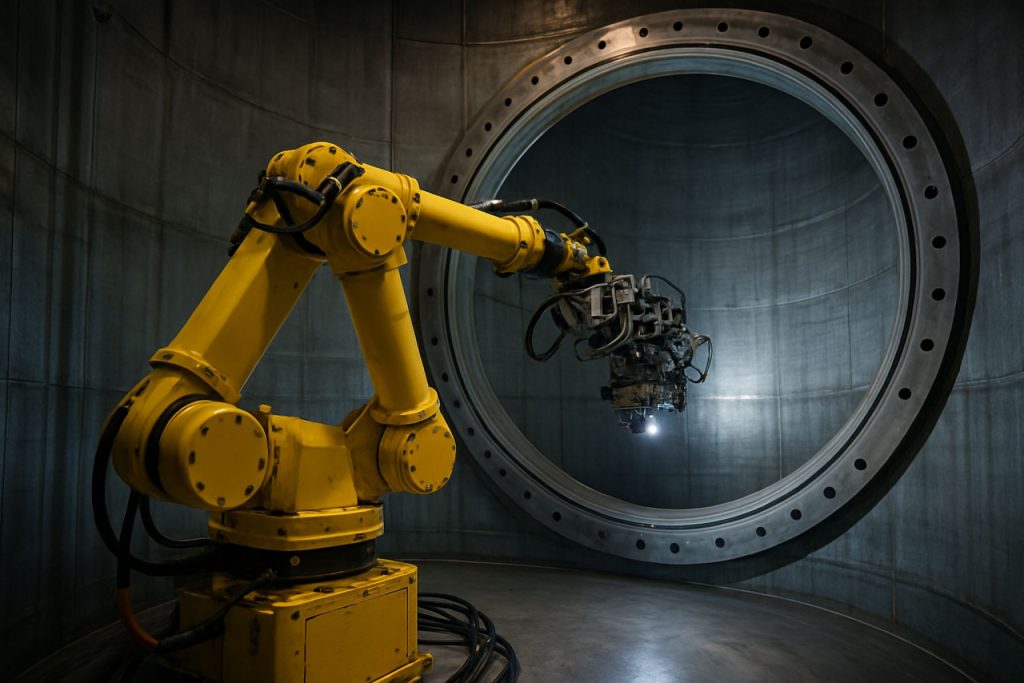
Table of Contents
- Executive Summary: The 2025 Landscape for Internal Liner Robotics in Nuclear Reactors
- Core Technology Overview: Robotics for Internal Liner Inspection and Maintenance
- Key Industry Players and Their Latest Solutions (e.g., framatome.com, westinghousenuclear.com)
- Market Size and Forecasts: Projections Through 2030
- Regulatory Landscape and Industry Standards (Referencing iaea.org, asme.org)
- Adoption Drivers: Safety, Efficiency, and Cost Reduction
- Challenges and Barriers: Technical, Regulatory, and Workforce Considerations
- Case Studies: Successful Deployments in Operational Reactors
- R&D Pipeline: Innovations on the Horizon (2025–2030)
- Future Outlook: Strategic Opportunities and Threats for Stakeholders
- Sources & References
Executive Summary: The 2025 Landscape for Internal Liner Robotics in Nuclear Reactors
The 2025 landscape for internal liner robotics in nuclear reactors is characterized by rapid technological adoption, increased safety demands, and evolving regulatory expectations. Internal liner robotics refer to advanced remotely operated or autonomous robotic systems designed to inspect, repair, and maintain the internal liners of nuclear reactor vessels and associated infrastructure. These liners are critical for preventing corrosion, maintaining structural integrity, and ensuring safe reactor operation. Traditionally, maintenance and inspection have required extensive human intervention, leading to high radiation exposure risks and substantial reactor downtime.
In 2025, the nuclear industry is witnessing a marked acceleration in the deployment of specialized robotics tailored for internal liner tasks. Companies such as Westinghouse Electric Company, Framatome, and Hitachi, Ltd. are at the forefront, offering advanced robotic platforms that leverage artificial intelligence, machine vision, and modular tool attachments. These systems are increasingly deployed during scheduled outages to conduct precise, high-resolution inspections and execute complex repairs—including weld overlays and liner replacements—without the need for direct human access.
The push toward greater automation is driven by several factors. First, regulatory bodies such as the International Atomic Energy Agency and national nuclear authorities are tightening inspection requirements and emphasizing preventive maintenance, making advanced robotics indispensable. Second, the aging global reactor fleet, particularly in North America, Europe, and parts of Asia, requires more frequent and sophisticated liner interventions to extend operational lifespans. For example, Westinghouse Electric Company reports growing demand for their remotely operated underwater vehicles (ROVs) and inspection crawlers, which can navigate complex geometries and provide real-time data for predictive maintenance.
The next few years are expected to see further integration of robotics with digital twin technologies and advanced analytics, enhancing predictive maintenance and minimizing unplanned outages. Investments in human-robot collaboration interfaces are rising, allowing remote operators to execute intricate tasks with improved safety and efficiency. Suppliers are also focusing on modularity and interoperability, ensuring that robotic platforms can adapt to different reactor designs and liner materials.
Looking forward, the outlook remains highly positive for internal liner robotics in nuclear reactors. As safety standards continue to evolve and reactor operators seek to maximize uptime and lifespan, the adoption of these advanced robotic solutions is set to become standard practice across the industry, with continuous innovation anticipated from leading suppliers and OEMs.
Core Technology Overview: Robotics for Internal Liner Inspection and Maintenance
Robotic systems for internal liner inspection and maintenance in nuclear reactors have become increasingly sophisticated, particularly as the global fleet of reactors ages and regulatory demands intensify. By 2025, these robotic solutions are recognized as vital for ensuring reactor integrity, enhancing safety, and reducing both human exposure and operational downtime. Internal liners—typically metallic cladding installed inside reactor containment structures—play a critical role in shielding, structural support, and containment of radiation and radioactive material. Over time, these liners are subject to degradation, including corrosion, mechanical wear, and stress-induced cracking, necessitating regular, precise inspection and timely maintenance.
Modern internal liner robotics leverage advanced mobility, imaging, and non-destructive evaluation (NDE) technologies to operate in the challenging, high-radiation, and confined environments of reactor containment. Leading suppliers, such as Westinghouse Electric Company and Framatome, have introduced robotic platforms capable of traversing vertical and horizontal liner surfaces, equipped with ultrasonic, eddy current, and visual inspection tools. These robots are designed for rapid deployment, often through small access ports, and can deliver real-time, high-resolution data to inform maintenance decisions.
For instance, Westinghouse Electric Company has developed robotic inspection crawlers with modular toolsets tailored for liner weld inspection and corrosion mapping in pressurized water reactors (PWRs) and boiling water reactors (BWRs). Similarly, Framatome offers remotely operated vehicles (ROVs) for containment liner inspection, integrating 3D mapping and automated defect recognition. These systems are routinely deployed in scheduled outages and have demonstrated significant reductions in inspection times compared to manual techniques, while also minimizing radiation exposure to personnel.
The outlook for 2025 and the next few years indicates accelerated adoption of AI-enabled analytics and autonomous navigation within these robotic platforms. Companies are investing in machine learning algorithms that enhance defect detection accuracy and automate reporting, further streamlining maintenance workflows. Additionally, there is a push towards multi-functional robotics capable of not only inspection but also in-situ repair, such as localized grinding, welding, or application of corrosion-resistant coatings. Industry bodies, such as the Nuclear Energy Institute and American Nuclear Society, are actively supporting the standardization and qualification of these robotic tools to ensure regulatory compliance and interoperability across reactor designs.
As nuclear operators face growing pressure to extend reactor lifespans and meet stringent safety standards, internal liner robotics are poised to become indispensable, with ongoing R&D targeting improved reliability, miniaturization, and integration of advanced sensing capabilities throughout the remainder of this decade.
Key Industry Players and Their Latest Solutions (e.g., framatome.com, westinghousenuclear.com)
The market for internal liner robotics in nuclear reactors is shaped by a select group of global industry leaders and innovative technology suppliers. As the industry emphasizes safety, efficiency, and regulatory compliance, robotic solutions have become essential for inspection, maintenance, and repair of reactor internal liners. Key players are advancing their offerings with increasingly autonomous, precise, and radiation-hardened systems.
Framatome is a central figure in nuclear reactor services, with specialized robotics for internal liner inspection and repair. The company’s robotic platforms are engineered to navigate confined and high-radiation environments, supporting ultrasonic testing, visual inspection, and remote welding. In 2023-2025, Framatome has focused on integrating advanced data analytics and AI-driven diagnostics into its robotics suite, aiming to reduce human intervention and reactor downtime. The company’s ongoing projects in Europe and North America illustrate the growing adoption of robotics for internal liner maintenance, especially in aging reactor fleets (Framatome).
Westinghouse Electric Company also remains at the forefront, providing a portfolio of field-proven robotic manipulators and inspection crawlers specifically designed for internal liner applications. Westinghouse’s latest generation of robots, developed as part of its ongoing modernization initiatives, feature modular architectures and enhanced remote control, enabling efficient deployment and retrieval even in complex reactor geometries. In recent years, Westinghouse has emphasized collaborative robotics—allowing human operators to safely guide or intervene in robotic operations when needed, while maintaining strict ALARA (As Low As Reasonably Achievable) radiation exposure standards (Westinghouse Electric Company).
Across Asia, Mitsubishi Heavy Industries has been a significant contributor, deploying robotics for both inspection and remediation of boiling water and pressurized water reactor liner systems. Their solutions feature radiation-tolerant cameras and sensor arrays, and are increasingly equipped with machine learning algorithms for defect recognition and real-time data processing. The company is expected to expand deployment throughout 2025 as Japan’s nuclear restarts accelerate (Mitsubishi Heavy Industries).
Looking ahead, leading players anticipate further automation and digitization of internal liner robotics. Integrating predictive maintenance tools, remote wireless communications, and cloud-based analytics are key trends projected to shape deployments in 2025 and beyond. Regulatory bodies and utilities are expected to continue investing in these technologies to ensure reactor longevity and safety, especially as many plants approach license renewal milestones.
Market Size and Forecasts: Projections Through 2030
The market for internal liner robotics in nuclear reactors is poised for significant growth through 2030, driven by the increasing need for enhanced safety, efficiency, and cost control in reactor maintenance and decommissioning. As of 2025, global investment in nuclear infrastructure is on an upward trajectory, with both operating reactors and new builds in Europe, Asia, and North America adopting advanced robotic technologies for internal liner inspection, cleaning, and repair.
Current estimates indicate that the global nuclear robotics market—including internal liner robotics—has already surpassed USD 500 million in annual spending, with internal liner inspection and maintenance representing a rapidly growing segment within this domain. This growth is fueled by the aging nuclear fleet in countries like the United States, France, and the United Kingdom, many of which require increasingly sophisticated solutions to meet regulatory and operational demands. For example, Holtec International and Framatome have both developed and deployed robotic systems targeting the inspection and maintenance of reactor vessel liners, with commercial contracts and pilot projects reported in several major markets.
Looking forward, the market is expected to expand at a compound annual growth rate (CAGR) of 8-10% through 2030, with projections suggesting the internal liner robotics segment could exceed USD 1 billion in annual spending by the decade’s end. Key drivers include stricter regulatory requirements for in-service inspection, the need to minimize human exposure to radiation, and the cost efficiencies offered by automated solutions. In particular, countries in East Asia—such as China, Japan, and South Korea—are anticipated to account for a considerable share of new deployments, reflecting their active nuclear construction programs and commitment to advanced maintenance technologies. Companies like Hitachi and Mitsubishi Electric are investing in R&D and commercialization of specialized robotic platforms for these markets.
- Utilities and operators are increasingly integrating robotics into planned outage schedules, expanding the addressable market for service providers and technology suppliers.
- The rise of digital twin technologies and artificial intelligence is further enhancing the capabilities and market appeal of internal liner robotics, as seen in pilot collaborations with leading utilities and OEMs.
- Decommissioning projects, particularly in Western Europe, are expected to be a major demand driver for internal liner robotic solutions over the next five years, as reflected in procurement and partnership announcements by EDF and Westinghouse Electric Company.
Overall, the outlook through 2030 indicates robust growth, with technological innovation and regulatory imperatives supporting sustained investment in internal liner robotics across the global nuclear sector.
Regulatory Landscape and Industry Standards (Referencing iaea.org, asme.org)
The regulatory landscape for internal liner robotics in nuclear reactors is evolving rapidly, reflecting both technological advancement and heightened safety imperatives. In 2025, industry standards and international guidelines form the backbone of regulatory compliance for robotic interventions within reactor internals, particularly for maintenance, inspection, and repair of reactor vessel liners and associated containment structures.
The International Atomic Energy Agency (IAEA) remains central to shaping global nuclear safety practices. Its safety standards, such as the IAEA Safety Standards Series, emphasize the necessity for reliable, remotely operated systems to minimize human exposure to radiation during inspection and repair tasks. Recent IAEA technical documents and collaborative research projects have highlighted the integration of robotics as a key enabler for both operational safety and lifecycle extension of reactor liners, especially as many power plants approach or exceed their originally licensed lifespans.
National regulatory bodies commonly adopt or adapt IAEA guidelines, but most also require compliance with technical codes developed by organizations such as the American Society of Mechanical Engineers (ASME). ASME’s Boiler and Pressure Vessel Code (BPVC), particularly Section XI for in-service inspection, stipulates stringent requirements for the qualification of non-destructive examination (NDE) technologies, including robotic systems. Updates anticipated in the 2025/2026 code cycles are expected to further clarify the certification processes for robotic platforms, sensor payloads, and data integrity protocols, in response to the increasing sophistication and deployment of such systems.
A trend in the next few years is the harmonization of standards for robotic inspection systems. The IAEA has initiated working groups focused on the interoperability, cybersecurity, and performance validation of robotics in nuclear applications. These efforts align with parallel initiatives by ASME to establish standard methods for the qualification and accreditation of remote-operated inspection devices. Leading reactor operators and robotics manufacturers are active participants in these standardization processes, aiming for globally recognized benchmarks that facilitate cross-border deployment and regulatory approval.
Looking forward, regulatory authorities are anticipated to place greater emphasis on robust lifecycle data management, traceability, and the integration of artificial intelligence in robotic platforms. This will likely result in new or revised guidelines, supporting the safe and effective adoption of internal liner robotics across diverse reactor types. The close collaboration between international bodies such as the IAEA and standards organizations like ASME ensures that the regulatory environment will remain responsive to technological innovation while upholding nuclear safety and environmental protection.
Adoption Drivers: Safety, Efficiency, and Cost Reduction
The adoption of internal liner robotics within nuclear reactors is increasingly driven by the industry’s prioritization of safety, operational efficiency, and cost reduction—imperatives that have gained renewed urgency as aging reactor fleets require extended operation and enhanced maintenance protocols. In 2025 and the coming years, several converging trends are accelerating the deployment of robotic solutions for tasks such as inspection, cleaning, and repair of reactor liners.
Safety remains the paramount driver. Manual inspection and maintenance of internal reactor liners expose personnel to significant radiation and hazardous environments, necessitating strict controls on exposure time and protective measures. Robotic systems, such as submersible crawlers and articulated manipulators, enable remote operation inside high-radiation zones, dramatically reducing occupational risks and improving compliance with international safety standards. Industry leaders like Westinghouse Electric Company and Framatome have developed robotic platforms that can conduct visual and non-destructive testing, leak detection, and surface cleaning with minimal human intervention. The use of such robotics supports regulatory requirements and public expectations for nuclear safety.
Efficiency gains are another major adoption driver. Traditional liner maintenance methods are time-consuming, often requiring lengthy reactor downtimes and complex scaffolding installations. Robotic solutions streamline these processes, offering precise, repeatable operations that reduce outage durations and improve plant availability. For example, robotic crawlers equipped with advanced sensors and imaging systems can rapidly map liner conditions and identify defects, allowing for targeted interventions. Companies like Hitachi and Mitsubishi Electric are actively integrating artificial intelligence and data analytics into their robotic systems, further boosting inspection speed and defect detection accuracy.
Cost reduction is a critical outcome of enhanced safety and efficiency. By minimizing human resource needs and shortening maintenance windows, internal liner robotics help lower direct labor costs and lost revenue from downtime. Moreover, early defect detection via robotics can prevent expensive unplanned outages and extend the service life of critical reactor components. As nuclear operators face mounting financial pressures in competitive energy markets, the return on investment for robotic solutions becomes increasingly compelling.
Looking forward, the next few years are expected to see broader adoption of internal liner robotics, particularly as digitalization initiatives accelerate and legacy reactors pursue life extension projects. Continued advancements in robotics design, autonomy, and data integration are poised to further strengthen the business case, positioning internal liner robotics as a standard feature of nuclear reactor maintenance worldwide.
Challenges and Barriers: Technical, Regulatory, and Workforce Considerations
The deployment of internal liner robotics in nuclear reactors faces a complex array of challenges and barriers as the industry advances in 2025. These hurdles span technical, regulatory, and workforce dimensions, each playing a crucial role in shaping the pace and success of adoption.
Technical challenges remain at the forefront. Reactor internals present highly constrained, radioactive, and often submerged environments, demanding exceptional miniaturization, radiation hardening, and reliability from robotic systems. The robots must navigate complex geometries and perform precision tasks such as inspection, cleaning, and repair of metallic liners, often under limited visibility and with strict contamination controls. For example, leading reactor robotics providers such as Westinghouse Electric Company and Framatome have developed advanced remotely operated vehicles (ROVs) and crawler robots, but these require continuous innovation to keep pace with evolving reactor designs and degradation phenomena. Battery life, tether management, and robust wireless communications inside containment structures are ongoing engineering concerns. Interoperability with existing plant instrumentation and data platforms also presents integration challenges.
Regulatory barriers are significant. Introducing robotics for internal liner work must align with stringent nuclear safety standards and licensing procedures. Regulators such as the U.S. Nuclear Regulatory Commission and international bodies demand comprehensive qualification, validation, and cybersecurity assessments for any robotic system used in safety-critical applications. The process for gaining approval of new robotic platforms can extend project timelines and necessitate exhaustive documentation and demonstration of fail-safe operation, as highlighted in the ongoing pilot deployments at utilities partnering with EDF and other major operators. Additionally, requirements for maintaining traceability of inspection data and secure handling of digital records add complexity to system implementation.
Workforce considerations are increasingly pertinent. The integration of robotics shifts skills requirements from manual liner work toward robotics operation, programming, and maintenance. Nuclear facilities must invest in workforce retraining, certification, and safety culture adaptation to empower operators and engineers to work alongside advanced robotic tools. With global shortages of skilled nuclear technicians and engineers, the transition may be slowed if workforce development does not keep pace with technological advancements. Partnerships between industrial suppliers such as Hitachi and utilities often include dedicated training programs and simulator-based curricula to address this gap.
Looking forward, overcoming these challenges will require sustained collaboration between technology vendors, reactor operators, regulators, and workforce development organizations. Progress in real-world deployments through 2025 and beyond will likely hinge on iterative field trials, adaptive regulatory frameworks, and comprehensive workforce engagement to ensure safe, effective, and efficient use of internal liner robotics in nuclear reactors.
Case Studies: Successful Deployments in Operational Reactors
In recent years, the deployment of internal liner robotics in nuclear reactors has transitioned from developmental trials to real-world applications, demonstrating notable successes in operational settings. As of 2025, several reactors globally have benefited from integrating advanced robotic systems for inspection, maintenance, and repair of internal liners, significantly enhancing both safety and efficiency.
A prominent example comes from France’s fleet of pressurized water reactors (PWRs), where robotic solutions have been deployed to inspect and repair stainless steel liners within containment structures. EDF, a leading operator, has collaborated with robotics specialists to introduce remotely operated vehicles (ROVs) equipped with high-definition cameras and ultrasonic sensors. These robots are capable of traversing challenging environments, identifying micro-cracks, and performing weld repairs without exposing personnel to radiation. In 2023–2024, such systems were credited with reducing outage durations by up to 15% during scheduled maintenance cycles.
In the United States, Westinghouse Electric Company has continued to refine and deploy its AVATAR and Laser Peening robotic platforms for liner inspections and remedial work. These robots have been utilized in boiling water reactors (BWRs) and PWRs to inspect liner welds and apply advanced surface treatments, extending the lifespan of critical reactor components. According to recent operational data, Westinghouse’s robotic interventions in 2023–2025 have contributed to early detection of liner degradation, reducing unplanned outages and associated costs.
Further, in Japan, Hitachi has reported successful robotic deployments within boiling water reactors for internal liner inspection and decontamination tasks. Hitachi’s robots are designed to navigate narrow passages and perform detailed visual and radiometric inspections, ensuring compliance with updated regulatory standards. These deployments, initiated in late 2023, have set new benchmarks for minimizing human entry into high-radiation zones while improving data collection accuracy.
Looking ahead, the adoption of internal liner robotics is expected to accelerate through 2026 and beyond as operators seek continual improvements in reactor safety, regulatory compliance, and cost efficiency. As robotic technology advances—incorporating AI-powered diagnostics and autonomous navigation—future deployments are projected to further reduce maintenance times and enhance the overall reliability of nuclear infrastructure.
R&D Pipeline: Innovations on the Horizon (2025–2030)
The period from 2025 through the end of the decade is set to witness significant R&D advancements in internal liner robotics designed for nuclear reactor applications. These autonomous and semi-autonomous systems, tasked with inspecting, repairing, and maintaining reactor liner surfaces, are becoming increasingly critical as the global fleet of nuclear power plants ages and regulatory scrutiny on safety intensifies.
A major driver for innovation is the need to safely extend the operational lives of reactors beyond their original design limits. Internal liner degradation, including corrosion, cracking, and coating failures, poses both safety and economic risks. Robotics equipped with advanced sensors and manipulator arms are being refined to detect, characterize, and even remediate these issues with minimal human intervention. Over the next five years, several nuclear technology leaders are expected to deploy new generations of robots capable of higher-resolution imaging, precise non-destructive evaluation (NDE) techniques, and automated weld or coating repairs in high-radiation environments.
For example, Westinghouse Electric Company is known for developing remotely operated inspection vehicles for reactor vessel internals and liners, and they are expected to continue expanding the capabilities of their robotic platforms. Similarly, Framatome has ongoing R&D focused on robotic manipulation and inspection tools for both boiling water and pressurized water reactors, aiming to reduce outage times and increase repair accuracy. There is also growing collaboration between utilities, original equipment manufacturers, and research institutes to accelerate development cycles and field validation of these systems.
A notable trend is the integration of AI and machine learning into robotic platforms, enabling real-time data analysis and adaptive inspection strategies. Companies such as Holtec International are exploring the use of predictive analytics in conjunction with robotic inspections to anticipate liner degradation and optimize maintenance schedules. Furthermore, modular robotics—allowing for rapid configuration changes and deployment in reactors of varying designs—are on the horizon, with several prototypes undergoing testing in simulated reactor environments.
Looking toward 2030, the outlook is for increased automation, higher sensor fidelity, and more robust radiation-hardened electronics, all contributing to safer, faster, and more cost-effective maintenance of nuclear reactor liners. These innovations are expected to play a vital role in supporting both life extension for existing plants and the safe introduction of advanced reactor designs that require novel liner materials and geometries.
Future Outlook: Strategic Opportunities and Threats for Stakeholders
The future of internal liner robotics for nuclear reactors is shaped by the increasing demand for plant safety, cost efficiency, and regulatory compliance. As of 2025, key stakeholders—including nuclear plant operators, equipment manufacturers, technology developers, and regulatory bodies—face both strategic opportunities and emerging threats in deploying and advancing these technologies.
One major opportunity lies in the accelerating global push to extend the operational lifespans of existing nuclear reactors. Many reactors worldwide are approaching or surpassing their original design lives, requiring comprehensive inspection, maintenance, and refurbishment. Robotic systems, capable of performing precision inspection, cleaning, and repair tasks inside reactor liners, are becoming essential. Companies such as Westinghouse Electric Company and Framatome are advancing remotely operated and autonomous robots tailored for these high-radiation, confined environments, enabling more frequent and thorough liner assessments while minimizing human exposure.
Rising regulatory scrutiny and evolving global safety standards also drive the adoption of advanced liner robotics. Regulatory bodies, including those in the U.S. and Europe, are increasingly mandating more rigorous, data-driven inspection regimes that are difficult to meet with manual approaches alone. Robotic technologies, equipped with high-resolution imaging and nondestructive testing sensors, offer the precision and repeatability required for compliance. This is prompting increased collaboration between technology developers and utilities, as seen in joint projects and pilot deployments aiming to standardize robotic inspection protocols.
For technology suppliers, the next few years present a growing market as utilities invest in digital transformation and predictive maintenance. Partnerships with established nuclear equipment manufacturers and utilities will be critical, as integration with existing plant systems and regulatory acceptance are significant adoption hurdles. Companies like Hitachi and GE are expanding their portfolios to include robotics and digital inspection solutions, strengthening their positions in this evolving landscape.
However, stakeholders must also anticipate key threats. The foremost challenge is technological: ensuring that robotic systems can withstand extreme radiation, high temperatures, and complex geometries inside reactor liners. Reliability and fail-safes must be proven through extensive testing and qualification, which can slow commercialization. Cybersecurity risks are another concern, as increasing connectivity and data acquisition expose new potential vulnerabilities.
Overall, the outlook for internal liner robotics in nuclear reactors is robust, with significant opportunities for innovation and market expansion balanced against technical, regulatory, and operational risks. Stakeholders that proactively invest in R&D, strategic partnerships, and compliance readiness are best positioned to capture value as the industry transitions toward greater automation and digitalization.