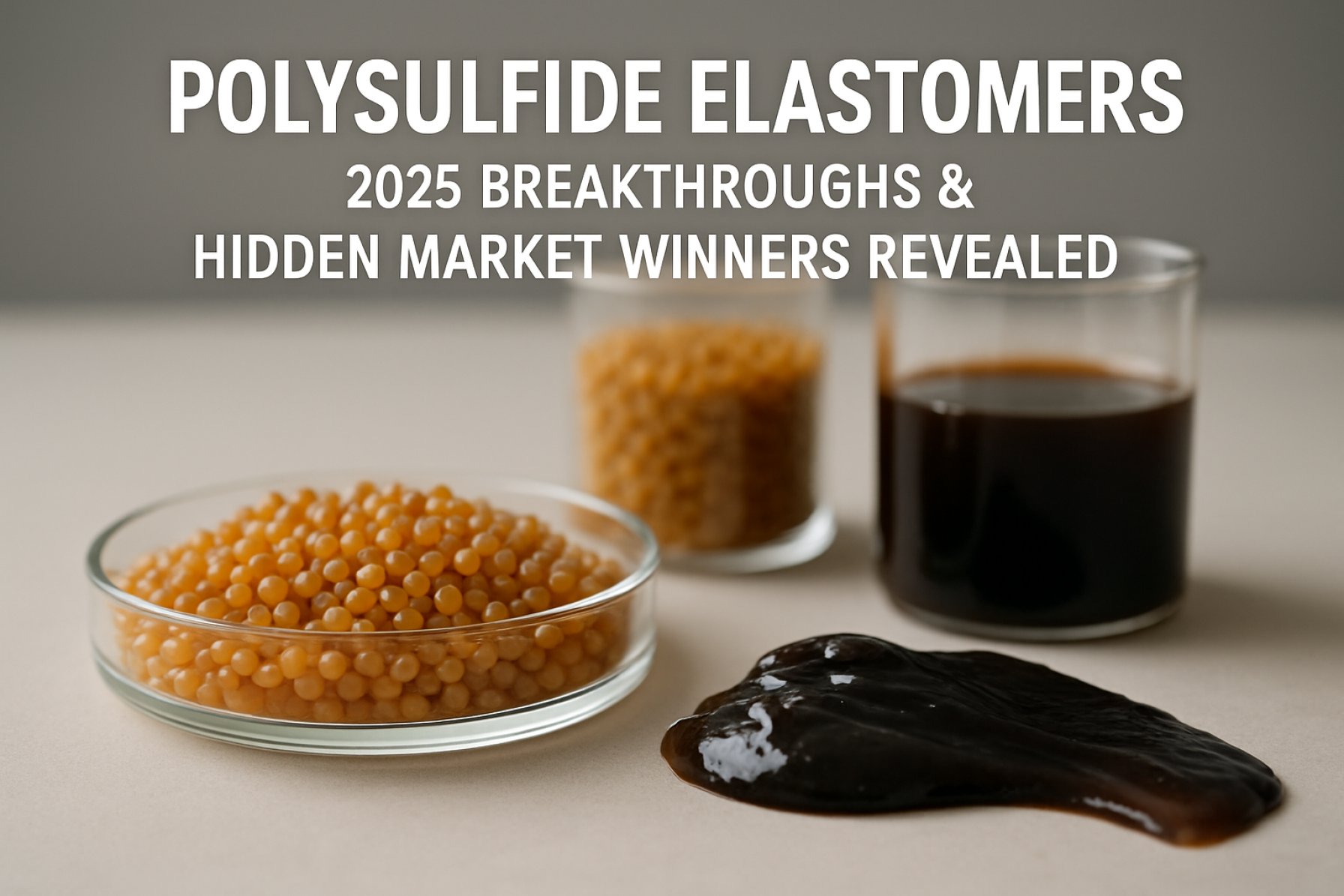
Table of Contents
- Executive Summary: Key Insights for 2025–2030
- Market Size & Growth Forecasts Through 2030
- Emerging Applications and End-Use Trends
- Technological Advances in Polysulfide Formulation
- Competitive Landscape: Leading Manufacturers and Innovators
- Regulatory Environment and Industry Standards
- Supply Chain Dynamics and Raw Material Sourcing
- Sustainability Initiatives and Green Chemistry Solutions
- Regional Opportunities: Hotspots for Expansion
- Future Outlook: Disruptive Innovations and Strategic Roadmaps
- Sources & References
Executive Summary: Key Insights for 2025–2030
Polysulfide elastomers, known for their exceptional chemical resistance, flexibility, and impermeability, are poised to maintain a critical role in specialized industrial applications from 2025 to 2030. Recent trends indicate a strong focus on enhancing formulation efficiency, environmental compliance, and performance customization to meet evolving regulatory and end-user requirements in sectors such as aerospace, construction, and automotive.
Leading manufacturers are investing in research to further optimize the balance between mechanical properties and processability. For example, Momentive Performance Materials continues to refine their two-part polysulfide sealants, emphasizing longer service life and improved adhesion under extreme conditions. Similarly, Henkel AG & Co. KGaA has expanded its portfolio with formulations designed for both manual and automated application processes, responding to the growing demand for efficiency in large-scale manufacturing environments.
Environmental regulations are shaping polysulfide elastomer formulations, particularly regarding VOC content and the use of hazardous curing agents. In line with REACH and other international standards, companies such as AkzoNobel are developing low-emission, phthalate-free alternatives, a trend expected to accelerate through the forecast period. Industry bodies, including the SAE International, are also updating standards to reflect these environmental and safety considerations, directly influencing formulation strategies.
Market outlook for 2025–2030 suggests steady demand growth, particularly in applications requiring long-term chemical and fuel resistance, such as aircraft fuel tank sealants and structural joints in infrastructure projects. The ongoing shift towards sustainable construction and the modernization of transportation fleets in North America, Europe, and Asia-Pacific is anticipated to drive further innovation in polysulfide elastomer technology, emphasizing recyclability and life-cycle performance.
In summary, polysulfide elastomer formulation is entering a dynamic period marked by regulatory adaptation, technological advancement, and broader industrial adoption. The next five years will likely see increased collaboration between manufacturers, raw material suppliers, and regulatory bodies as the sector aligns with both performance and sustainability imperatives.
Market Size & Growth Forecasts Through 2030
The global market for polysulfide elastomer formulation is poised for steady growth through 2030, driven by expanding applications in aerospace, construction, automotive, and electronics sectors. As of 2025, industry data indicates a robust demand for high-performance sealants and adhesives, particularly those offering superior chemical and weather resistance, which are hallmark characteristics of polysulfide-based systems.
Key manufacturers such as H.B. Fuller and Momentive continue to expand their polysulfide elastomer portfolios, investing in formulation innovation to meet evolving industry standards and sustainability benchmarks. Notably, the aerospace industry is projected to remain a primary driver of demand, as polysulfide sealants are critical for fuel tank sealing and environmental barrier applications due to their resistance to aviation fuels and flexibility across temperature extremes. PPG Industries and Royal Adhesives & Sealants (now a part of H.B. Fuller) are among the suppliers ramping up production to accommodate new aircraft builds and fleet maintenance programs worldwide.
In the construction sector, infrastructure investment and regulatory pushes for more durable, weatherproof building materials are fueling a gradual uptick in polysulfide elastomer use, particularly in structural glazing and façade sealing. Companies like Sika AG report ongoing development of advanced polysulfide-based sealant formulations tailored to both traditional and emerging markets in Asia and the Middle East, anticipating heightened demand through 2030.
Looking ahead, the market outlook remains positive. Industry stakeholders forecast a compound annual growth rate in the mid-single digits, with Asia-Pacific expected to outpace North American and European growth due to rapid industrialization and infrastructure expansion. Additionally, sustainability pressures are prompting R&D into lower-VOC, more environmentally friendly polysulfide formulations, a trend echoed by technology updates from manufacturers such as Evonik Industries. Given their established performance advantages and continued innovation, polysulfide elastomer formulations are well-positioned to maintain and expand their market share in high-value, performance-critical applications through the end of the decade.
Emerging Applications and End-Use Trends
In 2025, polysulfide elastomer formulations are witnessing renewed interest and innovation, particularly as industries seek advanced materials with enhanced chemical resistance, flexibility, and durability. These elastomers, characterized by their sulfur-sulfur backbone, are being increasingly utilized in diverse applications driven by evolving regulatory, sustainability, and performance demands.
A core area of growth is in the aerospace and defense sectors, where polysulfide-based sealants and adhesives are critical for fuel tank sealing, fuselage assembly, and window installations due to their exceptional resistance to fuels, solvents, and wide temperature ranges. PPG Industries and Henkel AG & Co. KGaA continue to invest in next-generation formulations, focusing on improved cure profiles and lower volatile organic compound (VOC) content to address both environmental and operational requirements.
In civil engineering, polysulfide elastomers serve as joint sealants for highways, bridges, and structural glazing, favored for their long-term elasticity and weathering resistance. Innovations are being driven by stricter infrastructure standards and the need for longer maintenance intervals. For example, Sika AG reports development of hybrid sealant products that blend traditional polysulfide chemistry with silane-terminated polymers, aiming to combine the best features of both chemistries for construction applications.
The oil and gas industry remains a significant end-user, employing polysulfide elastomeric formulations in downhole seals, gaskets, and chemical containment systems. Here, the push is toward formulations that withstand aggressive hydrocarbons and sour gas environments, extending operational lifespans and reducing the risk of environmental incidents. Momentive Performance Materials and Huntsman Corporation are actively exploring novel curing agents and reinforcement additives to enhance mechanical and barrier properties.
Another emerging application is in electric vehicle (EV) battery manufacturing, where polysulfide elastomers are being evaluated for cell-to-pack sealing and potting, leveraging their chemical inertness and ability to dampen vibrations. Automotive suppliers such as Dow are collaborating with battery OEMs to tailor formulations for high-voltage insulation and electrolyte compatibility.
Looking ahead, the outlook for polysulfide elastomer formulations is robust, supported by the increasing complexity of end-use requirements and a clear shift toward sustainability. Manufacturers are expected to prioritize bio-based plasticizers, recyclable packaging, and reduced emission chemistries, aligning with global sustainability targets and customer expectations across sectors.
Technological Advances in Polysulfide Formulation
Polysulfide elastomer formulation is undergoing a period of notable technological advancement in 2025, driven by evolving industry requirements for high-performance sealants and coatings in aerospace, construction, and energy applications. Central to these advances is the continual refinement of base polymer chemistry, with manufacturers optimizing molecular weight distribution and crosslinking density to achieve desired flexibility, adhesion, and chemical resistance.
Recent developments include the introduction of novel curing agents and accelerators, designed to lower cure times and allow for ambient temperature application. For example, Henkel has launched new polysulfide sealant formulations that offer rapid curing while maintaining the elastomer’s hallmark resistance to fuels and hydraulic fluids—a critical feature for aerospace and automotive sectors. Their latest systems also demonstrate improved sag resistance, enabling application on vertical and overhead surfaces without slumping.
Sustainability and environmental considerations are prompting significant innovation. Many suppliers are working to reduce volatile organic compound (VOC) content, responding to regulatory pressures and customer expectations. PCC Group is among those offering low-VOC polysulfide polymers, developed through advances in purification and polymerization techniques. These improvements enable manufacturers to meet stringent emission standards without sacrificing material performance.
Another trend shaping the formulation landscape is the integration of nanoscale fillers and functional additives. By incorporating nanoclays or modified silicas, formulators can enhance mechanical robustness, elongation, and barrier properties of the elastomers. Everkem reports that their latest polysulfide sealants exhibit increased resistance to UV degradation and weathering, extending service life in demanding outdoor environments.
Automation and process control are also being leveraged to ensure batch-to-batch consistency and scalability. Companies such as Evonik are investing in advanced mixing and metering equipment, enabling precise dosing of reactive components and additives, which is especially important for two-part systems used in critical infrastructure and transport applications.
Looking ahead, the next few years are expected to see further digitalization of formulation workflows, with predictive modeling and AI-assisted design increasingly employed to accelerate development cycles and optimize performance attributes. As sustainability imperatives intensify and end-use demands become more exacting, polysulfide elastomer formulation is poised for continued innovation, balancing regulatory compliance, durability, and application efficiency.
Competitive Landscape: Leading Manufacturers and Innovators
As the demand for robust sealants and chemically resistant materials continues to rise across aerospace, construction, and automotive sectors, the competitive landscape for polysulfide elastomer formulation is witnessing significant activity in 2025. Key players are intensifying their focus on innovation, sustainable chemistry, and strategic expansion to capture evolving market needs.
Established Leaders: H.B. Fuller Company and Henkel AG & Co. KGaA remain dominant forces in the development and supply of polysulfide-based sealants and adhesives. H.B. Fuller, for instance, continues to expand its PPG-branded aircraft sealant portfolio, leveraging polysulfide technology for fuel tank and fuselage sealing applications. Similarly, Henkel’s LOCTITE portfolio includes advanced polysulfide sealants designed for demanding industrial and transportation environments. Both companies are investing in enhanced curing technologies and more environmentally friendly formulations, responding to regulatory trends and end-user sustainability requirements.
Specialized Innovators: Companies such as Akzo Nobel N.V. and Masco Corporation (through its subsidiary Tremco) are advancing formulation science, with Akzo Nobel focusing on aerospace sealants featuring improved chemical resistance and reduced volatile organic compound (VOC) emissions. Tremco, meanwhile, has expanded its product lines with new polysulfide-based sealants for infrastructure projects, emphasizing long service life and flexibility under harsh conditions.
Regional and Niche Players: In Asia and the Middle East, companies like ChemLink and Sika AG are strengthening their regional footprints by tailoring polysulfide elastomer formulations for local construction and industrial needs. Sika’s 2025 strategy includes the launch of new, high-performance polysulfide joint sealants engineered for use in transportation infrastructure, reflecting the region’s rapid urbanization and investment in megaprojects.
Innovation Outlook: Looking ahead, the competitive focus is shifting toward hybrid formulations that blend polysulfide with other elastomer chemistries to enhance performance and reduce environmental impact. Leading manufacturers are also exploring bio-based feedstocks and circular economy approaches in polysulfide production. As end-users prioritize lifecycle cost and regulatory compliance, the next few years will likely see further consolidation, joint ventures, and investment in R&D, especially targeting aerospace and civil engineering applications.
Regulatory Environment and Industry Standards
The regulatory environment and industry standards for polysulfide elastomer formulation are rapidly evolving as global priorities shift toward sustainability, product safety, and performance in critical applications. As of 2025, manufacturers of polysulfide elastomers—widely used as sealants in aerospace, construction, and automotive sectors—are adapting their product development strategies to comply with increasingly stringent chemical regulations and updated industry standards.
In the United States, polysulfide elastomer formulations are subject to the Toxic Substances Control Act (TSCA) and oversight by the U.S. Environmental Protection Agency, particularly regarding permissible levels of hazardous substances such as lead, mercury, and certain phthalates. The Federal Aviation Administration continues to specify performance requirements for sealants used in aircraft fuel tanks and fuselage applications, which often directly reference industry standard specifications such as AMS-S-8802 (for fuel tank sealants) and MIL-PRF-81733 (for sealing compounds).
In Europe, the Registration, Evaluation, Authorisation and Restriction of Chemicals (REACH) regulations administered by the European Chemicals Agency are influential in shaping formulation decisions. These regulations require manufacturers and importers to register chemicals used in elastomer production and demonstrate compliance with safety and environmental standards. Notably, recent updates to the REACH candidate list and restriction lists are prompting formulators to move away from legacy plasticizers and certain curing agents in favor of alternatives with a lower environmental footprint.
Industry bodies such as the SAE International and ASTM International are actively updating test methods and performance standards for polysulfide elastomers to reflect advancements in material science and evolving end-use requirements. ASTM C920 and SAE AMS-S-8802 remain central references for sealant performance, but ongoing revisions through 2025 are expected to address issues such as volatile organic compound (VOC) emissions and long-term durability under extreme conditions.
Major manufacturers including Henkel and Momentive Performance Materials are investing in R&D to develop formulations that not only comply with current regulatory mandates but also anticipate stricter environmental and performance standards likely to emerge in the next few years. The outlook for 2025 and beyond suggests a continued tightening of regulatory requirements, especially concerning environmental impact, workplace safety, and product lifecycle management. Companies that proactively align formulations with evolving standards are expected to retain a competitive edge in global markets.
Supply Chain Dynamics and Raw Material Sourcing
The supply chain landscape for polysulfide elastomer formulation in 2025 is shaped by a confluence of factors, including the availability and sourcing of key raw materials such as dihalides (primarily dichloroalkanes), sodium polysulfide, plasticizers, and fillers. As demand rises across aerospace, construction, and automotive sectors, manufacturers are increasingly focused on securing sustainable and robust raw material streams to ensure production continuity and meet evolving regulatory requirements.
Key polysulfide precursors—such as sodium polysulfide and organic dihalides—are primarily sourced from established chemical producers with vertically integrated supply chains. Leading global suppliers, such as Momentive and Henkel, have reinforced their procurement strategies by increasing reliance on long-term contracts and dual sourcing from multiple geographies, thus reducing vulnerability to single-point disruptions. This trend is expected to continue through 2025 and beyond, as geopolitical tensions and logistics bottlenecks in key production regions persist.
In 2025, raw material pricing volatility—particularly for sulfur derivatives and specialty plasticizers—remains a challenge. Fluctuations are driven by energy market dynamics, regulatory interventions on chemical production, and the ongoing shift toward greener chemistries. Notably, polysulfide sealant manufacturers are exploring bio-based and low-VOC plasticizer alternatives to align with tightening emission standards in North America and Europe. Companies like 3M are piloting formulations that incorporate sustainable additives while maintaining critical performance metrics for applications such as fuel tank sealing and insulating glass.
The outlook for polysulfide elastomer supply chains over the next few years involves increased digitalization and traceability. Major producers are investing in digital supply chain platforms to monitor inventory, forecast demand, and manage supplier relationships in real time. For example, Momentive has announced initiatives aimed at enhancing transparency and agility in its global operations, which is expected to help mitigate future disruptions and respond more flexibly to market shifts.
Overall, the polysulfide elastomer industry is likely to see continued emphasis on supply chain resilience, sustainable sourcing, and regulatory compliance, with innovation in raw material selection and digital infrastructure playing pivotal roles in shaping the sector’s trajectory in 2025 and the years to come.
Sustainability Initiatives and Green Chemistry Solutions
In 2025, sustainability in polysulfide elastomer formulation is gaining prominence, driven by regulatory pressures, customer demand, and the global transition towards lower environmental impact materials. Major manufacturers of polysulfide elastomers are focusing on reducing the carbon footprint of their products, improving recyclability, and integrating green chemistry approaches throughout production cycles.
One of the central developments is the shift toward bio-based plasticizers and renewable feedstocks. Companies such as Momentive Performance Materials are actively exploring the use of bio-derived plasticizers to replace traditional phthalate-based options in their polysulfide sealant formulations. This move is aligned with both regulatory trends in Europe and North America restricting hazardous substances and with corporate sustainability goals.
Energy efficiency in manufacturing processes is another focal point. Henkel AG & Co. KGaA has reported investments in process optimization to reduce energy consumption and waste during the compounding of their polysulfide-based sealants, particularly those used in the aerospace and construction sectors. These process improvements include closed-loop systems for solvent recovery and increased use of renewable electricity in their production facilities.
Waste reduction and recycling are also being addressed. Several industry leaders, including PCC SE, are developing take-back schemes and initiatives for the collection and recycling of end-of-life elastomeric products. These programs aim to recover valuable materials and minimize landfill disposal, which is particularly challenging with crosslinked elastomers like polysulfides.
On the formulation front, research continues into reducing or eliminating the use of heavy metals such as lead and cadmium, which have traditionally been used as curing agents or stabilizers. Manufacturers are increasingly incorporating alternative curing systems based on less toxic metal oxides or organic catalysts, in line with initiatives from regulatory bodies such as the European Chemicals Agency (ECHA).
Looking ahead, the next few years are expected to see further collaboration between chemical producers, end-users, and sustainability-focused organizations to accelerate the adoption of green chemistry principles in polysulfide elastomer formulation. The industry outlook points to increased transparency in supply chains, wider use of life cycle assessments, and the continued rollout of environmentally improved polysulfide products, ensuring that the sector aligns with global sustainability targets while maintaining the critical performance characteristics of these materials.
Regional Opportunities: Hotspots for Expansion
The global landscape for polysulfide elastomer formulation is evolving, with several regions emerging as hotspots for expansion in 2025 and the coming years. Driven by robust demand in construction, aerospace, automotive, and electronics, opportunities are particularly notable in Asia-Pacific, North America, and parts of Europe.
Asia-Pacific remains the fastest-growing region for polysulfide elastomer applications. China and India continue to invest heavily in infrastructure, transportation, and industrial development, fueling demand for durable sealants and adhesives. For example, Sika AG has expanded its manufacturing footprint in China, targeting local requirements for high-performance polysulfide-based construction materials. Additionally, H.B. Fuller operates a dedicated innovation center in India, focusing on the customization of elastomeric formulations for regional market needs, including weatherproofing and chemical resistance.
In North America, polysulfide elastomers are witnessing renewed attention due to infrastructure revitalization programs and the growth of the aerospace sector. The United States, in particular, is seeing increased investment in transportation and aviation, where polysulfide sealants are valued for their fuel and weather resistance. Henkel AG & Co. KGaA has ramped up its production of aerospace-grade polysulfide sealants in its North American facilities to meet the demand from both commercial and defense aerospace manufacturers.
Europe demonstrates steady growth, with Germany, France, and the U.K. leveraging polysulfide elastomers for both renovation and new building projects, particularly in waterproofing and insulating applications. Momentive Performance Materials supports the region with advanced polysulfide formulations tailored for stringent EU environmental and safety regulations.
Looking ahead, regional opportunities are likely to be influenced by sustainability trends and regulatory shifts. Manufacturers are investing in greener chemistries and lower-VOC formulations to comply with tightening standards, especially in the EU and North America. Furthermore, the Middle East is emerging as a promising market, where large-scale infrastructure and energy projects require high-performance elastomeric materials, creating openings for global and regional suppliers to establish local partnerships and manufacturing bases.
Overall, the outlook for polysulfide elastomer formulation in 2025 and beyond is marked by geographic diversification, with tailored solutions and local partnerships playing a key role in capturing regional opportunities and responding to evolving market requirements.
Future Outlook: Disruptive Innovations and Strategic Roadmaps
The future of polysulfide elastomer formulation is poised for transformative change as the industry integrates advanced chemistries and sustainable practices to meet evolving market demands. In 2025 and the years ahead, disruptive innovations are centered around enhancing performance attributes—such as chemical resistance, flexibility, and longevity—while addressing regulatory and environmental imperatives.
A primary area of innovation is the development of low-volatile organic compound (VOC) and isocyanate-free polysulfide systems. Leading manufacturers are investing in greener formulation chemistries to meet tightening global emissions standards and the growing demand for sustainable construction and aerospace sealants. For example, Henkel is pioneering polysulfide-based sealants with improved environmental profiles, focusing on lowering hazardous air pollutant content without sacrificing performance.
Digitalization and process automation are also reshaping production approaches. Companies such as Evonik Industries are leveraging advanced analytics and process control to optimize molecular weight distribution and crosslinking density, leading to more consistent product quality and tailored elastomer properties for specialized applications like insulating glass and marine sealants.
Material hybridization represents another strategic avenue. Collaborations between polysulfide suppliers and end-users are fostering the integration of polysulfide elastomers with complementary polymers—such as epoxy and polyurethane—to create hybrid systems. These innovations, as seen in the product portfolio of H.B. Fuller, deliver synergistic benefits, including improved adhesion, UV resistance, and accelerated curing times.
In terms of strategic roadmaps, industry leaders are prioritizing circularity and lifecycle management. Efforts are underway to develop recycling-ready formulations and end-of-life strategies for polysulfide-containing products, reflecting broader commitments to sustainable manufacturing by organizations like Sika AG. The aim is to minimize environmental impact while maintaining the high-performance standards required in critical sectors such as civil engineering and aerospace.
Looking forward, the competitive landscape will be shaped by continuous R&D investments, regulatory compliance, and collaborative innovation. As end-user industries—particularly construction, automotive, and aerospace—demand higher durability and sustainability, polysulfide elastomer formulation will remain at the forefront of advanced materials development, with disruptive technologies and strategic partnerships driving market evolution through 2025 and beyond.