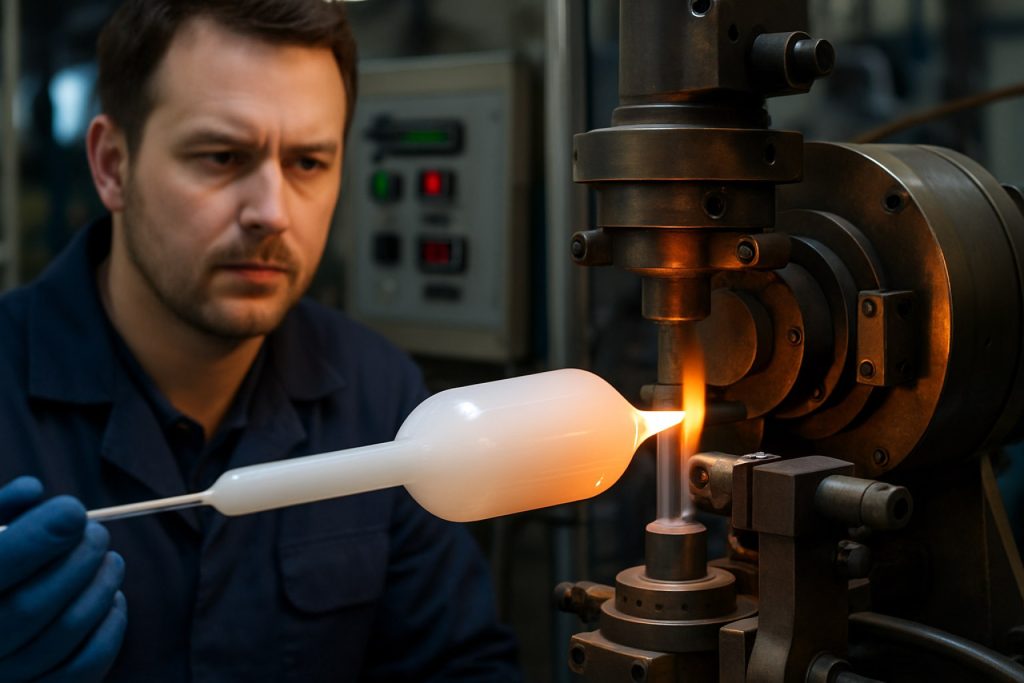
Preform-Based Optical Fiber Manufacturing in 2025: Unleashing High-Speed Connectivity and Next-Gen Innovations. Explore Market Growth, Disruptive Technologies, and Strategic Shifts Shaping the Industry’s Future.
- Executive Summary: 2025 Market Outlook and Key Drivers
- Global Market Size, Growth Rate, and Forecasts to 2030
- Technological Advances in Preform Fabrication and Fiber Drawing
- Major Players and Competitive Landscape (e.g., corning.com, fujikura.co.jp, prysmiangroup.com)
- Raw Materials, Supply Chain Dynamics, and Sustainability Initiatives
- Emerging Applications: 5G, Data Centers, and Quantum Communications
- Regional Analysis: Asia-Pacific, North America, Europe, and Rest of World
- Investment Trends, M&A Activity, and Strategic Partnerships
- Challenges: Cost Pressures, Quality Control, and Environmental Regulations
- Future Outlook: Disruptive Innovations and Market Opportunities Through 2030
- Sources & References
Executive Summary: 2025 Market Outlook and Key Drivers
The preform-based optical fiber manufacturing sector is poised for continued growth in 2025, driven by surging global demand for high-speed data transmission, the expansion of 5G networks, and the ongoing digital transformation across industries. Preforms—high-purity glass rods from which optical fibers are drawn—remain the foundation of the industry, with technological advancements and capacity expansions shaping the competitive landscape.
Leading manufacturers such as Corning Incorporated, Fujikura Ltd., Sumitomo Electric Industries, Ltd., and Yokogawa Electric Corporation continue to invest in preform production technologies. These companies are focusing on improving process efficiency, reducing contamination, and enabling the production of specialty fibers for emerging applications such as quantum communications and advanced sensing.
In 2025, the market is expected to see robust activity in both mature and emerging regions. Asia-Pacific, led by China and India, remains the largest and fastest-growing market for optical fiber preforms, fueled by government-backed broadband initiatives and rapid urbanization. Major Chinese producers, including Yangtze Optical Fibre and Cable Joint Stock Limited Company (YOFC) and Hengtong Group, are expanding their preform manufacturing capacities to meet domestic and international demand. These expansions are supported by investments in automation and green manufacturing processes to address both cost and sustainability pressures.
Technological innovation is a key market driver. The adoption of advanced vapor deposition methods—such as Modified Chemical Vapor Deposition (MCVD), Outside Vapor Deposition (OVD), and Vapor Axial Deposition (VAD)—is enabling higher yields and improved fiber performance. Companies are also developing new preform compositions to support ultra-low-loss fibers and multi-core designs, which are critical for next-generation data centers and submarine cable systems.
Supply chain resilience remains a strategic focus in 2025, as manufacturers seek to mitigate risks from raw material shortages and geopolitical uncertainties. Vertical integration, long-term supplier partnerships, and regional diversification of production sites are being prioritized by industry leaders.
Looking ahead, the preform-based optical fiber manufacturing market is expected to maintain a positive trajectory over the next few years. The convergence of digital infrastructure investments, technological advancements, and sustainability initiatives will continue to shape the sector, with established players and new entrants alike vying for market share in a dynamic global environment.
Global Market Size, Growth Rate, and Forecasts to 2030
The global market for preform-based optical fiber manufacturing is poised for robust growth through 2030, driven by surging demand for high-speed internet, 5G network rollouts, and expanding data center infrastructure. As of 2025, the market is characterized by significant investments in capacity expansion and technological innovation, particularly in Asia-Pacific, which remains the dominant production hub.
Key industry leaders such as Corning Incorporated, Fujikura Ltd., Sumitomo Electric Industries, Ltd., Prysmian Group, and Yangtze Optical Fibre and Cable Joint Stock Limited Company (YOFC) are actively expanding their preform and fiber production capacities to meet global demand. For example, Corning Incorporated has announced ongoing investments in new and existing facilities to support the growing needs of the telecommunications and data center sectors. Similarly, YOFC continues to lead in China, the world’s largest optical fiber market, with new preform production lines and R&D initiatives.
In 2025, the global preform-based optical fiber manufacturing market is estimated to be valued in the tens of billions of US dollars, with annual growth rates projected in the high single digits to low double digits through 2030. This growth is underpinned by the rapid deployment of fiber-to-the-home (FTTH) networks, 5G backhaul, and the proliferation of cloud computing. The Asia-Pacific region, led by China, India, and Japan, is expected to maintain its leadership, accounting for the majority of new capacity additions and technological advancements.
Looking ahead, the market outlook remains positive, with several trends shaping the industry. These include the adoption of advanced vapor deposition techniques for preform manufacturing, increased automation, and a focus on sustainability and energy efficiency in production processes. Major players such as Fujikura Ltd. and Sumitomo Electric Industries, Ltd. are investing in next-generation preform technologies to enhance fiber quality and reduce costs.
By 2030, the global preform-based optical fiber manufacturing sector is expected to see continued consolidation among leading manufacturers, with strategic partnerships and joint ventures further strengthening supply chains and innovation pipelines. The industry’s trajectory will be closely tied to the pace of digital infrastructure development worldwide, ensuring sustained demand for high-performance optical fiber.
Technological Advances in Preform Fabrication and Fiber Drawing
Preform-based optical fiber manufacturing remains the cornerstone of global fiber optic production, with ongoing technological advances in both preform fabrication and fiber drawing processes. As of 2025, the industry is witnessing significant innovation aimed at increasing throughput, reducing costs, and enabling new fiber types for advanced applications.
Preform fabrication, the initial stage in fiber manufacturing, has traditionally relied on methods such as Modified Chemical Vapor Deposition (MCVD), Outside Vapor Deposition (OVD), and Vapor Axial Deposition (VAD). Leading manufacturers, including Corning Incorporated, Fujikura Ltd., and Sumitomo Electric Industries, Ltd., continue to refine these processes. For example, Corning Incorporated has invested in automation and process control to improve preform uniformity and reduce contamination, which is critical for high-performance fibers used in data centers and 5G networks.
Recent years have seen the adoption of advanced plasma and laser-based deposition techniques, which offer greater control over dopant profiles and enable the fabrication of specialty fibers, such as those with ultra-low loss or novel refractive index profiles. Fujikura Ltd. and Sumitomo Electric Industries, Ltd. are actively developing preforms for multicore and hollow-core fibers, targeting next-generation communications and sensing applications.
In fiber drawing, the focus has shifted toward higher-speed, precision-controlled furnaces and real-time monitoring systems. Corning Incorporated and Prysmian Group have implemented advanced draw towers equipped with AI-driven feedback loops, which optimize fiber geometry and minimize defects. These improvements are essential for meeting the growing demand for high-bandwidth, low-latency optical networks.
Sustainability is also a growing concern. Companies such as Furukawa Electric Co., Ltd. are exploring energy-efficient furnace designs and recycling of process gases to reduce the environmental footprint of preform and fiber production.
Looking ahead, the next few years are expected to bring further integration of digital manufacturing technologies, such as machine learning for process optimization and digital twins for predictive maintenance. The continued evolution of preform-based manufacturing will be crucial for supporting the expansion of global fiber networks, the rollout of 5G and beyond, and the emergence of quantum and specialty fiber applications.
Major Players and Competitive Landscape (e.g., corning.com, fujikura.co.jp, prysmiangroup.com)
The preform-based optical fiber manufacturing sector in 2025 is characterized by a concentrated group of global leaders, each leveraging advanced technologies and extensive production capacities to meet the surging demand for high-performance optical fibers. The competitive landscape is shaped by innovation in preform fabrication methods, vertical integration, and strategic investments in capacity expansion to address the needs of telecommunications, data centers, and emerging applications such as 5G and fiber-to-the-home (FTTH).
- Corning Incorporated remains a dominant force in the industry, with a legacy of pioneering the vapor deposition process for preform manufacturing. The company continues to invest in research and development, focusing on ultra-low-loss fibers and specialty products for next-generation networks. Corning’s global manufacturing footprint and supply chain resilience have enabled it to maintain a leading market share, particularly in North America and Asia. The company’s commitment to sustainability and innovation is evident in its ongoing expansion of preform and fiber production facilities (Corning Incorporated).
- Prysmian Group, headquartered in Italy, is another major player with a comprehensive portfolio spanning optical fiber, cables, and connectivity solutions. Prysmian’s vertical integration—from preform production to finished cable—ensures quality control and cost efficiency. The company has recently announced investments in expanding its preform manufacturing capacity in Europe and North America, aiming to support the rapid deployment of broadband infrastructure and 5G networks. Prysmian’s focus on innovation includes the development of bend-insensitive and high-capacity fibers (Prysmian Group).
- Fujikura Ltd. of Japan is recognized for its advanced preform fabrication technologies, including outside vapor deposition (OVD) and vapor-phase axial deposition (VAD). Fujikura’s global reach is supported by manufacturing sites in Asia, Europe, and the Americas, enabling it to serve diverse markets efficiently. The company is actively investing in automation and digitalization of its preform and fiber production lines to enhance productivity and product consistency (Fujikura Ltd.).
- Sumitomo Electric Industries, Ltd. is another key Japanese manufacturer, known for its expertise in both preform and fiber production. Sumitomo Electric’s innovations in low-loss and specialty fibers have positioned it as a preferred supplier for high-speed and long-haul network projects. The company is expanding its global manufacturing network and increasing R&D spending to address the evolving requirements of the optical communications market (Sumitomo Electric Industries, Ltd.).
Looking ahead, the competitive landscape is expected to remain robust, with these major players driving technological advancements and capacity expansions. The focus will be on meeting the growing demand for high-quality preforms, supporting the global rollout of high-speed broadband, and enabling new applications in data-intensive sectors. Strategic partnerships, sustainability initiatives, and continued investment in automation are likely to shape the industry’s trajectory through the next several years.
Raw Materials, Supply Chain Dynamics, and Sustainability Initiatives
Preform-based optical fiber manufacturing remains the dominant method for producing high-quality optical fibers, with the process relying heavily on the availability and purity of raw materials such as silica (SiO2), germanium, and various dopants. In 2025, the global supply chain for these materials is characterized by both consolidation and strategic expansion, as leading manufacturers seek to secure reliable sources and mitigate risks associated with geopolitical tensions and logistical disruptions.
The primary raw material, high-purity silica, is sourced from a limited number of specialized suppliers capable of meeting the stringent requirements for optical fiber preforms. Companies such as Corning Incorporated, Fujikura Ltd., and Sumitomo Electric Industries, Ltd. maintain vertically integrated operations, controlling significant portions of their raw material supply chains. This integration allows for greater quality control and supply stability, particularly important as demand for optical fiber continues to rise with the expansion of 5G, data centers, and broadband infrastructure.
Supply chain dynamics in 2025 are shaped by ongoing efforts to localize production and reduce dependency on single-source suppliers. For example, Prysmian Group and OFS Fitel, LLC have invested in regional preform manufacturing facilities to serve North American and European markets, aiming to buffer against international shipping delays and trade uncertainties. Additionally, manufacturers are increasingly entering into long-term contracts with chemical suppliers to ensure a steady flow of high-purity precursors such as silicon tetrachloride and germanium tetrachloride.
Sustainability initiatives are gaining momentum across the sector. Major players are implementing closed-loop recycling systems for silica and dopant chemicals, reducing waste and minimizing environmental impact. Corning Incorporated has publicly committed to reducing greenhouse gas emissions and water usage in its manufacturing processes, while Fujikura Ltd. and Sumitomo Electric Industries, Ltd. are investing in energy-efficient furnace technologies and renewable energy sourcing for their preform plants. These efforts are not only driven by regulatory requirements but also by increasing customer demand for sustainable fiber solutions.
Looking ahead, the outlook for preform-based optical fiber manufacturing in the next few years is shaped by continued investment in supply chain resilience, raw material innovation, and sustainability. As digital infrastructure projects accelerate worldwide, the industry is expected to prioritize both capacity expansion and environmental stewardship, ensuring a stable and responsible supply of optical fiber to meet global connectivity needs.
Emerging Applications: 5G, Data Centers, and Quantum Communications
Preform-based optical fiber manufacturing remains the backbone of the global fiber optic industry, and its relevance is intensifying as emerging applications such as 5G, hyperscale data centers, and quantum communications drive demand for higher performance and specialized fiber types. In 2025 and the coming years, the sector is witnessing significant investments and technological advancements to meet the stringent requirements of these next-generation applications.
The rollout of 5G networks worldwide is accelerating the need for low-loss, high-bandwidth optical fibers capable of supporting massive data throughput and ultra-low latency. Leading manufacturers such as Corning Incorporated, Furukawa Electric Co., Ltd., and Prysmian Group are expanding their preform production capacities and introducing new fiber designs tailored for dense urban deployments and fronthaul/backhaul connections. For instance, Corning Incorporated has announced ongoing investments in its optical fiber and cable manufacturing facilities to address the surging demand from 5G and broadband infrastructure projects.
Hyperscale data centers, which form the backbone of cloud computing and AI-driven services, are also fueling innovation in preform-based fiber manufacturing. The need for ultra-low attenuation, bend-insensitive, and multi-core fibers is prompting companies like Fujikura Ltd. and Sumitomo Electric Industries, Ltd. to develop advanced preform fabrication techniques, including vapor-phase axial deposition (VAD) and outside vapor deposition (OVD), to produce fibers with precise geometries and minimal signal loss. These innovations are critical for supporting the high-density, high-speed interconnects required in modern data centers.
Quantum communications represent a frontier application with unique demands for ultra-pure, low-defect optical fibers to enable secure quantum key distribution (QKD) and entanglement transmission over long distances. Companies such as NKT Photonics and OFS Fitel, LLC are actively engaged in research and pilot production of specialty fibers, including hollow-core and polarization-maintaining fibers, using advanced preform engineering. These efforts are supported by collaborations with academic and government research institutions to accelerate the commercialization of quantum-ready fiber networks.
Looking ahead, the preform-based optical fiber manufacturing sector is expected to see continued growth and diversification, with a focus on automation, sustainability, and the development of fibers tailored for specific emerging applications. Strategic investments by industry leaders and the integration of new materials and process controls will be pivotal in meeting the evolving needs of 5G, data centers, and quantum communications through 2025 and beyond.
Regional Analysis: Asia-Pacific, North America, Europe, and Rest of World
The global landscape for preform-based optical fiber manufacturing in 2025 is characterized by dynamic regional developments, with Asia-Pacific, North America, Europe, and the Rest of World each playing distinct roles in the industry’s evolution.
- Asia-Pacific: This region continues to dominate preform-based optical fiber manufacturing, driven by robust demand for high-speed internet, 5G deployment, and expanding data center infrastructure. China remains the world’s largest producer and consumer of optical fiber preforms, with major players such as Yangtze Optical Fibre and Cable Joint Stock Limited Company (YOFC) and Hengtong Group leading large-scale production and technological innovation. Japan and South Korea also maintain significant capacities, with companies like Fujikura Ltd. and Samsung (through its materials division) investing in advanced preform technologies. India is rapidly scaling up its domestic manufacturing, supported by government initiatives to boost local production and reduce import dependence.
- North America: The region is marked by a focus on high-performance specialty fibers and R&D-driven advancements. Corning Incorporated, headquartered in the United States, remains a global leader in preform and optical fiber innovation, with ongoing investments in expanding manufacturing capacity and developing next-generation fiber types. The U.S. government’s broadband infrastructure initiatives are expected to further stimulate domestic demand and production through 2025 and beyond.
- Europe: European manufacturers emphasize quality, sustainability, and specialty applications. Prysmian Group (Italy) and Nexans (France) are prominent in both preform production and integrated fiber solutions, serving telecom, energy, and industrial markets. The region’s focus on digital transformation and green infrastructure is driving investments in new preform facilities and process optimization, with a growing emphasis on reducing the carbon footprint of fiber manufacturing.
- Rest of World: Other regions, including the Middle East, Africa, and Latin America, are witnessing gradual growth in preform-based optical fiber manufacturing, primarily through joint ventures and technology transfers with established Asian and European firms. Local production remains limited but is expected to increase as digital infrastructure projects accelerate and governments seek to localize supply chains.
Looking ahead, the Asia-Pacific region is expected to maintain its leadership in both volume and innovation, while North America and Europe will continue to drive advancements in specialty fibers and sustainable manufacturing. The global market is likely to see further capacity expansions, technology upgrades, and regional diversification as digital connectivity becomes ever more critical.
Investment Trends, M&A Activity, and Strategic Partnerships
The preform-based optical fiber manufacturing sector is experiencing dynamic investment trends, strategic partnerships, and notable M&A activity as global demand for high-capacity fiber networks accelerates into 2025. The industry is characterized by a small number of dominant players, significant capital requirements, and a focus on technological innovation to meet the needs of 5G, FTTx, and data center expansion.
Leading manufacturers such as Corning Incorporated, Furukawa Electric Co., Ltd., Prysmian Group, Sumitomo Electric Industries, Ltd., and Yokogawa Electric Corporation continue to invest heavily in expanding preform and fiber production capacity. For example, Corning Incorporated has announced multi-year capital expenditure plans to increase preform output at its U.S. and international facilities, responding to surging demand from telecom and hyperscale data center customers. Similarly, Furukawa Electric Co., Ltd. and Sumitomo Electric Industries, Ltd. are scaling up their manufacturing footprints in Asia and North America, with a focus on advanced preform technologies such as ultra-low loss and bend-insensitive fibers.
M&A activity in the sector remains robust, with strategic acquisitions aimed at vertical integration and geographic expansion. In recent years, Prysmian Group has completed several acquisitions to strengthen its position in the optical fiber value chain, including investments in preform manufacturing capabilities. The trend is expected to continue into 2025, as companies seek to secure supply chains and access new markets. Additionally, joint ventures and technology partnerships are increasingly common, particularly between established manufacturers and regional telecom operators or infrastructure investors. These collaborations often focus on co-developing next-generation preform and fiber solutions tailored to local network requirements.
Strategic partnerships are also emerging around sustainability and supply chain resilience. For instance, major players are entering agreements with specialty chemical suppliers and equipment manufacturers to ensure a stable supply of high-purity raw materials and to develop more energy-efficient preform fabrication processes. Yokogawa Electric Corporation, known for its process automation solutions, is collaborating with fiber manufacturers to optimize production lines and reduce operational costs.
Looking ahead, the outlook for investment and partnership activity in preform-based optical fiber manufacturing remains strong. The sector is expected to see continued consolidation, with leading firms leveraging M&A and alliances to maintain technological leadership and meet the evolving needs of global connectivity infrastructure.
Challenges: Cost Pressures, Quality Control, and Environmental Regulations
Preform-based optical fiber manufacturing remains the dominant method for producing high-quality optical fibers, but the sector faces mounting challenges in 2025 and the coming years. Chief among these are cost pressures, stringent quality control demands, and tightening environmental regulations.
Cost pressures are intensifying due to several factors. The prices of key raw materials—such as high-purity silica and specialty dopants—have shown volatility, influenced by global supply chain disruptions and energy costs. Major manufacturers like Corning Incorporated and Fujikura Ltd. have reported ongoing efforts to optimize their preform production processes, including investments in automation and digitalization to reduce labor and energy expenses. However, the capital-intensive nature of preform fabrication, especially for advanced fibers (e.g., bend-insensitive or multicore designs), continues to challenge smaller players and new entrants.
Quality control is another critical concern. As data rates and network reliability requirements rise, telecom operators and data center providers demand fibers with ever-tighter tolerances for attenuation, geometry, and mechanical strength. Leading producers such as OFS Fitel, LLC and Sumitomo Electric Industries, Ltd. have responded by deploying advanced in-line monitoring systems and real-time analytics during preform and fiber drawing stages. These systems help detect micro-defects and ensure consistency, but they also add to operational complexity and require ongoing investment in metrology and process control technologies.
Environmental regulations are becoming more stringent, particularly regarding emissions, waste management, and energy consumption. The preform manufacturing process, especially the Modified Chemical Vapor Deposition (MCVD) and Outside Vapor Deposition (OVD) methods, involves hazardous chemicals and generates byproducts that must be carefully managed. Companies such as Prysmian Group and FiberHome Telecommunication Technologies Co., Ltd. are increasingly investing in cleaner production technologies, recycling initiatives, and energy-efficient equipment to comply with evolving regulations in key markets like the European Union and China. These efforts, while necessary, can increase operational costs and require significant capital outlays.
Looking ahead, the industry is expected to see continued consolidation as larger players leverage economies of scale to manage costs and regulatory compliance. At the same time, ongoing R&D into greener chemistries, process automation, and digital quality control is likely to shape the competitive landscape, with sustainability and reliability emerging as key differentiators in the preform-based optical fiber sector.
Future Outlook: Disruptive Innovations and Market Opportunities Through 2030
The preform-based optical fiber manufacturing sector is poised for significant transformation through 2030, driven by both incremental process improvements and disruptive innovations. As global demand for high-capacity data transmission continues to surge—fueled by 5G, cloud computing, and the anticipated expansion of AI-driven applications—manufacturers are intensifying efforts to enhance preform quality, reduce costs, and increase production scalability.
Leading industry players such as Corning Incorporated, Fujikura Ltd., Sumitomo Electric Industries, Ltd., and OFS Fitel, LLC are investing heavily in next-generation preform fabrication technologies. These include advanced vapor deposition methods (MCVD, OVD, and VAD), automation, and real-time process monitoring to ensure higher purity and uniformity in preforms. For example, Corning Incorporated continues to refine its proprietary processes to support ultra-low-loss and bend-insensitive fibers, which are critical for dense urban deployments and data centers.
A notable trend is the push toward sustainability and resource efficiency. Companies are exploring closed-loop systems for chemical recycling and waste minimization during preform production. Fujikura Ltd. and Sumitomo Electric Industries, Ltd. have both announced initiatives to reduce the environmental footprint of their manufacturing operations, aligning with broader industry and regulatory pressures for greener supply chains.
On the innovation front, the development of specialty preforms for multi-core and hollow-core fibers is gaining momentum. These advanced designs promise to dramatically increase data throughput and reduce latency, opening new market opportunities in high-performance computing, quantum communications, and next-generation telecom networks. OFS Fitel, LLC and Corning Incorporated are actively engaged in R&D collaborations to commercialize these disruptive fiber types within the next few years.
Looking ahead to 2030, the preform-based optical fiber manufacturing market is expected to see robust growth, particularly in Asia-Pacific and North America, where infrastructure upgrades and digital transformation initiatives are accelerating. The sector’s outlook is further buoyed by ongoing investments in automation, digital twins, and AI-driven quality control, which are set to enhance yield and reduce time-to-market for new fiber products. As a result, companies that can rapidly scale innovative preform technologies while maintaining cost and sustainability advantages are likely to capture significant market share in the evolving global landscape.
Sources & References
- Sumitomo Electric Industries, Ltd.
- Yangtze Optical Fibre and Cable Joint Stock Limited Company (YOFC)
- Prysmian Group
- Prysmian Group
- Furukawa Electric Co., Ltd.
- Sumitomo Electric Industries, Ltd.
- OFS Fitel, LLC
- Furukawa Electric Co., Ltd.
- NKT Photonics
- Nexans