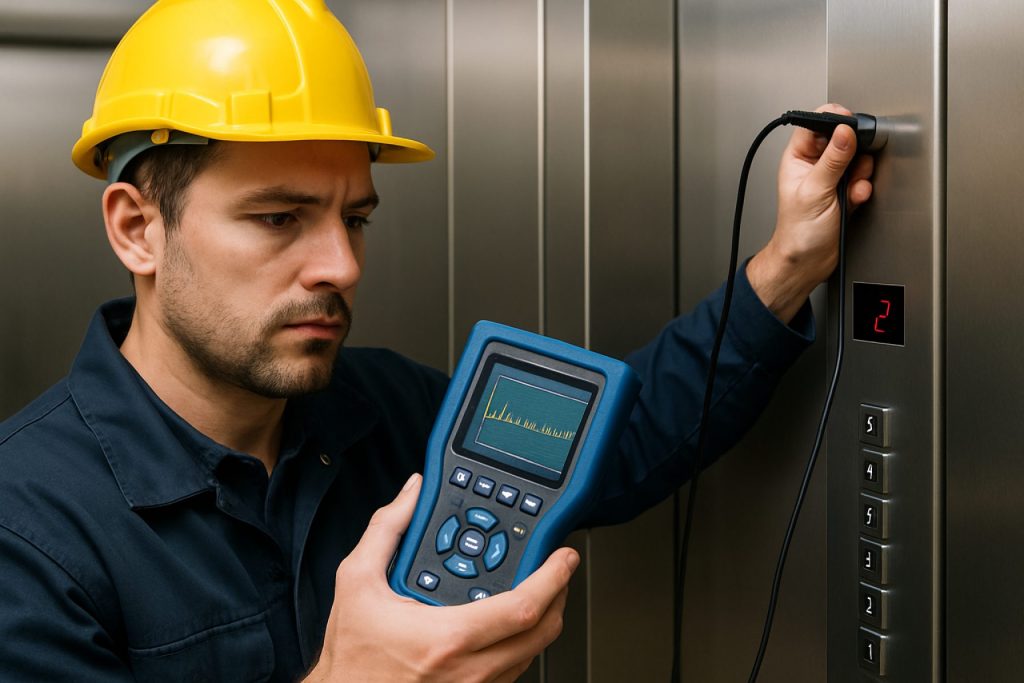
How Elevator Vibration Verification Systems Will Transform Safety and Efficiency in 2025—And What the Next 5 Years Hold for the Industry
- Executive Summary: 2025 at a Glance
- Global Market Size and Forecast (2025–2030)
- Key Drivers: Safety, Regulations, and Smart Building Integration
- Leading Innovators and Technology Providers
- Latest Advances in Vibration Sensing and Data Analytics
- Emerging Industry Standards and Compliance Trends
- Regional Analysis: North America, Europe, Asia-Pacific, and Beyond
- Challenges and Barriers to Widespread Adoption
- Case Studies: Real-World Applications and Impact
- Future Outlook: Next-Gen Verification Systems and Opportunities
- Sources & References
Executive Summary: 2025 at a Glance
The global market for elevator vibration verification systems is experiencing significant momentum in 2025, driven by heightened safety regulations, urbanization, and demand for predictive maintenance in vertical transportation. Vibration verification systems are now integral components in both new elevator installations and modernization projects, offering real-time monitoring and diagnostic capabilities to detect anomalies, reduce downtime, and extend equipment lifespan.
In 2025, regulatory bodies are intensifying focus on elevator safety, with vibration monitoring highlighted as a critical parameter for compliance and risk mitigation. Building codes and standards in regions such as Europe and East Asia increasingly reference vibration analysis as a benchmark for ride quality and mechanical integrity. This is accelerating adoption across commercial, residential, and public sector projects.
Key industry leaders, such as Otis Worldwide Corporation and KONE Corporation, are integrating advanced vibration monitoring solutions within their flagship elevator lines. These systems utilize accelerometers and IoT-enabled sensors to continuously track vibration patterns, automatically triggering alerts for deviations that may indicate wear, misalignment, or potential failures. Schindler Group and TK Elevator are similarly investing in proprietary monitoring platforms, often coupled with cloud-based analytics for fleet-wide oversight and predictive maintenance scheduling.
Supplier and component specialists like ifm electronic and SICK AG are expanding their offerings of industrial-grade vibration sensors tailored for vertical mobility applications, supporting both OEMs and retrofit markets. These collaborations are fostering greater interoperability and data sharing across building management systems and elevator control networks.
The technological outlook for 2025 and the near future points towards further integration of artificial intelligence and machine learning algorithms, enabling more precise fault detection and lifecycle optimization. Manufacturers are also exploring wireless sensor networks for simplified installation and enhanced scalability, especially in high-rise and complex building environments. The convergence of vibration verification with broader smart building initiatives positions this sector for continued growth and innovation through 2026 and beyond.
Global Market Size and Forecast (2025–2030)
The global market for elevator vibration verification systems is experiencing steady growth as the demand for safer, more efficient, and technologically advanced vertical transportation solutions increases worldwide. As of 2025, the sector is being shaped by a robust pipeline of infrastructure projects, urban verticalization, and modernization initiatives in both mature and emerging markets. According to industry sources, elevator vibration verification systems—which encompass hardware and software designed to detect, analyze, and mitigate vibration issues in elevator operations—are becoming a fundamental component in new installations and retrofits.
Market participants include leading elevator manufacturers and a growing number of specialized sensor and diagnostic technology providers. Major elevator OEMs such as Otis Worldwide Corporation, KONE Corporation, Schindler Group, and TK Elevator have integrated vibration verification and condition monitoring systems directly into their latest elevators, leveraging IoT and advanced analytics to reduce unplanned downtime and enhance ride comfort. These companies invest heavily in digitalization, predictive diagnostics, and remote monitoring platforms, helping to set industry benchmarks for vibration control.
The Asia-Pacific region is expected to maintain the largest share of demand through 2030, driven by high-rise construction in China, India, Southeast Asia, and the Middle East. Europe and North America are seeing increased retrofitting activity, as building owners prioritize elevator modernization to comply with stricter safety and performance standards. Building codes in many jurisdictions now recommend or require vibration measurement and verification in both new and existing elevators, supporting ongoing market growth.
Between 2025 and 2030, the global market size for elevator vibration verification systems is projected to grow at a compound annual growth rate (CAGR) in the mid-to-high single digits, reflecting the sector’s move toward smart building integration and lifecycle asset management. Technological advances—such as AI-based vibration pattern recognition, wireless sensor networks, and cloud-based data analytics—are anticipated to further drive adoption. Market leaders like Otis Worldwide Corporation and KONE Corporation are expected to expand their portfolios with more sophisticated verification and diagnostic tools in the coming years, while partnerships between OEMs and sensor manufacturers will proliferate as interoperability and open protocols gain traction.
- 2025: Market valued in the upper hundreds of millions USD globally, with Asia-Pacific dominating new installation demand.
- 2026–2028: Retrofitting activity intensifies in developed markets; AI and predictive analytics become standard in premium segments.
- 2029–2030: Market growth remains robust as building codes tighten and smart building investments accelerate; major OEMs and sensor suppliers consolidate positions.
Key Drivers: Safety, Regulations, and Smart Building Integration
The global focus on elevator safety, regulatory compliance, and the integration of smart building technologies is sharply accelerating the adoption of elevator vibration verification systems in 2025 and the coming years. Vibration verification systems, which use advanced sensors and analytic algorithms to monitor and diagnose elevator performance, play a pivotal role in preventing mechanical failures and ensuring passenger safety. Several key drivers are shaping this evolution.
- Safety and Reliability: As urban density increases and high-rise buildings proliferate, there is heightened emphasis on passenger safety and continuous elevator operation. Vibration verification systems detect early anomalies—such as misalignments, bearing wear, or imbalances—that can lead to unexpected stoppages or accidents. Leading manufacturers like Otis and KONE are embedding predictive maintenance and advanced monitoring into their elevator platforms, with vibration data forming a core input for their diagnostic suites.
- Regulatory Requirements: Regulatory agencies in North America, the European Union, and Asia-Pacific are progressively mandating stricter maintenance protocols and real-time monitoring capabilities for elevators. For instance, updates to standards such as EN 81 and ASME A17.1/CSA B44 are driving the installation of monitoring systems that can verify compliance and generate audit trails. Major industry players, including Schindler and TK Elevator, have responded by offering integrated vibration analysis as part of their compliance and maintenance packages.
- Smart Building Integration: The rapid growth of the smart building sector is fueling the adoption of IoT-enabled elevator solutions. Vibration verification systems are increasingly being networked into building management systems (BMS) to share real-time status, predict faults, and optimize energy usage. Companies such as Hitachi and Mitsubishi Electric are deploying elevators that communicate vibration and operational data to centralized dashboards, allowing facility managers to coordinate responses across assets.
- Outlook: As digitalization and urbanization continue, the demand for robust elevator vibration verification is expected to climb. Industry leaders are investing in AI-driven analytics and wireless sensor technologies to enhance system accuracy and reduce maintenance costs. Collaboration between elevator OEMs, sensor manufacturers, and BMS platform providers will likely intensify, fostering further innovation and standardization in vibration monitoring across global markets.
Leading Innovators and Technology Providers
The field of elevator vibration verification systems is rapidly evolving, with 2025 marking a significant period of innovation, digitalization, and standardization. Leading technology suppliers are focusing on advanced sensor integration, real-time analytics, and predictive maintenance capabilities to address growing safety, comfort, and regulatory requirements across global markets.
Among the dominant players, Otis Worldwide Corporation stands out for its commitment to elevator performance monitoring. As of 2025, Otis is leveraging digital platforms such as its Otis ONE IoT-based system, integrating vibration sensors and accelerometers to continuously monitor ride quality, detect anomalous vibration patterns, and enable remote diagnostics. Through cloud connectivity, these systems offer proactive maintenance alerts and detailed verification reports, helping operators reduce downtime and improve passenger experience.
KONE Corporation, another global leader, emphasizes its 24/7 Connected Services platform, which incorporates vibration verification as a core feature. KONE’s solution uses advanced machine learning algorithms to analyze elevator operational data, including vibration signatures, and automatically flags deviations from established comfort and safety thresholds. In 2025, KONE continues to expand integration capabilities with building management systems, aligning with smart building trends and stricter urban mobility standards.
Japan-based Mitsubishi Electric has also made significant strides, developing proprietary vibration measurement and verification systems tailored for both new installations and modernization projects. Their latest elevator models feature in-built multi-axis sensors that monitor vibration and noise in real-time, with data accessible through secure digital dashboards. These systems support compliance with evolving local and international ride quality regulations, such as ISO 18738.
In addition to OEMs, specialized sensor and measurement technology providers such as HBM (Hottinger Brüel & Kjær) supply high-precision accelerometers and vibration analysis equipment, enabling both manufacturers and third-party inspectors to conduct rigorous elevator vibration verification. HBM’s offerings are increasingly integrated into automated verification workflows, streamlining commissioning and periodic inspection processes.
Looking ahead into the next few years, the industry is expected to see further convergence between elevator vibration verification and broader condition monitoring ecosystems. This will be driven by developments in edge computing, wireless sensor networks, and AI-powered diagnostics. As digital standards mature and smart city initiatives expand, collaboration between elevator OEMs, sensor companies, and digital platform providers will be key to setting new benchmarks in safety, reliability, and regulatory compliance for vertical transportation systems worldwide.
Latest Advances in Vibration Sensing and Data Analytics
The field of elevator vibration verification systems is undergoing rapid transformation as advanced sensing technologies and powerful data analytics become increasingly central to elevator safety and performance. As of 2025, key developments are centered on the integration of high-precision accelerometers, IoT connectivity, and machine learning algorithms to monitor, analyze, and predict elevator vibration anomalies in real-time.
Recent product launches and system upgrades by leading elevator manufacturers demonstrate the shift toward continuous, data-driven verification. For example, Otis Worldwide Corporation has integrated edge-computing vibration sensors into its Gen3 and Gen360 platforms, enabling real-time diagnostics and predictive maintenance. These sensors capture multidirectional vibration data, which is then analyzed to detect deviations from established vibration baselines, facilitating early intervention before issues escalate.
Similarly, KONE Corporation has deployed its 24/7 Connected Services system, utilizing cloud-based analytics and a network of onboard accelerometers to track elevator ride quality and mechanical health. This system leverages artificial intelligence to differentiate between normal operational vibrations and those that may indicate misalignment, component wear, or rail irregularities. The company reports that these advances have contributed to a measurable reduction in unplanned downtime and maintenance visits.
Suppliers such as Schindler Group and TK Elevator are also enhancing their platforms with digital twin technology, where real-time vibration data feeds virtual models of elevator systems. This enables simulations and scenario analysis, allowing service teams to diagnose faults remotely and validate repair effectiveness through post-maintenance vibration verification.
On the standards front, organizations like the Elevator World and the International Organization for Standardization (ISO) are actively working to update vibration measurement protocols, reflecting the increased granularity and reliability of new sensor arrays. These evolving standards are expected to drive further adoption of automated verification systems across new installations and modernization projects.
Looking ahead, the next few years will likely see even greater adoption of wireless sensor networks, with self-calibrating devices and edge-AI capabilities. Such advancements are anticipated to not only improve elevator ride comfort and safety but also reduce lifecycle costs through more accurate, condition-based maintenance scheduling. As urban infrastructure grows taller and more complex, elevator vibration verification systems will play a critical role in ensuring dependable and smooth vertical transportation.
Emerging Industry Standards and Compliance Trends
The landscape for elevator vibration verification systems is rapidly evolving in 2025, driven by heightened regulatory scrutiny, urban densification, and the integration of advanced digital technologies. Industry standards are increasingly converging toward harmonized, data-driven frameworks to ensure ride quality, passenger safety, and system durability—particularly as high-rise construction proliferates in global metropolitan centers.
One key development is the ongoing revision and adoption of international standards such as ISO 18738-1 and ISO 18738-2, which articulate the measurement and reporting protocols for the ride quality of elevators and escalators. These standards are being referenced more frequently in both national and regional building codes, prompting elevator manufacturers and building operators to invest in more sophisticated vibration verification tools and processes. Organizations like the Schindler Group and Otis Elevator Company—two of the world’s largest elevator manufacturers—have publicly acknowledged the integration of vibration analytics within their predictive maintenance platforms and compliance documentation.
Recent years have seen a shift from periodic manual testing to continuous real-time monitoring using embedded sensors and IoT-enabled platforms. Companies such as KONE and TK Elevator (formerly ThyssenKrupp Elevator) are deploying cloud-based systems that automatically log, analyze, and report vibration data for compliance and performance optimization. This not only streamlines regulatory verification but also aligns with emerging standards requiring transparent, auditable records of elevator operation and maintenance activities.
Furthermore, regulatory bodies in Europe, Asia, and North America are expected to formalize minimum vibration performance thresholds, with stricter enforcement slated for the next few years. The Elevator World, Inc., a recognized industry information body, has reported on new compliance trends, including the expectation for third-party verification and digital recordkeeping of vibration data as part of the elevator commissioning and annual inspection processes.
Looking forward, the industry is likely to see the establishment of interoperable data standards to enable cross-vendor verification and benchmarking. The increasing prevalence of smart buildings and digital twins is expected to further accelerate the adoption of advanced vibration verification systems, as building owners demand seamless integration with broader facility management platforms for both compliance and predictive analytics.
- ISO standards are being more widely enforced in national codes.
- Major OEMs (e.g., Schindler, Otis, KONE, TK Elevator) are embedding real-time vibration monitoring and analytics in their offerings.
- Regulators are moving toward mandatory digital recordkeeping and third-party verification of vibration compliance.
- Industry-wide interoperable data protocols are anticipated, enabling benchmarking and integration with smart building systems.
Regional Analysis: North America, Europe, Asia-Pacific, and Beyond
The global market for elevator vibration verification systems is undergoing significant transformation in 2025, with regional dynamics shaped by regulatory trends, technological adoption, and urbanization rates. North America, Europe, and Asia-Pacific stand out as the primary regions driving innovation and deployment, while other emerging markets are gradually increasing their involvement.
- North America: In the United States and Canada, stringent building codes and a focus on occupant comfort in commercial real estate have spurred investments in advanced vibration monitoring solutions. Major elevator manufacturers such as Otis Worldwide Corporation and Schindler Group are integrating real-time vibration verification systems in both new installations and modernization projects. The adoption of IoT and predictive analytics is prevalent, with system data increasingly linked to building management platforms. There is also a notable rise in retrofitting older elevator stock in urban centers, supporting safety and lifecycle extension initiatives.
- Europe: The European market is characterized by rigorous safety regulations and a strong emphasis on sustainability and accessibility. Countries such as Germany, France, and the UK are implementing EN 81-20 and EN 81-50 standards, which mandate precise vibration measurement and verification protocols. European elevator majors, including KONE and TK Elevator, are leveraging sensor-based verification systems to improve ride comfort and reduce maintenance costs. Additionally, the region’s focus on green buildings and smart city initiatives is fostering the adoption of digital vibration verification as part of broader elevator health monitoring ecosystems.
- Asia-Pacific: Rapid urbanization, particularly in China, India, and Southeast Asia, is fueling new elevator installations and the integration of advanced verification technologies. Local and multinational manufacturers such as Hitachi and Mitsubishi Electric are deploying AI-enhanced vibration verification systems to ensure reliability in high-rise and high-traffic environments. Governments in the region are updating elevator safety regulations, and there is increasing demand for systems that provide remote diagnostics and real-time alerts, supporting the maintenance of vast elevator fleets in dense urban settings.
- Beyond Major Regions: In Latin America, the Middle East, and Africa, elevator vibration verification is still emerging but gaining traction in premium commercial and residential developments. Global companies are introducing scalable, cost-effective solutions tailored to markets with less stringent regulations, aiming to increase safety awareness and compliance.
Looking forward, the outlook for elevator vibration verification systems is robust across all regions, driven by digitalization, regulatory evolution, and the need for predictive maintenance. Collaboration between manufacturers, building operators, and regulatory bodies is set to enhance system sophistication and global market penetration through 2026 and beyond.
Challenges and Barriers to Widespread Adoption
Elevator vibration verification systems are increasingly recognized for their potential to enhance ride quality, safety, and predictive maintenance in modern vertical transportation. However, several challenges and barriers continue to impede their widespread adoption, especially as we move through 2025 and look toward the next few years.
One primary challenge is the integration of advanced vibration monitoring with legacy elevator infrastructure. Many buildings, especially in mature markets, still operate older elevator systems that lack digital interfaces or standardized protocols, making retrofitting with contemporary vibration sensors and data loggers both technically complex and costly. Leading manufacturers such as Schindler and Otis have developed proprietary solutions for their new-generation elevators, yet cross-compatibility with third-party systems or multi-brand fleets remains limited, slowing adoption in mixed-building portfolios.
Another barrier is the cost-benefit analysis for building owners and operators. While the long-term advantages of predictive maintenance and minimized downtime are well documented, the upfront investment for hardware, software, and integration can be significant, particularly in mid-tier or low-traffic buildings. Return on investment is often most compelling for high-rise or high-traffic environments, as evidenced by deployment patterns among premium commercial properties serviced by TK Elevator and KONE. This financial calculus may limit uptake in smaller-scale or budget-sensitive projects.
Data privacy and cybersecurity concerns are also emerging as critical issues. Vibration verification systems frequently require cloud connectivity for remote diagnostics and AI-driven analytics. As these systems collect and transmit operational data, building owners are increasingly wary of potential vulnerabilities, especially given the sensitive nature of some commercial tenants. Companies like KONE have started to emphasize cybersecurity features in their digital offerings, but industry-wide standards and certifications are still evolving.
Finally, regulatory and standards alignment remains a work in progress. While organizations such as the Elevator World and the International Organization for Standardization are contributing to the development of vibration measurement and reporting protocols, adoption varies by region. This patchwork regulatory environment complicates procurement decisions and creates uncertainty for suppliers and property managers planning multi-country deployments.
In summary, while the technological case for elevator vibration verification systems is strong, widespread adoption in 2025 and the near future will hinge on overcoming integration hurdles, clarifying value propositions, addressing cybersecurity, and achieving regulatory harmonization.
Case Studies: Real-World Applications and Impact
In recent years, the adoption of advanced elevator vibration verification systems has accelerated, driven by the increasing demands for safety, ride comfort, and predictive maintenance in modern buildings. Real-world applications demonstrate how these systems are improving elevator performance and reliability, particularly as urban environments become more vertical and technologically integrated.
A prominent example is the deployment of vibration monitoring solutions by Otis Elevator Company, one of the world’s largest elevator manufacturers. By integrating sensor-based systems capable of real-time vibration analysis, Otis has improved its ability to detect anomalies that can indicate issues such as rail misalignment, worn rollers, or imbalanced loads. These systems not only enable prompt maintenance but also contribute to enhanced passenger comfort by minimizing vibrations that can lead to ride disturbances.
Similarly, Schindler Group has implemented advanced vibration verification as part of its “Digital Elevator Maintenance” suite. Their smart sensors continuously gather vibration data, which is processed through cloud-based analytics to predict potential faults before they escalate. This proactive approach has been credited with reducing unscheduled downtime and extending the operational lifespan of elevator components in several high-rise installations globally.
In Asia, Hitachi, Ltd. has showcased its commitment to elevator safety and comfort by employing vibration verification systems in its next-generation high-speed elevators. As elevator speeds increase—especially in super-tall skyscrapers—the need for precise vibration monitoring becomes critical. Hitachi’s solutions provide not only compliance with rigorous safety standards but also a smoother user experience, which is increasingly demanded by luxury residential and commercial clients.
On the supplier side, companies like ifm electronic and SICK AG supply industrial-grade vibration sensors and condition monitoring hardware, which are integrated into elevator systems worldwide. Their products are designed for harsh elevator environments and enable OEMs and service providers to deploy scalable vibration verification across diverse fleets.
Looking ahead to 2025 and beyond, the role of elevator vibration verification systems is set to expand further, particularly as building owners prioritize smart infrastructure and data-driven maintenance. The integration of IoT platforms and machine learning algorithms is expected to make these systems even more predictive and autonomous, thereby reducing costs and improving safety margins. As global cities continue to grow vertically, case studies from industry leaders suggest that vibration verification will remain a cornerstone of reliable and user-friendly vertical transportation.
Future Outlook: Next-Gen Verification Systems and Opportunities
As the elevator industry continues its push toward greater safety, comfort, and intelligent operation, elevator vibration verification systems are set for significant technological advances through 2025 and the years immediately following. These systems—crucial for monitoring, diagnosing, and minimizing vibration—are evolving from basic measurement tools to fully integrated, predictive maintenance platforms that leverage digitalization and AI.
Leading elevator manufacturers such as Otis, KONE, Schindler, and TK Elevator have all signaled investments in advanced diagnostic technologies as part of their broader digital transformation initiatives. These companies are increasingly embedding vibration sensors and IoT-enabled verification modules in both new and retrofit elevator installations. For instance, KONE’s cloud-connected elevators and predictive analytics platforms are already being deployed for proactive maintenance and real-time ride quality monitoring, laying the groundwork for more sophisticated vibration verification in the near term.
The next generation of these systems will likely feature:
- Real-time analytics: Onboard edge computing will process vibration data locally, enabling immediate detection of anomalies that could signal mechanical wear, misalignment, or rail defects. This approach reduces latency and dependence on cloud connections, a trend echoed by industry leaders.
- Integration with digital twins: Companies like Schindler are building digital twin models of elevator installations to simulate and predict vibration behavior under varying load and usage conditions. Such models are expected to be increasingly used as verification tools in design and ongoing operation.
- Standardization and compliance: Regulatory bodies and organizations such as ISO continue to update standards (e.g., ISO 18738) relating to ride quality and vibration measurement. This is pushing suppliers to develop systems that not only measure but also document compliance, opening opportunities for manufacturers who can provide robust, auditable solutions.
- Remote diagnostics and service opportunities: With elevators in buildings becoming more connected, remote verification of vibration parameters is becoming more feasible. This enables service providers to offer new maintenance contracts focused specifically on ride quality assurance.
Looking ahead, the elevator market’s steady urbanization, growth in high-rise construction, and rising user expectations for comfort and uptime are all driving demand for next-generation vibration verification systems. Suppliers with strong digital capabilities, proven reliability, and a commitment to compliance are poised to capture significant market share as these trends accelerate through 2025 and beyond.
Sources & References
- Otis Worldwide Corporation
- KONE Corporation
- Schindler Group
- TK Elevator
- ifm electronic
- SICK AG
- Hitachi
- Mitsubishi Electric
- HBM (Hottinger Brüel & Kjær)
- Elevator World
- International Organization for Standardization
- Schindler
- Otis
- KONE
- Elevator World
- International Organization for Standardization