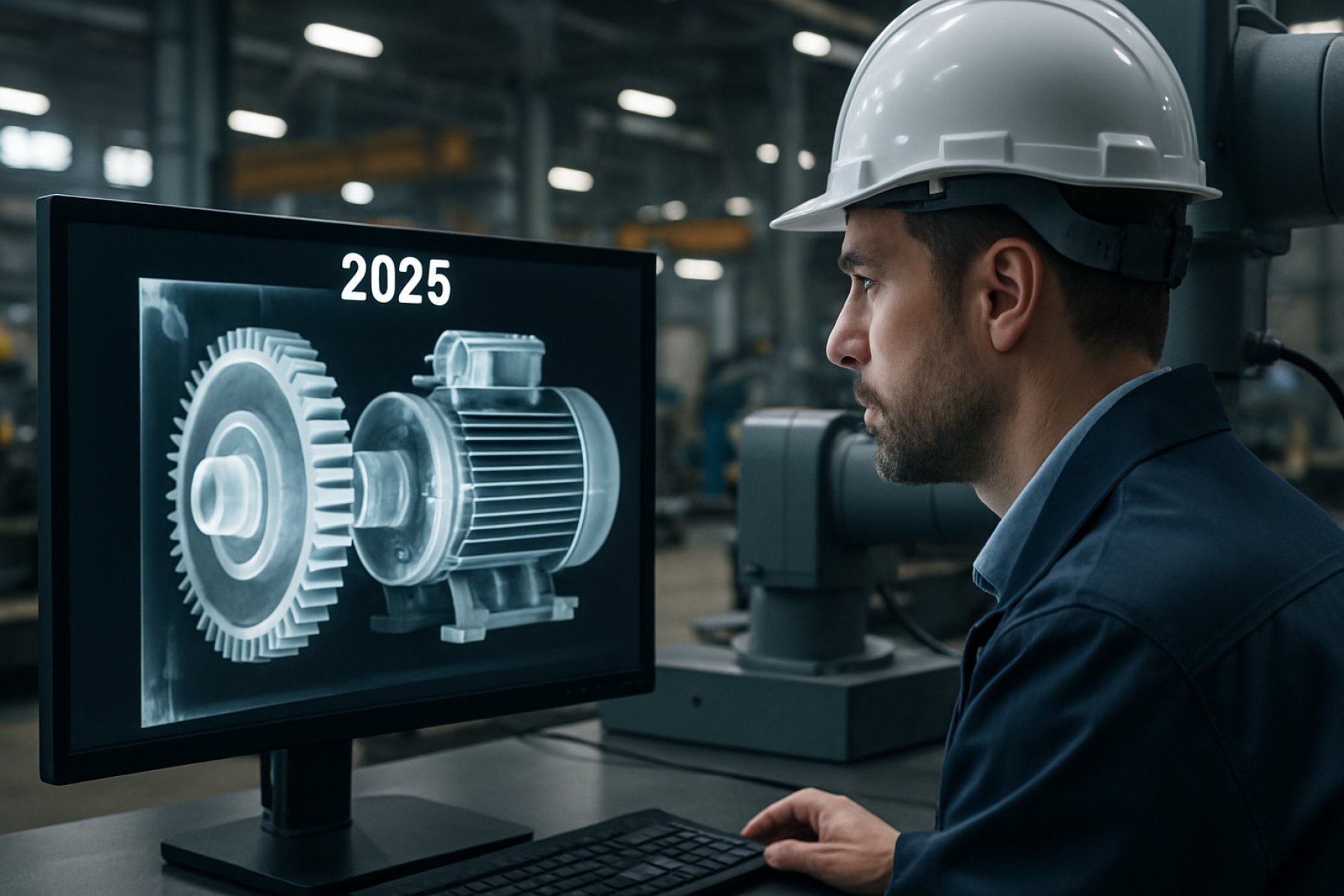
Table of Contents
- Executive Summary: 2025 Outlook and Key Trends
- Market Size and Forecasts Through 2030
- Breakthrough Technologies Reshaping X-ray Diagnostics
- Key Players and Strategic Partnerships (e.g., waygate-technologies.com, gehealthcare.com, olympus-ims.com)
- Emerging Applications Across Industries: Aerospace, Automotive, Energy, and More
- Regulatory Landscape and Industry Standards (e.g., asnt.org, astm.org)
- Integration with AI, Robotics, and Digital Twins
- Challenges: Data Security, Cost, and Adoption Barriers
- Regional Hotspots: North America, Europe, and Asia-Pacific Growth Drivers
- Future Outlook: Disruptive Innovations and Investment Opportunities
- Sources & References
Executive Summary: 2025 Outlook and Key Trends
Expanded nondestructive X-ray diagnostics are poised for significant growth and technological evolution in 2025, driven by advances in digital imaging, automation, artificial intelligence (AI), and the increasing demand for high-throughput quality assurance across industries. This technology, which enables the inspection and analysis of materials, assemblies, and products without causing any damage, is seeing adoption beyond traditional sectors such as healthcare and aerospace, reaching into electronics, automotive, energy, and additive manufacturing.
In the coming year, integration with AI and machine learning algorithms is set to transform X-ray diagnostics. Major manufacturers are rolling out systems that combine high-resolution imaging with automated defect recognition and predictive analytics, resulting in faster, more accurate inspections and reduced reliance on specialist operators. For instance, GE HealthCare and Siemens Healthineers continue to invest in digital X-ray platforms enhanced by AI to streamline clinical workflows and improve diagnostic confidence. In industrial settings, Waygate Technologies is advancing automated X-ray and computed tomography (CT) solutions with machine learning capabilities for faster decision-making in nondestructive testing (NDT).
The miniaturization and portability of X-ray devices are also expanding point-of-use diagnostics. Companies such as Vidisco are introducing portable digital radiography systems, enabling on-site inspections in remote or challenging environments, including pipeline integrity checks and field maintenance in the energy sector. Similarly, in electronics manufacturing, the demand for inline, high-throughput inspection is addressed by YXLON International, which is deploying advanced automated X-ray systems capable of 3D analysis for defect detection at micro and nano scales.
Regulatory expectations for product quality and safety, particularly in medical devices and automotive components, are accelerating the adoption of advanced X-ray diagnostics. Initiatives such as the European Union’s MDR (Medical Devices Regulation) and stricter automotive safety standards are prompting manufacturers to implement more rigorous nondestructive evaluation. Industry bodies like The American Society for Nondestructive Testing (ASNT) are developing updated guidelines and certification programs to support the deployment of new technologies.
Looking ahead, expanded nondestructive X-ray diagnostics are expected to see increased convergence with Industry 4.0 frameworks, enabling real-time process monitoring and closed-loop quality control. With investments from leading players and continued innovation, 2025 will mark a pivotal year for the broader adoption of sophisticated, efficient, and automated X-ray diagnostic solutions across a wide array of sectors.
Market Size and Forecasts Through 2030
The global market for expanded nondestructive X-ray diagnostics is undergoing significant transformation, with strong momentum expected to continue through 2030. Advances in digital radiography, computed tomography (CT), and real-time imaging are propelling growth across healthcare, industrial, and research applications. In 2025, the demand for advanced X-ray diagnostic systems is being driven by the need for more precise, rapid, and cost-effective inspection methods, especially in sectors such as aerospace, automotive, electronics, and medical device manufacturing.
Major manufacturers are reporting notable investments and product launches tailored to these trends. For example, GE HealthCare has emphasized ongoing expansion of its digital X-ray portfolio, integrating artificial intelligence (AI) to enhance diagnostic accuracy and workflow efficiency. Similarly, Siemens Healthineers continues to introduce new X-ray imaging solutions that leverage automation and advanced image processing, targeting both clinical and industrial users. In the industrial domain, Philips and ZEISS are investing in high-resolution industrial CT and X-ray systems for quality assurance and failure analysis, reflecting the growing adoption of nondestructive testing (NDT) in manufacturing.
Healthcare remains the largest segment for X-ray diagnostics, with digitalization and the expansion of screening programs fueling ongoing demand. In 2025, emerging economies in Asia-Pacific and Latin America are experiencing rapid uptake of mobile and portable X-ray units, supported by initiatives to improve access to diagnostic imaging. Carestream and Konica Minolta have highlighted increased shipments of mobile digital radiography systems to hospitals and clinics in these regions.
Looking ahead, industry leaders forecast sustained growth through 2030, with compounded annual growth rates (CAGR) in the high single digits for both medical and industrial applications. Factors such as AI-driven image analysis, integration with cloud-based data management, and stricter regulatory standards in manufacturing are expected to further accelerate market expansion. Companies like Waygate Technologies (a Baker Hughes business) are developing next-generation industrial X-ray systems with 3D imaging and automated defect recognition, anticipating increasing demand for high-throughput, non-contact inspection.
Overall, by 2030, the expanded nondestructive X-ray diagnostics market is projected to reach new highs, driven by technological innovation, broadening end-user adoption, and a global focus on quality, safety, and operational efficiency.
Breakthrough Technologies Reshaping X-ray Diagnostics
In 2025, the field of nondestructive X-ray diagnostics is witnessing rapid technological expansion, fueled by growing demand for advanced inspection solutions across industries such as aerospace, electronics, automotive, and additive manufacturing. Key breakthroughs are emerging in detector technology, artificial intelligence (AI)-powered analytics, and multimodal imaging—each reshaping how X-ray diagnostics are deployed for quality assurance, failure analysis, and process optimization.
One of the most notable advancements is the adoption of high-resolution flat panel detectors and photon-counting detector arrays, which enable unprecedented clarity and sensitivity in both two-dimensional and three-dimensional imaging. For instance, Varex Imaging Corporation has expanded its portfolio to include next-generation digital detectors with enhanced dynamic range and real-time imaging capabilities, catering to industrial applications that require precise characterization of complex assemblies and microstructures. Simultaneously, Canon Medical Systems is investing in compact, high-speed detectors aimed at automating inspection workflows for electronics and battery manufacturing.
AI-driven image analysis is another transformative force. Companies like Siemens Healthineers are integrating deep learning algorithms into nondestructive testing (NDT) platforms, enabling automated defect recognition, anomaly detection, and predictive maintenance. These solutions not only accelerate inspection throughput but also reduce human error, a critical advantage as manufacturing tolerances tighten and component geometries become more intricate.
Expanded nondestructive X-ray diagnostics are now leveraging hybrid and multimodal imaging systems. For example, Carl Zeiss AG has launched systems that combine X-ray computed tomography (CT) with advanced material analysis, offering comprehensive insights into internal features, porosity, and structural integrity in a single scan. Such systems are increasingly deployed in the inspection of lightweight composite materials and high-density electronic assemblies, areas where traditional X-ray imaging alone may fall short.
Looking ahead, industry stakeholders anticipate even broader adoption of portable and in-line X-ray diagnostics, with miniaturized sources and cloud-based data platforms enabling real-time, on-site analysis and remote expert collaboration. Initiatives by organizations such as Comet Group are paving the way for ruggedized, high-power X-ray modules that can be integrated directly into manufacturing lines or field service equipment. As these technologies mature, the outlook for nondestructive X-ray diagnostics points toward greater automation, higher resolution, and seamless integration with digital manufacturing ecosystems.
Key Players and Strategic Partnerships (e.g., waygate-technologies.com, gehealthcare.com, olympus-ims.com)
The landscape of nondestructive X-ray diagnostics is witnessing rapid evolution driven by major industry players through strategic partnerships, technology integration, and geographic expansion. In 2025, established companies and emerging innovators alike are advancing the capabilities and reach of X-ray-based nondestructive testing (NDT) across critical sectors such as aerospace, automotive, electronics, and energy.
-
Waygate Technologies (formerly GE Inspection Technologies), a division of Baker Hughes, continues to be a leader in industrial X-ray and computed tomography (CT) solutions. The company has recently expanded its Phoenix product line, enhancing high-resolution micro-CT systems for electronics and battery inspection. Waygate Technologies is actively collaborating with manufacturing partners to integrate artificial intelligence (AI) algorithms for automated defect recognition, aiming to streamline quality assurance in high-volume production environments
(Waygate Technologies). -
GE HealthCare remains at the forefront of medical X-ray diagnostics, with a focus on digital and AI-powered imaging systems. In 2024–2025, the company has announced partnerships with healthcare networks to deploy X-ray solutions that enable faster, more accurate diagnostics, especially in underserved regions. Their ongoing commitment to remote and mobile X-ray technologies is helping address global challenges in healthcare accessibility
(GE HealthCare). -
Evident (formerly Olympus IMS) has maintained momentum in expanding its industrial X-ray and CT inspection offerings. The company is forming alliances with component suppliers and research institutions to enhance imaging software and detector performance. New product introductions in 2025 emphasize faster scan times and improved image clarity, supporting applications in additive manufacturing and advanced materials
(Evident (Olympus IMS)). - Strategic partnerships between OEMs, software providers, and research organizations are increasingly central. For example, collaborations between industrial X-ray system manufacturers and AI firms are accelerating the development of predictive maintenance and real-time defect classification tools. These alliances are expected to produce commercially available, fully automated inspection platforms within the next few years, substantially reducing inspection times and false positive rates.
Looking ahead, the convergence of digitalization, cloud connectivity, and advanced analytics is set to further transform nondestructive X-ray diagnostics. Key players are investing in open-architecture systems and interoperable platforms, paving the way for scalable, multi-site inspection solutions. As regulatory standards evolve and demand for traceable, high-throughput inspection grows, these strategic collaborations will likely dictate the competitive landscape through 2025 and beyond.
Emerging Applications Across Industries: Aerospace, Automotive, Energy, and More
In 2025, nondestructive X-ray diagnostics are experiencing rapid expansion across key industries such as aerospace, automotive, and energy, driven by advances in detector technology, imaging software, and system automation. This expansion is marked by adoption of both traditional X-ray computed tomography (CT) and novel high-energy and digital radiography solutions tailored to industry-specific challenges.
In aerospace, the demand for lightweight, complex parts manufactured via additive manufacturing (AM) is fueling the need for advanced nondestructive inspection (NDI) tools. Leading firms such as GE Aerospace and Nikon Corporation are deploying X-ray CT systems to detect internal defects, porosity, and dimensional inaccuracies in 3D-printed metal and composite components. These systems, with resolutions down to a few microns, are essential for ensuring safety and certification compliance as next-generation aircraft components enter service.
The automotive sector is leveraging expanded X-ray diagnostics to address the challenges of electrification and lightweighting. Companies like Waygate Technologies (a Baker Hughes business) have introduced automated X-ray inspection systems designed for high-throughput battery and electronics inspection, enabling manufacturers to noninvasively verify weld quality, check for internal voids in battery cells, and monitor structural integrity of lightweight assemblies. These advances support the push toward safer, more reliable electric vehicles, and facilitate in-line and at-line inspection for mass production.
In the energy sector, expanded X-ray diagnostics are being adopted for the inspection of critical infrastructure such as pipelines, pressure vessels, and turbine components. Carl Zeiss AG is providing high-energy X-ray CT systems capable of penetrating thick metal sections, enabling early detection of corrosion, cracks, and inclusions that could lead to catastrophic failure. The ability to perform these inspections in situ, sometimes with portable or robot-mounted systems, is reducing downtime and extending asset lifespans.
Looking forward, integration with artificial intelligence (AI) and machine learning is expected to further enhance defect recognition and automate the interpretation of complex datasets. Major equipment manufacturers are already embedding AI-driven analytics into their platforms, with Siemens and Philips investing in advanced software modules for real-time anomaly detection. As these capabilities mature over the next few years, the scope and efficiency of nondestructive X-ray diagnostics are poised to grow, supporting broader adoption across manufacturing, infrastructure, and even medical device sectors.
Regulatory Landscape and Industry Standards (e.g., asnt.org, astm.org)
The regulatory landscape for nondestructive X-ray diagnostics is undergoing significant evolution as technological advancements expand the capabilities and applications of these methods across industries. In 2025, regulatory bodies and standards organizations are intensifying their focus on harmonizing standards, ensuring safety, and accommodating emerging modalities such as digital radiography, computed tomography (CT), and advanced image analysis driven by artificial intelligence (AI).
The American Society for Nondestructive Testing (ASNT) continues to play a pivotal role in certification and qualification of personnel involved in X-ray nondestructive testing (NDT). ASNT’s certification programs, including updates to the SNT-TC-1A guidelines, are being revised to reflect the integration of new X-ray imaging modalities and the expanding use of digital data management. In 2025, ASNT is expected to release new guidance addressing competency requirements for operators using advanced digital radiography and automated defect recognition systems.
Similarly, the ASTM International is actively updating and expanding its suite of NDT standards, with particular emphasis on X-ray and CT techniques. Standards such as ASTM E2737 (for digital detector array evaluation) and ASTM E2698 (for digital radiography using computed radiography systems) are being revised to account for recent innovations in detector technology, higher resolution imaging, and new calibration protocols. Notably, ASTM committees are collaborating with industry partners to ensure that these standards remain aligned with rapid advances in X-ray hardware and software, including the adoption of AI-driven analysis.
Globally, regulatory alignment is also a priority. Organizations such as the International Organization for Standardization (ISO) are working to harmonize standards like ISO 17636 for X-ray testing of welds, facilitating cross-border acceptance of inspection results and supporting international supply chains. In 2025 and beyond, ISO’s technical committees are expected to further integrate digital radiography and CT into core standards, providing clear guidance on data integrity, traceability, and cybersecurity for radiographic data.
Looking ahead, regulatory bodies are anticipated to place growing emphasis on data security and privacy in digital X-ray diagnostics, especially as industrial and medical applications converge. Industry stakeholders are also calling for increased interoperability between equipment manufacturers, which is expected to drive the development of new standards for data formats and communication protocols. As innovation accelerates, ongoing collaboration among standards bodies, industry, and end-users will be critical to ensuring that expanded nondestructive X-ray diagnostics are deployed safely, effectively, and in compliance with evolving global norms.
Integration with AI, Robotics, and Digital Twins
In 2025, the integration of advanced nondestructive X-ray diagnostics with artificial intelligence (AI), robotics, and digital twins is accelerating across industries such as aerospace, automotive, and manufacturing. This expanded approach is fundamentally reshaping how defects are detected, analyzed, and predicted, resulting in increased reliability, reduced downtime, and streamlined quality assurance processes.
AI-driven image analysis is at the forefront, enhancing the interpretive power of X-ray data. Deep learning algorithms are now capable of automatically detecting subtle flaws in real time, reducing human error and increasing throughput. For instance, GE HealthCare and Siemens Healthineers have deployed AI-powered image processing in their medical X-ray systems, with similar principles being adopted in industrial X-ray computed tomography (CT) for parts inspection. In industrial settings, Waygate Technologies (part of Baker Hughes) has incorporated AI-based defect recognition into its high-resolution X-ray and CT solutions, allowing for automated inspection workflows and advanced analytics.
Robotics is increasingly being paired with X-ray diagnostics to automate repetitive or hazardous inspection tasks. Robotic arms equipped with X-ray detectors can scan complex components from multiple angles in confined spaces, improving safety and consistency. YXLON International—a division of Comet Group—has recently introduced robotic X-ray inspection cells capable of continuous, unmanned operation for automotive and aerospace components, with integration into production lines for real-time feedback and process control.
Digital twin technology, whereby a virtual replica of a physical asset is maintained using real-time X-ray data, is becoming more prevalent. By continuously updating digital twins with in-situ X-ray inspection results, manufacturers can predict maintenance needs, optimize part lifecycles, and simulate the impact of defects on structural integrity. Siemens is leveraging this approach in its Digital Enterprise portfolio, enabling closed-loop manufacturing where NDT (nondestructive testing) data informs both design improvements and predictive maintenance.
Looking ahead to the next few years, the convergence of X-ray diagnostics with AI, robotics, and digital twins is expected to deepen. Industry participants are investing in cloud-based platforms for centralized data analysis and remote diagnostics. Ongoing collaborations, such as those between GE Digital and manufacturing partners, are targeting fully automated, AI-driven inspection ecosystems. These advances promise not only faster and more accurate defect detection but also a shift toward predictive and prescriptive maintenance models, reducing costs and enhancing operational resilience.
Challenges: Data Security, Cost, and Adoption Barriers
As nondestructive X-ray diagnostics continue to expand across industries—from aerospace and automotive to energy and medical devices—the sector faces a set of persistent and evolving challenges in 2025 and the coming years. The primary hurdles include data security, the high cost of advanced systems, and barriers to adoption, particularly in sectors with stringent regulatory or legacy infrastructure.
Data Security. With the growing integration of digital radiography, computed tomography (CT), and artificial intelligence (AI)-driven interpretation, sensitive imaging data is increasingly transferred, stored, and processed in networked environments. This raises concerns around data interception, unauthorized access, and compliance with data privacy standards, particularly in sectors handling proprietary designs or patient information. Companies such as GE HealthCare and Siemens Healthineers have rolled out enhanced cybersecurity features, including encrypted data transmission, multi-factor authentication, and audit trails, to address these vulnerabilities. Nonetheless, the rapid pace of digital transformation often outstrips the implementation of robust security protocols, leaving gaps that require continuous monitoring and incident response investments.
Cost Constraints. The adoption of state-of-the-art X-ray systems—such as high-energy micro-CT and automated defect recognition platforms—demands significant capital outlay. For example, micro-CT systems from Bruker and digital X-ray inspection platforms from ZEISS can represent six- or seven-figure investments. While equipment leasing and service-as-a-subscription models are emerging, many small and medium-sized enterprises (SMEs) struggle to justify the expense, especially when existing conventional inspection solutions suffice. Furthermore, the need for specialized facilities (e.g., radiation shielding) and ongoing maintenance amplifies total cost of ownership, potentially delaying return on investment.
Adoption Barriers. Even as regulatory bodies such as the U.S. Food & Drug Administration and International Atomic Energy Agency support advanced NDT (nondestructive testing) technologies, broad implementation is slowed by several factors:
- Workforce Skills Gap: Mastery of digital X-ray modalities and AI-augmented interpretation requires upskilling. Organizations like The American Society for Nondestructive Testing are expanding certification and training programs, but the pace of talent development may lag behind technology deployment.
- Legacy Integration: Many manufacturers rely on decades-old infrastructure, complicating seamless integration of new digital or automated inspection systems.
- Regulatory Compliance: Meeting new standards for digital data integrity, traceability, and imaging quality requires investment in validation and documentation processes, adding another layer of complexity.
Looking ahead, overcoming these challenges will depend on collaborative efforts among equipment manufacturers, regulatory bodies, and end users to develop scalable, secure, and cost-effective solutions. Standardization and modularity, coupled with ongoing training and cybersecurity enhancements, will be critical to unlocking the full potential of expanded nondestructive X-ray diagnostics through 2025 and beyond.
Regional Hotspots: North America, Europe, and Asia-Pacific Growth Drivers
The landscape for nondestructive X-ray diagnostics is rapidly evolving, with North America, Europe, and Asia-Pacific emerging as pivotal regions driving growth and innovation. Across these regions, a confluence of regulatory support, technological advancement, and escalating demand from industries such as healthcare, aerospace, automotive, and electronics is shaping the market outlook for 2025 and the years immediately ahead.
In North America, the United States continues to spearhead advancements in nondestructive X-ray diagnostics, buoyed by significant investments in healthcare infrastructure and industrial quality assurance. Key manufacturers such as GE HealthCare are expanding their X-ray imaging portfolios with AI-powered diagnostic and inspection systems for both clinical and industrial use. The Food and Drug Administration’s ongoing support for digital radiography and AI-assisted diagnostic tools is accelerating the clinical adoption of advanced X-ray modalities.
Europe is witnessing robust growth, particularly in Germany, France, and the UK, where regulatory harmonization and strong industrial bases underpin demand. Companies like Siemens Healthineers and Philips are leading the charge in digital transformation, introducing mobile and compact X-ray systems that offer high-resolution imaging with reduced radiation doses. The European Union’s emphasis on medical device innovation, as reflected in the Medical Device Regulation (MDR), is further incentivizing investments in nondestructive diagnostic technologies. The region also benefits from a strong automotive and aerospace sector, driving adoption of advanced X-ray computed tomography (CT) for quality assurance and failure analysis.
In the Asia-Pacific region, rapid industrialization and expanding healthcare investment—particularly in China, Japan, South Korea, and India—are fueling demand for both medical and industrial X-ray diagnostics. Shimadzu Corporation and Canon Inc. are expanding their reach with digital radiography and micro-CT systems tailored to local market needs. Recent launches of portable and automated X-ray inspection solutions for electronics and battery manufacturing underscore the region’s role as a global production hub. Additionally, government initiatives in China and Japan to modernize healthcare delivery and implement strict quality standards in manufacturing are expected to bolster market growth through 2025 and beyond.
As these regions continue to focus on digitalization, AI integration, and miniaturization, the nondestructive X-ray diagnostics segment is poised for accelerated adoption and innovation. Industry stakeholders are likely to see expanded opportunities in preventive maintenance, remote diagnostics, and real-time digital imaging across both healthcare and industrial sectors in the next few years.
Future Outlook: Disruptive Innovations and Investment Opportunities
The outlook for expanded nondestructive X-ray diagnostics is marked by accelerating innovation and significant investment, positioning the sector for substantial growth through 2025 and into the late 2020s. This momentum is driven by advances in digital detector technology, machine learning for image interpretation, and the industrialization of high-resolution computed tomography (CT) and phase-contrast imaging, which are broadening the scope and precision of X-ray-based inspection across industries.
In 2025, manufacturers are set to introduce new generations of X-ray detectors with enhanced sensitivity and speed. For instance, Siemens Healthineers and GE HealthCare have announced plans to further develop photon-counting CT technology, a disruptive advancement that allows for improved image quality at lower radiation doses. These technologies are expected to transition from medical diagnostics into industrial quality assurance, notably in aerospace, automotive, and advanced electronics manufacturing.
Industrial X-ray system suppliers, such as Waygate Technologies (a Baker Hughes business) and YXLON International, are investing in multi-energy and high-throughput systems that can not only detect micron-scale defects but also characterize material composition and density variations in complex assemblies. This is particularly relevant as sectors like battery manufacturing and additive manufacturing demand finer defect detection and real-time monitoring capabilities.
Another transformative trend is the integration of artificial intelligence (AI) and advanced analytics with X-ray diagnostics. ZEISS Industrial Quality Solutions is actively developing AI-powered defect recognition and automated reporting solutions for in-line and at-line inspection. Such software-driven enhancements are anticipated to reduce labor costs, increase throughput, and enable predictive maintenance protocols in manufacturing environments.
Investments are also flowing into the miniaturization and mobility of X-ray systems. Companies like Varex Imaging are advancing portable and handheld X-ray sources and detectors suitable for point-of-care diagnostics, field inspections, and maintenance in remote locations. These developments expand the reach of nondestructive testing (NDT) to new use cases, such as infrastructure monitoring and disaster response.
Looking ahead, the convergence of high-resolution imaging, AI, and connected digital platforms is expected to create entirely new business models—such as X-ray diagnostics as a service—and open investment opportunities in both hardware and software. Industry partnerships and R&D initiatives, particularly those supported by organizations like The American Society for Nondestructive Testing (ASNT), are likely to accelerate standards development and technology adoption globally, setting the stage for expanded market penetration and new applications across sectors.
Sources & References
- GE HealthCare
- Siemens Healthineers
- Waygate Technologies
- Vidisco
- YXLON International
- The American Society for Nondestructive Testing (ASNT)
- Philips
- ZEISS
- Carestream
- Konica Minolta
- Varex Imaging Corporation
- Comet Group
- Waygate Technologies
- Evident (Olympus IMS)
- GE Aerospace
- Nikon Corporation
- Siemens
- ASTM International
- International Organization for Standardization (ISO)
- Bruker
- International Atomic Energy Agency
- Shimadzu Corporation
- Canon Inc.