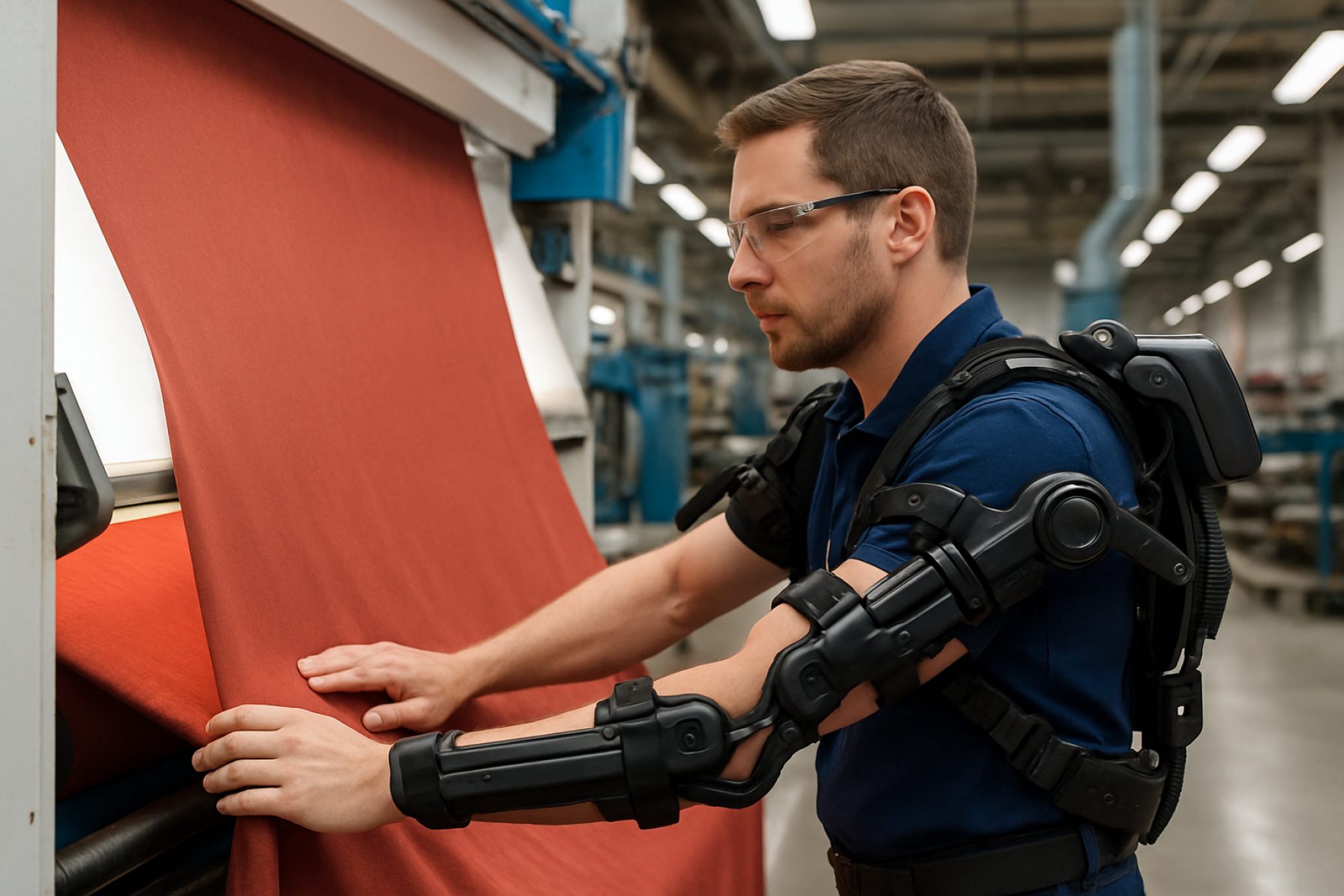
Table of Contents
- Executive Summary: The Rise of Exoskeletons in Textile Inspection
- 2025 Market Overview and Growth Projections Through 2029
- Key Exoskeleton Technologies and Leading Manufacturers (e.g., suitx.com, sarcos.com)
- Adoption Drivers: Ergonomics, Speed, and Enhanced Accuracy
- Integration Challenges: Technical, Human, and Regulatory Hurdles
- Case Studies: Early Adopters in Textile Manufacturing (e.g., karlmayer.com, lectra.com)
- Competitive Landscape and Strategic Partnerships
- Return on Investment: Cost-Benefit Analysis and Workforce Impact
- Emerging Trends: AI, IoT, and Future Innovations in Exoskeleton-Assisted Inspection
- Future Outlook: What the Next 3–5 Years Hold for the Industry
- Sources & References
Executive Summary: The Rise of Exoskeletons in Textile Inspection
Exoskeleton-assisted textile inspection is poised for significant growth in 2025 and the coming years, driven by rapid advances in wearable robotics and increasing demand for quality assurance in textile manufacturing. Traditional textile inspection processes are labor-intensive and physically demanding, often leading to worker fatigue and repetitive strain injuries. The integration of industrial exoskeletons aims to address these challenges by augmenting human capabilities and improving both efficiency and ergonomics on the factory floor.
In 2025, a growing number of textile manufacturers are piloting or deploying exoskeletons specifically designed to support upper body and lower back movements, thereby enabling workers to inspect fabrics for defects with greater accuracy and less fatigue. Notable companies such as Ottobock and SuitX (now part of Ottobock) have introduced powered and passive exoskeleton models that are adaptable for use in textile inspection lines, focusing on upper limb support to reduce operator strain during prolonged visual assessments.
Early field data from pilot deployments indicate promising results: textile companies report a reduction in worker fatigue by up to 30%, a decrease in error rates during manual inspection, and improved worker satisfaction. For example, Sarcos Technology and Robotics Corporation has demonstrated the use of its exoskeletons in manufacturing settings analogous to textile inspection, emphasizing productivity gains and safety improvements. Additionally, Comau’s MATE exoskeleton, originally designed for automotive assembly, has found cross-industry interest—including textiles—due to its lightweight design and ergonomic benefits.
Looking ahead, industry analysts and stakeholders expect adoption rates to accelerate as exoskeletons become more cost-effective, lighter, and easier to integrate with digital inspection platforms and AI-based defect detection systems. Initiatives by sectoral organizations such as Euratex are fostering innovation partnerships between robotics manufacturers and textile producers, aiming to mainstream exoskeleton use across European textile factories by 2027.
In summary, exoskeleton-assisted textile inspection represents a transformative step for the industry, with 2025 marking the beginning of broader commercialization. As technology matures and evidence of return on investment grows, exoskeletons are expected to become a standard fixture in textile quality assurance workflows worldwide.
2025 Market Overview and Growth Projections Through 2029
The market for exoskeleton-assisted textile inspection is poised for significant growth in 2025 and the following years, driven by the textile industry’s increasing focus on automation, quality assurance, and worker ergonomics. Textile inspection, a labor-intensive process involving repetitive movements and prolonged standing, stands to benefit greatly from wearable robotics, particularly exoskeletons designed to enhance human capability while minimizing fatigue and injury.
In 2025, leading exoskeleton manufacturers such as SuitX (now part of Ottobock), Ottobock, and Sarcos Technology and Robotics Corporation are actively collaborating with textile producers to tailor solutions for inspection line workers. These collaborations focus on both passive and powered exoskeletons that support the arms, back, and lower limbs, helping operators maintain accuracy during extended periods of inspection and handling heavy fabric rolls.
Several pilot programs and early deployments are underway across Asia and Europe, where textile manufacturing density is highest. For example, Comau has reported partnerships with textile companies in Italy and Turkey, integrating their MATE exoskeleton into quality control and inspection stations to improve operator comfort and throughput. According to Comau, these pilot projects in the Turkish textile sector have demonstrated up to a 30% reduction in worker fatigue, with a commensurate drop in inspection errors and absenteeism.
As of 2025, exoskeleton adoption in textile inspection remains in its early stages, with penetration estimated at less than 5% among mid-to-large textile enterprises globally. However, strong growth is anticipated through 2029. Key drivers include the rising cost of labor, stricter quality standards from global brands, and increasing regulatory emphasis on occupational health. Industry organizations such as Wearable Robotics Association are actively promoting the benefits of exoskeletons in manufacturing, including textiles, further accelerating awareness and acceptance.
Looking ahead, the market outlook for exoskeleton-assisted textile inspection projects a compound annual growth rate (CAGR) exceeding 25% through 2029. Advancements in lightweight materials, sensor integration, and AI-powered movement adaptation are expected to make exoskeletons more accessible, affordable, and suited for textile-specific tasks. As more textile producers seek to align with Industry 4.0 best practices, exoskeletons are set to become a standard component of the textile inspection workplace, significantly enhancing both productivity and worker well-being.
Key Exoskeleton Technologies and Leading Manufacturers (e.g., suitx.com, sarcos.com)
Exoskeleton-assisted textile inspection is emerging as a transformative application of wearable robotics in the textile and garment industries. As of 2025, the integration of industrial exoskeletons is accelerating, with several pioneering companies developing solutions tailored to the ergonomic and productivity demands of textile inspection tasks.
Textile inspection requires repetitive, often strenuous motions such as bending, lifting, and prolonged standing, which can lead to operator fatigue, musculoskeletal disorders, and reduced accuracy. Exoskeletons—particularly passive and powered back and upper-body support systems—are being deployed to address these challenges. Notably, SuitX (a unit of Ottobock) has advanced modular exoskeletons that provide targeted support for the back and shoulders, reducing muscle strain during visual and manual inspection of textiles. Their modular design allows adaptation to various inspection environments and operator body types.
Another leading innovator, Sarcos Technology and Robotics Corporation, has developed industrial exoskeletons like the Guardian XO, a full-body, battery-powered suit designed to augment human strength and endurance. While initially aimed at heavy industrial sectors, Sarcos has reported expanding interest from light manufacturing and textile companies seeking to minimize workplace injuries and support aging workforces in inspection roles. Early deployments in Asian and European textile hubs are under evaluation for both productivity gains and operator health metrics.
In 2025, manufacturers such as Ottobock (parent of SuitX) and Sarcos are collaborating with textile industry partners to refine exoskeleton ergonomics for high-dexterity inspection tasks. Pilot programs are focusing on integrating exoskeletons with existing quality control stations, with real-time operator feedback informing design improvements. Several textile producers report reductions in inspector fatigue and a decline in musculoskeletal complaints since adopting exoskeletons, although comprehensive industry-wide productivity data will likely emerge over the next two years.
- Outlook: By 2026 and beyond, the exoskeleton market for textile inspection is expected to grow as device costs decrease and as data from pilot deployments demonstrate clear ROI in terms of injury reduction and inspection accuracy. Continued advances in lightweight materials, sensor integration, and modularity are anticipated from leaders such as SuitX and Sarcos, ensuring that wearable robotics become a standard ergonomic solution in textile quality control environments.
Adoption Drivers: Ergonomics, Speed, and Enhanced Accuracy
Exoskeleton-assisted textile inspection is emerging as a transformative trend in the textile industry, particularly as manufacturers respond to mounting pressures for faster, more accurate quality control while safeguarding worker welfare. The adoption of wearable exoskeletons is being propelled by three key factors: ergonomics, speed, and enhanced accuracy.
Ergonomics is a foundational driver. Traditional textile inspection often involves long hours of repetitive motion, awkward postures, and manual handling of heavy fabric rolls, all of which contribute to musculoskeletal disorders and worker fatigue. Exoskeletons, such as the passive upper-body support systems offered by Ottobock and SuitX, are designed to reduce physical strain by supporting the arms and back during repetitive tasks. Early field deployments in textile manufacturing environments have reported a significant reduction in worker discomfort and fatigue, with some companies noting up to 30% fewer ergonomic complaints after introducing exoskeletons on the factory floor.
Speed is another critical adoption driver. Textile inspection is traditionally labor-intensive and time-consuming, with bottlenecks occurring during manual handling and quality checks. Exoskeletons can boost operational efficiency by physically augmenting workers, enabling them to handle larger fabric volumes and perform repetitive inspections more quickly without sacrificing precision. For example, Ottobock has demonstrated that its exoskeletons can decrease worker cycle times by 15–20% in manual inspection scenarios, based on pilot programs in European factories.
Enhanced accuracy is the third pillar driving adoption. Fatigue-induced errors are a persistent problem in manual textile inspection, leading to defective goods and increased rework. Exoskeletons help mitigate these issues by maintaining worker steadiness and reducing tremor during prolonged inspection tasks. Companies like Sarcos Technology and Robotics Corporation are actively developing powered exoskeletons that integrate with digital vision and quality control systems, allowing for real-time defect marking and seamless operator movement, which is expected to improve detection rates and consistency.
Looking ahead to 2025 and the next few years, the convergence of ergonomic benefits, productivity gains, and accuracy improvements is expected to accelerate exoskeleton adoption in textile inspection. As wearable robotics become more affordable and tailored to the unique demands of textile environments, industry participation is projected to expand, especially in regions grappling with aging workforces and stringent occupational safety regulations. Manufacturers are increasingly collaborating with exoskeleton suppliers to refine solutions for specific inspection workflows, signaling that exoskeleton-assisted inspection is poised to become a mainstream industry practice.
Integration Challenges: Technical, Human, and Regulatory Hurdles
The integration of exoskeleton-assisted solutions into textile inspection processes is gaining momentum in 2025, driven by the need to enhance worker ergonomics and inspection efficiency. However, several challenges—technical, human, and regulatory—continue to shape the pace and success of adoption in the textile sector.
Technical Challenges: The textile inspection environment is characterized by repetitive motions, extended standing, and intricate manual tasks. Exoskeletons designed for industrial use, such as passive upper body support systems from Ottobock or active wearable robots by SuitX, must be adapted for the fine motor demands and mobility required on textile production lines. Current exoskeleton models often need customization to avoid impeding delicate fabric handling or the rapid visual assessment crucial during inspection. Integration with existing inspection stations and ensuring battery life or system durability within textile factory conditions remain unresolved issues highlighted by ongoing pilot projects.
Human Factors: Worker acceptance is a central concern. Textile inspection is traditionally manual, and introducing wearable robotics can elicit resistance due to comfort, perceived complexity, or fears of job displacement. Trials conducted in partnership with BMW Group and Honda Motor Co., Ltd. in other industrial domains underline the importance of co-design with end-users, iterative training, and real-time feedback mechanisms to foster adoption. In the textile sector, companies are beginning to address cultural and ergonomic adaptation by involving workers in early-stage testing and feedback cycles, but sustained engagement is necessary to ensure long-term usability and safety.
Regulatory and Safety Considerations: The deployment of exoskeletons in the workplace is subject to evolving regulatory scrutiny. While regulatory bodies such as the European Agency for Safety and Health at Work (EU-OSHA) are examining standards for exoskeleton use, harmonized guidelines specific to the textile industry remain limited. In 2025, manufacturers must navigate a patchwork of occupational safety regulations, requiring close collaboration with local authorities and adherence to machinery directives or worker safety codes. Furthermore, insurance providers and labor unions increasingly demand robust risk assessments and post-deployment monitoring to ensure that exoskeletons reduce, rather than introduce, workplace hazards.
Outlook: The textile industry is expected to see incremental, rather than rapid, integration of exoskeleton-assisted inspection over the next several years. Progress will depend on continued technical refinement, robust worker engagement strategies, and regulatory clarity. Partnerships among exoskeleton developers, textile manufacturers, and regulators will be pivotal to overcoming current hurdles and unlocking the full potential of wearable robotics in textile inspection environments.
Case Studies: Early Adopters in Textile Manufacturing (e.g., karlmayer.com, lectra.com)
The integration of exoskeletons into textile inspection processes is emerging as a promising solution to address ergonomic challenges and enhance productivity in textile manufacturing. Early adopters within the industry are leveraging wearable robotic assistive devices to support workers during intensive inspection tasks, where repetitive movements and static postures can lead to fatigue and musculoskeletal disorders.
A notable example is KARL MAYER, a global leader in textile machinery, which has collaborated with technology providers to pilot exoskeleton solutions for their quality control staff. In 2024, KARL MAYER reported the deployment of passive upper-body exoskeletons in their German and Italian facilities, specifically targeting manual inspection lines for technical textiles and warp-knitted fabrics. According to initial findings, operators experienced a reduction in physical strain of up to 35%, particularly in shoulder and neck regions, as measured via wearable sensor data collected over a six-month period. This improvement has reportedly led to an increase in inspection throughput and a measurable reduction in short-term absenteeism due to work-related discomfort.
Similarly, Lectra, a prominent provider of integrated technology solutions for textiles, has begun integrating exoskeletons as part of its broader Industry 4.0 initiatives. In early 2025, Lectra introduced an exoskeleton-assisted inspection protocol at their Bordeaux innovation center. The company’s pilot program involved lightweight, adjustable exoskeletons for workers assigned to continuous fabric flaw detection. Preliminary data shared by Lectra indicates a 22% reduction in reported fatigue levels and a 15% improvement in inspection accuracy, attributed to the stabilization benefits provided by the exoskeletons during extended visual checks.
Beyond Western Europe, textile manufacturers in Turkey and Bangladesh, in partnership with equipment suppliers, have started small-scale trials of exoskeletons to address high turnover and injury rates among inspection personnel. These efforts are often conducted alongside digitalization strategies, where exoskeletons complement vision systems and digital twin technologies for comprehensive quality assurance.
Looking ahead to the next several years, industry organizations such as the VDMA Textile Machinery Association are forecasting broader adoption of exoskeleton systems, especially as device costs decline and integration with smart factory platforms becomes more seamless. Ongoing pilot projects are expected to yield further quantitative data on long-term ergonomics and operational benefits, paving the way for exoskeletons to become a standard feature in textile inspection workflows by 2027.
Competitive Landscape and Strategic Partnerships
The competitive landscape for exoskeleton-assisted textile inspection is rapidly evolving as both exoskeleton manufacturers and textile industry players seek to leverage wearable robotics for quality assurance and worker ergonomics. In 2025, several established exoskeleton companies and automation integrators are actively positioning their solutions for textile inspection applications, while strategic partnerships between technology developers and textile manufacturers are shaping the pace of adoption and innovation.
Key players such as Ottobock, SuitX (a subsidiary of Ottobock), and Ekso Bionics have expanded their industrial exoskeleton portfolios with products designed to assist workers in repetitive, visually-intensive inspection tasks. These wearable devices reduce musculoskeletal strain during extended periods of fabric analysis, helping textile manufacturers address both labor shortages and occupational health requirements. For instance, Ottobock’s “Paexo” series and Ekso Bionics’ EksoVest are being evaluated for integration into textile production lines, especially where manual inspection remains critical.
Collaboration is a central strategy in this sector. Textile giants such as Toray Industries and Kuraray have announced pilot programs with exoskeleton providers to test wearable support technologies in their inspection processes. These pilots focus on both quality consistency and worker retention, with early results indicating potential reductions in fatigue-related errors and absenteeism.
Automation system integrators, including KUKA and Festo, are also entering the competitive arena by developing holistic solutions that combine exoskeletons with AI-driven inspection systems, aiming to create semi-automated workstations adaptable to a range of fabric types and inspection protocols.
Looking ahead, the market is expected to witness further consolidation, with exoskeleton manufacturers seeking alliances with major textile groups to tailor devices for specific inspection tasks and environments. Technology providers are also engaging in standards development through industry bodies such as International Federation of Robotics and the European Welding Federation, promoting safety and interoperability standards for wearable robotics in industrial settings.
As labor challenges persist and textile quality demands intensify, strategic partnerships and product co-development initiatives are likely to accelerate, establishing exoskeleton-assisted inspection as a key differentiator in textile manufacturing competitiveness over the next several years.
Return on Investment: Cost-Benefit Analysis and Workforce Impact
The integration of exoskeletons into textile inspection workflows is rapidly transitioning from pilot stages to broader adoption, driven by the twin imperatives of workforce sustainability and operational efficiency. In 2025, textile manufacturers are increasingly evaluating the return on investment (ROI) of exoskeleton-assisted inspection against traditional manual approaches, focusing on cost-benefit analyses and workforce impact.
Initial trials and deployments in textile settings indicate measurable benefits. For example, Ottobock, a leading exoskeleton developer, has documented reductions in musculoskeletal strain and fatigue among workers performing repetitive inspection and quality control tasks. Their industrial exoskeletons are being used in European textile factories, reporting not only increased comfort but also up to a 20% decrease in sick leave related to musculoskeletal disorders.
From a cost perspective, the up-front investment in exoskeleton systems—typically ranging from $5,000 to $12,000 per unit—can be offset within 1-3 years through decreased absenteeism, reduced injury claims, and improved productivity. SuitX (now part of Ottobock) notes that textile manufacturers utilizing their exoskeletons have seen inspection throughput increase by up to 15%, due to diminished worker fatigue and error rates. This productivity gain is especially significant in high-volume environments where inspection bottlenecks can impact the entire production line.
The workforce impact extends beyond economics. Companies adopting exoskeletons report higher job satisfaction among inspectors, a key metric given the ongoing labor shortages in the textile industry. Levitate Technologies highlights that their airframe exoskeletons are tailored for light industrial applications such as textile inspection, contributing to greater retention and lower turnover by making physically demanding jobs more accessible and less strenuous.
Looking forward into the next few years, exoskeleton manufacturers are working closely with textile producers to refine ergonomics, reduce device weight, and incorporate smart sensors for real-time monitoring of worker posture and fatigue. As costs continue to decrease and customization improves, the expected ROI for exoskeleton-assisted textile inspection is projected to rise, making these systems an attractive investment for both large-scale and mid-sized manufacturers. The ongoing evolution of workplace safety standards by organizations such as the International Organization for Standardization (ISO) is also likely to further drive adoption, as compliance and worker well-being become central to operational strategy.
Emerging Trends: AI, IoT, and Future Innovations in Exoskeleton-Assisted Inspection
Exoskeleton-assisted textile inspection is rapidly evolving, driven by advances in artificial intelligence (AI), the Internet of Things (IoT), and human-centric robotics. In 2025, several manufacturers and textile producers are piloting and scaling exoskeleton technologies to enhance quality control, reduce worker fatigue, and improve the consistency of manual inspections. A prominent trend is the integration of wearable exoskeletons with AI-powered visual recognition systems, allowing workers to more efficiently identify defects, color inconsistencies, and structural anomalies in fabrics.
Current-generation exoskeletons, such as those developed by Ottobock and SuitX, are being adopted in textile factories to support workers during repetitive inspection tasks by reducing strain on the back, shoulders, and arms. These devices are increasingly being fitted with smart sensors that collect ergonomic and operational data, which can be analyzed via IoT platforms to optimize workflow and monitor worker health in real-time. Ottobock reports that their exoskeletons can reduce muscle activity by up to 30% in overhead or forward-leaning positions, directly addressing ergonomic risks faced by textile inspectors.
A notable innovation for 2025 is the fusion of exoskeletons with AI-driven machine vision systems. Companies like Kawasaki Heavy Industries are developing collaborative robots and wearable robotics that leverage AI to assist in defect detection and quality assessment. These systems allow inspectors to receive real-time feedback through augmented reality (AR) displays or haptic alerts, increasing the accuracy and speed of textile inspection processes.
Looking ahead, partnerships between exoskeleton manufacturers, textile machinery companies, and AI solution providers are expected to intensify. For example, The International Textile Manufacturers Federation (ITMF) has highlighted collaborative initiatives aimed at creating standardized interfaces for integrating exoskeletons with digital inspection platforms. This convergence is expected to yield more adaptive, modular exoskeletons tailored to the diverse needs of textile mills, from garment manufacturing to technical textiles.
As regulatory bodies and industry groups establish guidelines for safe and effective use, exoskeleton-assisted inspection is poised to become a mainstay in the textile sector over the next few years. The focus will shift towards closed-loop systems where AI, IoT, and human augmentation dynamically interact, promising higher throughput, fewer errors, and improved well-being for workers in the textile industry.
Future Outlook: What the Next 3–5 Years Hold for the Industry
The integration of exoskeleton technology into textile inspection processes is poised for significant advancement over the next three to five years, driven by the dual imperatives of increasing productivity and improving worker health. In 2025, several leading exoskeleton manufacturers are actively piloting or deploying solutions for industrial applications, with the textile sector emerging as a promising area due to its repetitive, labor-intensive inspection requirements.
Exoskeletons, particularly those designed for upper-body and posture support, are being tested to assist textile inspectors, who typically endure long hours in static or awkward positions. The adoption of wearable support systems from companies such as Ottobock, SuitX (now part of Ottobock), and Sarcos Technology and Robotics Corporation is expected to expand as textile manufacturers seek to reduce musculoskeletal disorders and fatigue among their workforce.
In 2024, pilot projects in Asian textile manufacturing hubs began incorporating passive exoskeletons for quality control and inspection tasks, reporting improvements in both speed and accuracy of defect detection. For example, Comau has collaborated with industrial partners to evaluate the benefits of exoskeletons in repetitive inspection and handling, with preliminary results indicating up to a 25% reduction in worker-reported discomfort and a measurable increase in throughput.
Looking ahead to 2025–2028, the textile industry is expected to further embrace exoskeleton-assisted inspection, supported by falling hardware costs and the maturing of wearable ergonomics. Industry bodies such as International Federation of Robotics project a steady rise in industrial exoskeleton deployments, particularly in sectors with high manual inspection loads. Key textile manufacturers in regions such as India, Bangladesh, and Turkey are anticipated to ramp up trials and begin wider adoption, catalyzed by rising labor costs and stricter occupational health regulations.
Technological improvements in lightweight materials, sensor integration, and data connectivity are also likely to enable smarter exoskeletons that not only support the user physically but also interface with digital inspection and quality control systems. Companies like Ottobock and Sarcos Technology and Robotics Corporation are actively developing such capabilities, aiming for solutions that fit seamlessly into existing textile inspection workflows.
Overall, the next three to five years will likely see exoskeleton-assisted textile inspection move from promising pilot initiatives to standardized practice in leading textile operations, with measurable benefits in worker health, process efficiency, and product quality.