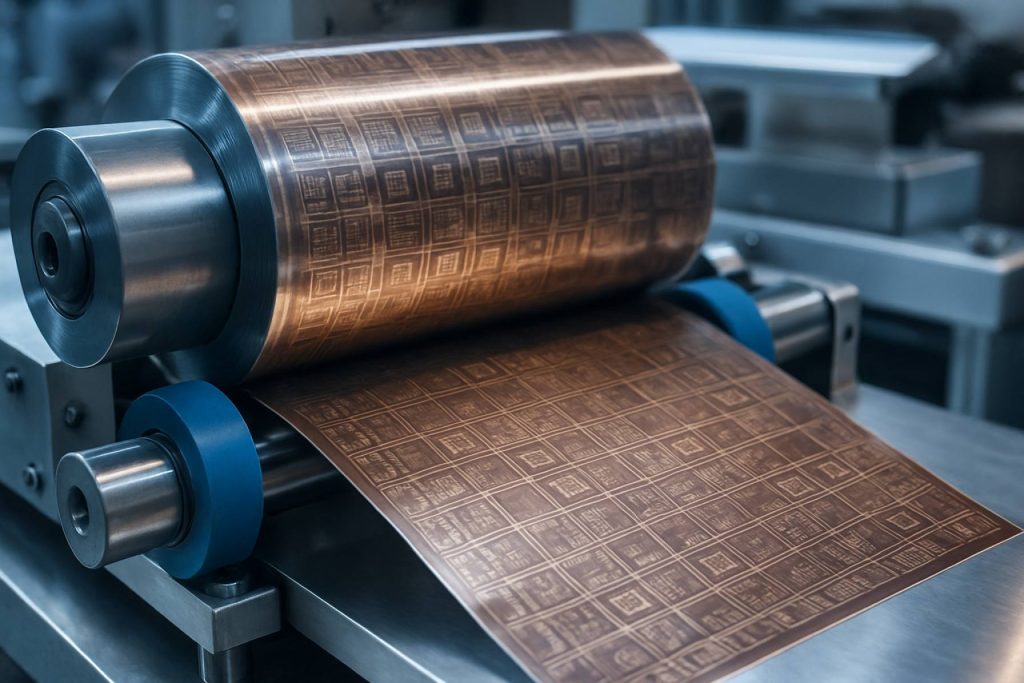
Roll-to-Roll Lithography Equipment Manufacturing in 2025: Unveiling the Next Wave of High-Speed, Scalable Production. Explore How Advanced Lithography is Shaping the Future of Flexible Electronics and Beyond.
- Executive Summary: Key Trends and 2025 Market Snapshot
- Technology Overview: Principles of Roll-to-Roll Lithography
- Major Manufacturers and Industry Players (e.g., asml.com, nikon.com, canon.com)
- Current Market Size and 2025–2030 Growth Forecasts
- Emerging Applications: Flexible Displays, Solar Cells, and IoT Devices
- Innovation Pipeline: Recent Advances and R&D Initiatives
- Competitive Landscape and Strategic Partnerships
- Supply Chain Dynamics and Equipment Integration Challenges
- Regulatory Environment and Industry Standards (e.g., sematech.org, ieee.org)
- Future Outlook: Opportunities, Risks, and Strategic Recommendations
- Sources & References
Executive Summary: Key Trends and 2025 Market Snapshot
The roll-to-roll (R2R) lithography equipment manufacturing sector is entering 2025 with strong momentum, driven by surging demand for flexible electronics, advanced packaging, and cost-effective large-area patterning solutions. R2R lithography, which enables continuous processing of flexible substrates, is increasingly favored for applications in flexible displays, wearable sensors, photovoltaics, and printed electronics. The technology’s scalability and compatibility with high-throughput manufacturing are key factors underpinning its adoption across multiple industries.
In 2025, the market is characterized by a growing number of collaborations between equipment manufacturers, material suppliers, and end-users to accelerate innovation and address technical challenges such as alignment precision, defect control, and integration with other R2R processes. Leading equipment manufacturers, including SÜSS MicroTec and Meyer Burger Technology AG, are expanding their R2R lithography portfolios, focusing on both nanoimprint and photolithography systems. These companies are investing in modular platforms that support rapid changeovers and customization for diverse substrate types and process requirements.
The sector is also witnessing increased activity from Asian manufacturers, particularly in Japan and South Korea, where companies such as Toray Industries and Samsung Electronics are leveraging R2R lithography for next-generation display and semiconductor applications. These firms are not only developing proprietary R2R equipment but also collaborating with global partners to enhance process integration and yield.
Sustainability and cost reduction remain central themes in 2025. R2R lithography’s ability to minimize material waste and energy consumption aligns with the broader industry push toward greener manufacturing. Equipment makers are responding by introducing systems with improved process control, lower defect rates, and compatibility with recyclable substrates. For example, SÜSS MicroTec has highlighted the environmental benefits of its R2R platforms in recent product communications.
Looking ahead, the outlook for R2R lithography equipment manufacturing is robust. Market participants anticipate double-digit annual growth rates through the next several years, fueled by the proliferation of flexible and wearable devices, the expansion of IoT, and the ongoing shift toward additive and hybrid manufacturing paradigms. Strategic investments in R&D, automation, and global supply chain partnerships are expected to further accelerate technology adoption and market expansion.
Technology Overview: Principles of Roll-to-Roll Lithography
Roll-to-roll (R2R) lithography is a high-throughput manufacturing process that enables the continuous patterning of flexible substrates, such as plastic films or metal foils, by unwinding them from a feed roll, processing them through various lithographic steps, and rewinding them onto a take-up roll. The core principle involves synchronizing substrate movement with precise pattern transfer, typically using techniques such as nanoimprint lithography, gravure, flexography, or photolithography. In 2025, the manufacturing of R2R lithography equipment is characterized by a focus on scalability, alignment accuracy, and integration with advanced materials and digital controls.
Key equipment manufacturers in this sector include NIL Technology, which specializes in nanoimprint lithography systems for both R2R and sheet-based processes, and KROENERT, a German company with a long history in web coating and printing machinery, now offering R2R platforms for micro- and nano-patterning. Meyer Burger Technology AG is also active in the field, providing R2R solutions for the photovoltaic and electronics industries, focusing on high-precision coating and patterning.
The equipment typically consists of several integrated modules: unwinding and rewinding stations, web tension control, cleaning units, coating or resist application, exposure or imprint modules, development and etching stations, and in-line inspection systems. In 2025, manufacturers are increasingly incorporating machine vision and AI-driven feedback loops to ensure sub-micron alignment and defect detection, responding to the demand for higher yields in applications such as flexible displays, printed electronics, and advanced packaging.
Recent advances include the adoption of UV-curable resists for faster processing, and the use of roll-to-roll nanoimprint lithography (R2R NIL) for sub-100 nm feature sizes. Companies like NIL Technology are developing turnkey R2R NIL systems capable of continuous patterning at web speeds exceeding 10 meters per minute, with demonstrated uniformity suitable for commercial production of optical films and sensors. Meanwhile, KROENERT is integrating modular platforms that allow rapid switching between different lithographic techniques, catering to the growing diversity of flexible electronics applications.
Looking ahead, the outlook for R2R lithography equipment manufacturing is positive, driven by the expansion of markets such as flexible OLED displays, wearable sensors, and large-area photonic devices. Equipment makers are expected to further enhance automation, reduce material waste, and enable even finer patterning resolutions. Strategic collaborations between equipment suppliers and material developers are anticipated to accelerate the commercialization of next-generation R2R lithography systems, positioning the technology as a cornerstone of future high-volume, low-cost micro- and nano-fabrication.
Major Manufacturers and Industry Players (e.g., asml.com, nikon.com, canon.com)
The roll-to-roll (R2R) lithography equipment manufacturing sector is experiencing notable growth and diversification as of 2025, driven by increasing demand for flexible electronics, advanced packaging, and large-area micro- and nano-patterning. Unlike traditional wafer-based lithography, R2R systems enable continuous processing of flexible substrates, making them essential for high-throughput, cost-effective production of devices such as flexible displays, solar cells, and sensors.
While established semiconductor lithography giants like ASML Holding, Nikon Corporation, and Canon Inc. dominate the market for wafer-based photolithography, their direct involvement in R2R lithography equipment is limited. Instead, the R2R segment is characterized by a mix of specialized equipment manufacturers, technology developers, and collaborative ventures between research institutions and industry.
Key industry players in R2R lithography equipment include KROENERT GmbH & Co KG, a German company with a long-standing reputation in web coating and printing machinery, which has expanded its portfolio to include R2R nanoimprint and photolithography solutions. Meyer Burger Technology AG, based in Switzerland, is another significant manufacturer, particularly in the context of R2R equipment for photovoltaic and micro-patterning applications. Roland DG Corporation from Japan, known for digital printing and advanced manufacturing systems, has also made strategic moves into R2R processing technologies.
In the United States, MITRE Corporation and Oak Ridge National Laboratory have played pivotal roles in advancing R2R lithography through public-private partnerships and technology transfer initiatives, fostering the commercialization of new equipment platforms. Additionally, 3M Company leverages its expertise in materials and web handling to support R2R lithography processes, particularly for flexible electronics and advanced films.
The outlook for the next few years suggests continued expansion, with increasing investment in R2R lithography equipment manufacturing driven by the proliferation of flexible and wearable devices, as well as the push for sustainable, large-area electronics. Industry collaborations and consortia, such as those involving imec and Fraunhofer Society, are expected to accelerate innovation and standardization in R2R lithography platforms. As the technology matures, further integration of automation, in-line metrology, and AI-driven process control is anticipated, positioning R2R lithography as a cornerstone of next-generation electronics manufacturing.
Current Market Size and 2025–2030 Growth Forecasts
The roll-to-roll (R2R) lithography equipment manufacturing sector is experiencing robust growth, driven by expanding applications in flexible electronics, advanced packaging, photovoltaics, and display technologies. As of 2025, the global market size for R2R lithography equipment is estimated to be in the low single-digit billions (USD), with leading manufacturers reporting increased order volumes and capacity expansions. The sector is characterized by a mix of established equipment giants and specialized innovators, each contributing to the rapid evolution of R2R processes.
Key players in the R2R lithography equipment market include Mitsubishi Electric Corporation, which has developed advanced web handling and precision coating systems, and Tokyo Ohka Kogyo Co., Ltd. (TOK), a major supplier of lithography materials and process equipment. Roland DG Corporation is also active in the sector, leveraging its expertise in digital printing and precision machinery for R2R applications. In Europe, Meyer Burger Technology AG is notable for its R2R solutions in the photovoltaic industry, while Coatema Coating Machinery GmbH specializes in modular R2R pilot and production lines for printed electronics and microfabrication.
The demand for R2R lithography equipment is being propelled by the proliferation of flexible and wearable devices, the adoption of advanced driver-assistance systems (ADAS) in automotive electronics, and the scaling of thin-film solar cell production. Industry sources report that equipment utilization rates are at record highs, with lead times for new systems extending into late 2026 for some manufacturers. The integration of R2R lithography with nanoimprint and photolithography techniques is further expanding the addressable market, enabling high-throughput, cost-effective patterning at sub-micron resolutions.
Looking ahead to 2030, the R2R lithography equipment market is forecast to grow at a compound annual growth rate (CAGR) in the high single digits, outpacing many traditional semiconductor and display equipment segments. This growth is underpinned by ongoing investments in next-generation flexible displays, organic light-emitting diode (OLED) panels, and printed sensors. Strategic partnerships between equipment makers and material suppliers, such as those seen between Tokyo Ohka Kogyo Co., Ltd. and leading display manufacturers, are expected to accelerate innovation and commercialization cycles.
- 2025 market size: Estimated low single-digit billions (USD), with strong order backlogs.
- Key growth drivers: Flexible electronics, photovoltaics, advanced packaging, and automotive applications.
- Leading companies: Mitsubishi Electric Corporation, Tokyo Ohka Kogyo Co., Ltd., Roland DG Corporation, Meyer Burger Technology AG, Coatema Coating Machinery GmbH.
- 2030 outlook: High single-digit CAGR, driven by new applications and technology integration.
Emerging Applications: Flexible Displays, Solar Cells, and IoT Devices
Roll-to-roll (R2R) lithography equipment manufacturing is experiencing significant momentum in 2025, driven by the rapid expansion of emerging applications such as flexible displays, advanced solar cells, and Internet of Things (IoT) devices. The R2R process, which enables continuous patterning of flexible substrates, is increasingly recognized as a key enabler for high-throughput, cost-effective production of next-generation electronics.
In the flexible display sector, R2R lithography is crucial for fabricating organic light-emitting diode (OLED) and micro-LED panels on plastic substrates. Major display manufacturers are investing in R2R-compatible equipment to scale up production and reduce costs. For example, Samsung Electronics and LG Display have both announced initiatives to integrate R2R processes into their flexible display manufacturing lines, aiming to meet growing demand for foldable smartphones, rollable TVs, and wearable devices. Equipment suppliers are responding by developing advanced R2R lithography systems with higher resolution and improved registration accuracy, tailored for the stringent requirements of display fabrication.
The photovoltaic industry is another major driver, with R2R lithography enabling the mass production of flexible and lightweight solar cells. Companies such as First Solar and Heliatek are leveraging R2R equipment to manufacture thin-film and organic photovoltaic modules, which are increasingly used in building-integrated photovoltaics (BIPV) and portable power solutions. The scalability and material efficiency of R2R processes are expected to further reduce the levelized cost of electricity (LCOE) from solar, supporting broader adoption in both developed and emerging markets.
For IoT devices, the demand for flexible, lightweight, and low-cost sensors and circuits is accelerating the adoption of R2R lithography. Manufacturers such as PARC, a Xerox Company and Jabil are actively developing R2R-compatible electronics manufacturing platforms, enabling the integration of printed sensors, antennas, and batteries into smart labels, wearables, and industrial monitoring systems. The ability to produce large volumes of flexible electronics at low cost is seen as a critical factor in scaling IoT deployments across sectors such as logistics, healthcare, and smart infrastructure.
Looking ahead, the outlook for R2R lithography equipment manufacturing remains robust. Industry analysts anticipate continued investment in R&D to improve throughput, resolution, and process integration, with a focus on hybrid systems that combine R2R lithography with other patterning and deposition techniques. As end-user applications mature and demand for flexible, high-performance electronics grows, R2R equipment manufacturers are poised to play a pivotal role in shaping the future of advanced manufacturing.
Innovation Pipeline: Recent Advances and R&D Initiatives
The roll-to-roll (R2R) lithography equipment sector is experiencing a surge in innovation, driven by the demand for high-throughput, cost-effective manufacturing of flexible electronics, displays, and advanced packaging. As of 2025, leading equipment manufacturers and research institutions are intensifying their R&D efforts to address challenges such as resolution limits, process integration, and material compatibility.
One of the most significant advances in recent years is the development of high-resolution R2R nanoimprint lithography (NIL) systems. Companies like NIL Technology are at the forefront, offering equipment capable of sub-100 nm patterning on flexible substrates. Their innovations focus on improving stamp durability, alignment accuracy, and throughput, which are critical for scaling up production of flexible displays and optical components.
Another key player, Rolleto, specializes in R2R photolithography systems tailored for printed electronics and sensor applications. Their recent R&D initiatives include integrating advanced UV-LED exposure modules and real-time process monitoring, enabling higher yields and reduced defect rates. These improvements are essential for applications such as flexible printed circuit boards and wearable devices.
In the materials domain, collaborations between equipment manufacturers and chemical suppliers are accelerating the development of new resists and functional inks compatible with R2R processes. For example, DSM is working with equipment makers to optimize UV-curable materials that enhance pattern fidelity and process speed, supporting the mass production of micro-optics and anti-counterfeiting features.
Research institutions are also playing a pivotal role. The imec research center is actively engaged in R2R lithography research, focusing on hybrid integration of NIL and photolithography for next-generation flexible electronics. Their pilot lines are testing new process flows that combine high-resolution patterning with scalable manufacturing, aiming to bridge the gap between lab-scale innovation and industrial adoption.
Looking ahead, the innovation pipeline is expected to deliver further advances in automation, defect inspection, and multi-layer alignment. The integration of artificial intelligence for process control and predictive maintenance is a growing trend, with several equipment makers investing in smart manufacturing solutions. As the market for flexible and wearable electronics expands, R2R lithography equipment manufacturers are poised to play a central role in enabling the next wave of electronic device miniaturization and functionality.
Competitive Landscape and Strategic Partnerships
The competitive landscape of roll-to-roll (R2R) lithography equipment manufacturing in 2025 is characterized by a mix of established industrial machinery giants and specialized technology firms, each leveraging strategic partnerships to accelerate innovation and market reach. The sector is driven by the growing demand for flexible electronics, advanced packaging, and large-area microfabrication, with manufacturers focusing on high-throughput, precision, and cost-effective solutions.
Key players in the R2R lithography equipment market include Mitsubishi Electric Corporation, Tokyo Electron Limited, and KROENERT GmbH & Co KG. Mitsubishi Electric Corporation has expanded its portfolio to include advanced R2R systems for micro-patterning and flexible substrate processing, leveraging its expertise in automation and precision engineering. Tokyo Electron Limited, a global leader in semiconductor production equipment, has invested in R2R lithography as part of its strategy to address the growing flexible electronics and display markets. KROENERT GmbH & Co KG, a German company with a long history in coating and laminating machinery, has developed modular R2R platforms that integrate lithographic patterning for applications in printed electronics and photovoltaics.
Strategic partnerships are a defining feature of the industry in 2025. Equipment manufacturers are collaborating with material suppliers, research institutes, and end-users to co-develop tailored solutions. For example, KROENERT GmbH & Co KG has partnered with specialty chemical companies to optimize photoresist formulations for high-speed R2R processing. Similarly, Mitsubishi Electric Corporation has engaged in joint development projects with leading display manufacturers to refine R2R lithography for next-generation OLED and micro-LED panels.
Emerging players and startups are also contributing to the competitive dynamics by introducing novel R2R lithography techniques, such as nanoimprint and direct-write processes. These companies often collaborate with universities and public research organizations to access advanced know-how and pilot-scale facilities. The presence of consortia and industry alliances, particularly in Asia and Europe, is fostering pre-competitive research and standardization efforts, which are expected to accelerate commercialization in the coming years.
Looking ahead, the competitive landscape is likely to intensify as demand for flexible, large-area, and cost-efficient microfabrication grows across sectors such as wearables, IoT devices, and energy harvesting. Companies that can offer integrated, scalable, and customizable R2R lithography solutions—while maintaining strong partnerships across the value chain—are expected to capture significant market share through 2025 and beyond.
Supply Chain Dynamics and Equipment Integration Challenges
The roll-to-roll (R2R) lithography equipment manufacturing sector in 2025 is characterized by both rapid innovation and significant supply chain complexities. As demand for flexible electronics, advanced packaging, and large-area microfabrication grows, manufacturers are under pressure to deliver higher throughput, precision, and integration capabilities. The supply chain for R2R lithography equipment is inherently global, involving specialized suppliers of precision rollers, high-performance UV sources, advanced photomasks, and motion control systems.
Key players such as Meyer Burger Technology AG and Tokyo Ohka Kogyo Co., Ltd. (TOK) are actively expanding their R2R lithography portfolios, focusing on both equipment and process materials. Meyer Burger Technology AG is recognized for its expertise in precision coating and printing systems, which are integral to R2R lithography lines. Tokyo Ohka Kogyo Co., Ltd. supplies advanced photoresists and process chemicals, and has invested in R2R-compatible materials to support next-generation device fabrication.
Supply chain disruptions, particularly in the procurement of high-precision optical components and specialty polymers, have been a recurring challenge. The COVID-19 pandemic and subsequent geopolitical tensions have exposed vulnerabilities in sourcing critical subsystems, such as high-uniformity UV lamps and custom-engineered web handling modules. In response, equipment manufacturers are increasingly seeking to localize key supply nodes and establish dual sourcing strategies to mitigate risks.
Integration challenges are also prominent, as R2R lithography systems must interface seamlessly with upstream and downstream processes—such as substrate cleaning, coating, and metrology. The trend toward modular equipment design is gaining traction, allowing manufacturers to offer configurable platforms that can be tailored to specific customer requirements. Companies like Meyer Burger Technology AG are developing modular R2R lithography solutions that facilitate easier integration with existing production lines, reducing downtime and accelerating time-to-market for new products.
Looking ahead, the outlook for 2025 and beyond suggests continued investment in automation, in-line inspection, and digital process control to enhance yield and reduce operational costs. Industry collaborations are expected to intensify, with equipment makers partnering with material suppliers and end-users to co-develop solutions that address both technical and supply chain bottlenecks. As the sector matures, the ability to rapidly adapt equipment designs and supply strategies will be a key differentiator for leading R2R lithography equipment manufacturers.
Regulatory Environment and Industry Standards (e.g., sematech.org, ieee.org)
The regulatory environment and industry standards for roll-to-roll (R2R) lithography equipment manufacturing are evolving rapidly as the technology matures and finds broader adoption in flexible electronics, photovoltaics, and advanced packaging. In 2025, the sector is shaped by a combination of international standards, industry consortia, and region-specific regulations, all aimed at ensuring interoperability, safety, and quality in high-throughput manufacturing environments.
A key player in the development of standards for lithography and semiconductor manufacturing is the SEMI (Semiconductor Equipment and Materials International), which issues widely adopted standards covering equipment interfaces, safety, and process control. SEMI’s standards, such as SEMI S2 (Environmental, Health, and Safety Guideline for Semiconductor Manufacturing Equipment), are increasingly referenced by R2R equipment manufacturers to ensure compliance with global best practices. In parallel, the IEEE (Institute of Electrical and Electronics Engineers) continues to develop technical standards relevant to flexible and printed electronics, including those that impact R2R lithography processes, such as substrate handling, alignment, and process monitoring.
Environmental regulations are also a significant consideration. The European Union’s REACH and RoHS directives, as well as similar regulations in North America and Asia, require R2R equipment manufacturers to minimize hazardous substances and ensure recyclability of components. Compliance with these directives is now a baseline expectation for equipment exported to major markets, prompting manufacturers to invest in greener materials and processes.
Industry consortia and collaborative research organizations play a pivotal role in harmonizing standards and accelerating innovation. For example, SEMI and IEEE frequently organize working groups and technical committees that bring together equipment makers, end-users, and academic researchers to address emerging challenges in R2R lithography, such as nanoscale patterning accuracy and process integration with other manufacturing steps.
Looking ahead, the next few years are expected to see increased standardization around data interoperability (e.g., equipment-to-factory communication protocols), predictive maintenance, and in-line metrology for R2R systems. This is driven by the growing adoption of Industry 4.0 principles and the need for seamless integration of R2R lithography into smart manufacturing environments. As the technology scales, regulatory scrutiny on workplace safety, emissions, and energy efficiency is likely to intensify, further shaping equipment design and operational protocols.
In summary, the regulatory and standards landscape for R2R lithography equipment manufacturing in 2025 is characterized by a convergence of global safety, environmental, and interoperability requirements, with leading industry bodies such as SEMI and IEEE at the forefront of shaping the sector’s future.
Future Outlook: Opportunities, Risks, and Strategic Recommendations
The outlook for roll-to-roll (R2R) lithography equipment manufacturing in 2025 and the following years is shaped by accelerating demand for flexible electronics, advanced packaging, and cost-effective large-area patterning. As industries such as display manufacturing, photovoltaics, and printed electronics scale up, R2R lithography is increasingly recognized for its high throughput and material efficiency compared to traditional batch processes.
Key players in the sector, including KATEE (Korea Association of Technology for Electronics Equipment), Meyer Burger Technology AG, and Tokyo Ohka Kogyo Co., Ltd., are investing in R&D to enhance resolution, registration accuracy, and process integration. For example, Tokyo Ohka Kogyo Co., Ltd. is advancing photolithography materials and process solutions tailored for R2R systems, while Meyer Burger Technology AG is leveraging its expertise in precision equipment for solar cell manufacturing to expand into flexible substrates.
Opportunities in the near term are driven by the proliferation of flexible OLED displays, wearable sensors, and smart packaging. The global push for sustainable manufacturing is also favoring R2R processes due to their lower energy consumption and reduced material waste. In 2025, several pilot lines and commercial installations are expected to come online, particularly in Asia, where government-backed initiatives are supporting the adoption of advanced manufacturing technologies.
However, the sector faces notable risks. Technical challenges remain in achieving sub-micron patterning at high speeds, maintaining uniformity over large areas, and integrating R2R lithography with upstream and downstream processes. Equipment manufacturers must also navigate supply chain uncertainties, especially for precision components and specialty materials. Furthermore, the capital-intensive nature of R2R lithography equipment development may limit market entry to established players or those with strong financial backing.
Strategically, equipment manufacturers are advised to:
- Invest in collaborative R&D with material suppliers and end-users to accelerate process optimization and address integration challenges.
- Focus on modular equipment designs that allow for customization and scalability, catering to diverse application requirements.
- Strengthen after-sales support and process engineering services to help customers maximize yield and throughput.
- Monitor regulatory trends and sustainability standards, positioning R2R lithography as a green manufacturing solution.
In summary, while the R2R lithography equipment sector in 2025 is poised for growth, success will depend on technological innovation, strategic partnerships, and the ability to deliver reliable, high-performance systems for next-generation electronics manufacturing.
Sources & References
- Meyer Burger Technology AG
- KROENERT
- ASML Holding
- Nikon Corporation
- Canon Inc.
- Roland DG Corporation
- Oak Ridge National Laboratory
- imec
- Fraunhofer Society
- Mitsubishi Electric Corporation
- Tokyo Ohka Kogyo Co., Ltd.
- Coatema Coating Machinery GmbH
- LG Display
- First Solar
- PARC, a Xerox Company
- Rolleto
- DSM
- IEEE