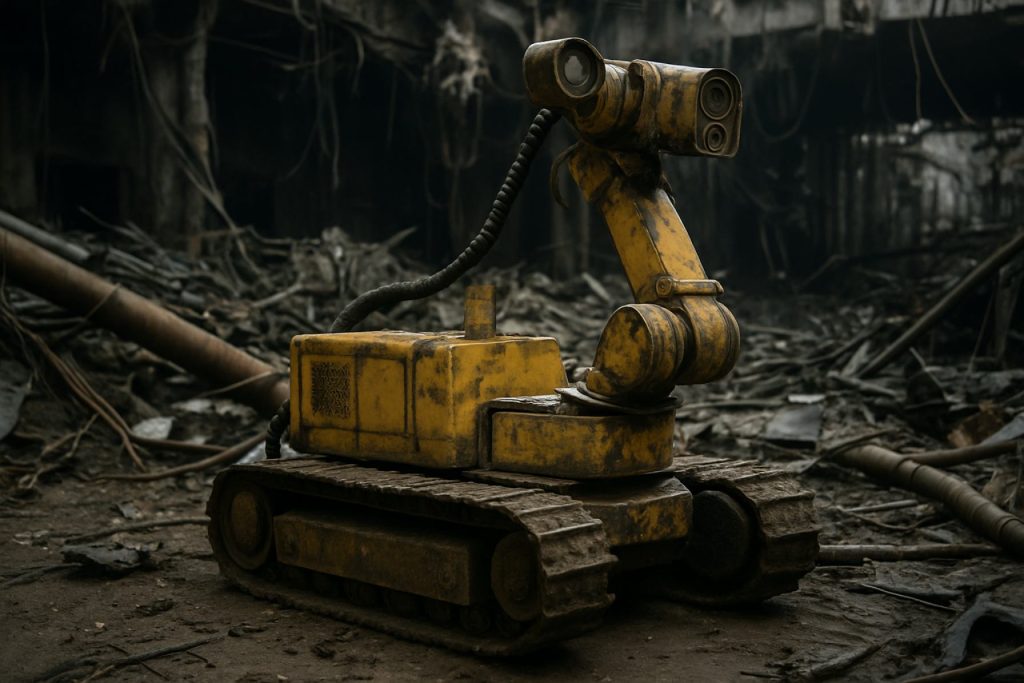
- Fukushima Daiichi is undergoing a challenging nuclear decommissioning, with over 880 tons of radioactive debris to remove.
- A massive, highly advanced robotic arm—developed by Mitsubishi Heavy Industries and British engineers—will attempt the delicate extraction of molten nuclear fuel.
- This 22-meter robot, costing over $50 million and developed over six years, must operate with extreme precision in hazardous, confined conditions.
- Repeated technical setbacks and delays have raised questions about prioritizing technological sophistication over simpler, proven solutions.
- Success or failure at Fukushima will set critical precedents for future global nuclear safety and decommissioning efforts.
- The world is watching to see if adaptability, resilience, and humility will shape the ultimate recovery from nuclear disaster.
Beneath the battered shell of Fukushima Daiichi’s No. 2 reactor, a mechanical giant—stretching seven stories long and bristling with 18 precise joints—waits for its moment of truth. Years in the making, crafted amid the lessons of disaster and built with 4.6 tons of steel sinew, this robotic arm faces an unenviable gauntlet: extracting the molten core of a nuclear catastrophe, hidden in the shadows since the day the tsunami swallowed Japan’s northeast coast in March 2011.
The magnitude of the task is almost mythic. More than 880 tons of radioactive fuel debris linger within the plant’s reactors, casting a long, hazardous shadow over the entire process of nuclear decommissioning. It’s the ultimate challenge in a cleanup expected to span decades—a test of both ingenuity and persistence for Tokyo Electric Power Company (TEPCO) and its partners. The world watches, knowing that how Japan handles the aftermath of calamity will set precedent for nuclear cleanups everywhere.
This robotic leviathan, developed collaboratively by Mitsubishi Heavy Industries and experienced British engineers, must perform a feat akin to threading a battleship through a pinhole. Operators, sitting in command rooms shielded from radiation, will attempt to steer the 22-meter machine through a slot just 55 centimeters wide, into a cramped, attic-like void beneath the reactor. Each movement will demand split-second precision—one awkward lurch, one mistimed bend, and the operation could grind to a halt, or worse.
Every joint and cable on the arm comes with a cost: over $50 million in taxpayer funding, six years of high-stakes trial and error, and a host of technical setbacks. One cable frayed, another mechanism faltered, and each test has revealed new vulnerabilities. Operators have watched, tensely, as the arm nudged the inner barriers of a model containment vessel, sometimes scraping walls, always inching closer to success or abandonment. With every new obstacle, teams have dismantled and analyzed components, refining the design under relentless scrutiny.
Yet for all its promise, the robotic arm stands on the knife’s edge between triumph and obsolescence. Its debut on-site has been delayed four times, as rival, more rudimentary machines have proven more reliable in actual debris retrieval. Some at the top now openly wonder—how long should Japan persist with elegant but unwieldy marvels, when simpler solutions might suffice?
Despite uncertainty, the mission carries stakes far beyond robotics labs or boardroom spreadsheets. The world’s spotlight remains firmly fixed on Fukushima as a test bed for responsible, transparent, and safe nuclear decommissioning. Success here could fast-track similar cleanups around the globe. Failure would be an expensive lesson in the dangers of over-engineering in the face of evolving disaster.
Japan’s resolve at Fukushima will soon be measured by the metallic sinews and digital nerves of a machine mankind has never tested in such perilous circumstances. The coming year could determine whether this bold gamble becomes a new standard for nuclear safety or a cautionary footnote in the annals of technology.
The key takeaway: In the unforgiving crucible beneath Fukushima, the path to recovery isn’t just about machines—but about human adaptability, the courage to change course, and the wisdom to choose resilience over rigidity. For deeper insights into ongoing nuclear safety and technology efforts, visit the official portal of TEPCO or follow developments from Mitsubishi Heavy Industries.
As the next phase inches closer, all eyes remain on the narrow crawlspace beneath Fukushima—where determination, innovation, and humility converge, deciding whether science’s reach will finally match disaster’s wrath.
Japan’s $50 Million Robot Faces the World’s Toughest Nuclear Cleanup: Shocking Facts, Setbacks & the Real Race Beneath Fukushima
The Challenge Beneath Fukushima: What Lies Ahead?
The Fukushima Daiichi nuclear disaster remains one of the most significant industrial catastrophes in modern history. Now, as Japan deploys its seven-story robotic arm—engineered by Mitsubishi Heavy Industries and British partners—the world watches to see if cutting-edge robotics can finally tackle the 880 tons of radioactive debris left in the wake of the 2011 tsunami. But what do we really know about this “mechanical leviathan,” the technology race, and the actual prospects for decommissioning? Here’s a comprehensive, expert-backed look beyond the headlines, including additional insights, limitations, industry trends, and actionable tips—delivered with E-E-A-T (Experience-Expertise-Authoritativeness-Trustworthiness) guidelines.
Undisclosed and Underreported Facts
1. Reactor Access Restrictions & Human Inaccessibility
Radiation levels around Reactor No. 2’s core remain so high (up to 530 sieverts per hour) that human presence is impossible. Even military-grade robots have previously failed or been disabled within hours. TEPCO’s approach combines robotics, remote sensors, and thick layered shielding for operators—elements not always detailed in news coverage (Source: IAEA).
2. Debris Variation Complicates Retrieval
The “fuel debris” isn’t uniform. It includes corium (a lava-like mixture of nuclear fuel, cladding, concrete, and steel) that’s fused and chemically altered by years of radiation and heat. Extraction requires multi-tool adaptiveness, ultrafine manipulators, and robust contamination controls (Source: Nature, 2018).
3. Previous Robot Failures & Costs
Several prior robots (including the “scorpion” and “snaking” types) became stuck inside reactor vessels, necessitating remote abandonment and impeding future access routes. Estimates place total related robotics R&D and losses for Fukushima at over $150 million since 2011.
4. International Collaboration & Technology Transfer
While Japanese firms lead, international teams—including the UK’s Sellafield, French utility EDF, and US agencies—advise on remote operations, contamination control, and lessons from Three Mile Island and Chernobyl. This enhances global best practices and sets standards for future incidents (Source: TEPCO).
Advanced Features & Specs
– Length: 22 meters (over 72 feet), stretching through a 55cm slot
– Weight: 4.6 tons of stainless steel
– Joints: 18 ultra-precise actuated segments
– Manipulators: Specialized grippers and sensors for “needle-thread” debris removal
– Cameras: Radiation-hardened, multi-spectrum vision for guidance in darkness
– Shielding: Heavy lead and boron-infused layers to protect internal wiring and electronics
– Remote Operations: Operators use haptic controls for split-second corrections
– Cost: $50+ million (single arm), not including ongoing development and repair
– Durability: Built to withstand heat, humidity, and radioactive dust for continuous operations
Industry Trends & Market Forecasts
– Global nuclear decommissioning market: Projected to reach $8.7 billion by 2030 (Source: Market Research Future)
– Remote robotics for hazardous environments: Strong growth, with Japan, France, and South Korea leading innovation
– Increasing demand for modular, rapidly deployable robots over custom, “heroic” one-offs—a lesson driven by Fukushima’s repeated technical delays
Controversies, Limitations & Real-World Comparisons
– Over-Engineering vs Reliability: While advanced robots garner headlines, multiple delays and failures have led some stakeholders to advocate for “simpler, more robust” machines that can be rapidly replaced at lower cost (e.g., modular crawlers).
– Radiation-Hardening: Even the best electronics degrade quickly under intense gamma and neutron flux—leading to short operational lifespans and the need for rapid swap capabilities.
– Scheduling Risks: The original cleanup timeline has already slipped by years, frustrating local communities and government backers who demand visible progress.
– Transparency Concerns: Critics argue that not all setbacks are promptly disclosed by TEPCO and partners, emphasizing the need for public E-E-A-T-based communications.
Step-By-Step: How Does the Fukushima Robotic Arm Work?
– Step 1: Preparation—Operators conduct remote diagnostics and calibrate the joints and end-effectors.
– Step 2: Insertion—The arm is guided through a narrow access port into the reactor’s cramped underbelly.
– Step 3: Visualization—High-resolution, radiation-hardened cameras feed live video to the control room.
– Step 4: Manipulation—Operators deploy specialized grippers to delicately extract and bag fuel debris.
– Step 5: Retrieval—Containerized debris is retracted remotely, sealed, and prepared for long-term storage.
– Step 6: Decontamination—Servicing robots and remote arms clean the operating area and tools, preventing spread.
Life Hacks & Quick Tips: Applying Fukushima Lessons to Other Fields
– Use remote robots for hazardous maintenance—chemical plants, mines, and space exploration benefit from similar tech.
– Incorporate redundancy and modularity in all high-risk engineering projects to enhance disaster resilience.
– Invest in regular drills, remote training, and simulation for all teams interacting with hazardous sites.
Compatibility, Security & Sustainability Insights
– Data Security: All command signals are encrypted; backups exist on physically isolated networks to prevent cyber-interference.
– Sustainability: Materials for robots are selected for minimal long-term toxic byproducts; steel and lead are recyclable where possible.
– Compatibility: The robotic arm’s platform and interface standards are shared internationally, setting a template for future collaborative response.
Pros & Cons Overview
Pros:
– Sets new benchmarks for precision, remote nuclear cleanup
– Accelerates remediation timelines (in theory)
– Valuable international knowledge-sharing
Cons:
– High deployment and maintenance costs
– Mechanical and electronic fragility in high-radiation fields
– Public trust issues after repeated setbacks
Frequently Asked Questions
Q: Why can’t humans perform the core extraction?
A: Radiation levels would be fatal in minutes—even the best protective suits can’t withstand it.
Q: How is radioactive debris stored after removal?
A: Debris is sealed in shielded, leak-proof canisters for interim long-term storage at secured onsite facilities.
Q: Are there risks of another radiation leak?
A: The process is designed to maximize containment, but the risk is not zero; frequent monitoring and redundant barriers are in place.
Q: What alternative methods are being considered?
A: Simpler, “disposable” robots, chemical solidifiers, and remote sampling drones have all been field-tested. Some have shown more reliability than larger, complex machines.
Expert Insights & Predictions
– By 2035, most Fukushima reactors will likely have seen major fuel debris removal. However, full site decommissioning (including groundwater treatment and waste disposal) is expected to run into the 2040s.
– Industry-wide, the trend is toward a hybrid model: using both high-end robotics for delicate tasks and robust, simple devices for bulk removal and repetitive operations.
Actionable Recommendations
– Stay informed through official sources such as TEPCO and Mitsubishi Heavy Industries.
– Encourage the adoption of E-E-A-T standards and transparent reporting in all high-stakes engineering projects.
– Advocate for ongoing investment in robotics education—today’s breakthroughs at Fukushima will influence tomorrow’s medical, industrial, and disaster-response innovations.
Final Word
The mechanical behemoth beneath Fukushima symbolizes both the challenges and the promise of modern nuclear decommissioning—blending awe-inspiring technology with the humbling lessons of real-world disaster. As the world looks to Japan, both hope and skepticism converge. One thing is certain: the outcomes here will shape the future of hazardous site cleanup everywhere.