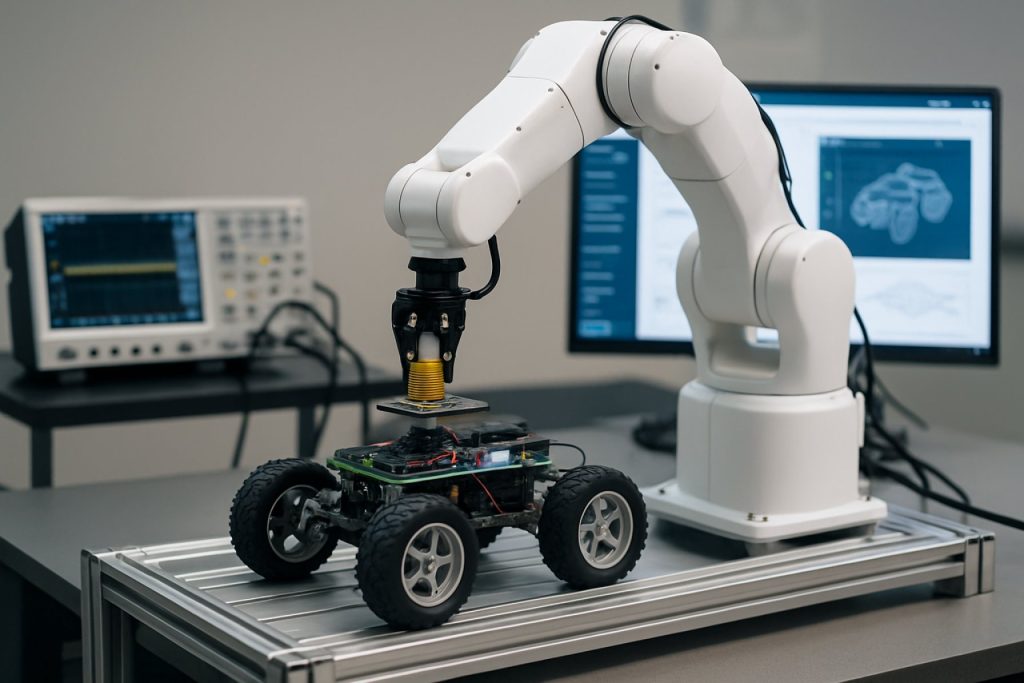
Table of Contents
- Executive Summary: 2025 Market Landscape and Key Drivers
- Triboelectric Robotics Testing Bench Technology: Core Innovations and New Advances
- Global Market Size, Growth Projections, and Regional Hotspots (2025–2030)
- Major Players and New Entrants: Profiles and Strategic Moves
- Emerging Applications in Robotics, Manufacturing, and Automation
- Supply Chain, Materials, and Manufacturing Trends
- Regulatory Standards, Compliance, and International Collaboration
- Investment, Funding, and Partnership Opportunities
- Challenges and Risk Factors Impacting Market Trajectory
- Future Outlook: Disruptive Trends and Long-Term Forecasts
- Sources & References
Executive Summary: 2025 Market Landscape and Key Drivers
The triboelectric robotics testing bench manufacturing sector is poised for significant advancements in 2025, shaped by accelerated research in triboelectric nanogenerators (TENGs), increasing demand for intelligent sensors, and the integration of advanced automation in robotics. These testing benches are critical for the evaluation, calibration, and validation of triboelectric devices and materials used in next-generation robotic systems. As triboelectric technologies continue to transition from laboratory prototypes to scalable applications, the need for precise, repeatable, and customizable testing platforms is becoming a key industry driver.
Currently, the market landscape is defined by a small number of specialized manufacturers and research institutions with capabilities in both triboelectric material processing and robotic system integration. Companies such as ABB and Festo are actively investing in modular robotics and smart automation, providing foundational technologies that enable the design of adaptable testing benches. Additionally, organizations like SMC Corporation and igus are contributing advanced motion components and sensor integration solutions, which are essential for the high-precision requirements of triboelectric testing.
In 2025, the primary market drivers include the proliferation of soft robotics, wearable devices, and energy-harvesting systems, all of which rely heavily on efficient triboelectric elements. The demand for standardized and automated testing platforms is further fueled by the need to accelerate product development cycles and ensure quality assurance as triboelectric technologies enter commercial markets. Major research hubs and industry collaborations are focusing on developing open-source and modular test bench architectures, capable of supporting rapid customization and high-throughput testing.
On the data front, industry bodies are projecting a robust increase in the deployment of triboelectric testing benches, with growth rates outpacing traditional electromechanical testing platforms. This trend is being reinforced by government-sponsored innovation programs and academic-industry partnerships, particularly in Europe and Asia, where TENG research and industrialization are strongly supported. For instance, ABB and Festo have announced initiatives to enhance laboratory automation solutions, which are directly relevant to the triboelectric testing market.
Looking ahead, the next few years are expected to see increased standardization efforts and interoperability among testing components, driven by both user demand and regulatory requirements. The integration of AI-driven analytics and remote monitoring capabilities is anticipated to become mainstream, aligning triboelectric testing infrastructure with broader Industry 4.0 objectives. Companies with strong portfolios in automation, sensor technology, and modular robotics—such as Festo and SMC Corporation—are well positioned to shape and benefit from these emerging opportunities.
Triboelectric Robotics Testing Bench Technology: Core Innovations and New Advances
The manufacturing landscape for triboelectric robotics testing benches is experiencing significant technological advancement as research and industry collaboration intensify in 2025. These testing benches, critical for evaluating triboelectric nanogenerators (TENGs) and robotic sensor systems, are being reimagined with a focus on automation, precision, and modularity.
Core innovations shaping the sector include the integration of high-precision motion control systems—often leveraging piezoelectric actuators and linear motors—to replicate real-world contact and sliding scenarios with sub-micron accuracy. Manufacturers are increasingly deploying programmable logic controllers (PLCs) and advanced human-machine interfaces (HMIs) to enable customizable, repeatable testing protocols and real-time data acquisition. In 2025, leading automation hardware suppliers such as Festo and ABB are providing the underlying actuation and control solutions that allow for complex motion profiles and seamless integration with laboratory data management systems.
Another notable advance is the adoption of modular bench architectures, which enable rapid reconfiguration for testing various triboelectric material combinations and robotic components. Companies specializing in laboratory automation, such as Thorlabs, are offering customizable platforms with plug-and-play sensor mounts, environmental control options (temperature, humidity), and vibration isolation, supporting a broad spectrum of triboelectric evaluation scenarios.
Precision sensors are a cornerstone of new testing bench designs. In 2025, the use of high-sensitivity electrometers and force-displacement sensors—provided by manufacturers like Keithley—enables the accurate quantification of charge transfer and mechanical input/output. Furthermore, the integration of high-speed data acquisition systems allows researchers to capture transient triboelectric signals and correlate them to mechanical events with millisecond or better resolution.
Looking ahead, the next several years are expected to see further convergence between triboelectric testing benches and robotic automation platforms. Industry outlooks point to the emergence of AI-driven testing protocols, where machine learning algorithms optimize testing parameters and rapidly interpret complex datasets. Early-stage collaborations between robotics integrators and specialized triboelectric device manufacturers, such as those facilitated by ABB, suggest a future where standardized, high-throughput triboelectric testing becomes a routine part of intelligent robotics development pipelines.
Overall, 2025 marks a period of rapid technological maturation for triboelectric robotics testing bench manufacturing, underpinned by advances in automation, modularity, and precision instrumentation—setting the stage for accelerated innovation in triboelectric-powered robotics and sensor technologies in the coming years.
Global Market Size, Growth Projections, and Regional Hotspots (2025–2030)
The global market for triboelectric robotics testing bench manufacturing is poised for robust growth entering 2025 and throughout the next five years, driven by surging investment in advanced robotics, sensor technologies, and the growing adoption of energy-harvesting solutions in automation. As triboelectric nanogenerator (TENG) technologies mature, their application in robotic testing benches—devices that simulate, evaluate, and optimize robot movements and sensor systems—has become increasingly sought after by manufacturers aiming for energy-efficient and responsive robotic systems.
In 2025, market activity is concentrated in North America, Europe, and East Asia, with the United States, Germany, Japan, South Korea, and China emerging as primary hotspots for both research and industrial-scale manufacturing. Leading robotics and automation firms are advancing the integration of triboelectric technologies into testing infrastructure, motivated by the need for real-time feedback, durability, and reduced operational energy costs. Companies such as FANUC, Yaskawa Electric Corporation, and ABB are actively investing in testing platforms that leverage triboelectric sensing, reflecting a broader trend towards smart automation and predictive maintenance.
Data from recent industry events and supplier activity indicates that the global market value for triboelectric robotics testing benches is expected to surpass several hundred million USD by 2030, with a compounded annual growth rate (CAGR) projected in the range of 10–15%. This expansion is underpinned by increased adoption in sectors such as automotive manufacturing, precision assembly, and electronics, where reliability and adaptive feedback are critical. The proliferation of collaborative robots (cobots) and the transition to Industry 4.0 have further accelerated demand for advanced testing benches integrating triboelectric systems, particularly in Germany and Japan, where industrial automation is highly prioritized.
Regionally, China is ramping up both domestic production and export capacity, supported by government incentives and partnerships with global suppliers of triboelectric materials and sensor components. Meanwhile, European initiatives aimed at sustainable manufacturing and digitalization provide fertile ground for market growth, with Germany and France investing in next-generation testing infrastructure. In North America, research-driven firms and university spin-offs are collaborating with established robotics manufacturers to refine triboelectric bench designs and scale up deployment.
Looking ahead to 2030, the outlook remains positive, with ongoing advancements in material science and sensor miniaturization expected to lower costs and improve bench capabilities. Strategic alliances between triboelectric material suppliers and robotics integrators are likely to accelerate innovation, ensuring continued expansion and the emergence of new regional players in the triboelectric robotics testing bench manufacturing market.
Major Players and New Entrants: Profiles and Strategic Moves
The landscape of triboelectric robotics testing bench manufacturing in 2025 is defined by the interplay of established leaders in robotics R&D hardware, emerging interdisciplinary startups, and strategic partnerships aimed at commercializing next-generation triboelectric sensing and actuation systems. The industry is characterized by a strong presence of companies with deep roots in precision instrumentation and automation, as well as a cohort of newer entrants leveraging advances in materials science and triboelectric nanogenerators (TENGs).
Among the major players, Keysight Technologies and National Instruments continue to support research institutions and OEMs with modular test benches and data acquisition solutions. Both companies have expanded their product portfolios to include customizable testing rigs and advanced sensor integration capabilities, addressing the unique needs of triboelectric device evaluation. Their platforms’ open architectures facilitate the inclusion of triboelectric modules and enable high-precision signal measurement, positioning them as preferred partners for robotics labs and advanced manufacturing lines.
A notable strategic move in 2024-2025 is the partnership between ABB and several leading universities to co-develop robotic test cells optimized for the rapid prototyping of triboelectric-powered end-effectors. ABB’s expertise in automation and collaborative robotics is being leveraged to refine standardized testing protocols for TENG-based systems, with the goal of accelerating industrial adoption in sectors ranging from healthcare automation to flexible electronics assembly.
On the supplier side, companies such as Festo and Bosch Rexroth are integrating triboelectric sensor calibration modules into their standard robotics test benches, responding to increasing demand from OEMs seeking to validate energy harvesting and self-powered sensor arrays. These enhancements are often developed in close collaboration with academic spin-offs and consortia focused on soft robotics and wearable applications.
The sector is also witnessing new entrants, notably startups spun out from university research programs in China, South Korea, and the US. These companies, often supported by government innovation funds or university-industry accelerators, are introducing compact, modular testing benches tailored for rapid material screening and iterative device optimization. Their systems emphasize ease of use, plug-and-play sensor interchangeability, and cloud-based data analytics, aiming to lower the barrier for small labs and prototyping teams.
Looking ahead, the next few years are expected to see intensified collaboration between established instrumentation firms and material innovators, as well as increased standardization efforts spearheaded by industry bodies. The convergence of triboelectric technology with AI-driven robotics is likely to further reshape the market, driving demand for advanced, scalable testing solutions and opening new opportunities for both incumbents and agile new entrants.
Emerging Applications in Robotics, Manufacturing, and Automation
The integration of triboelectric nanogenerators (TENGs) into robotics has rapidly gained traction, steering advancements in robotics testing bench manufacturing. In 2025, leading robotics and automation firms are increasingly focusing on the development and deployment of triboelectric-based testing benches to enable self-powered sensing, actuation, and real-time diagnostics. This shift is largely fueled by demands for higher energy efficiency, wireless operation, and adaptive automation in both industrial and research settings.
Major robotics manufacturers such as FANUC and KUKA have begun to explore the integration of triboelectric modules within their automation platforms. These modules allow for the harvesting of mechanical energy from robotic joints and end-effectors, which can then be used to power embedded sensors or auxiliary devices on the testing benches. Such capabilities are particularly valuable in flexible manufacturing environments where cabling is undesirable or frequent system reconfiguration is required.
Recent years have also seen specialized suppliers, like Festo, collaborating with academic partners to prototype triboelectric-enabled robotic test benches. These collaborations focus on developing modular testing systems that leverage TENG-based self-powered sensors for real-time feedback on force, strain, and displacement. This eliminates the need for external power sources and reduces maintenance complexity, while supporting automated calibration and health monitoring of robotic arms and grippers.
Data from pilot deployments in 2024 indicate that triboelectric testing benches can reduce sensor maintenance cycles by up to 40% and improve detection accuracy in adaptive assembly lines. Furthermore, the adoption of these benches aligns with ongoing industry initiatives to enhance sustainability and reduce the energy footprint of smart factories, as promoted by organizations such as International Federation of Robotics.
Looking ahead, the market outlook for triboelectric robotics testing benches is highly positive. By 2027, it is anticipated that a substantive portion of new testing infrastructure in advanced manufacturing plants will incorporate triboelectric sensing and energy harvesting components. Ongoing research by robotics solution providers and automation equipment manufacturers aims to increase the robustness of TENG components, ensure compatibility with legacy systems, and standardize interface protocols. The next few years will likely witness further partnerships between industrial stakeholders and material science innovators, accelerating the mainstream adoption of triboelectric technologies within robotics testing and automation.
Supply Chain, Materials, and Manufacturing Trends
The manufacturing of triboelectric robotics testing benches is evolving rapidly in 2025 due to increasing demand for advanced materials, robust supply chains, and precision engineering. The core challenge in this sector lies in sourcing high-performance triboelectric materials, such as specific polymers, nanocomposites, and surface coatings, that can reliably generate and measure electrical signals upon contact or motion. The market is witnessing a shift toward eco-friendly and recyclable materials, with major polymer suppliers like Dow and BASF investing in sustainable triboelectric materials suitable for repetitive testing environments.
Precision manufacturing is essential for these benches, as even minor inconsistencies in surface texture or alignment can significantly affect measurement accuracy. Companies specializing in advanced automation and robotic assembly, such as FANUC and Yaskawa Electric, are increasingly integrated into the supply chain to ensure repeatable, high-tolerance builds. Meanwhile, specialized suppliers of triboelectric measurement and calibration equipment, like Keithley Instruments (a subsidiary of Tektronix), are collaborating with bench manufacturers to embed smart sensors and data acquisition systems for real-time diagnostics.
The supply chain landscape in 2025 is shaped by ongoing geopolitical uncertainties and logistics disruptions. Manufacturers are responding by diversifying their sourcing networks, emphasizing regional suppliers, and leveraging digital traceability platforms. For instance, leading electronics manufacturing services providers such as Flex and Jabil are offering modular manufacturing solutions, allowing for rapid scaling and localization of testing bench production in response to shifting global conditions.
Additive manufacturing (3D printing) is also gaining traction, especially for custom components and rapid prototyping. Companies like Stratasys are providing solutions for fabricating complex triboelectric sensor housings and fixtures with high material accuracy. This trend is expected to accelerate as triboelectric robotics testing becomes more specialized, requiring bespoke designs for emerging robotic applications in wearables, flexible electronics, and soft robotics.
Looking ahead, the industry is expected to continue its focus on material innovation, automation, and supply chain resilience. As collaborative robotics and AI-driven manufacturing become more pervasive, triboelectric testing bench production will likely see further integration of smart diagnostics and adaptive manufacturing processes, enabling rapid iteration and high-quality assurance for next-generation robotics research and deployment.
Regulatory Standards, Compliance, and International Collaboration
As triboelectric robotics advance in sophistication and deployment, the manufacturing of testing benches for these systems is increasingly shaped by evolving regulatory standards, compliance mandates, and international cooperation. In 2025, this landscape is characterized by dynamic interplay among global standardization bodies, national regulatory agencies, and industry consortia. The integration of triboelectric nanogenerators (TENGs) into robotics necessitates rigorous, standardized testing environments, which in turn drives the establishment and harmonization of protocols for bench manufacturing.
Key regulatory frameworks influencing triboelectric robotics testing bench manufacturing include directives from the International Organization for Standardization (ISO) and the International Electrotechnical Commission (IEC). Both organizations are actively developing and updating standards for electrical safety, electromagnetic compatibility, and mechanical robustness related to triboelectric devices. In particular, ISO/TC 299 (Robotics) and IEC/TC 101 (Electrostatics) have initiated joint working groups to address the unique challenges presented by triboelectric phenomena in robotics, focusing on repeatability, safety, and interoperability of testing setups.
Regionally, the European Committee for Electrotechnical Standardization (CENELEC) and the American National Standards Institute (ANSI) are aligning their requirements with international standards, emphasizing laboratory accreditation and traceability in testing bench manufacturing. In 2025, new guidance from CENELEC on electrostatic discharge (ESD) testing methods for robotics has begun to be adopted by manufacturers, requiring updates in material selection, grounding, and shielding within test bench designs.
On the compliance front, manufacturers must increasingly demonstrate adherence to documentation and traceability protocols, especially for benches used in regulated sectors such as healthcare robotics and autonomous systems certification. The UL Standards organization has expanded its certification portfolio to include triboelectric-based robotic testing apparatus, offering specific marks for ESD performance and operator safety.
International collaboration is also intensifying as manufacturers and research institutes in Asia, Europe, and North America form consortia to standardize test methodologies and share best practices. For example, the Association for Advancing Automation (A3) is leading cross-border initiatives aimed at harmonizing triboelectric test protocols, ensuring that equipment manufactured in one region can be reliably certified and used globally.
Looking ahead, the next few years are expected to see further convergence of standards and compliance regimes, with an emphasis on digital traceability and interoperability. This will likely include the adoption of blockchain or similar technologies for certification tracking, and increased involvement of industry stakeholders in shaping regulatory frameworks to keep pace with rapid technological advancements in triboelectric robotics.
Investment, Funding, and Partnership Opportunities
Investment and partnership activities in the field of triboelectric robotics testing bench manufacturing are poised to accelerate in 2025, reflecting broader trends in soft robotics and smart materials research. Triboelectric nanogenerators (TENGs) are increasingly critical for the development of self-powered robotic systems, creating demand for specialized testing infrastructure. This has attracted the attention of both established automation firms and emerging deep-tech startups, whose collaborative efforts are reshaping the investment landscape.
Leading robotics manufacturers and academic institutions are prioritizing grants and research funding to develop advanced testing benches capable of evaluating TENG-powered actuators and sensors under real-world conditions. For example, Siemens and ABB have recently expanded their investment in research consortia focusing on next-generation automation and energy harvesting, including triboelectric applications. Their facilities increasingly integrate sophisticated test benches for rapid prototyping and benchmarking of triboelectric systems.
On the startup front, companies specializing in flexible electronics and triboelectric components—such as Xsensio—are attracting seed and Series A funding rounds from venture capital firms that recognize the potential for scalable, energy-efficient robotics. These investments often include provisions for shared access to specialized testing equipment, sometimes via public-private partnerships with technical universities or industry clusters.
Government-backed initiatives are also driving funding. Several European Union Horizon Europe projects and similar programs in Asia-Pacific are earmarking resources for collaborative research infrastructure, including triboelectric testing benches. In China, the Chinese Academy of Sciences supports joint ventures between research labs and industrial partners to develop standardized testing protocols and shared manufacturing platforms for triboelectric robotics.
Looking forward, industry outlook for the next few years suggests increasing cross-sector partnerships. Automation leaders are expected to form alliances with sensor manufacturers and universities to standardize testing methodologies and accelerate market entry. Similarly, component suppliers such as Schneider Electric are evaluating collaborative pilot projects to integrate triboelectric testing capabilities into their innovation hubs.
In summary, 2025 will likely see robust investment and partnership activity centered on triboelectric robotics testing bench manufacturing, driven by the convergence of smart robotics, energy harvesting, and automated quality assurance. The sector’s progress will depend on continuing collaboration among industry, academia, and government to ensure scalable and reliable manufacturing of these critical testing systems.
Challenges and Risk Factors Impacting Market Trajectory
The manufacturing of triboelectric robotics testing benches in 2025 faces a unique set of challenges and risk factors that could influence its market trajectory over the coming years. A primary concern remains the technical complexity involved in integrating triboelectric nanogenerators (TENGs) with robotic testing platforms. Precise calibration and measurement are critical, as even minor inconsistencies in materials or surface treatments can significantly impact performance and repeatability. Manufacturers such as ABB and Festo, both recognized for their advanced automation solutions, have highlighted the ongoing difficulties in achieving the necessary sensitivity and durability for reliable triboelectric testing setups.
Supply chain volatility continues to present risks. The specialized polymers, conductive materials, and nanostructured surfaces required for high-performance triboelectric systems are subject to fluctuations in global availability and cost. Recent events in the electronics supply chain, as reported by Rockwell Automation, underscore the potential for delays or shortages in sourcing critical components, which can impede production timelines for testing benches.
Additionally, there is a lack of standardized protocols for evaluating triboelectric performance in a robotics context. This can result in inconsistent benchmarking across different manufacturers and research groups, impeding widespread adoption and confidence among industrial users. Industry organizations such as the IEEE have initiated efforts to develop testing and safety standards for emerging electromechanical systems, but comprehensive guidelines tailored specifically to triboelectric robotics testing are still in development as of 2025.
Another significant risk is the rapid pace of technological change. As advancements in materials science and nanotechnology accelerate, testing benches must be continually updated to accommodate new triboelectric materials and architectures. This creates a moving target for manufacturers, potentially leading to obsolescence of existing equipment or the need for costly retrofits. Companies like Siemens are investing heavily in modular and upgradeable automation platforms, yet the speed of innovation in triboelectric applications may still outpace development cycles.
Finally, regulatory and intellectual property (IP) concerns present potential hurdles. As the market grows, clear frameworks for IP protection and compliance with safety regulations will be crucial. Uncertainty in these domains could stifle collaboration and slow adoption, particularly for startups and smaller manufacturers seeking to enter the field.
Looking ahead to 2025 and beyond, overcoming these challenges will require coordinated efforts between material suppliers, robotics manufacturers, standards bodies, and regulatory agencies to ensure robust, scalable, and adaptable testing solutions for triboelectric systems.
Future Outlook: Disruptive Trends and Long-Term Forecasts
Looking ahead to 2025 and beyond, the field of triboelectric robotics testing bench manufacturing is poised for significant transformation, spurred by rapid advancements in materials science, sensor integration, and automated manufacturing. The proliferation of triboelectric nanogenerators (TENGs) in robotics and wearables has driven demand for specialized testing environments capable of evaluating energy harvesting efficiency, mechanical durability, and system integration under real-world conditions.
A key trend shaping the sector is the convergence of triboelectric technologies with Industry 4.0 manufacturing principles. Companies in the robotics and automation sector, such as FANUC Corporation and KUKA AG, are increasingly incorporating advanced sensor arrays—including triboelectric-based solutions—into their robotics platforms, fostering a need for testing benches that can accommodate multi-modal data acquisition and real-time analytics. The integration of AI-driven diagnostics within test benches is also anticipated to streamline fault detection and predictive maintenance, thus reducing downtime and improving the reliability of triboelectric systems.
The expansion of the flexible electronics industry is another driver, with leading electronics manufacturers like Samsung Electronics investing in stretchable and wearable devices powered by triboelectric modules. The development of testing benches tailored for these applications—offering precise control over mechanical deformation, environmental simulation, and long-duration cycling—is expected to see robust growth. Manufacturers are beginning to adopt modular bench designs, allowing for rapid customization as new triboelectric materials and device architectures emerge.
Standardization efforts, led by international organizations such as the International Organization for Standardization (ISO), are projected to accelerate over the next few years. The establishment of unified testing protocols for triboelectric devices will facilitate interoperability and quality assurance, supporting global supply chains and regulatory compliance. This trend is likely to stimulate cross-industry collaboration between robotics OEMs, academic research laboratories, and test equipment manufacturers.
Looking further ahead, the growing adoption of green manufacturing practices and circular economy principles is expected to influence the design and material selection of triboelectric testing benches. Innovations in recyclable polymers, energy-efficient actuators, and digital twinning technologies are anticipated to become mainstream, with companies like ABB Ltd investing in sustainable industrial automation solutions.
In summary, the future of triboelectric robotics testing bench manufacturing will be defined by technological convergence, standardization, and sustainability, with global industry leaders and standards bodies setting the pace for disruptive innovation and long-term growth.
Sources & References
- ABB
- SMC Corporation
- igus
- Thorlabs
- Keithley
- FANUC
- Yaskawa Electric Corporation
- Bosch Rexroth
- KUKA
- International Federation of Robotics
- BASF
- Yaskawa Electric
- Flex
- Stratasys
- International Organization for Standardization
- European Committee for Electrotechnical Standardization
- American National Standards Institute
- UL Standards
- Siemens
- Xsensio
- Chinese Academy of Sciences
- Rockwell Automation
- IEEE