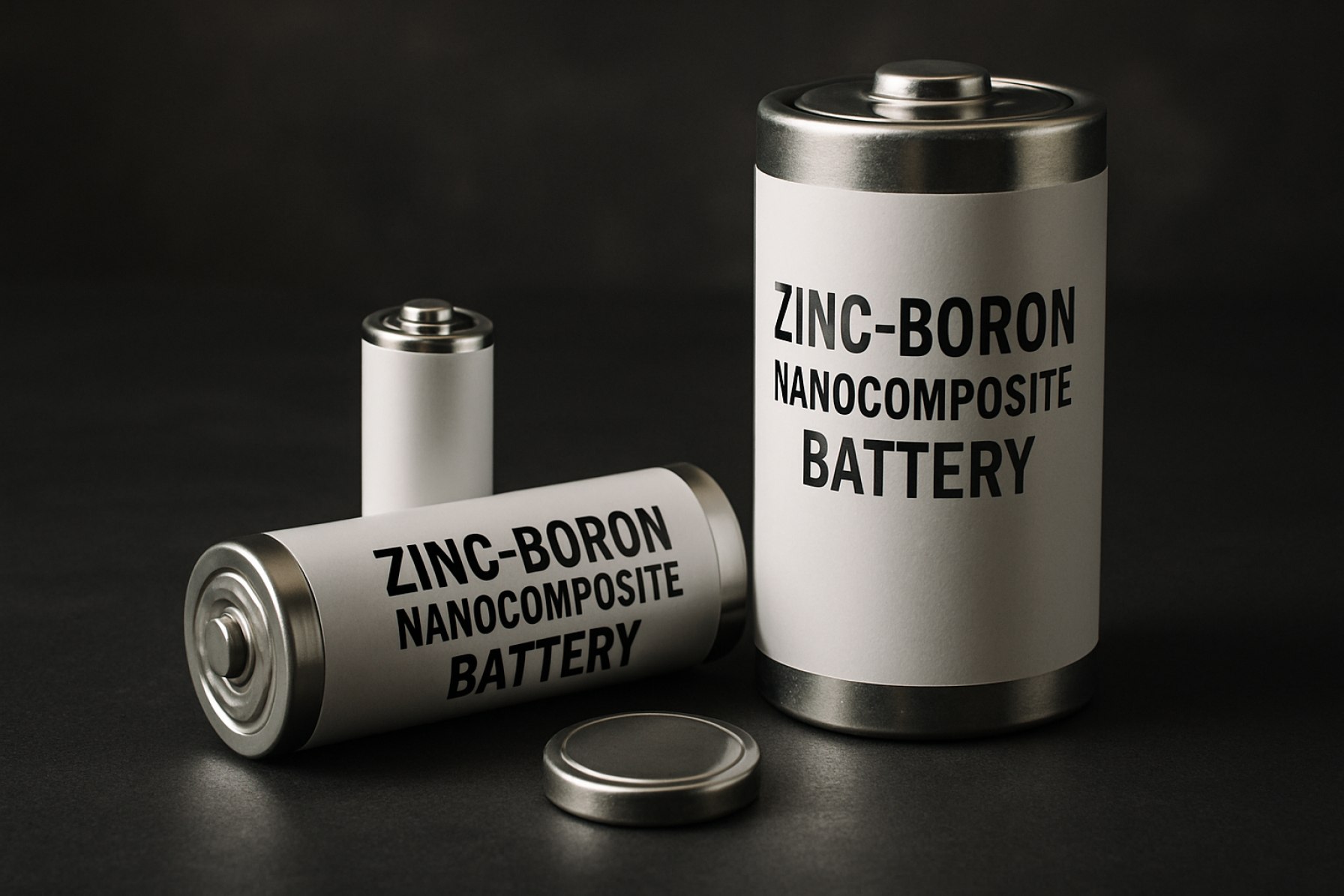
Table of Contents
- Executive Summary: Key Findings & Market Highlights 2025–2030
- Technology Overview: Zinc-Boron Nanocomposites and Their Unique Advantages
- Current Manufacturing Landscape and Leading Players
- Breakthrough Innovations: Recent R&D and Emerging Patents
- Production Challenges and Solutions in Scaling Nanocomposite Batteries
- Cost Dynamics and Price Forecasts for 2025–2030
- Competitive Analysis: Zinc-Boron vs. Lithium-Ion and Other Chemistries
- Key Application Sectors: EVs, Grid Storage, and Beyond
- Regulatory Landscape and Industry Standards (ieee.org, batteryindustry.tech)
- Future Outlook: Market Size, Growth Trajectories, and Strategic Opportunities
- Sources & References
Executive Summary: Key Findings & Market Highlights 2025–2030
The zinc-boron nanocomposite battery sector in 2025 is characterized by accelerated advancements in material science, scaling pilot production, and growing interest from both established battery manufacturers and emerging startups. The integration of boron-based nanomaterials with zinc anodes addresses key industry challenges—namely dendrite formation, limited cycle life, and cost efficiency—positioning these batteries as strong contenders for grid storage and mobility applications over the 2025–2030 period.
- Manufacturing Innovations: Several companies have announced pilot production lines for zinc-boron nanocomposite batteries, leveraging automated slurry processing, roll-to-roll coating, and in-line quality monitoring. For instance, EOS Energy Enterprises has expanded its R&D facilities to accelerate prototyping of zinc-based chemistries, with a stated focus on scalable nanocomposite integration. Similarly, Zinc8 Energy Solutions has reported advancements in electrode engineering, including the use of boron compounds for improved conductivity and cycle stability.
- Performance Benchmarks: Initial data from pilot lines in 2025 indicate that zinc-boron nanocomposite batteries are achieving cycle lives exceeding 4,000 cycles at >80% capacity retention—a significant improvement over conventional zinc batteries. Energy density is reported in the range of 90–120 Wh/kg, with ongoing optimization to close the gap with lithium-ion performance for stationary storage (EOS Energy Enterprises).
- Supply Chain and Scalability: Zinc and boron are globally abundant and less geographically constrained than lithium or cobalt, providing a favorable outlook for supply chain stability. Battery manufacturers such as Zinc8 Energy Solutions emphasize that the use of widely available raw materials supports cost reduction and domestic manufacturing in North America and Europe.
- Commercialization Outlook (2025–2030): Industry roadmaps project that by 2027–2028, the first commercial-scale deployments of zinc-boron nanocomposite batteries will enter grid and microgrid markets, with pilot projects already underway in partnership with utility providers (EOS Energy Enterprises). Cost parity with mid-tier lithium-ion chemistries is targeted by 2030, driven by economies of scale, automation, and ongoing material innovation.
In summary, zinc-boron nanocomposite battery manufacturing is entering a critical phase of industrial validation and early commercialization. The next five years will see intensified competition, with key players investing in proprietary manufacturing processes, strategic partnerships, and demonstration projects to capture opportunities in the rapidly evolving energy storage landscape.
Technology Overview: Zinc-Boron Nanocomposites and Their Unique Advantages
Zinc-boron nanocomposite battery manufacturing represents an emerging frontier in the development of advanced, sustainable energy storage systems. These batteries leverage the synergistic properties of zinc and boron at the nanoscale, promising significant improvements in safety, energy density, and operational lifespan compared to conventional lithium-ion chemistries. As of 2025, the technology is transitioning from laboratory-scale innovation to pilot and early commercial-scale manufacturing, driven by growing demand for safer, non-flammable, and environmentally benign alternatives.
The unique advantages of zinc-boron nanocomposites stem from the combination of zinc’s high theoretical capacity and boron’s exceptional chemical stability and conductivity. At the nanoscale, boron additives can suppress dendrite growth—one of the primary causes of short-circuiting and cell failure in zinc-based batteries—while enhancing charge transport and mechanical integrity of the electrode. This results in batteries that offer high coulombic efficiency, robust cycle stability, and resistance to thermal runaway, a critical safety concern in lithium-based systems.
Recent developments indicate that zinc-boron nanocomposite electrodes can achieve energy densities upwards of 250 Wh/kg, rivaling or surpassing some lithium-ion designs while maintaining non-toxicity and recyclability. For example, companies such as Zinc8 Energy Solutions and Eos Energy Enterprises have aggressively pursued zinc-based battery innovations, with active research into boron-doped and nanostructured cathode and anode materials. While these companies have not yet announced full commercial deployment of zinc-boron nanocomposites, they have signaled ongoing pilot-scale evaluations and strategic partnerships for advanced materials integration.
On the manufacturing side, scalable synthesis of zinc-boron nanocomposites involves sol-gel processing, chemical vapor deposition, and electrodeposition techniques, with increasing emphasis on automation and quality control for uniform particle distribution. Industry stakeholders such as Umicore are investing in next-generation cathode manufacturing lines capable of handling nanostructured materials and ensuring batch-to-batch consistency. The push towards gigafactory-scale zinc-based battery production is expected to accelerate as supply chains for boron compounds, notably from suppliers like Eti Maden, become more robust and cost-competitive.
Looking to the next few years, the outlook for zinc-boron nanocomposite battery manufacturing is optimistic. Anticipated advancements in materials engineering, process scale-up, and vertical integration will likely position these batteries as a viable solution for grid storage, e-mobility, and backup power markets. Industry and research collaborations are expected to yield further breakthroughs in cycle life, manufacturability, and system integration, paving the way for broader adoption by the late 2020s.
Current Manufacturing Landscape and Leading Players
The landscape for zinc-boron nanocomposite battery manufacturing in 2025 is characterized by a transition from laboratory-scale innovation to early-stage commercialization, with significant investments in pilot production lines and partnerships between materials suppliers, battery developers, and end-user industries. The unique properties of zinc-boron nanocomposites—such as enhanced conductivity, improved cycle stability, and superior safety profiles—have attracted attention as the energy storage sector seeks alternatives to lithium-ion technologies.
Several organizations are actively engaged in advancing zinc-based battery technologies, with a select few focusing on nanocomposite approaches. Eos Energy Enterprises has expanded its focus from zinc hybrid cathode batteries to exploring advanced additives, including boron-based nanomaterials, to improve performance and longevity of its aqueous zinc systems. In 2024, Eos announced a pilot project integrating nanocomposite-modified electrodes, with scale-up plans targeting 2025 for select grid storage partners.
Materials companies such as Umicore and 3M have entered the supply chain, developing specialty boron and nano-zinc powders tailored for battery manufacturing. These companies are investing in refining particle size distribution and surface functionalization processes to enable uniform dispersion in electrode slurries, with commercial samples available to battery producers in 2025.
In Asia, Tsinghua University and its spin-off companies are collaborating with regional battery manufacturers to establish pilot-scale production lines for zinc-boron nanocomposite anodes and cathodes. These efforts are supported by government grants under China’s “New-Type Energy Storage Demonstration Projects” initiative, aiming for domestic deployment in stationary and mobility applications within the next three years.
Meanwhile, BASF has leveraged its expertise in advanced materials to prototype boron-doped zinc oxide nanostructures for next-generation batteries, partnering with European automotive OEMs to co-develop manufacturable electrode coatings. Prototypes are undergoing validation in 2025, with a view toward limited commercial release by 2026.
Looking ahead, the zinc-boron nanocomposite battery sector is expected to progress from pilot validation to small-batch production by 2026–2027. Key challenges remain in scaling up uniform nanocomposite synthesis, maintaining cost-competitiveness, and ensuring compatibility with existing battery assembly lines. However, with persistent investment from leading materials suppliers and battery firms, the technology is positioned to carve out a niche in grid storage and heavy-duty mobility markets over the next few years.
Breakthrough Innovations: Recent R&D and Emerging Patents
The field of zinc-boron nanocomposite battery manufacturing has witnessed notable breakthroughs in recent years, with several organizations filing patents and disclosing advanced research in the quest for safer, more efficient, and scalable next-generation batteries. As of 2025, the focus has shifted from fundamental material synthesis to the integration of boron nanomaterials with zinc-based chemistries for both primary and secondary battery systems.
A prominent recent innovation is the development of boron-doped graphene and boron carbide nanostructures as conductive additives and protective layers on zinc anodes. This approach aims to suppress dendrite growth, a significant obstacle in conventional zinc batteries. In 2024, Samsung Electronics filed a patent application for a zinc-boron composite electrode that leverages boron’s chemical stability to enhance cycle life and improve safety margins for large-scale energy storage systems.
On the materials front, Mitsubishi Chemical Group disclosed progress in synthesizing boron-rich nanocomposites that act as both solid electrolytes and interfacial stabilizers, significantly reducing interfacial resistance and boosting energy density. Their 2025 pilot line is expected to validate the scalability of these materials for mass production.
In the United States, 3M has advanced the field through its proprietary nanostructured boron-polymer blends, intended to be incorporated into zinc battery separators. Their 2025 R&D roadmap includes pilot deployments in stationary grid storage applications, targeting both improved cycle stability and enhanced operational safety.
Meanwhile, Chinese battery manufacturers such as CATL are collaborating with academic institutes to file patents on zinc-boron composite cathodes, especially for use in high-rate and flexible battery formats. Their research highlights the role of boron nanomaterials in facilitating rapid ion transfer and maintaining electrode integrity during repeated charge-discharge cycles.
The outlook for the next several years is marked by a transition from lab-scale demonstrations to commercial pilot lines, with industry leaders expecting to achieve initial commercialization by 2026–2027. Early-stage deployments will likely focus on stationary storage and specialty applications where non-flammable, sustainable chemistries are at a premium. These breakthroughs are also aligned with growing regulatory and market demands for batteries that are both environmentally benign and inherently safe, positioning zinc-boron nanocomposite technology as a strong contender in the evolving energy storage sector.
Production Challenges and Solutions in Scaling Nanocomposite Batteries
The transition from laboratory-scale prototypes to commercial production of zinc-boron nanocomposite batteries presents several technical and operational challenges, particularly as the industry approaches scalability targets in 2025. Although the fundamental advantages of zinc-boron systems—such as enhanced energy density, improved cycle life, and inherent safety—have been validated in controlled environments, scaling manufacturing processes to meet industrial demand introduces complex hurdles.
One of the primary challenges lies in the synthesis and uniform dispersion of boron-based nanomaterials within the zinc matrix. Maintaining consistent particle size distribution and preventing agglomeration during high-throughput production are critical for achieving reproducible battery performance. Companies like AMTE Power and NantEnergy, both active in advanced battery material research and pilot-scale manufacturing, have cited the need for precise material engineering controls and robust quality assurance protocols to translate laboratory gains into reliable, mass-produced cells.
Electrode fabrication processes must also contend with the chemical reactivity of boron nanostructures. Boron’s high surface area enhances electrochemical activity but also accelerates side reactions with aqueous electrolytes, particularly during the calendar life of the battery. To address this, manufacturers are developing protective coatings and electrolyte additives, as well as refining slurry mixing and calendaring steps to limit boron exposure before cell assembly. For instance, Primobius, which specializes in battery recycling and advanced electrode materials, has indicated ongoing development of scalable methods for handling sensitive nanomaterials while minimizing contamination and degradation throughout the production line.
Another persistent issue is the adaptation of existing battery manufacturing infrastructure. Many current facilities are optimized for lithium-ion chemistries, requiring significant retooling to accommodate zinc-boron nanocomposite electrodes. Automated assembly lines must be recalibrated for novel material viscosities and layer thicknesses, while formation protocols for initial cell conditioning are being redefined to suit the electrochemical profiles of zinc-boron systems. Pilot programs at AMTE Power and NantEnergy are examining modular upgrades and flexible production systems as interim solutions, awaiting larger capital investments in dedicated manufacturing assets.
Looking ahead to the next few years, the industry is expected to focus on integrating advanced in-line monitoring techniques—such as spectroscopy and machine vision—to ensure nanomaterial uniformity during roll-to-roll processing. Cross-sector collaboration between material suppliers, equipment manufacturers, and battery integrators will be key to overcoming production barriers. With ongoing efforts and anticipated advancements, zinc-boron nanocomposite batteries are poised to enter low- to mid-scale commercial deployment by the late 2020s, with gradual increases in process efficiency and product yield as manufacturing expertise matures.
Cost Dynamics and Price Forecasts for 2025–2030
The global push for safer, lower-cost, and more sustainable energy storage solutions is accelerating the development and commercialization of zinc-boron nanocomposite batteries. As industry players scale up pilot lines and advance toward mass production, an evolving landscape of cost dynamics is emerging for 2025 and the subsequent years.
Currently, the principal cost drivers in zinc-boron nanocomposite battery manufacturing stem from the sourcing and processing of high-purity zinc and boron compounds, nanomaterial synthesis, and the integration of these materials into scalable cell architectures. Manufacturing costs are further influenced by cell design complexity, yield rates in electrode fabrication, and the adoption of advanced electrolyte formulations. As of early 2025, pilot projects indicate manufacturing costs for zinc-based batteries remain higher than mature lithium-ion alternatives, largely due to the novelty of nanocomposite integration and the relative lack of large-scale infrastructure.
However, several manufacturers are reporting rapid cost declines as they refine their processes and scale up. For example, Eos Energy Enterprises and ZnShine New Energy are both investing in automated electrode manufacturing lines and streamlined nanomaterial synthesis pathways, which are expected to reduce per-kWh costs by as much as 30–40% between 2025 and 2027. Additionally, Zinc8 Energy Solutions has announced initiatives to localize boron sourcing and develop in-house nanocomposite processing, further lowering both supply chain and production expenses.
Industry analysts and technology developers project that, as manufacturing volumes increase and economies of scale are realized, zinc-boron nanocomposite battery pack costs could approach $90–$120 per kWh by 2030—down from early estimates of $200–$250 per kWh in 2025. Key to this transition will be the maturation of nanomaterial supply chains, reductions in energy and water consumption during synthesis, and the spread of modular cell manufacturing approaches. These trends are supported by recent partnerships, such as Eos Energy Enterprises collaborating with supply chain partners to secure long-term contracts for boron and zinc derivatives, and ZnShine New Energy leveraging vertically integrated manufacturing to stabilize input costs.
Looking ahead, the outlook for zinc-boron nanocomposite battery costs remains highly positive. Should ongoing pilot deployments prove successful and regulatory approvals proceed as anticipated, the next few years will likely see continued downward pressure on prices, positioning this technology as a competitive alternative for stationary storage and grid-scale applications by the close of the decade.
Competitive Analysis: Zinc-Boron vs. Lithium-Ion and Other Chemistries
As of 2025, the competitive landscape for zinc-boron nanocomposite battery manufacturing is rapidly evolving, with a particular focus on how this emerging chemistry compares to established technologies such as lithium-ion, zinc-air, and sodium-ion batteries. The primary competitive advantages being investigated for zinc-boron nanocomposites include enhanced safety, reduced reliance on critical minerals, and the potential for lower-cost, scalable production.
Lithium-ion batteries, produced at scale by manufacturers such as CATL and Panasonic, remain the market leaders in terms of energy density and cycle life. However, they are associated with safety risks (thermal runaway), supply chain vulnerabilities due to dependence on lithium and cobalt, and environmental concerns regarding mining and recycling. In contrast, zinc-boron nanocomposite batteries typically use more abundant and less geopolitically sensitive materials, positioning them as a promising alternative for stationary storage and certain mobility applications.
Companies like EOS Energy Enterprises and Zinc8 Energy Solutions have advanced zinc-based batteries for grid storage, though not yet with boron nanocomposites. Early pilot projects in 2025 are focusing on the integration of boron nanostructures to improve cycle stability and rate performance, aiming to overcome dendrite formation and zinc corrosion—persistent challenges in traditional zinc chemistries. Laboratory data in recent industry disclosures suggest that nanocomposite approaches can yield cycle lives surpassing 3,000 cycles with minimal capacity fade, rivaling some lithium-iron-phosphate (LFP) chemistries (Zinc8 Energy Solutions).
Manufacturing processes for zinc-boron nanocomposite batteries are anticipated to be less energy-intensive than lithium-ion, as they avoid high-temperature sintering and toxic solvents. Pilot lines set up in North America and East Asia are leveraging aqueous electrolytes and modular assembly, potentially allowing for more localized supply chains and simplified recycling protocols. The U.S. Department of Energy, through initiatives like the ARPA-E program, is supporting demonstration projects aiming to validate these manufacturing claims and scale up production over the next two to three years.
Outlook for 2025 and beyond sees zinc-boron nanocomposite batteries carving out a niche in long-duration grid storage, rural electrification, and backup power markets where safety, cost, and supply chain resilience are paramount. While lithium-ion is expected to dominate high-density mobility applications, ongoing advances in nanocomposite formulations and manufacturing could position zinc-boron as a strong competitor in stationary and specialty sectors by 2027, challenging both legacy and next-generation chemistries.
Key Application Sectors: EVs, Grid Storage, and Beyond
Zinc-boron nanocomposite battery technology is rapidly gaining traction as a promising solution for next-generation energy storage, with key application sectors including electric vehicles (EVs), grid-level energy storage, and emerging areas such as portable electronics and backup power. The unique properties of zinc-boron nanocomposites—such as high theoretical capacity, intrinsic safety, and material abundance—are driving significant interest and investment from both established manufacturers and innovative startups.
In the electric vehicle sector, the global push for sustainable and affordable alternatives to lithium-ion batteries is fueling research into zinc-based chemistries. Companies like Eos Energy Enterprises have demonstrated large-scale zinc battery deployments for stationary applications, while ongoing R&D efforts are targeting improvements in energy density and cycle life using boron-based nanomaterials. These advancements are expected to make zinc-boron nanocomposite batteries increasingly competitive for light commercial EVs and urban mobility solutions by 2025 and beyond.
Grid storage represents another major application, with utilities and independent power producers seeking safe, long-duration storage systems to balance renewable energy fluctuations. Zinc-boron nanocomposite batteries, with their non-flammable aqueous electrolytes and potential for low-cost scale-up, are positioned as attractive candidates for multi-hour and daily cycling. Pilot projects and test installations are anticipated to accelerate over the next few years, supported by collaborations between research institutions and manufacturers such as Zinc8 Energy Solutions, which is advancing zinc-based flow batteries for utility-scale storage.
Beyond transportation and grid storage, zinc-boron nanocomposite batteries are being explored for diverse sectors including backup power systems, telecommunications, and portable consumer electronics. The inherent safety and environmental friendliness of these batteries make them suitable for indoor and sensitive installations where traditional chemistries pose risks. Companies like PrimeTech Composite are developing advanced nanocomposite materials that could find their way into compact, high-performance batteries for off-grid and emergency applications as early as 2025.
Looking forward, the outlook for zinc-boron nanocomposite battery manufacturing is robust, with ongoing improvements in materials engineering, scalable production techniques, and system integration. As regulatory pressures and market demands for sustainable energy storage intensify, the adoption of zinc-boron nanocomposite batteries across EVs, grid storage, and beyond is expected to accelerate, supported by strategic investments and industry partnerships.
Regulatory Landscape and Industry Standards (ieee.org, batteryindustry.tech)
The regulatory landscape for zinc-boron nanocomposite battery manufacturing is rapidly evolving as the technology advances toward commercialization in 2025 and beyond. Regulatory bodies and industry standards organizations are focusing on establishing guidelines that address safety, environmental, and performance aspects unique to nanomaterial-enabled batteries. Unlike traditional lithium-ion technologies, zinc-boron nanocomposite batteries present distinct challenges and opportunities, including novel chemistries, materials handling, and end-of-life management.
In 2025, the IEEE continues to play a significant role in shaping technical standards for emerging battery chemistries. The IEEE Standards Association’s ongoing work on energy storage and nanomaterials standards includes efforts to define test methodologies, safety criteria, and performance metrics tailored to next-generation batteries. These activities aim to harmonize international approaches, facilitating cross-border trade and accelerating market adoption of zinc-boron nanocomposite technologies.
Meanwhile, the industry is actively collaborating through consortia and working groups to ensure compliance with existing and forthcoming regulatory frameworks. For instance, battery manufacturers are closely monitoring the European Union’s Battery Regulation (adopted in 2023, entering phases of enforcement through 2025–2027), which imposes rigorous requirements on sustainability, material sourcing, labeling, and recycling for all battery types, including advanced chemistries. These regulations are prompting zinc-boron battery developers to invest in traceability systems and eco-design strategies to meet environmental and circular economy demands.
On the safety front, key players are working with industry bodies to validate the benign failure modes and low flammability of zinc-boron nanocomposite batteries compared to traditional lithium-ion cells. Manufacturers such as ZAF Energy Systems and Eos Energy Enterprises (both active in zinc-based battery development) are participating in pilot projects to demonstrate compliance with international transport and storage regulations, including UN Manual of Tests and Criteria and UL safety standards.
Looking ahead, the next few years are expected to bring increased harmonization of standards globally, with organizations like the IEEE and regional authorities integrating findings from real-world deployment of zinc-boron nanocomposite batteries. The industry outlook anticipates that by 2027, comprehensive regulatory frameworks will be in place to address the entire lifecycle of these batteries—from raw material sourcing and nanomaterial safety to recycling protocols—enabling broader adoption in grid storage and mobility sectors. As industry standards mature, manufacturers are expected to benefit from clearer pathways to certification, streamlined quality assurance, and enhanced consumer and environmental safety.
Future Outlook: Market Size, Growth Trajectories, and Strategic Opportunities
The zinc-boron nanocomposite battery sector is poised for significant developments in 2025 and the following years, driven by the need for safer, more sustainable alternatives to traditional lithium-ion batteries. As the global energy storage market continues to expand—fueled by the electrification of transportation, grid modernization, and renewable integration—zinc-based chemistries are gaining attention for their inherent safety, cost-effectiveness, and environmental compatibility. The incorporation of boron nanomaterials into zinc batteries is projected to enhance energy density, cycle life, and charge rates, positioning these technologies for strategic growth.
The outlook for zinc-boron nanocomposite battery manufacturing is closely tied to the activities of pioneering companies and emerging manufacturing partnerships. Entities such as EOS Energy Enterprises and ZAF Energy Systems are actively advancing zinc-based battery platforms, with 2025 expected to see the first scaled manufacturing pilots incorporating advanced nanocomposite materials. While boron-enhanced formulations are still in pre-commercial stages, research collaborations with specialty chemical suppliers and nanomaterial innovators—such as 3M and BASF—are anticipated to yield breakthroughs in cathode and electrolyte engineering, potentially unlocking double-digit improvements in performance metrics.
Industry forecasts suggest that the global zinc battery market could surpass $3 billion by the end of the decade, with nanocomposite subsegments capturing a growing share as manufacturing processes are refined and validated. Strategic opportunities abound in stationary storage for renewables, microgrid deployments, and backup power for critical infrastructure—markets where safety and total cost of ownership outweigh sheer energy density. In the near term, demonstration projects and government-supported pilots are expected to play a critical role; for instance, EOS Energy Enterprises has secured contracts for multi-megawatt zinc battery installations as part of U.S. Department of Energy initiatives, setting a precedent for technology validation and market entry.
- Manufacturers are seeking joint ventures and licensing agreements to accelerate scale-up and derisk commercialization, signaling a move toward more integrated supply chains for nanomaterials and battery components.
- Strategic investments by automotive and grid technology leaders are anticipated as the performance of zinc-boron nanocomposites approaches that of incumbent lithium-ion solutions in high-cycling and high-safety applications.
- Regulatory support for sustainable and non-critical mineral battery chemistries is likely to create favorable market conditions, especially in North America and the European Union.
In summary, 2025 marks a transitional year for zinc-boron nanocomposite battery manufacturing, with substantial momentum toward commercialization, strategic partnerships, and market differentiation based on safety, sustainability, and cost advantages. Continued innovation and pilot deployments will determine the pace and scale of adoption in the next several years.